1 Introduction
Coumarins are one of the important classes of heterocyclic compounds whose synthesis has been the focus of attention from many organic and medicinal chemists. Many products, which contain the subunit of coumarin, exhibit useful and variant biological activities, such as inhibition of platelet aggregation [1], antibacterial [2] and anticancer [3] properties, inhibition of steroid 5α-reductase [4] and of HIV-1 protease [5]. Coumarins also serve as intermediates for the synthesis of fluorocoumarins, chromenes, coumarones, and 2-acylresorcinols [6].
Many routes have been used for the synthesis of coumarins, such as Baylis–Hillman [7], Knoevenagel [8–10], Perkin [11], Reformatsky [12], and Wittig reactions [13], but, between these routes, the Pechmann method is a much simple method for the synthesis of coumarins based on a two-component (phenol and β-ketoester) coupling under acid catalysis [14]. In the past decades, more than 60 methodologies with different catalysts were used for the Pechmann condensation. In the conventional method, concentrated sulfuric acid is used as the catalyst [15]. In addition, several other acid catalysts, including Lewis acids, such as InCl3 [16], BiCl3 [17], ZrCl4 [18], VCl3 [19], and Sm(NO3)3·6H2O [20], are known to affect this condensation. Butyl methylimidazolium ionic liquids also have been utilized as catalysts for this reaction [21–23], but these methods also generated strongly acidic wastes and highly expensive and non-recyclable reagents. To solve these problems, a number of heterogeneous alternatives, such as SBA-15-SO3H [24], Amberlyst-15 [25], montmorillonite clays [26–28], and other solid acids [29–32] have been employed for this purpose in the Pechmann condensation. Although these methods are improvements, most of them suffer from disadvantages, such as harsh reaction conditions, long reaction times, poor yields, poor selectivity, use of toxic or expensive reagents, and use of large amounts of catalyst. Thus, the searches for new reagents and methods that utilize ecofriendly protocols are still in demand.
In recent years, there has been considerable growth of interest in the catalysis of organic reactions by solid acid catalysts. Solid acids provide numerous opportunities for recovering and recycling from reaction environments; also, they can lead to improved processing steps, better process economics, and environmentally friendly industrial manufacturing. Amongst solid acids, metal oxides have been used extensively either as catalysts or as supports in conjunction with other active components for many industrial oxidation, reduction and acid–base-catalyzed reactions. Among semiconducting oxides, TiO2, due to its low cost and long-term stability, has been widely used as a solid acid catalyst in organic transformations, such as Friedel–Crafts alkylation of indoles [33], synthesis of bis(indolyl) methanes [34], Mannich synthesis of β-aminocarbonyls [35], and esterification of free fatty acids [36]. But traditional TiO2 has many limitations in the nature of its active sites, because TiO2 nanoparticles can lonely catalyze the organic reactions by their weak Lewis acidity, so with surface modification of TiO2 by acidic moieties, we can benefit from the dual acidity of titanium and acidic groups. To solve this problem, for the first time, we successfully prepared sulfonic acid-functionalized nanocrystalline titania (TiO2–Pr–SO3H) by modification of TiO2 with sulfonic acid moieties [37,38]. The preparation strategy for the nanoreactor is shown in Scheme 1. In our first report, we used this reagent as an efficient catalyst for the preparation of quinoxaline derivatives [37], our procedure provided better activity with high yields and turnover compared to the previously reported heterogeneous ones. Also, we used this reagent for the promotion of the N-Boc protection of amines successfully [38]. Herein and in continuation of the above-mentioned studies, we are reporting the promoting effect of TiO2–Pr–SO3H as a new catalyst for the preparation of coumarin derivatives (Scheme 2).

Preparation of nanocrystalline titania-based sulfonic acid (TiO2–Pr–SO3H).
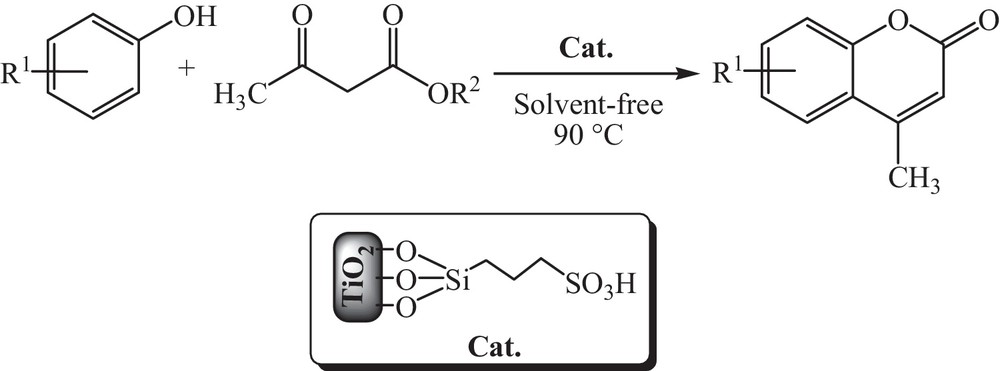
Preparation of coumarins in the presence of TiO2–Pr–SO3H.
2 Experimental
2.1 Materials
Chemicals were purchased from Merck (Darmstadt, Germany) and Sigma–Aldrich (St. Louis, MO, USA). All of the yields refer to the isolated products. Identification of the products was confirmed by comparison of their physical constants with those of authentic samples. The purity determination of the substrate and reaction monitoring were accompanied by thin-layer chromatography (TLC) on silica gel POLYGRAM SILG-UV254 (Carl Roth GmbH, Karlsruhe, Germany) plates.
2.2 Catalyst preparation
2.2.1 Synthesis of 3-mercaptopropyltitania
To 20 g of TiO2 (anatase, from Sigma–Aldrich) in dry toluene, 25 mL of (3-mercaptopropyl) trimethoxysilane were added, and the reaction mixture was refluxed for 24 h. After this period, the mixture was filtered to obtain 3-mercaptopropyltitania (MPT), which was washed with acetone and dried.
2.2.2 Oxidation of 3-mercaptopropyltitania
MPT was oxidized with 10 wt% H2O2 in methanol (20 mL) for 24 h at room temperature. The prepared sample was then treated with 1 N H2SO4 at ambient temperature for complete protonation, and then, the mixture was filtered and washed with H2O and acetone to obtain TiO2–Pr–SO3H catalyst (Scheme 1).
2.3 Catalyst characterization
The synthesized catalyst was characterized by Fourier transform–infrared spectroscopy (FT–IR), X-ray diffraction (XRD), scanning electron microscopy (SEM), transmission electron microscopy (TEM), and thermogravimetric analysis (TGA). Also, the acidic property of the synthesized catalyst was evaluated by the calculation of the Hammett acidity function [37,38].
2.4 General procedure
A mixture of substrate (1 mmol), methyl or ethyl acetoacetate (1 mmol) and TiO2–Pr–SO3H (8 mg) was taken in a 25-mL round bottomed flask equipped with a condenser. The mixture was heated in an oil bath at 90 °C under stirring and the reaction was monitored by TLC. After completion, the mixture was allowed to cool, ethyl acetate (5 mL) was added and the catalyst was recovered by filtration, washed with ethyl acetate (5 mL), dried and reused according to the procedure mentioned above. Evaporation of the solvent from the filtrate and recrystallization of the solid residue from hot ethanol afforded the requested coumarins in high yields. The results are given in Table 2 and spectral data and melting points are in good agreement with those reported in the literature [24–29].
Pechmann synthesis of coumarins in the presence of TiO2–Pr–SO3H.
Entry | R1 | R2 | Time (min) | Yielda (%) |
1 | 3-OH | Et | 32 | 93 |
2 | 3-OH | Me | 45 | 85 |
3 | 4-OH | Et | 30 | 92 |
4 | 2,3-(OH)2 | Et | 28 | 91 |
5 | 2,3-(OH)2 | Me | 33 | 95 |
6 | 3-OMe | Et | 24 | 86 |
7 | 3-OMe | Me | 38 | 92 |
8 | 3-Me | Et | 30 | 95 |
9 | 3-Me | Me | 60 | 90 |
10 | 3-Me-5-OH | Et | 26 | 93 |
11 | 3,5-(OH)2 | Et | 22 | 93 |
12 | 3,5-(OH)2 | Me | 23 | 90 |
13 | 2-naphthol | Et | 75 | 83 |
14 | 2-naphthol | Me | 90 | 81 |
a Isolated yields.
3 Results and discussion
In order to optimize the reaction conditions, we conducted the preparation of 4,7-dimethylcoumarin from the reaction of m-Cresol (1 mmol) and ethylacetoacetate (1 mmol) in the presence of various amount of TiO2–Pr–SO3H at different temperatures and in solventless media (Table 1). As shown in Table 1, the above-mentioned reaction in the absence of catalyst and in the presence of 20 mg bare TiO2 did not produce any product in 120 min at 100 °C (entries 1, 2). However, using 20 mg of TiO2–Pr–SO3H at 100 °C yielded 92% of 4,7-dimethylcoumarin in 30 min (entry 3). Decreasing the amount of catalyst show better results in the yield of the product and also decreasing the reaction temperature from 100 °C to 90 °C did not affect the duration of the reaction and the product yield (entry 9).
The Pechmann condensation reaction between m-Cresol and ethylacetoacetate in different conditions.
Entry | Catalyst | Catalyst (mg) | Temperature (°C) | Time (min) | Yield (%)a |
1 | — | — | 100 | 120 | NRb |
2 | TiO2 | 20 | 100 | 120 | trace |
3 | TiO2–Pr–SO3H | 20 | 100 | 30 | 92 |
4 | TiO2–Pr–SO3H | 15 | 100 | 30 | 90 |
5 | TiO2–Pr–SO3H | 10 | 100 | 30 | 93 |
6 | TiO2–Pr–SO3H | 8 | 100 | 30 | 95 |
7 | TiO2–Pr–SO3H | 5 | 100 | 45 | 80 |
8 | TiO2–Pr–SO3H | 8 | 95 | 30 | 90 |
9 | TiO2–Pr–SO3H | 8 | 90 | 30 | 95 |
10 | TiO2–Pr–SO3H | 8 | 80 | 60 | 75 |
a Isolated yield.
b No reaction.
After optimization of the reaction conditions, the reaction of other phenols with ethyl acetoacetate or methyl acetoacetate in the presence of TiO2–Pr–SO3H is carried out and the results are presented in Table 2. It can easily be seen that the Pechmann condensation proceeded smoothly under solvent-free conditions and gave good to high yields ranging from 81% to 95%. Many phenols, such as resorcinol, hydroquinone, pyrogallol, 3-methoxy phenol, m-Cresol, orcinol and phloroglucinol could be converted into the corresponding coumarins in high yields. As shown in Table 2, the reaction of 2-naphthol is slower than with other phenols and the yields of the products are fewer due to steric hindrance around the reaction centre (entries 13, 14). Phenols that have more than two hydroxyl groups in their structure are slightly more active compared to other phenols because hydroxyl groups activate the aromatic ring and their reaction is faster with higher yields (entries 4, 5, 11 and 12) [30]. It is noticeable that only one product can be obtained by these phenols, because the new produced ring deactivates other hydroxyl groups by resonance and the reaction cannot continue farther.
The possible mechanism for the preparation of coumarins in the presence of TiO2–Pr–SO3H as a promoter is shown in Scheme 3. On the basis of this mechanism, intermediate I is generated from the transesterification of phenol with ethyl acetoacetate or methyl acetoacetate. Then, Michael addition reaction generates a new ring to afford species II. Rearomatization leads to the formation of the coumarin skeleton III. At last stage, TiO2–Pr–SO3H can be regenerated by dehydration.
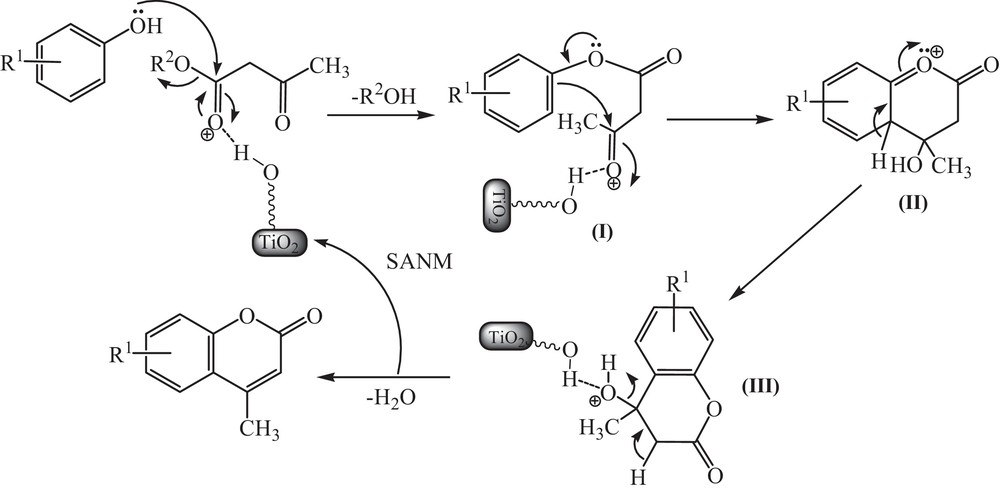
Proposed mechanism for the Pechmann condensation using TiO2–Pr–SO3H.
The recycling performance of TiO2–Pr–SO3H was investigated in the reaction of pyrogallol and ethyl acetoacetate. After performing one reaction under the conditions described in Table 1, the catalyst was recovered by filtration, washed with ethyl acetate (5 mL), dried at 100 °C and reused for a consecutive run under the same reaction conditions. Thus, after the first run, which gave the corresponding coumarin with 91% yield, and after recovery, the catalyst was subjected to a second reaction affording the product obtained with 89% yield; the average time for 15 consecutive runs was 25 min and 88.5% yield for all (Fig. 1). Also, TEM and SEM images of TiO2 and of the recycled catalyst demonstrated that the morphology of the catalyst did not change after the fifth run (Figs. 2 and 3). This reusability shows the high stability and turnover of solid titania-based sulfonic acid (TiO2–Pr–SO3H) under the conditions employed. It should be noted that the recyclability test was stopped after 15 runs.

(Color online.) Reusability of the catalyst in the synthesis of 7,8-dihydroxy-4-methylcoumarin.
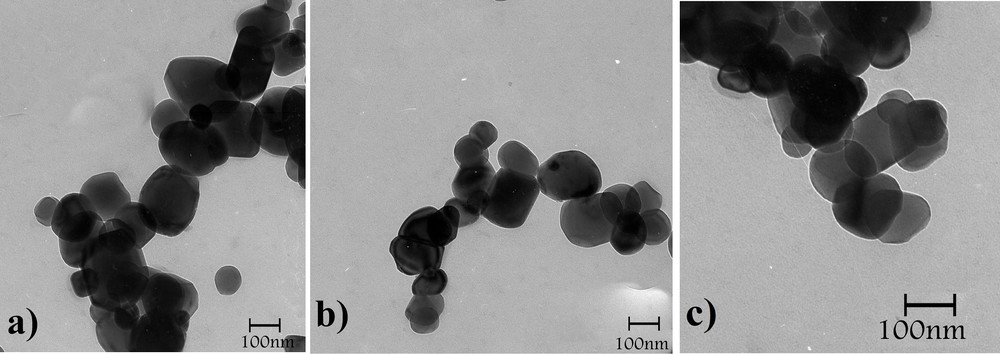
TEM images of fresh TiO2–Pr–SO3H (a) and TiO2–Pr–SO3H after the first (b) and fourth (c) runs.
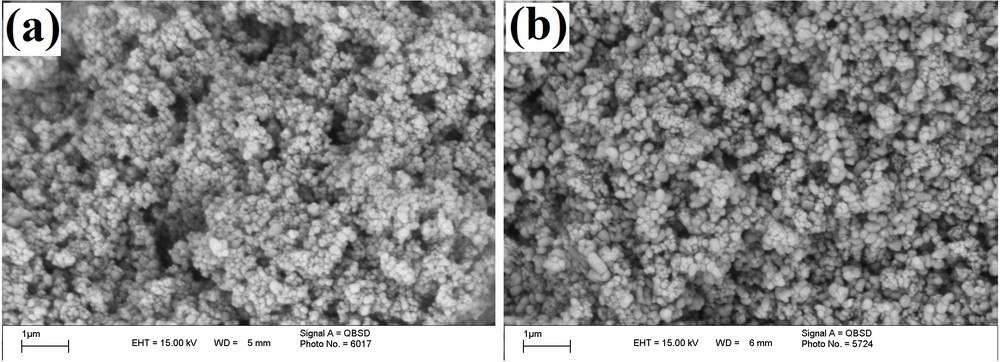
SEM images of fresh TiO2–Pr–SO3H (a) and TiO2–Pr–SO3H after the fourth (b) run.
To illustrate the efficiency of the present method, Table 3 compares our result in the synthesis of 7-hydroxy-4-methylcoumarin with the same results reported by the relevant reagents in the literature. By comparing with different homogeneous Lewis acid catalysts [16–20], ionic liquids [22,30] and other solid acids with different supports such as montmorillonites [27], polymers [31] and silica [32], TiO2–Pr–SO3H give the 7-hydroxy-4-methylcoumarin with using a lower amount of catalyst and with an excellent yield. Also, our synthesized catalyst can be reused 14 times without noticeable decrease in its catalytic activity (Table 3, last column).
Compared performance of various catalysts in the synthesis of 7-hydroxy-4-methylcoumarin.
Catalyst | Catalyst loading (mg) | Reaction Temp. (°C) | Time (min) | Yield (%) | Time of runsa |
TiO2–Pr–SO3H (this work) | 8 | 90 | 32 | 93 | 15 |
InCl3 [16] | 22.2 | Reflux in 65 °C under N2 | 30 | 98 | – |
BiCl3 [17] | 15.8 | 75 | 60 | 92 | – |
ZrCl4 [18] | 24 | RT | 5 | 92 | – |
VCl3 [19] | 15.8 | 50–55 | 120 | 92 | – |
Sm(NO3)3·6H2O [20] | 24 | Reflux in 80 °C | 20 | 98 | – |
Chloroaluminate [22] | 265 | 130 | 35 | 90 | – |
Mont-K10 [27] | 72 | 150 | 240 | 96 | 5 |
Mont-KSF [27] | 72 | 150 | 300 | 88 | 5 |
[Msim]HSO4b [30] | 25 | 40 | 25 | 94 | 5 |
PEG-SO3Hc [31] | 11 | 80 | 10 | 91 | 3 |
Silica-bonded S-sulfonic acid [32] | 100 | 80 | 15 | 89 | 5 |
a For one reaction.
b Msim = 3-methyl-1-sulfonic acid imidazolium.
c With methylacetoacetate as β-keto ester.
4 Conclusion
In conclusion, in this article, we have reported the applicability of a new catalyst for the synthesis of coumarins via the Pechmann condensation of phenols with methyl or ethyl acetoacetate in the absence of solvent. Our methodology has several advantages: it is green by avoiding toxic catalysts and traditional solvents, the catalyst is very cheap, it proceeds with high reaction rates, affording excellent yields, there is no side reaction, the catalyst is easy to prepare and to handle, it can be effectively recovered and reused with a high turnover rate, it needs only a lower loading and a simple experimental procedure. Further work to explore this novel catalyst in other organic transformations is in progress.
Vous devez vous connecter pour continuer.
S'authentifier