1 Introduction
Mineralizers are inorganic substances which accelerate the reaction process in the solid phase, liquid phase and in the solid–liquid interface [1]. They have a major impact on the determination of the burning zone and the rate of clinker compound formation. Mineralizers facilitate the clinkerization process, decrease the liquid phase temperature and mineral fusible eutectic, save the clinker production energy and improve the cement compound reactivity [2,3].
Several works, carried out in different laboratories [4–8], were about the influence of mineralizers on the decrease in the clinker burning temperature. It was noted that a minimization of the energy expenditure is possible by using small quantities of these inorganic substances. Mineralizers can, in some cases, improve the hydraulic properties of Portland clinker [7,9]. Moreover, the effect of mineralizers on the clinker minerals formation and the phase transformation during the clinkerization was the subject of much research [10–13].
The aim of this work was to examine the influence of some mineralizers (calcium, potassium and sodium fluorides) on the decreasing of burning temperature of industrial raw mixtures, and to study their effects on chemical, mineralogical, physical, structural, morphological and mechanical properties of the clinker cement.
These mineralizers were added separately to three categories of industrial raw mixtures of three Algerian cement factories (units of Zahana, Beni-Saf and Chlef). The mixtures were burned at different temperatures: 1200, 1250, 1300 and 1350 °C.
2 Experimentation
The development of clinker formation was followed mainly on the basis of the free lime contained in the burned samples. It is the most used procedure so far because calcium oxide, initially formed by dissociation of CaCO3, is gradually consumed by giving clinker phases. The formation of the latter will be complete when the free lime content tends to zero.
In order to prepare 3 g of mixture, 1% of mineralizer (KF, NaF or CaF2) was added to the industrial raw mixture (Table 1). After homogenization in a mixer for 20 min, the mixture was put in a platinum crucible and introduced into a muffle furnace with a heating rate of 30 °C/min. The sample was maintained at the desired burning temperature for 30 min, then cooled quickly under air and crushed. The burned mixture was analyzed by the traditional method at the laboratory of Zahana factory, according to the European standard (NE-2-1-015-1984), in order to determine the residual free lime content.
Chemical composition (wt.%) of the raw mixture (MC) of three cement factories
Raw mixture | CaO | SiO2 | Al2O3 | Fe2O3 | MgO | SO3 | K2O | Na2O |
Zahana (MCZ) | 66.33 | 22.90 | 4.27 | 2.60 | 1.58 | 0.83 | 0.71 | 0.77 |
Beni-Saf (MCB) | 65.67 | 21.98 | 5.47 | 3.63 | 0.54 | 1.65 | 0.43 | 0.62 |
Chlef (MCC) | 65.40 | 19.15 | 4.70 | 4.49 | 0.30 | 2.84 | 1.38 | 1.73 |
The chemical composition of samples was determined by X-ray fluorescence (PW 1404X), the morphology by scanning electron microscopy, using a Philips XL30 microscope. The former reported in Table 1, is expressed as the weight percentage of oxides in the three raw mixtures (MC): Zahana (MCZ), Beni-Saf (MCB) and Chlef (MCC), without taking into account the loss on ignition.
The chemical composition of alite (3CaO.SiO2 or C3S) in these clinkers was determined by scanning electron microprobe analysis on a Castaing type (CAMEBAX) electron microscope.
Crystallized phases in the clinker minerals were identified by X-ray diffraction with a Philips PW 1800 diffractometer equipped with a variable slit opening using the Cu Kα radiation.
Mechanical and physical tests on the clinker cements were carried out according to French standards (NF P15-431, 432, 442, 451, 461). The addition effects on the setting time, expansion, specific area, mechanical resistance and hydration heat of these products were determined. These cements were prepared at the Zahana factory, in accordance with the standardized method (NF P15-301) used in the industry, by adding 5% gypsum and 15% pozzolana to the synthesized clinkers. The mineralizer effectiveness was compared to the ordinary clinker produced by the Zahana factory (COZ).
3 Effect of alkaline fluoride on the clinkerization temperature
All the used fluorides (KF, NaF, CaF2) played an interesting role in the decrease of clinkerization temperature for the three types of raw mixtures, as shown in Fig. 1. The free lime content was reduced, reaching very low values at burning temperatures lower than 1300 °C, which implies the alite formation at this low temperature.
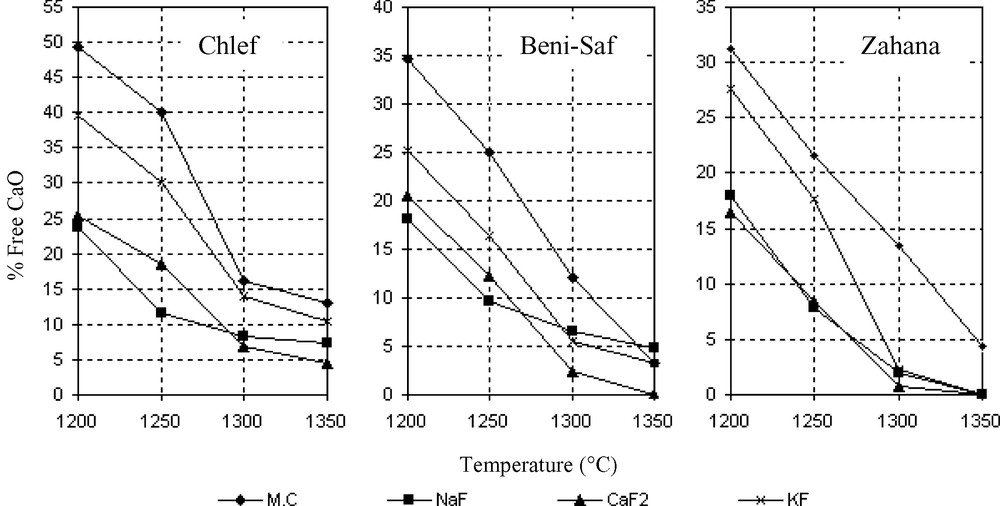
Effect of alkaline fluorides on the burning temperature of the clinker raw materials.
The presence of the fluorinated salts accelerates the clinker minerals formation by decreasing the lower limit of phases' stability in the mixture. This effectiveness is due primarily to the presence of fluoride anions, characterized by high electronegativity, which interact with the ions (Ca2+, Si4+) on the solid surface. This surface is maintained in a high-energy state, leading to polarization and rearrangement of atoms, which increases the solid activity either to form new phases, or to melt [14].
The influence of the salts containing fluorine on the burning temperature varies considerably with the nature of the cation combined with fluorine. The NaF effectiveness on the lime combination below 1280 °C is greater, compared to the other mineralizers (Fig. 1). This is due to the fluoride effect, which increases appreciably with the decrease in atomic number of the fluorine-combined cation [14]. The KF effect is not so important below 1280 °C. However, above this temperature it becomes very effective. This can be seen by the fast formation of C3S (3 CaO·SiO2) and C2S (2 CaO·SiO2). CaF2 presents an intermediate effect between CaF2 and NaF.
4 Action of alkaline fluorides on clinker minerals formation
The clinkers obtained by burning (at 1300 °C) the raw mixtures of Zahana containing 1% NaF, KF or CaF2 were retained for this study. The ordinary clinker of Zahana (COZ), burned at 1470 °C, has been taken for comparison.
4.1 Chemical composition of clinkers
The results of the chemical analysis by X-ray fluorescence of the clinkers are reported in Table 2.
Chemical composition (wt.%) of the synthesized clinkers
Clinker with | Burning T (°C) | %CaO | %SiO2 | %Fe2O3 | %Al2O3 | %MgO | %SO3 |
NaF | 1300 | 66.22 | 19.80 | 3.89 | 5.06 | 1.81 | 1.07 |
CaF2 | 1300 | 66.86 | 20.20 | 3.89 | 4.78 | 1.80 | 2.29 |
KF | 1300 | 66.36 | 20.41 | 3.31 | 5.15 | 1.80 | 2.02 |
COZ | 1470 | 67.37 | 20.46 | 2.74 | 4.42 | 2.45 | 1.04 |
The weight percentage of each oxide in these clinkers is very close. However, the presence of salts containing fluorine increases the wt.% of Fe2O3, and decreases the wt.% of MgO in the synthesized clinkers. This suggests that salts containing fluorine mainly act on Fe and Mg reactivity. On the other hand, results reported in Table 2 suggest that CaF2 acts on the reactivity of sulfur by increasing significantly the wt.% of S.
4.2 Mineralogical composition of clinkers
The mineralogical composition of these clinkers was determined from the optical microscope observations by using the polished section method. The results are reported in Table 3.
Mineralogical composition of synthesized clinkers
Clinker with | Burning temperature (°C) | % Alite | % Belite | % C3 A | % C4 AF | % P.A. |
NaF | 1300 | 55 | 25 | 8 | 9 | 24.06 |
CaF2 | 1300 | 53 | 28 | 6 | 11 | 22.98 |
KF | 1300 | 48 | 32 | 6 | 11 | 23.01 |
COZ | 1470 | 52 | 29 | 6 | 11 | 20.20 |
The weight percentages of clinker minerals [alite (C3S), belite (C2S), 3CaO.Al2O3 (C3A) and 4 CaO·Al2O3·Fe2O3 (C4AF)] were calculated compared to the crystallized mass, while the percentage of the amorphous phase (P.A.) is given compared to the total mass of the sample, by using the following Bogue method:
- ● if the aluminic module, % P.A. = 6.1 Al2O3 (%Fe2O3) + %MgO + %SO3 + %K2O.
- ● if MA ≤ 1.38, % P.A. = 8.2 (%Al2O3) – 5.22 (%Fe2O3) + % MgO + % SO3 + %K2O + %Na2O.
The alite content in the clinkers burned at low temperature (1300 °C), by using the fluorides (NaF and CaF2) as mineralizers, is higher than that of the ordinary clinker of Zahana (COZ). This result is explained by the great effect of fluorides on the clinker phases' formation even in the solid state [5].
The presence of F– in the mixture accelerates the lime combination by forming C2S at low temperature. This latter phase reaches significant values with the appearance of the amorphous phase, which intensifies the alite formation.
The contents of tricalcium aluminate (C3A) and tetracalcium aluminoferrite (C4AF) in these clinkers are very close. Nevertheless, the percentage of C4AF (4 CaO·Al2O3·Fe2O3) is higher than C3A (3 CaO·Al2O3).
4.3 Chemical composition of alite in the clinkers
The chemical compositions of alite, obtained from EDAX analyses, in the four clinkers (ordinary clinker of Zahana, clinker with CaF2, NaF and KF) are reported in Table 4.
Chemical composition (wt.%) of alite in synthesized clinkers
Clinker | CaO | SiO2 | Al2O3 | Fe2O3 | MgO | Na2O | K2O | SO3 | CaO/SiO2 |
COZ | 72.35 | 24.69 | 1.11 | 0.30 | 1.16 | 0.13 | – | 0.25 | 2.93 |
With CaF2 | 64.90 | 25.15 | 2.70 | 0.41 | 1.63 | 1.19 | – | 3.96 | 2.58 |
With NaF | 62.44 | 25.56 | 2.29 | 0.52 | 2.03 | 3.99 | – | 3.15 | 2.44 |
With KF | 64.01 | 25.40 | 2.52 | 0.86 | 1.93 | 1.44 | 0.98 | 2.76 | 2.52 |
The CaO/SiO2 ratio in alite of clinkers containing fluorides is smaller than in the ordinary clinker. This is due to the reduction of CaO content in this phase, because these mineralizers promote Ca substitution by Mg, Na and K [15], which is confirmed by the high amount of these agents in alite (Table 4). Alumina, iron oxide and sulfur oxide are present in the alite of these clinkers, with contents higher than those in the ordinary clinker. The smallest ratio (lime/silica) is observed in the case of the clinker containing NaF.
5 Effect of alkaline fluorides on clinker minerals structure
In order to show the fluorides, effect on the clinker mineral structure, the morphological and structural properties of the ordinary clinker of Zahana (COZ), burned at 1470 °C without mineralizers, were characterized. The scanning electron micrograph (Fig. 2) shows that this clinker presents crystals with hexagonal and circular shapes for alite and belite, respectively. The presence of these phases is confirmed by X-ray diffraction analyses (Fig. 3).

Scanning electron micrograph of Zahana ordinary clinker burned at 1470 °C (COZ).
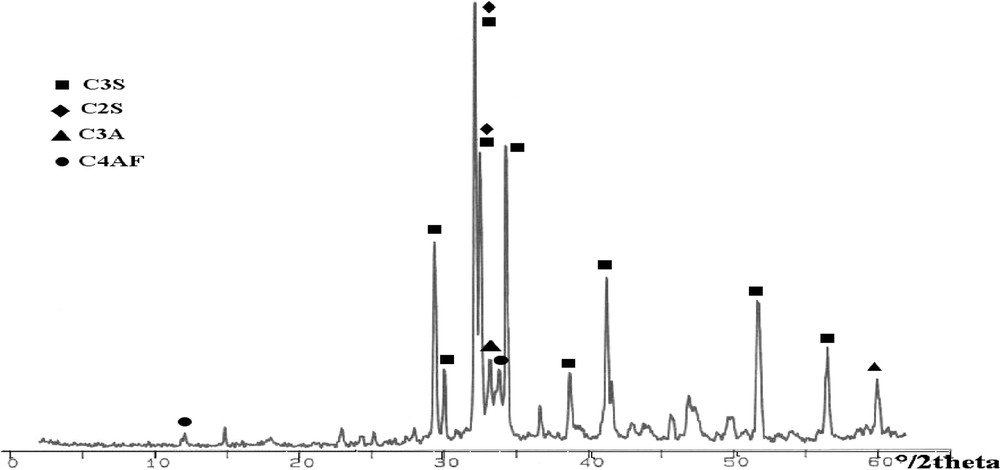
X-ray pattern of Zahana ordinary clinker burned at 1470 °C (COZ).
5.1 Silicates phases (alite and belite)
As it is noticed on the scanning electron micrographs (Figs. 4,6 and 8), the crystallized phases (alite and belite) present different morphologies and crystal sizes. They form coarse aggregates in the clinker with CaF2, which could reduce their hydraulic activity appreciably. These phases are characterized by small crystals in clinker with NaF (Fig. 6) and irregular morphologies in clinker with KF, the crystal sizes of which are variable (Fig. 8).
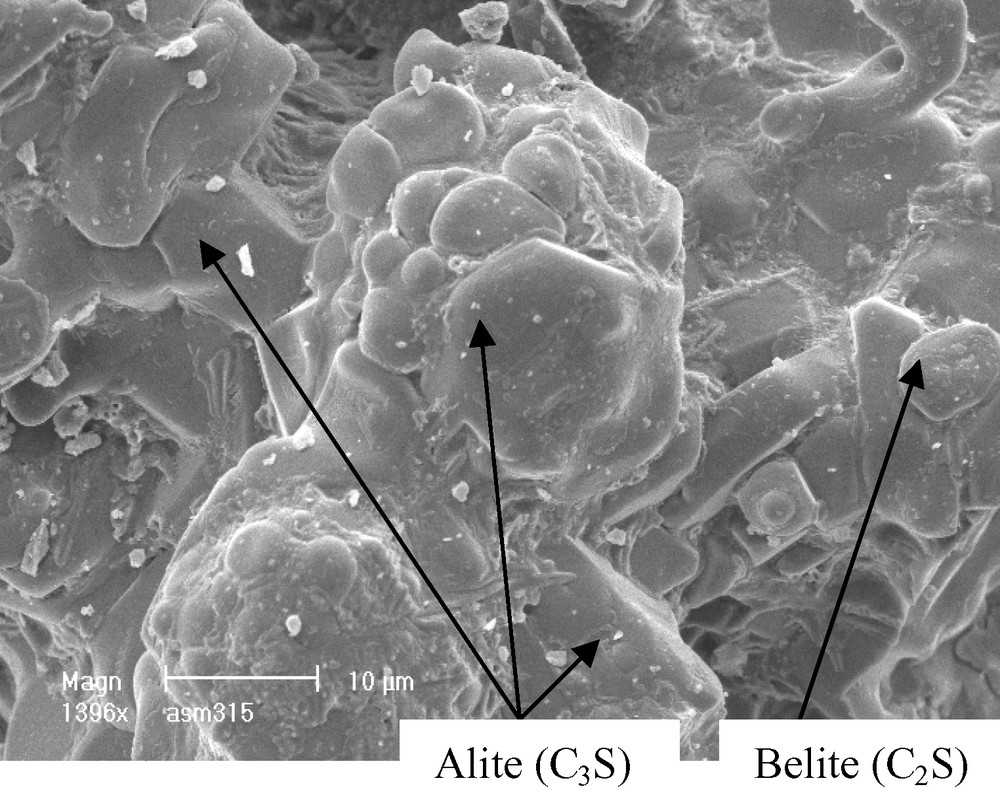
Scanning electron micrograph of CaF2-clinker burned at 1300 °C.

Scanning electron micrograph of NaF-clinker burned at 1300 °C.
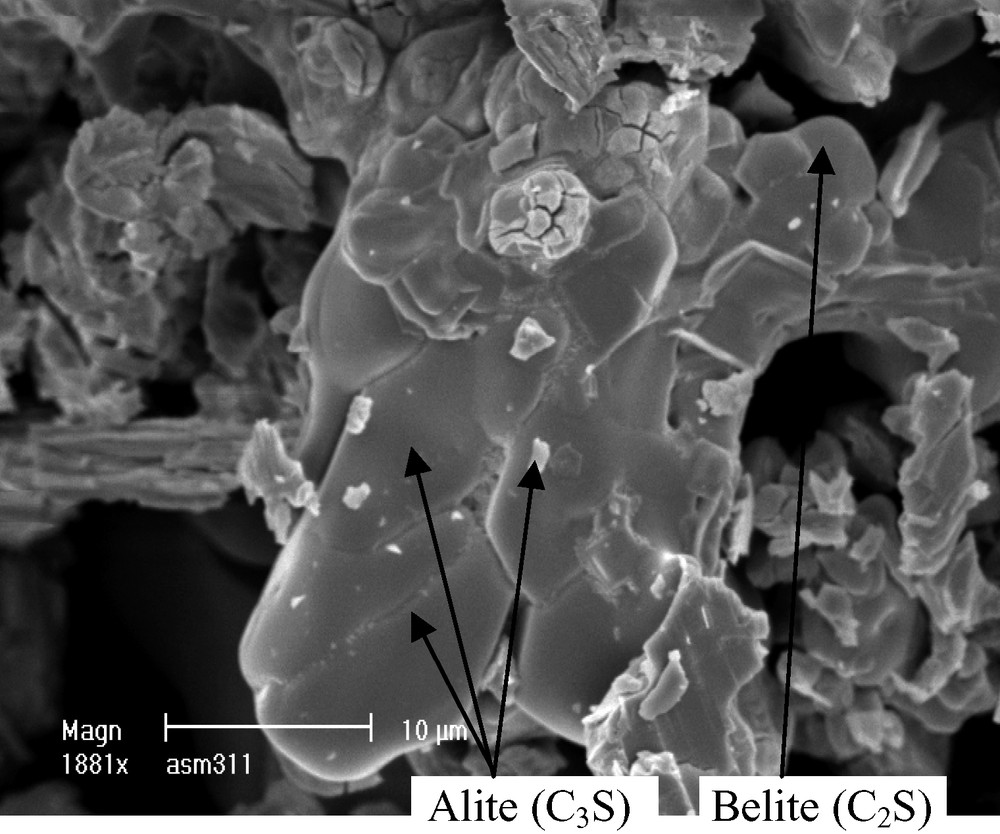
Scanning electron micrograph of KF-clinker burned at 1300 °C.
The XRD pattern of clinker with CaF2 or NaF (Figs. 5 and 7) shows that the crystallinity of these solid solutions (alite and belite) is slightly different from the one reported in Fig. 3 (Zahana clinker). From the relative intensity of the peaks, it seems that there is more alite in both clinkers than in the Zahana ordinary clinker. Such results are in agreement with the analyses reported in Fig. 1 (Zahana) and Table 3. The DRX pattern of clinker with KF (Fig. 9) presents peaks less intense than those of COZ, which indicates the incomplete crystallization of the calcium silicates.

X-ray pattern of CaF2-clinker burned at 1300 °C.

X-ray pattern of NaF-clinker burned at 1300 °C.

X-ray pattern of KF-clinker burned at 1300 °C.
On the other hand, the inter-reticular distances in the alite crystal lattice of clinkers with CaF2 or KF are larger than those of COZ (Table 5). This could explain the presence of inserted elements in these solid solutions. Such results are in agreement with the chemical composition (Table 4) which seems to indicate that CaF2 and KF support the incorporation of MgO, SO3, Na2O, K2O, Al2O3 and Fe2O3, as it was observed by Kleem and Jawed [15]. The increase of inter-reticular distances is responsible for the large crystal size of alite and belite in these clinkers (Figs. 4 and 8).
Main inter-reticular distances of alite crystal lattice in different clinkers
Clinker with | Main inter-reticular distances of alite (C3S) | ||||
Peak 1 | Peak 2 | Peak 3 | Peak 4 | Peak 5 | |
COZ | 3.0386 | 2.7777 | 2.7507 | 2.6112 | 2.1871 |
NaF | 3.0336 | 2.7717 | 2.7421 | 2.6082 | 2.1827 |
CaF2 | 3.0476 | 2.7879 | 2.7599 | 2.6217 | 2.1957 |
KF | 3.0471 | 2.7888 | 2.7583 | 2.6187 | 2.1945 |
The short inter-reticular distances of clinkers with NaF (Table 5) are explained by the decrease in the CaO/SiO2 ratio in C3S with the substitution of Ca by Mg and Na (Table 4). This substitution allows the reduction in the crystal lattice parameters of alite, because of the calcium atomic diameter, which is larger than that of magnesium and sodium. Consequently, crystals characterized by reduced sizes are formed [16]. This is confirmed by scanning electron micrograph (Fig. 6).
The morphology and crystal structure of these phases in the clinker with NaF, particularly the alite, contribute to the improvement of hydraulic activity of its minerals [17].
5.2 Aluminates and aluminoferrites phases (C3A and C4AF)
C4AF seems to be better crystallized in clinker with CaF2 than in the COZ one (Fig. 3 peak at 33.9°/2θ and Fig. 5 peak at 33.8°/2θ). On the other hand, these peaks are shifted from their usual positions. This could be explained by the presence of CaF2, which supports the aluminate crystallization in the form of C11A7CaF2, at temperatures varying between 1250 and 1300 °C [18], and the aluminoferrite in the phase C6A2F or C8A3F [16]. The CaF2 addition inhibits C3A formation and supports C4AF crystallization [7].
C4AF and C3A crystallization in clinkers with NaF or KF (Figs. 7 and 9) is more significant than that in COZ. But contrarily to NaF-clinker and COZ, C4AF is crystallized better than C3A in KF-clinker, as it is shown by their peaks' intensities (Fig. 9). This is explained by the strong presence of SO3 in the mixture (Table 2), which improves the crystallization of C4AF [19].
6 Effect of alkaline fluorides on cement hydraulic properties
To determine the physical and mechanical properties of selected cements, containing low contents of free lime at low temperature (1300 °C), great quantities of clinker are synthesized to carry out the hydration and hardening tests.
The mixture made up of 80% synthesized clinker, 5% gypsum and 15% pozzolana, was crushed and mixed, in accordance with the used factory method, for obtaining Portland cement (CPJ or CEM II), according to standard (NF P15-301). Then 450 g of this cement were mixed with 1350 g of standardized sand and 225 g of water, to obtain mortars for the physical and mechanical analyses.
6.1 Density and specific area of Blaine (SSB)
Table 6 reports the results of the density and specific area of the synthesized clinkers, by using a densitometer and permeameter of Blaine, according to the method recognized by French standardization (NF P15-442).
Density and specific area of Blaine (SSB) of the synthesized clinkers
Clinker with | Burning temperature (°C) | Density (g/ml) | SSB (cm2/g) |
NaF | 1300 | 1.19 | 2724.73 |
CaF2 | 1300 | 1.23 | 2887.43 |
KF | 1300 | 1.26 | 2774.74 |
COZ | 1470 | 1.23 | 3180.28 |
All clinkers have an identical density, which shows that the addition of small quantities of mineralizer does not affect this property (Table 6).
The specific area (SSB) of clinkers containing fluorides (Table 6) is smaller than that of ordinary clinker (COZ). This is due to the presence of great quantities of amorphous phase (glass) in these products (Table 3), which decrease the porosity and improve the hardness of the clinker grains.
6.2 Mechanical strength
The results of compressive and bending strengths of prepared cements, determined by mechanical tests according to the French standard (NF P15-451), are given in Table 7.
Mechanical resistance of prepared cements
Cement with | Burning temperature (°C) | Compressive strength (kg/cm2) | Bending strength (kg/cm2) | ||||
2 days | 7 days | 28 days | 2 days | 7 days | 28 days | ||
NaF | 1300 | 124.63 | 285.00 | 580.00 | 25.00 | 45.00 | 65.40 |
CaF2 | 1300 | 165.88 | 263.68 | 322.00 | 36.25 | 39.00 | 43.00 |
KF | 1300 | 158.38 | 215.88 | 504.00 | 20.00 | 32.50 | 51.40 |
COZ | 1470 | 169.00 | 332.00 | 431.00 | 35.00 | 62.50 | 70.00 |
The compressive and bending strengths of clinker cement are not affected by CaF2 addition at short times (2 days). Whereas this mineralizer reduces the evolution rate of these resistances, of which their values at 28 days are lower than those of COZ (Table 7). This is due on one hand to the texture of alite and belite, characterized by coarse crystals (Fig. 4 and Table 5), and on the other, to the strong presence of SO3 in this clinker (Table 2). This later reduces the cement hardening by forming the ettringite (3CaO·Al2O3·3CaSO4·32H2O). This ettringite, formed during the clinker hydration, precipitate on the mineral surface and slow down the hydration reactions [20,21].
Contrary to CaF2, the cement of KF-clinker has a mechanical strength at 2 days lower than that of Zahana cement. This resistance evolves slowly up to 7 days, after which it evolves quickly, to reach compressive strength values higher than those developed by the industrial cement at 28 days (Table 7). The bending strength remains relatively weak at 28 days compared to Zahana cement.
The mechanical resistance of clinker cement with NaF appears to be relatively weak in the short time, but it evolves quickly to reach strength compressive values higher than those developed by industrial cement (Table 7). The bending strength is also considerable in this cement. These characteristics are due to the high alite rate (Table 3) and its disturbed crystal lattice, both of which improve the clinker hydraulic reactivity [22].
6.3 Physical properties of cements
Physical tests used to determine the expansion, setting time and hydration heat of the cements, according to the French standard (NF P15-432), (NF P15-431) and (NF P15-461) successively, led to the results presented in Table 8.
Physical properties of prepared cements
Cement with | T (°C) of burning | Expansion (mm) | Setting time (hour:min) | Hydration heat (cal/g) | |||
Beginning | End | 3 days | 7 days | 28 days | |||
NaF | 1300 | 00 | 4:15 | 6:50 | 76.9 | 94.4 | 98.8 |
CaF2 | 1300 | 00 | 6:05 | 7:43 | 58.2 | 72.1 | 80.6 |
KF | 1300 | 00 | 3:50 | 5:55 | 60.5 | 84.7 | 94.3 |
COZ | 1470 | 00 | 3:55 | 5:45 | 56.3 | 68.6 | 88.4 |
The hydration heat of clinkers containing fluorides is stronger than that produced by the ordinary clinker of Zahana, in particular the clinker with NaF, which presents a very high value. This heat, released during hydration reactions of clinker minerals, increases with the presence of mineralizers. This is due to the disturbed structure of minerals, in particular alite, due to the presence of foreign elements within the crystal lattice, which facilitates their reaction with mixing water [22]. The strong heat release, at 28 days of hydration (Table 8), explains the fast evolution of the clinkers' mechanical resistance (Table 8).
Among these cements, the one containing KF is the only having a setting time identical to that of Zahana cement. NaF and CaF2 increase the cement setting time.
These analyses show that the use of 1% of KF, NaF or CaF2, as mineralizers to lower clinkerization temperature, improves the clinker hydraulic activity. This is explained by the strong alite percentage in clinker with NaF or CaF2 (Table 3), and the alite disorder in clinker containing KF (Figs. 8 and 9). Moreover, the presence of foreign elements (Na, Mg, K, Al, Fe and S) in the alite structure and the decrease of CaO/SiO2 ratio in this phase, as it is noticed in Table 4, allow the improvement of cements hydraulic properties.
7 Conclusion
Chemical and mineralogical analyses, carried out on clinkers from three Algerian cement factories (Zahana, Beni-Saf and Chlef), showed that these products present suitable properties, according to the international standards. Nevertheless, the cement production requires intense energy consumption, owing to the high clinkerization temperature used in these units, which often exceeds 1470 °C.
The study of the decrease of the clinkerization temperature without influencing the product quality, and by adding salts containing fluorine (mineralizers CaF2, NaF and KF) lead to satisfactory results.
These salts have a great effectiveness particularly with the Zahana clinker. It is obtained at 1300 °C only, by the addition of 1% of CaF2, NaF or KF.
The presence of these fluorinated mineralizers modifies the clinker properties. CaF2 seems to reduce the hydraulic activity.
NaF improves the clinker crystallization at low temperature, by supporting massive formation of alite. Thus, the hydraulic activity is increased, and the physical and mechanical properties of the clinker are improved.
KF improves physical and mechanical properties of cement. The great product resistance is ensured by alite which, in spite of its moderated percentage in the clinker, presents a significant hydraulic activity due to its disturbed crystalline structure.
Obtaining a clinker at 1300 °C is possible by the addition of 1% CaF2, NaF or KF. These mineralizers improve the structural properties of clinker minerals, which lead to the improvement of the cement hydraulic properties, particularly NaF which increase the C3S rate in the clinker.
Acknowledgments
The authors thank Dr. L. Josien, from the ‘Laboratoire des matériaux à porosité contrôlée’ for his technical assistance, and thank Dr. A. Mhamedi (PhD, Salford)) and Dr. N. Belabbes (MA, London), both from Mostaganem University, for their linguistic review of the text.