1 Introduction
The application of electrophotographic technology, often referred to as an ‘office copier’ was first introduced as a means of duplicating a document using a dry process. Subsequently, with the advent of computer technology, electrophotographic engines became popular as laser printers. Today, electrophotographic printers are used for a myriad of applications from small, desktop black and white printers to huge, full color presses used for commercial digital printing applications.
History abounds with examples in which technological innovations occurred because advances in two or more seemingly unrelated areas merge. Once such possible confluence may be occurring between electrophotography and nanofabrication.
Nanofabrication has become a goal of industry in recent years. While nanofabrication technology remains, at this time, a research objective, as opposed to a commercial means towards manufacturing, microfabrication has been in existence, at least in one area, since Chester Carlson first demonstrated the electrophotographic process more than 60 years ago [1]. Specifically, electrophotography produces documents and images by precisely placing large numbers (often exceeding 1010 per 8 1/2 × 11 in. page) of micrometer-size pigmented particles, generally called toner particles, in specific sites, whereby each site has a diameter of the order of 20 μm or less, at a high rate of speed. Failure to precisely place the particles would result in image degradation caused by a loss of resolution or sharpness, shifts in color balance, an increase in grain or background, etc. The precise placement of the particles onto the receiver requires a careful balance of adhesion or electrodynamic forces and electrostatic forces between charged particles and between those particles and various substrates during the entire image-forming process.
This paper describes the forces controlling the movement and placement of the micrometer-size toner particles used in the electrophotographic process and how that process, in itself, is an example of microfabrication. The paper then demonstrates how electrophotography can be used in the more general area of microfabrication and illustrates that concept with several demonstrated examples. Finally, this paper explores the physics and engineering associated with extending this technology into the process of fabricating microscopic components and devices.
2 Electrophotography: science and technology
To facilitate comprehension of this paper, it is worthwhile to first briefly describe the electrophotographic process [2]. The process begins by first uniformly charging a photoreceptor [3], typically using a grid controlled corona or a roller charger [4]. The photoreceptor is then image-wise exposed using a writer that comprises either a laser scanner or LED array, thereby creating an electrostatic latent image. A visible image is then developed on the photoreceptor by bringing the electrostatic latent image into close proximity with electrostatically charged toner particles, whereby the toner particles are attracted to and become deposited on the latent image bearing photoreceptor. Typically, toner particles have charges in the range of 10–15–10–14 C and diameters in the range of 8–10 μm [5]. The image is next transferred to a receiver material such as paper. This is most often accomplished by subjecting the toner particles to an applied electric field to urge them towards the receiver. The toned image on the paper is then fused and the photoreceptor is cleaned and made ready for the next image.
As an example of the precision needed in depositing toner particles, let us consider the formation of a gray pictorial image. In graphic arts, pictorial images are formed by breaking up the original image into grid patterns similar to graph paper [6]. The finer the grid spacing, the more detail of the original image is captured in the printed copy. Typical rulings for better quality prints are in the range of 1501 lines per inch, or approximately 167 μm between adjacent grid lines.
Now, suppose one is using a writer with a resolution of 600 dpi2, corresponding to approximately 23.6 dots per cm (dpcm). That means that each point on the grid can be divided into 16 separate regions and either exposed or not exposed, thereby creating 16 picture elements or pixels, with a center-to-center spacing of the pixels of approximately 40 μm. In a two-bit system where the photoreceptor can either be developed or not developed, that means that 16 Gy levels are possible. In contrast, the human eye can resolve over 100 Gy levels [7]. To achieve images in which the levels of gray are limited by the sensitivity of the human eye would require a writer with a resolution closer to 2400 dpi or approximately 945 dpcm, especially if a finer grid is used, as is common with higher quality publications. This would result in a spacing between pixels of approximately 10 μm, or one toner particle diameter.
If one were to produce color prints, the requirements become more stringent [8], as such prints are usually made by overlaying separations of the subtractive colors, cyan, magenta, and yellow, in addition to black, as well as any other custom color that may be desired. Such an overlaying process would allow errors introduced in the positioning and development of individual pixels to be compounded.
Thus far it has been assumed that the electrostatic latent image is developed by either placing or not placing a single toner particle on the pixel. This is referred to as a two-bit system. However, the intensity of the photoexposure can be varied, thereby creating a variation of the potential of each pixel. This would allow a multiple of smaller toner particles to be placed on a pixel, thereby allowing further modulation of the gray scale for a B&W image and a wider color gamut for full color images. This would, obviously, be most effective if smaller toner particles were used, allowing even closer placement of those particles to one another.
The main section of this paper will discuss the laws of physics that govern one's ability to accurately place charged toner particles in desired positions on an image. In a subsequent section, some speculative novel applications of this, or similar technology, will be presented.
3 Control of toner particles: a problem in electrostatics and electrodynamics
There are two basic types of interactions that control the placement and movement of toner particles. The first type of interaction is electrostatic. The second type is electrodynamic.
Electrostatic forces arise from the fact that the toner particles are charged. These forces are long-range and are significant in allowing the toner particles to be deposited on the charged photoreceptor. They also contribute to the adhesion of the particle to the photoconductor, as well as a Coulombic repulsion between toner particles. Electrostatic forces are also generally used to transfer the toned image from the photoreceptor to the final receiver.
Electrostatic forces between a uniformly charged spherical particle of radius R and charge q and its image charge in a grounded conducting plane [9] is given by(1)

The force needed to remove spherical polyester toner particles having a 7 μm diameter from an organic photoreceptor as a function of the square of the toner charge. Data from Ref. [10].
Electrodynamic forces principally arise from London or dispersion interactions whereby an instantaneous dipole fluctuation in one particle polarizes a neighboring particle. The resulting dipole–dipole interaction is the dominant contribution to van der Waals interactions [11–13]. Van der Waals forces are always attractive for dry toner particles.
As previously discussed, the transfer of the toner particles from the photoreceptor to the receiver is typically accomplished by applying an electrostatic field to urge the particles towards the paper. However, the magnitude of the applied field is limited by air breakdown due to Paschen [14] discharge. For air, the Paschen discharge curve is shown in Fig. 2. As can be seen, if one were transferring a monolayer of toner particles having a diameter of approximately 10 μm, to a smooth receiver so that the size of the air gap is fixed solely by the size of the toner, one would not be able to obtain a transfer field greater than approximately 3.8 × 107 V/m (see Fig. 2). This means that the maximum electrostatic force that one could exert on a 10 μm diameter particle with a charge of 5 × 10–15 C is approximately 190 nN. However, the force required to separate that particle from the photoreceptor is approximately 250 nN. This implies that one could not electrostatically detach the toner particle from the photoreceptor simply by applying an electrostatic force [15,16]. It should be noted that the force needed to remove this same toner without having first applied zinc stearate to the photoreceptor would be over 1000 nN [17].
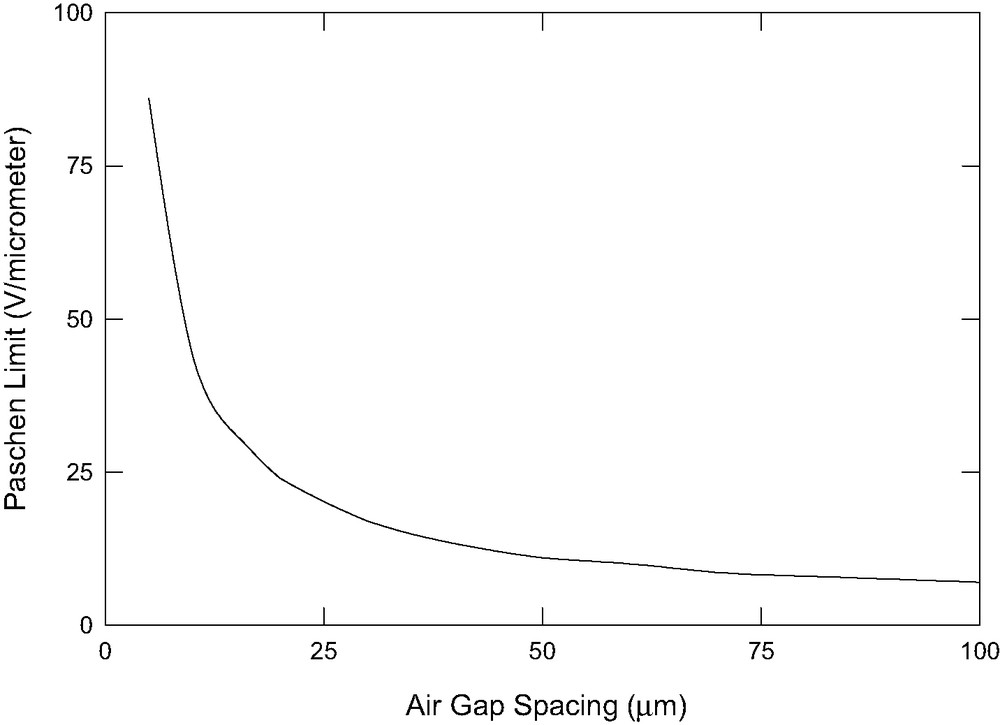
The Paschen discharge limit as a function of gap size in air.
As discussed elsewhere [18], because the toner particles are triboelectrically charged, it is reasonable to approximate the particle charge as varying with the surface area and having a constant surface charge density σ. Accordingly, the force FI adhering a toner particle of radius R to the photoreceptor, as calculated using the method of images [9] would be given by(2)
The second type of force that adheres toner particles to the photoreceptor arises from electrodynamic interactions. Specifically, an instantaneous dipole that occurs in one material can induce an instantaneous dipole in a neighboring material, giving rise to the principal component of the relatively short range van der Waals interactions. The reader is referred elsewhere to a detailed treatment of such interactions [19,20]. Suffice it to say, such interactions have been commonly attributed to giving rise to surface forces [21].
For the case in which a particle is bound to a substrate via surface forces, the force FS needed to remove that particle from the substrate, according to JKR theory [22] is given by(4)
Upon comparing Eq. (4) with Eqs. (2) and (3), it is clear that all three forces decrease with decreasing particle radius. However, the electrostatic forces, which vary as the square of the particle radius, decrease at a faster rate than do the surface forces. This implies that, for sufficiently small particles, surface forces should dominate over electrostatic forces. Moreover, there is a critical radius below which it would not be possible to electrostatically detach a particle using an applied electrostatic force. Upon substitution of reasonable values for wA, one estimates that this critical radius is of the order of 5–10 μm. In addition, one can further estimate that, for a spherical particle in contact with an electrically conducting substrate overcoated with a polymer, surface forces would dominate over image-charge forces when the particle radius is less than or of the order of several hundred micrometers.
Although not strictly correct, the force needed to detach a toner particle from the photoreceptor can be approximated by linearly combining Eqs. (2)–(4). The validity of this approximation is borne out in Fig. 1, which shows the linear dependence of the detachment force on the square of the particle charge per unit mass, with the y-intercept representing the van der Waals interaction. As previously mentioned, it is important to note that in this instance the substrate had been coated with zinc stearate to significantly reduce the surface forces. Upon combining Eqs. (2)–(4), one finds that the electric field Edetach necessary to detach a charged particle from a substrate is given by(5)
There are two items of particular note in Eq. (5). The first is that there is an optimal particle charge to facilitate particle detachment. The second is that the field required to remove a particle increases with decreasing particle size and that there is a limit, below which, one would not be able to electrostatically detach particles. For electrophotographic engines, this limit is in the range of R = 5–10 μm. Unfortunately, it is highly desirable to use smaller toner particles for the reasons discussed earlier in this paper. Therefore, other means of effecting toner transfer from the photoreceptor to the receiver have to be implemented. This will be discussed forthwith.
Adhesion of the toner particles to the photoreceptor is not the only area in which the balance between electrostatic and surface forces are significant. Rather, interparticle cohesion is also important. Specifically, consider a page printed on a laser printer. This page comprises agglomerates of highly charged particles that have been tightly packed together in an ordered form. However, as the particles all have the same sign charge, Coulombic repulsion between the particles should be significant. Such repulsion could result in the occurrence of individual toner particles becoming separated from the mass of toner particles to which they rightfully belong. These are known as satellite particles. As shown by Rushing et al. [23], it is not necessary to detach the toner particles from a substrate to create satellites. Rather, it is only necessary to slide the particles along the substrate. Moreover, as also shown by Rushing et al. [23], the force needed to slide a toner particle can be as low as only 10% as that needed to detach the particle form the substrate. Thus, proper control of the toner cohesion is also important in producing electrophotographic images.
As is intuitively obvious, cohesion and adhesion are not totally independent properties. Rather, Eq. (4) can be generalized to the case of two particles of radii R1 and R2 cohering by simply substituting the reduced radius Rred(6)
It is clear that, in order to reduce the size of the toner particles used in electrophotographic engines, it is necessary to decrease the van der Waals forces. This is commonly accomplished by deliberately adding asperities to the particles [24], generally by coating the toner particles with silica particles having cluster diameters of the order of 30 nm. The decrease in toner adhesion with increasing silica concentration has been reported elsewhere [5,15]. An example of this behavior is shown in Fig. 3.
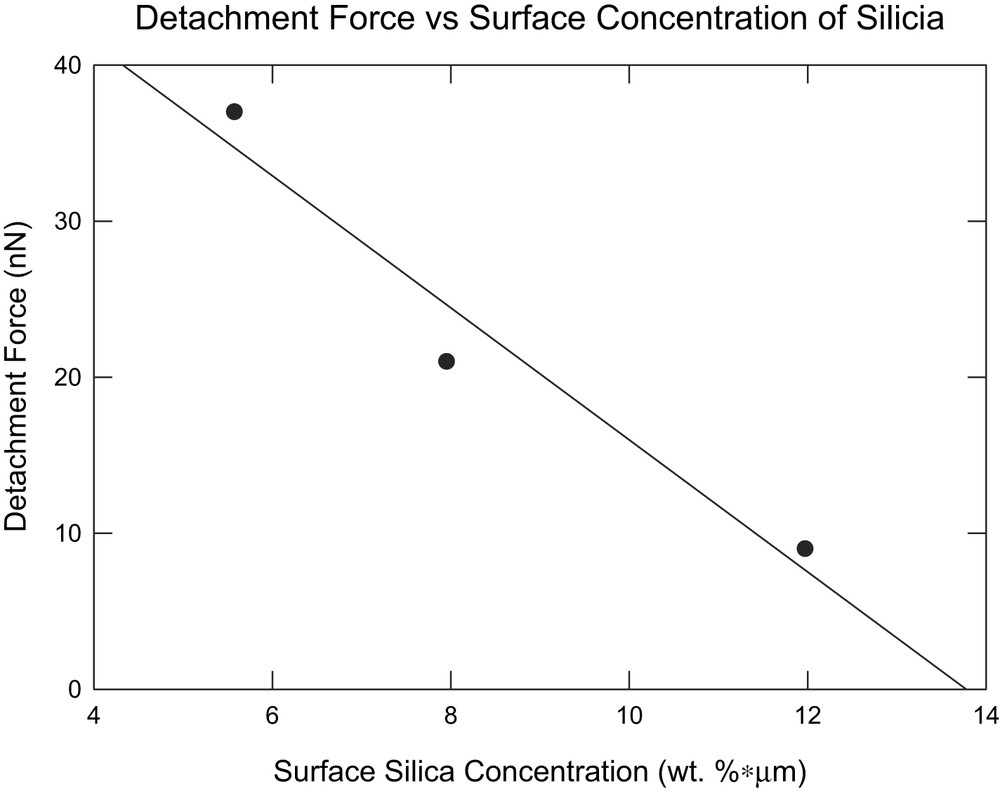
The effect of the surface concentration of silica on the force needed to remove 6.4-μm-diameter ground toner from an organic photoreceptor. Data from [5].
It is apparent from Fig. 3 that the force needed to separate toner particles from an organic photoreceptor decreases monotonically as the amount of silica on the surface of the toner particles increases.
Accompanying the decrease in toner adhesion to the photoreceptor is a corresponding decrease in toner cohesion [15,23]. This is observed in the transferred image by an increase in the number of satellite particles with increasing silica concentration, as seen in Fig. 4, as well as by a decrease in resolution caused by the satellite particles filling the gaps between the lines on a resolution test target, as described as shown in Fig. 5.
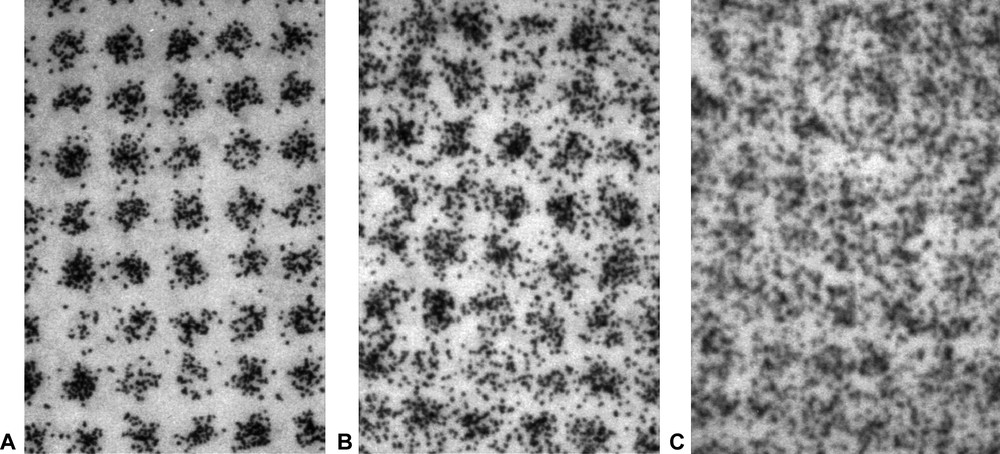
Halftone dots after transfer with (A) no silica, (B) 0.5% silica, and (C) 2% silica. From [15].
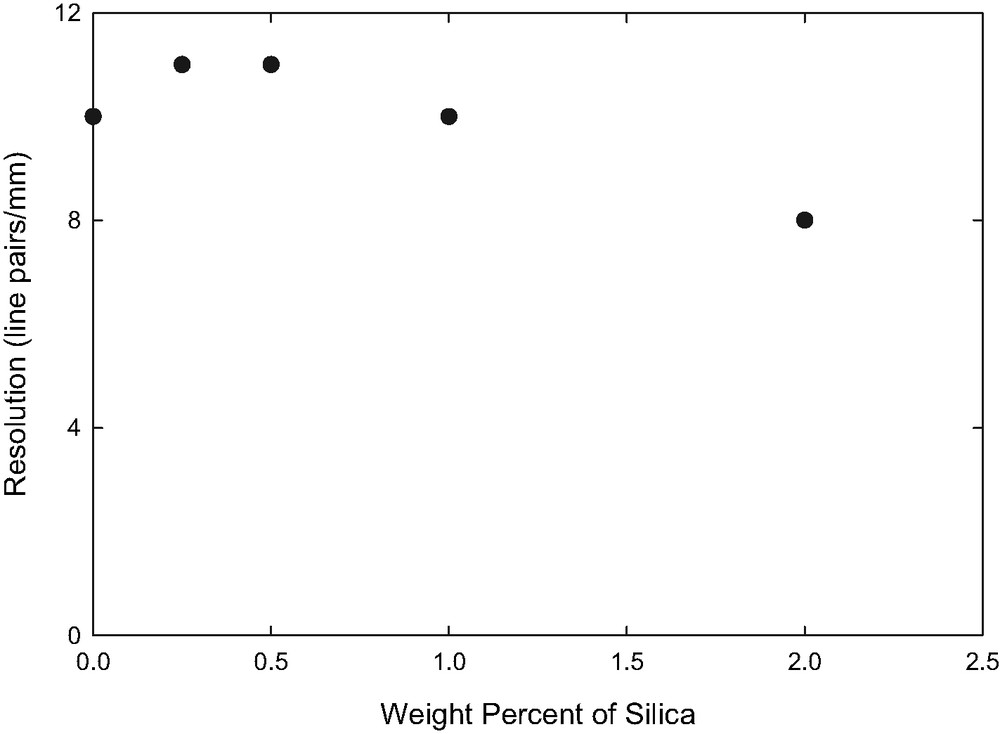
Resolution of transferred image as a function of silica concentration on the toner. Resolution determined to within 1 line pair per mm. Data from Ref. [15].
Subsequent to the transfer process, the toned image is fused, generally upon application of heat and pressure, to permanently fix the image to the receiver. The photoreceptor is cleaned and made ready for the next imaging cycle. These topics, however, are beyond the scope of this paper and the reader is referred elsewhere [2,4] for further details.
A more detailed account of the forces that affect toner transfer and the means of appropriately balancing those forces are also beyond the scope of this paper. For such an account, the reader is referred elsewhere [25]. Suffice it to say, the ability to successfully transfer a toned image to a receiver such as paper generally depends on being able to reduce adhesion forces without unduly compromising the cohesion forces that allow the alphanumeric characters and half-tone dots to remain intact, thereby enabling high quality and high information density images to be transferred to paper. In addition, the electrostatic forces acting on the toner particles either because of induced image charges or from the applied electrostatic field also have to be carefully optimized if high quality transfer is to occur. Finally, the success of electrophotographic technology in today's era of computer-generated documents and the demands for very high image quality is owed, in large measure, to the ability to carefully control the both the electrostatic and electrodynamic interactions that govern the movement of the toner particles.
4 Alternative uses for electrophotographic technology
In modern electrophotographic engines, the entire process to produce an image on paper can take less than 1 s. Considering the need to accurately place a precise number of individual, highly charged micrometer-size particles onto micrometer-size pixels and to be able to do that with four or more colors in a controlled and repeatable fashion does indeed qualify electrophotography as a microfabrication process. Perhaps it is even more impressive when one realizes that a single 8 1/2 × 11 in. sheet of paper can contain over 1010 such particles. That being the case, it is worthwhile to explore the more speculative issue of how electrophotographic technology can be expanded into areas beyond the production of documents and prints.
The key to using electrophotographic technology for microfabrication is to properly control the various forces acting on the toner particles. Specifically, as discussed earlier in this paper, in the ideal world, electrostatic forces would vary as the square of the radius of the toner particle. In contrast, van der Waals forces vary linearly with the particle radius. Thus, electrostatic interactions, including the applied electrostatic transfer force and the interparticle Coulombic repulsion, would all tend to vanish faster that do van der Waals or surface forces with decreasing particle size.
It should be clear from the preceding discussion that the path to using electrophotographic technology in novel microfabrication processes depends on the ability of this technology to utilize smaller and smaller toner particles. However, this depends on being able to control the different forces acting on those toner particles. If van der Waals forces are too strong, it may be difficult to electrostatically transfer the toners from the primary imaging member to an appropriate substrate. In some instances, this limitation can be addressed using novel approaches such as a thermally assisted transfer process [26,27]. This process allowed the use of 3 μm-diameter toner particles and resulted in full-color images of photographic quality. The basic physics underlying this transfer process is to use heat and pressure to soften the toner particles and, in some instances, a thermoplastic overcoat on the receiver. This reduces or eliminates the role of the asperities on the particles, thereby increasing the role played by surface forces. Naturally, it is necessary for the receiver to have higher adhesion to the toner particles than does the photoreceptor used in this process.
In addition to the role of the surface forces contributing to the adhesion of the toner to the photoreceptor or other imaging member, it is also necessary to consider the Coulombic repulsion and van der Waals attraction between particles. If cohesion is too great, agglomerates may form that eliminate the benefit of using small toner particles. In addition, there may be other transfer artifacts that occur such as “hollow character” [28], which is the failure to transfer the centers of fine lines from the photoreceptor to the receiver. Hollow character occurs when the adhesion of a toner particle to the photoreceptor and the cohesive forces are greater than the sum of the adhesive and applied electrostatic forces urging the toner particles to the receiver [28].
Alternatively, if the cohesive forces are too weak, interparticle electrostatic repulsion can result in the formation of toner satellites [23]. In this instance, necessary information or structure from a controlled mass of toner particles is lost. Adhesion, cohesion, and electrostatic repulsion are controlled with release agents such as zinc stearate, charge control agents, and particulate addenda such as nanometer-size silica particles appended to the surface of the toner particles, as discussed earlier in this paper. With this in mind, let us now explore actual and potential uses of electrophotographic technology beyond the realm of the printed document.
Electrophotography has been successfully used to produce printed circuits [29]. In this application, the toned image served as a mask to prevent underlying copper from being etched away. To form the printed circuit, an electrostatic latent image corresponding to the pattern of the desired printed circuit was formed on the photoreceptor and developed into a visible image. The image was then transferred to flex circuit material (i.e. thin copper on a Mylar backing) and fused. The flex circuit was then etched in a ferric chloride solution until the unmasked copper was dissolved, leaving a working printed circuit. If desired, the fused toner coating the circuit board could now be removed using an appropriate solvent.
Isolated satellite particles on the flex circuit material did not pose a problem in this application, as the underlying copper was removed by the naturally occurring undercutting during the etching process. However, voids in the actual circuit lines, caused be either incomplete transfer or corresponding to the vacancies left by the satellite particle could be problematic. This is because etching of the copper could occur in those areas, resulting in defects. Accordingly, it was desirable to reduce the toner-to-photoreceptor adhesion without reducing the toner cohesion. This was accomplished by coating the photoreceptor with zinc stearate, which had been shown to significantly reduce adhesion [16], prior to imaging. The resulting transfer step left few toner particles behind on the photoreceptor, with few satellite particles generated. After etching, the printed circuits that had been formed electrophotographically were tested and found to work quite well. In addition to conventional printed circuits, two dimensional motors that were used to drive the film advance and shutter mechanisms in laboratory versions of the Kodak Disc camera were also produced on flex circuit material. These motors were also found, upon testing, to be fully functional and capable of advancing the film disk frame by frame or opening and closing the camera's shutter in a controlled manner.
An advantage of producing printed circuits using electrophotographic technology is that it facilitates stacking of the circuits, thereby facilitating an increase in packing density. Specifically, electrophotography utilizes the well developed graphic arts processes of producing images in register from one sheet to the next and from the front side of a sheet to the back side of the same sheet (often referred to as ‘perfecting’ in the graphic arts industry). The ability to easily produce printed circuits in register facilitates the production of multilayered circuits, thereby increasing the packing density.
It is but a small leap of faith to envision a process for producing circuits in which the electronic components are produced by the toning step. Appropriate electrostatic separations of the circuit are written on the photoreceptor and a toning station with toner having the correct electronic properties are developed. It is conceivable to produce circuit elements with varying resistances by altering the line thickness and using a “semiconducting” toner. Other variations could include p- or n-doped toners, insulating toners, etc. These marking particles were used in an electrophoretic migration imaging process [30]. These are developed and transferred, in register, to a support. Such a process would allow the design, testing, debugging, and ultimate production of printed circuits in a fairly straightforward manner.
While such toners do not at present exist, there is much underlying chemistry that suggests that they can be made. For example, Van Allan et al. [30] demonstrated a method of producing photoconductive marking particles that would initially have one sign of charge but, under the influence of an applied electric field and illumination, would reverse charge. In a related technological area, the photoreceptors used in electrophotography are also typically designed to conduct predominantly holes [3].
Another application of electrophotography is in the area of lithography. Lithography, as traditionally practiced in the graphic arts industry, consists of printing images by taking advantage of the differences in surface energies of oliophilic and hydrophilic regions on press plates. Today, of course, lithography is being used for various high-tech applications, such as in the fabrication of microelectromechanical systems (MEMS) devices [31].
To produce a lithographic plate for use in an off-set printing press, a sheet of aluminum is first coated with a photocrosslinkable polymer. The plate is then image-wise exposed to light, cross linking the exposed portions of the polymer. The remainder is washed away. The plate is mounted in a printing press and sprayed with water. The crosslinked polymer, being oliophilic, repels the water whereas the now bare aluminum portions are coated with a thin layer of water. An oil-based ink is then applied to the plate. The ink adheres to the dry, polymer coated portions, but fails to coat the wet aluminum. This produces an inked image that can be transferred to paper. The process for producing a press plate takes about an hour and adds substantial costs to producing documents, especially if the runs are relatively short.
Mutz [32] was able to substantially shorten the time needed to produce press plates using electrophotography. He produced press plates by electrophotographically developing an electrostatic latent image on a photoreceptor and transferring that image to sheets of aluminum. He then used these plates in an offset press to print images in a conventional manner employing commercial printing inks.
For yet another distinct application of electrophotographic technology, Demers and Cherukuri [33] invented a device that allows the electrostatic dispersement of beads that contain bioactive agents such as pharmaceuticals, herbicides, pesticides, etc. This has spurred the use of technology closely related to that used in electrophotography [34] for the preparation of pharmaceuticals. This technology allows the controlled dispersement of specified quantities of pharmaceutical compounds.
5 Speculation into the future
It should be clear that, by controlling adhesive, cohesive, and electrostatic forces, electrophotographic technology can be used to control the placement of large numbers of micrometer-size particles onto a substrate. The particles can then be transferred to another substrate and fused into a solid mass if desired. This can be done precisely, repeatedly, and at a high rate of speed. Moreover, the ability to precisely address where each particle is to be deposited, as well as the quantity of particles to be deposited, gives electrophotography some unique capabilities. Indeed, in this manner, the production of documents by electrophotographic means can be considered a type of micromanufacturing.
However, as also demonstrated in this paper, the use of electrophotographic technology, today, is not limited to the production of documents. Rather, it has already found applications in the production of printed circuits, lithoplates, and pharmaceuticals. It is worthwhile, now, to speculate on further applications of electrophotographic technology.
Let us consider, for example, the production of a micrometer-size gear. This can be made, electrophotographically, from plastic in a fairly straightforward manner. However, one would probably want to use a substrate that is either water soluble or comprises a water soluble layer that can be dissolved, thereby releasing the gear. Alternatively, one could make a metallic gear in a manner by using the toner to serve as a mask and etching an underlying metallic substrate in a manner analogous to forming a printed circuit. One could go a step further and produce a micromachine by designing the machine on a computer, outputting the design to a laser or LED writer and producing an electrostatic latent image in a photoreceptor, and then transferring the image. Gear shafts can be produced from cylindrical ceramic, fiberglass, or carbon fibers, preferably coated with a release agent to prevent the toner from adhering to the shaft, positioned and deposited electrophotographic, possibly using an electrostatic field to correctly orient the cylindrical particle, and appropriately fusing the toner. Upon suitably releasing the components, one would have a simple, micromechanical machine. As with the printed circuits, multiple layers can be laminated together to form a more complex machine. In this instance, it may be desirable to even have some of the axles to protrude through the substrate and make connections with the registered machine in the next layer to couple the layers together.
One could still take this a step further. Particles need not be made from plastic, as is the case with toner. Once could use, for example, various ceramic particles and after producing the components electrophotographically, sinter them together. If an appropriate receiver had been chosen, for example paper, the receiver would incinerate, leaving just the components which could either be free or linked. The components could be simple structures comprising portions of MEMS devices or could be self-assembled and oriented with appropriate use of surface and electrostatic forces. The use of electrophotographic technology for micromanufacturing is limited only by the need to carefully control surface and electrostatic forces and by one's imagination.
6 Conclusions
Electrophotographic technology relies on the ability to control and properly balance adhesive, cohesive, and electrostatic forces. By doing so, one can precisely place micrometer-size particles onto micron-size pixels in a robust and high speed manner. This allows electrophotography to be used to produce hard copy prints from digital devices and, as such, is a form of micromanufacturing, with the hard copy being the production output. However, electrophotographic technology holds the promise of being suitable for many other micromanufacturing applications where the ability to precisely control the positioning, placement, and number of small particles is important.
1 Standard units used in graphic arts.
2 Dots per inch. This is standard units used in the graphic arts field.