1 Introduction
Agricultural activities generate important quantities of biomass resources and a suitable recovery strategy should be implemented to reduce their environmental impacts [1]. Among the various techniques for biomass valorization, its use as a feedstock for energy production is one of the most effective solutions for global problems such as the increase of energy demand and price, the depletion of fossil fuels and the increase of greenhouse gas emissions [2]. Biomass can be converted to various forms of energy through numerous thermochemical conversion processes namely, pyrolysis, gasification and combustion. Over the past few years, the development of products from biomass through the pyrolysis technique has been intensively investigated. Pyrolysis is thought to be more favorable for converting biomass into mainly valuable liquid hydrocarbons [3]. Fast pyrolysis is a process in which organic materials are rapidly heated at 450–600 °C in the absence of air. Under these conditions, vapours, permanent gases and charcoal are produced. The vapours are condensed leading to the formation of pyrolytic oil. The percentage of the pyrolytic oil depends strongly on the operating conditions but typically 60 wt% of the feedstock could be converted into pyrolysis oil. Fast pyrolysis transforms difficult-to-handle biomass of different nature into a clean and uniform liquid. Furthermore, the pyrolysis of biomass also produces gas and char as byproducts that could be used as energy sources in pyrolysis plants. The obtained pyrolytic oil (or bio-oil) is a liquid of high density and moderate heating value that can be upgraded in a biorefinery to gasoline and diesel blendstocks.
Biomass (agricultural residues, forestry products and city waste) can be used for energy production in several ways from old direct burning to modern gasification and fast pyrolysis [2]. A large number of feedstocks, such as wood, rice husk, bagasse, sludge, tobacco, tire shredder waste, and palm-oil residues, can be processed in the fast pyrolysis process. Among the abundant biomass sources in Tunisia, agricultural residues have huge bioenergy potential. This biomass includes a large amount of date palm residues, almond shells, vine plants, and olive residues [4–8]. Hence, the use of these residues as alternative sources of energy is a promising method. Several attempts have been performed to evaluate the potential of Tunisian agriculture residues through various thermochemical conversions. Jeguirim et al. have characterized four Tunisian biomass species: industrial by-product (Pine Sawdust), agro-industrial by-product (Olive Solid Waste), agricultural residue (Date Palm Trunk) and seaweed (Posidonia Oceanica) to assess their eventual utilization for energy recovery [9]. El May et al. have examined the combustion performance and the gaseous emissions of date stones in domestic pellet boilers [10]. Recently, several researchers have produced different agropellets from olive mill residues. The performance of these pellets was evaluated during combustion tests in household boilers [11,12]. These previous investigations have shown promising results for the combustion of Tunisian biomasses which could be useful as energy sources. However, several improvements are required to adapt the domestic boilers to these residues in order to increase the boiler efficiency and to decrease the gaseous and particulate emissions [10–12]. In addition, other thermochemical conversion processes such as gasification and pyrolysis should be examined. Due to the lack of experimental investigations on the pyrolysis and gasification, modeling and simulation could help strongly the development of these processes. Several models have been developed and applied to biomass pyrolysis. Usually, the influence of parameters such as size, shape, moisture, reaction mechanisms, heat transfer rates and particle shrinkage is the main objective of this study. In particular, modelling and simulation could contribute to the understanding of the thermochemical reaction mechanism, the optimization of the operating conditions and also the optimization of the process design instead of having costly and time consuming experimental studies [13]. However, pyrolysis is an extremely complex process, it generally goes through a series of reactions and can be influenced by many factors. Therefore, process design and simulation can be applied to control the overall process conditions and to investigate the optimum level of important factors such as temperature, moisture, and pressure. Among, the various simulation tools, SuperPro Designer (SPD) software is a very useful simulator due to its large database of specific chemical compounds and unit operations. This database is valuable to facilitate the calculation of physical, chemical and biological processes [14]. Application of SuperPro Designer has been reported for process simulation in the production of polyhydroxyalkanoates [15], bio-fuel production [16], and monitoring of biopharmaceutical facility [17]. Currently, to the best of our knowledge, there are no studies available on the experimental and simulation of the fast pyrolysis of Tunisian biomass resources. Therefore, the main focus of this study is to evaluate the potential of Tunisian agro-residues for biofuel production through the fast pyrolysis process and therefore to optimize the operating conditions using the SPD simulation tool.
The overall objective of these experiments was to investigate the yields and properties of pyrolysis products produced from both feedstocks as well as to identify the optimum pyrolysis temperature for obtaining the highest organic bio-oil yields on a dry basis.
2 Modeling and simulation
2.1 Pyrolysis plant
The basic diagram developed for the simulation of the biomass fast pyrolysis process is based on the available data in the literature [18]. The pyrolysis plant converts the biomass feedstock into liquid, solid and gaseous fractions. The simplified SuperPro Designer flowsheet of the pyrolysis plant is shown in Fig. 1. The methodology employed for modelling and the process details in SuperPro Designer along with the definitions of the investigated parameters are described in Tables 1 and 2. The fast pyrolysis process is modeled in a parallel sequence combining three standard reactors (in standard continuous reactors (Plug flow reactors or Continuously Stirred Tank Reactors) processing cellulose, hemicellulose and lignin separately. In fact, cellulose, hemicellulose and lignin are supposed to be pyrolyzed independently in wood without interactions. Hence each reactor should apply a kinetic reaction calculation with different kinetic parameters. The chemical reactions based on kinetic parameters were provided from the academic literature [19,20].
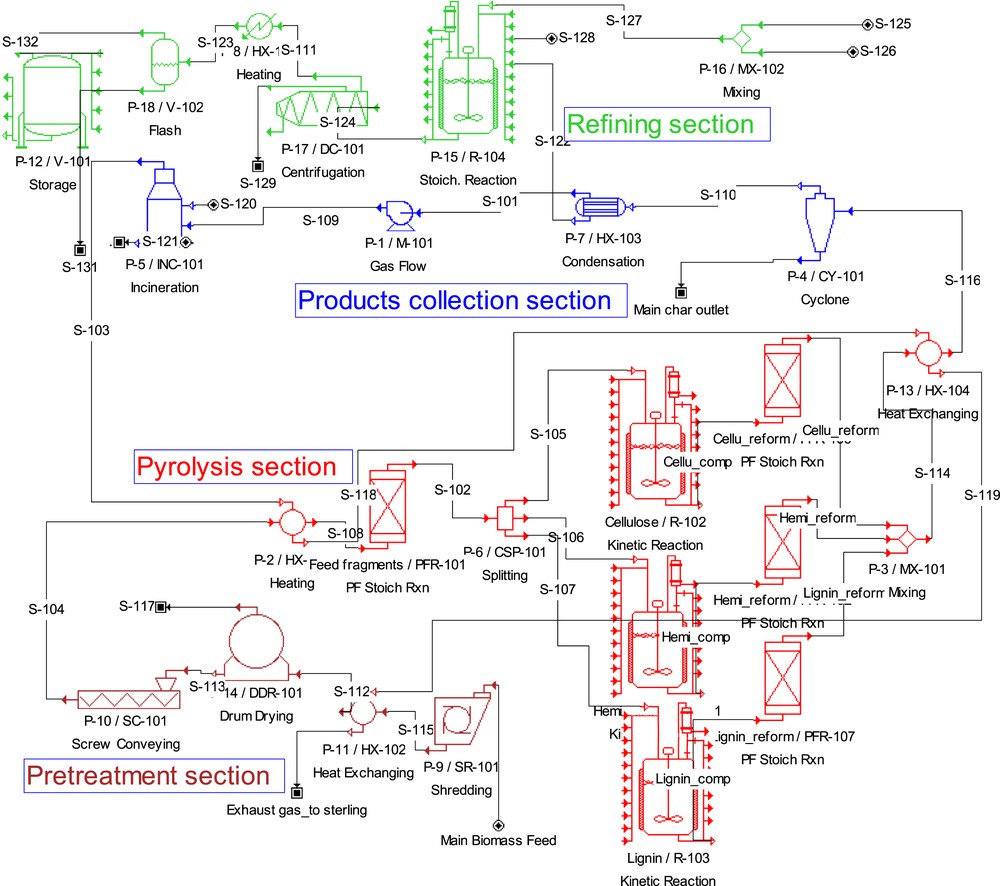
Flowchart diagram of the biomass pyrolysis process in SuperPro Designer.
Reactor block description in the simulation.
SuperPro Designer name | Description |
Feedstock dryer | P-14/DDR-101-simulates the drying process |
Feedstock fine shredder | P-9/SR-101-This unit procedure simulates shredding (size reduction) of biomass |
Screw conveyer | P-10/SC-101-This unit procedure simulates transport of biomass using a screw conveyor |
Cyclone | P-4/CY-101-separates the char component from gaseous streams |
Condenser/quencher | Simulates recovery (separation) of volatile compounds from a gaseous stream stoichiometric reactor |
Incinerator | The primary objective of the model is to calculate the composition of the flue gas stream and estimate the flow rate of auxiliary fuel if needed |
Various heat-exchangers | P-2/HX-101,P-11/HX-102,P-13/HX-104-Heating |
Stirred tank reactor CSTR | Cellulose/R-102,Hemicel/R-103, Lignin/R-103-This procedure is used to represent a sequence of continuous reactions that take place in a stirred reactor (CSTR) and which are described by stoichiometry and kinetics |
Plug flow reactor PFR | Feeds fragments PFR-101-stoichiometric reactor decompose the fed stream |
Decanter centrifuge | P-17/DC-101-simulates a decanter centrifuge for solid-liquid or liquid–liquid separation |
Flash Drum | P-18/V-102 flash simulates separation of volatile compounds in a flash drum. Several thermodynamic model options are available for handling the VLE calculations |
Storage | P-12/V-101 storage-simulates storage of continuous flows in a vertical-on-legs tank. |
Summary of pyrolysis reactions.
Pyrolysis reactions | Reactor |
Biomass→cellulose+hemicellulose+lignin+ash | Feed fragments/Plug flow reactor- PFR-101 |
Unreacted fraction+carbon+ash→char | Continuous kinetics in CSTR:cellulose/R-102 |
Tar+vapors (condensable)→bio-oil | Continuous kinetic reaction in CSTR:lignin |
Gas (unreacted)→process gas | Cellulose reform PFR-106, hemicellulose reform PFR-102, Lignin reform PFR-107 |
2.1.1 Biomass pretreatment section
In this section, the biomass stream is introduced into a shredding unit procedure (P-9/SR-6101) (Fig. 1). This unit simulates the feed shredding (size reduction) into small particle in order to ensure a rapid reaction. Secondly, the shredded sample is dried using a drum drying unit procedure (P-14/DDR-101). The latter simulates the drum drying under vacuum conditions. Next, the dried biomass is transported to the pyrolysis reactor using a screw conveyor. This step is simulated using the unit procedure (P-10/SC-101).
2.1.2 Pyrolysis section
In the pyrolysis section, the biomass heating occurs through heat exchange between the feed and the hot gas stream. The stream S-104 (Fig. 1) is fed to the plug flow reactor (PFR) which is the first reactor of the pyrolysis section. During the fast pyrolysis process biomass pyrolysis proceeds through a series of complex reactions consisting of primary activation and fragmentation reactions, followed by secondary vapor phase cracking reactions [19,20].
The pyrolysis process reactions are given in Table 3.
Primary pyrolysis reactions and Arrhenius parameters for the simulation process.
Pyrolysis reactions | A (s−1) | E (kJmol−1) | References |
Cellulose→active cellulose | 2.8.1019 | 240 | [19] |
Cellulose→0.60Char+0.4H2O | 6.7.105 | 110 | |
Active cellulose→gas | 3.6.1011 | 200 | |
Active cellulose→vapours | 6.8.109 | 140 | |
Active cellulose→0.6char+0.4H2O | 1.3.1010 | 150 | |
Vapours→gas | 3.6.1011 | 200 | |
Vapours→tar | 1.8.103 | 61 | |
Hemicellulose→active hemicellulose | 2.1.1016 | 187 | [20] |
Active Hemicelulose→vapours | 8.8.1015 | 202 | |
Active hemicellulose→x.Char+(1−x) gas | 2.6.1011 | 146 | |
Vapours→gas | 4.3.106 | 108 | |
Lignin→active lignin | 9.6.108 | 108 | [20] |
Active lignin→vapours | 1.5.109 | 144 | |
Active lignin→x.Char+(1−x) gas | 7.7.106 | 111 | |
Vapours→gas | 4.3.106 | 108 |
2.1.3 Product collection section
Char separating and vapor condensation for bio-oil recovery are the unit operations in this section including a gas cyclone and a condenser. A cyclone separates the solid char product and the liquid product is rapidly condensed. The produced gases are transported to the incineration procedure. One may note that no significant waste is generated since the residual char is recycled back into the process. After the product collection section, the produced liquid goes through an upgrading step. Each product stream from the process consists of organic condensate (bio-oil), solid residue (biochar) and non-condensable gases (pyrolytic gases).
2.1.4 Bio-oil refining section
This section is composed of a mixing vessel (V-102), a reactor (R-104), a decanter centrifugal separator (DC-101) and a biodiesel storage tank (V-101). The bio-oil is directly fed to the reactor (R-104). Methanol and the catalyst are mixed and 90% of the mixture is fed to the first reactor (R-104). Methanol reacts with bio-oil and yields biodiesel and glycerol. The material is then fed to a continuous centrifugal separator (DC-101) to separate the biodiesel from the aqueous phase, which is fed to the biodiesel crude storage (V-101).
2.2 Model verification
In order to validate the designed process, the developed model was tested for the fast pyrolysis of oak wood. The simulation results are compared with experimental data obtained for various operating conditions by Park et al. [21]. These authors have studied experimentally the influence of the reaction temperature, the size flow rate and the fluidizing medium on the product yields of the oak wood in a fluidized bed reactor. The wood oak proximate analysis and the major component fraction are shown in Table 4. The simulation was performed at different temperatures for a feed size of 0.7 mm, flow rate of 3 L/min, feeding rate of 2.5 g/min as realized by Park et al. during their experimental tests [21]. A comparison between the experimental and calculated products yields as well as the relative error is shown in Table 5.
Chemical composition of oak wood [21].
Chemical composition (wt%) | |
Cellulose | 50 |
Hemicellulose | 14.3 |
Lignin | 22.8 |
Proximate analysis (wt%) | |
Water | 10.4 |
Combustibles | 87.6 |
Ash | 2.0 |
The products yields of experiments and simulation results (%)
T (°C) | 400 | 450 | 500 | 550 | ||||||||
Yield | Exp% | Cal% | Error% | Exp | Cal | Error% | Exp | Cal | Error% | Exp | Cal | Error% |
Bio-oil | 46.0 | 47.5 | 3.1 | 48.0 | 50.6 | 5.1 | 45.0 | 47.4 | 5.1 | 36.0 | 40.7 | 11.6 |
Char | 29.1 | 32.8 | 11.2 | 22.0 | 25.3 | 12.9 | 18.9 | 20.7 | 8.8 | 15.8 | 17.5 | 9.3 |
Gas | 23.4 | 23.2 | 9.4 | 27.3 | 25.3 | 8.2 | 33.2 | 30.4 | 9.0 | 42.5 | 40.2 | 6.6 |
The simulated values confirm that the bio-oil fraction is maximized at 450 °C. However, above 450 °C, the bio-oil fraction decreases with increasing pyrolysis temperature. According to Park et al., a temperature below 450 may be inadequate for complete fast pyrolysis and may therefore explain the lower bio-oil fraction. In addition, simulation results confirmed that the gas yields increase and the char yields decrease with increasing pyrolysis temperature. This behavior resulted from the secondary cracking of the pyrolysis vapors and char into gas.
A comparison between experimental and calculated yields shows a good agreement. However, a slight discrepancy is observed and the mean error for the all tested values is 8.4%. Such discrepancy may be due to the interaction of the different biomass components. In fact, as mentioned previously, the SuperPro Designer simulation does not take into account such interaction and the fast pyrolysis process is modeled in a parallel sequence combining three standard reactors processing cellulose, hemicelluloses, and lignin separately.
3 Results and discussion
The fast pyrolysis of Tunisian agricultural and agrifood residues is simulated using the already validated model developed with the SuperPro Designer tool. The selected feedstocks chosen for the simulation are date palm rachis, olive stones, vine stems and almond shells. The main components of these biomasses taken from the published data are shown in Table 6 [5,22,23,24]. The selected operation conditions and primary parameters for the simulation are shown in Table 7.
The lignocellulosic contents of the Tunisian feedstocks.
Biomass type | Cellulose (%) | Lignin (%) | Hemicellulose (%) | Moisture | Fixed carbon | Ash | Refs |
Date palm rachis | 45 | 17.2 | 29.8 | 12.1 | 1.5 | 5 | [24] |
Olive stones | 25 | 35 | 35 | – | – | 5 | [22] |
Vine stems | 35 | 28.1 | 30.4 | – | 6.07 | 3.9 | [23] |
Almond shells | 26 | 28 | 29 | 7 | 6.33 | 2.71 | [5] |
Process parameters provided as input to the model.
Parameter | Value/range |
Main biomass feed rate | 62 kg/h |
Air temperature | 25 °C |
Pyrolyser temperature | 450–600 °C |
Residence time | 0.1–20 s |
Dryer temperature | 152 °C |
pressure | 1.013 bar |
Generally, in biomass fast pyrolysis, liquid bio-oil is regarded as the main product, while solid char and permanent gases are valuable byproducts. Hence, the main purpose of this study is to determine the optimum conditions for bio-fuel production for these selected Tunisian feedstocks. To reach this goal, two different simulation tests were carried out through the study of the effects of the pyrolysis temperature and residence time on the product yields. Firstly, the simulation was performed, for each feedstock at different final temperatures (450–650 °C) and at a residence time equal to 0.5 s. The results of the effect of temperature on the product yield (%) during the fast pyrolysis simulations for the four samples are shown in Fig. 2a–d. As observed in Fig. 2a–d, bio-oil yields for the different samples increase with increasing reaction temperature from 450 °C and reach a maximum at a pyrolysis temperature of 550 °C. Above 550 °C, the bio-oil yields decrease with increasing temperature 650 °C. Therefore, the optimum temperature for bio-oil production from the four samples at 0.5 s residence time is 550 °C. Similar results were obtained by Acıkgoz et al. [25] during the fast pyrolysis of linseed (Linum usitatissimum). Authors showed that the maximum oil yield of 57.7% was obtained at a final pyrolysis temperature of 550 °C [25]. Demirbas has also observed similar behaviour during the study of the fast pyrolysis of various biomass samples. The author found that the liquid product yields obtained during the pyrolysis of hazelnut shell, olive husk, beech and spruce wood samples raised from 36.3% to 47.5%, from 38.0% to 48.9%, from 34.8% to 45.4%, and from 32.2% to 43.1% when the temperature was increased from 625 to 800 K and then declined from 47.5% to 40.0%, from 48.9 to 42.6%, from 45.4% to 37.3% and from 43.1 to 34.9%, when the temperature increased to 875 K, respectively. The obtained values for the different samples in this present study are in the same range as those found by Demirbas [26]. In fact, the maximal bio-oil yield was 46.68%, 44.05%, 44.61%, and 46.26% for date palm rachis, olive stones, almond shells, and vine stems, respectively. The different yields obtained for the four samples are expected since the sample characteristics are different as shown in Table 6. Troger et al. reported that different feedstocks produced different char, condensate and gas fractions due to their ash content and polymer constituent variation [27]. The comparison between the different bio-oil yields shows that the higher fractions are obtained for date palm rachis and vine stems. Moreover, the bio-oil yield order follows the same cellulose content order in the four Tunisian feedstocks. Hence, the higher bio-oil yield for date palm rachis is attributed to its higher cellulose content (45%). Several investigations have evaluated the pyrolysis of cellulose extracted from different biomasses. Hosoya et al. have shown that cellulose leads to the highest tar yield (72%) during the investigation of the pyrolysis of wood and its cell wall constituents [28]. Such a result was confirmed by Wang et al. during the investigation on the interaction of components on the pyrolysis behavior of biomass. Authors showed that during cellulose pyrolysis, the bio-oil yield was 81.41 wt% while the gas and char yields represent only 12.15 and 6.44 wt%, respectively [29].
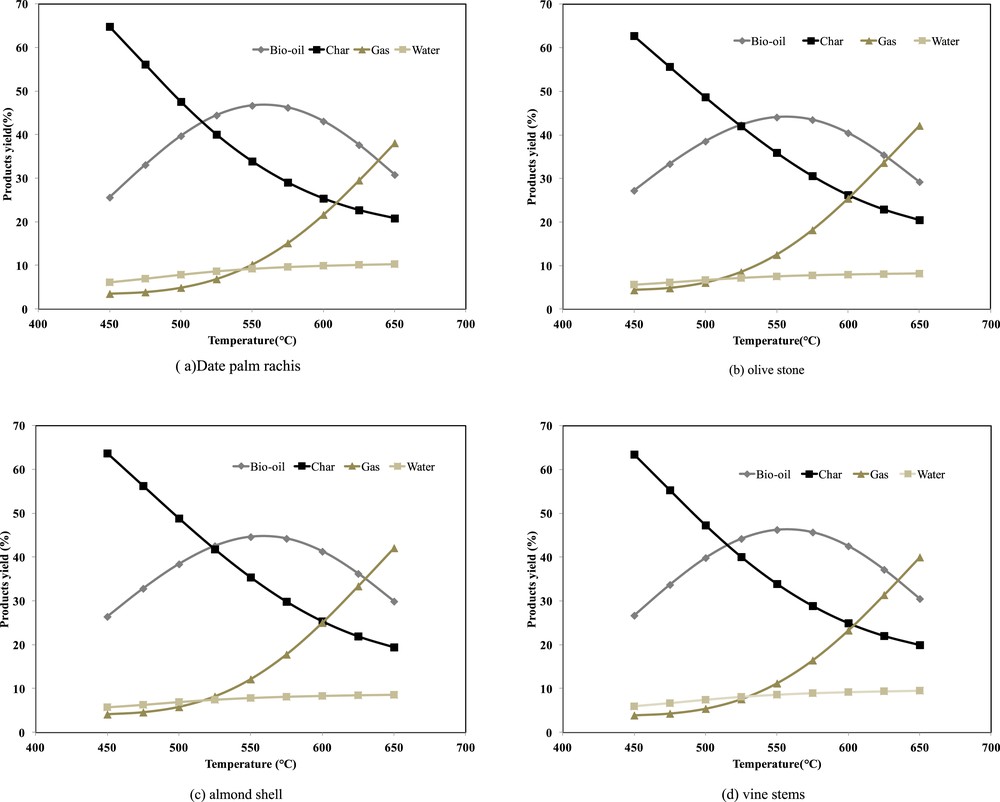
Effect of temperature on the product yield of the fast pyrolysis of Tunisian feedstocks.
The analysis of the product yields in Fig. 2a–d confirms the increase of the gas yields and the decrease of char yields with increasing temperature. In fact, the gas yield during the pyrolysis of date palm rachis, olive stones, almond shells, and vine stems increases from 3.47% to 38.08%, from 4.37% to 42.13%, from 4.11 to 42.08%, and from 3.88% to 40% when the temperature increases from 450 to 650 °C. Comparison between the different feedstocks shows that olive stones produce the highest gas yield at temperatures below 650 °C. However, the discrepancy between olive stones and almond shells is not very important. The increase in gas yields and the decrease in liquid yields at high temperatures are due to secondary cracking of pyrolysis vapors and [22]. This can be explained by the formation of secondary cracking reactions of the pyrolysis vapors at higher pyrolysis temperatures. The cracking has led to more higher gas production, which was also observed at other biomass waste in the literature [4]. The higher gas fractions obtained for olive stones seems to be correlated with the amount of hemicellulose and lignin. In fact, the investigation on the pyrolysis of the three biomass components found in the literature shows that hemicellulose and lignin generate equivalent gas yield. However, such a hypothesis is not valuable for almond shells with a lower hemicellulose and lignin content and equivalent gas yield compared to olive stones. Such behaviour indicates that the biomass polymer components are not the main factor affecting the pyrolysis product yields.
The second series of simulation was performed to evaluate the effect of residence time on the fast pyrolysis process. Therefore, the bio-oil yields were evaluated for different temperatures at different residence times ranging between 0.25 and 10 s. As can be seen in Fig. 3a–d, comparison between the different feedstocks shows that for date palm rachis, olive stones, and vine stems, the highest bio-oil yields are 47.44%, 45.51%, and 47.30% respectively, obtained at 575 °C and a residence time equal to 0.25 s. However, there is no significant difference between these optimized parameters and those obtained at 550 °C and 0.5 s. Therefore, other parameters such as bio-oil properties should be taken into account in order to select the suitable operating conditions.

Effect of residence time on bio-oil yield.
In addition, the bio-oil yields were found to marginally decrease with increasing residence time at high temperatures. In contrast at low temperatures, the bio-oil yields increase with increasing residence time. Therefore, for each temperature an optimum residence time is obtained. However, as mentioned previously, the highest bio-oil yields are obtained at a pyrolysis temperature of 575 °C and a residence time equal to 0.25 s. The decrease of the bio-oil fractions with increasing temperature at higher temperatures is in agreement with results from the literature. According to Mettler et al., a longer volatile residence time maximizes secondary reactions such as cracking and re-polymerization reactions, which increases the production of gases and char and decreases the liquid yields [30].
Several investigations have shown that maximum liquid yields are obtained with high heating rates at reaction temperatures around 500 °C and with short vapour residence times to minimise secondary reactions [31–33]. According to Bridgwater et al., thermal processes provide multiple and complex products in a short reaction time, which is known to influence the pyrolysis product yield [31]. In addition, there is a competitive effect between the residence times of volatiles and solids. As the residence time of solids increases, devolatilization increases. In contrast at high residence times of the volatiles, decomposition reactions that decrease bio-oil are promoted. Pattiya showed also that at higher temperatures or lower vapour residence time, the chances of secondary vapour cracking are less than the runs with longer vapour residence time, leading to higher molecular weight products [34].
The effect of residence time on product yields during pyrolysis has been demonstrated to be significant in previous investigations [35]. Generally, it is accepted that short residence times are suitable for production of liquids from pyrolysis. Vapor residence times of a few seconds to a few minutes are often recommended to obtain optimum yields of bio-oil through pyrolysis. However, at very short residence times, it is doubtful to conceive complete biomass thermochemical conversion due to heat transfer difficulties at the particle surface. Residence times for decomposition of biomass particles must be longer than the vapor residence times to obtain higher yields and biomass conversion.
4 Conclusion
The fast pyrolysis process of Tunisian agricultural and agrifood residues was optimized using SuperPro Designer simulation. The biomass thermochemical conversion was modeled by a parallel sequence combining three standard reactors processing cellulose, hemicelluloses, and lignin separately. The simulation includes pretreatment, fast pyrolysis, product collection and upgrading sections. The developed model was successfully validated with published experimental results of wood oak fast pyrolysis. Then, an optimization investigation on the fast pyrolysis of date palm rachis, olive stones, vine stems and almond shells was performed. In particular, the effect of reaction temperature and residence time on pyrolysis products for different biomass feedstocks was examined. The obtained results indicated that the highest bio-oil yield was obtained at 575 °C for a residence time equal to 0.25 s. Comparison between the different feedstocks indicates that the higher bio-oil fraction was obtained from the date palm rachis and vine stems. However, the difference between the samples is not significant and further investigations on the bio-oil properties are requested to select the suitable biomass for bio-oil production in Tunisia.