1 Introduction
Different procedures can be used to obtain amorphous materials: vapour condensation, melting followed by liquid quenching, solution gelling or crystals irradiation using high-energy beams. Glasses are non-crystalline solids with a short-range order, but no long-range order. Their structure is totally disordered at scale higher than a few nanometres, but homogeneous at the submicronic scale. Glasses are dense materials, but compared to crystals, they exhibit a more open structure. Most of the time, they are obtained from a liquid having low crystallisation ability during the cooling process. They exhibit the glass transition phenomenon. Such a transition arises when structural units of the super-cooled liquid have not enough time to reach their equilibrium configuration. A fast cooling of the melt leads to a glass having a high glass-transition temperature (Tg). Generally, a high glass-transition temperature corresponds to a low glass density. It is worth noticing that silica glass does not follow this rule.
Oxide glasses and especially silicate glasses are synthesised from a mixture of quartz (sand) and alkali or/and earth alkaline carbonates (sometimes sulphates or nitrates). They are heated and react together to form compounds whose melting temperature is lower than the one of silica crystals. The melt is then refined and its homogeneity is often enhanced by stirring.
Working of glass is generally performed from the melt or slightly supercooled liquid. Fibre drawing, casting of large pieces of glass, blowing and pressing are different forming processes which are performed within temperature ranges corresponding to perfectly controlled viscosities (path (a), Fig. 1). Microbeads or enamels are usually obtained by a sintering treatment of the glass powder.

Glass preparation: (a) conventional method, (b) sol–gel method.
2 From the solution to the gel
In this paragraph, we will briefly describe the different attempts performed to obtain gel from liquids at room temperature (path (b), Fig. 1). More information about gels synthesis and characterisation can be found in an excellent book written by Brinker and Scherer 〚1〛.
The gel is a two-phase system, constituted of a solid porous network bathing in a liquid. It is generally obtained through chemical reactions (hydrolysis and polycondensation) from an initial molecular liquid susceptible to be hydrolysed. According to chemical reactions, as a function of time, a solid develops inside the liquid and sol–gel transition occurs.
Silicates are the most common glasses. Two different types of gels can be chosen to synthesise them. The first one corresponds to gels obtained by condensation polymerisation of colloidal silica particles stabilised in aqueous solutions. Colloidal silica particles are prepared from a polycondensation reaction, performed under controlled conditions (pH, temperature, mineral additives) of soluble silicate species present in an aqueous solution. The soluble silicate species are obtained by dissolving in hot water a silicate glass with high alkali content. Colloidal particles (whose size is within the range 150–200 Å) have a spherical shape. They are totally dense, but contain between 2000 and 3000 ppm (in weight) of alkali ions remaining from the starting glass.
These colloidal gels are perfectly appropriate for the preparation of multi-component glasses. They allow us to easily obtain a melt at high temperatures, which is further quenched to give a glass. However, impurities (mainly alkali ions) often induce a crystallisation phenomenon during a further heating treatment 〚2〛.
The second way of obtaining gels consists in performing a chemical reaction in an alcoholic medium. Gel results of a series of reactions of hydrolysis and polycondensation of metal alkoxide chemical compounds. These compounds are often called organometallic compounds. The starting solutions can be purified. After gelling and drying, the resulting solid is of great purity.
Whatever the gel synthesis method, the amorphous network that will further be converted into glass is in contact with a liquid filling its porosity. So the second step deals with liquid removing. This drying step leads to a dried gel called ‘xerogel’. Several methods have been used to obtain xerogels. We can distinguish two xerogels families: freeze drying leads to ‘cryogels’ and supercritical drying leads to the well-known ‘aerogels’. Without any additional information, a xerogel is a gel dried at low temperature under atmospheric conditions. Xerogel shows some similarities with glass, but also noteworthy differences.
Xerogels, like glasses, exhibit a short-range order, while their structure is totally disordered at scales higher than 1–2 nm 〚3〛. The main differences between xerogels and glasses remain in their textural properties. A xerogel is a porous material. It arises from nucleation and growing of particles that agglomerate to form clusters. These clusters also grow and collapse, leading to the creation of a solid network.
Regarding the different steps of gel formation, the resulting solid phase is obviously porous. The porosity is within the range 50–90%, depending on the preparation details and drying conditions.
The pore size spans over a few angstroms (micropores) up to some hundred angstroms (mesopores). According to the fact that fluid within the gel encounters difficulties to flow, we can assume that the number of macropores is low.
Gel porosity induces the following consequences:
- • xerogel is a low density material
- • xerogel has a high specific surface area.
The high specific surface area facilitates reactions with atmosphere. Consequently, the xerogel surface is covered by 4 to 6 OH groups per nm2. This high density of surface silanols (Si–OH) plays a major role during the gel–glass conversion.
3 Details of the conventional drying process
As xerogel is very porous compared to glass, the following step consists in removing xerogel porosity to obtain a material having properties close to those of a full dense glass. This can be achieved performing a thermal treatment in a temperature range corresponding to viscous flow sintering. On one hand, the high specific surface area will be the main driving force for sintering. On the other hand, the OH groups located at the surface will modify sintering kinetics. Physical and chemical properties of the densified material can be expected to depend on the residual OH content as well as the gel chemical composition.
Before sintering, a drying step is obviously required. This stage, if performed without caution, usually destroys the gel integrity. The drying stresses have been carefully studied by Scherer. A comprehensive treatise is reported in reference 〚1〛 (chapter 8). Cracks that develop are due to capillary stresses induced by liquid evaporation, forming a concave meniscus at the pore surface 〚3〛. The Laplace law (equation (1)):
Consequently the solid network shrinks (Fig. 2). The liquid flows from the inside of the gel towards its surface. This liquid flow, J, which at the onset of drying is directly related to the liquid evaporation rate, VE, induces a stress gradient, ∇P, depending on the gel permeability, D, and on the liquid viscosity, η, according to the Darcy law (equation (2)):
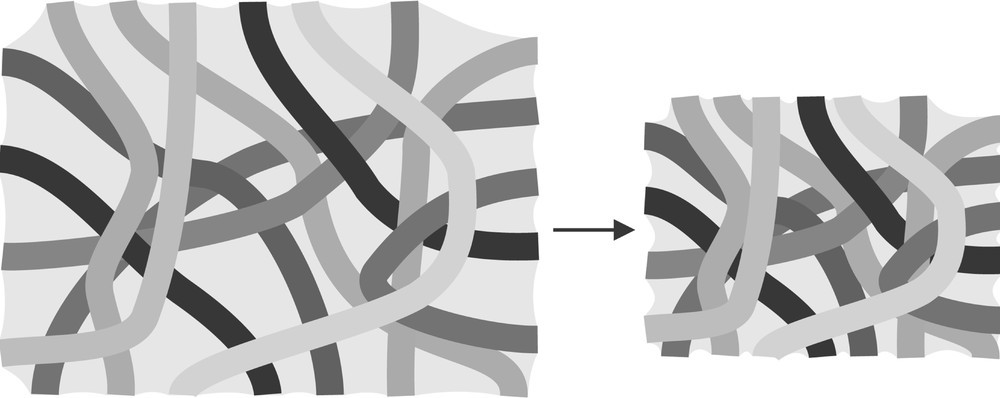
Solid network shrinkage correlated to meniscus radius evolutions during drying.
The gel shrinkage slows down as drying progress proceeds. The shrinkage stops when the solid network is no more compliant. At this moment, the liquid–vapour interface enters the pores and the curvature radius of the meniscus is the smallest. Consequently, for gel having a low permeability, at this instant, the stress gradient is maximal and the gel cracks 〚4〛.
4 From powered gel to glass
Although catastrophic for bulk glass synthesis, xerogel breakage after drying can be used to easily obtain grains of different composition. They can be used for a variety of applications, like preparation of abrasive powders or microbeads.
Abrasive powders of high quality are based on alumina. Alumina gels (pseudoboehmite), when heated at about 1000 °C, crystallise to give α-alumina crystals, whose morphology can be tailored by seeding the initial solution 〚5, 6〛.
To produce glass microbeads, the initial grains are screened and introduced then into a vertical furnace. At high temperature, grains of irregular shape transform into microbeads having a perfectly defined spherical shape, as a consequence of surface tension. Microbeads diameter obviously depends on initial grain size 〚7〛.
Controlling OH and organic residue contents allows preparation of hollow micro-spheres 〚8〛. A fast heating at high temperature causes the grain surface densification. The glassy surface that is no more porous hinders the removal of remaining gas molecules. These gases induce a swelling of the glass and the formation of an internal spherical cavity. Glass shells of 70 mm diameter with 1-μm wall have been used for laser-induced thermonuclear fusion 〚9〛.
Spherical micro-spheres can also be directly produced from a solution in which the silicon alkoxide is promptly reacted with a base aqueous solution 〚10〛. These spherical particles (0.1–1-μm diameter) have a narrow size distribution. Under gravity and because of their electrostatic repulsion, the spatial arrangement of settled particles is hexagonal 〚11〛. After drying and a gentle sintering treatment, a synthetic 3D opal is obtained (Fig. 3). These opals show peculiar optical properties such as 3D photonic band gap 〚12〛. The pore size, the refractive index difference between silica particles and the material filling the pores are parameters that can be modified in order to improve the required optical properties.

Artificial opal having photonic gap: (a) section, (b) surface.
Starting with a powdered gel, two different methods can also be used to synthesise a dense and transparent glass.
The first one consists in heating the xerogel powder up to temperatures corresponding to the stable liquid. This way is merely analogous to that commonly used to prepare glasses. However, several advantages are associated with gels. The homogeneity of the starting gel is at molecular level since the starting solution is itself homogeneous 〚13〛. Consequently, the stirring of the melt or repeated melting/casting/grinding stages that are commonly carried out to improve glass homogeneity are not useful. Moreover, because the composition is already achieved in the starting solution, the melting and fining stages are reduced in time.
Binary or multi-component silicate glasses and glasses difficult to prepare by melting crystalline compounds are easily prepared from gels. It is worth noticing that the sol–gel process has been successful to synthesise some borate 〚14〛 or fluoride glasses 〚15〛.
Another way to obtain glass from a gel powder consists in using a hot pressing technique. The required temperature to fully sinter the gel is in the range of the glass transition temperature of the parent glass. These temperatures for binary glasses based on glass forming oxides are generally high. Consequently, hot pressing requires dies and pistons made of graphite (Fig. 4). Correlatively, to avoid graphite oxidation, the hot pressing cell must operate under neutral atmosphere (N2) or under reduced pressure 〚16〛. This technique is suited to prepare multi-components and refractory oxide glasses that can decompose if melted at high temperatures. Up to now, these glasses were prepared by chemical vapour deposition 〚17〛.
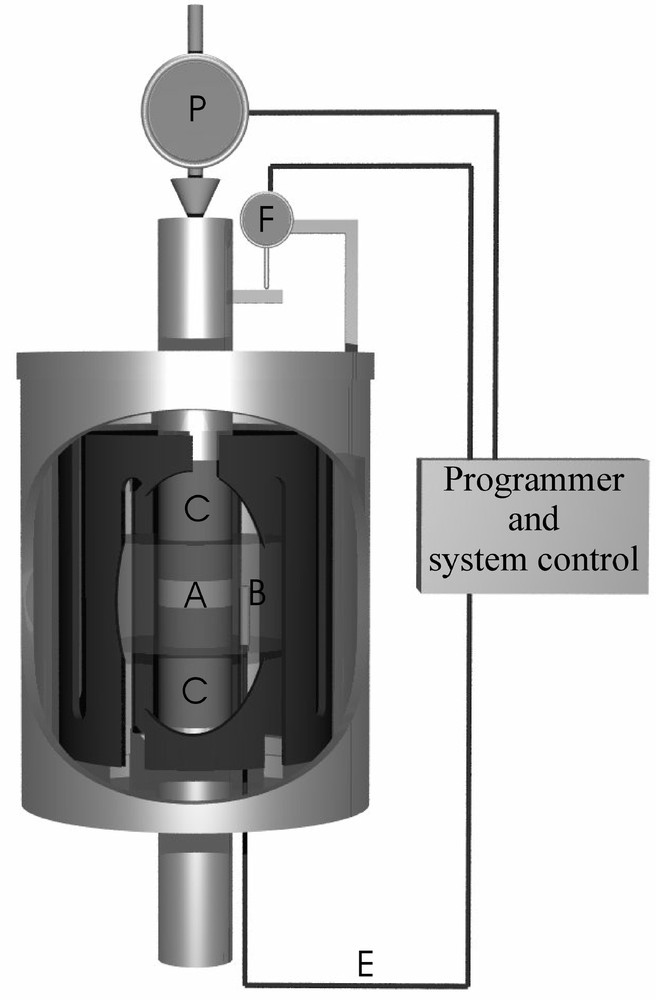
Hot pressing cell. A gel powder (A) placed in a die (B) is subjected to a pressure P using pistons (C). The thickness sample is recorded by a displacement sensor (F). The temperature increase is provided by a heating resistor (D) and recorded by a thermocouple (E).
5 From a monolithic dry gel to glass
Due to its high specific surface area a crack free xerogel should easily sinter and lead to a fully dense and monolithic glass by a simple heat treatment.
To avoid gel fracture occurring during drying, a detailed analysis of the mechanisms leading to the crack initiation has been performed. As previously mentioned, breakage of the gel originates from capillary forces which induce a stress gradient through the material. Such a gradient depends on the solvent evaporation rate, gel permeability, and gel geometrical dimension. Independently of the capillary stress, the probability of breakage can be reduced by increasing the mechanical strength of the solid network, by slowing down the drying rate, by increasing the gel permeability or by decreasing the viscosity of fluid flowing through the pores. Among these different ways, the method implying peculiar chemical compounds allowing one to slow down the drying rate seems to be the most efficient 〚18〛. However, the role of these chemical additives is quite complex, since it has been reported that they also modify the surface of the solid network 〚19〛.
As the time required to achieve drying is usually long, mobile chemical species that are not strongly linked to the surface can diffuse freely. This sometimes results in local concentration increase of these mobile elements. To avoid such a phenomenon, these species can be precipitated under the form of specific salts. This process has been applied to synthesise gels and consequently glasses showing graded properties such as gradient refractive index glasses 〚20, 21〛.
Another way to reduce the probability of fracture consists in decreasing the capillary stress. This effect can be obtained by enlarging the pore size. Unfortunately, this textural modification can further slow down the sintering kinetics.
The most efficient way to reduce capillary stresses is to directly act on the liquid–vapour surface energy γLV. Changing liquid–vapour interface to solid–vapour, then sublimating the solid, is known as the freeze drying technique. The first step consists in decreasing the temperature to convert liquid into solid. This transformation is quite rapid and occurs in a narrow temperature range. It induces a dimensional change that initiates cracks in the network. A few experiments have been performed using a glass forming liquid, in order to spread the liquid–solid transformation over a wider temperature range and to reduce the dimensional evolutions. Even in that case the gel network is often fractured. Changing the nature of the liquid or adding chemical compounds to reduce the surface energy has been also tried. Results are not very convincing. Fig. 5 summarises the different ways that can be followed to avoid the gel cracking during drying. Some modifications, supposed to favour monolithicity, have been shown to finally give an opposite result. For instance, the syneresis 〚1〛 induces shrinkage of the solid network still bathing in the liquid. As a consequence of shrinkage, the gel strengthens. However, the volume shrinkage leads also to a decrease of the pore size. During further drying process, this pore size decrease will result in an enhancement of capillary stresses and a lowering of the gel permeability and thus in a higher stress gradient. So syneresis acts in an opposite way to that anticipated.
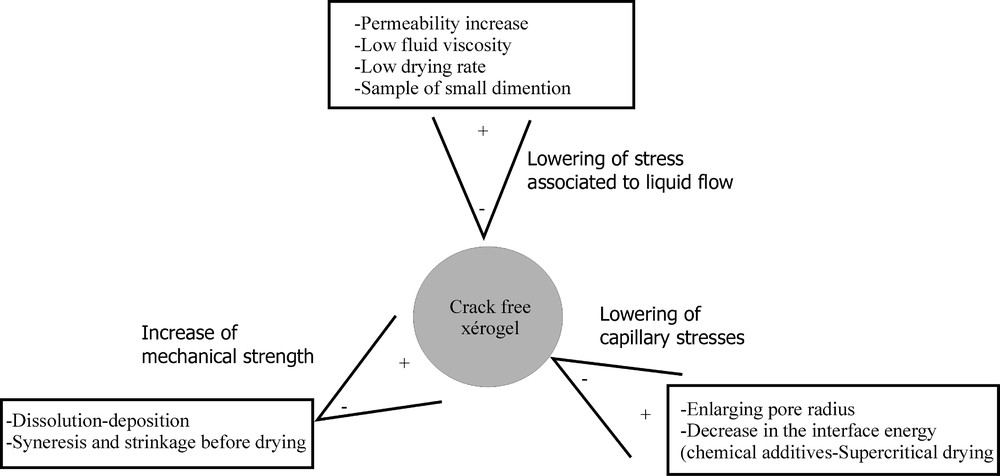
Ways to preserve the monolithicity of gels during drying.
An elegant method to eliminate capillary stresses is to provoke the vanishing of the liquid–vapour interface. The supercritical drying is based on the fact that, above the critical point, the liquid and the vapour are no more distinguishable and a single phase exists. There is no surface separation between the liquid and the vapour and consequently no surface energy 〚22〛. Details on the synthesis of monolithic silica aerogels have been reported 〚23〛.
During the supercritical drying (SD) treatment, the gel should not crack, since capillary forces are absent. However, a stress gradient can establish if the heating (first stage of SD) or depressurisation (last stage of SD) is too fast. This stress gradient is due to the low gel permeability. Gel can crack if the different stages of SD are not perfectly controlled and do not fit the gel dimensions 〚24〛.
Two kinds of liquids are particularly convenient to perform supercritical drying: alcohols having a low molecular weight and CO2. The critical temperature of CO2 is quite low (31.1 °C) and avoids chemical evolution of the gel structure. In the case of alcohols SD, an esterification reaction modifies the chemical nature of the gel surface. That feature leads to hydrophobic aerogels, a specific property of interest to conserve monolithic sample under atmospheric conditions. A hydrophilic aerogel adsorbs water molecules that condense within the smallest pores, inducing again capillary forces.
The conversion of silica aerogel to glass is achieved using a sintering treatment at temperature ranging between 1000 and 1100 °C for a short period of time. As temperature increases, the organic residues, providing the aerogels hydrophobicity, are oxidised to give rise to silanol groups. The final glass shows a strong IR absorption band located at 2.73 μm, assigned to OH vibration groups. High-water-containing glasses may bloat at high temperature where the viscosity is low 〚25〛. Thus gel dehydration using chloride or fluoride gases is often carried out before sintering. Resulting silica glass and binary oxide glasses prepared from this process exhibit excellent optical properties (Fig. 6). Multicomponent glasses, particularly those containing alkali or earth alkaline elements, are difficult to obtain. First of all, some of these elements, weakly linked to the silica network, are swept away by the supercritical fluid. On the other hand, at the onset of heating schedule required to sinter aerogel, chemical species such as alkali ions induce a crystallisation phenomenon.

Silica aerogel and resulting glass obtained after a sintering treatment of 30 min at 1000 °C.
6 Shaping the glass during gelling
In the course of hydrolysis and polycondensation reactions, the viscosity of the solution increases slowly as a function of time (Fig. 7). At a given time, the viscosity of the solution reaches a value (> 1 poiseuille), allowing fibre drawing. Consequently, fibres can be obtained directly from liquid solution around room temperature.

Viscosity change of a solution Si(OC2H5)/C2H5OH/H2O (42/42/16 volume percent) as a function of time measured from gelling time.
Gelling parameters can be optimised in order to increase the time duration where the viscosity of the solution allows one to draw fibre 〚26〛. The obtained fibre is usually densified by flash heating. Under controlled conditions, organic residues decompose and gaseous species are removed before closing the pore surface. Sometimes, this rapid heating leads to a change in geometrical shape and the resulting fibre is not perfectly cylindrical. Fibres issued from sol–gel are used as reinforcement in composites materials. Because of their poor optical properties, they cannot be used in photonic applications.
Sol–gel technique also allows preparation of thin solid coating. As for fibre drawing, the sol (liquid containing chemical species and leading to gel) is deposited on a substrate. Solvent evaporation results in an increase of the concentration of monomers, which become in contact and create the gel.
Different techniques allowing the formation of a thin and homogeneous layer can be found in the literature. The dip-coating process consists in dipping the substrate into liquid and drawing it at a constant rate. Lowering the liquid level (drain coating) obviously gives the same result. The film thickness increases with the withdrawal rate. Spin coating is a one-side deposition technique preferably devoted to substrates having a symmetry axis. It consists in deposing a drop of liquid on a rotated substrate. As rotation proceeds, the liquid spreads at the surface while the solvent evaporates. For a large and flat surface substrate having large size, the film deposit can also be performed using a wetted roller as shown in Fig. 8.
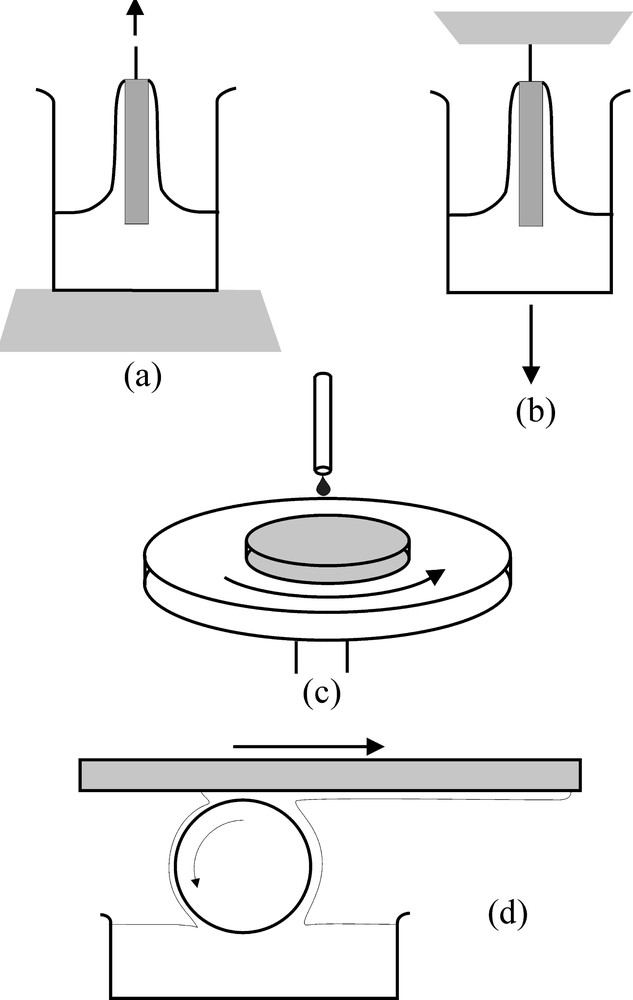
Preparation of thin layers deposited on substrates from liquid solutions: (a) dip-coating by substrate withdrawal, (b) dip-coating by lowering of the liquid vessel, (c) spinning, (d) roll coating.
Substrates of different nature (glass, silicon, plastics) can be covered with thin solid film issued from sol–gel techniques. However, after gelling, the film remains porous. The pore closure and the gel–glass transformation require a thermal sintering treatment. A significant effort has been devoted to thin solid films on glass substrate, in order to modify optical properties 〚27–30〛 (antireflective layer, coloured layer, hot and cold filters, planar optical guides, optical amplifier...) or to create additional properties (diffusion barrier, electrical conductivity...). If the substrate is a silicon wafer, the sol–gel layer can be easily thermally densified. Substrates made of organic compounds (PMMA, polycarbonate...) cannot withstand high temperatures and consequently a mineral thin film of gel cannot be converted into a fully dense material. New families of gels called hybrid gels have been proposed to overpass these difficulties. Densification is obtained by polymerising specific organic radicals linked to these new alkoxide precursors 〚31〛. These new precursors, both organic and mineral, extend the application field of thin films.
Scratch resistant layers deposited on organic substrate have been developed by means of hybrid alkoxides and nanocomposites 〚32〛.
Several investigations in the field of photochromic materials and in the field of planar waveguide for optical amplification or for wavelength multiplexing have been reported 〚33, 34〛.
Gelling process in the absence of water molecules has been published 〚35〛. This synthesis method should be interesting to enhance thin films optical properties by avoiding or at least reducing the OH group content.
7 Conclusion
The idea consisting in transforming amorphous but porous solid to get dense glass by a simple sintering treatment has proved to be efficient. Gels are now used in a lot of applications. Their homogeneity and their reactivity at low temperature have greatly contributed to their success. However, the cost and the organic nature of starting compounds can be considered as a drawback. Consequently, materials issued from gels concern mainly systems with very specific properties.
In this paper, we mainly focused on gels allowing glass synthesis. We must mention that they can also be used as obtained after a drying treatment for different applications as catalysts, thermal insulators, and low dielectric constant materials.
They have also been applied for the synthesis of fine ceramics.