1 Introduction
The stabilisation of polymeric materials is of paramount importance, first of all, from the point of view of the dynamically developing polymer industry. The ageing of polymeric materials due to their oxidation is widespread and poses a serious problem because the absorption of even a low quantity of oxygen can cause irreversible and damaging changes in their physical and mechanical properties. The degradation, ageing and stabilisation of polymers constitute a considerable area of interest in industry and science, and the aim is to obtain new, stable polymeric materials [1–10].
During their use, polymeric products are exposed to the action of external factors. The structure and properties of materials change as a function of time, but these changes depend on both the material structure and the type of environmental effects. The action of external factors on polymers results in the release of low-molecular compounds, such as initiators, solvents, stabilisers and the products of their degradation [11–18].
In recent years, we have witnessed very small changes in the application of various stabilisers. According to the available literature, phosphate derivatives are used as anti-ageing substances in polymers, while the most popular are cyclic amines with steric hindrance (HALS derivatives). Most of these compounds are carcinogenic or corrosive. Synthetic phenols are being increasingly used as antioxidants in food and polymers. Flavonoids synthesised by plants belong to such a group of phenol derivatives. Currently, several thousands of their derivatives are known. Most of them show a very high activity in the capture and slowing down of oxidation processes. Natural anti-ageing substances can change elastomeric materials into environmentally friendly goods. In this paper, we present the use of morin hydrate, one of the most popular flavonoids, as a natural anti-ageing substance for ethylene–octene rubber. Polyolefins [19–26] are widely used for various purposes, so the stabilisation of this type of material by incorporating ecological additives is now the subject of many studies.
2 Materials and methods
2.1 Reagents
The material of interest in this study was ethylene–octene rubber (Engage). Dicumyl peroxide, DCP (from Fluka), was used as a cross-linking agent, 1,3,5-triallyl-1,3,5-triazine-2,4,6(1H,3H,5H)-trione (Sigma–Aldrich Chemie GmbH) as a co-agent of cross-linking and hexadecyltrimethylammonium bromide, CTAB (Sigma Aldrich Chemie GmbH), as a dispersing agent. Aerosil 380 silica (from Degussa) was used as a filler.
The anti-ageing substances used included the following flavonoid derivatives: morin hydrates (Fluka 98%, 90%).
The compositions of the elastomer blends produced are given in Table 1.
Composition of Engage elastomer blends containing morin hydrate.
Composition | M1 (phr) | M2 (phr) |
Engage | 100 | 100 |
DCP | 2.00 | 2.00 |
CTAB | 2.00 | 2.00 |
1,3,5-Triallyl-1,3,5-triazine-2,4,6(1H,3H,5H)-trione | 0.5 | 0.5 |
A380 | 30 | 30 |
Morin hydrate | 1.5 |
2.2 Measurement methods
Rubber blends were prepared using a laboratory mixing mill with rolls of the following dimensions: length L = 330 mm, diameter D = 140 mm. The speed of rotation of the front roll was Vp = 20 rpm, the friction ratio was 1.1 and the average temperature of the rolls was approximately 40 °C.
The vulcanisation of rubber blends was carried out with the use of steel vulcanisation moulds placed between the shelves of an electrically heated hydraulic press. Teflon films were used as spacers to prevent the adherence of the blends to the press plates. Samples were vulcanised at a temperature of 160 °C under a pressure of 15 MPa for 30 min.
The density of cross-links in the vulcanisates network was determined by the method of equilibrium swelling according to standard PN-74/C-04236. The vulcanisates were subjected to equilibrium swelling in toluene for 48 h at room temperature. The swollen samples were then weighed on a torsion balance and dried in a dryer at a temperature of 60 °C to a constant weight, and after 48 h, they were reweighed. The cross-linking density was determined based on Flory–Rehner's equation [18]:
(1) |
The tensile strength of the vulcanisates was tested according to standard PN-ISO 37:1998 using a ZWICK tester, model 1435, for dumbbell w-3.
Ageing characteristics were determined according to standard PN-82/C-04216. Samples were exposed to air at elevated temperature (383 K) for 10 days in a dryer with thermo-circulation. UV ageing was performed using a UV 2000 apparatus from Atlas. The measurement lasted 288 h and consisted of two alternately repeating segments with the following parameters: daily segment (radiation intensity 0.7 W/m2, temperature 60 °C, duration 8 h), night segment (no UV radiation, temperature 50 °C, duration 4 h). Climatic ageing was carried out using a weatherometer (Atlas; Ci4000). The test was based on two variable segments simulating day and night conditions, and the samples were subjected to two different cycles: daily cycle (radiation intensity 0.4 W/m2, temperature 60 °C, duration 240 min, humidity 80%, rain water on), night cycle (no radiation, temperature 50 °C, humidity 60%, duration 120 min).
The ageing coefficient was calculated according to the relationship K = [TS′ × EB′]/[TS × EB], where TS indicates tensile strength, EB indicates elongation at break and TS′ and EB′ are the corresponding values after ageing.
The dispersion degree of the fillers in the elastomeric matrix was assessed from images obtained using a LEO 1530 scanning electron microscope (SEM). The samples tested consisted of vulcanisate fractures in liquid nitrogen dusted with carbon.
The colour of the vulcanisates obtained was measured using a CM-3600d spectrophotometer (Konica Minolta). The radiation source consisted of four impulse xenon tubes. The spectral range of the apparatus was 360–740 nm, where the change in colour dE*ab was calculated as follows:
(2) |
The CIE-LAB color scale is an approximately uniform color scale. In a uniform color scale, the differences between points plotted in the color space correspond to visual differences between the colors plotted. The CIE-LAB color space is organized in a cube form. The L* axis runs from top to bottom. The maximum for L* is 100, which represents a perfect reflecting diffuser. The minimum for L* is zero, which represents black. The a* and b* axes have no specific numerical limits. Positive a* is red. Negative a* is green. Positive b* is yellow. Negative b* is blue. A diagram representing the CIE-LAB color space is displayed below (Fig. 1).
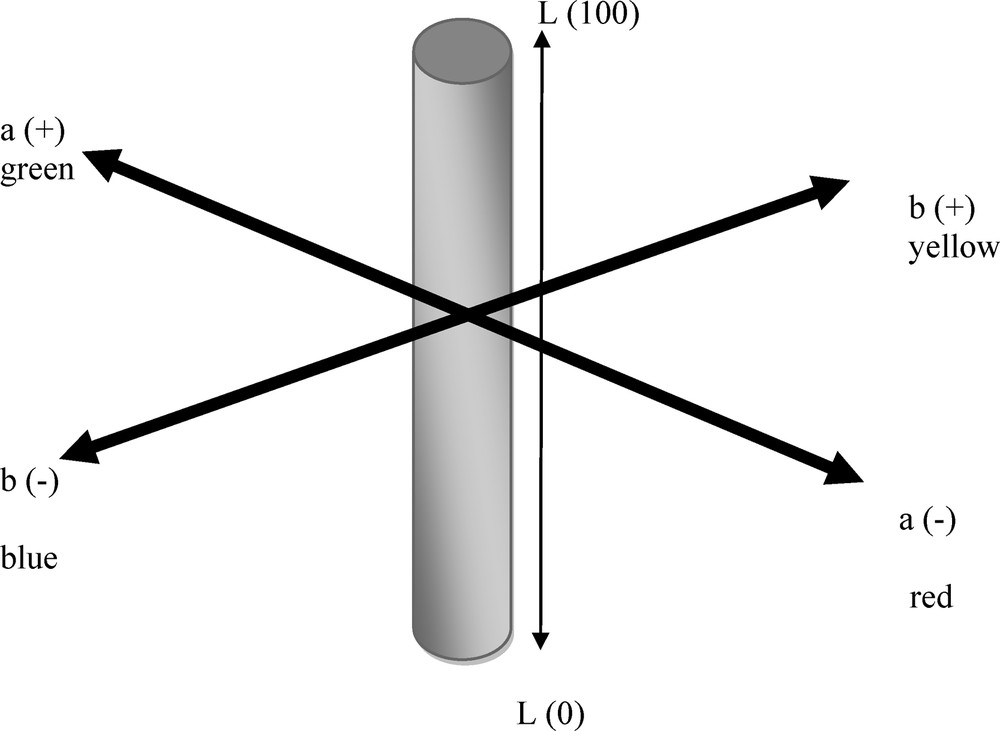
CIE-Lab color space coordinates.
The oxygen induction time (OIT) test was performed on a Mettler Toledo DSC instrument. Samples with a mass of 4 mg were heated from room temperature to the test temperature, 220 °C, at a rate of 20 °C/min under a nitrogen atmosphere. After 5 min at 220 °C, the gas was switched from nitrogen to air at a flow rate of 60 mL/min. When all antioxidants are consumed, the sample starts to oxidise, producing a deviation in the baseline. The OIT was measured as the time between the switch to airflow and the intersection with a tangent from the maximum derivative after oxidation has started. Two analyses of each sample were performed to ensure the accuracy of the results.
3 Results and discussion
3.1 Effect of morin hydrate on the cross-linking density of Engage vulcanisates
The standard vulcanisate of Engage shows a cross-link density of 3.64 × 10−5 mol/cm3. Under the influence of thermal ageing, the network node concentration is increased by 0.44 mol/cm3. During UV ageing, the value of ve changed slightly compared to the initial value of ve before ageing. On the other hand, the effect of climate conditions resulted in considerable changes in the network node concentration of the Engage sample already after 96 h. After 288 h of climatic ageing, the cross-link density decreased by 1.44 mol/cm3. However, UV radiation caused no clear changes in the cross-link density of the Engage rubber without the antioxidant (Table 2). The addition of morin hydrate to the Engage rubber decreased the network node concentration by 1.49 mol/cm3. Most likely, some peroxide radicals of the cross-linker reacted with the antioxidant. The greatest change in the network node concentration was observed under the influence of thermal and UV ageing. In these cases, changes in ve were visible already after 48 h of exposure to degrading factors. The smallest changes in the cross-link density of the vulcanisate of ethylene–octene rubber containing morin hydrate were observed after climatic ageing (Table 3).
Effect of ageing on the cross-linking density of Engage vulcanizates (reference sample).
Time of ageing [h] | ve(z) × 10−5 [mol/cm3] after thermal oxidation | ve(z) × 10−5 [mol/cm3] after weathering | ve(z) × 10−5 [mol/cm3] after UV ageing |
0 | 3.64 | ||
48 | 4.08 | 3.03 | 4.05 |
96 | 4.09 | 2.12 | 4.73 |
144 | 4.06 | 3.20 | 4.63 |
192 | 4.00 | 2.77 | 4.55 |
240 | 3.80 | 2.39 | 4.23 |
288 | 3.64 | 2.20 | 3.35 |
Effect of morin hydrate on the cross-linking density of Engage vulcanizates.
Time of ageing [h] | ve × 10−5 [mol/cm3] after thermal oxidation | ve × 10−5 [mol/cm3] after weathering | ve × 10−5 [mol/cm3] after UV ageing |
0 (before ageing) | 2.15 | ||
48 | 1.34 | 3.03 | 1.31 |
96 | 1.31 | 2.12 | 1.31 |
144 | 1.36 | 3.20 | 1.37 |
192 | 1.37 | 2.77 | 1.27 |
240 | 1.32 | 2.39 | 1.28 |
288 | 1.36 | 2.56 | 1.26 |
3.2 Effect of morin hydrate on the stabilisation of Engage vulcanisates after ageing
The standard vulcanisate of ethylene–octene rubber is characterised by a tensile strength (TS) of 26.8 MPa and an elongation at break of 399%.
The exposure of the vulcanisate to UV radiation with a wavelength of 340 nm resulted in a great deterioration in the material's mechanical properties: after 96 h, its TS had already decreased by 19.2 MPa. After 288 h of UV ageing, the standard vulcanisate of Engage showed a tensile strength of 4.17 MPa and an elongation at break of 156%. The calculated UV ageing factors are much lower than 1, which confirms the considerable degree of degradation of this sample. The thermo-oxidative ageing of the standard sample resulted in a slightly smaller decrease in the sample's TS than that caused by UV ageing. After 48 h of this ageing, TS decreased by 13.3 MPa and elongation by 103%. However, already after 192 h of exposure to an elevated temperature (100 °C), the standard sample showed such an extent of degradation that it has made it impossible to test its mechanical properties. Undoubtedly, the standard vulcanisate of Engage was degraded to the lowest extent under simulated climatic conditions. The climatic ageing factors for this sample after ageing for 144 h were close to unity. Only after 192 h of exposure to climatic conditions could one observe a progress in the vulcanisate degradation (K = 0.69) (Table 4).
Mechanical properties of the Engage vulcanizates subjected to ageing.
Time of ageing [h] | TS [MPa] | Eb [%] | K |
UV ageing | KUV | ||
0 (before ageing) | 26.8 | 399 | - |
48 | 7.68 | 190 | 0.14 |
96 | 10.5 | 217 | 0.21 |
144 | 8.70 | 198 | 0.16 |
192 | 7.11 | 194 | 0.13 |
240 | 4.91 | 149 | 0.07 |
288 | 4.17 | 156 | 0.06 |
Thermal ageing | Ktherm. | ||
48 | 13.5 | 296 | 0.37 |
96 | 12.0 | 302 | 0.34 |
144 | 9.5 | 319 | 0.28 |
192 | 9.3 | 165 | 0.14 |
240 | Degradation | Degradation | |
288 | |||
Weathering | Kweathering | ||
48 | 19.3 | 556 | 1.00 |
96 | 18.7 | 704 | 1.23 |
144 | 16.9 | 686 | 1.08 |
192 | 14.4 | 510 | 0.69 |
240 | 12.6 | 494 | 0.58 |
288 | 7.48 | 453 | 0.32 |
To assess the susceptibility of a material to ageing, sometimes it is necessary to compare the sample's colour before and after ageing. The colour of the standard vulcanisate changed to the greatest extent under the influence of UV radiation and under climatic conditions, i.e., in the presence of solar radiation. The smallest colour change was observed under the influence of elevated temperature, as confirmed by the lowest values of the product differential of parameters a and b, i.e., coefficients dE*ab presented in Fig. 2.

Colour difference (dE*ab) of Enagage vulcanizates after ageing.
The addition of morin hydrate to the ethylene–octene rubber slightly affected the material's mechanical properties. The tensile strength of the vulcanisate containing morin hydrate was 1.7 MPa lower and its elongation at break 43% lower compared to those of the reference sample.
The effect of UV radiation on the vulcanisate of Engage containing the antioxidant resulted in the minor degradation of the vulcanisate compared to that of the reference sample. After 40 h of UV ageing, TS was reduced by only 3.8 MPa. The UV ageing factors for this sample were close to unity, even up to 192 h of UV irradiation, and after 288 h the ageing factor was equal to 0.72, which indicates a slight degradation of this sample. Therefore, one may conclude that morin hydrate is a very good UV absorber for elastomers. The thermo-oxidative ageing of the Engage vulcanisate, performed for 144 h in the first stage, resulted in an increase in the material's elongation at break. Consequently, the ageing factors of that sample were above unity. After 192 h of exposure to elevated temperature, only a slight increase in degradation was observed (coefficient K = 0.90). After 288 h of thermal ageing, TS was reduced by only 5.6 MPa. Therefore, morin hydrate very well protected the vulcanisates of Engage against thermo-oxidative destruction. After 192 h of climatic ageing, the ageing factor was close to unity, indicating slight changes in mechanical properties. After 28 h of climatic ageing, it was observed that the ageing factor was equal to 0.65 and that of the reference vulcanisates amounted to 0.32 (Table 5). Hence, one may state with conviction that morin hydrate offers very good protection of the vulcanisates of Engage against the synergic action of climatic conditions.
Mechanical properties of the Engage vulcanizates containing morin hydrate subjected to ageing.
Time of ageing [h] | TS [MPa] | Eb [%] | K |
UV ageing | KUV | ||
0 (before ageing) | 25.1 | 442 | – |
48 | 21.3 | 508 | 0.98 |
96 | 18.6 | 483 | 0.81 |
144 | 18.4 | 468 | 0.78 |
192 | 18.5 | 501 | 0.84 |
240 | 16.9 | 466 | 0.71 |
288 | 17.5 | 456 | 0.72 |
Thermal ageing | Ktherm. | ||
48 | 23.2 | 616 | 1.29 |
96 | 23.6 | 663 | 1.41 |
144 | 23.1 | 566 | 1.18 |
192 | 22.3 | 447 | 0.90 |
240 | 22.6 | 458 | 0.93 |
288 | 19.5 | 425 | 0.75 |
Weathering | Kweathering | ||
48 | 24.6 | 415 | 0.92 |
96 | 19.1 | 555 | 0.96 |
144 | 24.0 | 429 | 0.93 |
192 | 23.8 | 499 | 1.07 |
240 | 25.0 | 397 | 0.89 |
288 | 20.6 | 350 | 0.65 |
The oxygen induction time test was used to measure the level of effective morin hydrate in Engage vulcanisate. Oxidative induction time (OIT) measurements provide a valuable characterization parameter associated with the long-term stabilities of polyolefin materials. The OIT is the same as the extrapolated onset temperature of the exothermal DSC effect that occurs. In isothermal OIT tests, the materials to be investigated are first heated under a protective gas, then held at a constant temperature for several minutes to establish equilibrium and subsequently exposed to an atmosphere of air. The time span from the first contact with oxygen until the beginning of oxidation is called the oxidation inductive time.
High OIT values indicate high resistance to oxidation. The oxidation induction time of the reference vulcanisate (with no antioxidant) was 0.53 min, while the addition of morin hydrate increased the OIT of the Engage vulcanisates by as much as 4 min (Fig. 3).

Oxygen induction time (OIT) values of Engage vulcanizate containing morin hydrate.
It should also be mentioned that flavonoids are natural pigments; hence, their addition to polymers considerably contributes to the change in the colour of the final polymeric product. Table 4 shows the parameters L, a and b of the standard Engage vulcanisate and of that containing morin hydrate. The Engage vulcanisate sample containing morin hydrate is darker than the reference sample, as indicated by the former lower value of parameter L. Hydroxymorin shifted the colour of the Engage vulcanisate towards red, as indicated by the increase in the value of parameter a by 27.73, and towards yellow, as indicated by the change in parameter b by 16.84 (Table 6).
Influence of morin hydrate on the colour (parameter L,a,b) of Engage vulcanizates.
L | a | b | dL | da | db | dE*ab | |
Engage | 82.33 | 0.24 | 9.72 | – | – | – | – |
Engage/morin hydrate | 38.47 | 27.97 | 26.56 | 43.86 | 27.73 | 16.56 | 16.56 |
The colour change of the morin hydrate-containing vulcanisate became clearly apparent under the influence of temperature and UV radiation (Fig. 4).

Colour difference (dE*ab) of Engage vulcanizates containing morin hydrate after ageing.
For a better understanding of morin hydrate morphology were studied scanning electron microscope. While automated SEM analysis provides quantified information about the chemistry, the size, and the amount of phases and particles present, morphological analysis provides information about the physical relationships between the size and the crystallinity of the phases present. It is an important phenomenon that the morphology varied with the concentration of antioxidant. The images of morin hydrate (Fig. 5) and morin hydrate-containing composites (Fig. 6) obtained by scanning electron microscopy (SEM) indicate that this flavonoid has a crystalline structure. Fig. 5 clearly shows crystals of morin hydrate, which are also visible in the vulcanisate of Engage containing this antioxidant. Unfortunately, this crystalline structure can adversely affect the dispersion of the antioxidant in the elastomer, but we plan to solve this problem by incorporating flavonoids into the elastomeric materials via impregnation from solution.
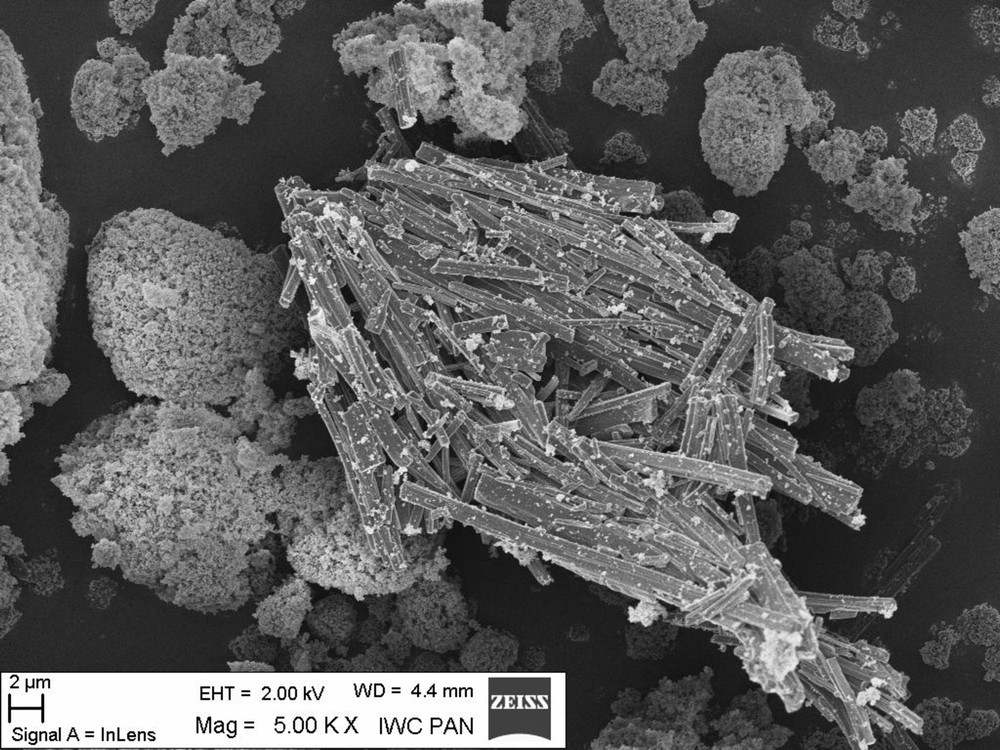
Morphology of morin hydrate measured by the method of scanning electron microscopy (SEM).

Morphology of Enagage vulcanizate with morin hydrate measured by the method of scanning electron microscopy (SEM).
To summarise, we conclude that the natural antioxidant from the flavonoid group used for elastomeric materials very well fulfils the role of an anti-ageing substance. It protects against the negative effects of UV radiation and elevated temperature as well as the synergic effects of climatic conditions.
In addition to its antioxidant function, morin hydrate can play the role of a natural pigment, whose colour changes under the influence of specified environmental factors. Therefore, a polymeric product containing morin hydrate may be treated as both a smart and pro-ecological material.
4 Conclusions
Based on the test results obtained, we conclude that the natural derivative morin hydrate can be undoubtedly used as a natural anti-ageing additive for polymers. The addition of morin hydrate considerably improves the stabilisation of polymer. Morin hydrate has shown to be a good UV absorber and thermal stabiliser as well as a protecting agent against the climatic factors. Moreover, this natural pigment imparts colour to final polymeric materials. The colour imparted is sensitive to UV radiation; hence, such polymers assume the features of smart materials. Materials susceptible to colour change under the influence of specified factors may be used in certain applications, e.g., food packaging.
Acknowledgements
This study was supported by the Ministry of Science of Higher Education IP 2012 037072.