1 Introduction
The properties of wood fibre materials are highly dependent on the properties of its constituents as well as on the arrangement and properties of the wood polymers. In general, there is a rather good knowledge of how various wood products relate to the fibre properties on a macroscopic level. However, when it comes to the microscopic level in understanding how the different wood polymers interact and contribute to the fibre properties and how these interactions are affected by processing, information is still lacking.
Cellulose is of course the main contributor to the strength properties of the wood fibre with its highly arranged crystalline structure. However, changes occurring in this crystalline and aggregate structure during processing have lately been shown to be of large importance for the properties of the fibres [1]. In this rearrangement also, the hemicelluloses has been claimed to play an important role [2]. For transverse properties of fibres, the hemicelluloses and lignin have also been shown to play a much more important role than the cellulose [3]; it is the reason why a more precise description of the arrangement of these constituents is necessary.
In this article, an effort is made to analyse various factors of importance for the understanding of the relation between the properties of the wood constituents, its ultrastructure and the macroscopic properties of the fibre material.
2 Ultrastructural arrangement
The structural arrangement of the wood polymers within the cell wall could from a mechanistic standpoint be viewed by analogy as a fibre-reinforced composite system, with cellulose fibrils as reinforcing materials in a matrix of lignin and hemicelluloses. The present conception of the arrangement could be illustrated as in Fig. 1.
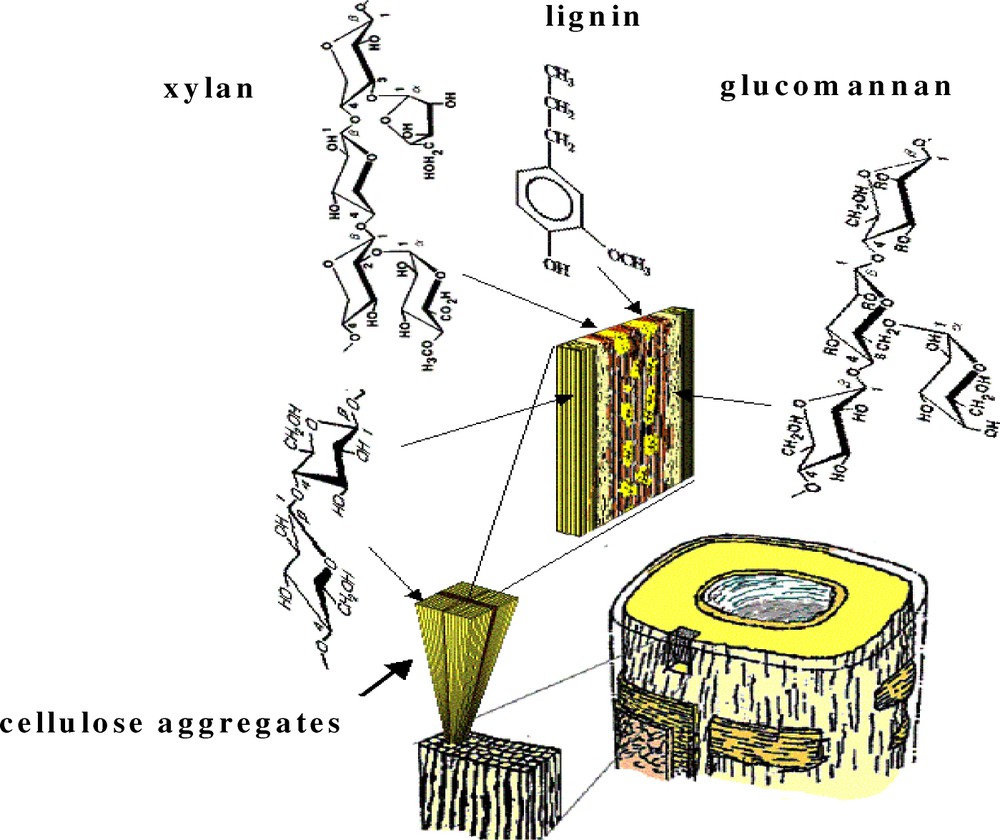
Schematic illustration of the arrangement of the wood polymers within the secondary wall of a softwood fibre (adopted after the original picture of Åkerholm and Salmén [4]).
The cellulose microfibrils in a typical softwood fibre are 3 to 4 nm in cross section [5] and aggregated into larger entities, cellulose aggregates, of an average cross section of 16 to 20 nm [6–8]. Most probably, some of the glucomannans are incorporated into these aggregates [7,9,10]. Adjacent to these aggregates mostly glucomannan is arranged in parallel with the fibrils having a high degree of coupling to them [11]. In the space of 3 to 4 nm in-between these cellulose aggregates [12], it is likely that the lignin matrix is interspaced with xylan entities [13]. Based on spectroscopic data, indications are also that the lignin has an orientation of the phenylpropane units along with the direction of the cellulose aggregates [4]. An orientation of the plane of the aromatic rings of the lignin in the tangential direction of the cell-wall surface has also been demonstrated by Raman studies [14,15]. This lignin although highly ordered in the structure in-between the cellulose aggregates seems to behave more freely; it is shown to exhibit a high degree of viscoelasticity at normal room temperature and humidity conditions in contrast to the more elastic properties of the carbohydrates [16]. For the xylan within the matrix, a preferred orientation has been indicated, i.e. the xylan is not arranged in a random fashion [16]. Presumably the xylan has an arrangement parallel to the cellulose fibrils in similarity with the other wood polymers.
The arrangement of the matrix on a larger scale is that of a tangential lamellation [17] as evident when observing the structure of the cross section of the secondary wall by AFM (Fig. 2). Here it is evident that also the cellulose aggregates line up in rows in the tangential direction [8]. However one must remember that on the three-dimensional level the structure of the cellulose aggregates are probably more resembling the lenticular structure proposed by Boyd [18] schematically illustrated in Fig. 3. Such an undulating behaviour of the cellulose aggregates and microfibrils are what has been observed when viewing the surface structure of the delignified secondary wall by electron microscopic techniques [19]. Thus the matrix material arranged in the tangential structure will be placed as successive disks both along the circumferential direction of the fibre as well as in the length direction of it. The size of these matrix material elements is probably to a high degree reflecting the size of the dissolved lignin particles, i.e. comparable to a spherical diameter of 5 to 10 nm [20,21]. Pore size distribution measurements also indicate that the holes created in the fibre structure from the dissolved lignin and hemicelluloses are in this range; i.e. with a mean diameter of 10 nm [22–24].
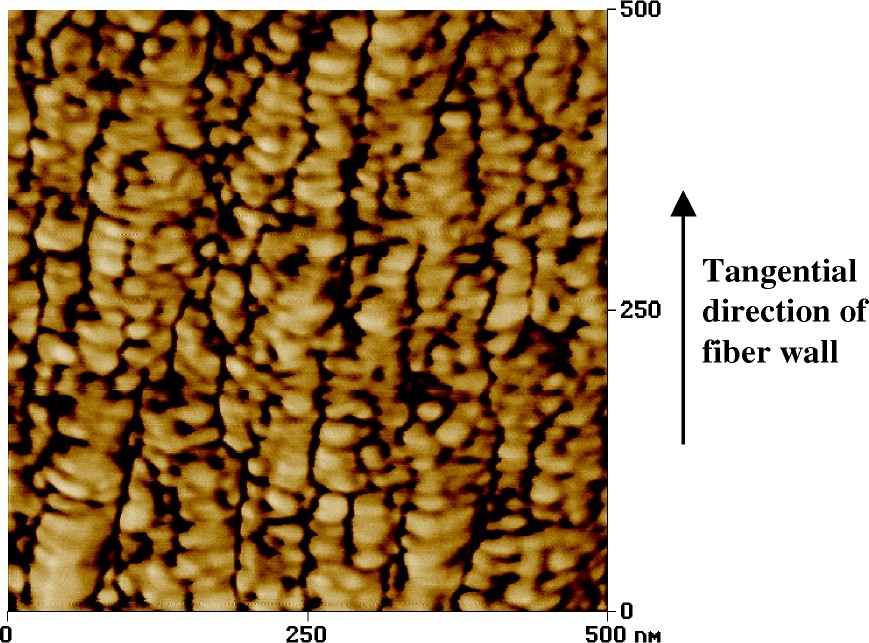
Atomic Force Microscopy (AFM) image of a transverse cross section of the secondary wall of a spruce wood fibre. Cellulose aggregates (lighter parts, averaging 20 nm, arranged in a pattern of tangential lamellation) are evident [8].
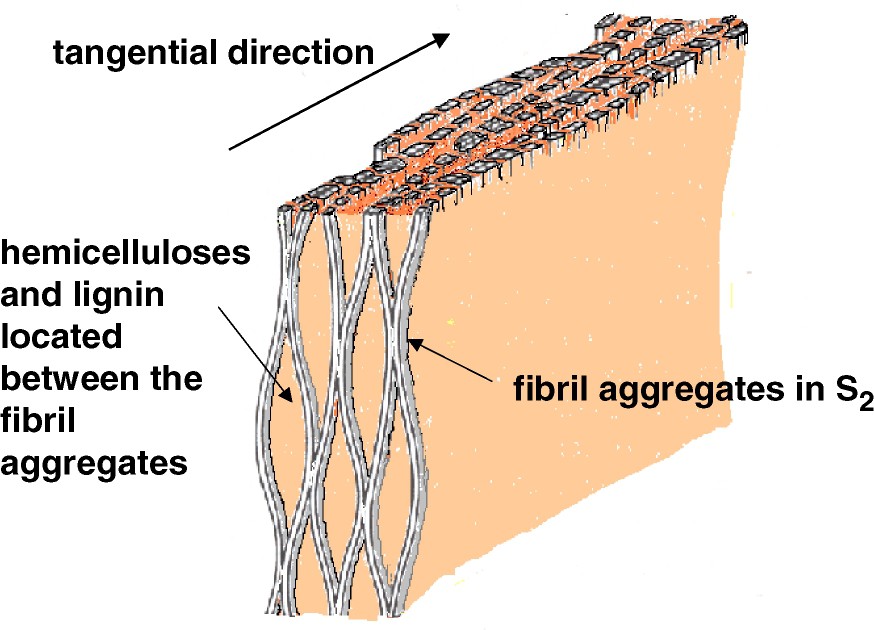
Schematic drawing of the cellulose aggregate structure adopted after the ideas of Boyd [18].
The matrix polymers thus exist in a very homogeneous blend in-between the ‘web’ of the cellulose aggregates. It is also apparent that it is only at the high temperatures in wet conditions above 100 °C, when the lignin softens, that an aggregation of the cellulose takes place, presumably an enlargement of the contract zones in the ‘web’ of the aggregates in Fig. 3 [8]. Based on rheological properties of wood fibres, it is however concluded that lignin and maybe also hemicelluloses exhibit their own separate softening temperatures [13], thus pointing to a mechanically heterogeneous mixture. Such behaviour requires material entities of around 5 to 15 nm in diameter [25,26], a situation that is not at all unrealistic considering the actual wood-fibre wall structure. However, it has from a mechanical point been mathematically shown that the matrix arrangement, i.e. that of a heterogeneous or homogeneous mixture, has very little influence on the elastic properties of the cell wall both along the fibre axis and in the transverse direction [3].
3 Rheological properties of wood polymers
Of the wood polymers, cellulose, hemicelluloses, and lignin, most attention has been given to the cellulose when it comes to determine mechanical properties of the wood constituents. The rationale is of course the cellulose being the stiff reinforcing material in the composite and therefore the component that to a high degree determines the properties of the fibre wall.
3.1 Cellulose
For cellulose there are both theoretical estimates as well as experimental determinations of the elastic properties. Most recent analysis tends to favour values in the longitudinal direction for the cellulose crystalline region between 120 to 170 GPa [27], although there are some older theoretical estimates of such high values as 246 and 319 GPa [28,29]. When comparing theoretical estimates with experiments both for cellulose I as well as the experimentally easier material cellulose II, it seems reasonable to come to a conclusion of a modulus value of ca 134–136 GPa for the stiffness of cellulose I [29].
3.2 Hemicelluloses
For hemicelluloses data are extremely scarce. Cousins' data on extracted xylan fractions [30] indicate an elastic modulus for the dry material of 8 GPa. However, it can be questioned how representative this value is. It is known that hemicelluloses will crystallize when isolated. Recent measurements performed on amorphous hemicellulose films made of Konjac glucomannan (only containing mannose and glucose units) indicate a glassy modulus in the range of 2 GPa and a softened modulus of 20 MPa [31]. It is also known that the hemicelluloses at least the glucomannan is oriented along the cellulose fibrils [11,32,33]. Considering an orthotropic arrangement in the cell wall, a set of reasonable moduli is depicted in Table 1.
Wood polymer data used for model calculations
Polymer | Dry conditions, i.e. 12% moisture, 20 °C | Moist conditions, 20 °C |
Cellulose | ||
134 GPa | 134 GPa | |
27.2 GPa | 27.2 GPa | |
G | 4.4 GPa | 4.4 GPa |
ν | 0.1 | 0.1 |
l/d | 50 000 | 50 000 |
Hemicellulose | ||
2.0 GPa | 20 MPa | |
0.8 GPa | 8 MPa | |
G | 1.0 GPa | 10 MPa |
ν | 0.2 | 0.2 |
Lignin | ||
2.0 GPa | 2.0 GPa | |
1.0 GPa | 1.0 GPa | |
G | 0.6 GPa | 0.6 GPa |
ν | 0.3 | 0.3 |
3.3 Lignin
The lignin structure within the softwood fibre varies from that of a more branched nature in the middle lamella and outer cell walls to that of the normal less branched guaiacyl type in the secondary wall of spruce wood fibres, a fact that also has a bearing on the physical properties [34]. Accurate elastic properties of the lignin in question may therefore be difficult to assess. Under dry conditions, values for an extracted isotropic lignin have been reported to between 4 to 7 GPa [35,36]. However, for the lignin also, an oriented structure along the cellulose fibrils has to be accounted for [4,15]. Reasonable values for lignin at 20 °C and 12% moisture content and wet are given in Table 1. Even under wet conditions, lignin retains the high stiffness up to its softening, above ca 80 °C [13].
4 Properties along fibres
In the fibre direction, a lot of measurements on elastic properties for different cellulosic fibre materials exist. It is quite clear that an important factor determining the elasticity is the fibril angle of the S2-layer. It is also clear that the properties of the cellulose almost solely determine the value of the elasticity, while both the elasticity of the lignin and the hemicelluloses have only a marginal influence [3]. Thus, the factors that govern the longitudinal fibre elasticity are the stiffness of the cellulose, the content of cellulose and the fibril angle of these cellulose microfibrils. This also means that the relative thickness of the S2-layer is of importance [37], as it quantifies the proportion of cellulose fibrils in the longitudinal direction. Variations between species of the relative proportion of the S2-layer in the range from 50 to 80% on a volumetric basis have been found [38]. The thickness proportion of the S2-layer for spruce fibres is though in the range of 80 to 90% [39].
When it comes to comparing theoretical estimates with different experimental measurements the difficulties mostly arises due to the lack of data on the factors of importance such as chemical composition, proportion of different cell wall layers, etc. There are of course also difficulties in the values given for the elastic measurements themselves when it comes to fibres, for which it is often clear that a lot of the fibres have been damaged in the process of isolation [40].
In Fig. 4, the influences of the factors of importance in the longitudinal direction, i.e. the proportion of S2-wall (varied from a typical value of 79% to a more extreme of 84%), and the content of cellulose in the S2-wall (varied from a typical value of 50% to a more extreme of 55%) were estimated together with measurements for wood by Cave [41]. The calculations are based on the data given in Table 1.
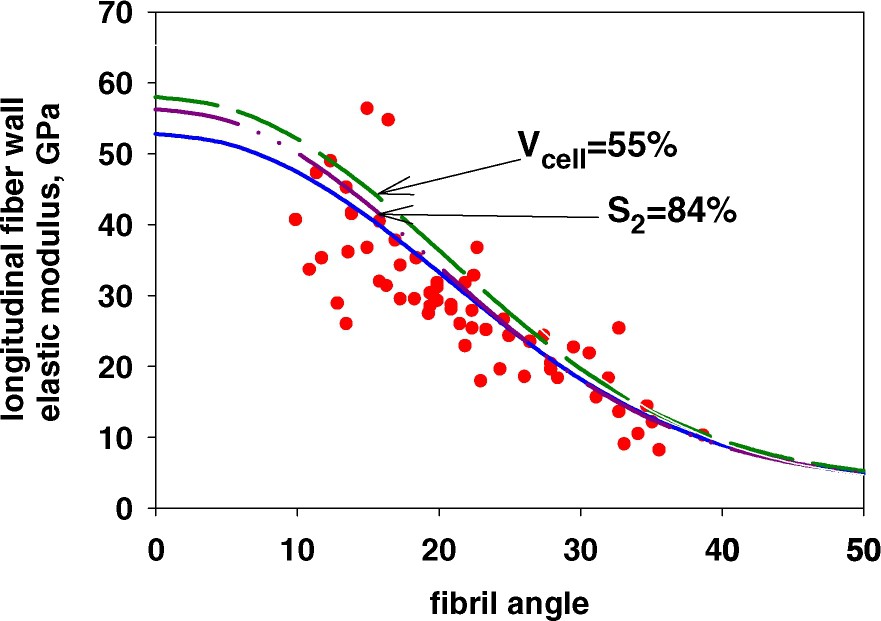
The elastic modulus of the fibre wall of wood in the longitudinal direction as a function of fibril angle in the S2-wall as affected by different factors; cellulose content in the S2-wall and proportion of S2-wall compared to measurements by Cave [41]. Reference values: cellulose content in S2-wall 50%, proportion of S2-wall 79%.
It is clear that most of the upper boundary of the experimental data (undamaged samples) lies within the regions predicted. Thus it is reasonable to assume that the variations seen in the experimental data are due to such natural variations in cell wall structure. The few experimental values that are higher are, as seen above, considerably higher. It could be questioned if these few outliers in modulus value are correct or if most likely they represent measurements for a wood material with a different fibril angle.
5 Properties in the transverse direction
When it comes to the properties in the cross direction to the fibre length data are extremely scarce and problems with sample preparation and measurement are exceedingly difficult to overcome. Data in the transverse direction of a double fibre wall indicate a behaviour in which earlywood fibres have a higher modulus than latewood ones, the former reaching values around 3 GPa [42,43]. As seen in Fig. 5, the variation in cell-wall properties affects the transverse properties a bit more than those in the longitudinal direction. Still all of the calculations fall above that of the transverse fibre wall measurements. It could here be discussed to what extent the fibre sections have been damaged in the process of isolation or to what extent there is still a lack in precision in the data for the cell wall components. It seems however clear that there are no indications that a higher elastic constant for the cellulose could fit in with these data.
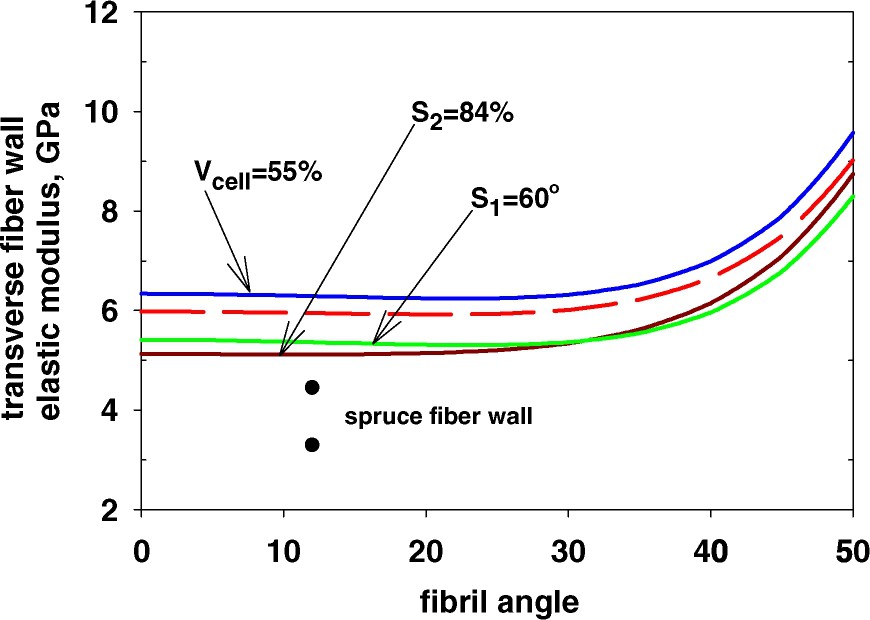
Transverse fibre-wall elastic modulus as a function of the fibril angle in the S2-wall as affected by different factors; cellulose content in the S2-wall, proportion of S2-wall and the fibril angle of the S1-wall. Measured values from Bergander and Salmén [43]. Reference values: dashed line; cellulose content in S2-wall 50%, proportion of S2-wall 79%, fibril angle in S1-wall 70°.
6 Softening effects
Moisture is well known to act as a softener for the wood polymers. In the range of normal relative humidities at room temperature and around it, only the hemicelluloses are affected by moisture to an appreciable extent. Modelling of this softening considering the measured stiffness of moist glucomannan reported in Table 1 is given in Fig. 6. It is interesting to note that the degree of softening is excellently modelled both in the fibre direction as well as in the transverse direction. In the latter case, the actual value of the modulus is overestimated, as previously mentioned, but as the modulus is given on a logarithmic scale, it is clearly seen that shifting the data up to the calculated ones gives a perfect match with the softening magnitude. It is also apparent from the magnitude in the modulus drop that the amorphous wood polymers play a more dominating role for the fibre properties in the transverse direction than they do in the longitudinal one.
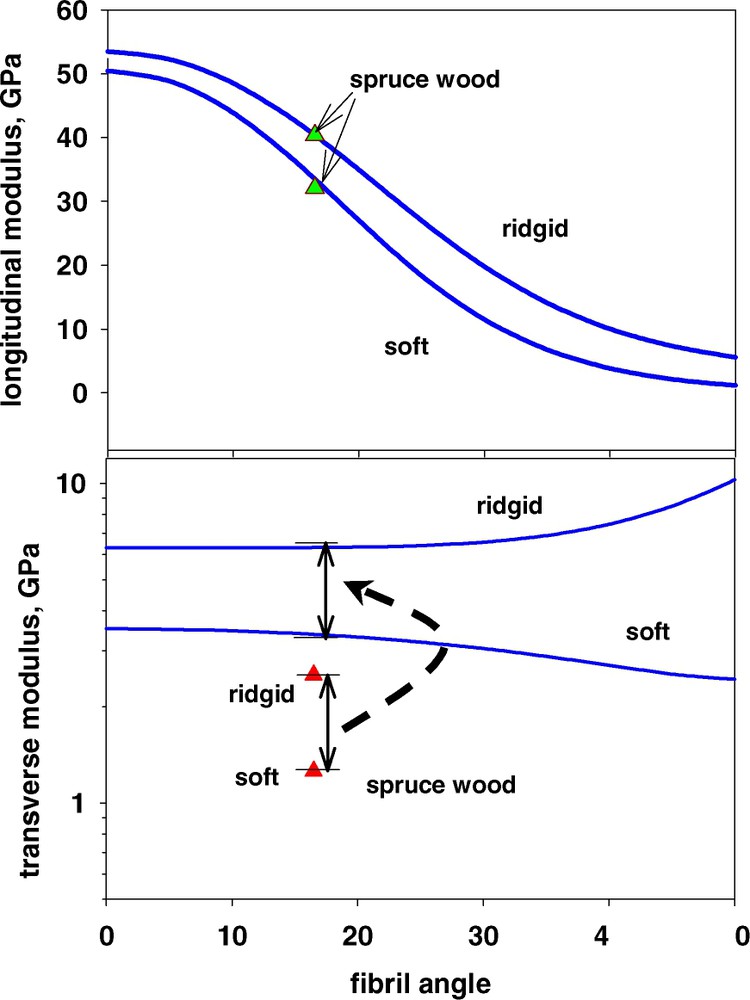
Modulus of the fibre wall of wood in longitudinal and transverse direction at dry (rigid) and moist (soft) conditions of the hemicelluloses. Measurements refer to data for softwood [44].
One also has to consider what happens with the parts of the cellulose fibrils that are accessible to moisture. At least 20% of the volume of the cellulose in a wood fibre will be absorbing moisture. If this means that the volume of material that softens when the relative humidity increases should be considered to be higher or if these parts of the cellulose still are restricted to such an extent that they will not contribute to the softening may be questioned. As seen in Fig. 7, a softening of the amorphous parts of the cellulose, modelled as if 20% of the cellulose had the same properties as the hemicelluloses, would imply a substantial decrease in the degree of softening of the wood fibre for small fibril angles in the longitudinal direction. In the transverse direction, the effect is much smaller. Compared to the measurements on wood (Fig. 7), it is however uncertain if the amorphous cellulose will behave as a softened amorphous component in this humidity range, as a larger drop in elasticity would have been expected for the measurements. However this should be checked on fibres or wood material having a fibril angle close to zero, where the softening effect is estimated to be quite large.
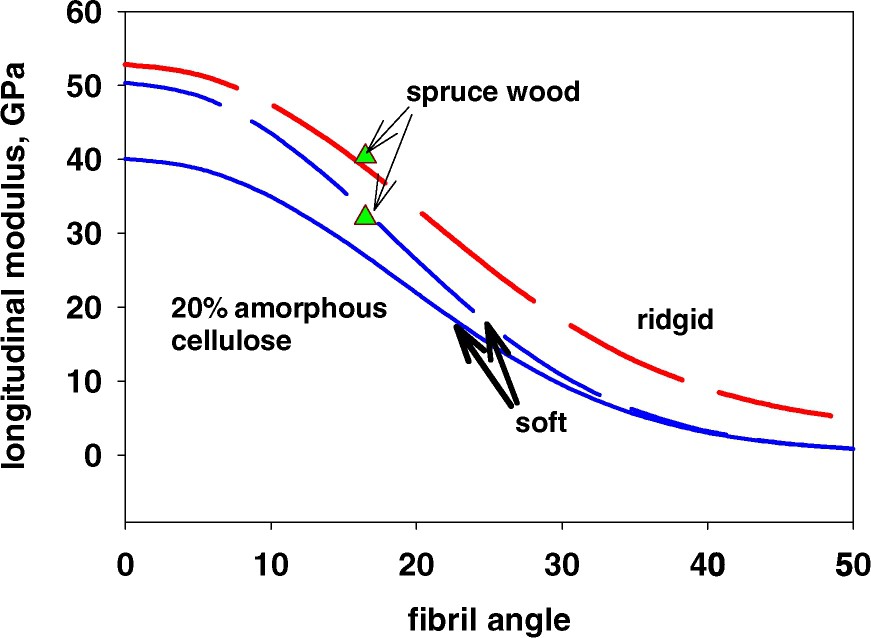
Influence of a softening due to a relative humidity increase (20% of the cellulose is considered here to be amorphous and to behave in the same way as the hemicelluloses).
7 Conclusions
Based on the comparisons of experimental data on elastic fibre and wood properties with such data calculated from the properties of the wood polymers, it seems evident that the stiffness of the cellulose fibrils is well described by the value of 134 GPa. It must also be concluded that it is highly likely that all of the wood polymers are orthotropic in nature, in relation to the low elastic properties exhibited for the fibre in its transverse direction.
It is also most likely that the water-absorbing disordered regions of the cellulose does not fully soften it the range of relative humidity rates at room temperature, thus the property changes only reflects the softening of the hemicelluloses.
It may also be concluded that the amorphous wood polymers play a more dominating role for the transverse fibre properties than they do for longitudinal fibre properties.