1. Introduction
It is estimated that 19,300 km of rivers and 72,000 ha of lakes and aquatic reservoirs are severely affected by mining effluents worldwide [1]. In addition to the economic damage they cause, acid mine drainage (AMD) poses serious risks to human health. The contamination of surface water and sediments by mining sites therefore represents a major public health issue [2, 3]. Like many other European countries, France has a long tradition of mining dating back to the Neolithic period [4]. In the 1980s, economic constraints led to the end of mining in mainland France [5]. The map of mineral deposits in France lists 1400 sites that have produced ores [6].
When mining waste or mining structures (galleries, mine shafts, and open pits) containing sulfide minerals, such as pyrite (FeS2) and pyrrhotite (Fe(1−x)S with x < 0.125), come into contact with water and oxygen, an oxidation reaction can occur that will lead to the production of AMD according to Equation (1) in the case of pyrite.
(1) |
If preventive measures such as handling plans, alkaline amendment, and covers are not implemented before the oxidation reactions begin, AMD production is difficult and even impossible to stop [10]. Besides their potential impacts on the environment, AMD can also contain valuable metals. In general, there is a positive correlation between the acidity of the treated effluent and the concentration of the metals in the water, particularly for Cu, Zn, Ni, and Mn, as explained by Plumlee et al. [11]. As the flows of AMD are difficult, if not impossible, to control permanently, they need to be treated for a long time. These systems represent a significant long-term cost to society, to which must be added the storage of solid waste resulting from these treatments that accumulates over time. Chemical neutralization involves mixing AMD with alkaline materials (such as limestone, magnesia, and lime) to precipitate most of the heavy metals. The AMD treatment by reaction with lime is described by Equation (2):
(2) |
On one hand, these metals can be potentially harmful for human health and for the environment, but, on the other hand, they can also be economic and technologically valuable, particularly in the current context of energy transition, as they can attain significant concentrations in the sludge. For instance, analyses carried out on lime treatment sludge from seven mines in Canada show that some metals can be present at very high concentrations: up to 1.4% of copper and 22% of zinc [17, 18]. There have been numerous studies focusing on the recovery of metals directly from AMD using specific processes [19, 20], but very few authors have studied the recovery of metals in historical sludge dumps produced through conventional lime treatment of AMD [21, 22].
The work of Macias et al. [18] is particularly noteworthy as well as the patent by Ziemkiewicz et al. [22] on the recovery of rare earth elements (REEs) from AMD, which includes liming of the AMD and subsequent treatment of the sludge although this process was designed specifically to recover REEs [23].
The recovery of valuable metals in AMD presents a significant challenge, as fluxes of these metals are often too low. Inline metal recovery is rarely economically viable due to both low water flow rates and/or low metal concentrations. Consequently, this research work aims to address the large-scale challenge posed by substantial sludge deposits that have accumulated over decades instead of developing a process for recovering metals directly from AMD or from the daily-produced sludge by lime treatment. By targeting these existing deposits, we propose a short treatment operation designed to recover valuable metals efficiently, offering a novel solution to a long-standing environmental and economic issue.
In particular, this study covers the selective leaching of metals from a specific AMD lime treatment sludge to recover Cu and Zn while decreasing the amount of Cd in the sludge. For this purpose, sludge from the lime treatment of AMD at a specific French site was characterized and the optimal acid leaching operating conditions (solid content, acid-to-solid ratio, temperature) were determined. Applying optimal conditions means maximizing the leaching yields of Cu, Zn (for economic viability), and Cd (for environmental concerns) while minimizing the leaching of Fe and Al.
The dissolution of Fe and Al consumes reagents without adding value, increasing the operational costs of the process. Moreover, high concentrations of Fe and Al in the leachate can impede the downstream recovery processes. Compared to a pregnant leach solution (PLS) without Fe and Al, the selective removal of these elements requires more reagents, potentially different ones, and additional treatment steps downstream. In particular, the solid/liquid separation of Al precipitates is challenging. Finally, the presence of Fe and Al in the PLS makes it more difficult to achieve the target purity of Cu and Zn products [24, 25].
2. Materials and methods
2.1. Mine site and sludge deposit
The ore deposit from which the AMD is produced is a stockwork containing barite (BaSO4), galena (PbS), sphalerite (ZnS), and chalcopyrite (CuFeS2) in altered soda-dacitic lavas near the Devonian Brévenne rift. It was covered by Triassic sediments (clay and sandstone), which were mineralized in turn by hydrothermal fluids during their deposit. Then, primary sulfides were oxidized allowing the formation of secondary minerals of lead, zinc, and especially copper. The mine was active from 1414 to 1842 for the extraction of copper, and it is estimated that 15,000 t of Cu was produced during this period. From 1842 to 1877, 9000 t of pyrite was mined for sulfuric acid production in addition to the reprocessing of mining waste produced during previous copper extraction (BRGM, internal communication).
AMD has been flowing from water adits since unknown but ancient times. Its average characteristics and uncertainties (95% confidence intervals) calculated using 134 monthly samples from 1998 to 2012 are presented in Table 1. Metals were analysed by SGS company in accordance with standard NF EN ISO 11885 and sulfate are in accordance with standard NF T 90-40. The AMD contains significant amounts of sulfate, iron, and zinc, but also some aluminum and copper.
Chemical composition of AMD samples from 1998 to 2012 (n = 134)∗
Flow rate (m3⋅h−1) | pH | Al (mg⋅L−1) | Cu (mg⋅L−1) | Fe (mg⋅L−1) | SO4 (mg⋅L−1) | Zn (mg⋅L−1) |
---|---|---|---|---|---|---|
7.2 | 2.7 ± 0.1 | 50 ± 5 | 32 ± 7 | 260 ± 40 | 2300 ± 150 | 210 ± 20 |
∗ n indicates the number of samples analyzed from 1998 to 2012.
Lime treatment of AMD started in the middle of the 19th century and still continues as of 2024. All the sludge resulting from more than 150 years of lime treatment was stockpiled on site. The size of the sludge deposits was estimated with GIS software using data from the bibliography including maps from different periods and settling pond cleaning reports as well as an elevation model and the depth of six sludge core samples drilled in 2002 (see Section 2.2.1). The total sludge volume is estimated at 77,000 m3 or around 170,000 t according to the measure of sludge density in the laboratory (2.2 ± 0.4 t⋅m−3, n = 3).
2.1.1. Core sample characterization
An aerial view of the sludge dump is shown on Figure 1, including the position of six core samples drilled in order to obtain a general characterization of the sludge accumulated on the site.
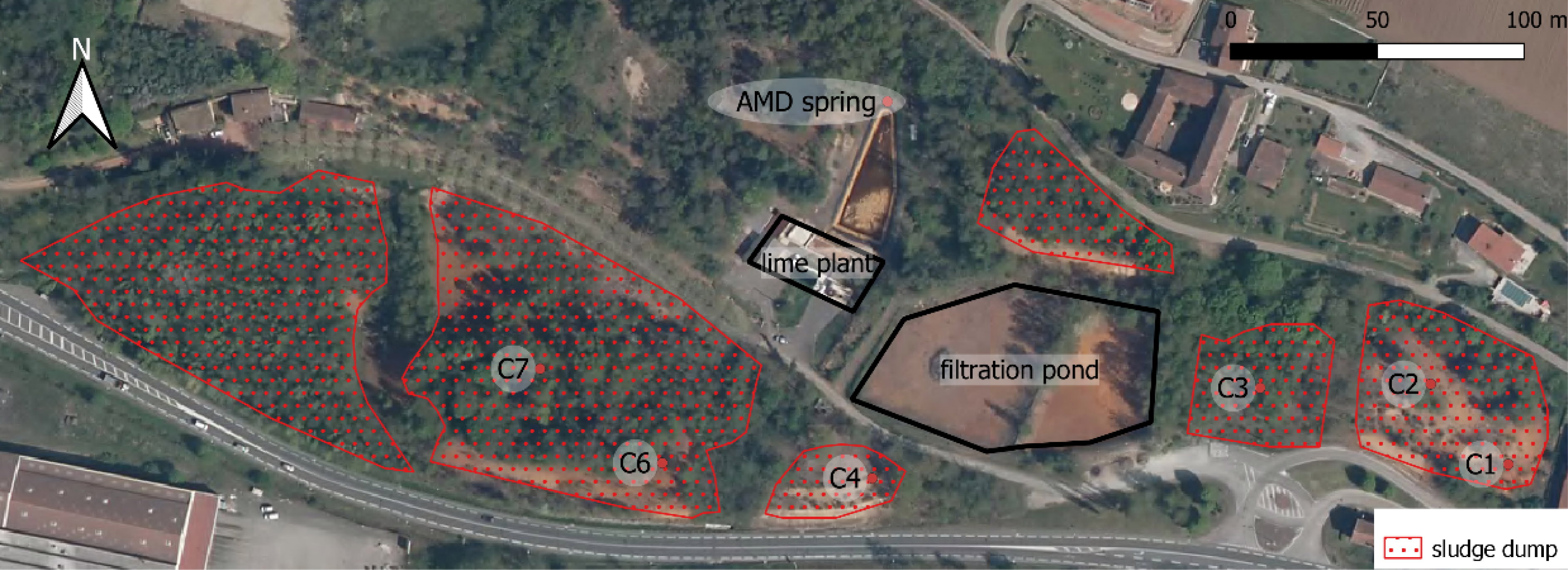
Sludge dump and core sampling locations (C1–C7) on the mining site. For details of the core samples’ depth and number of analyses, refer to Table 2.
The depth and number of analysis on each core sample are presented in Table 2. Sampling of core “C5” was planned but never actually drilled, and therefore, no results of this sample are available.
Sludge depth on each core and number of chemical analyses
Core | Core depth (m) | Sludge depth (m) | Number of analyses |
---|---|---|---|
C1 | 8 | 6 | 6 |
C2 | 8 | >8 | 3 |
C3 | 9 | 3 | 3 |
C4 | 6 | 4 | 2 |
C6 | 12 | 8 | 4 |
C7 | 10 | 8 | 4 |
22 samples allowed the calculation of a robust average and a good estimate of the heterogeneity of this sludge deposit and not specifically the inductively coupled plasma atomic emission spectroscopy (ICP-AES). Carbonates were analyzed by volumetric determination of mineral carbon (NF EN ISO 10693). Mineralogy of the core sample was characterized by X-ray diffraction (XRD, SIEMENS type D5000), scanning electron microscope (SEM, JEOL 6100), and transmission electron microscopy (TEM) with energy dispersive spectroscopy (EDS) (Philips CM 120). Both SEM and TEM analyses were employed to characterize our samples due to the wide range of crystal sizes present. SEM was used to observe larger crystals such as gypsum crystals that were up to 20 μm in size. TEM was used to study nanometric-sized mineral phases and to investigate possible carrier phases for the metals Cu and Zn, including clean mineral phases as well as substituted or adsorbed metals.
2.2. Leaching tests
2.2.1. Characterization of sludge sample used in leaching tests
For the leaching tests, six samples of superficial AMD sludge of a total mass of 15 kg were collected from different points of the site in 2021. Sample preparation included drying in an oven at 40 °C for a period of 48 h to remove excess moisture, disaggregating using a mortar, sieving at 2 mm, and mixing and homogenization of the six samples. Representative subsamples for characterization and leaching tests were then obtained using a riffle splitter. The density of the dried sludge was measured by water displacement. The chemical composition of the homogenized sample was determined by ALS laboratory by different in-house methods. Fusion decomposition was used for major elements such as Fe, Al, Si, and Ca, while Cu, Cd, and Zn were analyzed using a four-acid digestion method (HCl, HNO3, HF, and HClO4). Both analyses were followed by ICP-AES and the loss on ignition test at 1000 °C. Sulfate was determined from the difference between total sulfur (by Leco furnace and infrared spectroscopy) and sulfide (by Leco furnace and Na2CO3 leach). In selected experiments, metal contents of solid samples were measured before and after leaching using a portable X-ray fluorescence (pXRF) Niton XL3t 980 (Thermo Fisher) to perform mass balance calculation. Given the semi-quantitative nature of pXRF analysis, we implemented a stringent protocol to ensure that the data utilized in our study provided accurate elemental concentrations and enabled confident use in mass balance calculations. This protocol includes validation against standard samples, repeated measurements, and systematic verification of XRF spectra. They are inspired by the methods and principles presented by several authors including Touzé et al. [26], Lemière [27], and López-Núñez [28].
SEM images were collected on TESCAN Mira3 XMU (low vacuum field emission SEM) at BRGM, using a high voltage of 15 kV. EDS analyses were performed on an EDAX APEX system equipped with a 70 mm2 silicon drift detector (SDD). Sample powders were dispersed on an aluminum stub covered with a double-coated carbon conductive tape and coated with a 20 nm conductive carbon layer. TEM was conducted on JEOL ARM200CF (double Cs corrected cold FEG TEM/STEM) at the electron microscopy platform MACLE (CNRS Orleans). EDS analyses were obtained on a JEOL Centurio SDD detector. Images and analyses were performed at 200 kV.
2.2.2. Experimental setup
Three different experimental setups were used to study the leaching of Zn and Cu from the lime treatment sludge: 250 mL shake flasks, then 0.5 L stirred tank reactors (STRs), and finally 2 L STRs. The tests in 250 mL shake flasks were carried out only at low solid contents in order to avoid mass transfer and solubility limitations. Tests with higher solid contents necessitated the transition to STR, initially at 0.5 L and then at 2 L to ensure a good solid suspension. The progression to a larger volume was also driven by the need for sufficient sample quantities for accurate residue analysis via pXRF.
2.2.2.1. Tests in shake flask
For preliminary leaching tests, 250 mL shake flasks were used at low solid contents (<1.3% mass/mass). The working volume of these tests was fixed at 150 mL. Magnetic stirrers were added to the shake flasks, and agitation was carried out using a magnetic stirring table at 150 rpm (Supplementary Figure S1). Shake flasks were covered with Parafilm® to avoid excessive evaporation. For each experiment, the flasks were filled with 150 mL of deionized water and the specific amount of solid required. Then, the pH was decreased by adding H2SO4 to a value close to 3.0 ± 0.2. Throughout the duration of each test, pH was maintained between 3.0 and 3.5 by adding a solution of sulfuric acid (1 mol⋅L−1) dropwise when pH was higher than 3.5.
This value was chosen so that the solution would be as acidic as possible to leach a maximum of Cu and Zn without dissolving iron, as Fe3+ can begin to be significantly soluble below a pH of 3.0 [29]. Samples were taken to determine metal concentrations, and temperature, pH, conductivity, and redox potential (Eh) were measured directly in the reactors at the initial time and at approximately 0.25 h, 1 h, 2 h, 4 h, 6 h, and 24 h after the beginning of the experiment. For metal concentration measurements, about 2 mL of pulp was filtered at 0.45 μm, diluted 10 times using 1% HNO3, and placed at 4 °C. The total amount of solids passing through the filter was considered negligible since particle size measurements of the sludge showed that only 0.82% of particles were smaller than 0.42 μm. Metal concentrations (Al, Cd, Cu, Fe, and Zn) were then measured on the filtrate either by atomic absorption spectroscopy (SpectrAA 220FS, Varian) or using a 4210 microwave plasma atomic emission spectroscope from Agilent Technologies.
2.2.2.2. Tests in STRs
Leaching experiments were also performed in two types of reactors with working volumes of 0.5 L (Supplementary Figure S1) and 2 L. The experimental setup was fully described by Guezennec et al. [30]. They were equipped with four baffles mounted 90° apart and extended down to the base of the vessel for pulp mixing. The 0.5 L reactor was equipped with an axial flow three-blade 45° impeller, whereas the 2 L reactor (Figure 2) had a dual impeller system (axial/axial) with the same characteristics (three-blade 45° axial flow). The agitation speed was fixed at 600 rpm for both systems. The temperature control system (LAUDA MC) circulated warm water (22 °C, 40 °C, or 60 °C) in the reactor jacket to maintain constant operating temperatures. Experiments conducted above room temperature aimed to assess the potential for reducing iron solubility and thereby enhance the selectivity of the leaching process [31].
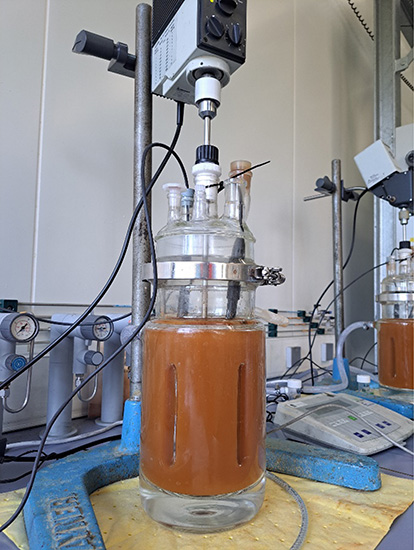
Photograph of the experimental setup using 2 L reactors.
The experimental procedure was similar to that for shake flasks but used the required working volume of deionized water according to the reactor size (0.5 L or 2 L). However, no pH control was performed in STR tests. The total amount of sulfuric acid required for the experiment was added before the solid in the reactors. The goal was to maintain an initially high acidic environment during the early stages of the reaction. The monitoring of physicochemical parameters and leachate sampling and analyses were performed as described for shake-flask experiments (Section 2.2.2.1). At the end of some of the tests in 2 L reactors, the entire amount of pulp was filtered using glass microfiber Whatman® filter grade GF/A (cut-off 0.8 μm).
2.2.3. Calculations
The solid content was calculated using Equation (3).
(3) |
The acid-to-solid ratios were calculated according to Equation (4).
(4) |
When solid analysis was not possible (for tests with solid contents lower than 1.3% m/m), leaching yields were calculated from analysis of the liquid phase as shown in Equation (5).
(5) |
When the compositions of the residual solid after leaching were analyzed (for tests with solid contents higher than 2.9% m/m), leaching yields were calculated both by Equation (5) and from the analyses of the solids according to Equation (6).
(6) |
Mass balances for the targeted metals were performed, and the differences between the leaching yields calculated from solid and liquid phases were always less than 10%.
3. Results
3.1. Core sample characterization
The sludge is mainly composed of Ca, Fe, and SO4 with significant amounts of Cu and Zn, with about 1% and 5% respectively of the total mass of the samples, as presented in Table 3. Other elements present in low amounts are Al and Si. It is important to highlight that there is also a non-negligible amount of Cd, a heavy metal potentially harmful for human health and the environment. Uncertainties calculated as 95% confidence intervals show that the concentration variabilities are generally low despite the fact that samples included come from different cores and several depths. This means that the sludge accumulated on the dump can be considered fairly homogeneous.
Average composition of sludge core samples and the sludge used in leaching tests
Compound (%) | Core samples (n∗ = 22) | Sludge used in leaching tests |
---|---|---|
Al2O3 | 3.3 ± 0.4∗∗ | 3.5 |
CaO | 24 ± 1 | 17 |
Cd | 0.011 ± 0.003 | 0.010 |
Al2O3 | 0.7 ± 0.3 | 1.3 |
Cu | 1.3 ± 0.2 | 1.1 |
Fe2O3 | 17 ± 1 | 16 |
SiO2 | 3.5 ± 0.8 | 7 |
SiO42− | 31.9 ± 0.6 | 26 |
Zn | 5 ± 1 | 5 |
Mass loss at 105 °C | 60 ± 2 | 26 |
∗Number of samples analyzed. ∗∗Uncertainties correspond to 95% confidence intervals.
The main minerals identified by XRD were gypsum (CaSO4⋅2H2O), quartz (SiO2), an amorphous phase (probable ferriferous, possibly ferrihydrite (Fe3−0.5y(OH)y⋅nH2O) as commonly observed in liming of AMD [17, 32]), feldspar ((Ba,Ca,Na,K,NH4)(Al,B,Si)4O8), illite ((K,H3O)(Al,Mg,Fe)2(Si,Al)4O10[(OH)2,(H2O)]), barite (BaSO4), calcite (CaCO3), lepidocrocite (𝛾FeO(OH)), and jarosite (KFe3(SO4)2(OH)6). The identification of metal-bearing phases was made very difficult by the abundance of gypsum and the high proportion of the amorphous phase. A detailed study of these samples by EDS–SEM and XRD revealed the presence of Cu–Fe crystallites with a “desert rose” morphology (Figure 3), identified by XRD as delafossite (CuFeO2) and ferriferous tabular crystallites with Zn. XRD diffractograms of a delafossite-rich sample and a lepidocrocite-rich sample are presented in Supplementary Figures S2 and S3. The only crystallized ferriferous phase identified in this specific sample is lepidocrocite. There are also some ferriferous aggregates with no trace of other metals and very abundant gypsum that contains no trace of metallic elements. No zinciferous mineral phase was clearly identified by XRD.
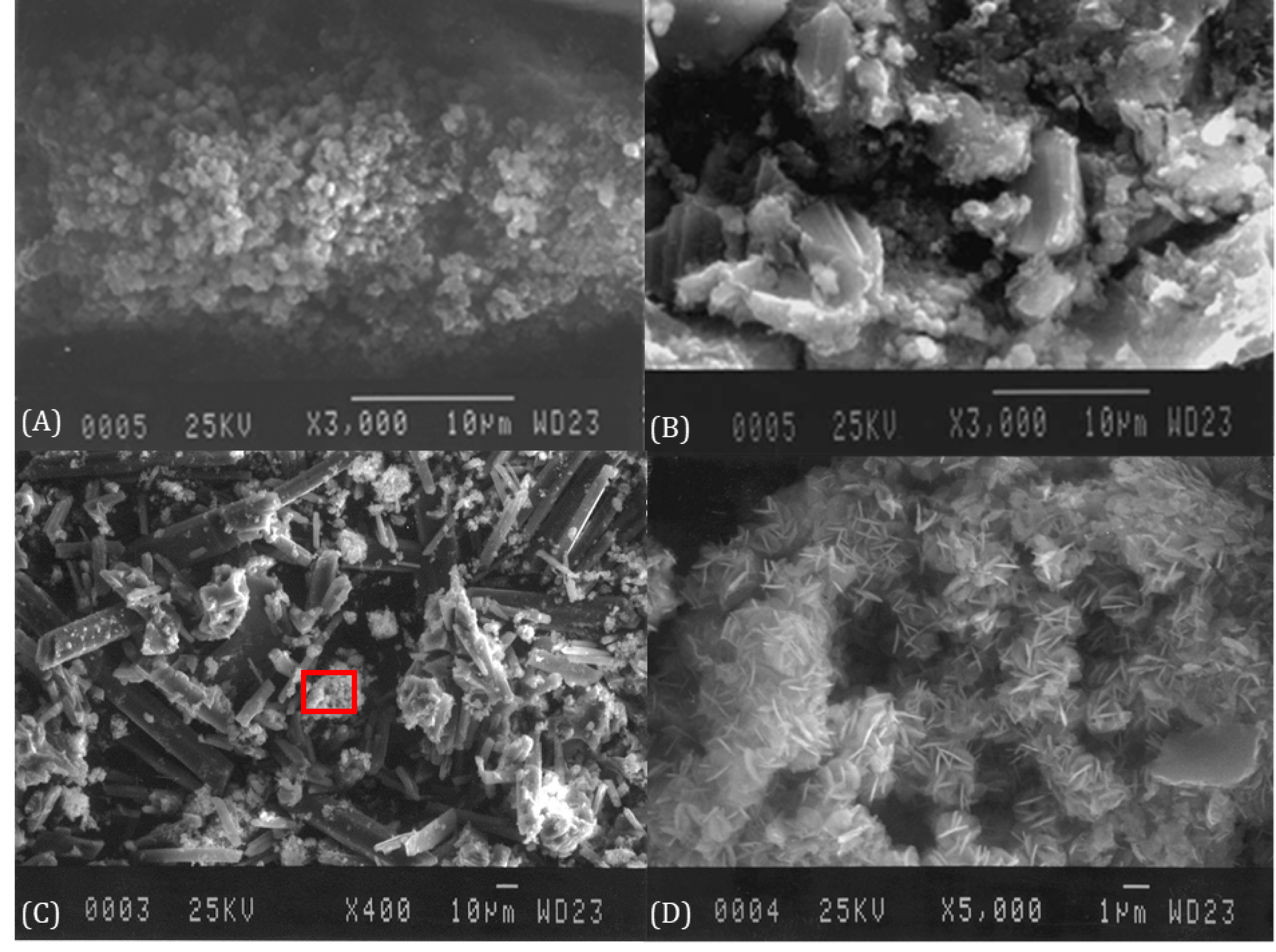
SEM microphotographs of (A) iron-rich aggregates, (B) tabular iron-rich zinciferous rods, (C) gypsum, and (D) delafossite, which is the focus of the red rectangle from (C).
3.2. Leaching tests
3.2.1. Characterization of sludge sample used in leaching tests and residues
As can be observed in Table 3, the composition of the sludge used in the leaching tests is similar to that of the core samples. Indeed, the contents of Fe, Cd, Cu, and Zn in the sludge used for the leaching test fall within the 95% confidence intervals of those found in the core samples. The EDS–SEM mapping of sludge before leaching is presented in Figure 4. This SEM map illustrates the elemental distribution within our sludge sample prior to leaching. Notably, Ca and S are closely linked, forming large and well-defined crystals indicative of gypsum. Conversely, the distribution of iron in the sample appears diffuse, with no identifiable crystalline form at this scale of observation. This suggests that the iron-bearing phases are very finely grained and/or pseudo-amorphous [29, 33]. Sulfur’s lack of association with iron suggests the minimal presence of iron sulfate minerals, such as schwertmannite and jarosite, in this sample. In contrast, Zn shows a strong association with Fe, which may be representative of metal-substituted iron oxides or oxyhydroxides. Interestingly, some regions rich in iron show no corresponding zinc presence, pointing to a heterogeneous distribution of zinc within the iron matrix. Cu is likely also associated with iron; however, its concentration is too close to the quantification limit and the bremsstrahlung background to allow a meaningful interpretation other than indicating the absence of any Cu-rich minerals. Gypsum crystals are completely devoid of zinc, whereas traces of copper are present. The absence of distinct copper or zinc hotspots at this scale indicates that there are no specific copper or zinc minerals present or if they are, they exist in such low abundance that they are not detectable.
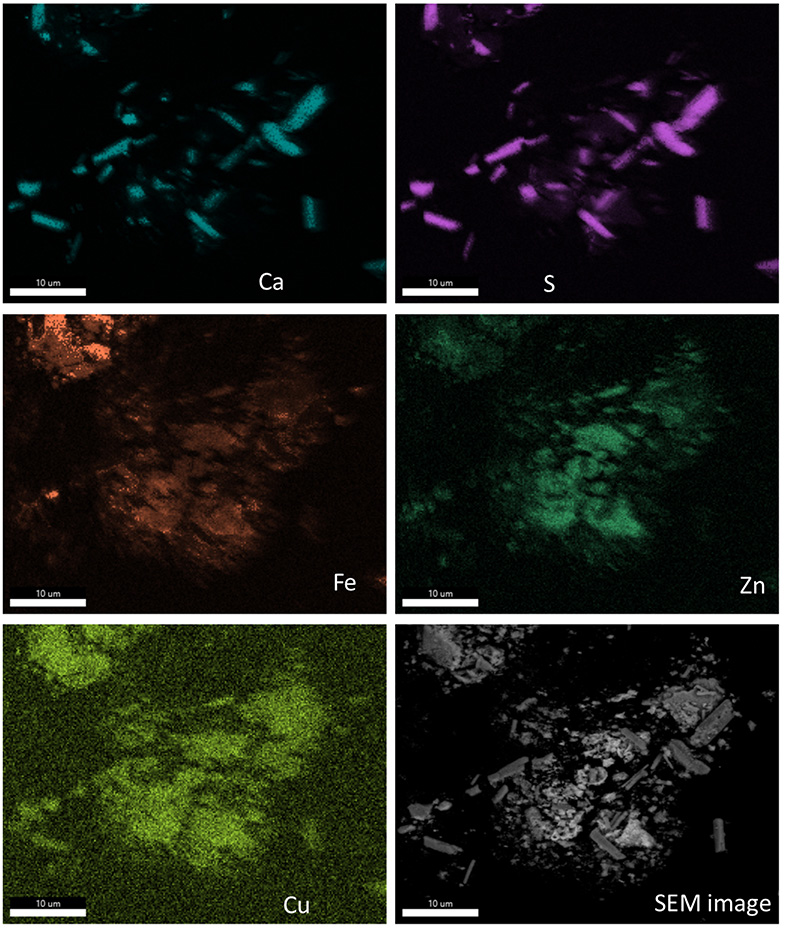
EDS–SEM mapping of sludge before leaching.
SEM mapping of residue after leaching (with an acid-to-solid ratio of 150 g⋅kg−1 and with 0.7% of solid content) was also carried out. However, the concentrations of Zn and Cu after leaching are too close to the quantification limit and the bremsstrahlung background to allow a meaningful interpretation aside from the absence of Zn-rich minerals at this scale. These results are presented in Supplementary Material Figure S4.
The TEM images and EDS analyses of a gypsum crystal and iron-rich aggregates are shown in Figure 5 and Table 4. They confirm the virtual absence of Cu and Zn in gypsum and their strong association with iron. On the EDS analyses of the gypsum crystals observed in the TEM, the stronger association of Cu with gypsum is much less obvious (compared with the SEM map). At this much smaller scale, the crystal form of the ferriferous phases is also poorly defined, suggesting very fine-grained or pseudo-amorphous minerals.
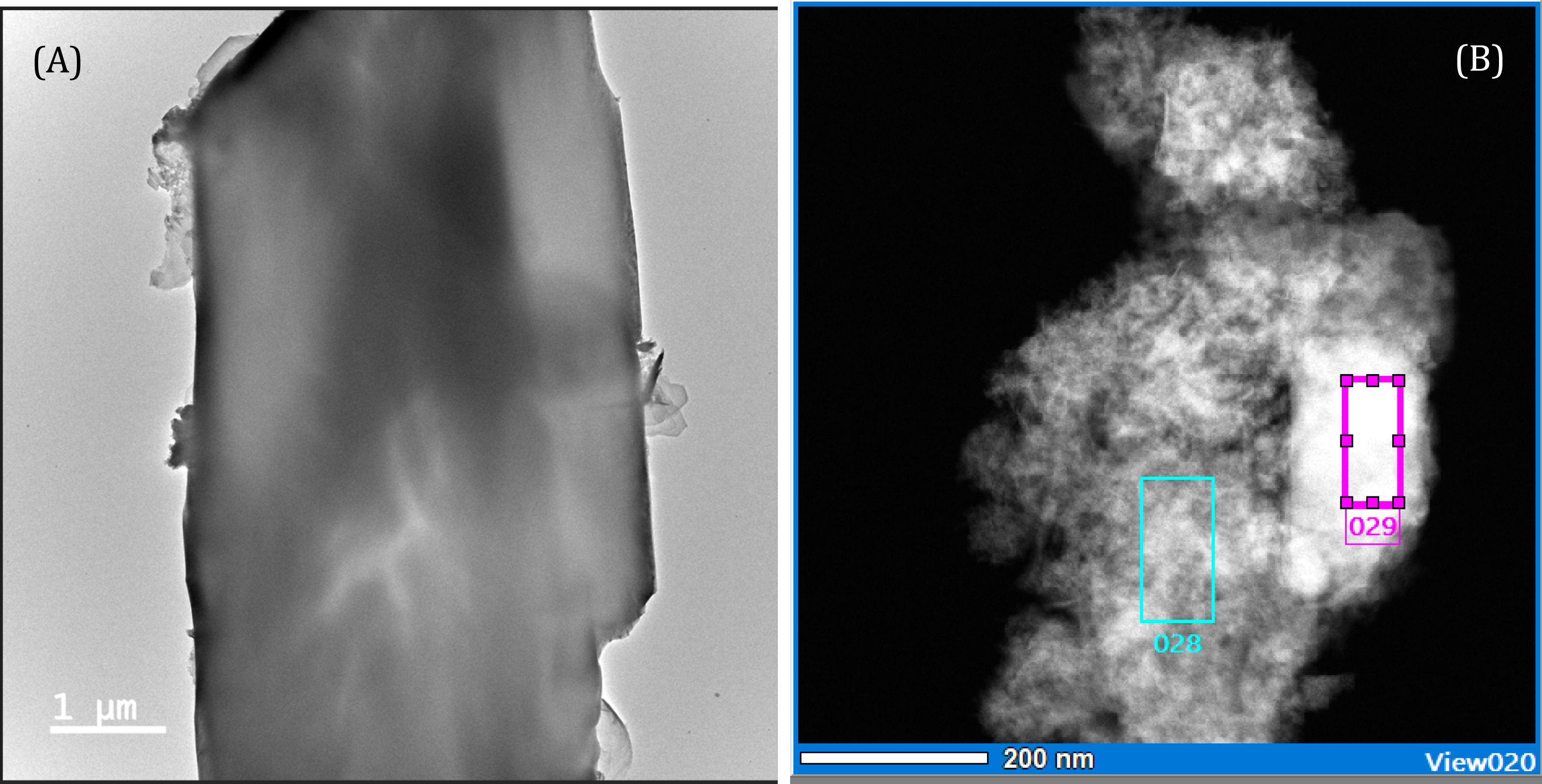
TEM microphotograph and location of semi-quantitative EDS analyses: (A) gypsum crystal and (B) iron-rich aggregates.
TEM–EDS analysis of gypsum crystal and iron-rich aggregates
Al (%) | Si (%) | S (%) | K (%) | Ca (%) | Fe (%) | Cu (%) | Zn (%) | |
---|---|---|---|---|---|---|---|---|
(A) Whole area | n.d | n.d | 46.59 | n.d | 52.52 | 0.3 | 0.1 | 0.49 |
(B) 28 | 8.37 | 3.77 | 5.33 | 0.17 | 0.91 | 60.50 | 7.40 | 13.56 |
(B) 29 | 7.77 | 9.37 | 2.38 | 0.98 | 1.30 | 61.17 | 5.63 | 11.40 |
3.2.2. Cu and Zn leaching behavior
Leaching tests of the sludge were performed first in shake flasks with low solid contents and with manual pH control in order to obtain basic information about the leaching kinetics. Preliminary tests conducted at solid contents of 1.1% and 0.75% with pH levels of 5.4 and 4.0, respectively, indicated that a pH below 4.0 is necessary to achieve substantial dissolution of target metals Zn and Cu. At these conditions, leaching yields were 0% for Cu and 24% for Zn at pH 5.4 and 8% for Cu and 37% for Zn at pH 4.0. For this reason, it was decided to perform experiments correcting manually the pH to 3.0 when it was higher than 3.5.
Table 5 shows the operating conditions at which the leaching tests in shake flasks were performed and the resulting Cu and Zn leaching yields. Figure 6 shows the Zn and Cu concentrations as well as the pH changes in time as a function of the leaching time for both tests lasting 24 h (T1 and T3). The pH increased between the monitoring points at fixed time intervals as a result of the leaching reactions, and it was necessary to manually decrease it with diluted H2SO4. In these experiments, the pH varied from 2.7 to 4.2. It is important to note that the “final pH” shown in Table 5 is the value measured at the last monitoring point without manual pH adjustment.
Operating conditions and results of shake-flask leaching tests
Leaching time (h) | Solid content (%) | Acid-to-solid ratio (g⋅kg−1) | Initial pH | Final pH | LYliquid (%) | ||
---|---|---|---|---|---|---|---|
Zn | Cu | ||||||
T1 | 24 | 0.68 | 106 | 2.7 | 3.6 | 75 | 66 |
T2 | 5.3 | 0.74 | 102 | 2.4 | 3.5 | 73 | 67 |
T3 | 24 | 0.79 | 118 | 3.4 | 3.6 | 75 | 70 |
T4 | 5.3 | 0.74 | 120 | 2.6 | 3.5 | 76 | 73 |
T5 | 5.3 | 0.73 | 125 | 3.2 | 3.5 | 77 | 71 |
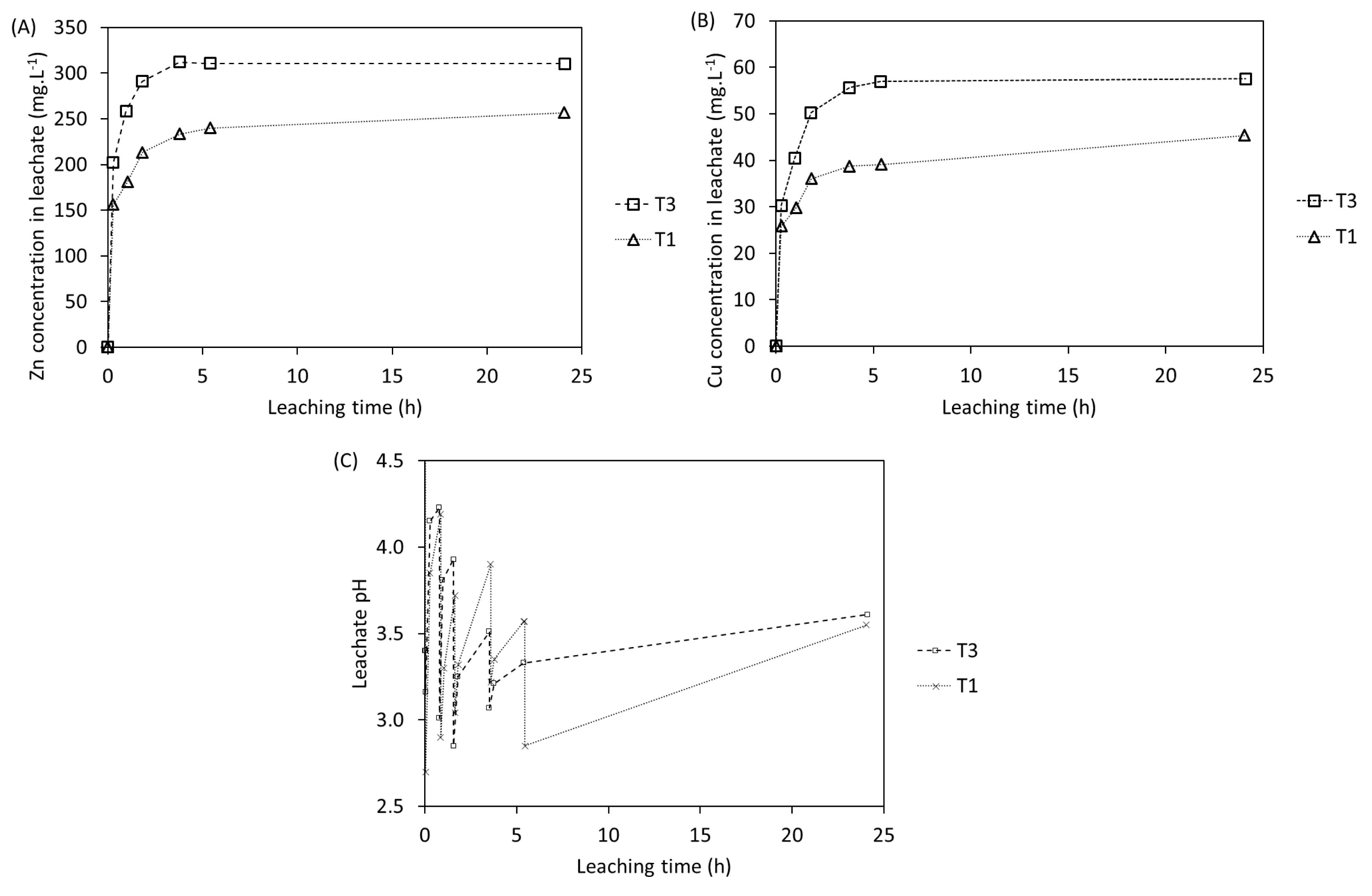
Concentrations of (A) Zn and (B) Cu and (C) leachate pH for tests with 24 h of duration in shake flasks.
The leaching curves follow a similar trend in both tests: (i) a very fast metal leaching during the first 0.25 h; (ii) a fast decrease in the leaching rate between 0.25 h and 4 h or 6 h; and (iii) a stabilization of the concentration at the end of the test. Moreover, it can be noted that for test T3, the concentrations of both Zn and Cu increase with time and reach a plateau around 310 mg⋅L−1 and 60 mg⋅L−1, respectively, after 4 h. However, it is not possible to say whether the concentration plateau was reached in test T1 since no samples between 6 h and 24 h were taken. Additionally, the final pH values of both tests are similar as well as the final leaching yields for both metals. Moreover, the pH curve shows that pH was manually decreased to slightly lower values in T3 than in T1 during the monitoring points between 2 h and 4 h. This resulted in a higher acid-to-solid ratio and a faster stabilization of the concentration of metals after 6 h. These results imply that the chemical reaction can be completed after only 6 h when the pH is kept low (<3.5) since the beginning of the reaction. Extrapolating this idea, adding more acid at the beginning of the reaction, and thus decreasing the pH at early stages of the reaction, may help to reduce the leaching time. Therefore, for the tests using STRs, it was decided to add the total required amount of acid at the beginning instead of controlling the pH.
In order to verify the repeatability of the leaching tests, three leaching tests in 0.5 L STR were carried out under very similar operating conditions (shown in Table 6). The concentrations of Zn and Cu as well as the leachate pH are depicted in Figure 7. It is important to highlight that for these tests, the total amount of acid necessary to reach the required acid-to-solid ratio in each reactor was added at the beginning of the experiment. The leaching behavior of the metals follows the same trend as in the shake-flask tests previously presented, confirming that 6 h is sufficient to reach an equilibrium in Zn and Cu concentrations under the conditions of the test. One can note that the pH also follows a similar trend. The final pH depends not only on the acid-to-solid ratio used but also on the solid content. A notable pH difference was observed for R3 compared to R1 and R2. Although the acid-to-solid ratio for R3 (153 g⋅kg−1) was slightly lower than that for R1 and R2 (157 g⋅kg−1), this difference seems insufficient to fully explain the pH discrepancy. It is possible that minor variations in the initial conditions or inhomogeneities within the sludge samples influenced the pH results. The results show that even with slight variations in the acid-to-solid ratio, the relative uncertainties of the leaching yield are 2 and 3% for Zn and Cu, respectively.
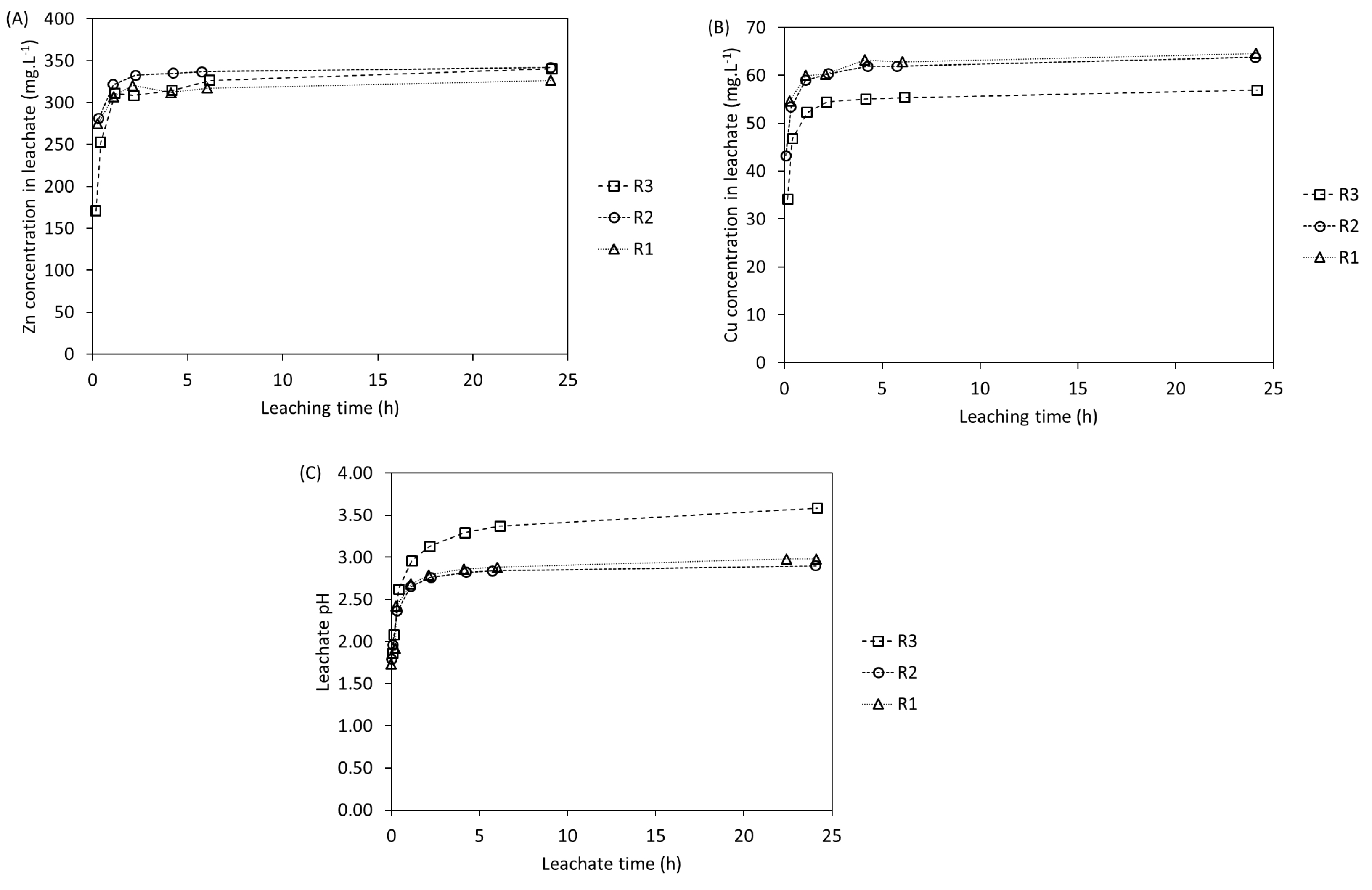
Concentrations of (A) Zn and (B) Cu and (C) leachate pH in 0.5 L STR tests.
Operating conditions and results of 0.5 L STR leaching tests
Solid content (%) | Acid-to-solid ratio (g⋅kg−1) | Initial pH | Final pH | Leaching yield (% liquid phase) | ||
---|---|---|---|---|---|---|
Zn | Cu | |||||
R1 | 0.72 | 157 | 1.7 | 3.0 | 78 | 80 |
R2 | 0.77 | 157 | 1.8 | 2.9 | 75 | 78 |
R3 | 0.70 | 153 | 1.9 | 3.6 | 79 | 74 |
Average | 77 | 77 | ||||
Std. deviation | 2 | 3 |
3.2.3. Effect of acid-to-solid ratio on leaching time and efficiency
As shown in Table 5, several acid-to-solid ratios were tested in 250 mL shake-flask experiments. The results are depicted in Figure 8. One can note that higher acid-to-solid ratios resulted in faster leaching rates during the first two hours. Moreover, the maximum leaching yield plateau is reached between 1 h and 2 h for both metals Zn and Cu, using an acid-to-solid ratio of 125 g⋅kg−1 (T5). However, regardless of the acid-to-solid ratio, we consistently observe incomplete dissolution (with a maximum leaching yield of approximately 77% for Zn and 75% for Cu) in these tests.
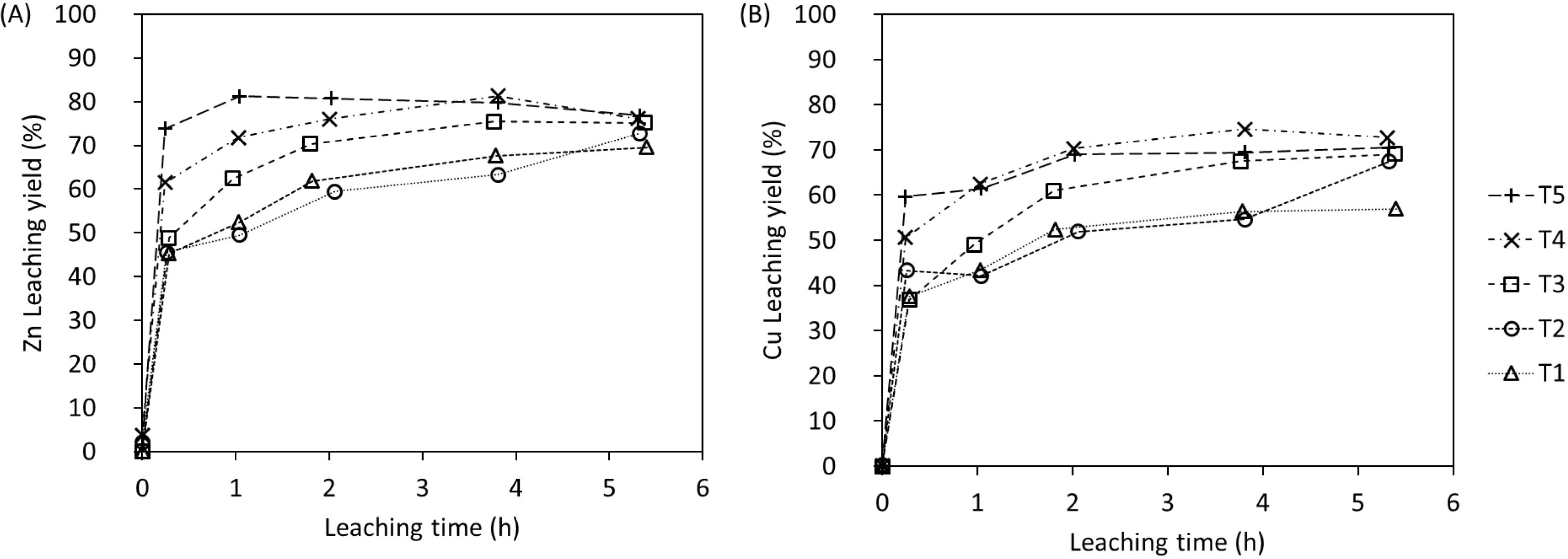
(A) Zn and (B) Cu leaching yields (LYliquid) for tests in shake flasks.
Experiments at different acid-to-solid ratios with low solid contents (between 0.6% and 1.3%) were carried out in 250 mL shake flasks, whereas 2 L reactors were used for higher acid-to-solid ratios with a solid ratio of 0.7% m/m at reaction times of 6 h and 24 h. The results are all depicted in Figure 9. They show that the leaching yield increased with acid-to-solid ratio up to about 250 g⋅kg−1 for both Zn and Cu, regardless of the experimental setup used. Further increases in the acid-to-solid ratio to 350 g⋅kg−1 and 450 g⋅kg−1 did not significantly increase the maximum leaching yield obtained, which was 90% for Cu and 84% for Zn.
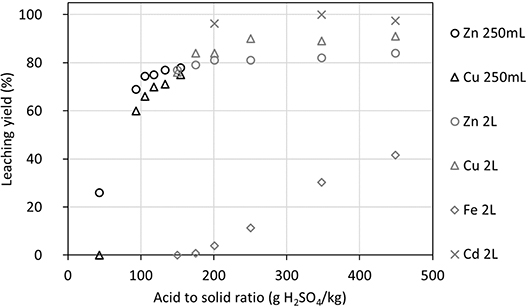
Metal leaching yields (LYliquid) at different acid-to-solid ratios in shake-flask tests and STRs for low solid contents (from 0.7% to 1.3% m/m).
The Fe leaching also increases with acid-to-solid ratio, and it becomes significant above 200 g⋅kg−1. This may be due to the dissolution of iron oxyhydroxides, such as ferrihydrite, caused by the low pH values (<3.0) obtained at the beginning of the experiments using high acid-to-solid ratios [29]. The initial pH (before solid addition) and the final pH at different acid-to-solid ratios in STRs for low solid contents (from 0.7% to 1.3% m/m) are presented in Supplementary Material Figure S5. One can note that the higher the acid-to-solid ratio, the lower the initial and final pH values. In the four reactors where Cd concentrations were measured, the leaching efficiency ranged from 96% to 100% for all acid-to-solid ratios tested (values of 200 g⋅kg−1 or higher as presented in Supplementary Material Table S1).
Experiments in 2 L reactors with a solid content of 2.9% at different acid-to-solid ratios with a reaction time of 24 h were performed to investigate the influence of acid-to-solid ratio on residue composition and on metal leaching yields compared to leaching tests at lower solid contents. Figure 10A shows the resulting leaching yields of these tests and Figure 10B shows the resulting Zn and Cu concentrations in the residues after leaching. An increase in acid-to-solid ratio from 200 to 450 g/kg resulted in an increase in dissolution rates of Cu from 86% to 93% and Zn from 82% to 92%.
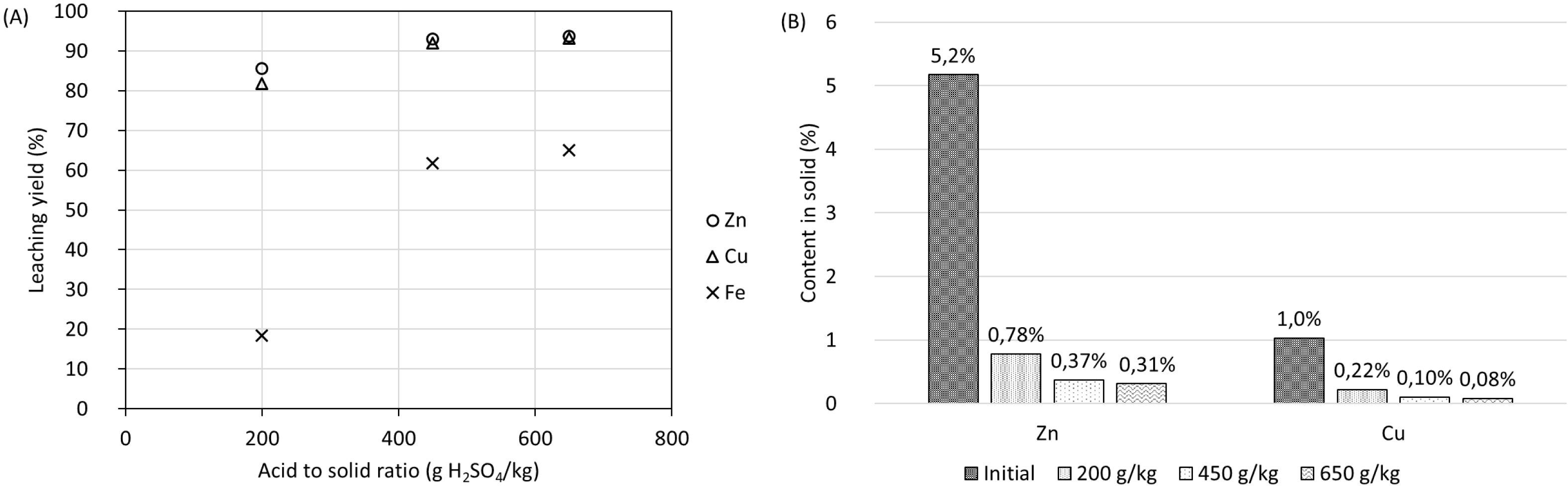
(A) Metal leaching yields (LYsolid) and (B) metal contents in solid residue at different acid-to-solid ratios with a solid content of 2.9% m/m.
An augmentation of the acid-to-solid ratio to 650 g⋅kg−1 did not have a visible impact on the leaching yield of Cu and Zn compared to an acid-to-solid ratio of 450 g⋅kg−1. On the other hand, the Fe leaching yield increased significantly when the acid-to-solid ratio increased from 200 g⋅kg−1 to 450 g⋅kg−1 and, as for Zn and Cu, it remained almost unchanged with a further increase in this parameter to 650 g⋅kg−1. The content in the leaching residue was reduced from 5.2% to 0.78% for Zn and from 1.0% to 0.22% for Cu, using an acid-to-solid ratio of 200 g⋅kg−1. For the tests using an acid-to-solid ratio of 650 g⋅kg−1, the Zn content in the leaching residue was 0.31% while the Cu content was 0.08%. These results demonstrate the limited effect of increasing significantly the acid-to-solid ratio on Zn and Cu leaching efficiencies for values higher than 200 g⋅kg−1.
3.2.4. Effect of solid content on leaching yield
Another set of experiments was performed in which the acid-to-solid ratio was fixed at 200 g⋅kg−1 (Figure 11) to assess the influence of solid content on leaching yields. In this case, an increase in solid content from 2.9% to 4.5% appeared to enhance the leaching efficiency for both metals. Further increasing this value to about 8.6% did not significantly influence the leaching yield. However, with a solid content of 16%, a leaching efficiency decrease is observed. Moreover, the variations in the leaching efficiency of these metals were also reflected in the metal content in the leaching residue.
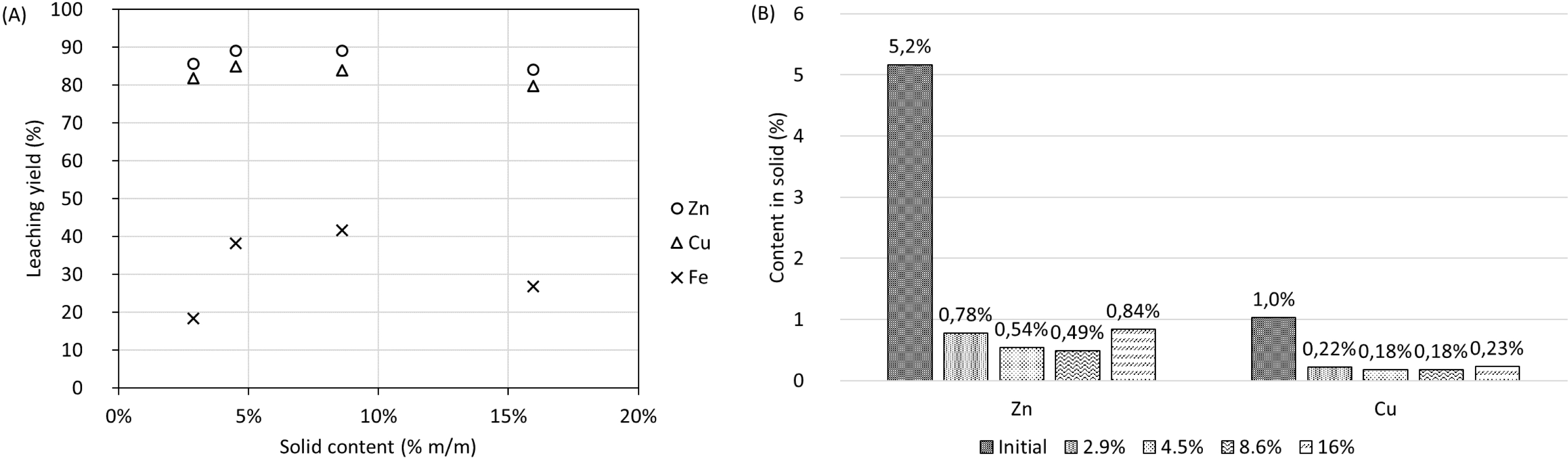
(A) Metal leaching yields (LYsolid) and (B) metal contents in solid residue at different solid contents at an acid-to-solid ratio of 200 g H2SO4⋅kg−1.
The results of these experiments suggest that the leaching efficiency of metals might have a positive correlation with the solid content up to 4.5%. However, further increases beyond 8.6% values could have a slightly negative effect on the leaching yields of Cu and Zn but a more substantial effect for Fe. Given the small variations observed and the limited number of data points (only two up to 4.5%) without replicates, these results should be interpreted with caution. Further statistical confirmation with replicates and more data points would be necessary to validate these findings.
Throughout the leaching experiments, the final calcium concentrations were consistently measured between 440 and 570 mg⋅L−1. These concentrations are close to or moderately lower than the Ca concentration of an aqueous solution in equilibrium with gypsum under standard conditions. Consequently, the dissolution rates of calcium were predominantly determined by the solid content, resulting in a wide range of leaching yields from 4% (at a solid content of 9.4%) to 64% (at a solid content of 0.7%) as presented in Supplementary Figure S6. There also appears to be a minor unknown phenomenon decreasing Ca concentration at lower pH.
3.2.5. Effect of temperature on leaching yield
The effect of temperature on metal leaching efficiency was also studied with an acid-to-solid ratio of 200 g⋅kg−1, a solid content of 2.9%, and a reaction time of 24 h. Figure 12 shows the Zn and Cu leaching yields as well as the Fe concentration in the leachate at 22 °C, 40 °C, and 60 °C. One can observe that by increasing the temperature from 22 °C to 40 °C, it was possible to increase both Zn and Cu leaching yields by respectively 2 and 4 percentage points (pp) at these conditions. However, no significant enhancement of efficiency is observed if the temperature is further increased to 60 °C. It is interesting to observe that the Fe concentration in the leachate decreases considerably as the temperature increases. It is known that Fe(III) can precipitate even at low pH values in the form of jarosite (KFe3(SO4)2(OH)6) or schwertmannite (Fe8O8(OH)6(SO4)⋅nH2O) and that this phenomenon is favored by the increase in temperature [34].
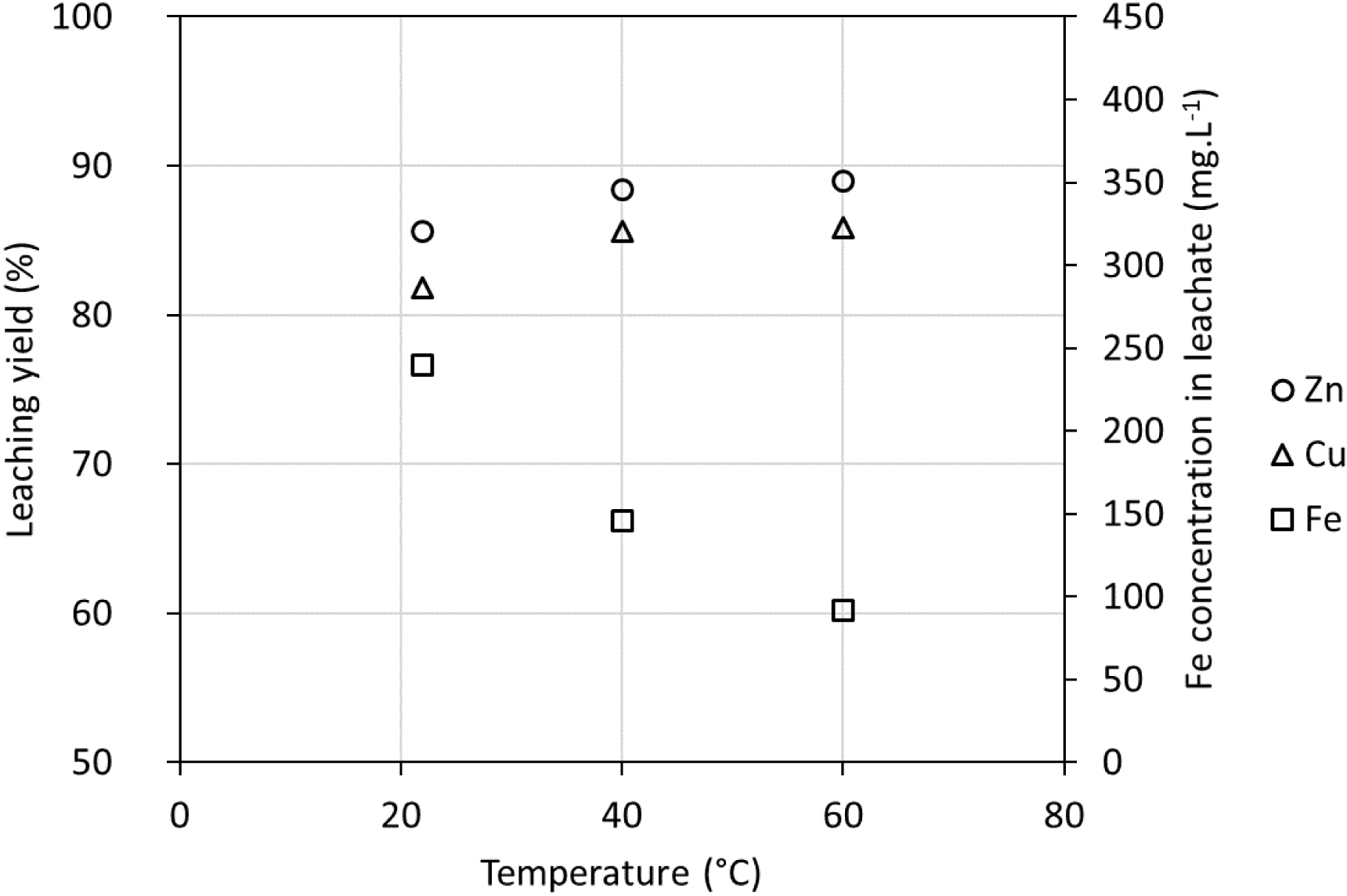
Metal leaching yields (LYsolid) at different temperatures using 200 g H2SO4/kg and 2.9% m/m of solids after 24 h.
4. Discussion
4.1. Implication of mineralogy on metal leaching behavior
A common result for all the leaching tests performed in this study is the presence of a concentration plateau for Zn and Cu at the end of the experiments, in general after 6 h, which corresponds to an incomplete leaching of these metals. The parametric study aimed at improving the leaching kinetics, which resulted in slightly higher leaching yields. However, it is clear that there is a limitation regarding the maximum leaching efficiency achieved at the conditions tested, which translates into an incomplete removal of Cu and Zn from the sludge. Nevertheless, introducing the entire acid quantity at the beginning of the reaction, rather than having a constant pH in the system, improved the leaching kinetics and yields for the same amount of acid. This implies that having a higher acidic environment at the early stages of the reaction is beneficial for metal leaching. Several hypotheses can explain these observations. Our first hypothesis is that a small proportion of Cu and Zn are embedded in the amorphous iron mineral. This is based on the limited evidence of Zn- and Cu-rich mineral phases in the sludge (excepting few delafossite crystals identified for Cu but which also contain Fe).
Figure 13 plots the correlations between Zn and Cu leaching yields and Fe leaching yields. A positive linear correlation was found for both Zn (R2 = 0.9161) and Cu (R2 = 0.9025) at 22 °C in 2 L reactors. Interestingly, for most experiments, the increases in metal leaching yields over 85% are observed for conditions involving high acid-to-solid ratios (>250 g⋅kg−1) or moderate-to-high solid contents (>2.9%). These conditions imply a very low pH (<1.7) at the beginning of the experiments, which caused the partial dissolution of Fe compounds.
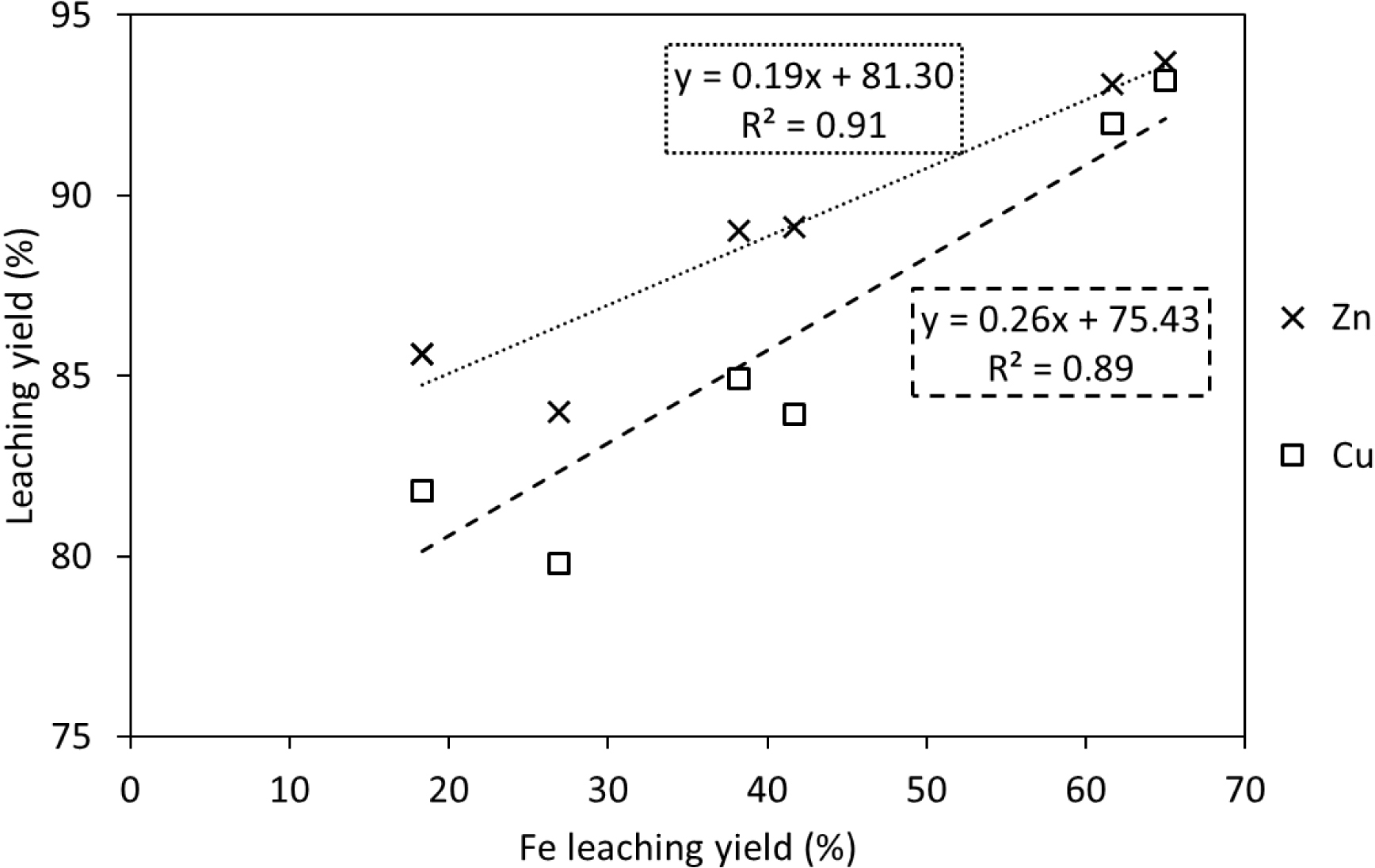
Correlation between targeted metal leaching yields and Fe leaching yields for experiments at 22 °C in 2 L reactors.
The maximum leaching yield obtained in this study was 94% for Zn and 93% for Cu at a solid content of 2.9% and an acid-to-solid ratio of 650 g⋅kg−1. However, when acid-to-solid ratios are higher than 200 g⋅kg−1, the improvement in both Cu and Zn leaching efficiencies is limited since a significant part of the acid added reacts with iron oxyhydroxides such as the ferrihydrite according to Equation (7) [33]:
(7) |
Besides, lower initial pH values obtained at high acid-to-solid ratios can also increase the solubility of the gypsum present in significant quantities in the sludge. Gypsum dissolved according to Equation (8) with a solubility product in water (Ksp) of 2.58 × 10−5 [35]:
(8) |
(9) |
(10) |
Due to the absence of specific literature detailing the acid leaching reaction of delafossite with sulfuric acid but knowing that in delafossite, iron is trivalent while copper is monovalent [37], we have proposed a plausible chemical reaction balanced stoichiometrically according to Equation (11).
(11) |
4.2. Implications in a potential industrial process for the valorization of sludge
The results of this study indicate the feasibility of selectively leaching Zn, Cu, and Cd from lime treatment sludge, particularly when compared to Fe, which is a predominant component of sludge. This is supported by the leaching tests in 2 L reactors at an acid-to-solid ratio of 175 g⋅kg−1, which demonstrated leaching yields of 84% for Cu and 79% for Zn and complete leaching of Cd while keeping the leaching yield for Fe below 1% as detailed in Figure 9.
The rise in temperature from 22 °C to 40 °C can also be a means to augment both Zn and Cu dissolution. It also decreases the Fe concentration in the leachate due to the precipitation of Fe oxyhydroxysulfates, which is favored at higher temperatures. Nonetheless, this would imply heating the reactors, which will influence the operating costs. Given the little gain regarding Zn and Cu leaching yields at 40 °C compared to ambient temperature, the implementation of heated reactors with temperature control might not be viable from an economic and environmental point of view. Nevertheless, this option should be further studied.
On the other hand, experiments show that it is possible that a high solid content in the reactor (16%) caused solid–liquid mass transfer limitations, which produced lower leaching yields than those found at lower solid contents. High solid contents can lead to increased viscosity and reduced mixing efficiency, hampering mass transfer between the solid phase and the leachate. This can limit the accessibility of the leachate to Cu and Zn minerals on the particles. Another factor that could explain this is the decreased ratio of surface area to volume: as the solid content increases, the available surface area for reaction per unit volume of the solution decreases, leading to lower reaction rates. An optimum solid content at which metal leaching is optimal should exist, probably between 5% and 15% m/m. In any case, more information is needed on this point to define whether the efficiency limitation at high solid contents is linked to the kinetics of the chemical reactions involved in mineral dissolution or is related to the hydrodynamic conditions of the reactor.
Nonetheless, at 16% solid content and an acid-to-solid ratio of 200 g⋅kg−1, the leachate contains 8.2 g⋅L−1 Zn, 1.5 g⋅L−1 Cu, and 1.7 g⋅L−1 Fe. These concentrations of Cu and Zn are sufficient for an economically viable downstream metal recovery process to be envisaged [24, 40]. Iron concentrations at this level are obviously an issue given the objective of selective leaching (as explained in Section 1), but as shown in Figure 9, a limited decrease in acid-to-solid ratio significantly decreases iron leaching. Nevertheless, the optimum operating conditions for leaching will have to be investigated in reactors fed in continuous mode.
5. Conclusion
Sludges produced from the lime treatment of AMD can sometimes represent a significant deposit of valuable metals. On the site presented in this study, the deposit of anthropogenic ore is estimated at 150 kt containing 1.3% Cu and 5.1% Zn. These contents of Cu and Zn are higher than those found in many deposits being mined today. The selective leaching process applied in this study allowed the leaching of more than 80% of Cu and Zn from the sludge under optimal operating conditions, which are defined between 5% m/m and 15% m/m of solid content with an acid-to-solid ratio between 150 and 200 g⋅kg−1 at room temperature (22 °C). Using more acid marginally increases the dissolution rates at the cost of much higher acid consumption linked to the dissolution of iron and therefore a loss of selectivity. Increasing the temperature to 40 °C improves the dissolution of Cu and Zn and decreases that of Fe, but its potential economic impact has not yet been estimated. The results of this work will serve to further develop the process by adding selective precipitation and purification steps. Moreover, the data acquired during this study will be used to carry out a preliminary economic assessment, including operating expenses, capital expenses, and return on investment.
Declaration of interests
The authors do not work for, advise, own shares in, or receive funds from any organization that could benefit from this article, and have declared no affiliations other than their research organizations.
Funding
This work has been funded by the Department for Mine Safety and Risk Prevention of BRGM: French Geological Survey.
Acknowledgments
The authors would like to thank the former and current project team members: Maxime Vignon, Rachel Seillier, Rany Ajami, Benoit Henry, Jérémy Engevin, Camille Becquet, Mohamed Djemil, Stéphane Touzelet, and Marine Respaut. This project has benefited from the expertise and facilities of Platform MACLE-CVL, which was co-funded by the European Union and Centre-Val de Loire Region (FEDER).
Vous devez vous connecter pour continuer.
S'authentifier