1 Introduction
Wood contains about 25% of lignin, which together with hemicelluloses and cellulose form the structural components of trees and various plants. Lignins are a by-product mainly obtained from the pulp and paper industry. Most of the raw material is burnt as an energy source, although it offers many other added-value uses. One of the possible applications is to use lignins in the formulation of polymeric materials in order to increase their content of renewable resources. In many cases, lignins are used only as low-cost fillers [1], and the objective is to minimize the loss of ultimate mechanical properties. The elongation at break is generally drastically decreased by the addition of lignins (cohesion loss), while the tensile strength can be maintained relatively constant (up to a 40% w/w incorporation rate): generally (blends with polyolefins) a slight decrease of strength at break as a function of lignin content is obtained, but when a more compatible polymer is used (polyamide, polyesters), the reinforcing effect of lignin filler leads to an increase of the Young modulus, stress at yield and strength. While aiming at an improvement of the reinforcing effect, different strategies of filler/polymer compatibilisation have been proposed: the use of lignin-grafted polymers ([2], lignin/PS blends), surface grafting of lignin particles ([3], lignin PP blends), use of plasticisers to decrease the degree of association of lignins ([4], lignin PVC blends), or decrease in the lignin polarity by grafting ethyl or acetyl groups on hydroxyls ([5], lignin/hydroxypropyl cellulose blends). Better than acting as an expensive (modified or formulated) reinforcing filler, lignins can also bring specific properties acting as chemically active solute in the polymer phase: crosslinker in PP [6], antioxidant in PP and polybutadiene [7–9], polyaniline conductivity modifier [10], hydrophobic coplasticiser in starch materials [11]. In these cases, a partial solubility of lignin in the matrix is required. Improving the solubility of lignins in polymers could open up new fields of application, using the aromatic structure as macromonomers in the synthesis of original macromolecules; lignin-based copolymers have currently no economical interest, since they are obtained in solvents, but new applications are opened by bulk polycondensation ([12,13], polyesters).
The aim of this paper is (i) to examine good polymer candidates exhibiting good compatibility with Kraft lignin, the most abundant available industrial lignin – obviously they generally correspond to semi polar macromolecules –, (ii) to select very polar (e.g., starch) and apolar (e.g., polypropylene) polymers in order to identify the structural features of good lignin candidates, exploiting the natural variability of lignin structure.
The usual criterion used in the applied researches in the field of polymer blends is to look at the glass transition of the two components (if one for the blend, perfect blend, if two , they are shifted). The problem is that this method cannot be applied when one component is in minor content. In this paper, the compatibility is simply evaluated by the blend morphology, studied by visible microscopy.
2 Experimental
2.1 Kraft lignin–polymer blends
Kraft lignin was provided by Westvaco Charleston SC, USA.
Characteristics of tested polymers are given in Table 1. PP, PEBD, POE, PS, PAN, PVC, PVAc, PHBV, PEA, PBSA have been blended with lignins using the following systematic procedure. Lignins are dissolved in dioxan/water (9:1), mixed at 1% in weight (dry basis) in each polymer powder and dried under vacuum overnight. The blend is extruded with three zone micro-extruders heated at 180–190–200 °C respectively and equipped with a slit die heated at 200 °C (Scamia, France), at a rotational speed of 80 rpm. Film thickness is approximately 500 μm. All the materials were obtained in these conditions except PEA, which was extruded at lower temperature (135–145–150 °C), because of its too low viscosity at 200 °C.
Characteristics of polymers used for blend formulations
Polymer | Provided by | ||
PEBD | Low density polyethylene | 7.7–8.3 | Cryovac (Italy) |
PP | Polypropylene | 9.2–9.4 | Cryovac (Italy) |
POM | Polymethylene oxyde | 11.8 | Aldrich |
POE | Polyethylene oxyde | 9.9 | Aldrich |
PS | Polystyrene | 9.1 | Cryovac (Italy) |
PAN | Polyacrylonitrile | 12.3–12.7 | Cryovac (Italy) |
PVC plast | Plasticised PVC | 9.4–10.8 | Dorlyl (France) |
PVC | Polyvinyl chloride | 9.4–10.8 | Cryovac (Italy) |
PVAc | Polyvinyl acetate | 9.4 | Aldrich |
PHBV | Poly(hydroxybutyrate-co-hydroxyvalerate) | 8.9 | Monsanto |
PEA | Poly(ester amide) (PEA) | 9.8 | Bayer (France) |
PBSA | Poly(butylene succinate-adipate) (bionolle) | 10.1 | Showa high polymer Co. (Japan) |
Starch | 18.8 | Amylum (France) |
Polymer solubility parameters are calculated from group contribution methods. The average value of the results obtained from the methods of Small, Van Krevelen, and Hoy is displayed in Table 1. The solubility parameter of lignins being generally given between 10 and 11 (cal cm−3)1/2 (10.5 in Ref. [14]), the selected polymers exhibit solubility parameter values mainly between 9 and 10.5. We focused on polymers of lower polarity than lignin, because current material applications involve rather hydrophobic structures.
2.1.1 Image analysis
The acquisition of images was made with a Leica Leitz DMRB microscope equipped with a Sony power HAD DXC950P video camera. Images were analysed by Vision Stage software. The grey level images are treated to clean the picture. After thresholding operations, the binary images are treated in order to eliminate artefacts (remove small objects, border kill, and operations of erosion–reconstruction). The last step consists in a quantitative determination of particles (number and surface).
2.1.2 UV microspectrophotometry
The same microscope is used for UV microspectrophotometry. Measurements are done at 280 nm (Xenon UV lamp XBO 75 W) on 10- to 60-μm thick samples (depending on the nature of the polymer and the concentration of lignin in the sample). Measurement area has a 40-μm diameter.
2.2 Lignins–polypropylene blends
The Kraft lignin was fractionated by successive solvent extractions using a Soxhlet apparatus: dichloromethane extraction (extract noted KLDi) followed by methanol extraction (extract noted KLM, and residue noted KLMr). Extractions were run until the solvent was colourless, then the solvent was removed under vacuum and the lignins dried under vacuum overnight. Yields are KLDi: 6%, KLM: 40%, KLrM: 54%. As reported in a previous paper [15], the average molecular weight of LKDi, LKM and LKrM were respectively Mw = 490 g mol−1 and Mn = 240 g mol−1, Mw = 3060 g mol−1 and Mn = 440 g mol−1, Mw = 8270 g mol−1 and Mn = 1030 g mol−1.
The PP/lignin fractions blends are obtained using the same procedure as with Kraft lignin polymer blends.
2.3 Lignins–plasticised starch blends
Kraft lignin was provided by Westvaco (Charleston SC, USA). Fractions were obtained by successive solvent extractions, using the same procedure as for lignin PP blends, but at a lower scale and without any Soxhlet apparatus. Moreover, the Kraft lignin batches were different for both extractions. As a consequence the lignin yields and characteristics are slightly different:
- • KLDi, yield 1%, Mn = 294 g mol−1;
- • KLM, yield 48.7%, Mn = 788 g mol−1;
- • KLrM, yield 48.8%, Mn = 1334 g mol−1.
Despite these variations, the orders of magnitude are the same and the characteristics can be considered as comparable considering the general character of this paper. The structure of these three lignin fractions was intensively investigated in Ref. [11].
Wheat starch (type A, 87% dry matter, 27% amylose, 73% amylopectine) was commercially available (F33 Amylum Aquitaine, France).
Glycerol was used as a plasticiser, in a glycerol/dried starch ratio of 22:78 (w/w). The casting method is used for processing plasticised starch-lignin blends. Dimethylsulphoxide is employed as casting solvent using a 5-wt% polymer concentration. The use of such a good solvent of lignins and starch allows the components to mix intimately at a molecular level. However, it requires a long drying step (5 hours at 90 °C and atmospheric pressure followed by a 12-h drying at 60 °C under vacuum). Films with 80:20 starch/lignin ratio are prepared from the native Kraft Lignin and from the KLrM and KLM fractions, whereas the low-molecular-weight KLDi fraction is only incorporated in a 90:10 ratio.
2.3.1 Image analysis
Light microscopy is realized on film cross-sections (∼10 μm) suspended in water.
2.3.2 Starch revelation
Blue staining by a 10-min treatment of lugol reagent followed by washing. Lignin detection by fluorescence is performed using a UG exciter filter transmitting wavelengths from 300 to 400 nm and a filter barrier transmitting wavelengths above 400 nm. The average diameter of particles is calculated from scanned micrographs using an IMAQ-vision (National Instrument) image analysis software.
3 Results
3.1 Compatibility of Kraft lignin with different polymers. Correlation with the solubility parameter
Examples of images obtained by visible microscopy are given in Fig. 1. As expected from the large range of solubility parameters, different morphologies are obtained, ranging from an apparently homogeneous blend (lignin/PBSA) to a dispersion of aggregates (lignin/PE). Aggregates can be characterized both by their concentration (number of aggregates per picture) and their dimension (e.g., surface). Image analysis was used to correlate the blend morphology using the solubility parameters of the polymer matrix. Different descriptors were tested. The total surface of aggregates per photograph that describes both the concentration and the dimension of aggregates is clearly the best-correlated descriptor. It can be seen in Fig. 2 that the surface per photo (‘SPP’) shows a minimum value near 9.5–10 (cal cm−3)1/2. Obviously, the dependence of lignin solubility upon polymer solubility parameter is verified; this minimum corresponds roughly to the solubility parameter range given for lignins; the real minima position is probably higher than 10, but the lack of experimental data in the ‘polar’ range does not allow us to validate this assumption.

Blend morphology of Kraft lignin (1%) in PEBD and PBSA (visible microscopy).
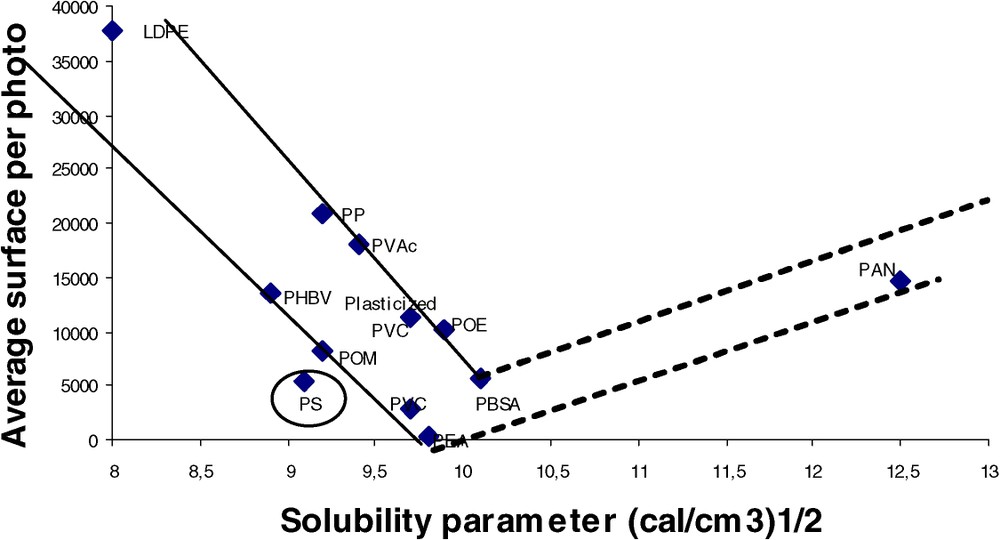
Correlation between SPP and the solubility parameter of the polymer matrix.
More generally, the compatibility seems very sensible to the variation of solubility parameter: even if the polymer descriptor used is coarse (because δ was calculated, and because we did not use three dimensional solubility parameters), it is worth noting that the ‘compatibility’ range probably concerns less than one unity of δ.
Looking at the results of a more detailed analysis (Fig. 2), the following remarks apply. (i) The position of polystyrene is surprising; although its solubility parameter is low, a good compatibility is obtained. Specific interactions between lignin and the polymeric matrix as already evidenced on other blends systems [16] or a slight chemical reactivity (grafting) are likely to account for this unexpected compatibility. (ii) PVC can be either very compatible, or not, depending on its formulation: plasticised PVC has a lower compatibility, probably due to the fact that all its sorption sites are saturated. Another interpretation is that the presence of plasticisers could shift slightly the macroscopic apparent value of the solubility parameter. The low compatibility of formulated PVC could explain the disappointing mechanical and weathering properties of lignin PVC blends described previously [17,18]. (iii) It was already known that the family of biodegradable polyesters were good candidates to be blended with lignins. However, as a consequence of the wide range of solubility parameter covered by this family, a wide range of degrees of compatibility towards lignins is obtained. As previously mentioned, the compatibility is very sensitive to δ. Consequently, it makes it easy to optimise the compatibility by changing the nature and/or the ratios of the comonomers constitutive of polyesters. (iv) Only non-hydrolysed polyvinyl acetate was tested. The low compatibility of PVAc obtained here could be optimised as a function of the hydroxyl concentration, which can be monotonously adjusted by the degree of hydrolysis (numerous commercial products are proposed).
3.2 Compatibility of Kraft lignin with different polymers. Concentration effects
The best compatibility was obtained for PEA, PS, PBSA, and unplasticised PVC (Fig. 2). Fig. 3 shows the evolution of the total surface per picture (SPP) with the lignin content. As the morphology descriptor chosen is empirical, we can obviously not discuss on the mathematical dependence of SPP on lignin content. On the whole, we can remark that SPP increases with lignin content (decrease of compatibility). More surprising is the behaviour of PS, which on the contrary shows a decrease of SPP with the increasing lignin content: at a 10% concentration, the PS compatibility (evaluated by a morphologic criterion) becomes the best in the panel tested.
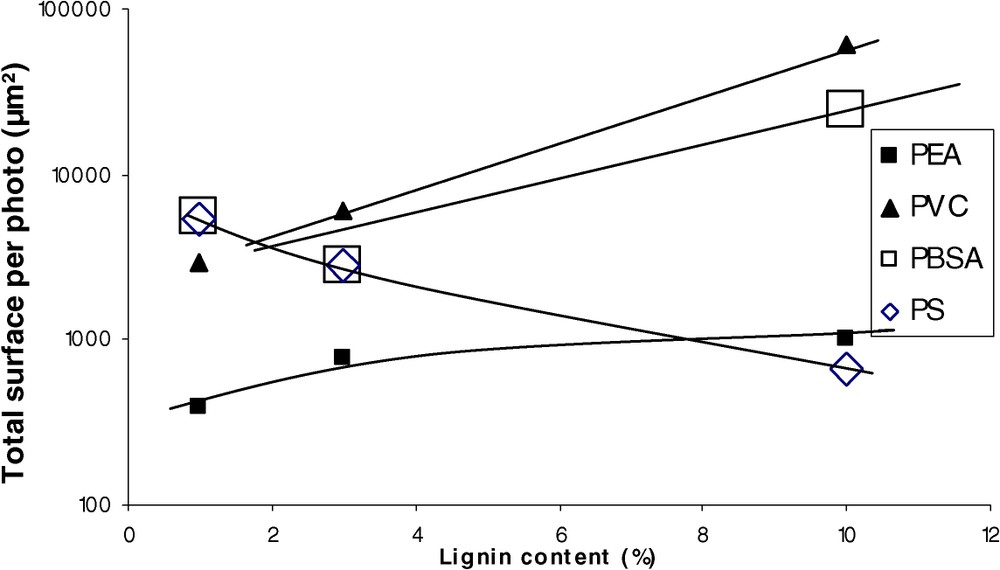
Evolution of SPP with lignin concentration.
Another way to assess the compatibility of lignin with polymers is to measure their solubility. The lignin concentration was determined through the UV absorbance of microtome section (UV microspectrophotometry) in homogeneous areas assuming that the undetectable material at the scale of visible microscopy is soluble (i.e. no aggregate at the sub-micron scale, which is obviously wrong) (Fig. 4).

UV absorbance on microtome sections (UV microspectrophotometry) in homogeneous areas (where aggregates are not observed at the visible-microscopy scale) as a function of lignin concentration.
Taken as reference of low affinity, PP shows a constant absorbance as a function of lignin concentration: the increase in lignin concentration leads to an increase in the surface and the number of aggregates and the ‘soluble’ fraction remains constant within the experimental detection range: the saturation of PP by soluble lignins is obtained with very low lignin contents. In the case of the other polymers, the plots of the optic density versus lignin concentration show a linear increase of absorbance with increasing lignin content. Accordingly, an extinction coefficient can be calculated using the Beer–Lambert law. For PEA, the calculated absorption coefficient has a higher value than those determined by UV spectrometry in solution for Kraft lignin (dioxan/water 90/10 vol/vol, –25 l cm−1 g−1) (see Fig. 4). The discrepancy results from the fact that (i) the UV absorption in solids is different and (ii) the possible presence of sub-micron aggregates could perturb the measure.
In the case of PS, the slope is lower (lower solubility, considering extinction coefficient obtained in PEA as a reference) and remains constant in the concentration range tested. The singular evolution of the PS morphology (Fig. 3) does not correspond to a variation of the solubility coefficient of lignin in PS at high concentration. The decrease in SPP at high concentration is also apparent: the insoluble fraction increases with the lignin concentration, but the diameter of aggregates decreases at a lower level than the resolution of optical microscopy. There are two explanations for the decrease in the aggregates' diameter: the increase in lignin concentration in the polymer phase improves the compatibility with lignin aggregates, or the increase in lignin concentration in PS allows the formation of grafted compounds during extrusion (cf. free radical reactivity of polystyrene), which could act as a compatibiliser at the interfaces.
Considering blend morphologies at low concentration (Fig. 2), PHBV is less compatible than PS. In contrast, the absorbance in (apparently) homogeneous phase indicates a better solubility of lignins in PHBV. This confirms that the blend morphology is only indicative of compatibility, and that it cannot be directly correlated to the proportion of soluble fraction.
In the two following paragraphs, the effects of the lignin structure is investigated considering given selected polymers. In these cases, the quantitative use of the blend morphology can be considered more relevant for the assessment of compatibility and solubility.
3.3 Compatibility of lignins with polypropylene. Lignin structure effect
As reported in a previous paper [15], the average molecular weight of LKDi, LKM and LKrM increased with the solvent polarity ranging from Mn 240 to 1030 g mol−1 (see experimental part), whereas the total hydroxyl contents and nature (aliphatic + phenolic) were roughly identical. The variations of blend morphology (Fig. 5) are consequently mainly connected to the molecular weight. The KLDi sample leads to a very fine morphology. Its high antioxidant property [15] suggests that this fine morphology is associated to a good solubility in the matrix. The objective is not here to show again that the solubility increases with decreasing molecular weight, but rather to look at the molecular weight range, which is necessary to obtain enough solubility together with a fine morphology: in PP, Mw must be lower than 1000 g mol−1. Even if the Kraft lignin is highly depolymerised (due to the drastic conditions of the Kraft paper process), the KLDi fraction represents only 6% of original material. This means that only a quantitatively minor fraction of Kraft lignin is compatible with polypropylene.

Blend morphology of LKDi, LKM, and LKrM (1%) in polypropylene (visible microscopy).
3.4 Compatibility of lignins with thermoplastic starch. Lignin structure effect
As expected from the difference between lignin and starch solubility parameters, a heterogeneous structure is obtained from the blend of the two components (Fig. 6). The structure of cast films from lignin free plasticised starch is based on partially demixed amylose and amylopectine. In starch/lignin films, a heterogeneous distribution of lignin between the two molecular phases is observed: lignin aggregates occur mainly in the amylopectine phase, and consequently is brown coloured. Only few aggregates are observed in the non-coloured amylose domains. This suggests that soluble lignin (and lignin aggregates) is mainly present in (and compatible with) the amylopectine phase, in agreement with the expected less ordered structure of amylopectine compared to amylose.

Blend morphology of Kraft lignin (20%) in plasticised starch (visible microscopy).
Analysing the morphology of the films containing the different lignin fractions allowed us to discriminate the lignin fractions in relation to their molecular weights (Fig. 7). Indeed, lignin structural variations turned out to affect both size and distribution of lignin particles within amylose and amylopectine. Two interesting phenomena are observed. (i) The increase of the average particle diameters (Table 2) from 0.6 μm (starch/LKDi) to 1.0 μm (starch/LKrM), which indicates a better compatibility of low molecular weight components. The number of particles also increases with increasing molecular weights. In the amylose phase, the dependence on the molecular weight is more pronounced, since the low-molecular-weight fraction is the only one to be detected. (ii) The methanol (intermediate) fraction shows a singular ill-explained behaviour: within this fraction, aggregates preferentially occur at the interface between amylose and amylopectin, without any phenolic compounds dissolved in the matrix [19].

Blend morphology of LKDi, LKM, and LKrM in plasticised starch (fluorescence microscopy).
Average diameter of lignin aggregates
LKDi | LKM | LKrM | |
Mn (g mol−1) | 294 | 788 | 1334 |
Average diameter of lignin aggregates (μm) | |||
0.6±0.2 | 0.9±0.3 | 1.0±0.3 |
As for PP lignin blends, the solubility (and the compatibility) of lignins seems highly dependent on the molecular weight distribution. Only a small fraction of low molecular weight Kraft lignin (KLDi yield = 1%) is really compatible, and probably only a small proportion of this fraction is soluble in starch.
4 Conclusion
In this paper, two types of polymer/lignin blends were studied, depending on the polarity of the continuous polymer matrix: partially compatible blends and totally incompatible systems.
Compatible blends could be easily improved by a careful choice of the polymer structure: the blend morphology is very sensible to the variation of solubility parameter; in a low range of polymer matrix solubility parameter , both heterogeneous and homogeneous systems are obtained. By modulating the nature of the comonomers (polyesters, polyesteramides, polyamides) or the PVAc degree of hydrolysis, highly compatible blends could be easily obtained. As only low shifts of the solubility parameter are needed, it could be also possible to exploit lignin variability to improve compatibility.
Both PVC and polystyrene show a rather good compatibility with lignin; specific observations were done on these polymers: PVC, which is often studied from industrial formulations, exhibits a better compatibility when it is not plasticised. PS blends show an increasing compatibility with an increasing lignin concentration (in the 1–10% studied range).
Only low molecular weight lignins are compatible with apolar and very polar matrixes. Although not abundant, these compounds induce interesting specific properties (plasticisers in starch, antioxidants in polypropylene). Rather than using extraction strategies to produce (with a low yield) these components, the controlled pyrolysis of lignins (or direct pyrolysis of natural components) should provide an interesting raw material [20,21]. Since the specific properties of lignins are most frequently based on their phenolic (rather than polymeric) character, mixtures of phenolic residues themselves could be advantageously incorporated into the blends.