Abridged English version
As announced in a previous paper [7], we present here an application of the methodology given there to estimate the energy yield of a system dedicated to producing ethanol from corn. In 2005, around 21 Mtep of transport fuel were made out of cereals or oil producing plants, to which the USA contributed 7.5 Mtep through the processing of corn into ethanol [18]. This production is increasing by 20% each year. The energy expenditure of this system is studied from the farm to the fuel station, through ethanol refining and transport. The raw data (direct energies and material consumption, the associated corn production, the different heat values and/or the external costs) are deduced from articles published on the topic [11,16,17,19–22] as well as technical documents [1,4,8,12,13,15,19,24] and reports from the US Departments of Agriculture and Energy [2,3,6,9,14].
Data for farms are reported for the nine States producing together more than 90% of ethanol, in 1991, 1996 and 2001. Data are processed to give the expenditure per corn mass unit from which expenditure per ethanol energy unit is deduced. The three main expenditures are transport fuel (less than 4% of ethanol value in 2001), grain drying (2.5%), and fertiliser application (from 12 to 22%, depending on the State). The last term is the most important, due to the cost of ammonia production and its large application rate. Some saving can be made by plant modernization, but recent refineries give values close to the theoretical yield. The drying process depends on meteorology and can increase costs up to 8.5%, as in 1996. Irrigation is seldom used except on one third of the corn harvest area in Nebraska, a State close to the western, arid part of USA. The cost to pump water from the aquifer was then about 29% of the ethanol energy value in 2001.
At the refinery, two processes are used to extract ethanol from corn grain, both based on enzymatic and fermentation steps. The two differ in the way they extract ethanol by-products. In the main process – the dry process – they are recovered after ethanol distillation and dried to make animal feed, whereas in the wet process the main constituents – oil, gluten meal – are separated during the first steps for more value-added uses. From the cost of each process established in [11] and from the part of each process deduced from the production of ethanol and its different by-products in 2005 [19], the average cost at the refinery in 2005 is found to be 70% of the ethanol value. A recently built plant in Nebraska reduces this cost down to 13%, thanks to the methanic fermentation of part of the by-products, and by avoiding by-product drying. The use of by-products in place of other animal feed, like soy feed or corn grain, can save the energy of producing them, about 12% of the ethanol value.
The grain transport from the farm to the refinery by means of medium and large trucks over an average distance of 100 km costs 2.3% of the ethanol value. The ethanol transport from the plant to the fuel station by truck and train or fluvial barge over an average distance of 1300 km is 2.1% of the ethanol value.
The average total cost for the 2001 harvest, assuming the 2005 refining situation and no irrigation, is 97 ± 3% (see Fig. 1 for cost details), without taking into account any by-product saving. By applying the same method, the cost of producing gasoline from crude oil is around 25% of its heating value (see Fig. 2 for a comparison between ethanol and gasoline costs). Of course, these results are independent of the resource availability of oil or of corn, as well as of other energy and materials needed to process them. This availability will be the focus of another study.

Schéma des différentes étapes de la chaîne de production de l’éthanol depuis le champ de maïs jusqu’à la station d’essence et coûts énergétiques associés à chaque étape. Données moyennes en 2001 pour la ferme (hors irrigation), en 2005 pour le parc d’usines (cf. Tableau 8).
Fig. 1. Diagram of the ethanol production chain from the cornfield to the gasoline station, and associated energy costs. Average data for the farm (without irrigation) in 2001 and for the refineries in 2005, reported in Table 8.
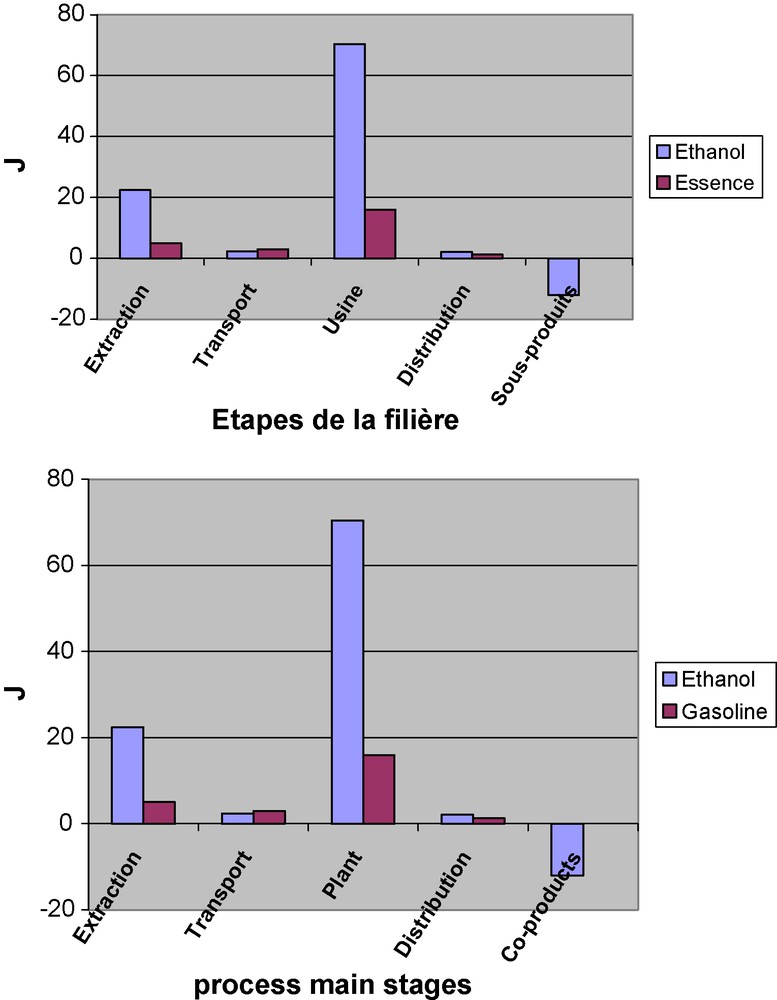
Comparaison des coûts à chaque étape entre filières pour produire 100 J d’éthanol et 100 J d’essence.
Fig. 2. Comparison of costs at each stage between the systems to produce 100 J of ethanol and 100 J of gasoline.
The expenditure rate expression given in [7] now allows us to compare all energy systems using biomass as primary energy feed and processing it down to a mechanical energy at a vehicle wheel with an intermediary energy, such as methane, fuel, or electricity. By applying this formula, the corn process cost in 2005 is 130% of the corn grain value, whereas the gasoline process cost is 85% of the crude oil value, assuming an energy yield of the vehicle of 30%.
1 Introduction
Avec la hausse récente des prix du pétrole, les pouvoirs publics remettent en avant des programmes de substitution des carburants dérivés du pétrole par des carburants d’origine agricole, ou agrocarburants. Il s’agit pour l’instant principalement d’éthanol issu de plantes amylacées (maïs, blé, tubercules…) ou sucrières (canne à sucre, betterave sucrière…), et d’esters d’huiles végétales obtenues de plantes oléagineuses (colza, tournesol, palmier à huile…). Depuis 2001, la production d’agrocarburants croît d’environ 15 % par an. En 2005, elle a représenté 31 Mt ou plus de 21 Mtep (1 tonne équivalent pétrole ou tep = 41,9 GJ) dont 18 Mtep d’éthanol pur [18]. Les deux principaux producteurs d’éthanol d’origine agricole sont le Brésil et les États-Unis d’Amérique, avec chacun environ 7,5 Mtep destinés au transport. Aux États-Unis, l’éthanol, obtenu principalement à partir du maïs, est considéré comme un des principaux outils pour réduire la dépendance énergétique du pays et connaît une croissance de plus de 20 % par an depuis 2001. Sa production doit doubler avant 2012 [19]. L’industrie de l’éthanol bénéficie de subventions au niveau fédéral et aussi au niveau des États (le total est estimé entre 5 et 7 milliards de dollars pour 2006 [18]).
Ces programmes ne sont pas sans susciter des réserves : faible rendement par surface agricole et donc faible production (environ le centième de la production de carburants pétroliers estimée à 1900 Mt en 2006), utilisation de terres arables au détriment de la production alimentaire, mauvais rendement énergétique… L’analyse énergétique, introduite dans les années 70 avec les crises pétrolières, établit si les dépenses énergétiques D nécessaires pour extraire une ressource naturelle énergétique et la transformer en une forme utile aux activités humaines ne dépassent pas son contenu énergétique, ou gain, G. Cette analyse doit traduire les contraintes des lois thermodynamiques régissant les transformations entre différentes formes d’énergie. Elle a donné lieu depuis une dizaine d’années à une controverse concernant la rentabilité énergétique de la production d’éthanol aux États-Unis. Elle oppose des fonctionnaires des services des ministères de l’Agriculture, USDA, et de l’énergie, USDOE, d’une part [11,20–22], et des scientifiques des universités de Berkeley et de Cornell [16,17], d’autre part. D’autres scientifiques de l’université de Berkeley [10] ont mené une étude dont les résultats sont proches de ceux des fonctionnaires de l’USDA (il s’agit principalement d’une compilation et d’une vérification des études précédentes). Le taux de dépenses énergétiques global, T = D/G, varie selon les publications de 69 % [21], ce qui indique un taux de dépenses inférieur à 1 (ou un rendement énergétique R = 1 – T positif) à 122 % [16] (indiquant un rendement R négatif), en passant par 81 % [11]. Les mêmes auteurs ont pu présenter des taux différents d’une publication à l’autre, comme Shapouri et al. [22], passant de T = 83 % [20] à T = 69 % [21]. Ce débat met en lumière la difficulté à réaliser une analyse d’une filière énergétique, comme celle de l’éthanol, de manière exhaustive et sans une part d’arbitraire. Il a cependant permis d’améliorer la qualité et la quantité des données sur le sujet.
Cet article reprend, dans une première partie, les données de base contenues dans ces différents articles ainsi que d’autres documents, provenant pour la plupart des ministères de l’Énergie et de l’Agriculture des États-Unis, pour mener une analyse plus poussée et quasi-complète des différentes dépenses de la filière éthanol américaine et pour estimer les taux de dépense associés. Il suit la méthodologie exposée dans un article général concernant la détermination du rendement énergétique [7]. Cette méthodologie, dont l’outil de travail est le taux T, vise à réduire la part des hypothèses arbitraires, à contrôler et estimer les incertitudes sur T, et à pouvoir comparer les performances entre différentes filières servant un même usage. Cet outil est suffisamment souple pour permettre l’intégration d’améliorations des procédés et tenir compte de contraintes autres que techniques, comme celles environnementales.
La partie suivante explicite la méthodologie dans le cas de la filière de l’éthanol, indique les sources des données de base utilisées et précise les facteurs de conversion énergétique. La troisième partie analyse les données, en déduit les différents taux de dépense pour chaque étape de la filière et par type de dépense et présente ensuite une synthèse de l’étude sous forme de taux, en indiquant les principaux facteurs influant sur celui-ci et en donnant la part des différentes énergies primaires (charbon, pétrole brut, gaz naturel…). Elle compare aussi le taux global pour la filière éthanol par rapport à celui d’autres filières menant à des produits pour les mêmes usages énergétiques (carburants pour les transports). Elle souligne la nécessité de reformuler ce taux, et en donne des expressions simples, si une comparaison avec d’autres filières énergétiques partant de la même ressource primaire – biomasse – et aboutissant au même point final – énergie mécanique pour les transports – doit être faite. La conclusion rappelle les principaux résultats de cette étude et mentionne l’extension nécessaire de cette analyse à l’étude de la disponibilité des différentes ressources (terres arables, eau, gaz naturel, engrais…), ainsi qu’il est écrit dans l’article décrivant la méthode [7].
2 Méthodologie et données de base
2.1 Chaîne d’extraction et de transformation du maïs en éthanol
La filière énergétique étudiée est décomposée en différentes étapes successives depuis l’extraction de la ressource naturelle – champ de maïs – jusqu’à sa transformation en une forme utile pour les applications recherchées – éthanol comme carburant. Le bilan des formes d’énergie entrant et sortant est réalisé à chaque étape (correspondant à un procédé ou à un ensemble de procédés liés) afin de déterminer les dépenses énergétiques, Di, de l’étape. Ces dépenses incluent les formes directes (combustibles, électricité…), mais également les formes indirectes (équipement, consommables matériels…). En effet, ces dernières représentent les produits de filières extérieures dans lesquelles des dépenses énergétiques ont été nécessaires pour leur réalisation. Il peut être d’ailleurs dit la même chose des formes directes d’énergie. De manière générale, toutes les formes énergétiques dissipées pour le fonctionnement de la filière étudiée, que cela soit dans la filière ou dans d’autres, doivent être comptabilisées. La comptabilité remonte, pour chaque filière énergétique, à la ressource naturelle énergétique sous la forme où elle est mesurée précisément pour la première fois, ou énergie primaire (pétrole, gaz naturel, charbon…). Les dépenses incluent aussi les pertes propres de la ressource traitée entre l’entrée et la sortie de chaque étape, i.e. entre l’énergie primaire et la forme finale d’énergie de la filière étudiée. Dans un premier temps, l’éthanol représentera à la fois l’énergie primaire et la forme finale. Les gains G représentent alors le contenu énergétique de l’éthanol, et les dépenses propres sont nulles. Cette convention est celle adoptée dans tous les articles ayant étudié la filière éthanol ; elle semble la plus naturelle, du fait que les dépenses sont données ou se ramènent facilement par unité d’éthanol produit. Dans la synthèse, nous verrons qu’une autre convention est possible, et est même nécessaire pour des comparaisons avec d’autres filières concurrentes. G inclut aussi le gain des sous-produits des usines d’éthanol. Comme ils sont utilisés comme aliment pour animaux, le gain ne correspond pas à leur pouvoir calorifique, à la différence du cas de l’éthanol [7]. Seule sera considérée l’énergie primaire nécessaire à la production des aliments qu’ils remplacent.
2.2 Origine des données de base par étape
Les données de base correspondent aux données avant toute conversion et interprétation, telles que mesurées sur les sites de production ou les moyens de transport. Pour chaque dépense intervenant le long de la chaîne de production, les informations contenues dans les différents articles publiés sur ce débat sont confrontées pour mettre en évidence les points d’accord et de désaccord. La référence [10] contient un récapitulatif utile de ces dépenses, pour chaque article, données dans les unités d’origine et dans les unités du système international. Pour les données officielles des ministères reproduites dans les articles, les valeurs sont, en cas de doute, vérifiées par rapport aux documents d’origine, quand ils sont accessibles sur les pages Internet de ces ministères (données souvent mises en ligne), ou confrontées aux données d’autres sources.
2.2.1 Étape (a) : la ferme
Les informations concernant les dépenses en énergies et en matériels dans les fermes sont rassemblées par des services de l’USDA, en particulier le National Agriculture Statistics Service (NASS) et l’Economic Research Service (ERS) lors d’enquêtes portant sur un bilan d’une année. Les enquêtes sont menées tous les quatre ou cinq ans sur un échantillon de fermes dont le nombre est plus ou moins proche du nombre total de fermes (les données de production par culture sont, en revanche, disponibles tous les ans). Les valeurs sont données dans les unités employées dans la ferme (volume de combustibles et de récoltes, masse d’engrais et de désherbants épandus, consommation électrique… en unités anglo-saxonnes) et moyennées au niveau de chaque État. Elles sont présentées par unité de surface de maïs récolté. Elles montrent des variations importantes entre États (parfois du simple au double). Il est probable qu’elles varient entre fermes au sein d’un même État. Des vérifications redondantes et l’examen des valeurs anormales permettent de réduire les erreurs d’enquêtes. Du fait de l’échantillonnage et d’autres erreurs comme l’interprétation des questions, l’incertitude sur les valeurs est estimée par les auteurs des rapports à au moins quelques pourcents de cette valeur. À travers les articles de Shapouri, les principales enquêtes utilisées sont le Farm Cost and le Return Survey de 1991 [20], devenu Agriculture Resource Management Survey en 1996 [22] et en 2001 [21]. Pour ses études, Shapouri retient les neuf principaux États producteurs, avec plus de 90 % du volume d’éthanol (Illinois, Indiana, Iowa, Michigan, Minnesota, Nebraska, Ohio, Dakota du Sud et Wisconsin), situés tous dans le Nord-Est du pays, autour des Grands Lacs. Ont été également utilisés dans ce présent article les enquêtes de l’USDA Farm and Ranch Irrigation Survey 1998 et 2002, et le Census of Agriculture 1997 et 2002. Toutes ces enquêtes ne concernant pas les mêmes années, il faut être prudent lorsqu’il s’agit de regrouper des données d’années différentes, du fait des changements météorologiques d’une année sur l’autre et de leur influence sur les rendements agricoles et les dépenses (fluctuations possibles de 20 %) ou des variations des surfaces dédiées à une culture.
Les données concernant le coût de fabrication des engrais sont indiquées dans différentes références [10,11,16,21].
2.2.2 Étapes (b) et (d) : transport et distribution
Il s’agit du transport du maïs entre la ferme et l’usine d’éthanol, ainsi que du transport de l’éthanol aux stations d’essence. Les références [11,21] indiquent les moyens de transport utilisés et donnent des distances typiques d’après quelques enquêtes des services fédéraux. Pour des distances jusqu’à 100 km, le transport se fait par camion. Au-delà, il se fait en général par train de marchandises ou par péniche fluviale. Presque tous les moyens utilisent des carburants pétroliers, et en général le gazole. Leurs dépenses en carburants par distance parcourue et par masse de charge utile peuvent être trouvées à partir de plusieurs sources différentes [1,11,21], permettant des estimations indépendantes dont les écarts donnent une idée des incertitudes.
2.2.3 Étape (c) : l’usine d’éthanol
Les données des dépenses en combustibles et électricité de ces usines sont contenues principalement dans l’article [11]. Elles résultent d’enquêtes réalisées par les services fédéraux et d’investigations auprès des gérants et des fabricants d’usines. Celles-ci sont réparties suivant deux types selon leurs procédés de transformation du maïs en éthanol (procédés dit à sec et dit humide). Un coût moyen est retenu pour chacun des deux types et suivant le combustible utilisé, charbon ou gaz naturel. Les données sur les usines construites après 2002, presque uniquement de procédé à sec avec du gaz naturel, sont également précisées d’après les informations des fabricants. En raison des enquêtes, l’incertitude sur ces données est faible, quelques pour cent au plus. Jusqu’en 2005 inclus, ces données peuvent s’appliquer pour presque toutes les usines, les usines pouvant présenter des dépenses plus faibles représentant moins de 1 % de la capacité totale [19].
2.3 Conversions énergétiques
Le choix des pouvoirs calorifiques volumiques ou massiques des ressources énergétiques produites et utilisées dans la filière d’étude (éthanol, combustibles, électricité) est indiqué ici. Sont estimées aussi les dépenses énergétiques qui ont été nécessaires dans des filières extérieures pour produire, à partir des énergies primaires, les énergies utilisées dans la filière éthanol (combustibles, électricité). Les dépenses énergétiques au niveau du système étudié, c’est-à-dire avant de tenir compte des dépenses dans les autres filières, seront indiquées par J ou Je (pour l’électricité), et celles prenant en compte les pertes notées Jtot.
Pour les combustibles contenant de l’hydrogène, il est précisé si le pouvoir calorifique est inférieur (PCI), pour lequel la chaleur latente de la vapeur d’eau formée n’est pas récupérée, ou si le pouvoir calorifique est supérieur (PCS), dans le cas d’une récupération totale. Le choix entre PCI ou PCS est souvent délicat (voir [7]). Nous faisons le choix du PCS, sauf dans le cas où le combustible est utilisé dans des applications dans lesquelles récupérer sa chaleur latente n’est pas possible ou n’a pas d’intérêt, comme dans les transports. De ce fait, le pouvoir calorifique de l’éthanol est compté en PCI, ainsi que ceux des combustibles utilisés dans les étapes (a), (b) et (d). Les combustibles dans les usines de fabrication de l’éthanol, des engrais… et dans les centrales électriques sont comptés par leur PCS.
2.3.1 Maïs et éthanol
Les quantités de maïs récoltées par surface agricole sont exprimées dans une unité de volume, le boisseau. Du fait de la présence d’air entre les grains (dont le volume peut être variable), cette donnée est moins précise que celle de la masse pour être convertie en énergie. Par ailleurs, les quantités indiquées correspondent à des grains avec un certain taux d’humidité, a priori variable et non précisé dans les références [20–22]. Cependant, il est précisé dans [11] que l’unité de production correspond à un boisseau standardisé de masse 25,4 kg et contenant 15 % d’humidité en masse. Cette conversion est celle adoptée par les services de USDA, comme l’indiquent ses documents officiels [2]. Le taux d’humidité de 15 % correspond au seuil au-delà duquel la bonne conservation du maïs n’est plus assurée. Le séchage des grains à la ferme ou dans les silos à grain permet d’ajuster l’humidité à cette valeur. Le département des variétés agricoles de l’université de l’Illinois recueille chaque année, pour différentes exploitations de cet État, les données d’humidité des maïs récoltés et leur quantité par surface [13]. Pour 2001, ces données montrent un taux d’humidité plus élevé que 15 % (19 % en moyenne), mais accompagné d’un rendement agricole plus élevé que celui indiqué dans la référence [21] pour l’Illinois la même année. Cette comparaison semble indiquer que le boisseau pris dans la référence [21] correspond bien à une masse de 25,4 kg de maïs, avec 15 % d’humidité. Le taux n’est donc pas toujours de 15 %, mais le compromis entre un faible coût du séchage et une humidité pas trop élevée à l’entrée des usines doit placer ce taux d’humidité en moyenne vers 15 %. L’utilisation d’un même étalon par les fermiers et les producteurs d’éthanol permet la conversion des récoltes en volume d’éthanol produit, et donc en énergie. Au niveau de la ferme, les quantités d’énergie seront exprimées par unité de masse de maïs – tmaïs – en prenant un maïs à 15 % d’humidité, sauf indication contraire.
L’éthanol pur étant formé d’une seule molécule, son PCI est connu précisément : 21,3 GJ/m3 à 15 °C sous 1013 hPa (conditions dites standard, adoptées dans tout le reste de l’article). À l’usine, l’éthanol anhydride est dénaturé avec 5 % en volume d’essence, pour le rendre impropre à la consommation, conformément à la réglementation. La référence [16] suggère que le chiffre de production d’éthanol dénaturé est utilisé pour le calcul du rendement énergétique, surévaluant ainsi de 5 % ce rendement. Cependant, la référence [11] mentionne explicitement que son bilan est établi par rapport à l’éthanol anhydre. Elle est aussi très précise sur les termes employés pour définir l’éthanol dans la filière (hydraté, anhydre, dénaturé). Il est donc difficile de croire qu’une telle erreur ait pu être commise, et nous l’excluons donc. Par défaut, le mot « éthanol » sera compris dans la suite comme éthanol anhydre, sauf précision contraire.
2.3.2 Hydrocarbures
Les pouvoirs calorifiques des hydrocarbures utilisés (dérivés du pétrole et du gaz naturel et charbon) ne sont pas les mêmes d’une référence à l’autre. Le PCI du diesel varie ainsi entre 37,8 [10] et 35,8 GJ/m3 ([21], à l’aide d’un calcul entre les Tableaux 2 et 3), soit un écart de 6 %. Ces combustibles ne sont pas des corps purs, et leur composition peut être variable. Nous prendrons les pouvoirs calorifiques de la référence [21], du fait qu’ils reposent sur les bases de données du ministère américain de l’Énergie – USDOE – en charge de collecter les données énergétiques : ces données ont plus de chance de refléter les caractéristiques des combustibles utilisés dans les exploitations agricoles. Le gaz de pétrole liquéfié (GPL), hydrocarbure composé majoritairement de butane et de méthane, est vendu sous une pression de quelques bars pour le maintenir sous forme liquide.
Détail des dépenses par hectare, en énergie finale, moyennées sur les données des huit États et de l’État du Nebraska pour 1991, 1996 et 2001 à partir des données des références [20–22]
Table 2 Itemized expenditure per hectare, in final energy and on average over the eight chosen States and the State of Nebraska for 1991, 1996 and 2001 from data in references [20–22]
GJ/ha | 8 États 1991 | NE 1991 | 8 États 1996 | NE 1996 | 8 États 2001 | NE 2001 |
Diesel GJ/ha | 1,7 | 6,0 | 2,3 | 6,0 | 1,6 | 4,2 |
Essence GJ/ha | 1,0 | 1,2 | 0,89 | 1,2 | 0,48 | 0,52 |
GPL GJ/ha | 0,68 | 0,82 | 1,4 | 0,82 | 0,93 | 0,84 |
Élect. Gje/ha | 0,21 | 0,86 | 0,68 | 0,73 | 0,15 | 1,4 |
Gaz naturel GJ/ha | 0,08 | 3,9 | 0,32 | 1,3 | 0,20 | 2,3 |
Rendement t/ha | 7,58 | 8,16 | 7,80 | 8,10 | 8,80 | 8,40 |
Dépenses par tonne de maïs, en énergie finale, moyennées sur les données des huit États et de l’État du Nebraska pour 1991, 1996 et 2001 à l’aide du Tableau 2
Table 3 Itemized expenditure per metric ton of corn, in final energy and on average over the eight chosen States and the State of Nebraska for 1991, 1996 and 2001 using Table 2
GJ/tmaïs | 8 États 1991 | NE 1991 | 8 États 1996 | NE 1996 | 8 États 2001 | NE 2001 |
Diesel GJ/tmaïs | 0,23 | 0,74 | 0,30 | 0,74 | 0,18 | 0,49 |
Essence GJ/tmaïs | 0,13 | 0,15 | 0,11 | 0,15 | 0,055 | 0,061 |
GPL GJ/tmaïs | 0,09 | 0,10 | 0,18 | 0,10 | 0,11 | 0,10 |
Élect. Gje/tmaïs | 0,028 | 0,11 | 0,087 | 0,090 | 0,017 | 0,16 |
Gaz naturel GJ/tmaïs | 0,011 | 0,48 | 0,041 | 0,17 | 0,023 | 0,28 |
Les dépenses des filières extérieures sont obtenues grâce aux facteurs d’efficacité indiqués dans la référence [21]. Le facteur d’efficacité est égal au rapport entre l’énergie finale (diesel, essence…) et le contenu de l’énergie primaire utilisée (pétrole brut…) additionné de toutes les autres énergies qui ont été nécessaires pour produire et transporter l’énergie finale. Ces taux ont été déterminés par les services de l’USDOE et font partie des données de base du modèle GREET développé par laboratoire national d’Argonne [14]). Ces caractéristiques énergétiques sont présentées dans le Tableau 1.
Pouvoirs calorifiques inférieur (PCI) et supérieur (PCS) des hydrocarbures et leur facteur d’efficacité ; (s) signifie pris sous conditions standard de température 15 °C et de pression 1013 hPa
Table 1 Low (LHV) and high (HHV) heat values of hydrocarbons and the yield factor of their processing (ratio of the heat value to the sum of the heat and the energy used); (s) means taken under standard conditions with temperature 15 °C and pressure 1013 hPa
Hydrocarbures | PCI | PCS | Facteur d’efficacité |
Diesel | 35,8 GJ/m3(s) | 38 GJ/m3(s) | 0,84 |
Essence | 32,4 GJ/m3(s) | 35 GJ/m3(s) | 0,80 |
Gaz naturel | 34,4 MJ/m3(s) | 38 MJ/m3(s) | 0,94 |
GPL | 22 GJ/m3 | 24 GJ/m3 | 0,99 |
Charbon | 23,8 GJ/t | 0,98 |
Le prix du GPL est très élevé. Cela pourrait se comprendre par des coûts d’extraction et de transport faibles et par l’absence de coût de raffinage. Cet hydrocarbure provient à 40 % des raffineries de pétrole (coupe en haut des tours de distillation atmosphérique) et à 60 % du gaz naturel au niveau des champs (par séparation sous compression de quelques bars).
Le charbon, aux États-Unis, est à plus de 60 % extrait de mines à ciel ouvert. Il est utilisé dans des centrales électriques proches des mines ou accessibles par chemin de fer. Son facteur d’efficacité élevé peut s’expliquer pour ces raisons.
Le coût du gaz naturel est surtout lié à son transport. Les États-Unis produisent 80 % du gaz naturel qu’ils consomment. On peut supposer que les distances entre champs et consommateurs ne sont pas trop élevées (moins de 1000 km). Cette situation est en train de changer, du fait de la nécessité, pour compenser le déclin de la production du pays, d’importer du gaz naturel en dehors des Amériques et sous forme cryogénique [3]. Le combustible de loin le plus utilisé dans la production d’éthanol est le gaz naturel (voir le paragraphe de synthèse). C’est donc celui dont les caractéristiques doivent être les plus précises. Son pouvoir calorifique moyen semble assez constant, au vu de la qualité du gaz naturel utilisé par les centrales électriques [9].
2.3.3 Électricité
Il est délicat de convertir une consommation électrique en énergie primaire, car cela fait intervenir des facteurs indépendants de la filière étudiée, comme la part des différentes énergies primaires dans la production électrique et le rendement associé à chacune d’entre elles. Les mêmes auteurs ont d’ailleurs pu changer d’avis d’un article à l’autre : différence entre les références [20] – rendement total de 27 % – et [22] – rendement total de 37 %. Graboski [11] détaille dans son annexe 1 son calcul pour obtenir le facteur de conversion. À partir des données de consommation en combustibles des centrales et de leur production nette, recueillies pour chaque État par le service statistique de l’USDOE, il établit un facteur moyen pour les principaux États producteurs d’éthanol. Cette donnée tient compte également du facteur d’efficacité de chaque combustible à partir des énergies primaires et des pertes sur le réseau électrique. Dans le cas des neuf États étudiés, 70 % de leur puissance électrique provient de la combustion du charbon. Les masses de charbon indiquées et leur pouvoir calorifique correspondent au charbon tel qu’il est reçu au niveau des centrales, c’est-à-dire avec un niveau d’humidité d’environ 10 % et un niveau de cendre presque identique [9]. Graboski exclut des dépenses les énergies renouvelables (moins de 3 % de l’électricité produite), mais surtout la chaleur produite dans les réacteurs nucléaires (20 % de l’électricité produite). Nous avons repris ses données pour les neuf États producteurs, en utilisant les PCS pour les combustibles et en incluant les énergies nucléaire et renouvelables. Les facteurs d’efficacité et les pertes sur le réseau (8,7 %) sont ceux de la référence [21], mieux à jour concernant les pertes énergétiques dans le système de production des États-Unis (valeurs de la base de données du modèle GREET des services de l’USDOE [14]). Le rendement thermodynamique est de 32 % en utilisant le PCS. En considérant toutes les pertes, le facteur de conversion est de 27 %. L’ensemble des énergies primaires pour produire l’électricité utilisée dans la filière sera appelé électricité primaire.
Il est intéressant de noter les rendements thermodynamiques pour le charbon, 31 %, et pour le gaz naturel, 25 %. Au niveau national, ces rendements sont de 32 % et 39 %, respectivement. Les centrales au charbon les plus récentes atteignent pourtant 40 %, tandis que les centrales au gaz avec cycles combinés dépassent les 50 %. Il semble que le parc des centrales électriques des États-Unis considérées ici est ancien.
3 Analyse de la chaîne de production énergétique
3.1 Dépenses au niveau de la ferme
La culture du maïs aux États-Unis est une culture intensive, c’est-à-dire très mécanisée et nécessitant beaucoup d’intrants sous forme synthétique. Les rendements agricoles, en t/ha, sont en contrepartie les plus élevés au monde. La culture, depuis les semis – vers fin avril – jusqu’à la récolte – de septembre à octobre – dure environ 130 jours. Le sol est mis en jachère ou utilisé pour des cultures moins exigeantes en nutriments, voire régénératrices en azote. Durant la période de culture, des énergies directes, comme des carburants pour les engins agricoles et les pompes d’irrigation, ou comme des combustibles pour le séchage des grains, sont dépensées. Des produits à fort contenu énergétique, comme les engrais, insecticides, herbicides…, sont épandus. À cela, il faut ajouter les énergies qui ont été utilisées à l’extérieur de la ferme pour fabriquer les équipements agricoles.
Les dépenses brutes sont données par unité de sole de maïs récolté. Elles seront ramenées par unité de masse de maïs produit (à 15 % d’humidité en masse) en utilisant le rendement agricole. Ces dépenses unitaires tiennent compte ainsi du rendement agricole et de ses variations. Le rendement agricole moyen sur les neuf États étudiés a été de 7,65 tmaïs/ha en 1991, 7,85 tmaïs/ha en 1996 et 8,75 tmaïs/ha en 2001. Le rendement de la distillerie en volume d’éthanol par tonne de maïs a peu varié entretemps (de 0,38 à 0,40 m3etOH/tmaïs), ce qui permettra une conversion aisée en taux de dépenses. Le rendement agricole entre les neuf États varie dans une fourchette de ± 10 % (sauf pour le Dakota du Sud, systématiquement plus faible de l’ordre de 25 %, mais ce faible rendement semble corréler avec sa faible consommation d’engrais azotés).
3.1.1 Combustibles et électricité
Les énergies dépensées directement au niveau de la ferme sont sous forme de diesel, essence, GPL, gaz naturel et électricité. Elles sont utilisées comme carburant pour les engins agricoles (tracteurs, moissonneuses-batteuses…), pour les pompes des systèmes d’irrigation… et comme combustibles pour le séchage. Ces dépenses varient d’un État à l’autre (et probablement à l’intérieur d’un même État [10]) et d’une année à l’autre. Deux utilisations de ces énergies peuvent expliquer en grande partie ces variations : le séchage des grains et l’irrigation par pompage de l’eau à partir des nappes phréatiques. L’importance de ces deux activités dans les dépenses va dépendre de la météorologie sur toute la durée de la culture et des caractéristiques climatiques moyennes locales.
L’examen des données par État montre que le Nebraska présente, pour toutes les années, des dépenses bien supérieures aux autres (en 2001, cinq fois la moyenne de consommation électrique, quatre fois celle de gaz naturel, deux fois celle de diesel). Le poids des dépenses du Nebraska fausse d’ailleurs les statistiques. La seule explication possible à ce poids élevé est l’importance de l’irrigation par pompage dans cet État. D’après l’enquête sur les coûts d’irrigation réalisée par l’USDA en 1998, plus de la moitié des surfaces consacrées au maïs au Nebraska nécessitent une irrigation, alors que les autres États présentent un taux bien plus faible, de 9 % au plus et de 2 à 3 % en moyenne.
Par ailleurs, si on examine les données des huit États – en écartant le Nebraska pour sa singularité – sur les trois années étudiées, on remarque des fluctuations importantes des dépenses d’énergie, en particulier d’électricité et de GPL. Entre 1991 et 1996, ces deux dépenses sont multipliées par trois et quatre, respectivement. Or, la météorologie de l’année 1991 a été très sèche, tandis que celle de 1996 a été très humide. Les taux d’humidité des grains récoltés ont donc été différents, ce qui explique les variations du coût du séchage entre 1991 et 1996.
Pour estimer la part des dépenses due au séchage et à l’irrigation, les données par État sont reprises pour faire une moyenne sur les huit États, hors Nebraska, pour chaque année étudiée. Les valeurs des surfaces consacrées à la culture de maïs à grain par État, nécessaires pour la pondération de la moyenne, sont obtenues à l’aide des données des recensements agricoles de 1992, 1997 et 2002 (Census of agriculture, NASS, USDA). Ce travail permet du reste de corriger les moyennes sur les neuf États des dépenses de combustibles en 2001 contenues dans les Tableaux 1 et 2 de l’article [21]. À cause d’une coquille ou d’une erreur, ces moyennes correspondent en réalité à celle de 1991 [20]. Les données des huit États et du Nebraska sont présentées, pour les trois années étudiées, converties en énergie finale par hectare (Tableau 2) et par tonne de maïs (Tableau 3). Le dernier tableau (Tableau 4) représente l’énergie totale, dépenses des filières extérieures incluses.
Détail et total des dépenses par tonne de maïs, ramenées en énergie primaire, moyennées sur les données des huit États et de l’État du Nebraska, pour 1991, 1996 et 2001. Dépenses en diesel, électricité et gaz naturel par hectare
Table 4 Primary energy itemized and overall expenditures per metric ton of corn, on average over the eight chosen States and the State of Nebraska, for 1991, 1996 and 2001. Expenditure in diesel, electricity, and natural gas per hectare
GJtot/tmaïs | 8 États 1991 | NE 1991 | 8 États 1996 | NE 1996 | 8 États 2001 | NE 2001 |
Diesel GJtot/tmaïs | 0,27 | 0,88 | 0,35 | 0,89 | 0,22 | 0,59 |
Essence GJtot/tmaïs | 0,17 | 0,19 | 0,14 | 0,19 | 0,068 | 0,095 |
GPL GJtot/tmaïs | 0,09 | 0,10 | 0,18 | 0,10 | 0,11 | 0,10 |
Électricité GJtot/tmaïs | 0,10 | 0,39 | 0,32 | 0,33 | 0,062 | 0,60 |
Gaz naturel GJtot/tmaïs | 0,012 | 0,51 | 0,044 | 0,18 | 0,024 | 0,29 |
Total GJtot/tmaïs | 0,64 | 2,1 | 1,0 | 1,7 | 0,48 | 1,7 |
Diesel+élec+gaz naturel GJtot/ha | 2,9 | 14,5 | 5,6 | 11,3 | 2,7 | 12,4 |
3.1.1.1 Coût de l’irrigation
Ce coût est estimé en comparant les dépenses entre Nebraska et les huit autres États. Les énergies utilisées pour alimenter les moteurs de pompes sont le diesel, l’électricité et le gaz naturel [11]. Ce sont effectivement les dépenses les plus élevées. On note aussi la diminution de ces dépenses dans le Nebraska en 1996, année de météorologie humide. Pour mener une estimation du coût d’irrigation, nous supposons que la différence de dépenses de ces énergies entre le Nebraska et les autres États n’est due qu’à l’irrigation, les autres sources de dépenses, déplacements des engins et séchage, étant similaires. Ceci n’est pas tout à fait exact pour les dépenses de séchage, qui doivent être plus faibles dans le Nebraska, du fait de son climat plus sec. En effet, la consommation de GPL, utilisé surtout pour le séchage, a été moins élevée en 1996 dans le Nebraska qu’ailleurs. La différence pour le GPL est cependant faible, et la différence de dépenses dues au séchage entre le Nebraska et les huit autres États est probablement encore plus faible pour les autres combustibles. Elle est donc négligée. Des données du Tableau 4, tenant compte des dépenses totales en énergie primaire, nous déduisons le total de ces dépenses pour le Nebraska et les huit États. Elles sont ramenées par unité de surface à l’aide des rendements agricoles par groupe d’États et par année. La différence entre le Nebraska et les huit autres États donne : 11,6 GJtot/ha en 1991, 5,7 GJtot/ha en 1996, 9,8 GJtot/ha en 2001. Il ressort de la comparaison de ces données qu’en 2001 le temps a été sec, mais moins qu’en 1991, ce que confirment les commentaires des références [20–22].
L’analyse des données pour déterminer le coût d’irrigation se complique du fait qu’une partie seulement des surfaces cultivées en maïs à grain au Nebraska est irriguée avec un système de pompage de nappes souterraines (il existe aussi un système d’irrigation par gravité, sans besoin de pompes). Graboski [11] a mené une analyse assez détaillée des coûts d’irrigation, à l’aide de résultats de l’enquête de l’USDA consacrée à l’irrigation État par État pour l’année 1998. Le même type d’enquête a eu lieu pour 2002, mais risque de ne pas être représentatif de la situation en 2001. En effet, les précipitations ont été plus faibles en 2002 qu’en 2001 et 1998, ce que reflètent les rendements agricoles sensibles à cet indicateur, prenant en compte sa tendance générale à la hausse (8,4 tmaïs/ha en 1998, 8,8 tmaïs/ha en 2001, 8,1 tmaïs/ha en 2002). D’après l’enquête de 1998, 47 % de la sole de maïs est irriguée dans le Nebraska, 65 à 70 % de ces surfaces nécessitant un pompage. Ces surfaces représentent donc à peu près 1/3 de la sole de maïs dans le Nebraska en 1998 (46 % en 2002). On suppose que la même proportion existait en 2001. Nous supposons que les terres non irriguées par pompage dans le Nebraska, deux tiers de la sole de maïs, présentent les mêmes dépenses que dans le groupe des huit États, 2,7 GJtot/ha. Sur les terres irriguées par pompage, le coût total d’irrigation est donc de 24 GJtot/ha. En supposant que le rendement agricole d’une surface irriguée est de 25 % plus élevé que celui d’une surface non irriguée (valeur pour 1998 [11]), le rendement moyen de 8,4 tmaïs/ha est obtenu par un rendement de 9,7 tmaïs/ha sur terre irriguée (et 7,75 tmaïs/ha sur terre non irriguée). Le coût par tonne de maïs en 2001 est de 2,5 GJtot/tmaïs, à environ 45 % sous forme d’électricité primaire, 22 % de gaz naturel et 33 % de pétrole. Même s’il s’agit d’une estimation (incertitude d’environ 15 % ou ± 0,35 GJtot/tmaïs), cette valeur montre que le coût d’irrigation représente une part élevée des dépenses totales dans la ferme.
3.1.1.2 Dépenses de séchage
Après leur maturation, les grains pourraient sécher naturellement jusqu’au taux d’humidité de 15 % en retardant leur récolte [24]. Mais les risques de pertes liés à l’attente (due au mauvais temps ou à l’attaque de parasites) ou les profits possibles à vendre rapidement, joints aux difficultés un peu plus élevées que présente le moissonnage d’un maïs trop sec, amènent les fermiers à moissonner des grains avec des taux d’humidité plus élevés que 15 %. Il est donc nécessaire d’évaporer une partie de l’eau par chauffage. La chaleur latente de l’eau à 20 °C est 2,25 GJ/teau. Cependant, les consommations thermiques des séchoirs dépendent de la température et de l’humidité de l’air ambiant. Dans le Mississippi, la consommation moyenne des séchoirs est de 4,6 GJ/teau (correspondant au PCS du GPL consommé). En l’absence probable de récupération de la chaleur latente du GPL, la dépense réellement utilisée pour le séchage est de 4,3 GJ/teau (d’après le PCI du GPL). Avec de meilleures conditions atmosphériques, le coût est de 3,2 GJ/teau (PCS du GPL, ou 3,0 GJ/teau PCI). Pour les huit États, nous supposerons une dépense réelle de l’ordre de 3,7 GJ/teau (PCI et conditions intermédiaires). Entre 1991 et 1996, le taux moyen d’humidité des grains récoltés est passé de 18 % à 23 % [11]. Entre 18 et 15 %, par conservation de la masse sèche, la différence de masse d’eau à enlever par tonne de maïs à 15 % est de 37 kg/tmaïs. Entre 23 % et 15 %, cette quantité est de 100 kg/tmaïs. Le coût de séchage serait respectivement de 0,14 et 0,37 GJ/tmaïs, soit une différence de 0,23 GJ/tmaïs entre les deux années. En utilisant le Tableau 3, contenant les coûts en énergie finale par tmaïs, et en faisant la différence des dépenses entre 1991 et 1996, on obtient 70 MJ/tmaïs de dépense supplémentaire en diesel en 1996, 90 MJ/tmaïs en GPL, 60 MJe/tmaïs pour l’électricité et 30 MJ/tmaïs en gaz naturel. Une petite partie des dépenses de séchage est effectuée par les sociétés qui collectent le grain (voir ci-dessous). En faisant la différence de ces dépenses entre 1991 et 1996, le supplément extérieur est de moins de 10 MJ/tmaïs. Le surplus de dépenses en diesel est dû en partie au replacement de l’essence, moins utilisée (−20 MJ/tmaïs entre 1991 et 1996). Les deux façons d’estimer donnent des résultats très proches. En tenant compte des coûts en amont, la différence est d’environ 0,45 GJtot/tmaïs. Pour une année normale comme 2001, le coût est pris à environ 0,25 GJtot/tmaïs.
3.1.1.3 Dépenses par des sociétés extérieures
La rubrique custom work indiquée dans les tableaux de la référence [21] représente l’ensemble des coûts financiers facturés par des sociétés extérieures contractées lors des semis, de l’épandage de nutriments et de la récolte, ainsi que par les gérants des silos à grains pour un séchage complémentaire des grains réalisé en dehors de la ferme. Une partie de ces coûts concernent des dépenses d’énergie, carburants pour les sociétés extérieurs, GPL et électricité pour les silos à grain, non prises en compte dans le bilan énergétique des fermes (et donc dans les Tableaux 2 à 4). Graboski [11] a analysé le détail de ces coûts pour en déduire la part due aux énergies et de là les dépenses énergétiques correspondantes. Nous retenons les valeurs globales données dans les références [11,21] (dans ce dernier travail, la valeur est déterminée en faisant le rapport des valeurs par État entre les Tableaux 1 et 2). Les valeurs moyennées sur les neuf États sont de 0,53 GJtot/ha ou 0,07 GJtot/tmaïs en 1991, 0,60 GJtot/ha ou 0,08 GJtot/tmaïs en 1996 et 0,57 GJtot/ha ou 0,07 GJtot/tmaïs en 2001. Ces valeurs sont ajoutées aux dépenses énergétiques directes en prenant 55 % pour le carburant et 45 % pour le séchage sous forme essentiellement de GPL (données approximatives déduites de l’analyse de Graboski [11]).
3.1.1.4 Bilan des dépenses de combustibles et d’électricité en 2001 sur huit États
Les dépenses totales de combustibles en 2001, moyennées sur les huit États, tenant compte des facteurs d’efficacité et du facteur de conversion électrique, sont de 0,48 GJtot/tmaïs (dont 62 MJtot/tmaïs en électricité primaire), comme l’indique le Tableau 4. Un peu moins de la moitié est dédiée au séchage (en supposant le coût d’irrigation négligeable). À cela, il faut ajouter une dépense de 0,07 GJtot/tmaïs effectuée par des sociétés extérieures. La décomposition suivant les différentes énergies primaires (pétrole, gaz naturel et électricité primaire) est estimée dans le Tableau 5. Les dépenses sont réparties suivant aussi les deux principaux postes, carburants et séchage. Le GPL est considéré comme un dérivé pétrolier, même pour la fraction extraite du gaz naturel brut.
Bilan des coûts en énergie primaire associés aux dépenses de carburants et de séchage, ramenés à une tonne de maïs. Ces coûts représentent une moyenne sur huit États pour 2001. Les incertitudes sont prises pour chacun à 10 % de leur valeur
Table 5 Balance of primary energy costs of transport and drying fuels per metric ton of corn and on average over the eight chosen States for 2001. Uncertainties are taken for each cost at 10 % of their value
GJtot/tmaïs | Pétrole | Gaz naturel | Électricité | Total | Incertitude |
Carburant | 0,32 | 0 | 0 | 0,32 | 0,03 |
Séchage | 0,14 | 0,024 | 0,062 | 0,23 | 0,02 |
Total | 0,46 | 0,024 | 0,062 | 0,55 | 0,04 |
3.1.2 Coûts des produits nécessaires à la culture du maïs
Ces produits (semences, engrais, désherbants et insecticides) doivent être renouvelés à chaque récolte, c’est-à-dire chaque année, et constituent, avec les combustibles et l’électricité, les dépenses d’exploitation d’une ferme. Les engrais apportent aux sols les éléments essentiels à la croissance des plantes, autres que H, C et O apportés par l’eau et le CO2 [12]. Les engrais les plus importants en quantité sont les engrais azotés, les phosphates et le potassium. Il est d’usage de rapporter les quantités épandues en masse du composé actif, azote (N), phosphate (P2O5) et potasse (K2O). Il est aussi épandu de la chaux, CaO, pour réguler le taux de Ca du sol et son acidité. Les apports de micronutriments comme le soufre sont négligés, vu leur faible poids. Les calculs des coûts seront menés à partir des données de l’année 2001 sur neuf États [21], avec une comparaison avec les coûts des années 1991 et 1996 par produits lorsque les données sont disponibles. Le bilan est fait seulement pour l’année 2001.
3.1.2.1 Semences
3.1.2.1.1 Taux d’application
En 2001, les surfaces des neuf États ont reçu en moyenne 71 000 grains de semences par hectare, à ±7500 [21]. En supposant qu’un millier de ces grains pèsent 332 g [16], le taux d’application est de 24 kgsemence/ha ou 2,7 kgsemence/tmaïs.
3.1.2.1.2 Coût de production
Ce point a été sujet à discussion, car les publications avant 2002 de l’USDA avaient largement sous-estimé leurs coûts. La référence [11] donne les détails de la production de ces semences à partir d’informations recueillies chez les fabricants. La première étape est l’étape de culture, identique à celle du maïs ordinaire, mais avec un rendement plus faible. Au lieu de 8,75 tmaïs/ha, on a obtenu 2,74 tsemence/ha (les semences ont des taux d’humidité de 12,5 %). Le coût en semence, produits synthétiques et carburants, hors séchage, est très proche de celui dans une ferme par unité de surface. D’après les Tableaux 5 et 6 pour 2001 et les huit États, et en se ramenant par unité de surface, cette dépense est de 16,2 GJtot/ha, d’où un coût pour les semences de 5,9 GJtot/tsemence, hors séchage et irrigation. Cette dépense se compose de gaz naturel à 65 %, de pétrole à 25 % et d’électricité primaire à 10 %. La deuxième étape consiste en un séchage des grains récoltés jusqu’à un taux d’humidité de 12,5 % en masse. Le taux d’humidité avant séchage peut atteindre 35 %. Nous le supposerons à 28 % en moyenne. Par conservation de la masse sèche, la masse d’eau à retirer par masse de semence finale est de 0,21 teau/tsemence. Avec un coût de séchage de 3,7 GJ/teau (en prenant le PCI du GPL), le coût est de 0,80 GJ/tsemence. Si on suppose que le séchage a lieu avec la rafle, comme semble l’indiquer Graboski [11], il faut enlever une quantité d’eau supplémentaire égale à environ 45 % de celle contenue dans les grains. Le coût total est de 1,1 ± 0,1 GJ/tsemence. On suppose, avec Graboski, que le séchage a lieu uniquement avec le GPL, pris comme un dérivé pétrolier. La troisième étape consiste dans le décorticage, le nettoyage, le calibrage, l’emballage et le stockage des semences. L’ensemble de ces opérations nécessite une consommation en électricité de 0,60 GJe/tsemence ou 2,2 GJtot/tsemence. La dépense globale est donc de 9,3 GJtot/tsemence (30 % en pétrole, 40 % en gaz naturel, 30 % en électricité primaire). Avec le taux d’application, le coût moyen est de 0,025 GJtot/tmaïs.
Dépenses énergétiques pour 2001 en semence et autres produits par tonne de maïs, moyennées sur neuf États. Décomposition suivant les différents produits et les principales énergies primaries
Table 6 Energy expenditure of seed and other products per metric ton of corn, on average over nine States for 2001. Decomposition according to the various products and the main primary energies
GJtot/tmaïs | Pétrole | Gaz naturel | Électricité primaire | Total | Incertitude |
Semence | 0,0075 | 0,010 | 0,0075 | 0,025 | 0,003 |
N | 0 | 1,08 | 0 | 1,08 | 0,06 |
K2O | 0,007 | 0,035 | 0,028 | 0,07 | 0,004 |
P2O5 | 0 | 0 | 0,065 | 0,065 | 0,007 |
CaO | 0 | 0 | 0,015 | 0,015 | 0,0015 |
Désherbant | 0,055 | 0,017 | 0,048 | 0,12 | 0,015 |
Total | 0,070 | 1,14 | 0,16 | 1,37 | 0,07 |
3.1.2.2 Engrais azotés
En 1991, l’agriculture des États-Unis a utilisé presque 10 MtN (millions de tonnes d’azote), dont 5 MtN sous forme d’ammoniac NH3, 2,5 MtN sous forme de solutions d’urée (NH2)2CO et de nitrate d’ammonium NH4NO3, 1,8 MtN sous forme d’urée seul et 0,7 MtN sous forme de nitrate d’ammonium seul [11]. Ces différents engrais ne présentent ni la même vitesse d’assimilation par les plantes, ni le même pouvoir de rétention par les sols. Ils sont utilisés de manière à obtenir un compromis satisfaisant entre rétention et assimilation.
3.1.2.2.1 Taux d’application
En 2001, le taux moyen d’application sur les neuf États a été de 150 kgN/ha, en hausse par rapport aux années précédentes (140 en 1991, 145 en 1996). Si on tient compte de la hausse du rendement agricole, ce taux est davantage constant et diminue même légèrement : 18 kgN/tmaïs en 1991, 17 kgN/tmaïs en 2001. La dispersion entre États, en kgN/tmaïs, est de l’ordre de 15 %, si on excepte quelques États particuliers. Dans le Minnesota, les agriculteurs épandent 18 % de moins d’engrais azotés que la moyenne, tandis que ceux de l’Ohio en épandent 40 % de plus.
3.1.2.2.2 Coûts de fabrication
Le corps de base de la fabrication des engrais azotés est l’ammoniac NH3. Sa production est la plus coûteuse des étapes. Elle s’opère entre un hydrocarbure, essentiellement le méthane CH4, et le diazote de l’air suivant la réaction globale en phase gazeuse [12] :
x est un paramètre proche de 1. En pratique, la synthèse se fait en plusieurs étapes, chacune avec ses conditions thermodynamiques (T, P) et cinétiques (T, catalyseur). La consommation d’énergie de cette synthèse est assimilée au PCS du méthane utilisé, même s’il ne s’agit pas à proprement parler d’une réaction de combustion. En l’absence de pertes, le coût énergétique correspondrait donc théoriquement au PCS de x mole de CH4 pour deux moles de N produites ou x 31,7 MJ/kgN (PCS (CH4) = 55,5 MJ/kg). La chaleur de réaction, assimilée à l’enthalpie standard ΔH0 de la réaction à 298 K [8], est nulle pour x = 0,79 ou pour 25 MJ/kgN de gaz naturel consommé. En l’absence de pertes thermiques et sans tenir compte des contraintes du second principe de la thermodynamique et de la cinétique de la réaction, cela correspondrait à la plus faible consommation d’énergie pour réaliser la réaction. En imposant une température d’inversion [8] de 500 K et en calculant l’enthalpie libre de la réaction (assimilée à l’enthalpie libre standard ΔG0 à 500 K), x vaudrait au minimum 0,85 à la limite d’évolution de la réaction (). La consommation correspondante de gaz naturel est équivalente à 27 MJ/kgN. On peut considérer cette situation comme étant la limite théorique. D’après les résultats d’un recensement de Kongshaug en 1998 [16], la consommation réelle nette s’est progressivement rapprochée de cette limite : 55 MJ/kgN en 1945, 46 MJ/kgN en 1973, 37 MJ/kgN en 1980 et 34,5 MJ/kgN en 1992 (il s’agit probablement des valeurs PCS). Ces progrès ont souvent été réalisés en intégrant les procédés, afin de récupérer la chaleur produite lors d’une étape et de l’utiliser pour d’autres. On peut s’attendre à de faibles progrès par rapport aux installations les plus récentes.
Les autres engrais azotés s’obtiennent par des réactions à partir de NH3. Par unité de masse N (ce qui est équivalent à travailler par unité de mole de N), les dépenses d’énergie de chaque réaction s’ajoutent. D’après la référence [16], en tenant compte des différences d’efficacité des installations avec leur âge, les dépenses nettes pour produire chaque forme depuis le diazote sont :
- • NH3 : de 34,5 à 47 MJ/kgN ;
- • (NH2)2CO : de 42 à 57 MJ/kgN ;
- • NH4NO3 : de 35 à 51 MJ/kgN.
À cela, il faut ajouter les pertes en amont (facteur d’efficacité du gaz naturel), les coûts de mélange des engrais et de la granulation (moins de 2 MJ/kgN), les frais d’emballage et de transport. D’après la référence [16], l’industrie des engrais aux États-Unis est ancienne, et donc les dépenses se rapprochent des estimations supérieures. Ce point est confirmé par les services d’USDA : ils considèrent un coût global, comprenant toutes les dépenses, dont le transport, de 57 MJ/kgN (PCI) [21], ou environ 63 MJ/kgN (PCS). La conversion PCI/PCS est effectuée en supposant que l’énergie utilisée est essentiellement du gaz naturel. L’incertitude est d’environ ±5 %.
En 2001, en tenant compte du taux d’application moyen de N, les dépenses ont donc été de :
3.1.2.3 Engrais phosphatés
En 2001, le taux d’application moyen a été de ou , avec des variations entre États qui peuvent atteindre ±35 % (). Le taux fluctue au cours du temps ( en 1991, en 1996).
3.1.2.3.1 Coût de fabrication
Le phosphate est extrait de minerais riches en apatite, un composé de la forme Ca3(P2O4)2, CaCl2 ou CaF2. Celui utilisé aux États-Unis provient d’un gisement très riche en Floride. Le minerai est broyé et sans doute soumis à une séparation physique pour extraire les minéraux contenant le phosphore. Le produit est dissous dans l’acide sulfurique pour donner des phosphates. L’estimation des coûts semble difficile, d’après la référence [16]. La valeur très faible de donnée dans la référence [11] repose sur l’attribution d’un gain d’énergie important à l’acide sulfurique. Cet acide est produit à partir de soufre S, sous-produit de l’industrie pétrolière et gazière ou de la métallurgie extractive. L’oxydation du soufre en acide s’accompagne d’un important dégagement de chaleur, souvent utilisé pour produire de la vapeur. Ce gain est probablement déjà pris en compte dans les coûts des industries qui produisent S et donc n’a pas lieu d’être compté lors de l’utilisation de l’acide. La valeur globale de Shapouri et al. [21], , est retenue. Le coût est surtout sous forme électrique, en dépenses de concassage et broyage. Du fait d’un facteur de conversion électrique généreux, Shapouri peut sous-estimer cette dépense en termes d’énergie primaire. Ce poste de dépense est de toute manière faible. Pour 2001, du taux d’application moyen on déduit un coût de 0,068 GJtot/tmaïs.
3.1.2.4 Potasse
Le taux d’application en 2001 a été de ou , avec des taux entre États de 2,8 à . En 1991 les taux étaient de ou et en 1996 de ou . Son épandage par unité de surface a donc, en moyenne, nettement augmenté après 1996 (plus de 60 % entre 1996 et 2001). Le rendement a augmenté aussi dans le même temps, moins vite cependant. Cette corrélation semblerait indiquer l’intérêt de la potasse pour augmenter les rendements agricoles.
Le coût de fabrication est faible, tant qu’il existera des gisements de sel riches en KCl. C’est le cas des sylvinites. Les États-Unis importent majoritairement leur potasse d’un gisement au Canada. KCl est séparé de NaCl par dissolution sélective dans l’eau suivant la température. KCl est utilisé directement ou associé avec d’autres engrais. La référence [11] fournit les dépenses brutes de la société canadienne exploitante du gisement. Le coût par tonne de K2O, tenant compte des facteurs d’efficacité des combustibles, est de . Il est arrondi à pour tenir compte des coûts d’acheminements et autres. Il se décompose environ pour moitié en dépense de gaz naturel, 40 % d’électricité et 10 % de pétrole.
Le coût moyen total au niveau de la ferme en 2001 a été de 0,065 GJtot/tmaïs.
3.1.2.5 Chaux agricole
Le taux d’application de la chaux est très variable dans le temps et suivant les États. Certains sols ne nécessiteront aucun épandage de chaux, tandis que d’autres, comme les sols granitiques, en nécessiteront une grande quantité (4 à 5 tCaO/ha). Pour cette raison, les données entre États apparaissent très disparates : de 0 à 70 kgCaO/ha, avec une moyenne de 18 kgCaO/ha ou 2 kgCaO/tmaïs en 2001. L’enquête de 1991 fait apparaître des valeurs, par État, aussi élevées que 750 kgCaO/ha (ou un peu moins de 100 kgCaO/tmaïs). Farrel et al. ont obtenu des services de l’USDA des données plus détaillées [10]. La chaux est appliquée à 55 % de la sole de maïs en moyenne (en intégrant une douzaine des principaux États producteurs ; la valeur varie entre presque 100 % et 5 % suivant les États), avec un taux de 5 tCaO/ha (faible dispersion entre États) et une fréquence de un tous les cinq à six ans (faible dispersion entre États aussi). L’épandage maximal est donc de 820 kgCaO/ha/an (100 % de la sole de maïs d’un État). Le fait que la chaux soit appliquée de manière très ponctuelle explique les écarts de valeurs reportées et le débat qui s’en est suivi.
3.1.2.5.1 Coût de fabrication
Une des difficultés pour estimer le coût de fabrication par tonne de chaux agricole concerne sa composition chimique. S’agit-il de chaux vive ou éteinte, CaO ou Ca(OH)2, dont le coût est élevé du fait de la calcination en CaO du calcaire pulvérisé CaCO3 (d’après un bilan des enthalpies standard de formation à 298 K, cette réaction nécessite au moins 180 kJ par mole de CaCO3 ou 3,2 GJ/tCaO [8], dont une partie peut être amenée sous forme de déchets d’hydrocarbures comme des pneus usagés), ou s’agit-il de calcaire CaCO3 ou dolomite – mélange de CaCO3 et de MgCO3 – finement broyé(e) (et dans ce cas, le coût se réduit surtout à l’énergie électrique pour concasser puis broyer la pierre, d’après [11]). Les sites Internet de différents fabricants de chaux agricoles (les sociétés canadienne Graymont, américaine Pacific Calcium et européenne Lhoist) indiquent qu’il s’agit d’un mélange, plus ou moins variable, des deux. La chaux agricole contiendrait souvent les sous-produits de l’industrie des ciments : poussières de carrière de calcaire et des fours à chaux, résidus de chaux éteinte, ce qui réduirait ses coûts. Le site des affaires agricoles de l’Ontario au Canada indique que l’efficacité de la chaux agricole dépend de sa concentration en Ca et surtout de sa mouture. Elle augmente avec la concentration en Ca et la finesse des grains (0,2 mm et moins). Comme les taux d’application sont exprimés en masse équivalente de chaux CaO (par exemple CaCO3 contient 56 % de CaO), la composition chimique exacte n’a pas d’importance. Le coût minimal est donc de 75 MJe/tCaO ou 275 MJtot/tCaO, qu’on peut arrondir à 0,3 GJtot/tCaO en incluant des coûts divers (travaux de carrière, transport, emballage…).
Pour une région où la chaux sous forme de calcaire est épandue sur toute la sole de maïs, le coût serait de 0,25 GJtot/ha/an ou 0,028 GJtot/tmaïs. En moyenne, sur les États producteurs, le coût est d’environ 0,015 GJtot/tmaïs (55 % des surfaces).
3.1.2.6 Désherbants et pesticides
Le taux d’application en 2001 a été, en moyenne, de 2,4 kg/ha et 0,15 kg/ha respectivement, avec des variations entre États de l’ordre de ±25 % (seuls les coûts financiers ont été reportés pour les années précédentes). Les références font apparaître des coûts de fabrication de ces produits de synthèse entre 300 et 360 GJtot/tproduit, en comprenant les coûts de transport. En prenant la valeur de Shapouri [21], le coût est d’environ 1,0 GJtot/ha ou 0,12 GJtot/tmaïs (avec un taux moyen d’épandage de 0,34 kg/tmaïs). Les dépenses dérivent du pétrole brut pour 45 %, de l’électricité primaire pour 40 % et du gaz naturel pour le reste [22].
3.1.2.7 Bilan des coûts en semence et produits de synthèse en 2001
Le Tableau 6 récapitule les coûts par tonne de maïs en semence et produits synthétiques pour l’année 2001, moyennés sur les neuf États. Ces coûts sont décomposés suivant les trois énergies primaires principales. L’incertitude est estimée à environ 5 % pour N et K2O et 10 % pour les autres.
Dans l’incertitude sur les coûts, nous n’avons pas tenu compte des écarts importants du taux d’application par tonne de maïs suivant les États (qui doivent sans doute exister aussi entre fermes). Cette variation peut refléter des différences de pratiques agricoles ou d’environnements : sol, climat… Les divers documents à notre disposition ne nous permettent pas de préciser cette origine. Pour rendre compte de ces écarts entre États, on considère dans le Tableau 7 les coûts pour deux États : l’État où l’ensemble des coûts est le plus élevé, l’Ohio, et celui où l’ensemble des coûts est le plus faible, le Minnesota (OH/MN). En arrondissant, on obtient 1,9 GJtot/tmaïs pour l’Ohio contre 1,1 GJtot/tmaïs pour le Minnesota.
Dépenses énergétiques pour 2001 en semence et autres produits par tonne de maïs, pour deux États, l’Ohio, OH, et le Minnesota, MN (OH/MN). Décomposition suivant les différents produits et les principales énergies primaries
Table 7 Energy expenditure of seed and other products per metric ton of corn, for two States, Ohio, OH, and Minnesota, MN (OH/MN) in 2001. Decomposition according to the various products and the main primary energies
GJtot/tmaïs | Pétrole | Gaz naturel | Électricité primaire | Total | Incertitude |
Semence | 0,0075 | 0,01 | 0,0075 | 0,025/0,026 | 0,003/0,003 |
N | 0 | 1,5/0,89 | 0 | 1,5/0,89 | 0,08/0,05 |
K2O | 0,010/0,005 | 0,047/0,022 | 0,038/0,018 | 0,095/0,045 | 0,005/0,003 |
P2O5 | 0 | 0 | 0,089/0,053 | 0,089/0,053 | 0,009/0,005 |
CaO | 0 | 0 | 0,025/0,0 | 0,025/0,0 | 0,003/0,0 |
Désherbant | 0,086/0,041 | 0,028/0,013 | 0,076/0,036 | 0,19/0,09 | 0,02/0,01 |
Total | 0,107/0,057 | 1,58/0,93 | 0,22/0,10 | 1,92/1,11 | 0,08/0,05 |
3.1.3 Équipements agricoles
L’équipement le plus utilisé dans une ferme, et donc celui qui s’use le plus vite, est le tracteur. La moissonneuse-batteuse est utilisée seulement au moment des récoltes, et sert sans doute à plusieurs exploitants. Le matériel périphérique tracté et actionné par le tracteur, ayant des utilisations ponctuelles, a une durée de vie plus longue. D’ailleurs, les coûts financiers se répartissent entre 85 % pour les engins motorisés et 15 % pour les autres. Nous allons considérer que 75 % des coûts énergétiques sont dus au tracteur. Un tracteur moyen suppose 110 kW de puissance, pèse environ 6 tonnes (site Internet des vendeurs de matériel agricole New-Holland et Valtra). Le tracteur est composé essentiellement d’acier, plus lourd que l’aluminium, mais moins cher à produire (30 GJtot/tacier en plaque, contre 50 GJe/tAl avant mise en forme). La fabrication, en partant des ressources naturelles, d’un camion de 7,2 t de masse à vide, dont six tonnes d’acier et une tonne d’aluminium environ ont coûté 500 GJtot, dont un coût pour l’aluminium d’environ 200 GJtot [5]. Les pneus de rechange sont omis. Sans l’aluminium, on peut assimiler le camion à un tracteur. Son coût est de l’ordre de 300 GJtot. La durée de vie prévue du camion est de 10 ans. Le fabricant de tracteurs Valtra affirme avoir des tracteurs cumulant 22 milliers d’heures de fonctionnement à raison de 3000 h par an (ou 8 h/j et 365 j/an, utilisation intensive sur des champs de canne à sucre au Brésil). Un document de l’agence de la protection de l’environnement des États-Unis indique une durée de vie des moteurs diesel de 100 kW de puissance de l’ordre de 4000 h à pleine charge (ce qui n’est sans doute pas le cas de l’exemple précédent, malgré son utilisation intensive). Par ailleurs, la culture du maïs se déroule sur 130 jours (auxquels on peut ajouter 10 jours pour des travaux de préparation du sol entre les dates de récoltes et de semis de l’année suivante). On peut estimer la durée de vie d’un tracteur exclusivement consacré à la culture du maïs de l’ordre de 14 ans (8 h par jour sur 140 jours par an avec 16 000 h de fonctionnement, avec des charges variables), 18 ans au maximum (avec 21 000 h de fonctionnement).
Il faut également connaître la surface travaillée par le tracteur pour en déduire la quantité de maïs récoltée pendant sa durée de vie. D’après le recensement agricole de 2002 [6], les surfaces consacrées au maïs à grain au niveau des neuf États sont de l’ordre de 100 ha par ferme. En supposant un tracteur par ferme, une durée de vie de 14 ans et un rendement agricole de 8,8 tmaïs/ha, il aura permis la récolte de 13 000 t de maïs, pour un coût de 300 GJtot. En intégrant la contribution des autres engins (25 % du total), le coût des équipements est de l’ordre de 0,030 GJtot/tmaïs. Cette estimation reste assez grossière et peut donc être fausse de plus de 50 % (on prendra ±0,025 GJtot/tmaïs). Il serait nécessaire de faire une étude plus poussée, mais, au vu de la faiblesse de ce poste par rapport aux dépenses d’exploitation, elle n’est pas utile. Étant donné l’origine sidérurgique des matériaux, grossièrement deux tiers de l’énergie primaire est du charbon, le reste étant de l’électricité.
3.2 Dépenses au niveau des usines
3.2.1 Procédés de production de l’éthanol
Dans ces usines, le grain de maïs est broyé pour séparer ses différents constituants, dont l’amidon (70 % en masse du grain sec ou 62 % du grain avec 15 % d’humidité en moyenne [11]). Il passe ensuite par plusieurs étapes de transformation biologique, chimique et physique (liquéfaction et hydrolyse enzymatiques de l’amidon pour obtenir des sucres, fermentation par levures des sucres en alcool, distillation de l’éthanol et évaporation de l’eau résiduelle) pour produire l’éthanol anhydride [4].
L’hydrolyse de l’amidon – un polysaccharose – fournit le glucose, suivant la réaction :
Une mole d’amidon à n monomères de masse molaire 162 g va fournir n moles de glucose de masse molaire 182 g. La réaction est activée par des enzymes (amylase et glucoamylase). Leur consommation varie de 250 à 300 g/m3EtOH [4]. Nous négligeons le coût énergétique associé. Le glucose est ensuite fermenté suivant :
Une mole de glucose (182 g mol−1) donne deux moles d’éthanol (2 × 46 g mol−1) et deux moles de dioxyde de carbone. Le rendement massique théorique serait de :
En réalité, d’autres réactions ont lieu lors de la fermentation [4]. Le rendement dit de Pasteur, tenant compte de réactions inévitables (production de glycol, 3 %, autoconsommation des levures, 1 %…), est de 0,419 m3EtOH/tmaïs. Le rendement actuel varie de 0,40 à presque 0,42 m3EtOH/tmaïs (pour les conversions, la valeur de 0,41 sera prise). Le rendement actuel est donc très proche du rendement théorique, indiquant de très faibles gains de rendement, et donc d’énergie, dans l’avenir. D’un point de vue thermodynamique, les réactions globales ci-dessus sont exothermiques, en particulier lors de la fermentation des sucres (rupture de liaisons C–C et C–H pour former du CO2). La chaleur dégagée – 1,2 MJ/kgEtOH [4] – doit être évacuée pour maintenir les levures à une température optimale de 30–35 °C. La chaleur nécessaire lors de la distillation, de la concentration des effluents et du séchage des résidus représente une dépense importante d’environ 6,5 GJ/tetOH. La solution d’éthanol obtenue après fermentation (contenant au plus 12 % d’éthanol en volume, comme pour un vin) doit être distillée pour obtenir le produit pur. L’importante dilution des solutions est nécessaire pour éviter l’empoisonnement des microorganismes par le glucose et l’éthanol. Du fait de l’existence d’un azéotrope de l’éthanol avec l’eau à 96 % en masse (il se comporte vis-à-vis de la distillation comme un corps pur), la purification complète nécessite l’utilisation de procédés plus complexes et plus coûteux. Cette dernière étape était auparavant effectuée avec l’ajout d’un solvant organique (benzène ou cyclohexane) pour une distillation ternaire. Elle est actuellement réalisée par passage de la vapeur de l’azéotrope sur des tamis moléculaires absorbeurs d’eau, procédé moins coûteux (0,2 GJ/tEtOH [4]). À cela s’ajoutent les dépenses en électricité pour le fonctionnement de concasseurs, broyeurs, pompes, agitateurs et centrifugeuses.
Il existe deux procédés distincts pour récupérer les résidus ou sous-produits de la production d’éthanol, qui différencient aussi les deux types d’usines d’éthanol [23]. Le procédé dit humide sépare et récupère les constituants du grain autres que l’amidon (germes riches en huile, fibres et gluten riches en protéine) avant l’action enzymatique. Ce procédé n’est pas destiné à produire spécifiquement de l’éthanol (il peut également produire du sirop de maïs, mais au détriment de l’éthanol). Il donne des sous-produits (huile, son et gluten de maïs) mieux valorisables que ceux donnés avec l’autre procédé. À part l’huile, ils sont vendus comme aliment d’élevage. Il nécessite, en revanche, plus d’énergie par volume d’éthanol produit. Le deuxième procédé, dit à sec, est beaucoup plus orienté vers la production d’éthanol. Les constituants non fermentables ne sont récupérés qu’à la fin du procédé. Ils sont séchés et mis ensemble pour constituer les résidus secs de distillation (à 10 % d’humidité). Les unités de production sont plus petites et nécessitent donc un investissement financier plus faible que pour le procédé humide.
Procédé humide : rendement de conversion pris à 0,40 m3EtOH/tmaïs
3.2.2 Capacités et production des usines fin 2005
Début 2001, il y avait 54 usines d’éthanol avec une capacité totale de 7,3 Mm3/an, répartie de manière à peu près égale entre les deux procédés [11]. La production d’éthanol en 2000 a été de 6,1 Mm3, soit 85 % de la capacité. Début 2006, le nombre d’usines est passé à 95, avec une capacité totale de 16,4 Mm3/an, les nouvelles usines utilisant principalement le procédé à sec. Vingt-neuf nouvelles unités sont en construction et neuf autres vont s’agrandir [19]. La production d’éthanol en 2005 a été de presque 15 Mm3 (14,8 Mm3). Plus de 36 Mt de grains de maïs ont été utilisées, représentant environ 13 % de la récolte de grains de maïs des États-Unis en 2005 (280 Mt) ; 256 kt d’huile de maïs, 430 kt de gluten de maïs et 2400 kt de son ont été produits par le procédé dit humide, d’où une production d’éthanol par ce procédé de 4,0 Mm3. Sa capacité est d’environ 4,5 Mm3 (début 2001 la capacité représentait 4,0 Mm3, d’où une faible progression). Les usines utilisant le procédé à sec, avec une capacité de 12 Mm3, ont produit presque 11 Mm3 d’éthanol en 2005. La production de résidus aurait dû être de presque 8,5 Mt, mais une petite partie n’a pas été séchée pour économiser le coût de séchage et a été vendue à proximité comme fourrage. La production réelle a été de 9 Mt.
3.2.3 Dépenses en énergie des usines
Les coûts d’investissement (énergies indirectes pour la fabrication et l’assemblage des matériaux de construction et pour les équipements des usines) sont sans doute négligeables, étant donné la rapidité de construction de ces usines (deux ans ou moins), leur durée de vie prévue (20 ans) et le faible investissement financier. Ces coûts ne font d’ailleurs pas l’objet de controverses.
Les données concernant les coûts d’exploitation et les caractéristiques des usines construites après 2001 sont issues d’une enquête directe, précise et exhaustive, auprès des gérants et fabricants d’usines (annexe 4 du rapport [11]). Les dépenses brutes sont données en PCS et quantité d’électricité par volume d’éthanol produit. L’expression des dépenses brutes par volume d’éthanol évite les incertitudes liées à la conversion entre boisseau de grains et volume d’éthanol obtenu. On peut calculer les dépenses de ces usines suivant le procédé utilisé et en se fondant sur la situation en 2005 pour les pondérations de moyenne [19].
3.2.3.1 Procédé à sec (75 % de la production de 2005)
Les usines utilisant ce procédé seront toutes assimilées aux nouvelles usines, étant donné le poids de ces dernières en 2005 et le faible écart de consommation entre les nouvelles et les anciennes. Treize pour cent des unités de production d’avant 2001 utilisent du charbon, tandis que toutes les unités après 2001 brûlent du gaz naturel. La part du charbon est donc négligeable. Il semble qu’aucune usine n’utilise la cogénération (c’est-à-dire la production, à partir du combustible, de la vapeur ou de la chaleur et de l’électricité) [11,19]. La consommation d’énergie est de 11 GJ/m3EtOH (PCS) et 0,72 GJe/m3EtOH. En tenant compte des pertes en amont pour le gaz naturel et du facteur de conversion électrique on a :
Ces dépenses correspondent à une production de résidus séchés jusqu’à 10 % d’humidité. Cependant, en 2005, une économie de séchage a été faite, correspondant à entre 500 et 600 kg d’eau non évaporée (pour 11 Mm3 d’éthanol produit). En prenant un coût de séchage de 4 GJtot/teau, l’économie attribuée au gaz naturel est d’environ 0,2 GJtot/m3EtOH. Le coût est donc de 11,3 GJtot/m3EtOH (gaz naturel) et de 2,67 GJtot/m3EtOH (électricité primaire).
3.2.3.2 Procédé humide (25 % de la production de 2005)
Le coût moyen est de 15,5 GJ/m3etOH (PCS) en combustible (75 % de charbon et 25 % de gaz naturel) et 0,70 GJe/m3EtOH en électricité achetée à l’extérieur (quelques centrales produisent une partie de leur électricité par cogénération [11,19] ; cette partie n’est bien sûr pas comptée dans les dépenses). En tenant compte de la part de chaque combustible et de leur perte en amont, le coût total en combustible est de 15,8 GJtot/m3EtOH (charbon et gaz) et de 2,81 GJtot/m3EtOH (électricité primaire).
3.2.3.3 Coût moyen
En pondérant par la part de production de chaque procédé, le coût total est de :
- • combustible : 12,3 GJtot/m3EtOH, dont environ 22 % en charbon et 78 % en gaz naturel ;
- • électricité primaire : 2,70 GJtot/m3EtOH.
Le total donne environ 15 GJtot/m3EtOH, ce qui représente plus de 70 % du PCI de l’éthanol (21,3 GJ/m3EtOH). L’incertitude est faible : moins de 5 % (elle sera prise à ±2 GJtot/m3EtOH).
Est-il possible de diminuer ces dépenses, les plus élevées de la filière ?
Une source d’économie proviendrait de la concentration de l’amidon en solution avant hydrolyse et de celle de l’éthanol avant la distillation [44]. Cependant, cela demande de ne pas augmenter la viscosité de la solution d’amidon et de disposer de levures résistant aux fortes concentrations en éthanol. La résolution de ces deux contraintes fait l’objet d’études de recherche, et les solutions ne sont donc pas encore opérationnelles.
Il existe cependant d’autres façons d’améliorer le rendement avec des procédés maîtrisés. Une usine de procédé à sec fonctionne depuis avril 2007 à Mead, dans le Nebraska ; elle utilise le gaz produit par méthanisation de matière organique dans deux digesteurs de 15 000 m3 chacun [15]. La matière organique du digesteur provient des résidus liquides de la distillation (ou vinasse) et de 270 000 tonnes par an de déjection de 28 000 têtes de bétail à l’engraissage à proximité de l’usine. Les résidus filtrés de la distillation sont utilisés sans séchage pour l’alimentation du bétail à l’engraissage. L’économie de séchage des résidus et le gaz des digesteurs permettraient à l’usine de réduire ses dépenses d’énergies externes aux seules dépenses d’électricité, représentant ainsi seulement 12,5 % du PCI de l’éthanol. L’usine produit 95 000 m3 d’éthanol par an, c’est-à-dire environ 0,5 % de la production actuelle des États-Unis. Elle n’est donc pas représentative de la situation en 2007, et encore moins de celle de 2005. Cette usine montre néanmoins que des économies importantes sont possibles. Cependant, la généralisation du procédé ne se fera pas rapidement, à cause des temps de retour d’expérience sur l’usine pilote avant un déploiement et un investissement importants, et à cause des délais de construction à grande échelle d’une infrastructure plutôt lourde. D’autre part, une grande partie, voire peut-être même la totalité des résidus – la proximité d’un élevage est sans doute difficilement généralisable – sera utilisée dans le digesteur au détriment de la fabrication d’aliments pour bétail. La pression des éleveurs pourrait ralentir cette généralisation (mais il s’agit là d’une contrainte en dehors de l’analyse énergétique). Il est à noter que l’économie est réalisée grâce au procédé de méthanisation et non pas celui de production d’éthanol.
3.2.4 Gain des sous-produits
Ce point est sujet à fort débat. Certains auteurs considèrent que, n’étant pas une ressource énergétique, il n’y a pas lieu de considérer leur gain (ils recommandent même d’en faire des engrais naturels pour éviter l’appauvrissement des sols [16]). D’autres répartissent les dépenses de production de l’éthanol au prorata des masses des sous-produits et de l’éthanol obtenus, c’est-à-dire le cas le plus favorable dans l’estimation des dépenses pour réduire les coûts [21], à l’opposé d’ailleurs de leurs précédents articles [20,22] ou de ceux de leurs collègues [11]. Le rendement énergétique établit le taux de dépenses en énergie primaire par rapport au pouvoir calorifique de la ressource énergétique transformée par la filière. Les sous-produits de l’industrie de l’éthanol ne sont pas utilisés comme ressources énergétiques, mais exclusivement comme aliments, principalement pour l’élevage. Or, l’alimentation n’est pas une énergie primaire, même si elle possède un pouvoir calorifique. Si les différentes énergies primaires sont interchangeables pour leurs divers usages énergétiques, au moins en théorie, les énergies primaires ne peuvent pas se substituer aux aliments. Dans le cas de l’éthanol, l’objectif est même de produire de l’énergie, en défaut, à la place d’aliments, en excès. Si le pouvoir calorifique des aliments devait être assimilé à un gain énergétique, il serait alors plus intéressant de fournir directement les grains de maïs aux élevages, car les lourdes dépenses en usine seraient évitées et les gains plus importants (avec le PCS des grains de 16 GJ/tmaïs, le taux T serait de 14 % au lieu de 86 %, voir le paragraphe 4 de synthèse).
Le gain énergétique qu’apportent les sous-produits ne peut qu’être indirect. Il représente l’économie d’énergie réalisée en utilisant les sous-produits à la place d’autres aliments qui auraient nécessité de l’énergie pour leur production. Graboski [11] est celui qui donne le plus de détails pour estimer ce gain. Notre estimation suit sa démarche en la simplifiant et en utilisant les données de production de 2005. En 2005, les sous-produits du procédé à sec, 8,5 Mt à 10 % d’humidité, ainsi que le son (2,4 Mt) et le gluten de maïs (0,43 Mt) du procédé humide, sont utilisés comme aliments pour les ruminants à plus de 75 %, pour les porcs à presque 20 % et pour les volailles pour le reste. Deux cent cinquante-six kilogrammes d’huile, vendue comme substitut à l’huile de soja dans l’alimentation humaine, ont été aussi extraits des grains de maïs. Pour simplifier les calculs, les sous-produits destinés à l’élevage sont supposés ne servir de nourriture qu’aux ruminants. Ces animaux ont un appareil digestif qui permet de mieux utiliser, par rapport aux porcs et surtout aux volailles, les qualités énergétiques et nutritionnelles des sous-produits de l’éthanol. La ration du bétail est fixée de manière à avoir des apports caloriques et protéiniques suffisants et permettant de compenser les déficits en acide de lysine introduits par les dérivés du maïs. Graboski établit alors une ration qui comprend jusqu’à 20 % de sous-produits et la compare avec une autre ration équilibrée sans les sous-produits de la production de l’éthanol. La composition alimentaire prévue pour 2012 par Graboski est celle qui se rapproche le plus en pourcentage de la composition entre les sous-produits des différents procédés de l’industrie de l’éthanol en 2005. Elle sera choisie pour notre estimation. Les deux régimes équivalents nutritionnellement se composent, en quantité totale :
Régime avec les sous-produits | Régime sans les sous-produits | |
Sous-produit de l’éthanol | 11,3 Mt (20 %) | 0 |
Maïs entier | 28,3 Mt (50 %) | 36 Mt (60 %) |
Autres (souvent sous-produits de l’agroalimentaire) | 17 Mt (30 %) | 17,5 Mt |
Tourteau de soja | 0 | 1,0 Mt |
Grains de soja entiers | 0 | 5,5 Mt |
Total | 56,6 Mt | 60 Mt |
Les 250 kt d’huile de soja que peut remplacer l’huile de maïs sont extraits de 1,5 Mt de grains de soja entiers. Il en résulte aussi la production de 1,0 Mt de tourteau de soja (le reste est formé des enveloppes des gains). Pour chaque ingrédient de chaque ration, sont associées les dépenses d’énergie nécessaires à leur production. Les sous-produits ont une dépense nulle (les dépenses sont toutes associées à l’éthanol). Le transport n’est pas compté, en le supposant identique pour les deux régimes. La différence de coûts entre chaque ration pour les ingrédients autres que le maïs et le soja est négligée. Le gain provient donc du coût pour produire 7,7 Mt de maïs entier, 7,0 Mt de soja entier et pour transformer 1,5 Mt de grains de soja en huile et en tourteau. D’après les coûts donnés pour le soja [11] et notre estimation pour ceux du maïs (Tableaux 4 et 5, coût moyen en 2001), nous avons :
- • coût maïs entier (ferme) avec 2,0 GJtot/tmaïs, soit 15,4 MGJtot ;
- • coût soja entier (ferme) avec 2,7 GJtot/tsoja, soit 19,0 MGJtot ;
- • coût soja transformé (industrie) avec 2,3 GJtot/tsoja, soit 3,5 MGJtot.
Les coûts de concassage des deux premiers aliments sont négligés. La différence de coût entre les régimes doit être ramenée à la quantité associée d’éthanol (15 Mm3 d’éthanol en 2005) :
- • gain sur le maïs par mètre cube d’éthanol : 1,03 GJtot ;
- • gain sur le soja entier par mètre cube d’éthanol : 1,30 GJtot ;
- • gain sur le soja par mètre cube d’éthanol : 0,25 GJtot ;
- • total 2,6 GJtot/m3etOH.
Le gain par rapport au PCI de l’éthanol est donc 0,12 Jtot/JEtOH. L’incertitude est importante et sera prise à presque 20 % ou ±0,5 GJ/m3EtOH ou ±0,024 Jtot/JEtOH.
3.3 Transport du maïs et de l’éthanol
3.3.1 Transport des grains de la ferme à la distillerie
Ce transport se fait en camion ou remorques agricoles, car les distances sont relativement faibles, inférieures à une centaine de kilomètres. Il se fait en deux étapes, un transport de la ferme à la coopérative locale, de 15 km en moyenne, et un trajet des coopératives à l’usine d’éthanol, de 80 km en moyenne [11]. Estimer le coût énergétique du transport, connaissant la masse à transporter et la distance, nécessite la donnée du coût du transport par unité de distance et de charge utile. Nous avons utilisé les coûts unitaires, en tonne de charge utile et en kilomètres, fournis par l’étude « explicite » menée en 2002 pour l’Ademe (via [1]). Les coûts sont donnés en fonction du type de déplacement et du type de véhicule et comprennent le trajet de retour à vide (par rapport aux données initiales, les valeurs ont été converties en MJ/(t km)). Il est à noter que ce coefficient de coût n’est pas très physique, car une très grande partie des coûts ne dépend pas de la charge utile et est fonction de la vitesse, de la surface frontale et de l’aérodynamisme du camion. Pour la distance de 15 km, on a supposé un chargement pour un camion de catégorie de charge utile entre 3 et 6,5 t, avec un coût de 2 MJ/(t km), soit 30 MJ/tmaïs. La seconde partie du trajet est réalisée par un poids lourd de catégorie de charge utile entre 13 et 25 t, avec un coût de 1,7 MJ/(t km), donnant un coût de 136 MJ/tmaïs sur 80 km. Le coût total est donc de 166 MJ/t. En tenant compte du coefficient de rendement pour obtenir le carburant, diesel, à partir du pétrole brut, le coût est de 200 MJtot/tmaïs ou, avec la conversion de 0,41 m3EtOH/tmaïs, 480 MJtot/m3EtOH (2,2 % du PCI de l’éthanol). Graboski indique une valeur très proche de 490 MJtot/m3EtOH [10,11].
3.3.2 Transport de l’éthanol de l’usine aux stations à essence
Les étapes du transport de l’éthanol à la station à essence ainsi que la consommation de carburants par kilomètre et par tonne de charge utile sont détaillées dans les références [22] et [23]. Entre les usines d’éthanol et les centres de mélange et de stockage des carburants, le transport se fait par camion citerne sur une distance moyenne de 130 km, avec un coût de 1,5 MJ/(t km). Du centre aux dépôts locaux, le transport du carburant contenant de l’éthanol se fait surtout en train ou par voie fluviale à cause des distances, environ 1100 km, à un coût de 0,27 MJ/(t km). Pour la dernière étape, des dépôts aux stations d’essence, sur une distance moyenne d’environ 40 km, le trajet se fait en camions citernes (2 MJ/(t.km)). Le coût global est de 450 MJ/m3EtOH (2,1 % du PCI de l’éthanol). Malgré les distances, il est plus faible que pour le transport de grains. Deux raisons à cela : un moyen de transport plus économique et un pouvoir calorifique massique utile plus concentré entre l’éthanol et le maïs. Pour les deux dépenses de transport, l’incertitude est prise entre 5 et 10 %.
4 Synthèse, calcul du taux de dépenses en énergie et comparaisons
4.1 Taux de dépense en énergie sans gain des sous-produits
Suivant la méthodologie décrite dans la référence [7], nous déterminons le taux de dépenses T0 en prenant le rapport entre les dépenses et le gain énergétiques de la filière (T0 = Dtot/G). Dans un premier temps, le gain se réduit à celui du produit principal, l’éthanol. Le gain et T, en incluant les sous-produits, sont estimés dans le paragraphe suivant. Pour établir les taux de dépense, les dépenses calculées précédemment sont ramenées par unité de volume d’éthanol (à l’aide de la conversion 0,41 m3EtOH/tmaïs), puis par unité de pouvoir calorifique d’éthanol (PCI = 21,3 GJ/m3EtOH). Les valeurs obtenues sont données en pourcentages dans le Tableau 8.
Détail et total des dépenses énergétiques de la filière éthanol en % du PCI de l’éthanol, depuis le champ de maïs jusqu’à la station d’essence
Table 8 Itemized and overall energy expenditure of the corn/ethanol processing as a fraction of the ethanol LHV, from the cornfield to the gasoline station
Jtot/Jéthanol en % | Dérivés pétrole | Gaz naturel | Charbon | Électricité primaire | Total par dépense | Incertitude |
Carburants + séchage 2001 (1) | 5,27 | 0,27 | 0,71 | 6,3 | ±0,4 | |
Carburants + séchage 1996 (2) | 8,13 | 0,55 | 3,66 | 12,0 | ±0,9 | |
Engrais 2001 des 9 États (3) | 0,84 | 13,1 | 1,8 | 15,7 | ±0,8 | |
Engrais 2001 Ohio (4) | 1,2 | 18,1 | 2,5 | 21,8 | ±0,9 | |
Engrais 2001 Minnesota (5) | 0,7 | 10,6 | 1,1 | 12,4 | ±0,8 | |
Supplément irrigation 2001 (6) | 9,4 | 6,4 | 13 | 29 | ±4 | |
Équipements agricoles (7) | 0,23 | 0,12 | 0,35 | ±0,25 | ||
Usines éthanol en 2005 (8) | 45,0 | 12,7 | 12,7 | 70,4 | ±2 | |
Transport maïs et éthanol (9) | 4,4 | 4,4 | ±0,4 | |||
Total moyen en 2001 (1) + (3) + (7) + (8) + (9) | 10,5 | 58,3 | 12,9 | 15,3 | 97,0 | ±2,3 |
Pour rappel, l’électricité primaire regroupe toutes les énergies primaires utilisées pour produire l’électricité consommée dans la filière ; la part de chacune des énergies a été estimée par la production sur les neuf États étudiés (73 % charbon, 20 % nucléaire et 4 % gaz naturel pour les principales énergies). La première ligne du tableau concerne les dépenses de carburants et de combustibles pour le séchage effectuées en moyenne en 2001 sur les neuf États étudiés, sauf le Nebraska. La deuxième concerne les dépenses de carburants et de séchage effectuées en moyenne en 1996 dans les neuf États, sauf le Nebraska. La troisième ligne du tableau donne les dépenses de matériel consommable (engrais…) effectuées en moyenne en 2001 sur les neuf États. Les quatrième et cinquième lignes concernent les mêmes dépenses, mais seulement pour l’Ohio et le Minnesota, respectivement. La sixième ligne du tableau représente les dépenses de pompage en 2001 pour la partie de la récolte de l’État du Nebraska qui a nécessité une irrigation par nappe d’eau souterraine. Le coût des équipements agricoles est estimé sur la septième ligne. La huitième ligne indique les dépenses totales en usine. La neuvième ligne donne les dépenses en carburant pour le transport des grains et de l’éthanol (les coûts indirects des camions et des trains ont été négligés au vu du faible coût des équipements agricoles, plus sollicités). Il est rappelé que les incertitudes sont représentées par un écart-type et que l’écart-type total est la racine carrée de la somme des carrés des écarts-types des différentes dépenses, supposant leur indépendance (suivant la théorie des probabilités). Les résultats s’appuient sur les données brutes accessibles les plus récentes, celles de 2001 pour la ferme et celles de 2005 pour l’usine. L’année 2001 a présenté des températures élevées, mais sans excès, avec des précipitations moyennes (données du service NASS de l’USDA, confirmées par nos comparaisons de dépenses par rapport à 1991 et 1996). Son rendement agricole a été le plus élevé par rapport aux années précédentes. D’après les informations données par l’USDA et par le National Climatic Data Center (NCDC), les années suivantes ont présenté des températures plutôt chaudes, voire très chaudes, avec une pluviosité correcte (sauf 2002 et en partie 2006). La météorologie de ces années est proche de celle de 2001. La différence porte essentiellement sur la hausse du rendement agricole, passant de 8,75 tmaïs/ha à 9,5 tmaïs/ha entre 2001 et 2005, due aux améliorations apportées aux plants de maïs. Comme les dépenses, même à la ferme, sont presque toutes proportionnelles à la masse de maïs récoltée et non à la surface, les données de dépenses en 2001 pour la ferme peuvent être utilisées pour l’année 2005.
Pour produire 100 J d’éthanol en 2001 sans pompage d’eau pour irrigation, il a été dépensé :
- • sur les neuf États : 97 ± 2 J ;
- • pour l’Ohio (le moins efficace en engrais) : 103 ± 2,5 J ;
- • pour le Minnesota (le plus efficace en engrais) : 93,5 ± 2 J ;
- • pour les fermes du Nebraska irrigant par pompage : 126 ± 5 J.
En prenant les dépenses de carburant et de séchage à la ferme de 1996, où les précipitations ont été plus élevées qu’en 2001 (et en maintenant les autres coûts identiques à ceux de 2001), le coût est de : 103 ± 2,5 J.
En moyenne, sur les États considérés, ces dépenses ont été en 2001 sous forme de gaz naturel pour environ 60 %, de charbon pour 24 %, de pétrole pour 10 %, et de chaleur nucléaire pour 4 %. Le reste représente les énergies renouvelables (biomasse, hydroélectrique).
Pour l’usine utilisant du gaz issu de la méthanisation des résidus, le taux de dépenses est de 39 ± 2 GJ (en prenant les taux moyens de 2001 hors irrigation pour les autres dépenses).
La Fig. 1 illustre l’ensemble des éléments de la chaîne de production de l’éthanol, complétée des valeurs des flux en énergie primaire des différentes étapes pour produire à partir du maïs 100 J d’éthanol et économiser 12 J en sous-produits utilisés en aliments d’élevage. La figure a été obtenue à partir des données moyennes en 2001 pour la ferme (hors irrigation), en 2005 pour le parc d’usines du Tableau 8.
4.2 Taux de dépenses avec gain des sous-produits
Pour tenir compte du gain apporté par les sous-produits, le taux de dépenses T doit s’écrire :
(1) |
L’écart-type de l’incertitude sur T, σT, s’obtient à partir de ceux de T et α, σT0 et σα, tenant compte du fait que T est le produit des deux autres :
En remplaçant les expressions par les valeurs correspondantes, le taux de dépenses moyen pour 2001 est donc de 86 ± 3 %. En conclusion est donnée la décomposition de ce taux suivant les différentes étapes de la filière et suivant les énergies primaires, ainsi que ses variations avec des paramètres comme l’utilisation du pompage pour irriguer.
Pour l’usine utilisant la méthanisation des résidus, le taux de dépenses est de 37 ± 2 % (en supposant que, par rapport aux autres usines, un tiers des résidus est valorisé en aliment de bétail).
4.3 Comparaison avec la filière essence
L’éthanol pour carburant est généralement utilisé aux États-Unis comme additif direct à l’essence jusqu’à hauteur de 10 % en volume [4]. Un nouveau type de véhicule, la voiture à carburant modulable, qui accepte jusqu’à 85 % d’éthanol, est en train de se développer. Dans tous les cas, l’éthanol est un substitut à l’essence et il est donc intéressant de comparer leurs taux de dépenses respectifs suivant l’expression (1). Pour l’essence, le taux est calculé à partir du facteur d’efficacité ɛ de l’USDOE [14] vu au § 2.3.2, ɛ = 0,80.
La filière éthanol peut être aussi vue comme un procédé de transformation du gaz naturel et du charbon en essence. Elle peut alors être comparée à la filière de production d’hydrocarbures liquides par transformation thermochimique du charbon ou du gaz. La transformation thermochimique du gaz par le procédé Fischer–Tropsch présente un rendement de conversion d’environ 55 %. La « transformation » du gaz et du charbon en éthanol dans la filière étudiée ici est donc plus efficace, avec un rendement de conversion d’environ 120 %, d’après le Tableau 8.
Ces différentes façons de présenter le rendement de la filière éthanol ne peuvent pas faire l’économie d’une étude directe de la disponibilité des ressources : disponibilité en surface agricole avec les contraintes pour maintenir leur fertilité, disponibilité à terme des ressources fossiles et minérales consommées… Cette étude, complément indispensable à l’analyse énergétique [7], doit faire l’objet d’un autre article en raison de sa longueur et n’est donc pas abordée ici. On peut seulement noter que la production de gaz naturel aux États-Unis a commencé à décliner ; l’administration prévoit une augmentation des importations [3]. On peut aussi remarquer que, s’il faut cultiver le maïs dans des régions plus arides, le taux de dépenses risque d’augmenter, de l’ordre de 25 % d’après le Tableau 8.
4.4 Modification du taux pour une comparaison plus large
Le taux calculé avec la formule (1) ne permet pas de faire de comparaison aisée avec d’autres filières utilisant la biomasse pour produire une forme d’énergie utilisable dans les transports. En effet, la filière éthanol pourrait être comparée avec le procédé de fermentation méthanique qui produit à partir de la plante entière du méthane (après épuration), utilisable dans une voiture au gaz naturel ou brûlé pour produire de l’électricité utilisée dans les transports [4] ; il en va de même pour des procédés comme la pyrolyse, la gazéification… [4]. Même dans le cadre plus restreint des filières produisant des carburants, le taux issu de (1) ne tient pas compte de la différence de valorisation énergétique en aval au niveau du véhicule (différence de rendement thermodynamique entre moteur diesel et moteur essence, écart de consommation entre véhicules suivant leur masse et géométrie…). En amont, elle ne permet pas non plus de comparaison avec des filières produisant des carburants à partir de la plante entière (procédé d’hydrolyse/fermentation éthanolique de la biomasse lignocellulosique, procédé de gazéification suivi d’une synthèse et d’un hydrocraquage… [4]).
Pour réaliser cette comparaison, il est nécessaire d’élargir la filière, de manière à partir d’une même ressource naturelle (ici, la plante) et à parvenir à une même forme d’énergie (énergie mécanique Em en sortie du moteur du véhicule, voire au niveau de la roue). Le gain G correspond alors au pouvoir calorifique de la biomasse (PCS) et les dépenses associées à G comprennent les énergies dissipées entre la forme initiale associée à G et la forme finale Em + Gsp (la valorisation énergétique des résidus, directement ou indirectement, doit être incluse dans la forme finale). T s’écrit :
(2) |
Cette formule peut être réarrangée pour faire intervenir une énergie intermédiaire, carburant, électricité, gaz naturel…, dont le pouvoir calorifique associé à G est Gint (quantité d’énergie produite par GJ de biomasse) :
(3) |
Dans T ont été introduits le taux intermédiaire T0 = Dtot/Gint et le rendement du moteur Rm = Em/Gint. Dtot inclut toutes les pertes externes, jusqu’à la roue, comme le coût du véhicule. Rm peut se décomposer en Rm1 et Rm2 pour séparer le rendement mécanique du moteur de celui de la transmission jusqu’à la roue. La formule (3) permet d’utiliser des intermédiaires de calculs qui apparaissent plus naturellement lors du traitement des données de base et qui sont utiles pour des comparaisons étape par étape de la filière.
Dans le cas de la filière du maïs, nous allons estimer T d’après (2) ou (3), en prenant comme ressource énergétique initiale le grain de maïs. On pourrait considérer la plante entière, mais, d’une part, à force de sélectivité, feuilles et tiges se sont appauvries en énergie et, d’autre part, ces parties sont nécessaires au renouvellement de la matière organique du sol [11,16]. Il s’agit d’une contrainte environnementale indépendante de l’analyse énergétique, mais dont on peut tenir compte. D’après Shapouri et al. [20], 61 % du pouvoir calorifique se trouve dans l’éthanol, tandis que les résidus en concentrent 39 % (dans le cas du procédé à sec qu’on suppose unique). Il faut ajouter les pertes thermiques dues à la décomposition des molécules d’amidon en glucose (1,2 GJ/tEtOH). Avec PCS(éthanol) = 23,5 GJ/m3EtOH et avec une conversion de 0,41 m3EtOH/tmaïs, on a PCS(grain) ou G = 16 GJ/tmaïs (ou 19 GJ/tmaïs pour le maïs sans humidité) et Gint = GEtOH(PCI) = 8,7 GJ/tmaïs. Gsp/GEtOH vaut 0,12 d’après le § 3.2.4. En prenant un rendement de 30 % pour Rm (réduit à Rm1 ici) et avec les données de 2001, T(éthanol) vaut, du pouvoir calorifique du grain à l’énergie du moteur :
Nous avons supposé que, dans la dernière étape, entre la station d’essence et le moteur, il n’y avait plus que des pertes propres. Du plus économique (Minnesota) au plus dispendieux (partie du Nebraska), le taux varie de 124 à 145 %. Le taux pour l’usine avec digesteurs est de 103 %. Dans tous les cas, le taux dépasse 100 %, indiquant qu’il faut dépenser plus d’énergie extérieure qu’il n’en est récupéré en sortie.
On peut faire une estimation pour la filière essence avec le même raisonnement :
En réarrangeant pour utiliser les données du paragraphe précédent :
Le deuxième terme du produit se situe entre 1 et ɛ = 0,8 selon l’importance des pertes propres par rapport aux pertes extérieures. En prenant 0,9, on a :
Rm est pris identique entre les deux calculs. Entre l’essence pure et un mélange pauvre en éthanol, il ne semble pas qu’il y ait de différence [4]. En revanche, les Brésiliens ont développé un moteur adapté à l’éthanol hydraté (6 à 8 % d’eau en volume), qui améliore Rm de plus de 10 % (avec, en outre, une économie sur le coût de la déshydratation).
5 Conclusion et perspectives
Suivant la méthodologie générale présentée par les mêmes auteurs [7], cet article estime le rendement énergétique R, ou plus précisément son complément par rapport au taux de dépenses T = 1 – R, pour la filière produisant de l’éthanol à partir de maïs aux États-Unis d’Amérique. Le taux ne pourra jamais être plus précis que quelques pourcents, du fait des incertitudes sur les données de base qui ont permis de le calculer. En outre, il présente des variations importantes en fonction de paramètres comme la pluviosité sur un État pour une année donnée ou le procédé utilisé dans l’usine de conversion du maïs en éthanol. Il dépend aussi crucialement du choix fait pour l’énergie finale, éthanol ou énergie mécanique aux roues du véhicule utilisant l’éthanol. Une valeur unique de taux sans son contexte n’a donc aucun sens.
Le taux moyen sur la production en 2005, année chaude, mais suffisamment arrosée, pour les neuf États qui sont les plus importants producteurs d’éthanol (plus de 90 %) et en l’absence d’irrigation de pompage, depuis le champ de maïs jusqu’à la station d’essence et en considérant l’éthanol comme la ressource énergétique primaire, est de 86 ± 3 %, ce qui revient à dire que, pour 100 J d’éthanol produit et d’énergie économisée grâce aux résidus de la filière, 86 ± 3 J d’énergies primaires ont été nécessaires. Les énergies primaires sont sous forme de gaz naturel à 60 %, de charbon à 24 % (dont près de la moitié utilisée pour produire plus 70 % de l’électricité alimentant la filière), de pétrole à 11 %, le reste provenant surtout de la chaleur des réacteurs nucléaires (pour produire plus 20 % de l’électricité de la filière). Parmi ces dépenses, 19,5 J ont été consommés à la ferme (dont 14 J pour les engrais, principalement l’ammoniac), 4,0 J ont servi au transport des grains de maïs et de l’éthanol, et 62,5 J ont été dissipés à l’usine. Le taux varie entre 83 ± 3 % pour l’État du Minnesota, du fait d’un taux d’application d’engrais azotés plus faible, et 112 ± 5 % pour la partie du Nebraska où pomper l’eau du sous-sol est nécessaire à la culture. Le taux moyen de 1996, hors irrigation, a été de 92 ± 3 %, en raison d’une plus forte humidité dans les grains, qui ont nécessité un séchage supplémentaire.
Si le grain de maïs est considéré comme énergie primaire et la filière est étendue jusqu’à l’énergie mécanique à la roue, le taux moyen pour 2005 hors irrigation est d’environ 130 %. Plus d’énergies de filières externes sont utilisées que d’énergies finales ne sont produites, remettant en question la rentabilité de cette filière.
Les économies possibles sur la filière éthanol, compte tenu des techniques connues et maîtrisées peuvent provenir de la fabrication de l’ammoniac en petite partie (avec des usines modernes proches du rendement théorique), de l’utilisation de la cogénération dans les usines, mais surtout de la valorisation énergétique des résidus par méthanisation. Une usine pilote basée sur ce principe, qui a démarré en 2007, permet un taux de dépenses de 37 % au lieu de 86 % (ou 103 % au lieu de 130 % si l’on va jusqu’à la roue).
Par comparaison, le taux de dépenses de la filière qui va du pétrole brut à la roue via l’essence (et que la filière éthanol devrait concurrencer), calculé avec la même méthodologie, est inférieur à 85 %. Cette filière est donc bien plus économique que celle de l’éthanol, et il sera peut-être plus avantageux de produire du pétrole à partir du sable asphaltique, malgré les difficultés, comme au Canada, que de produire de l’éthanol à partir de maïs. Cependant, un comparatif complet doit examiner la disponibilité des ressources de chaque filière (pétrole, mais aussi terres arables propices au maïs, gaz naturel…), comme il est mentionné dans la référence [7]. Cette disponibilité peut dépendre d’un taux de dépenses acceptable, ce qui peut conduire à exclure des terres demandant beaucoup d’irrigation. La question spécifique de la disponibilité des ressources sera traitée dans un autre article.
L’étude de la filière éthanol à partir du maïs, par l’analyse fine en étapes successives depuis l’extraction de la ressource naturelle jusqu’à sa transformation en éthanol comme carburant, nous a permis d’illustrer la méthode conduisant à l’estimation du rendement d’une filière énergétique [7]. La décomposition en éléments de base de la chaîne de la production d’énergie de la filière doit permettre d’accéder, au-delà du coût énergétique de la filière, à son coût environnemental dans le cadre du développement durable (bilans carbone, azote, par exemple).