1 Introduction
The synthesis of porous materials has attracted and still attracts intensive attention, and significant advances have been made with respect to structural, compositional and morphological control. These efforts are triggered by the wide range of interesting applications of porous solids as catalysts, adsorbents, sensors, in energy storage, and many others, in addition to the curiosity driven research which is focused on these materials due to the intellectual fascination which the structures create. Porous materials are normally classified into three types by pore diameter, i.e. microporous (below 2 nm), mesoporous (2–50 nm), and macroporous (exceeding 50 nm) [1]. Zeolites are the most extensively investigated class of microporous materials [2], and ordered mesoporous materials of the M41S family can be regarded as the most prominent class of mesoporous solids since their discovery in 1992 [3]. Numerous important developments were based on the initial discoveries, and several excellent reviews about synthesis, properties and applications of mesoporous materials are available [4–15]. Macroporous solids are a rather separate class of materials if they only possess macropores. However, they often exhibit hierachical pore systems, i.e. a combination of macropores with micropores and/or mesopores [16]. From a viewpoint of applications, for instance in catalysis, the active sites are often located in the micropores and mesopores, while the macropores favor mass transfer and reduce transport limitations.
The fabrication of porous materials, especially the creation of mesoporous materials, has been extensively investigated over the last years. Several novel strategies have been developed in the past decade, which are reflected in the numerous publications related to this area. Template methods [10], which imply a more or less direct replication of the pore system from the template, seem to be one of the most promising synthetic pathways to create porous materials, especially if materials with ordered porosity are the goal. The shape and size of the template in many cases is correlated to the resulting pore system. However, in some cases, especially for microporous materials, it is not easy to achieve a one-to-one replica due to the still low degree of understanding of the template function. This situation is quite different for ordered mesoporous materials synthesized via a liquid crystal templating pathway, or for colloidal crystals [17,18]. In these cases the synthesis indeed corresponds to a direct templating mechanism, where a relatively precise replica of the template is created. This replication process can be so perfect that one is tempted to use the term “nanocasting” to describe this process, which implies that the template is actually used as a true mold to produce the mesoporous materials with controllable pore size, pore morphology and distribution, properties and composition of the network as well as the desired macroscopic shape.
Two kinds of templates, defined as hard template and soft template, respectively, are usually available for nanocasting processes, and the structures and properties of the templates play a very important role with respect to the properties of the replicated porous materials. Nanocasting from soft templates was first developed, and organic precursor species, often polymers, which allow the formation of liquid crystals can be used as soft templates [8,19]. For clarity of terminology, one should keep in mind, that not all surfactant assisted synthesis pathways are nanocasting routes, since many syntheses rely on a cooperative assembly between surfactant and inorganic phase and do not replicate a preformed surfactant structure [4]. In any case, in casting processes on the macroscopic scale, the mold is normally rigid, i.e. made of wax, plaster, metal, or others. The nanoscale analogon of a real casting procedure thus also would need a hard mold, such as an inorganic solid. This was achieved with the use of siliceous mesoporous frameworks as a true mold to replicate other materials, such as carbon [20] or metal oxides [21,22], by which the pore structure of the parent can be transferred to the generated porous materials with various composition. Compared to a hard template, the soft templates do not really provide a rigid framework, but are rather nanoreactors. In these confined spaces the liquid phase structured by the surfactant is solidified by some chemical reaction, for instance a sol-gel reaction or a reductive coupling, thus leading to a mesostructured solid.
Nanocasting with soft templates suffers from some restrictions. Selection of the organic template and the inorganic precursor species has to consider their compatibility. Moreover, successful assembly of diverse inorganic precursors with the organic template usually requires very strictly controlled conditions, e.g. pH value, solvents, temperature and so on, which is often not easy to achieve and to control. As an alternative pathway which partially solves the above problems—but may create others—the hard template nanocasting has been developed recently [23], by which one employs inorganic porous materials as hard templates to cast the negative replica. In the following we will focus on some recent development in nanocasting with hard templates to produce porous materials and highlight some perspectives of this pathway.
The principle of the nanocasting pathway with hard template which involves three main steps is represented in Scheme 1: (i) formation of the template (ii) the casting step and (iii) removal of the template. Clearly, a three-dimensional pore network is necessary in the template to create a stable replica. Furthermore, after incipient wetness impregnation of the voids of the template with the precursors, the precursor should be easily converted to the desired composition with as little volume shrinkage as possible. In addition, the templates should be easily and completely removed to obtain the true replicas. In order to control the morphology and structural parameters of the replicas, the hard templates should have controllable morphology and structure. Based on these requirements for selecting hard templates to be used in nanocasting pathways, ordered mesoporous silica seems to be an ideal hard template, which can be used as a mold for other mesostructures with various compositions, such as polymer [18,24], ordered mesoporous carbon [20,25] and metal oxides [26,27]. Mesoporous silica with various different structures can be synthesized using surfactant based processes, and silica is relatively easily dissolved in HF or NaOH. Alternatively, mesoporous carbons with solid skeleton structure are also suitable choices as hard template due to the excellent structural stability on thermal treatment (at least in inert atmosphere) and the resistance to chemical attack. A pronounced advantage of carbon is the fact that it is much easier to remove than silica, namely by simple combustion. It must be pointed out here that the nanocasting will only be suitable for framework compositions which are stable under the conditions used to remove the mold, that is, stable in relatively concentrated NaOH or HF in the case of silica or at high temperature up to 500oC in oxidative environments, as in the case of carbon.
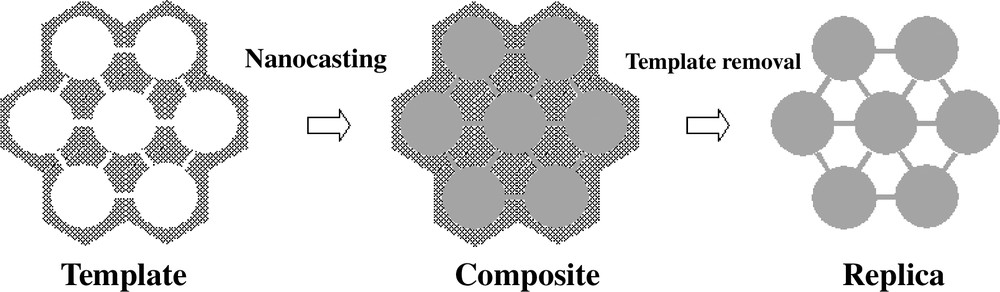
Illustration of the nanocasting pathway.
2 Porous silica as template
Of the many ordered mesoporous silicas reported so far, only materials with a three-dimensionally connected pore system, such as MCM-48 [20] or MSU-H [28] are suitable. SBA-15 [17] with its hexagonally packed unidimensional mesopore system would on first sight not be expected to be useful as hard template. However, micropores in the wall connect the unidimensional, hexagonally packed mesopores [29], thus providing the cross-linking necessary for obtaining a stable replica. Generally, to create the nanocast, an ordered mesoporous silica is impregnated with precursor(s) to give the desired composition. After the subsequent solidification of the precursor in the pore system and removal of the silica template by HF or NaOH leaching, a mesoporous structure with a new composition can be obtained. For more details, one can refer to the recent reviews by Ryoo et al. [6] and Lee et al. [13]. A convincing example is the synthesis of ordered mesoporous carbons (CMK family) pioneered by the group of Ryoo et al. [6]. They used the MCM-48 with cubic Ia3d structure as the template and sucrose as carbon precursor [20]. Furfuryl alcohol and resorcinol/formaldehyde also can be used as alternative carbon precursors [20]. After thermal treatment of the composite at 800–1100 °C in vacuum or inert gas, the carbon precursor is transformed into a pure carbon material. Subsequent removal of the silica mold gives an ordered mesoporous carbon, named CMK-1 with I41/32 or lower symmetry [20], or CMK-4 carbon with cubic Ia3d symmetry when partially disordered MCM-48 silica was used as template [30]. Interestingly, the same group subsequently found that SBA-15 with hexagonally ordered cylindrical channel structure can also be nanocasted to create a carbon-copy, named CMK-3 [31]. This work incidentally proved that the mesopores in SBA-15 are most probably interconnected through the walls via micropores because otherwise the stability of the carbon replica could not be explained.
These carbon materials show remarkable structural and textural properties. The replica of the original structure is surprisingly closely related to the original material, as observed both on the nanometer scale and on the micrometer scale, and correspondingly both on the level of the pore system and the whole particle (see Fig. 1). The values of the specific textural parameters exceed those for the silica molds used in their synthesis because of the very low density of a carbon framework and the additionally formed porosity in the framework during the carbonization step. BET surface areas up to 1800 m2 g–1 and pore volumes up to 1.3 ml g–1 have been achieved for these materials. Compared to other mesoporous silicas, SBA-15 can be synthesized with adjustable pore size and pore wall thickness over relatively wide ranges, which further provides an opportunity to fine-tune the pore diameter of the replicated mesoporous carbon [17,20]. However, the size of the pore is predominantly governed by the silica wall thickness, because the pores of the carbon replica are formed by dissolution of the silica framework [32,33].
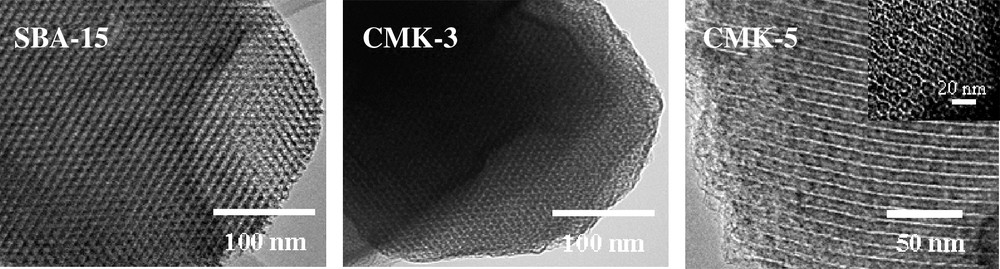
TEM images of SBA-15 and its replica CMK-3 and CMK-5.
CMK-3 mesoporous carbon inherits the hexagonal structure of SBA-15 due to completely filling of the mesopores of the SBA-15 by the carbon precursor, a process labeled volume templating in the case of colloidal crystals [34]. If the pore system of the SBA-15 is only coated by the carbon precursor instead of completely filling it, a surface-templated mesoporous carbon, named CMK-5, with an array of hollow carbon tubes is obtained [23,32,33,35,36]. A TEM image of CMK-5 is presented in Fig. 1. The removal of the silica mold then results in two different types of pores in the CMK-5 matrix. One type of pores is generated in the inner part of the channels which are not filled with carbon precursor. The other type of pores is obtained after silica removal in the spaces where the silica walls of the SBA-15 template had previously been. Since there are two different mechanisms for the pore generation, it should be possible to control the properties of such two pore systems independently. Moreover, due to the fact that the tubular structure exhibits two external surfaces, CMK-5 can reach very high surface areas and large pore volumes, which gives this material a high potential in adsorption and as catalyst support. A first example has been given in the initial publication on CMK-5 where it had been used as support for the anode catalyst in a PEM fuel cell [23].
In our studies to explore the synthesis of CMK-5, we found that SBA-15 can directly be used as template, instead of using aluminum impregnated SBA-15. Furfuryl alcohol is used as a carbon source and oxalic acid as the catalyst in this process. The time-consuming impregnation step of SBA-15 with aluminum which creates the acid sites necessary for polymerization of furfuryl alcohol could thus be avoided. Also the carbonization under argon instead of vacuum is an interesting alternative for the synthesis of CMK-5 type carbons. Both the external and internal diameter of the carbon tubes in the CMK-5 structure can be tuned by adjusting the concentrations of the furfuryl alcohol solutions diluted in trimethylbenzene. As seen in Fig. 1, the TEM image of CMK-5 carbon prepared following this simplified pathway is quite similar to the previously published images [32,33]. Therefore, a facilitated synthesis of CMK-5 carbon is possible compared to previous reports [36].
The pore sizes of carbons from the CMK-series reported so far are below about 4.0 nm. We therefore started investigations with the aim to create mesostructured carbons with larger pore diameter. This lead to the synthesis of nanocast carbon No. 1 (NCC-1), which consists of connected nanotubes, which are hexagonally ordered, and has high-pore-volume and bimodal pore size distribution [37]. Different to the template for the synthesis of CMK-5, here SBA-15 aged at 140 °C for 3 days was used as template. For synthesis of NCC-1, both SBA-15 and aluminum loaded SBA-15 can be employed. The TEM image shows that two pore systems of NCC-1 can be clearly identified (Fig. 2). The isotherms of such carbons have a pronounced double hysteresis loop, as seen in Fig. 2. This demonstrates the existence of the bimodal pore system, with the step at lower relative pressure corresponding to the pores left by the silica template and the step at higher pressure to the pores in the inner part of the nanotubes. The pore diameter in NCC-1 can be adjusted by choosing different concentrations of furfuryl alcohol for loading of SBA-15 or changing the conditions of the hydrothermal treatment. If higher concentrations of furfuryl alcohol are used, the second loop essentially disappears. This could be due to the high carbon loading, resulting in a complete blockage of the mesopores in SBA-15, or to the sizes of inter- and intratube pores approaching each other, so that the two steps coalesce. This pathway allows a flexible tailoring of pore size over wide ranges with the possibility to create independent systems.
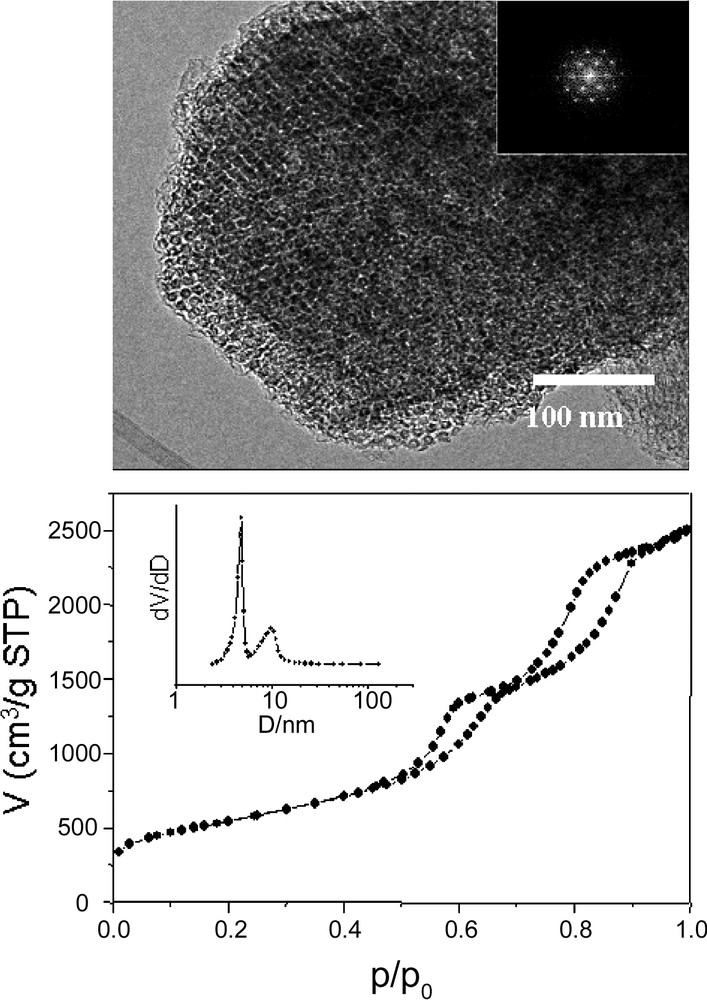
TEM image and nitrogen sorption isotherm (insert is the pore size distribution) of NCC-1.
By now, also other structures than the ones initially used have been replicated. Large pore ordered silica, KIT-6, with cubic Ia3d symmetry was synthesized in a triblock copolymer-butanol mixture [38]. The pore size of this material can be easily tuned from 4 to 12 nm via hydrothermal treatment. Using this silica as hard template, rod-like or tube-like mesoporous carbons, maintaining the same symmetry Ia3d as the parent silica, were synthesized, depending on the carbon precursors [38]. This is in contrast to the carbon synthesized using MCM-48 as template [20,30] where typically the symmetry is reduced upon replication, see above. When sucrose was used as carbon precursor, rod-like mesoporous carbon named as CMK-8 was generated, which was faithful negative replica of the parent silica KIT-6. On the other hand, using furfuryl alcohol as carbon precursor, tube-like mesoporous carbon named as CMK-9 was afforded. The faithful replica of KIT-6 was attributed to the presence of pores connecting the two independent channel systems and thus preventing shifting of the two carbon networks generated with respect to each other, which would reduce the symmetry.
From the viewpoint of the practical application, monolithic carbons are easier to handle than the powdered ones. The nanocasting pathway provides an opportunity to create carbon monoliths directly from silica monoliths. Related to the synthesis proposed by Nakanishi [39], silica monoliths with hierarchical structure can be prepared by addition of poly (ethylene glycol) and/or hexadecyltrimethylammonium bromide (CTAB) as porogen [40]. An interconnected macroporosity is induced by spinodal decomposition in a gelling silica sol in the presence of the PEG, while the mesopores originate from voids in between the silica particles forming the gel. Such silica monoliths containing a three-modal porosity were used as the host matrix and furfuryl alcohol, diluted in TMB, as carbon precursor was introduced in the pore system of the silica monoliths by one-step impregnation. Oxalic acid was added to this solution as a polymerization catalyst for furfuryl alcohol [41,42]. The polymerization of the furfuryl alcohol occurred in the mesopores of the silica monolith which had been templated by the surfactant, while the polymerization degree in the macropores remained low. The portion of the furfuryl alcohol present in the macropores evaporated during carbonization, resulting in a positive replica of the silica monolith on the micrometer scale and a negative replica on the nanometer scale, as shown in Fig. 3. The nanocasted carbon monoliths exhibit a three or four-modal porosity [42]. Combined volume and surface templating, together with controlled synthesis of the starting silica monoliths used as the scaffold, enables a flexible means of pore size control on several length scales simultaneously.
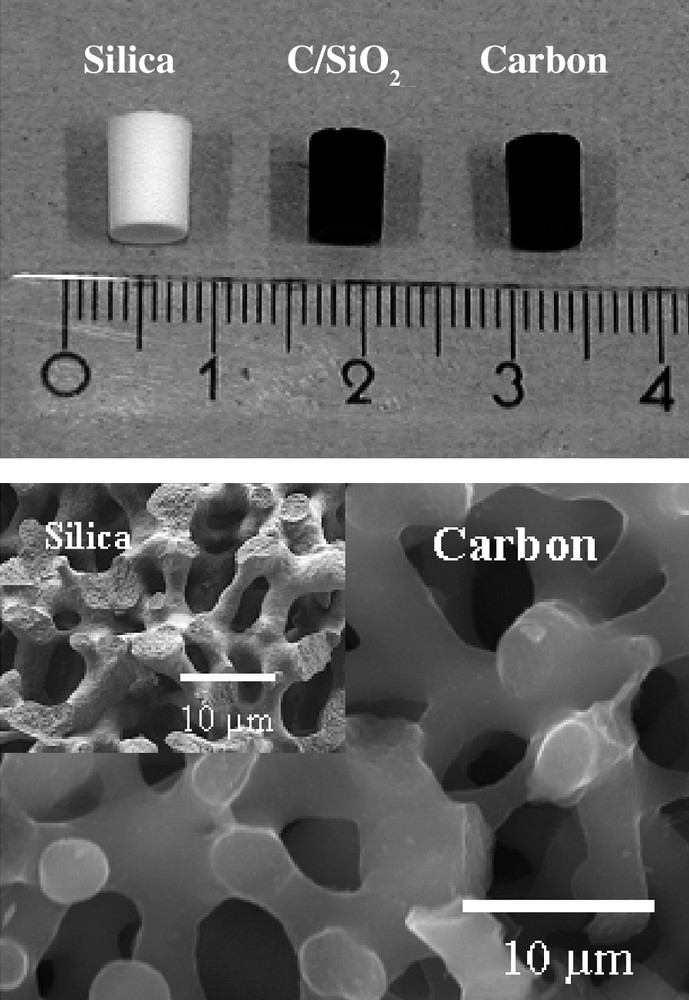
Representative photograph of silica, silica-carbon composite, and carbon monolith after leaching of silica. Top figure: scale in centimeters.
More recently, OMC with other frameworks, i.e. nitrogen-containing and graphitic skeletons, have been achieved [43–45]. One attractive target in the synthesis of ordered mesoporous carbon is the introduction of functional groups into the frameworks. Analogous to the synthesis of CMK-3, ordered mesoporous carbons (OMC) containing nitrogen groups have been synthesized, using mesoporous silica SBA-15 as template, polyacrylonitrile (PAN) as carbon source and 2,2′-azobisisobutyronitrile as initiator [43]. A series of procedures, i.e. stabilization, carbonization and removal of the silica template, leads to the formation of PAN-based OMC. By changing the stabilization temperature and carbonization temperature, PAN-based OMC with either monomodal or bimodal pore size distributions can be prepared. In the case of PAN-based OMC with bimodal pore size distribution, the connectivity between the adjacent pores was improved due to the randomly distributed, incompletely coated pore walls. By combining the pore connectivity and the surface functionality, such PAN-based OMC could become promising materials for the use as adsorbent and catalyst. An alternative access to nitrogen containing carbons is provided by using pyrrole vapor as precursor. Since the polymerization proceeds oxidatively, the loading with polypyrrole can be rationally determined by controlling the amount of pre-impregnated Fe(III) species, which act as oxidant to induce the formation of radical cations (C4NH5+•). Two of these radical cations couple to a dimer with deprotonation, thus forming a bipyrrole. After deprotonation, the bipyrrole is reoxidized and couples with another radical cation. By a sequence of such steps the polypyrrole chain grows [44].
Ordered porous carbons are excellent candidate materials for electrodes due to their thermal stability, corrosion resistance, and high electronic conductivity (especially for carbon with a graphitic skeleton). Ryoo’s group has synthesized porous carbon with graphitic framework structures through in situ conversion of aromatic compound – acenaphthene – to mesophase pitch inside the silica templates [45]. This synthesis required the silica template to be pretreated with AlCl3 in order to initiate the polymerization of the aromatic compound. Silica template and carbon source were sealed into an autoclave, and thermally treated to 750 °C for carbonization of the mesophase pitch in the template. The complete carbonization of the carbon source was achieved after the composite was cooled down and then further treated at 900 °C under vacuum in a fused-quartz reactor. The graphitic ordered porous carbon was then recovered by the removal of the silica template using an aqueous solution of HF or NaOH. Later on, Pinnavaia’s group also achieved the synthesis of a CMK-3 type carbon with graphitic walls. In this synthesis, carbon precursors were infiltrated into MSU-H silica via either wet impregnation for the carbon precursors such as naphthalene, anthracene or pyrene, or chemical vapor deposition for benzene. Slightly deviating from Ryoo’s procedure, the reaction was performed without autoclaving, and the silica template was used without pretreatment. MSU-H silica impregnated with the carbon precursor was heated at 160 °C in a covered vial to initiate the carbonization. This step was repeated until the desired amount of carbon precursor was infiltrated. Then the composite was heated up to the final temperature to obtain the carbon silica composite. After removal of the silica template, a pure carbon replica was obtained, which shows high electronic conductivity compared to normal CMK-3 carbon with amorphous characteristic [46].
As we discussed in the introduction part, metal oxides synthesized using surfactant as template often lose the ordered structure after removal of the template. Using mesoporous silica as hard template to achieve ordered metal oxides is alternative way and a very interesting topic both for fundamental research and practical applications. For instance, using aminopropyltriethoxysilane functionalized SBA-15 as template, and H2Cr2O7 as chromium precursor, 3-D porous chromium oxide single crystals were prepared via chemical adsorption of chromium precursor, thermal treatment and template removal by aqueous HF solution [47]. In this synthesis, calcination temperatures higher than 350 °C were needed in order to create the crystalline phase. This material is believed to have potential as catalyst with a high activity due to its large surface area (58 m2 g–1) and possible shape selective properties. Zhao and co-works have demonstrated recently that microwave digested 3-D mesoporous silica can be used as hard template and hydrated metal nitrates as source to fabricate various ordered crystalline gyroidal metal oxides [48,49]. These mesostructured metal oxides, Co3O4, Mn2O3, CeO2 and In2O3, have been prepared via impregnation and thermolysis procedures. These ordered metal oxide have large surface areas of 50–140 m2 g–1 and exhibit single crystallinity in domains. Recently, in our group nanocasted ordered mesoporous Co3O4 with the spinel structure on the atomic scale was synthesized. Vinyl-functionalized large pore Ia3d silica was used as template and Co(NO3)2 as cobalt precursor. Following impregnation, drying and calcination at 450 °C, the silica template was removed with NaOH aqueous solution [50]. The material is antiferromagnetic and shows a weak ferromagnetic transition at low temperatures. It is believed that the vinyl groups in the silica play an important role for bonding of the Co2+ in the pores. This process seems to be extendable to other metal oxides and has recently been used to produce ordered mesoporous ferromagnetic CoFe2O4.
3 Porous carbon as template
Mesoporous silica can be used as a suitable template to synthesize porous carbon and other materials. Presumably, this pathway could be reversed to structure porous silica or other inorganic solids with a mesoporous carbon template. That would possibly break through some of the restrictions of porous silica as mold. In many cases, silica is unsuitable to synthesize framework compositions other than carbon, since the leaching of the silica typically affects the material which is filled into the silica pore system. Furthermore, removal of the carbon template is easily performed by simple combustion or other techniques such as high-temperature hydrogenation [10,51]. Disordered porous carbon has been used as a template for the synthesis of high surface inorganic material, such as porous oxide or zeolite [52,53]. Activated carbons or carbon aerogels were used in these cases. The direct impregnation of activated carbons with concentrated aqueous metal nitrate solution and subsequent removal of the carbon templates by combustion lead to the formation of porous metal-oxides and even more complex oxides, such as spinels [52]. Recently, mesoporous carbon aerogels were also used as template to synthesize ZSM-5 monoliths with uniform mesoporous channels [53]. We have explored the preparation of mesoporous alumina using carbon aerogel as template and aluminum nitrate as alumina precursor [54]. The generated alumina consists of small transparent granules with 3–6 mm in size and has inherited the three-dimensional network structure of the carbon aerogel template (Fig. 4). The mesopore surface area of the alumina can be as high as 365 m2 g–1, and the pore volume reaches 1.55 cm3 g–1 after calcination at 600 °C for 8 h in air. XRD measurements confirmed an amorphous phase of alumina even at 700 °C. The pore parameters can be varied in a certain range by variation of the carbon aerogel template and the loading amount of the alumina precursor. At high loading, interestingly, the obtained glassy alumina clearly shows a bimodal pore size distribution in the mesopore range, as shown in Fig. 4. The templating action of the carbon aerogels can be traced back to their unique properties, including the three dimensional connectivity of the pore system, the high pore volume and the narrow pore size distribution. In addition, the purity is much higher compared to activated carbon. However, the disordered pore structure characteristics in activated carbons and carbon aerogels are not ideal for a nanocasting process, since for such materials the loading is often inhomogeneous, which results in an unavoidable partial disruption of the material upon template removal, and corresponding loss of surface area and porosity [54]. In addition, it is much more difficult to prove that a true nanocasting is operative with hard templates having a disordered pore system.
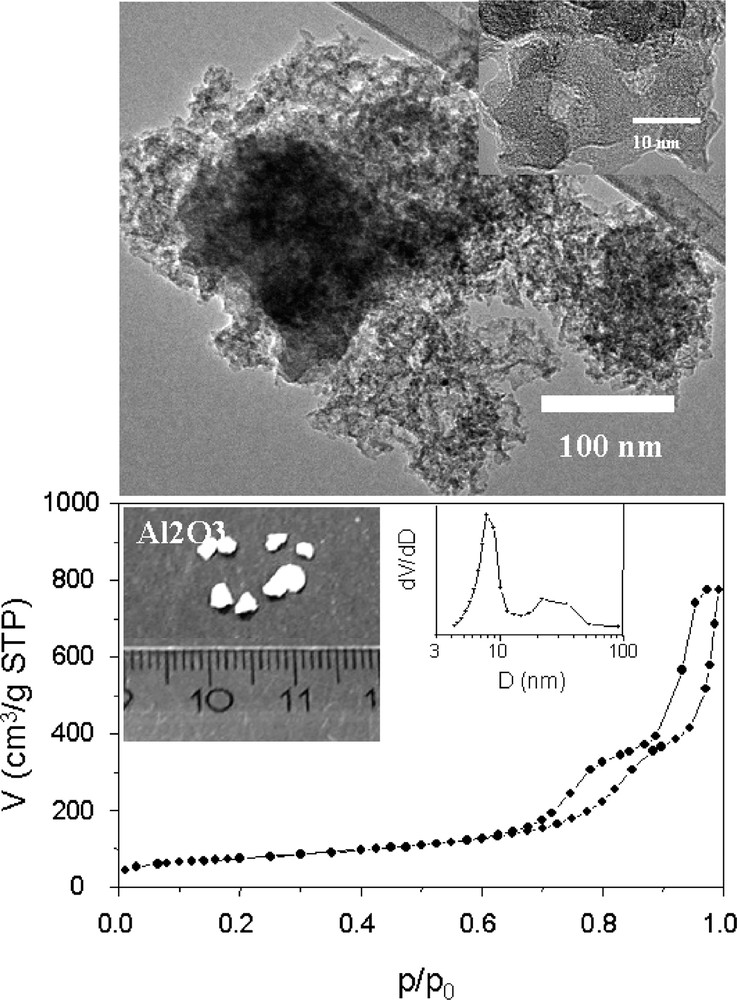
TEM image, photograph, and nitrogen sorption isotherm (insert is the pore size distribution) of glassy mesoporous alumina nanocasted from carbon aerogel. Back figure: scale in centimeters.
In principle, ordered mesoporous carbon, CMK-3, could be used as a template to construct other compositions with ordered mesoporous structure. Two independent groups, including us, almost simultaneously confirmed the possibility of this principle [51,55,56]. Tetraethoxysilane (TEOS) as silica source can be conveniently infiltrated into the pore system of CMK carbon, and hydrolysis can be initiated by treatment with HCl solution. A repeated impregnation procedure is necessary in order to achieve the desired loading. After inducing silanol condensation to an as complete as possible extent by thermal treatment at 700 °C under nitrogen flow, the composites are calcined at 550 °C to produce a white powder, designated as NCS-1 for nanocast silica No. 1. Alternatively, the carbon can be removed in a fluidized bed reactor in flowing air to avoid temperature hot spots which could damage the ordered structure of the obtained silica. This procedure results in enhanced adsorbed volume in nitrogen sorption experiments. XRD and TEM measurements confirmed that NCS-1 has hexagonally ordered cylindrical channels (here only the TEM image is shown in Fig. 5). The resemblance of the NCS-1 with the SBA-15 structure and morphology is obvious (Figs. 1 and 5), although small deviations in textural properties exist between the original SBA-15 and the NCS-1 obtained by repeated nanocasting. This nanocasting of silica from CMK-3 type carbon demonstrates the possibility of the true positive replication of the original SBA-15. Although this brings one back almost to the starting point, that is, a mesoporous silica, nanocasting of silica from CMK-3 can be considered as a feasibility study, since it essentially demonstrates the principle possibility to use ordered porous carbon to template other composition with ordered structure. In addition, the textural properties of the NCS-1 are not completely identical to the SBA-15, so that some fine tuning is possible via this pathway.
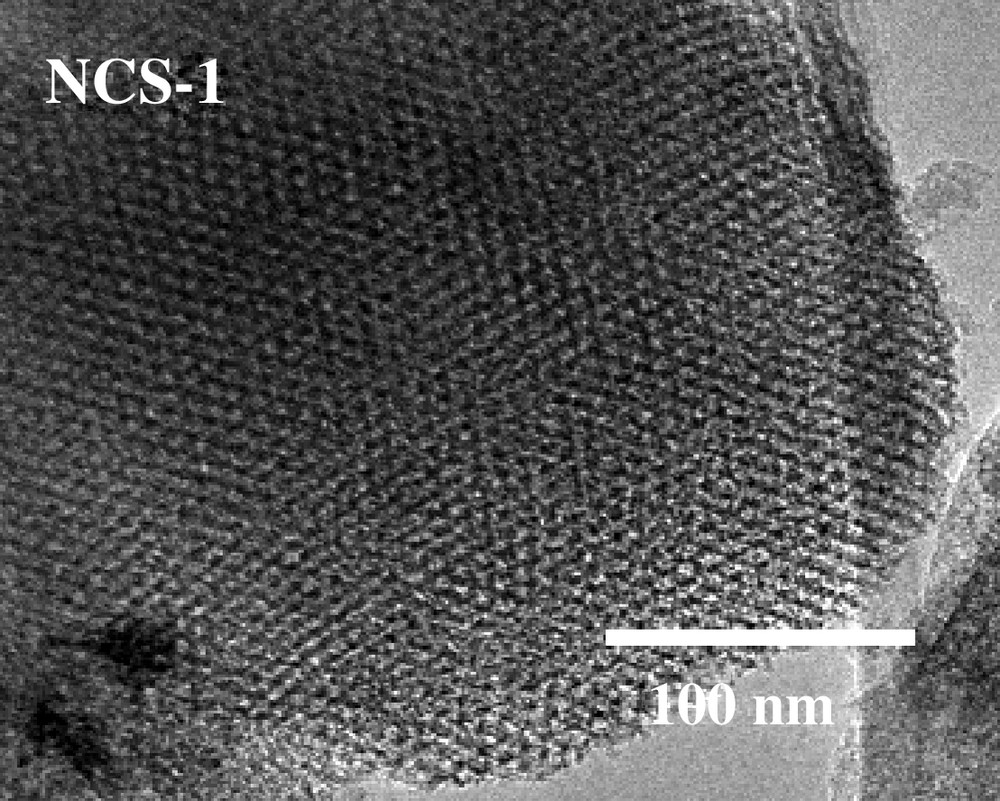
TEM image of nanocast silica NCS-1.
To obtain well-ordered porous products by nanocasting, two requirements should be satisfied for the precursor of the expected composition. (i) The precursor should have a high solubility in a suitable solvent or should exist in liquid state to maximize the loading amount and produce a sufficiently rigid skeleton in the calcined solid to avoid collapse. (ii) The resulting material should have a melting point higher than the temperature at which the carbon templates are combusted. Silica has an excellent thermal stability, and TEOS as silica precursor allows a high filling degree of the pore system of the porous carbon. In addition, the moderate hydrolysis rate helps to avoid a too rapid and vigorous reaction. Alternatively, an aqueous Na2SiO3 solution can be used as silica precursor [55]. However, in principle, it is possible to template many different inorganic frameworks other than silica by ordered carbon. It should be possible to use also other carbon template structures, such as CMK-1 [20] or CMSU-H [28] under properly chosen conditions with adopted precursors.
More recently, analogous to the synthesis of NCS-1, Roggenbuck and Tiemann [57] has succeeded in the synthesis of magnesium oxide with hexagonal p6mm symmetry via a nanocasting pathway using CMK-3 carbon as template. This is the first report on an ordered porous metal oxide with intrinsic basicity other than NCS-1. We attempted to use CMK-3 as template to synthesize mesoporous alumina. However, such alumina cannot maintain the ordered structure as the case in NCS-1 even though mesoporous alumina can be achieved [58]. This is mainly due to the complicated phase transition of alumina during a calcination process. More recently, porous metal oxides, such as Al2O3, TiO2, ZrO2, V2O5, etc., with high thermal stabilities as well as crystalline frameworks were prepared via the above nanocasting technique [59]. However, the obtained metal oxides cannot maintain the original ordered structure as the template has. Currently, the synthesis of novel ordered metal oxides is still ongoing in our group using ordered carbon templates.
4 Nanocasting pathway to create functionalized porous solids
As discussed above, many new materials have been created by the nanocasting strategy and removal of the template leads to the negative replica of the primary template. Meanwhile, the nanocasting pathway also essentially provides a possibility to functionalize the inner or outer surface of porous materials to satisfy the demands of a desired practical application. Ryoo’s group has confirmed that the surface of ordered nanoporous carbon (CMK-3) can be nanocast by an organic polymer, for example polystyrene [60]. The resultant materials, exhibiting surface properties of the polymers, as well as the electric conductivity of the carbon framework, could provide new possibilities for advanced applications. Such a strategy, furthermore, might be extended to other inorganic templates, such as mesoporous silicas.
Most of the as-made porous carbon materials have particle sizes in the submicron range. Therefore, they exhibit high adsorption–desorption rates due to the fact that their pores directly open to the particle surface. However, these carbons are notoriously difficult to separate from solutions, and thus magnetic separation is an attractive alternative to filtration or centrifugation and therefore high on the wish-list in catalysis for a long time [61]. Introduction of ferromagnetism in carbon particles while retaining their pore system is difficult, though: the commonly employed strategy to synthesize magnetic carbon materials is the condensation of divalent and trivalent iron salts in an activated carbon slurry in the presence of hydroxide with subsequent calcination [62]. Magnetic silica gel can be synthesized by entrapment of magnetite particles in the forming gel [63]. Such synthesis procedures, however, lead to substantial blocking of the pore space, while the pore size distribution of the carbons is inherently broad. In addition, the materials are not stable against corrosive media and high temperature, which lead to dissolution of the magnetic component and coalescence of the particles, respectively, thus sacrificing most of the advantages of the porous carbon. In order to overcome these limitations, we investigated the possibility of a combination of nanocasting, spatially selective deposition of magnetic nanoparticles, and protection of the nanoparticles by a nanometer thick carbon layer to nanoengineer a magnetically separable ordered mesoporous carbon. The overall synthetic strategy is shown in Scheme 2, which includes (i) the use of the mesostructured SBA-15 as template to synthesize a carbon/SBA-15 composite, (ii) deposition of cobalt nanoparticles [64] selectively on the outer surface of the composite particle, (iii) protection of the cobalt particles by a nanometer thick carbon layer, (iv) removal of the silica scaffold by hydrofluoric acid (HF) aqueous solution. After a sequence of well-designed manipulation steps, ordered mesoporous carbons with surface grafted magnetic particles was successfully synthesized [65], of which a typical TEM image is presented in Fig. 6. Such magnetic nanocomposites have very high surface area, a large pore volume, and uniform pore size. Applications of this porous carbon as magnetically separable adsorbent and catalyst have been demonstrated. However, one may envisage also other applications, such as, for instance, magnetically directable drug carrier. If a drug was loaded onto the porous carbon, one could possibly accumulate the magnetic particles in the target area in the organism, and then induce release of the drug by magnetic heating (in an alternating magnetic field) of the particles [66]. Experiments in progress will show whether such applications can be realized.
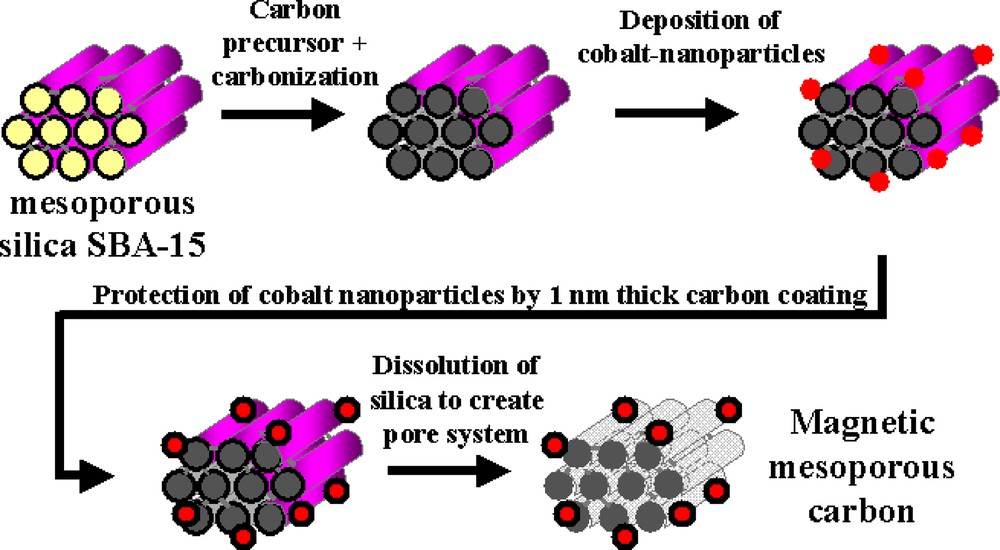
Illustration of the synthesis pathway of magnetic mesoporous carbon.
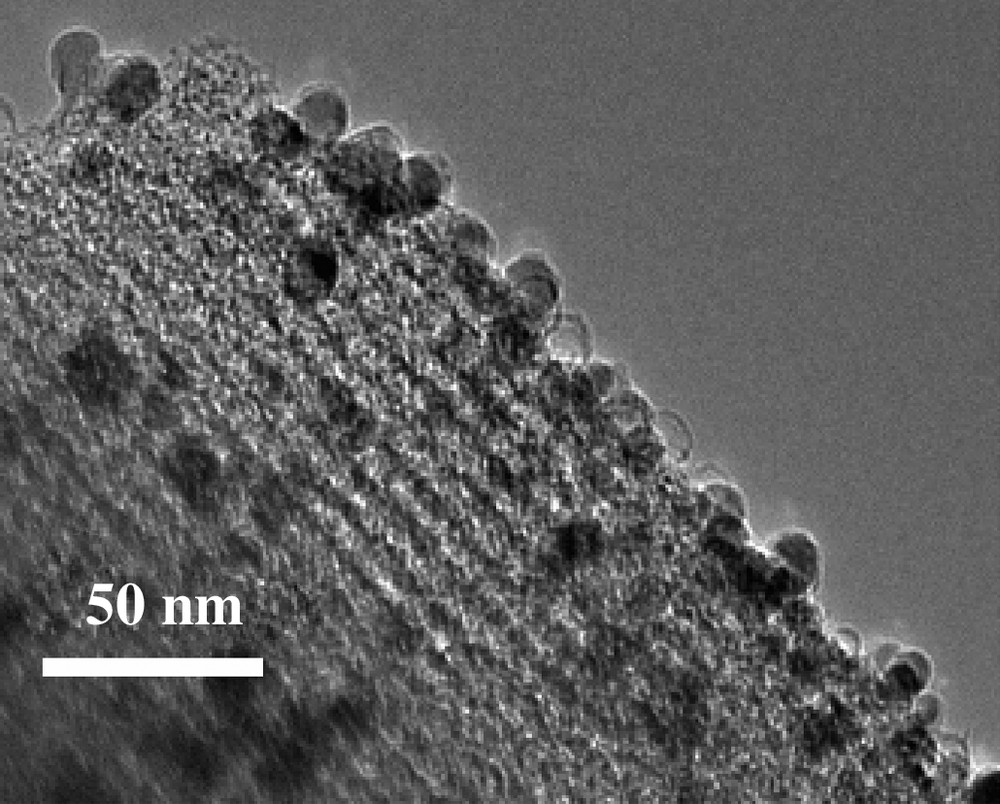
TEM image of magnetic mesoporous carbon with surface grafted cobalt nanoparticles. Acid treatment leads to the formation of some empty hollow carbon shells.
It would also be attractive to synthesize magnetic ordered mesoporous silica. Related to preparation of the magnetic carbon, we attempt to functionalize the mesoporous silica with magnetic anchors, while simultaneously keeping the pore system open. To achieve that, a strategy of reversible polymer protection of the silica pore system was developed [67]. As an example, SBA-15 was selected as a mold system. First, the pores of SBA-15 were filled with a thermally decomposable polymer (PMMA) in order to prevent incorporation of the cobalt nanoparticles in the pore system. This approach is to some extent related to protection group strategies in organic synthesis, with the difference that not parts of a molecule are temporarily passivated but certain regions in a solid material. Subsequently, the cobalt nanoparticles suspended in toluene were deposited on the outer surface of SBA-15 via a wet impregnation method. After a drying stage to remove the toluene, the composite was wetted with furfuryl alcohol (FA) solution containing also oxalic acid to initiate polymerization of the FA. Afterwards, the composite was treated at 80 °C and then at 850 °C under argon in order to convert the FA into a thin carbon coating on the surface of the cobalt nanoparticles. Simultaneously with the heat treatment to carbonize the poly-FA, the PMMA in the pores of the SBA-15 was decomposed to restore the accessible pore system. The acid resistance of such magnetic SBA-15 was test in 0.1 M aqueous HCl solution at room temperature for 10 days. After the acid treatment, the magnetic SBA-15 was examined by high resolution TEM. As shown in Fig. 7, it can be clearly seen that cobalt nanoparticles were deposited on the outer surfaces of the silica particles (Fig. 7a), as well as the open ends of the mesopores (Fig. 7a, insert). On the other hand, empty carbon shells were also observed due to the dissolution of those cobalt nanoparticles which were not fully protected by the carbon coating (Fig. 7b).

TEM images of magnetic mesoporous silica after acid treatment.
In summary, magnetic carbon and silica can be fabricated with magnetic anchors grafted to the outer surface while maintaining an open pore systems. This strategy, however, only serves to illustrate a more general possibility. Reversible protection and reopening of the pore system of porous solids allows to deposit functional sites in such materials in a spatially selective manner.
5 Conclusions and outlook
The nanocasting pathway, especially using hard templates, to create porous materials has been reviewed briefly. Using this approach, one can create negative – or, after repeated nanocasting, positive – replicas which can preserve fine structural details of template. It has been demonstrated in principle that this technique allows the generation of porous material on the nanometer scale with partly variable textural parameters. The samples are produced as monoliths or powder with ordered or disordered structures, which mainly depend on the structures of primary templates. The range of the templates applied in nanocasting already extends from silica to carbon, which is easily removed by simple combustion.
The systematic exploration of the nanocasting pathway will add a new dimension in the fabrication of many porous inorganic materials with different hard templates. Generally, today the strategies for the synthesis of the porous inorganic materials are concentrated on surfactant-assisted methods, which often pose more complex problems than nanocasting, as attempts to remove the surfactant often result in structural collapse of the desired porous solid. Furthermore, mostly expensive alkoxides are used as raw materials, and the hydrolysis rate of such alkoxides is not easy to control. Carbon as template makes it possible to use inorganic concentrated salt solution, such as metal nitrate and acetate, instead of alkoxides as precursors to replicate porous metal oxides, etc. However, one still has to synthesize the ordered mesoporous mold in a first synthetic step, which is a major drawback in the nanocasting pathways.
The remaining challenge is how to increase loading as much as possible to ensure a rigid structure, thus avoiding collapse of the pore system after removal of the mold. Basically, a very high concentration of the precursor solution, if at all possible, the neat precursor, is highly recommended. Although the replication of non-silica materials seems to be not as straightforward as for silica, it can be foreseen that these obstacles could be overcome in the coming years by continuing research efforts in this rapidly developing field. It is almost certain, that the nanocasting pathway will be extended to many other compositions which are not accessible by solution based methods.
Acknowledgements
A.-H. Lu, acknowledges the Alexander von Humboldt Foundation for a scholarship. The authors would like to thank the Leibniz-Program and the FCI for support in addition to the basic funding provided by the Institute.