1 Introduction
The microwave-hydrothermal (M-H) synthesis of molecular sieves is a relatively new area of research [1–7]. It offers many distinct advantages over the conventional hydrothermal synthesis. These include rapid heating to crystallization temperature due to volumetric heating, resulting in homogeneous nucleation, fast supersaturation by the rapid dissolution of precipitated gels and eventually a shorter crystallization time compared to conventional autoclave heating [1–7]. It is also energy efficient and economical [1–7]. On the other hand, Friedel-Crafts aceylation of aromatic compounds and aromatic heterocyclic compounds is an excellent example of electrophilic substitution catalyzed by acidic or basic catalysts, which has been widely used in industry for production of various organic value-added intermediates. Preparation of aromatic ketones has received much attention in recent years because of their commercial importance, as they are being largely used as intermediates in the synthesis of pharmaceuticals (naproxen, dextromethorphan, ibuprofen), dyes, fragrances, and agrochemicals [8]. Conventionally, these reactions are carried out in presence of homogeneous catalysts such as AlCl3, and BF3, strong mineral acids like H2SO4, HF, or supported Lewis acid catalysts, using acid chloride or anhydride as an acylating agent [9]. Regrettably, the use of these catalysts in industry causes many environment related problems as they are highly corrosive in nature and cannot be regenerated for more use. Moreover, the separation of the homogeneous catalysts from the product mixture is hard and often a stoichiometric amount excess of the catalysts is required as the Lewis acid catalysts form a complex with the product ketones, which is then destroyed in the hydrolysis step required for product isolation. To avoid these environmental associated problems, it is desirable to develop a catalyst process which is stable, environmentally friendly, and recyclable. A class of interesting catalytic systems which has been widely used these days and can eliminate the corrosion and environmental problems is the heterogeneous solid Brönsted acid zeolites and zeotypes molecular sieves, which are highly efficient, sustainable, recyclable, and ecofriendly. Indeed, the acetylation of anisole and 1,2-dimethoxy benzene leads to the synthesis of p-acetylanisole and 4-acetylveratrole, which are commercially important products and are being used as the precursors of a sun protector and of a component in an insecticide formulation [10], respectively. Different catalysts including zeolites [11–18], heteropoly acids [19,20], sulfated metal oxides [21] and AlSBA-15 [22], have been investigated for the Friedel-Crafts alkylation and acetylation reactions. Indeed, in the present study we have studied the liquid phase of acetylation of 1,2-dimethoxybenzene with acetic anhydride over Ni-MCM-41 catalysts synthesized by microwave irradiation method.
2 Experimental
2.1 Synthesis of the catalysts
M-H synthesis of Ni-MCM-41 mesoporous molecular sieves with different Si/Ni ratios (Si/Ni = 80, 50, 10) was performed using a MARS5 (CEM Corp., Matthews, NC, USA) microwave digestion system. This system operates at a maximum power of 1200 W and the power can be varied from 0 to 100% and is controlled by both pressure and temperature to a maximum of 350 psi and 513 K, respectively. A 2.45 GHz microwave frequency was used which is the same as that used in domestic microwave ovens. The syntheses were carried out in double-walled digestion vessels, which have an inner liner and cover, made up of Teflon PFA and an outer strength vessel shell of Ultem polyetherimide. In a typical synthesis, 21.32 g of sodium metasilicate (Na2SiO3 9H2O, CDH) was dissolved in 60 g of water. The reaction mixture was stirred for 2 h. Meanwhile, cetyltrimethylammonium bromide (5.47 g, CTABr, OTTO Chemie) and nickel nitrate were dissolved in 20 g of distilled water. Then, the resultant solution was added dropwise to the sodium metasilicate solution. The final mixture was stirred for 1 h. The pH of the gel was adjusted by using 2 M sulfuric acid (H2SO4; 98% Merck) and it was stirred for another 3 h. Thus obtained gel was allowed to crystallize under M-H conditions at 373 K for 2 h. The crystallized product was filtered off, washed with warm distilled water, dried at 383 K and finally calcined at 813 K in air for 6 h.
2.2 Characterization techniques
The X-ray diffraction (XRD) patterns of samples were recorded with a powder XRD instrument (Rigaku D/max 2500PC) with Cu Kα radiation (λ = 0.15418 nm). It was operated at 40 kV and 50 mA. The experimental conditions correspond to a step width of 0.02° and the scan speed of 1°/min. The diffraction patterns were recorded in the 2θ range of 1–10°. Fourier transform infrared spectra of samples were recorded on a Nexus FT-IR 470 spectrometer made by Nicolet Corporation (USA) with KBr pellet technique. The effective range was from 400 to 4000 cm−1. Specific surface area and pore size were measured by using a NOVA2000e analytical system made by Quantachrome Corporation (USA). The specific surface area was calculated by the Brunauer-Emmett-Teller (BET) method. The pore size distribution and pore volume were calculated by the Barrett-Joyner-Halenda (BJH) method. Transmission electron microscopy (TEM) morphologies of samples were observed on a Philips TEMCNAI-12 with an acceleration voltage of 100–120 kV. The nickel content in the samples was determined by the inductively coupled plasma (ICP) technique (Vista-MAX, Varian). The density and strength of the acid sites of the different Ni-MCM-41 samples were determined by the temperature programmed desorption (TPD) of pyridine. About 100 mg of the materials were evacuated for 3 h at 523 K under vacuum (P < 10−5 kPa). Thereafter, the samples were cooled to room temperature under dry nitrogen followed by exposure to a stream of pyridine in nitrogen for 30 min. Subsequently, the physisorbed pyridine was removed by heating the sample to 393 K for 2 h in a nitrogen flow. The TPD of pyridine was performed by heating the sample in a nitrogen flow (50 mL/min) from 393 to 873 K with a rate of 10 K/min using a high-resolution thermogravimetric analyzer coupled with a mass spectrometer (SETARAM setsys 16MS). The observed weight loss was used to quantify the number of acid sites assuming that each mole of pyridine corresponds to one mole of protons.
2.3 Catalytic testing
Acetylation of 1,2-dimethoxybenzene with acetic anhydride has been carried out under liquid phase conditions. The liquid phase reaction set up consists of two necked 50 mL round bottom flask duly fitted with a condenser in one end for cooling and another vent is closed with Teflon septum for collecting samples by glass syringe at regular intervals. The whole system was kept in a thermostated oil bath attached with a magnetic stirrer coupled with a heating plate. In a typical reaction, the catalyst was added to a solution of 2.6 g 1,2-dimethoxybenzene (18.9 mmol), 0.4 g acetic anhydride (3.8 mmol) and 50 mL chlorobenzene together with 1 g nitrobenzene as internal standard. Then, the reaction mixture was heated to the required temperature and the samples were collected with regular intervals of time. The collected samples were analyzed periodically by a gas chromatograph (HP-6890) equipped with a FID detector using a DB-5 capillary column. The products were confirmed with GC-MS (HP-5973) analysis.
3 Results
3.1 Characterization of the samples
The small angle XRD patterns of Ni-MCM-41 (Si/Ni = 80, 50, 10) synthesized by the microwave irradiation method are shown in Fig. 1. The Ni-MCM-41 (80) sample gives a very strong (100) peak followed by (110) and (200) lower intensity peaks. All three distinct Bragg reflections at low angles were indexed on a hexagonal lattice. However, when the nickel content ratio increased from 50 to 10, the intensities of the long range ordered peaks were gradually reduced. However, compared with the pattern of the typical MCM-41 mesoporous molecular sieve [23], it can be noted that the d100 spacing in Ni-MCM-41 samples is significantly larger than MCM-41 (for both as-synthesized and calcined samples) shows the incorporation of Ni in the MCM-41 structure. The nickel content in Ni-MCM-41 is increased with Ni content in the synthesis gel (Table 1). The porosity of the samples was evaluated by N2 adsorption isotherms. The specific surface areas and pore size distributions and pore volumes calculated by BET and BJH methods are summarized in Table 1. However, combined with the surface area data (689m2/g) listed in Table 1 and the XRD data (Fig. 1), the sample Ni-MCM-41 (10) still has a partial mesoporous structure, but the ordering is poor. Fig. 2 presents the pore size distribution curves of the three calcined samples Ni-MCM-41 synthesized by microwave irradiation method. As shown in Fig. 2, narrow and sharp peaks can be observed in an pore size range of ca. 2–3 nm for the samples Ni-MCM-41 (80) and Ni-MCM-41 (50), and the intensity of the peak also is strong as compared with that of the sample Ni-MCM-41 (10), indicating that the two samples have uniform pore size distribution as well. Additionally, as the nickel content in the sample increased, the intensity of the pore size distribution peak became weak, which reflects that the increase of nickel ions incorporated into the silica framework of MCM-41 mesoporous molecular sieve caused the partiel distortion of the mesoporous framework, resulting in the irregular pore size distribution and the poor mesoporous ordering. From Table 1, we can conclude that the specific surface area and pore volume of the resulting samples gradually decreased as the nickel content increased, and the pore size is in the range of 2.5–2.9 nm. Combined with the results of XRD, it is reasonable to conclude that the mesoporous ordering of the sample Ni-MCM-41 synthesized by the microwave irradiation method gradually decreased with the increase of the nickel content incorporated into the mesoporous framework. Fig. 3 presents the FT-IR spectra of the synthesized Ni-MCM-41 (50) sample before and after calcination at 813 K in air for 6 h. As shown in Fig. 3, the band at 3500 cm−1 is the characteristic band of the water adsorbed on the sample surface. The bands at 1620–1640 cm−1 are aroused by the flexion vibration of the OH bond [24]. The band at 1080 cm−1 is from the asymmetric extension vibration of Si-O-Si. The band about 810 cm−1 is due to the corresponding symmetric vibration of Si-O-Si bond, while the band at 460 cm−1 is assigned to rocking vibration of the Si-O-Si bond. The bands at 2921, 2850 and 1480 cm−1 are the characteristic bands of the surfactant alkyl chains. After the sample Ni-MCM-41 (50) was calcined at 813 K in air for 6 h, the bands at 2921, 2850 and 1480 cm−1 disappeared, certifying that the template had been effectively removed. The TEM images of the samples Ni-MCM-41 (80) and Ni-MCM-41 (50) are shown in Fig. 4. It is observed that the two samples exhibited the hexagonal arrays structure, indicating that the two samples synthesized under microwave irradiation conditions process the mesoporous framework. However, the mesoporous ordering of the sample Ni-MCM-41 (50) is poor as compared with that of the sample Ni-MCM-41 (80). Additionally, it can also be observed that there are not the particles and/or clusters containing nickel species on the surface of the two samples in Fig. 4. Furthermore, the acid site distribution and acid amounts of Ni-MCM-41 synthesized under microwave irradiation condition possess were determined using TPD of pyridine and the data are collected in Table 2. Weak (423 and 633 K), moderate (633–743 K) and strong (> 743 K) acid sites are found in all samples. The weak acid sites are attributed to surface hydroxyl groups and the medium and the strong acid sites originate probably from the incorporation of nickel atoms into the MCM-41 walls. It is interesting to note that the number of weak acid sites decreases with decreasing Si/Ni ratio. However, the amount of medium and strong acid sites decreases with increasing Si/Ni ratio. It should be noted that the total number of acid sites (medium and strong acid sites) of Ni-MCM-41 (10) prepared by M-H is higher than that of Ni-MCM-41 (50) and Ni-MCM-41 (80).

X-ray diffraction (XRD) patterns of Ni-MCM-41 materials in the domain of 1–10° (2θ) prepared by microwave-hydrothermal (M-H) process. A Ni-MCM-41 (80). B. Ni-MCM-41 (50). C. Ni-MCM-41 (10).
Physicochemical properties of different Ni-MCM-41 microwave-hydrothermal (M-H) samples.
Sample | Chemical analysis | SBET (m2.g-1) | Pore volume (cm3.g-1) | Pore diameter (nm) | |
Si/Ni (gel) | Si/Ni | ||||
Ni-MCM-41 | 10 | 9.6 | 689 | 0.66 | 3.0 |
Ni-MCM-41 | 50 | 49.3 | 938 | 0.88 | 2.8 |
Ni-MCM-41 | 80 | 78.9 | 1123 | 0.98 | 2.6 |
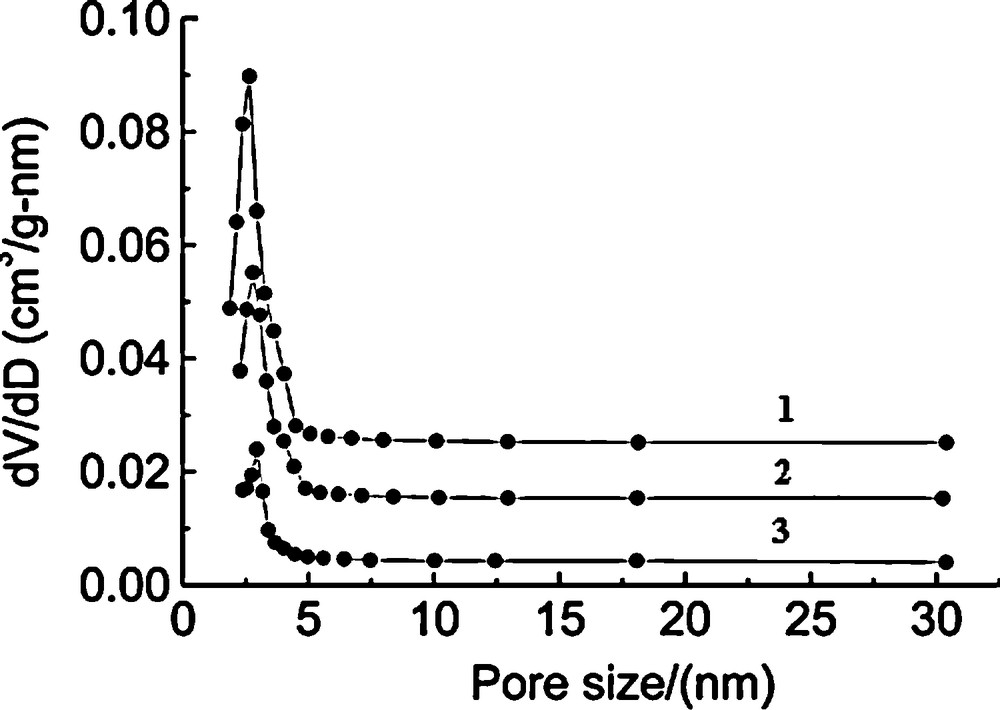
Pore size distribution curves of the Ni-MCM-41 materials prepared by microwave-hydrothermal (M-H) process. A. Ni–MCM-41 (80). B. Ni–MCM-41 (50). C. Ni–MCM-41 (10).
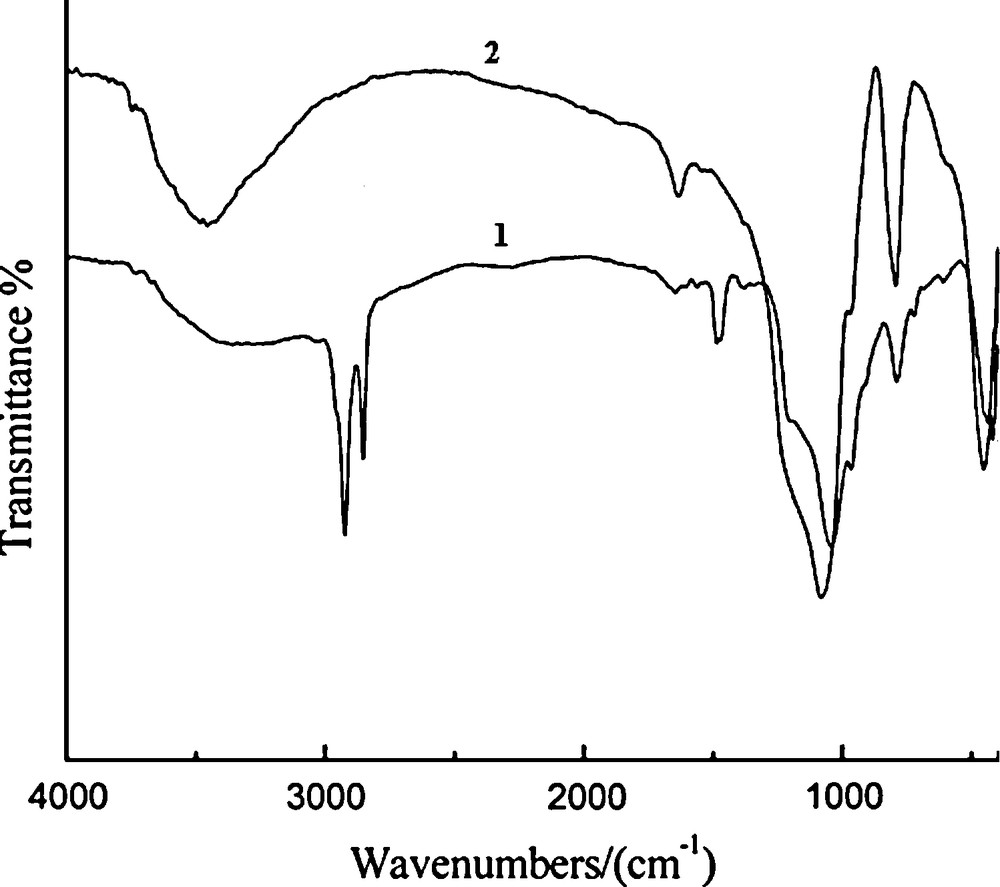
FT-IR spectra of the Ni-MCM-41 (50) material prepared by microwave-hydrothermal (M-H) process. A. Before calcination. B. After calcinations.

Transmission electron microscopy (TEM) images of the Ni-MCM-41 (80) and Ni-MCM-41 (50) materials prepared by microwave-hydrothermal (M-H) process.
Density and strength of acid sites of Ni-MCM-41 microwave-hydrothermal (M-H) catalysts with different Si/Ni ratios (Si/Ni = 80, 50, 10).
Sample | Acid sites (mmol/g) | |||
Weak (423–633 K) | Medium (633–743) | Strong (> 743) | Total (medium and strong acid sites) | |
Ni-MCM-41 (10) | 0.539 | 0.191 | 0.224 | 0.415 |
Ni-MCM-41 (50) | 0.601 | 0.123 | 0.179 | 0.302 |
Ni-MCM-41 (80) | 0.748 | 0.107 | 0.145 | 0.252 |
3.2 Catalytic activity
3.2.1 Catalytic performances of Ni-MCM-41(microwave-hydrothermal) materials with different Si/Ni ratio in the acetylation of 1,2-dimethoxybenzene with acetic anhydride
The acetylation of 1,2-dimethoxybenzene has been carried out over Ni-MCM-41 (M-H) materials with different nickel contents (Si/Ni = 80, 50, and 10) using acetic anhydride as an acylating agent. The acetylation of 1,2-dimethoxybenzene with acetic anhydride generates acetic acid in the products, which resulted from the acetic anhydride utilization. Only one product is obtained which is 3,4-dimethoxyacetophenone, due to the fact that both the ortho positions of 1,2-dimethoxybenzene are sterically crowded for the electrophilic reaction, acetylation preferentially occurs at the fourth position which is the most favored and para to one of the methoxy substituents. No products other than 3,4-dimethoxyacetophenone were found in the product mixture. The conversion and the selectivity in the acetylation of 1,2-dimethoxybenzene over Ni-MCM-41 (M-H) catalysts with different Si/Ni ratio (Si/Ni = 80, 50, and 10) at a reaction temperature of 333 K and under the standard reaction conditions (stoichiometric ratio 1,2DMB/AC = 5, catalyst weight = 0.1 g and a reaction time of 2 h) are given in Table 3. The activity of the catalysts is in the following order: Ni-MCM-41 (M-H) (10) > Ni-MCM-41 (M-H) (50) > Ni-MCM-41 (80). In fact, it is found that Ni-MCM-41 (10) is the mainly efficient catalyst, showing much higher conversion of acetic anhydride as compared with that of other catalysts studied. The Ni-MCM-41 (10) catalyst registers the complete acetic anhydride conversion and 100% selectivity to 3,4-dimethoxyacetophenone after 95 min of reaction. The very higher activity of Ni-MCM-41 (10) than other Ni-MCM-41 (M-H) catalysts may be mostly attributed to the fact that the catalyst exhibits higher acidity than other Ni-MCM-41 (M-H) catalysts (Table 2). On the other hand, the lower activity of Ni-MCM-41(M-H) (80) which has the highest surface area and larger pore volume is mainly due the presence of a lower number of active sites on the porous surface. Eelsewhere, it was interesting to compare the solids with zeolites catalysts investigated earlier under similar conditions. The activity of the catalysts is in the following order: Ni-MCM-41(M-H) (10) > BEA, > MFI. Indeed, it must be noted that although the acidity of the zeolites catalysts is much higher than that of the Ni-MCM-41 (M-H) (10), the catalytic activity of the latter is superior to that of zeolites catalysts. Thus, it has to be concluded that the accessibility of the active sites by the reactant molecules is higher in Ni-MCM-41 (M-H) (10) than that of the zeolite catalysts, which is supported by their enormous specific surface area and the specific pore volume, and large pore diameter with well-ordered pore structure. These exceptional textural characteristics of the Ni-MCM-41 (M-H) (10) are accountable for its higher catalytic activity and the results further confirm that the catalysts with high surface area, and large pore diameter is highly important for acetylation of substituted aromatic compounds. As the Ni-MCM-41 (M-H) (10) catalyst was found to be highly active, we opt to choose this catalyst for investigating the effect of other reaction parameters such as: the reaction temperature, the stoichiometric ratio 1,2DMB/AC, weight of the catalysts and the recycling of the catalysts on the conversion of acetic anhydride and the selectivity in the acetylation of 1,2-dimethoxybenzene.
The conversion and the selectivity of tert-butylation of anisole over Ni-MCM-41 microwave-hydrothermal (M-H) catalysts with different Si/Ni ratio (Si/Ni = 80, 50, and 10) at a reaction temperature of 333 K, stoichiometric ratio 1,2DMB/AC = 5, catalyst weight = 0.1 g and a reaction time of 2 h.
Sample | Acetic anhydride conversion (%) | Selectivity to 3,4-dimethoxyacetophenone (%) |
Ni-MCM-41 (10) | 100.0 | 100.0 |
Ni-MCM-41(50) | 89.5 | 100.0 |
Ni-MCM-41 (80) | 67.2 | 100.0 |
3.2.2 The effect of reaction temperature in the acetylation of 1,2-dimethoxybenzene with acetic anhydride
The effect of reaction temperature on the conversion of acetic anhydride in the acetylation of 1,2-dimethoxybenzene over Ni-MCM-41 (M-H) (10) at different reaction time is shown in Table 4. As expected, an increase in the reaction temperature had a favorable effect on the conversion of the acetic anhydride. The conversion of acetic anhydride increases with increasing the reaction temperature. However, the selectivity to 3,4-dimethoxyacetophenone was not changed with increasing the reaction temperature. The selectivity of the product was almost 100% for all the reaction temperature studied. It must be noted that the rate of the reaction at lower temperature is rather slow. On the other hand, at the reaction temperature more than 333 K, the rate of the reaction is very fast. The apparent rate constant of the reaction at different reaction temperature was calculated using the pseudo-first order rate law:
Catalytic activities of Ni-MCM-41 microwave-hydrothermal (M-H) (10) at different temperatures: 313, 333 and 353 K, stoichiometric ratio 1,2DMB/AC = 5, catalyst weight = 0.1 g.
Temperature (K) | Timea (min) | Selectivity to 3,4-dimethoxyacetophenone (%) | Apparent rate constant ka (× 103min-1) |
313 | 209.0 | 100.0 | 13.0 |
333 | 96.2 | 100.0 | 42.1 |
353 | 42.3 | 100.0 | 96.3 |
a Time required for complete conversion of acetic anhydride.

The plot of log [1/1–x] as a function of reaction time of Ni-MCM-41 microwave-hydrothermal (M-H) (10) catalyst at different temperatures: () 313, () 333 and () 353 K, stoichiometric ratio 1,2DMB/AC = 5, catalyst weight = 0.1 g.
3.2.3 The effect of the stoichiometric ratio 1,2DMB/AC on the acetylation of 1,2-dimethoxybenzene with acetic anhydride
The effect of the stoichiometric ratio 1,2DMB/AC on the conversion of acetic anhydride was studied over Ni-MCM-41 (M-H) (10) at a reaction temperature of 333 K as a function of reaction time and the results are shown in Table 5. When the 1,2DMB/AC ratio was varied, the conversion of acetic anhydride was significantly affected. The conversion of acetic anhydride is increased while increasing the 1,2DMB/AC from 1 to 10 at a reaction temperature of 333 K, while the selectivity to 3,4-dimethoxyacetophenone is almost constant in all the cases. It is shortened that the raise of the 1,2DMB/AC ratio may support the adsorption of more amount of 1,2-dimethoxybenzene on the catalyst surface compared to acetic anhydride molecules.
The conversion and the selectivity in the acetylation of 1,2-dimethoxybenzene over Ni-MCM-41 microwave-hydrothermal (M-H) (10) catalyst with different stoichiometric ratio 1,2DMB/AC at a reaction temperature of 333 K, catalyst weight = 0.1 g.
Stoichiometric ratio 1,2DMB/AC | Timea (min) | Selectivity to 3,4-dimethoxyacetophenone (%) | Apparent rate constant ka (× 103min-1) |
1 | 262.4 | 100.0 | 09.8 |
5 | 96.2 | 100.0 | 42.1 |
10 | 65.4 | 100.0 | 71.5 |
a Time required for complete conversion of acetic anhydride.
3.2.4 The effect of the weight of the catalysts in the acetylation of 1,2-dimethoxybenzene with acetic anhydride
The weight of the catalysts was varied to study its influence on the conversion of acetic anhydride in the acetylation of 1,2-dimethoxybenzene over Ni-MCM-41 (M-H) (10). The weight of the catalysts in the reaction mixture was changed from 0.02 to 0.2 g. Table 6 shows the influence of the weight of the Ni-MCM-41 (M-H) (10) catalyst on the conversion of the acetic anhydride in the acetylation of 1,2-dimethoxybenzene. The concentration of the catalyst in the reaction mixture has a huge impact on the conversion of acetic anhydride. The conversion of the acetic anhydride increases with growing the weight of the catalyst from 0.02 to 0.2 g at the reaction temperature of 333 K and the stoichiometric ratio 1,2DMB/AC = 5, whilst maintaining 100% selectivity to 3,4-dimethoxyacetophenone. This could be mostly due to the fact that the accessibility of the surface acidic sites is larger at higher catalyst concentration, which supports the increase in the conversion of acetic anhydride.
The conversion and the selectivity in the acetylation of 1,2-dimethoxybenzene over Ni-MCM-41 microwave-hydrothermal (M-H) (10) catalyst with different weight of the catalyst at a reaction temperature of 333 K, stoichiometric ratio 1,2DMB/AC = 5.
Weight of the catalyst (g) | Timea (min) | Selectivity to 3,4-dimethoxyacetophenone (%) | Apparent rate constant ka (× 103min-1) |
0.02 | 279.5 | 100.0 | 9.0 |
0.1 | 96.2 | 100.0 | 42.1 |
0.2 | 59.5 | 100.0 | 80.0 |
a Time required for complete conversion of acetic anhydride.
3.2.5 Recycling of the catalysts
The recyclability has been done over Ni-MCM-41 (M-H) (10) in the acetylation of 1,2-dimethoxybenzene at a reaction temperature of 333 K, a reaction time of 2 h, and a 1,2DMB/AC ratio of 5. After the reaction, the catalyst was filtered, washed several times with acetone and dried in an oven at 393 K. Then, the catalyst was activated at 823 K for 6 h under oxygen atmosphere. The recyclability experiments were carried out two times and the procedure for the activation was repeated every time after the reaction. The results on the recyclability are given in Table 7. The catalyst shows approximately similar conversion after two cycles, without any transform in the selectivity of the products. This shows that the catalyst is very stable under the specified reaction conditions, and be able to be recyclable.
Effect of recycling of the catalyst in the acetylation of 1,2-dimethoxybenzene over Ni-MCM-41 microwave-hydrothermal (M-H) (10) at a reaction temperature of 333 K, stoichiometric ratio 1,2DMB/AC = 5, catalyst weight = 0.1 g.
Catalyst | Timea (min) | Selectivity to 3,4-dimethoxyacetophenone (%) | Apparent rate constant ka (× 103min-1) |
Fresh | 96.2 | 100.0 | 42.1 |
First reuse | 98.3 | 100.0 | 39.4 |
Second reuse | 100.3 | 100.0 | 38.1 |
a Time required for complete conversion of acetic anhydride.
3.2.6 Applications to other aromatic compounds
The acetylation of other substrates with acetic anhydride was accomplished using the Ni-MCM-41 (10) under the optimized reaction conditions. The details of the reaction conditions and the results are presented in Table 8. The catalyst shows an amazing performance in the acetylation of aromatics used in the reaction. In the case of acetylation of méthoxybenzène (anisole), it was observed that the time required for complete conversion of acetic anhydride over Ni-MCM-41 (M-H) (10) catalyst is 37 min with 98.5% selectivity to (p) 4-methoxyacetophenone, while the rest is (o) 2-methoxyacetophenone. The data on the acetylation of 2-methoxynaphthalene with acetic anhydride under nitrobenzene as solvent are also presented in Table 8. In fact, the selectivity to 1-acetyl-2-methoxynaphthalene and 6-acetyl-2-methoxynaphthalene of 98.4% and 1.6%, respectively, was observed. The formation of the sterically hindered but kinetically favored product, 1-acetyl-2-methoxynaphthalene has been also watched for the zeolite catalysts with more external surface area and the proton exchanged MCM-41 catalyst at low reaction temperature because the position 1 is considered to be the most activated one [25,26]. Therefore, we consider the preferential formation of 1-acetyl-2-methoxynaphthalene in the Ni-MCM-41 (M-H) catalysts system could be mostly due the fact that the materials possess high surface area and pore volume, large pore diameter which support the formation of the kinetically favored 1-acetyl-2-methoxynaphthalene quite than thermodynamically favored 6-acetyl-2-methoxynaphthalene.
Acetylation of different aromatic substrates over Ni-MCM-41 microwave-hydrothermal (M-H) (10) catalyst at a reaction temperature of 333 K.
Substituent | Timea (min) | Reaction products (Selectivity [%]) |
1,2-dimethoxybenzene | 96.2 | 3,4-dimethoxyacetophenone (100%) |
Methoxybenzene (anisole) | 37 | p-methoxyacetophenone (98.5%) o-methoxyacetophenone (1.5%) |
2-methoxy naphthalene | 46 | 1-acetyl-2-methoxynaphthalene (98.4%) 6-acetyl-2-methoxynaphthalene (1.6%) |
a Time required for complete conversion of acetic anhydride.
4 Conclusion
Ordered hexagonal Ni-MCM-41 mesoporous molecular sieves with high specific surface area were successfully synthesized via the microwave irradiation method. After calcination, the template was effectively removed. The Si/Ni molar ratio is a key factor influencing the textural properties and structural regularity of Ni-MCM-41 mesoporous molecular sieves. High nickel content is unfavorable to the formation of the Ni-MCM-41 with highly ordered mesoporous structure. These samples have many medium acid sites. The study of the liquid phase of acetylation of 1,2-dimethoxybenzene and other two aromatic compounds with acetic anhydride using Ni-MCM-41 solids shows that these catalysts explain remarkable activities and can also be reused in this reaction several times.