1. Introduction
Lithium is a non-substitutable element of Li-ion batteries (LIBs) whose technology is indispensable in electromobility and energy transition. The worldwide usage for LIBs nowadays is about 700 GWh and is expected to increase in the next decade to around 4.7 TWh. The lithium demand for LIBs represents 60–66% of the market and is anticipated to rise to 95% by 2030. To satisfy this demand, around 120 to 150 new battery factories should be built around the globe [1]. Currently, the main supply of lithium are primary sources from Australia and Latin America. Primary sources include ores (pegmantite and granite) and salted waters such as continental and geothermal brines, volcano sediments, and sea water. Lithium content tends to be higher in mineral ore deposits compared to salted waters. However, access to these deposits is expensive since they must be mined from hard rock formations. Lithium extraction from continental brines is extremely energy-intensive, as the evaporation process in ponds can take up to 24 months. Additionally, the water consumption stands at 800 m3 per ton of lithium carbonate. Geothermal brines represent just 3% of the global lithium reservoirs with no significant commercial plans to exploit these reserves. Today, lithium extraction from seawater remains in the research phase mainly because researchers are exploring various methods to elevate lithium concentration in seawater, which typically ranges from 0.1 to 0.2 ppm [2].
Nowadays, world powers like eastern and western Europe, Russia, and some independent state members of the Commonwealth are developing projects to recover lithium by their own means and sources in order to gain lithium supply independence. Figure 1 illustrates the forecast of lithium production by country in comparison with lithium recovery from secondary sources. It shows that recycling represents a small fraction when compared with the larger volume of lithium obtained from primary sources. At present, only 5% of discarded batteries are recycled [3].
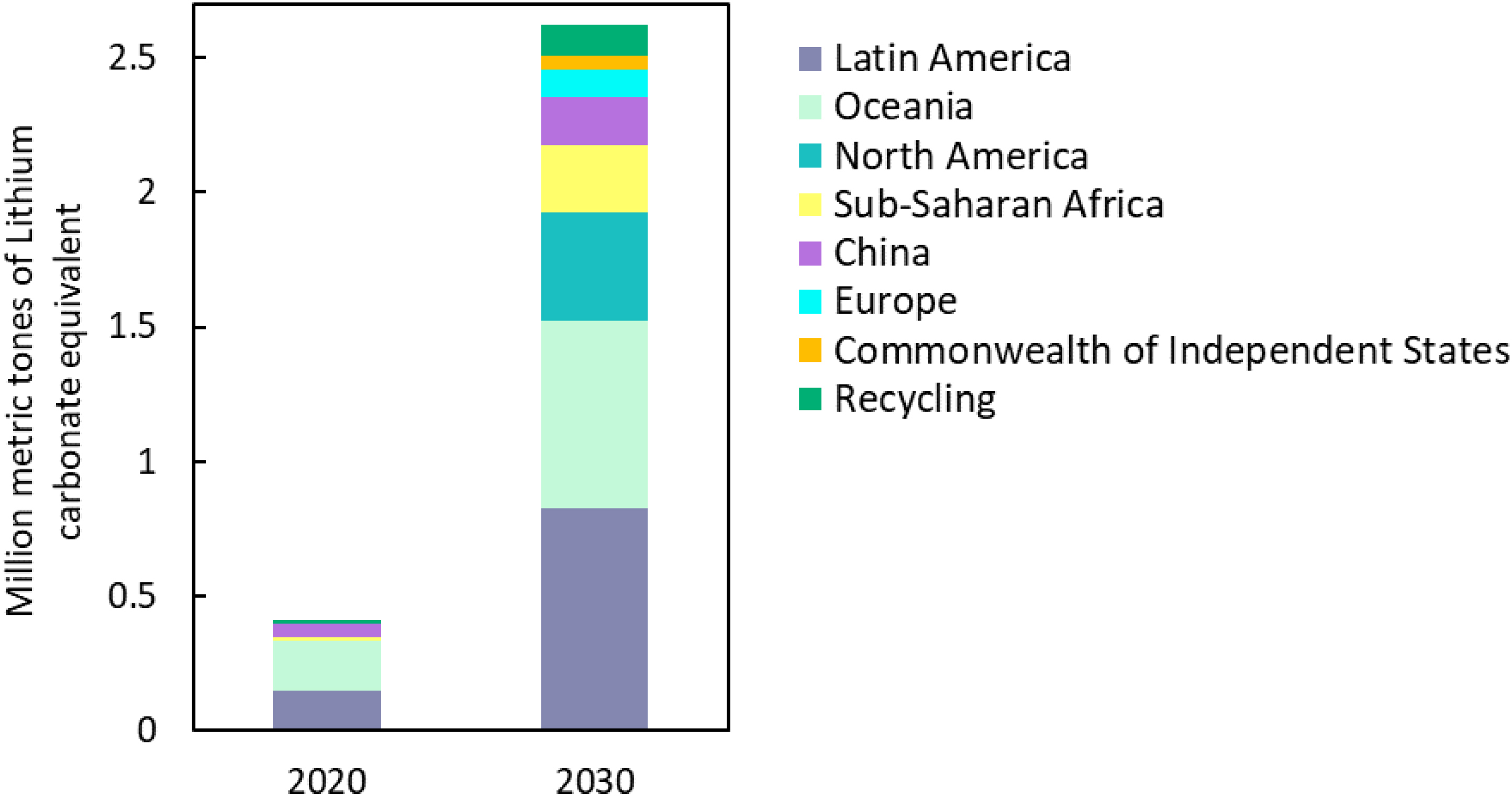
Global lithium product by source in million metric tons lithium carbonate equivalent. Data extracted from [1].
Nevertheless, while there is a slight improvement in the projected growth of lithium recycling from 2020 to 2030, it is still far from being able to compete with primary sources. Indeed the recycling industry faces numerous challenges, primarily related to waste management, engineering and commercialization. One of the technical difficulties lies in the design of LIBs. Batteries come in different sizes, forms, and chemistries, making the battery disassembly and materials separation extremely challenging. Therefore, scaling up pilot tests presents an arduous task, mainly because of the lack of regulation and standardization for the recovered materials [4]. Given the huge potential of battery recycling, ongoing advancements in recycling technologies are essential. This article aims to provide an overview of existing methods in metal recycling, including direct physical methods, pyrometallurgy, bio- and hydrometallurgy, with a specific focus on chemical precipitation.
2. Types of Li-ion batteries
LIBs are built with an anode, a cathode, an organic electrolyte, and a separator. The electrochemical properties of these batteries make them unique in the mobility market, characterized by their high specific and high-density energy. In addition, they can operate between 500 and 1000 cycles of charge-discharge, reaching at least 80% of their initial charge. On the other hand, LIBs require high-safety protocols during their handling to prevent overcharge and instability. At high temperatures and voltage, degradation may occur, and the potential fire hazard always exists [5]. Various cathode chemistries include commercial lithium cobalt oxide (LCO), lithium iron phosphate (LFO), lithium manganese oxide (LMO), lithium nickel cobalt aluminum oxide (NCA), and nickel manganese cobalt (NCM). Depending on their composition, different recycling methods are preferred. For instance, LCO, NCA, and NCM can be treated with hydrometallurgical, pyrometallurgical, and direct pathways, while LFP and LMO are usually directly recycled [6]. Table 1 provides an outlook for the battery market, showing the interaction between global demand, materials and battery prices. Notably, lithium and cobalt, recognized as critical raw materials, influence battery manufacturing costs.
3. Pre-treatment methods for spent Li-ion batteries
Typically, LIBs retain some residual energy inside and for that reason a 10 wt% NaCl solution is used to discharge them. For this, the battery is submerged entirely into the electrolytic solution, inducing a controlled short-circuit. Thus, the risk of explosion and the emission of toxic gases are prevented. Other discharge approaches include electronic techniques and the use of conductive liquids. Nevertheless, the NaCl solution has proved the best compromise between cost and efficiency [8, 9]. Once the battery is discharged, it undergoes separation and dismantling methods with the aim of separating the different materials according to their composition [9]. The choice of pre-treatment methods, whether mechanical, solvent-based, or involving calcination, depends on factors such as size, composition, and metal extraction processes. Pre-treatment methods can also be combined as needed.
Mechanical pre-treatment methods include crushing, sieving, particle size separation, flotation, gravity, and magnetic separation. Particle size separation aims to separate the minerals according to their particle size distribution after crushing and sieving. The studies with a commercial granulator showed that electrode materials have a cutoff diameter of less than 0.5 mm, copper pieces around 1–6 mm, and plastics greater than 6 mm [10]. The flotation method uses a chemical agent which follows the principles of hydrophilicity and hydrophobicity. This agent is able to trap hydrophobic metals inside bubbles of a foam and these will float to the surface while the hydrophilic ones will remain in the mixture [10]. During magnetic separation, steel pieces are recovered with almost 100% efficiency. Finally, gravity separation aims to separate different materials according to their density, for example, plastic, composites, and aluminum foils [10].
The solvent pre-treatment makes use of solutions and solvents to isolate active materials from the foils usually composed of copper or aluminum. This process essentially functions by dissolving the binder allowing to pull out the active materials [9].
The calcination pre-treatment aims to separate carbon and other organic material from the battery. The temperature range is 150 to 500 °C [9].
4. Methods of lithium extraction from spent Li-ion batteries
There are three main methods of recovering metals from LIBs: the bio- and hydrometallurgical, pyrometallurgical and direct recycling (Figure 2). These methods can also be combined or integrated for a more efficient metal recovery.
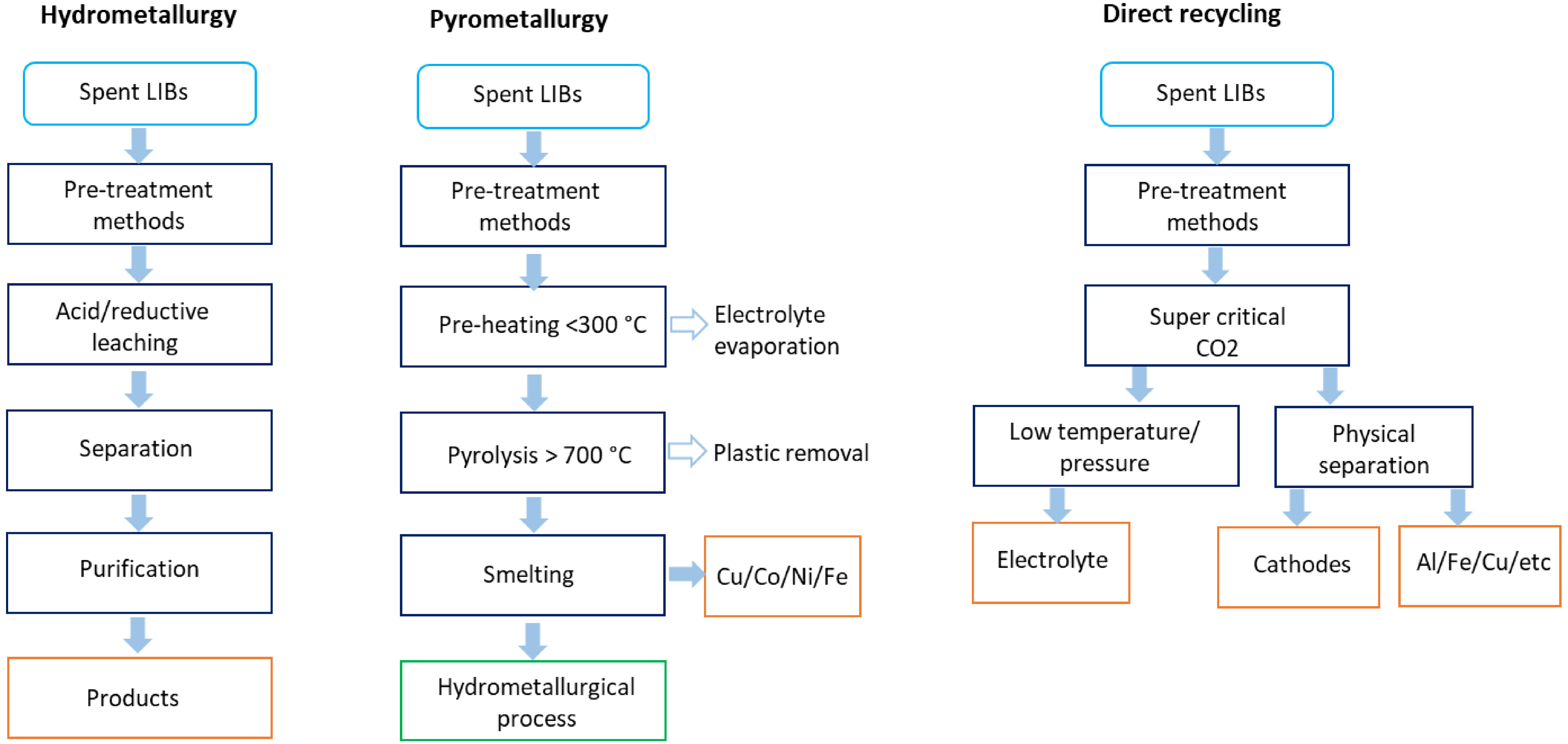
Methods of lithium extraction from spent lithium-ion batteries. Data extracted from [11].
Hydrometallurgy relies in extraction, purification, and recovery. Selective separation technologies are chosen according to the properties of products and impurities, requiring a leaching step [12]. While this method has low energy requirements and minimal gas emissions, wastewater treatment is essential [11]. In the bio-hydrometallurgy, bioleaching involves an interaction between microorganisms and metals for dissolution and then extraction. Bio-hydrometallurgy offers innovative contributions for a greener process [13].
The pyrometallurgical method involves the incineration and smelting of LIBs in a plasma arc furnace at temperatures above 700 °C. Metals such as copper, cobalt, iron, and nickel are recovered in the form of alloys, while plastics and all organic compounds are incinerated. Aluminum, manganese, silicon, calcium, lithium, and traces of iron are found in the slag, requiring a hydrometallurgical process for metal recovery [11, 14, 15] (Figure 2). Although a simple operation, it requires costly equipment, excessive energy and is polluting [12].
Lately there has been a growing exploration of the direct physical recycling process. This method begins with a mechanical pretreatment method leading to individual cells. Then, these cells undergo treatment using supercritical CO2, enabling the extraction and treatment of electrolytes. After reducing temperature and pressure, CO2 can be separated from the electrolytes. Finally, the cathode material can be reused (Figure 2). This method has demonstrated several advantages, including low energy consumption, a high recovery rate and it is environmentally friendly. Nevertheless, it has high operational and equipment requirements. Additionally, not all materials can be successfully recovered through this process [11], similar to the pyrometallurgical method which requires a hydrometallurgical method in order to recover metals effectively.
5. Hydrometallurgy
This section will provide a deep description of the hydrometallurgical process which is commonly combined with the pyrometallurgical process. This technique primarily involves two steps: leaching and purification. This method has a great worldwide industrial potential and is the predominant approach to extract lithium. Hydrometallurgy is more suitable in recycling lithium when LIBs have a single chemical composition [16].
5.1. Leaching process
The objective of leaching is to obtain metal ions in an aqueous solution from the cathodes of the spent LIBs. The mechanism involves the following steps: initially, the reagent diffuses and adheres to the material’s surface [17]. Then, an oxidoreduction reaction on the surface, results in the formation of highly soluble species. Reaction products detach from the surface and disperse (Figure 3). Choosing the right leaching agent is crucial to achieve high efficiency in the material dissolution. High selectivity towards the target metal is desired as well as the regeneration ability of the leaching agent. Leaching agents can be acids (inorganic or organic) or alkaline solutions. Acid leaching is the most common method since it can dissolve the cathode materials effectively. The most commonly used acids for leaching are hydrochloric acid, nitric acid, and sulfuric acid [8]. Sulfuric acid shows a non-oxidizing nature in contrast to HCl and HNO3. When HCl or HNO3 reacts with cathode materials, production of NOx or Cl2 gases is observed. Cl2 is hazardous for the environment as well as SOx and NOx. As a result, HCl is avoided because of its high cost and corrosive properties. Inorganic acids have demonstrated high efficiency for lithium and cobalt with rates of 98 and 95%, respectively [16].
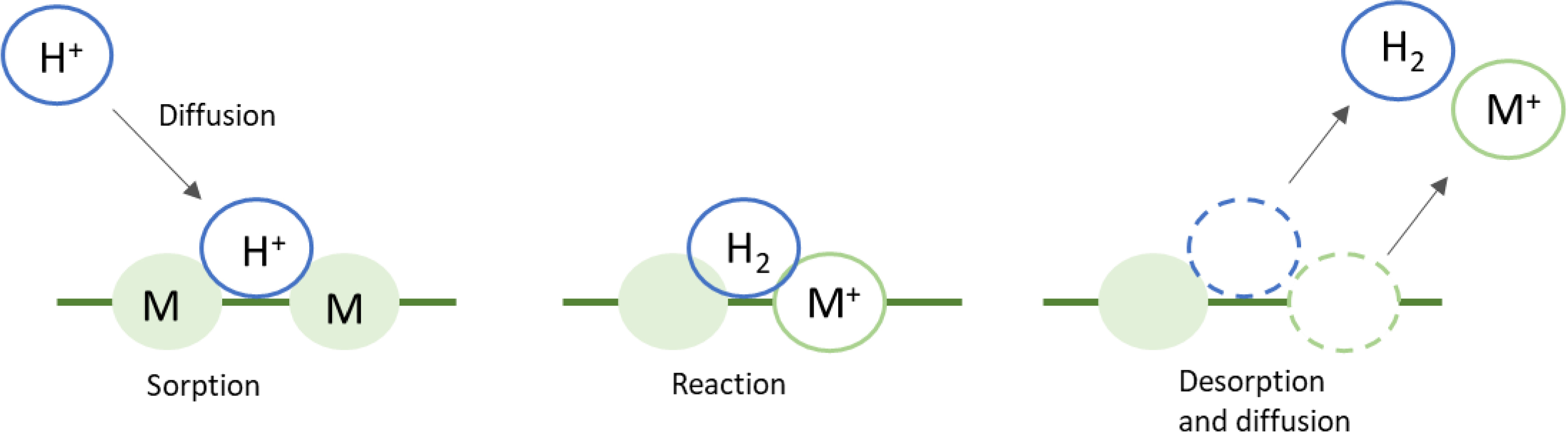
Mechanism of the leaching process of cathode materials from Li-ion batteries. Extracted from [17].
Table 2 shows various leaching agents reported in the literature, along with their corresponding leaching rates. The data indicate a consistent approximate yield of 99% for lithium, while the yield can vary from 70 to 90% for cobalt.
Research results for the highest leaching rates of spent Li-ion batteries in inorganic acids
Cathode materials | Leaching agent | T (°C) | S/L ratio (g/L) | Time (min) | Leaching rate (%) | Ref. |
---|---|---|---|---|---|---|
LCO | 2 M H2SO4 + 10 vol% H2O2 | 70 | 30 | 60 | Co 98.5 Li 99.8 |
[18] |
LCO | 2 M H2SO4 + 5 vol% H2O2 | 80 | 50 | 60 | Co ∼ 99 Li ∼ 99 |
[19] |
LCO | 1 M HNO3 + 1.7 vol% H2O2 | 75 | 10 | 30 | Co ∼ 99 Li ∼ 99 |
[20] |
LCO | 0.7 M H3PO4 + 4 vol% H2O2 | Co ∼ 99.7 Li ∼ 99.9 |
[21] | |||
LCO | 2 M H2SO4 + 5 vol% H2O2 | 75 | 100 | 60 | Co ∼ 70 Li ∼ 99.1 |
[22] |
The use of organic acids has been also explored, such as oxalic acid and citric acid among others. Organic acids exhibit notable characteristics such as their propensity for easy degradation, recyclability, and eco-friendliness. On the other hand, they are more expensive than the inorganic acids and their leaching rates are slower. As a result, the industry has not yet employed organic acids for the recovery of metals in spent LIBs [8].
Alkaline leaching is a well-known method in metal extraction, involving the interaction between hydroxide ions and metals. Sodium hydroxide and ammonium species are the most common leaching agents. Sodium hydroxide can dissolve the aluminum efficiently and it is slightly corrosive. Ammonia is used mainly in spent LIBs containing copper, cobalt, nickel, and zinc. Normally, for cathode leaching, a solution containing ammonium sulfite, ammonia, ammonium carbonate and deionized water is prepared. During the leaching process, ammonium carbonate acts as a buffer and ammonium sulfite serves as a reductant. Afterwards, ammonium sulfite converts nickel and cobalt from their insoluble high oxidation states of to their soluble lower oxidation states [8].
5.2. Purification process
The purification process aims to separate valuable metals from the spent LIB solution after the leaching process. This leaching solution includes elements such as iron, aluminum, copper, manganese, nickel, cobalt, and lithium. This process could include solvent extraction, electrochemical extraction, and chemical precipitation. To enhance metal recovery, these techniques usually are used in combination [8]. For example, the use of solvent extraction combined with chemical precipitation allows the selective separation of copper, nickel, and lithium through chemical precipitation, while cobalt and manganese are efficiently separated using solvent extraction.
5.2.1. Solvent extraction
Solvent extraction uses a two-phase system to separate lithium from the leached cathode material, resulting in an efficient method since it demonstrates to be highly selective for metal ions. This technique relies on relative solubility to separate ions from polar and non-polar liquid. Nonpolar extractants are mainly used to separate valuable metals such as cobalt, nickel, magnesium, and lithium. Common extractants include di-(2-ethylhexyl) phosphoric acid (D2EHPA), diethylhexyl phosphoric acid (DEHPA), bis-(2,4,4-tri-methyl-pentyl) phosphinic acid (Cyanex 272), trioctylamine (TOA), and 2-ethylhexyl phosphonic acid mono-2-ethylhexyl ester (PC-88A). In some cases, a mixture of two or more extractants is employed to enhance selectivity [8, 9]. Table 3 displays a compilation of solvent extraction processes conducted over recent years, employing various spent materials. The extraction efficiency and purity of Li2CO3 vary depending on the spent material and the extractant employed.
Research of solvent extraction process of spent Li-ion batteries (LIBs) in the literature [10]
Spent materials | Residue | Efficiency (%) | Purity (%) | Extractants | REF |
---|---|---|---|---|---|
LIB scraps | Li2CO3 | 80 | >98 | DEHPA Cyanex 272 | [23] |
LiCoO2 | Li2SO4 solution | Leaching 100 | >99.5 | PC-88A | [24] |
LiNi0.5Co0.2Mn0.3O2 | Li2CO3 | Leaching 94 | - | Cyanex 272 | [25] |
LIB scraps | Li2CO3 | 72 | 99.7 | DEHPA Cyanex 272 | [26] |
LiCoO2 | Li2CO3 | 86 | 74.2 | Cyphos II-101 | [27] |
5.2.2. Electrochemical extraction
Electrochemical deposition had demonstrated to be an effective method since it can separate the metals from a solution based on the potential difference between the electrodes. For example, Chu et al. [28] built a system using aluminum foil as cathode, the active material from the spent LIB as anode, and sulfuric acid as the electrolyte. Through electrolysis, a successful separation between the aluminum foil and the active material is achieved. The process can be explained as follows: copper enters the electrolyte as impurity and is electrodeposited on the cathode, while nickel, cobalt, and manganese remain undissolved. The aluminum foil remains insoluble within the solution [16]. This method proved to have an extraction efficiency for lithium ranging between 75–95% and the capability to extract other metals beyond Li2CO3. The recycled lithium exhibited a high purity level of 99%.
Other electrochemical methods extract lithium using a lithium-selective transmissive membrane where spent LIBs are placed in a system using a Li-ion–conductive ceramic solid electrolyte. When active material is placed in water, lithium in the charged cathode does not dissolve while the lithium in the anode dissolves in the water forming lithium hydroxide [9].
5.2.3. Chemical precipitation
Chemical precipitation is the most commonly used method for separating lithium from solutions after leaching the spent LIB cathodes. This method uses the pH-dependent difference of solubility in the active material to extract valuable metals. Chemical precipitation is used to remove ionic constituents from water by the addition of counterions to reduce solubility. Most metal are precipitated as hydroxides, sulfides, and carbonates [28]. Chemical precipitation generally involves simultaneous and rapid occurrence of nucleation, crystal growth, and other mechanisms, such as Ostwald ripening and agglomeration [29]. The main reactants include NaOH, Na3PO4 and Na2CO3 among others. They are used to precipitate valuable metals ions followed by lithium recovery, mainly in the form of Li2CO3 or Li3PO4 (Table 4). Li2CO3 is the most sought-after form of lithium as it consistently yields the highest purity levels.
Research of precipitation processes of spent Li-ion batteries (LIBs) in the literature
Spent materials | Residue | Efficiency (%) | Purity (wt%) | REF |
---|---|---|---|---|
LiCoO2 | Li2SO4 | 90 | - | [30] |
LIB scraps | LiF | 50 | >99 | [31] |
Cathode materials | Li2CO3 | 80 | 96.97 | [32] |
Cathode materials | Li2CO3 | 71 | - | [33] |
Mixed cathode materials | Li2CO3 | 80 | - | [34] |
LiNi0.3Co0.3Mn0.3O2 | Li2CO3 | Leaching 99.7 | - | [35] |
Cathode materials | Li3PO4 | 89 | - | [36] |
LiNi0.3Co0.3Mn0.3O2 | Li2CO3 | 98 | 99.9 | [37] |
LiFePO4 | Li3PO4 | 82.6 | 96.5 | [38] |
Cathode material and graphite | Li2CO3 | Leaching 99.9 | 99.4 | [39] |
LiFePO4 | Li2CO3 | 95.1 | 99.95 | [40] |
Cathode materials | Li2CO3 | >90 | 99.93 | [41] |
Cathode materials | Li3PO4 | 85.6 | - | [42] |
Anode | Li2CO3 | Leaching 100 | >99 | [43] |
LiNi0.3Co0.3Mn0.3O2 | Li2CO3 | Leaching 99 | - | [44] |
LiNi0.5Co0.2Mn0.3O2 | Li2CO3 | 76 | >99.5 | [45] |
LiFePO4 | Li2CO3 | 99.4 | - | [46] |
Cathode | Li2CO3 | 38 | >98.48 | [47] |
LiFePO4 | Li2CO3 | 80 | - | [48] |
LiNi0.5Co0.2Mn0.3O2 | Li2CO3 | 91.2 | 99 | [49] |
LiNixCo1−x −yMnyO2 | Li3PO4 | Leaching 99.1 | - | [50] |
5.3. Lithium precipitation in the form of Li2CO3
Carbonate precipitation is normally used in water treatment to reduce calcium hardness but nowadays it is a great option for lithium recovery from spent LIBs. It has been demonstrated that carbonate is able to decrease the solubility of some metals, while increasing that of others. The effect depends on the target metal and the pH at which the treatment is carried out [18, 51]. Lithium carbonate exhibits inverse solubility, thus the higher the temperature, the lower the residual content of dissolved lithium and therefore the higher the quantity of precipitated lithium carbonate [28, 52] (Figure 4).
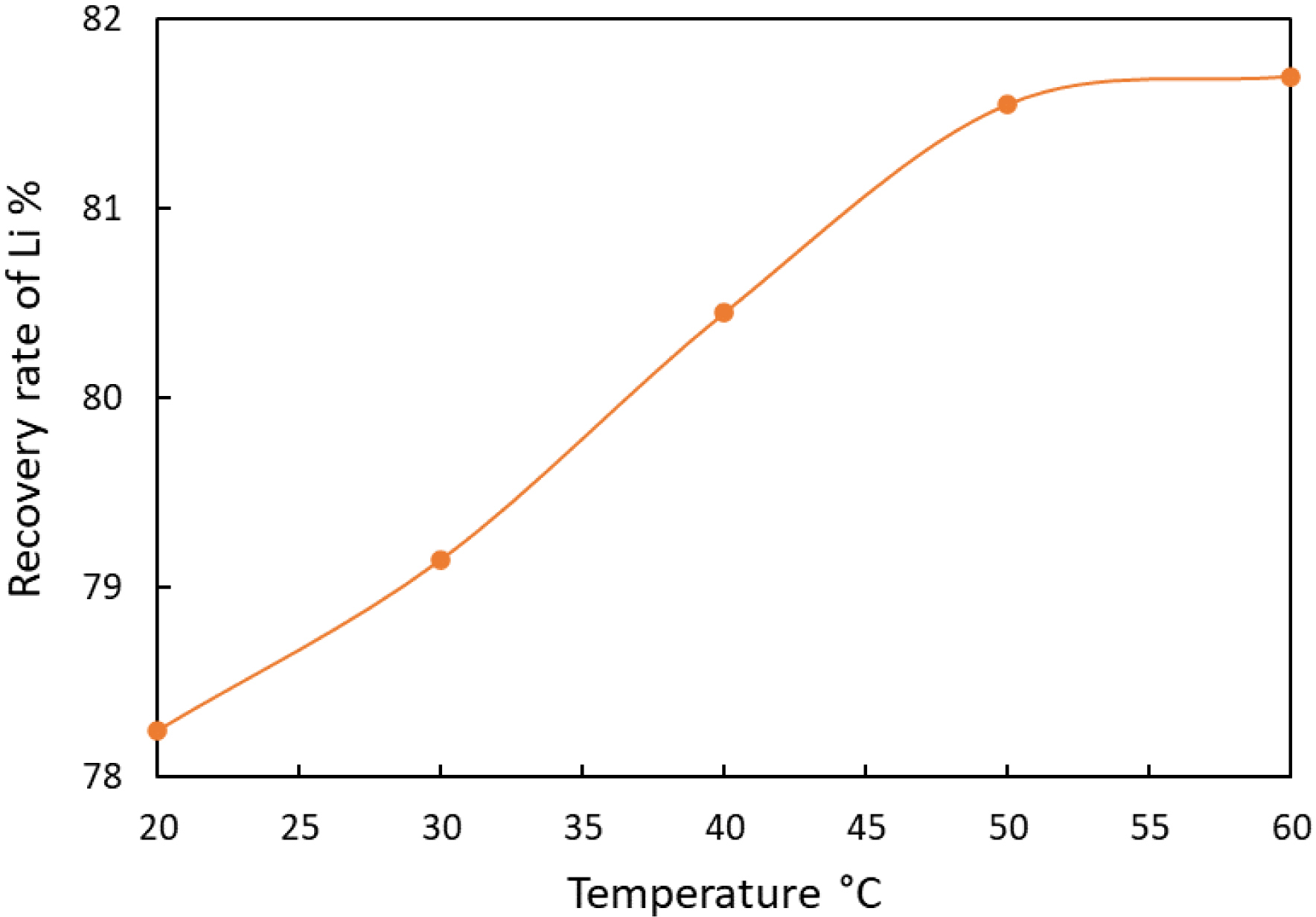
Evolution of the lithium recovery rate as a function of temperature. Data extracted from [34].
In the recycling industry, Li2CO3 is precipitated after a saturated solution of sodium carbonate is added into the mixture resulting from the leaching process. The precipitation reaction can be described as follows:
(1) |
The precipitation of Li2CO3 using carbon dioxide represents a promising and sustainable approach for lithium recovery. The carbonation process begins with the dissolution of CO2 in water:
(2) |
For precipitation to occur, the pH of the system should be alkaline, at least 8 and optimally higher than 10. This is mainly because the dominant species in the system shifts to
(3) |
(4) |
6. Conclusion
Nowadays, lithium recycling is becoming an economic, environmental, and governmental issue due to the growing demand of e-mobility and electronic devices. For that reason, finding novel routes in the development of greener and low-cost processes is indispensable in the recycling of Li-ion batteries (LIBs). The recycling industry has encountered numerous drawbacks and challenges in the extraction of valuable metals from LIBs. Because of this, secondary sources of lithium are currently considered as unreliable for its integration into the lithium supply chain. However, promising progress has been made in the past years with regards to recycling LIBs. Different treatments and processes are being explored and, among the methods studied, hydrometallurgy involving carbonate precipitation has proved to be the most affordable and eco-friendly approach for lithium extraction. Additionally, using CO2 not only produces a precipitate with superior purity but also plays a significant role in enhancing the sustainability of the process. Although this method offers several advantages, it is crucial to combine chemical precipitation with other techniques to enhance metal recovery yields. Further research should focus on improving and integrating hydrometallurgy with other technologies to advance the production of the next-generation batteries from recycled lithium.
Declaration of interests
The authors do not work for, advise, own shares in, or receive funds from any organization that could benefit from this article, and have declared no affiliations other than their research organizations.