1 Introduction
Chlorosilanes are extensively used as raw materials for preparing cyclosiloxane, silicone oil or resins on an industrial scale. Chemical engineering has been optimised to perfectly control the hydrolysis/condensation of these products, by regulating the contact time between these and water (possibly containing an acid), using tubular reactors for instance [1]. Cyclosiloxanes are for example obtained by hydrolysis of dimethylchlorosilane (DCMS) in a batch reactor and further fractionated through distillation [2]. Theoretical energetic studies [3] showed that the hydrolysis step does not require a catalyst, but proceeds through a penta- or hexacoordinated silicone complex with water before releasing HCl. Similarly, condensation reaction implies the formation of silanol/silanol complex with two molecules of water to energetically favour the Si–O–Si bond formation.
The preparation of linear PDMS dispersions by ring-opening polymerization of cyclosiloxanes has been well reported in the literature using either basic [4–9] or acid [6,10–14] catalysts. In particular, preparation of so-called ‘microemulsions’ (i.e., polymer particles of less than 80-nm diameter, according to industrial providers) by cyclosiloxane polymerization [15–18] is of interest to prepare materials useful in cosmetics or textile industries. Shot processes [16,17] are generally carried out to generate small and monodisperse particles. In one particular case [15], ionic–non-ionic surfactant mixtures allowed Gee to generate homogeneous microemulsions directly in batch, but drop-by-drop monomer addition [17] helps in decreasing both the particle size and polydispersity. A key point in microemulsion systems, including those obtained by radical polymerization [19], is the control of the final particle size, mainly by the surfactant content.
Cross-linked silicone microemulsions are easily prepared by hydrolysis–condensation of trifunctional alkoxysilanes [20–25] or chlorosilanes [26]. Besides, sparse results were published on the synthesis of linear PDMS chains from the former precursors in dispersion [22,27,28]. One group first proceeded [27] by adding a small content of dimethyldietoxysilane (DMDES) in a water/ammonia mixture, the latter being the catalyst of the reaction. Species formed were mainly D4 and small oligomers (particularly when adding methanol), i.e. polymerization is not favoured. In addition, emulsions with large particle sizes were attained, since no surfactant was present in these experiments. The control of the particle size was, in a second approach, exerted by introducing surfactants in the recipe [28], among which silicone-based surfactants led to particles of about 25 nm in diameter with narrow dispersity. Another group performed the hydrolysis/condensation of DMDES added dropwise into a quaternary ammonium surfactant/hydroxide sodium aqueous mixture [22]. Thanks to the interfacial catalysis provided by the ammonium hydroxide surfactant, microemulsions (particle size 56 nm) containing high molar masses (, ) were obtained.
In this article, the self-catalysed hydrolysis/condensation of dichlorodimethylsilane (DCMS) in emulsion to generate microemulsions is developed. The above monomer is added at controlled rate to a solution of polyoxyethylene(8) lauryl sulphate sodium, an electrosteric surfactant [29]. This latter avoids particle coagulation due to the high ionic strength resulting from chloride anion release. In addition, its sulphate moiety is able to capture a proton to self-catalyse ring-opening polymerization of cyclosiloxane or polycondensation of disilanol PDMS chains [26].
2 Experimental section
Two lots of DCMS were used: Lot 1 was provided by Aldrich (99%) and was stored without precaution; Lot 2 was purchased from Acros (99%) and stored under nitrogen between two experiments, to avoid adventitious hydrolysis. Injection of raw monomers in toluene SEC did not reveal the presence of any cycle or polymer. The Disponil surfactant FE32is, polyoxyethylene(8) lauryl sulphate sodium (POELSNa), a gift from Cognis, was used as received and characterized by electrospray mass spectrometry.
In a typical experiment, the surfactant is first dissolved in deionized water in a reactor equipped with a paddle agitator set at 400 rpm. The monomer is poured dropwise into the primary mixture either from a separatory funnel or through a syringe connected to a pump for constant feed rate. Time of addition was set to typically less than 2 h in the model experiment. The emulsion is let to evolve for at least a week along which samples are withdrawn. The samples are first decanted and filtrated on 0.45-μm Millipore filters to discard the floating organic phase (see text). Few drops are withdrawn and injected in excess deionized water to carry out particle size measurements. The rest of the sample is severely agitated with 2/3 of acetone and then centrifuged on a bench apparatus (3000 rpm). The organic phase (polymer + small cycles) is withdrawn and washed with a basic water/acetone mixture to come back to the neutrality without redispersing the organic phase, then with plain water to eliminate the excess of surfactant. The polymer/cycle phase is redissolved in CH2Cl2, dried under MgSO4, filtrated and evaporated before SEC analyses.
Electrospray ionisation analysis (negative ion mode) was performed on a triple quadrupole tandem mass spectrometer (Quattro 1, Micromass). The sample was prepared in CH3OH/H2O (50 ng μl–1) and introduced into the ESI source by infusion using a syringe pump (400 μl h–1). The source conditions were: capillary, 3000 V; HV lens, –300 V; cone voltage, –20 V, source temperature, 90 °C, drying gas N2 (300 l h–1) and nebulizing gas N2 (15 l h–1). Photon correlation spectroscopy measurements were carried out on a Zetasizer 4 from Malvern Instruments equipped with an helium/neon laser (λ = 633 nm). Raw data are the z-average diameter (dz) as well as a coefficient of variation (CV) transformed into a polydispersity index (PDI) according to . SEC analyses provided average molar masses, molar mass distribution, as well as small cycle conversions. They were carried out on a WATERS SEC apparatus equipped with a pump, a refractometer and three separation columns, of porosities 100, 500 and 103–104 Å (mixed bed). The eluting rate of the toluene solvent (that contains 3 ml l–1 of diisopropylethylamine) is 1 ml min–1. Columns are calibrated by polystyrene standards as described before. Conversions in small cycles were calculated by integrating SEC peaks after correcting for the refractive indexes of the eluent (toluene + N,N-diisopropylethylamine, nD = 1.4965), the polymer (nD = 1.4035) and small cycles (nD = 1.39602, value for D5).
3 Results and discussion
Caution. Chlorosilanes are very sensitive to moisture and release corrosive HCl. Safety rules, such as glasses- and glove-wearing, have to be strictly followed in manipulating such hazardous products. In addition, the acid can rapidly corrode steel equipment, so that using exclusively glassware is highly recommended.
3.1 Basic polymerization scheme
Table 1 gives the various recipes carried out in this study as well as the final parameters of the dispersions, i.e. rate of polymerization, particle size, polydispersity index, number average molar mass , molar mass distribution (MMD) and cycle contents at final conversion. Reactions were mainly conducted at room temperature (except run 5, conducted at 5 °C), at rather high contents in monomer (17 wt%, 12 wt% after hydrolysis/condensation) and surfactant (10 wt% compared to monomer) to generate small particles. The DCMS monomer was poured gradually to avoid temperature rising through acid/water mixing [2,26]. An electrosteric surfactant, namely polyoxyethylene(8) lauryl sulphate sodium (POELSNa), was chosen and its structure characterized by electrospray mass spectrometry (Fig. 1 ). It exhibits alkyl chains mainly composed of x = 12 methylene units with chains of 14 and 16 units that also show up. The ethoxylated moiety ranges between y = 0 to 10 ethoxy units, with a maximum set at 8 units. Even though this surfactant shows a fairly broad compositional distribution, it has exhibited remarkable qualities in stabilizing emulsions, even in high salt concentrations.
Recipes and main final results for DCMS hydrolysis/condensation performed at room temperature otherwise stated
Run | Overall volume | [POELSNa] | [DCMS] | Addition rate | Sampling time | Particle size | PDI | Final cycle contents | ||
(ml) | (× 102 mol l–1) | (mol l–1) | (ml h–1) | (days) | (nm) | (g mol–1) | (wt%) | |||
1a | 60 | 10.7 | 1.29 | 6.64 | 16 | 44.2 | 1.09 | 45900 | 2.14 | 9.4 |
2b | 120 | 10.7 | 1.29 | 9.4 | 5 | 49.8 | 1.11 | 41830 | 1.89 | 4.8 |
3b | 120 | 10.7 | 1.29 | 9.4 | 5 | 51.2 | 1.08 | 46920 | 1.91 | 6.7 |
4a | 60 | 21.4 | 1.29 | 6.64 | 12 | 47.7 | 1.104 | 39200 | 1.90 | 7.8 |
5a,c | 60 | 10.7 | 1.29 | 6.64 | 12 | 35.5 | 1.104 | 42500 | 2.05 | 8.9 |
6a | 60 | 5.3 | 1.29 | 6.64 | 12 | 85.3 | 1.082 | 49640 | 2.17 | 9.7 |
7a | 30 | 10.7 | 1.29 | 6.64 | 15 | 53.7 | 1.152 | 44220 | 2.07 | 8.9 |
8a | 60 | 10.7 | 1.29 | 2.82 | 12 | / | / | 37740 | 1.97 | 8.6 |
9b | 110 | 5.9 | 1.41 | 9.4 | 11 | 59.2 | 1.018 | 56600 | 1.94 | 7.8 |
10b | 140 | 18.5 | 1.11 | 9.4 | 11 | 44.1 | 1.108 | 41160 | 1.99 | 13.4 |
11b | 120 | 10.7 | 1.29 | 6.27 | 10 | 49.6 | 1.067 | 56060 | 1.90 | 8.75 |
12b | 120 | 10.7 | 1.29 | 18.81 | 6 | 63.2 | 1.135 | 48230 | 1.98 | 11.5 |
a Experiments carried out in cylindrical 100-ml reactor, and with an automatic syringe pump to add the DCMS; monomer Lot 1.
b Experiments carried out in a round reactor with monomer added drop by drop from a funnel vessel; monomer Lot 2.
c Reaction temperature: 5 °C.

Mass spectrometry electrospray analysis of sodium dodecylpolyoxyethylene(8) sulphate.
A typical SEC trace obtained in the course of a reaction is given in Fig. 2 . Blank injection of DCMS dissolved in toluene revealed that the monomer elutes at the same location as the toluene peak and also in negative polarity. Injection of samples of exact concentration did not reveal a variation of the negative peak with time after SEC trace normalization. This result indicates that, as expected [2], DCMS instantaneously hydrolyses once added in the reactor. In addition, only small cycles of typically 4 to 6 D units that elute at fixed retention time (Fig. 2) are present, since short disilanol terminated chains (typically, 3–4 D units) would elute after the toluene peak [8], where the baseline remains flat. High molar mass polymer is also observed right from the beginning.

Typical SEC trace obtained in this study.
The experiments presented in Table 1 were carried out using different lots of monomers, glassware and addition apparatus, but still produced similar data trends. The robustness of the process is established by compiling all particle size, polymer conversion, average molar mass and polymolecularity results (including data from kinetics sampling not reported in Table 1) and plotting a master curve of these parameters (Fig. 3 ). Particle size decreases constantly, while the average molar mass increases with polymer conversion. Particle size reduction with conversion is an indication that the polymerization process obeys an emulsion (initial big monomer droplets that vanished to form smaller particles) rather than a microemulsion (initial monomer swollen micelles that collapse under polymerization to generate bigger particles) mechanism. Molar masses still evolve after the polymer conversion levels off at about 90%, whereas particle sizes reach a constant value of 50 nm (see Fig. 3). MMDs reach the theoretical value of 2 expected from the Flory distribution. Note the scattering in the MMD data ascribed to the tailing of the surfactant peak on the polymer one (Fig. 2).

Basic features of DCMS emulsion hydrolysis condensation, i.e. particle size (□), cyclic contents (○) and polydispersity index (▴), against average molar mass , using data from Table 1 and all intermediate data obtained from sampling during the polymerization stage. Lines are only guides for the eyes.
A simple reaction scheme based on these preliminary observations and previous cationic cyclosiloxane polymerization studies [6,10–14] is proposed in Scheme 1 . Rapid hydrolysis and condensation of short disilanol in the water phase lead to cycles by end-biting of small dihydroxy oligomers. The strong acidity catalyses both the rapid condensation and end-biting reactions [30]. The cyclosiloxanes are so hydrophobic (solubility of D4 in water is 2.4 × 10–7 mol l–1) [31] that they gather into droplets stabilized against coalescence by the electrosteric surfactant and against Ostwald ripening by the few polymeric chains they contain. The surfactant also catalyses interfacial ring-opening polymerization of cyclosiloxane and PDMS polycondensation [13,32]. The last step, according to previous studies, is likely to occur in the bulk of the particles by phase transfer catalysis [8].

3.2 Detailed kinetics and colloidal studies
A model recipe was chosen and carried out in three experiments that differ in volume, reactor type and monomer addition conditions (see details in Table 1, runs 1–3).
The overall content of cyclosiloxanes was obtained from polymer and cycle SEC peak integration, after refractive index correction (see experimental part). Since SEC resolution is good enough to differentiate peaks of the various cyclosiloxanes (at least D4, D5 and D6) (Fig. 2), these were deconvoluted into a series of Gaussian peaks, as presented in Fig. 4 on an ideal case. D4, D5 and D6 cyclic contents, derived from the Gaussian curves integration, are presented in Fig. 5 as a function of time. D4 is created in high yields at the beginning, but rapidly disappears. On the other hand, a majority of D5, and to a lesser extent D6, are gradually formed and consumed as a function of time. Such a trend is very close to cyclosiloxane cationic ROP in miniemulsion, where 5- or 6-unit cycle contents pass through a maximum before being almost quantitatively consumed at long polymerization times [14]. This behaviour is quite different from the one observed in anionic process, where 4-unit cycles are always in excess compared to the less strained cycles. These latter gradually build up in the mixture with time for never disappearing [5,8].
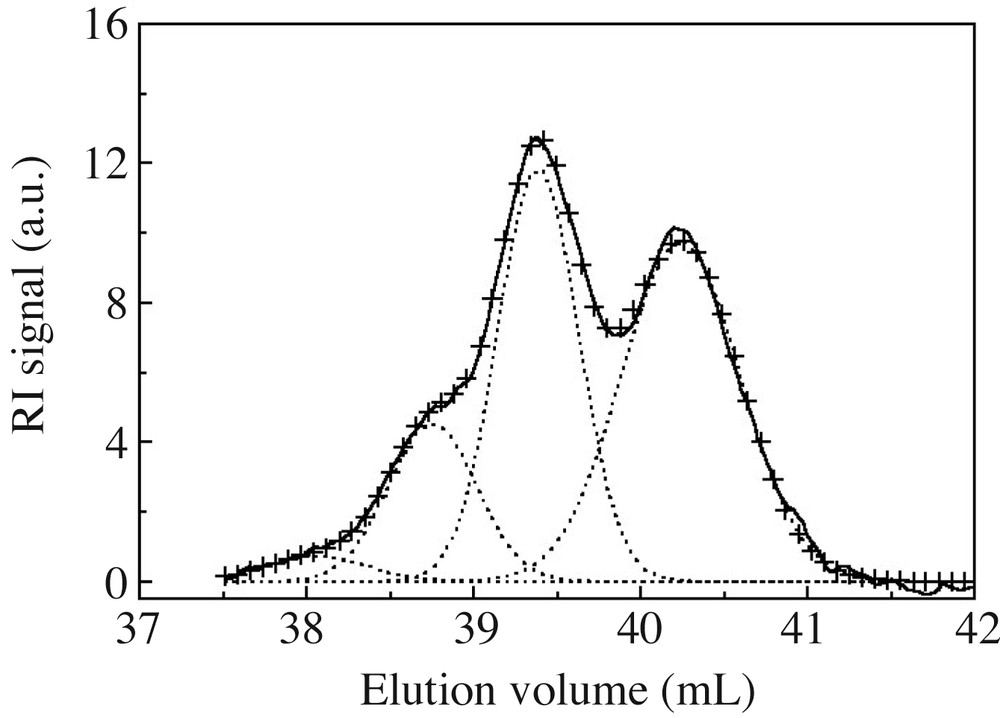
SEC trace deconvolution of small cycle area into Gaussian peaks. (–) Initial SEC trace; (+ +) fitted curve; (---) Gaussian distributions.
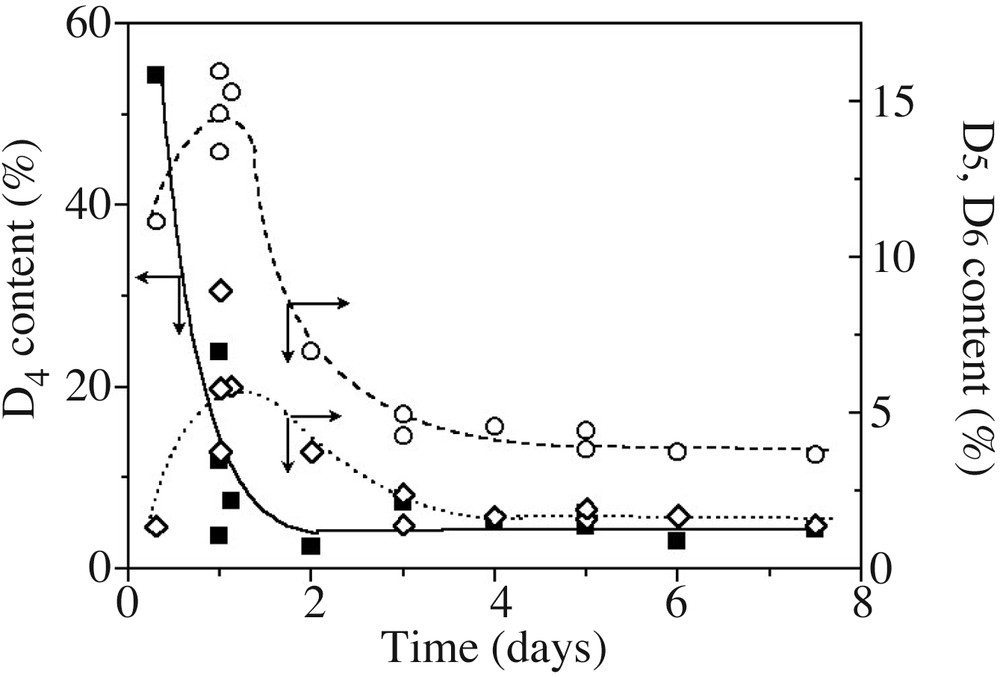
Evolution with time of D4 (■, –), D5 (○,– –) and D6 (◊,---) contents in the model experiment (Table 1, runs 1–3). Lines are only guides for the eyes.
Fig. 6 shows the evolution of the number average molar mass and MMD as a function of time. s smoothly evolve with time to reach 50 000 g mol–1 after seven days, in parallel with , which rises up to a value of 2. Polycondensation is a slow motion process here compared to experiments where dodecyl benzene sulphonate acid (DBSA) is used as a catalyst [32]. This result is a consequence of the weak ability of the proton to penetrate the surfactant ethoxylated layer at the shell of the particles. The equilibrium molar mass values are three times less than those involving a DBSA-catalysed PDMS condensation, values that depend on the organic phase content in the recipe [14].
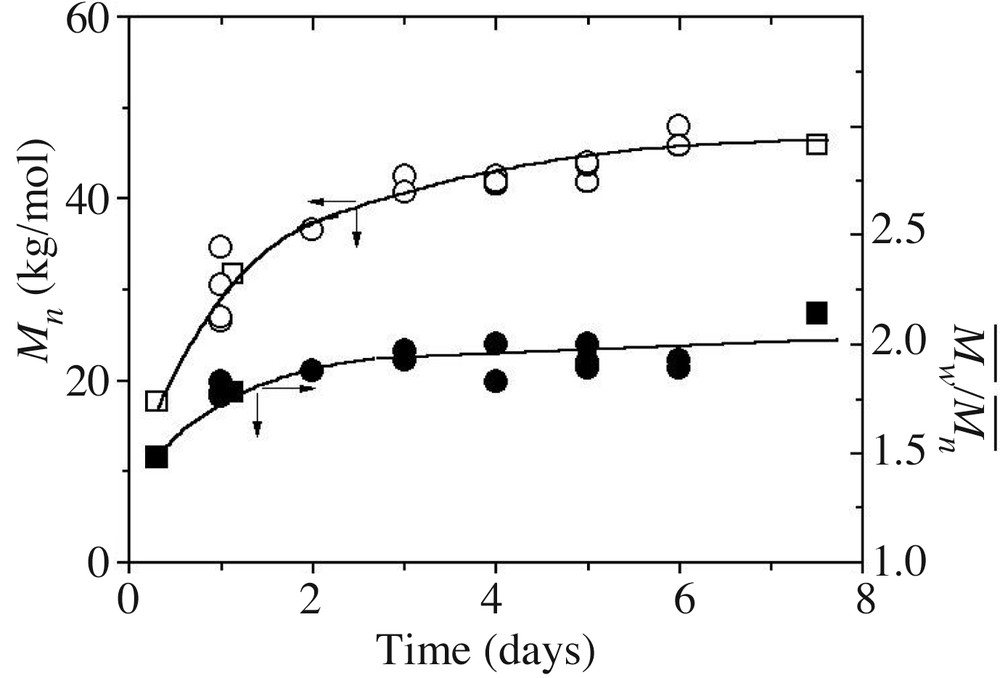
Number average molar mass (open symbols) and molar mass distribution (plain symbols) for DCMS hydrolysis/condensation in a model recipe (runs 1 (○) and 2,3 (), Table 1). Lines are only guides for the eyes.
Fig. 7 reports the average particle size (z-average diameter in nm) and polydispersity index as a function of time. The particle size decreases down to 50 nm, whereas the polydispersity index first increases and then decreases with time. Since small cycles and long-chain PDMS exhibit comparable densities (0.95 and 0.976, respectively), a decrease in particle size is related to an increase of the number of particles during the reaction. A tentative scheme based on emulsion micellar particle nucleation [33] is proposed to account for these results (Scheme 2 ). Cyclosiloxanes formed in situ are rapidly entrapped by the surfactant to produce large swollen particles containing few polymer chains. The primary diameter of 170 nm found here actually corresponds to typical sizes found in polymer-stabilized monomer droplets prepared in miniemulsion; these entities will be thus referred to as ‘monomer’ droplets (see Scheme 2). Two processes compete to deplete these droplets: (i) nucleation of a new particle via monomer diffusion towards an empty micelle; (ii) monomer diffusion towards the smaller particles to compensate for their rapid consumption by interfacial polymerization, which is faster in particles exhibiting large specific surface. Both processes decrease the average particle size of the dispersion, the second however to a lesser extent, since differences between particle sizes are less important. On the other hand, polydispersity increases with continuous nucleation, which prevails at the beginning of the polymerization, whereas it decreases with particle swelling, dominant at longer time when micelles have vanished. The fact that the particle size equilibrium is reached after long times (typically 4 days, see also Fig. 5) is explained by the considerably slow rates of diffusion of cyclosiloxanes [17], especially for those of 5 and 6 D units [11], in such a high ionic strength medium.

z-Average diameter (open symbols) and polydispersity index (plain symbols) for DCMS hydrolysis/condensation in a model recipe (run 1 (○) and 2 (), Table 1; particle sizes in run 3 were not measured). Lines are only guides for the eyes.

3.3 Influence of specific parameters
The influence of the concentration of surfactant was shown from experiments carried out at DCMS addition rates of 6.64 ml h–1 (runs 1,4–7,11) and 9.4 ml h–1 (runs 2,3,9,10). Particle sizes decrease with surfactant content, but to a low extent. Average molar masses decline with increasing surfactant concentration, which is again attributed to a shielding of the surface by the bulky surfactant that slows down the polycondensation reaction. Cycle contents also slightly decrease with increasing surfactant content (from 9.7 to 7.8 wt% at an addition rate of 6.64 ml h–1; Table 1, runs 1,4–7,11), but this discrepancy may not be significant regarding the scattering in SEC integration.
The same recipe was reproduced at different volume and addition rates (Table 1, runs 1-3,5,11,12). Slow addition of DCMS profits to a fine decrease of the final particle size as well as polydispersity index. This result indicates that a better repartition of cyclosiloxanes towards the micelles is exerted by slowly adding the monomer, in other words less big droplets form during the process [14, 34]. Batch D4 polymerization in similar surfactant and acidity conditions was also carried out in this study to check out the effect of ‘infinitely rapid’ addition rate. The particle size was much larger (172 nm) and the polydispersity index smaller (1.08) in these conditions. Nucleation of micelles is a faster step in this experiment since only D4, which diffuses more readily than bigger cyclosiloxanes [11], is injected here. Polydispersity index has then time to decrease while particles grow according to the second step in Scheme 2. Variations in molar masses as well as cycle contents with addition rate are difficult to observe (see Table 1) and would require generating further data to show a possible trend.
3.4 Unsolved problem
The formation of an oil layer at the top of the reactor was systematically observed here, the content of which varies within the experiments. Depending on the surfactant content, a turbid layer made of large droplets or an oily film was observed. It was also noticed that this layer gradually vanishes at long times and accordingly the average particle size increases, revealing the slow but real motion of the polymerization/polycondensation reactions. Such phase separation is recurrent of emulsion polymerization of cyclosiloxanes, but is so far poorly understood [15,34]. One way to avoid the formation of an oil layer is to generate by sonication droplets of finite size and high specific surface that rapidly polymerize. Another possibility is to use a PDMS seed [17] previously synthesized in the presence of similar electrosteric surfactant to avoid the formation of big monomer droplets. We are currently testing this second possibility.
4 Conclusion
It was demonstrated in this study that PDMS microemulsions are easily prepared from dichlorodimethylsilane hydrolysis/condensation, provided that the right surfactant is used, e.g. sodium dodecylpolyoxyethylene(8) sulphate. Such an electrosteric surfactant avoids rapid coagulation of the dispersion that may arise from ionic strength upgrade by Cl– release. In addition, once cyclosiloxanes form in the water phase, it catalyses the polymerization and polycondensation reaction, by bringing protons at the particle interface through its sulphate moiety. It was also shown that nanoparticles (50 nm diameter in average) formed through a micellar nucleation system, which in turns also explains the polydispersity of the final microemulsions (around 1.1). This mechanism scheme may be applicable to other processes involving shot addition of cyclosiloxanes in an aqueous surfactant/catalyst solution. The PDMS chains are exclusively linear (; ) and rather small contents of cyclosiloxanes remain in the particle (less than 5 wt% in best conditions), both features typical of a cyclosiloxane cationic polymerization process.
Other conditions need to be found to better control the nucleation process, playing for instance on the shear applied in the reactor, the temperature, the type of surfactant/initiator or the monomer content.
Acknowledgements
D. Lesage from LCSOB (University Paris-6, France) is gratefully acknowledged for providing the mass spectrometry analysis.