1 Introduction
Over the past two decades, the oxidation of sulfides to sulfoxides and sulfones gives beneficial starting chemical materials [1–5]. Sulfoxides are the major chemical intermediates to synthesize valuable chemicals, including medications [6,7] and antifungal agents [8,9], and also can play a role in the activation of enzymes. Numerous recent reports are available on the conversion of sulfides into sulfoxides using transition metal complexes [10–13], especially with Mo complexes [14–17]. The Mo(VI) complexes have been used intensively as catalysts for selective oxidation of organic compounds [18–20]. There are some key advantages for solvent-free reactions, such as significant contributions to protect the environment, health of people, high cost efficiency, and waste reduction [21]. According to previous reports, aqueous solution of hydrogen peroxide (30%) is one of the greenest oxidants, because it is cheap, nontoxic, and environmentally benign without waste products, so that water is the only residue [22–24]. A homogeneous catalyst recovering from a reaction mixture is often difficult and costs high, as well as is associated with additional wastes. Furthermore, insufficient chemical and thermal stability, the active metal leaching into the solvent, and catalyst recycling remain a scientific challenge [25]. Replacement of a homogeneous oxidation catalyst with environmental friendly heterogeneous catalyst may be promising address for such problems [26]. Accordingly, metal complex supporting has been the basic research subject in the catalytic fields [18,27–29]. A main idea for supporting of metal complexes is to anchor the metal complex onto a large surface area of inorganic materials, such as zeolite and metal oxide [30–36]. Nowadays, magnetite nanoparticles (NPs) have been recruited because of their unique properties, including the large surface area, low toxicity, separate-ability, and biocompatibility [37–43]. Magnetic separation renders the recycling of catalysts from the solution by external magnetic fields much easier than filtration and centrifugation. Following our previous review on catalytic activity of Schiff base complexes [19,27,30,44–46], herein we report the anchoring of novel cis-dioxomolybdenum(VI) macrocyclic Schiff base complex by a reaction of 1,4-bis(2-carboxyaldehyde phenoxy) butane, MoO2Cl2(DMF)2 and amino-modified magnetite NPs. The novel nanocatalyst (Fe3O4@Si(CH2)3–PBSB/MoO2) (PBSB: propylbromo Schiff base) was characterized using infrared (IR) spectroscopy, scanning electron microscope (SEM), transmission electron microscopy, diffuse reflectance spectra (DRS), vibrating sample magnetometry, energy-dispersive X-ray (EDX) spectroscopy, and X-ray powder diffraction (XRD) techniques and tested for methyl phenyl sulfide, diphenyl sulfide, benzyl phenyl sulfide, dipropyl sulfide, dibutyl sulfide, dimethyl sulfide, bis(4-hydroxyphenyl) sulfide, diallyl sulfide, and benzothiophene with H2O2 (30% aqueous) as oxidant. The reusability of Fe3O4@Si-APFSB-MoO2 (APFSB: aminopropyl phenoxybutane Schiff base) was also studied within the oxidation of methyl phenyl sulfide with H2O2 (30% aqueous) under solvent-free conditions for six times.
2 Experimental section
2.1 Materials and instruments
Methyl phenyl sulfide, diphenyl sulfide, benzyl phenyl sulfide, dipropyl sulfide, dibutyl sulfide, dimethyl sulfide, bis(4-hydroxyphenyl) sulfide, diallyl sulfide, benzothiophene, 1,4-dibromobutane, 2-hydroxybenzaldehyde, N,N′-dimethylformamide, ferrous chloride, ferric chloride, 3-aminopropyltrimethoxysilane (APTMS), and ammonia (25%[w/w]) were purchased from Merck Chemical Company. Proton nuclear magnetic resonance spectra were recorded using a Bruker NMR 400 (400 MHz) spectrophotometer in a CDCl3 solvent. CHNS analyses were performed using an Elemental Analyzer CHNSO-A PE 2400 series II system. Atomic absorption analysis was carried out on an Analytik Jena atomic absorption spectrometry. Analysis of the oxidation products was determined by gas chromatography (GC) using Agilent 7890 A with a capillary column and flame ionization detector. Column temperature was programmed between 180 and 200 °C with 2 °C/min rate. N2 was used as a carrier gas at a flow rate of 20 mL/min. IR spectra were obtained using a Fourier transform infrared (FT-IR) spectrometer spectomrx 1 in KBr pellets over the range of 4000–400 cm−1. Vibrating sample magnetometer (VSM) was recorded with MDKF-FORC/VSM (Megnatis-Daghigh-Kashan Co.). DRS data were recorded by Scinco 4100 in the range 200–900 nm using barium sulfate as reference. The powder small angle XRD studies were performed using Philips X'Pert with Cu Kα radiation (k = 1.54 Å). Surface morphology and distribution of NPs were investigated using LEO 1430 VP scanning electron microscopy.
2.2 Preparation of Fe3O4@SiO2–(CH2)3NH2
Fe3O4 NPs and Fe3O4@SiO2 were prepared according to chemical coprecipitation method given in the literature [39,47,48]. To this end, 1.25 g of FeCl2·4H2O and 3.40 g of FeCl3·6H2O were dissolved in 100 mL deionized water under nitrogen gas at 60 °C, and then 6 mL of 25% ammonia was added and stirred for 45 min. Next, the magnetite precipitates were separated and washed with water and ethanol several times. For preparation of Fe3O4@SiO2, 0.145 g of magnetic NPs were dispersed under ultrasonification for 30 min in the presence of N2 atmosphere. H2O (5 mL), ammonia (3 mL), and TEOS (0.4 mL) were added to the mixture and stirred for 5 h at room temperature. Afterward, the obtained solid was separated and washed several times with ethanol and water and dried under vacuum at room temperature. To the suspension of Fe3O4@SiO2 (0.5 g) in ethanol (50 mL) was added dropwise the APTMS (2.5 mL) dissolved in 50 mL ethanol. After stirring the mixture at 70 °C for 12 h, the aminated magnetic NPs were collected with external magnetic field and washed with water three times, FT-IR (KBr, cm−1): 3406 [υ(OH)], 2924 [υ(CH) aliphatic], 998 [υ(SiO)], 610 [υ(FeO)].
2.3 Synthesis of 1,4-bis(2-carboxyaldehyde phenoxy)butane
1,4-Bis(2-carboxyaldehyde phenoxy)butane was synthesized in accordance with Ilhan et al. [49]; thus, 1,4-dibromobutane (1.08 g, 5 mmol) was dissolved in 5 mL of dimethylformamide and then was added dropwise to a solution of 2-hydroxybenzaldehyde (1.22 g, 10 mmol) and potassium carbonate (0.691 g, 5.0 mmol) in dimethylformamide (30 mL). The mixture was refluxed for 15 h and cooled at room temperature. Next, 70 mL of distilled water was poured into the mixture and was kept at 0–4 °C for 2 h. The creamy precipitated solids were filtered and washed with water and dried in air. The obtained powder was crystallized from ethanol to characterize yield 1.19 g, 80% of 1,4-bis (2-carboxyaldehyde phenoxy)butane. Anal. Calcd for C18H18O4: C, 72.47; H, 6.08; Found: C, 72.1; H, 6.50; mp: 108 °C, IR (KBr, cm−1): 1678 [υ(CO)], 2956, 2862 [υ(aliphatic CH)]. 1HNMR (400 MHz, CDCl3): 10.52 (s, 2H, CHO), 7–7.80 (m, 8H, aromatic), 4.2 (t, 4H, aliphatic OCH2C), 2.1 (t, 4H, CCH2C) (supporting information, Fig. S1).
2.4 Preparation of Fe3O4@SiO2–(CH2)3–PBSB
A solution of 1,4-bis(2-carboxyaldehyde phenoxy) butane (1.49 g, 5 mol, in 60 mL of ethanol) was added to Fe3O4@SiO2–(CH2)3NH2 (1.0 g in 60 mL of ethanol) suspension. The reaction mixture was refluxed by stirring for 2 days. After cooling the mixture, Fe3O4@SiO2–(CH2)3–PBSB was separated using the external magnet and washed several times with water and ethanol, IR (KBr, cm−1): 623 [υ(FeO)], 994 [υ(SiO)], 1636 [υ(imine)CN], 2925, 2849 [υ(aliphatic)CH ], 3418 [υ(OH)].
2.5 Preparation of Fe3O4@SiO2–(CH2)3–PBSB/MoO2
345.2 g (1 mmol) of MoO2Cl2(DMF)2 (prepared by the method given in the literature [50]) dissolved in 40 mL of dichloromethane was added dropwise to the suspension containing 1 g of Fe3O4@SiO2–(CH2)3–PBSB in 40 mL of methanol, and the mixture was refluxed for a day. Then, the solid was separated using the external magnetic field and washed several times with water and ethanol to remove the unreacted MoO2Cl2(DMF)2 and dried at 40 °C. IR (KBr, cm−1): 588 [υ(FeO)], 916, 946[υ(cis, OMoO)], 1024 [υ(SiOSi)], 1652 [υ(CN)], 2938, 2860 [aliphatic, CH], 3410 [υ(OH)].
2.6 Studies of catalytic activity
The catalytic activity of heterogeneous Fe3O4@SiO2–(CH2)3–PBSB/MoO2 catalyst was evaluated by the oxidation of various sulfides [methyl phenyl sulfide, diphenyl sulfide, benzyl phenyl sulfide, dipropyl sulfide, dibutyl sulfide, dimethyl sulfide, bis (4-hydroxyphenyl) sulfide, diallyl sulfide, and benzothiophene]. For testing catalytic oxidation activity, 0.0008 g (3.8 × 10−4 mol) of Fe3O4@SiO2–(CH2)3–PBSB/MoO2, sulfides (10 mmol) and H2O2 (30%) (10 mmol) were added in a ratio of 1:1 to the catalytic reactor. The catalytic system was mixed by stirring for 3 min, the catalyst was removed by the external magnetic field, and the oxidation products were monitored through GC.
3 Results and discussion
3.1 Synthesis and characterization
Heterogeneous Fe3O4@SiO2–(CH2)3–PBSB/MoO2 catalyst was prepared according to procedures shown in Scheme 1 using a reaction of 1,4-bis(2-carboxyaldehyde phenoxy) butane, MoO2Cl2(DMF)2, and amino-modified Fe3O4@SiO2NPs. Fig. 1 indicates the FT-IR vibration of Fe3O4 NP (Fig. 1a), Fe3O4@SiO2–(CH2)3NH2 (Fig. 1b), supporting Schiff base ligand (Fig. 1c), and Fe3O4@SiO2–(CH2)3–PBSB/MoO2 (Fig. 1d). FeeO and SieO stretching bands appeared at 610 and 998 cm−1. As shown in Fig. 1c and d, the assigned band to CN stretching vibration of supporting Schiff base ligand at 1636 cm−1 has shifted to 1652 cm−1 after coordination with Mo6+ center [51]. Hence, the appearance of two adjacent bands at 916 and 946 cm−1 indicates the presence of MoO2 group (Fig. 1d) [52]. The existence of bands at about 2900 cm−1 can be assigned to aliphatic group (CH2) of APTMS. Considering all vibrations of IR spectra confirms the supporting of Schiff base Mo(VI) complex on the magnetic NPs. Fig. 2 shows the XRD pattern of Fe3O4 NP (a) and Fe3O4@SiO2–(CH2)3–PBSB/MoO2 (b). The comparison of two patterns (Fig. 2a and b) and those of standard Fe3O4 NPs (reference JCPDS card no. 87-2334) demonstrated diffraction peaks for Fe3O4 NPs and Fe3O4@SiO2–(CH2)3–PBSB/MoO2. The observed broad peak (about 2θ = 22–29) of Fe3O4@SiO2–(CH2)3NH2 and Fe3O4@SiO2–(CH2)3–PBSB/MoO2 was assigned to the existence of amorphous silicon dioxide. Fig. 3 shows the magnetization properties of synthesized Fe3O4 NPs and Fe3O4@SiO2–(CH2)3–PBSB/MoO2. The magnetization plots of Fe3O4 NPs and Fe3O4@SiO2–(CH2)3–PBSB/MoO2 reveal no hysteresis loop and have the magnetic saturation at 57.67 and 13.63 emu/g, respectively. It seems that the silica layer on magnetite NPs in Fe3O4@SiO2–(CH2)3–PBSB/MoO2 is the leading cause of decreased magnetic saturation. However, the result suggests that the catalyst can be separated from the solution using the external magnetic field. Fig. 4a and b presents the SEM image of Fe3O4 NPs and Fe3O4@SiO2–(CH2)3–PBSB/MoO2. The comparison of SEM images showed no change in morphology. Fig. 4c shows transmission electron microscopy images of the Fe3O4@SiO2–(CH2)3–PBSB/MoO2 nanocatalyst, which is approximately 15–18 nm in size. As presented in Fig. 5, EDX of Fe3O4@SiO2–(CH2)3–PBSB/MoO2 provides the existence of Mo, Si, C, Cl, and the other elements on the catalyst surface. The thermal stability of the catalyst was studied using thermogravimetric assay. Given the thermogravimetric analysis in Fig. S2, the weight loss at 125 and 413 °C for Fe3O4@SiO2–(CH2)3–PBSB/MoO2 can be attributed to the water removal and onset of molybdenum complex decomposition.
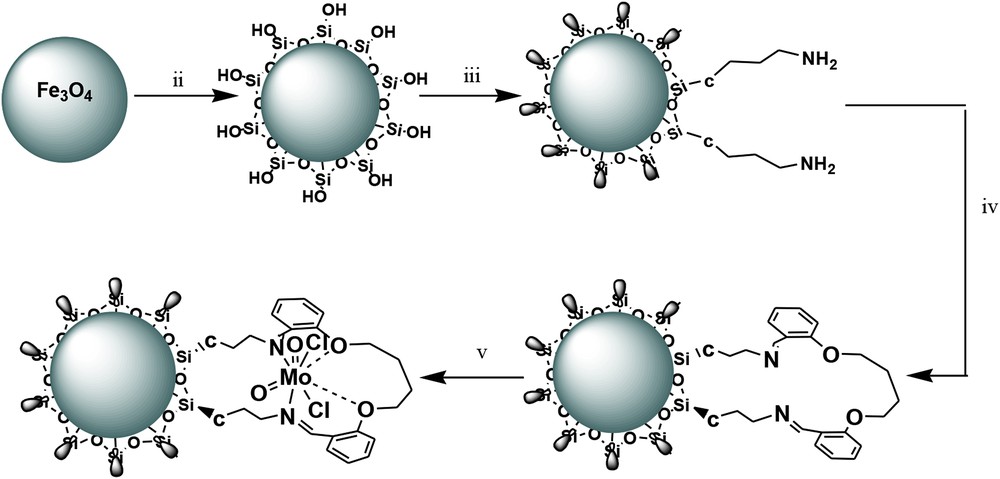
Preparation of the heterogeneous nanocatalyst, (i) K2CO3/DMF, (ii) tetraethoxysilane/EtOH, (iii) APTMS/EtOH, (iv) 1,4-bis(2-carboxyaldehyde phenoxy)butane + stirring at 70 °C for 48 h/EtOH, and (v) MoO2Cl2(DMF)2/EtOH.
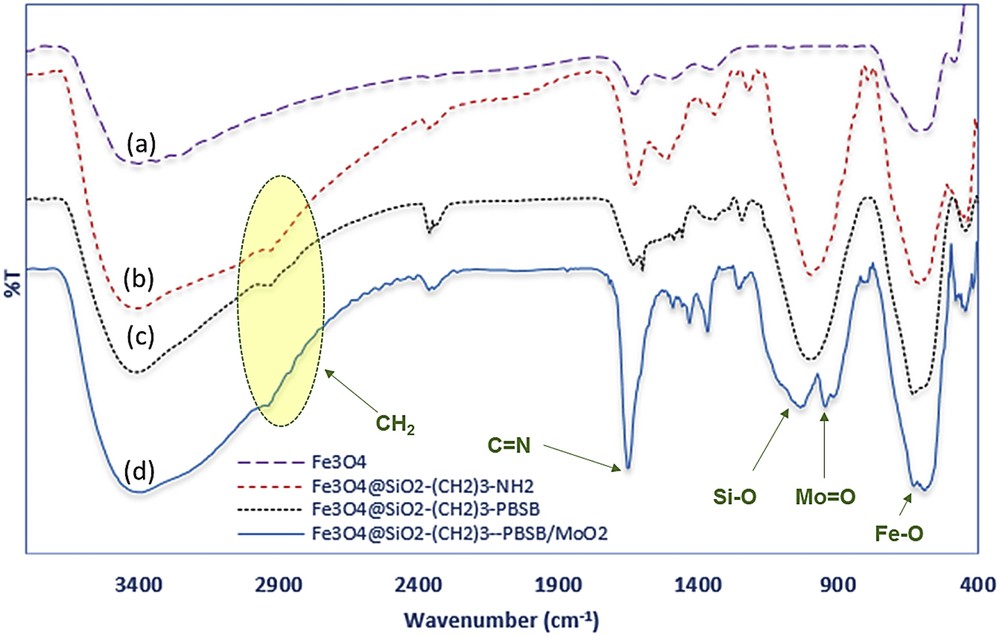
FT-IR spectrum of (a) Fe3O4 NP, (b) Fe3O4@SiO2–(CH2)3–NH2, (c) Fe3O4@SiO2–(CH2)3–PBSB, (d) Fe3O4@SiO2–(CH2)3–PBSB/MoO2.
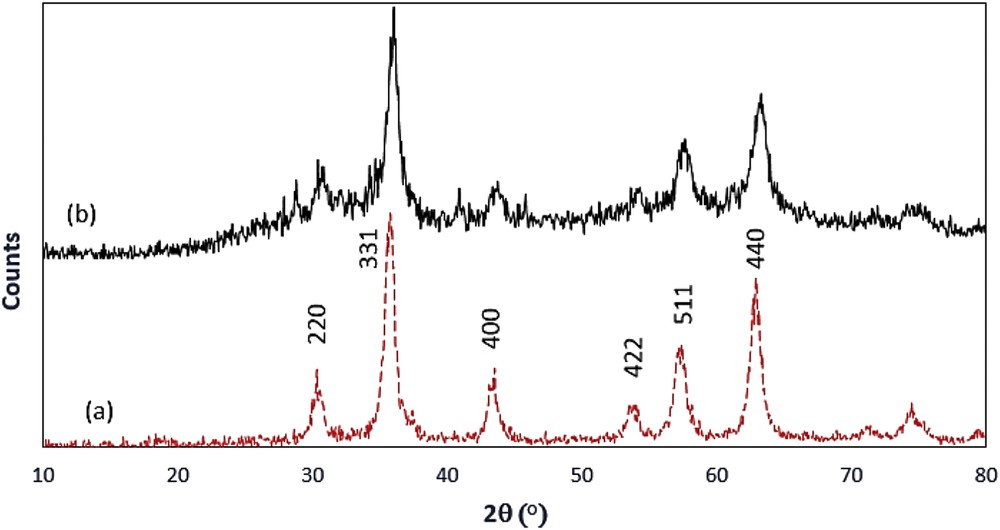
Pattern of XRD, (a) magnetite NPs, (b) Fe3O4@ SiO2–(CH2)3–PBSB/MoO2.
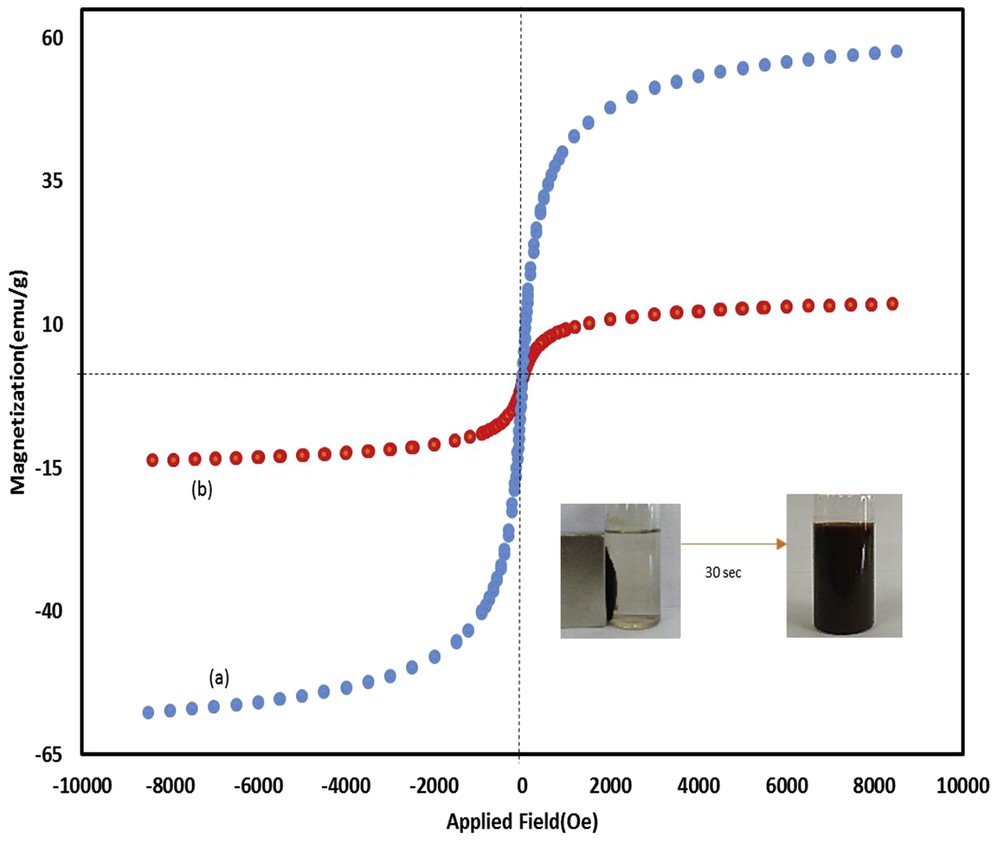
Magnetization response of (a) magnetite NPs and (b) Fe3O4@SiO2–(CH2)3–PBSB/MoO2 at 25 °C.
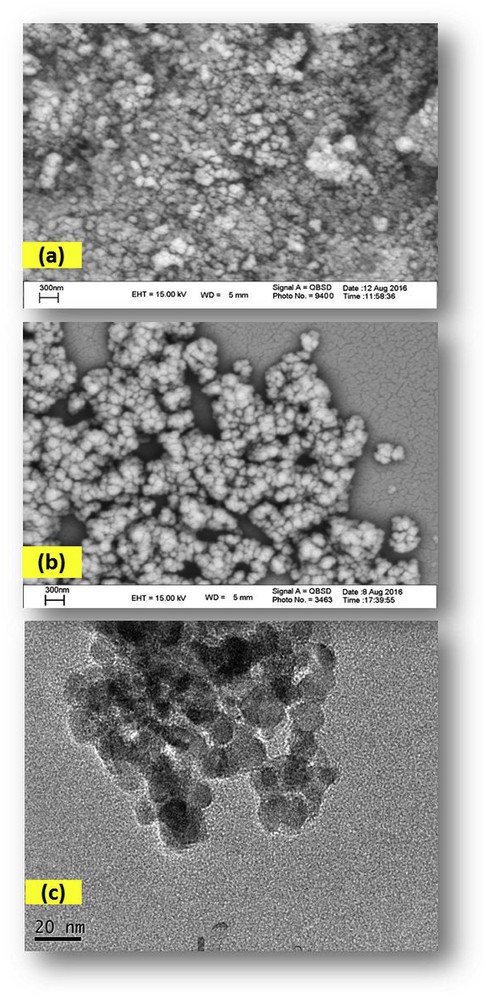
Scanning electron microscopy images of (a) magnetite NPs, (b) Fe3O4@SiO2–(CH2)3–PBSB/MoO2, and transmission electron microscopy images of (c) Fe3O4@SiO2–(CH2)3–PBSB/MoO2.
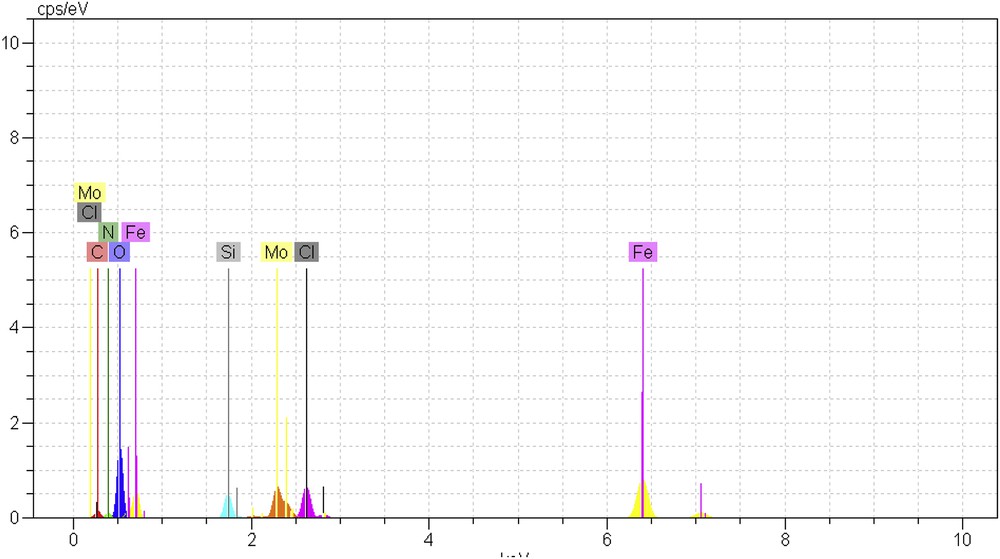
EDX spectrum of Fe3O4@ SiO2–(CH2)3–PBSB/MoO2.
3.2 Catalytic oxidation of sulfides by Fe3O4@SiO2–(CH2)3–PBSB/MoO2
The Fe3O4@SiO2–(CH2)3–PBSB/MoO2 catalyst was used to oxidize various sulfides using 30% H2O2. In the beginning of the catalytic process, some parameters were optimized, including the kind of solvent, amount of the catalyst, temperature of the catalytic reactor, reaction time, and substrate to oxidant molar ratio. After running the catalytic process for thioanisole oxidation with 30% H2O2 and various solvents (5 mL), it has been found that solvent-free conditions bring about the highest conversion (100%) in 3 min (Fig. 6). Fig. 7 shows that the best conversion of thioanisole to oxidation products was obtained at 50 °C. The thioanisole was oxidized by several [H2O2]/[thioanisole] ratios. For this purpose, the 0.5, 1, 1.5, 2 ratios were set in the separate catalytic reactions. According to Fig. 8, the best sulfoxidation result was obtained in the ratio of 1:0 [H2O2]/[thioanisole]. Our results suggested that sulfone product was increased by rising the [H2O2]/[thioanisole] ratio more than 1:0. The catalyst level was optimized for thioanisole oxidation using 0.0, 0.0007, 0.0008, 0.001, 0.003, 0.005, 0.007 g of Fe3O4@SiO2–(CH2)3–PBSB/MoO2. As illustrated in Fig. 9, the optimal amount of the catalyst was reported as 0.0008 g. It appears that by increasing the catalyst amount more than 0.0008 g caused the decomposition of H2O2. Finally, we selected the sulfides (10 mmol) as substrate, 30% H2O2 (10 mmol) as oxidant, and 0.0008 g of the catalyst (3.8 × 10−4 mmol determined by atomic absorption spectroscopy) at 50 °C by stirring under solvent-free conditions for 3 min. The catalyst reactor monitoring exhibited no color and Mo leaching (detected by atomic absorption spectroscopy) in the final solution after the catalytic procedure. The results of catalytic oxidation of sulfides, methyl phenyl sulfide, diphenyl sulfide, benzyl phenyl sulfide, dipropyl sulfide, dibutyl sulfide, dimethyl sulfide, bis(4-hydroxyphenyl) sulfide, diallyl sulfide, and benzothiophene, are summarized in Table 1. Our results demonstrated 100% conversion for thioanisole, dimethyl sulfide, and diallyl sulfide, as well as <99% conversion for dibutyl sulfide in 3 min. Therefore, excellent turnover frequency of the catalyst was achieved to oxidize the thioanisole (526,000 h−1), dimethyl sulfide (526,000 h−1), diallyl sulfide (526,000 h−1), dibutyl sulfide (521,000 h−1), and dipropyl sulfide (500,000 h−1). Accordingly, the reason for low oxidation conversion of bis(4-hydroxyphenyl) sulfide, diphenyl sulfide, benzyl phenyl sulfide, and benzothiophene is related to the steric effect of sulfides and the catalyst. The selectivity of oxidation reactions for sulfoxide production is in the acceptable ranges (Fig. 10). The catalytic oxidation of the substrate with aqueous H2O2 in the blank run (without catalysts) occurs with 2% conversion. The chemical and physical stabilities of the catalyst result in recycling and reusing of the catalyst several times (six times). As shown in Fig. 11, the catalyst was separated easily with the magnet and used several times for epoxidation process. A hot filtration test was performed for further investigations of catalyst leaching. For this purpose, the catalyst was removed from the reaction mixture after 1 min and the conversion was calculated after the other 3 min. The conversion showed no significant increase. Fig. 12 presents no change in the IR spectra for the catalyst before oxidation and sixth run. Therefore, comparison between DRS spectra of the catalyst (Fig. 13) before and after the oxidation process shows no change. Regarding the conversion results and literature [53], the proposed mechanism seems to be followed through a seven-coordinate intermediate (Scheme 2). In a catalytic cycle, oxidation process starts with attacking of H2O2 to Mo center and generation of oxo–peroxo Mo(VI) precursor. In the following, sulfur electron pair attacks the σ∗(OO) of oxo–peroxo Mo(VI), and the catalyst is regenerated with production of sulfoxide.
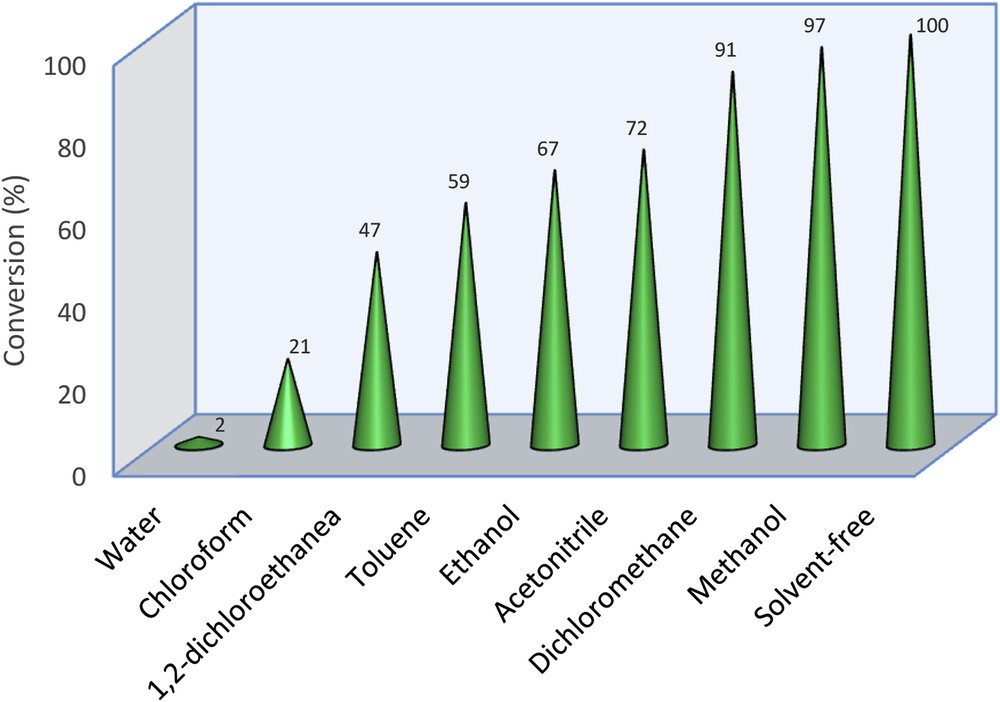
Oxidation of thioanisole (1 mmol) in various solvents (5 mL) and under solvent-free conditions with 30% H2O2 (1 mmol) and catalyst (3.8 × 10−4 mmol) during 3 min.
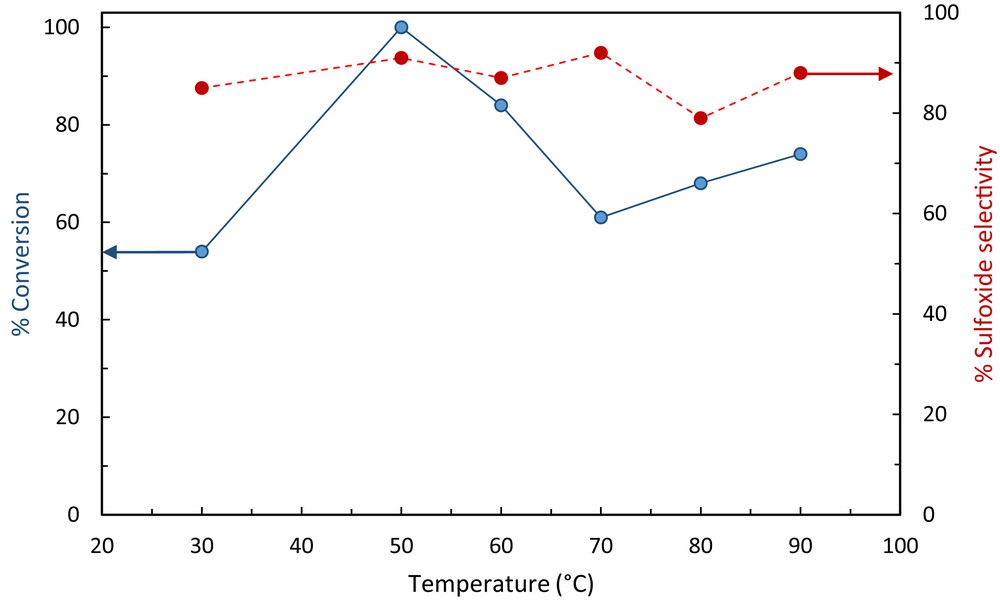
Optimization of catalytic reaction temperature, thioanisole (1 mmol), 30% H2O2 (1 mmol), catalyst (3.8 × 10−4 mmol), solvent-free conditions, 3 min.
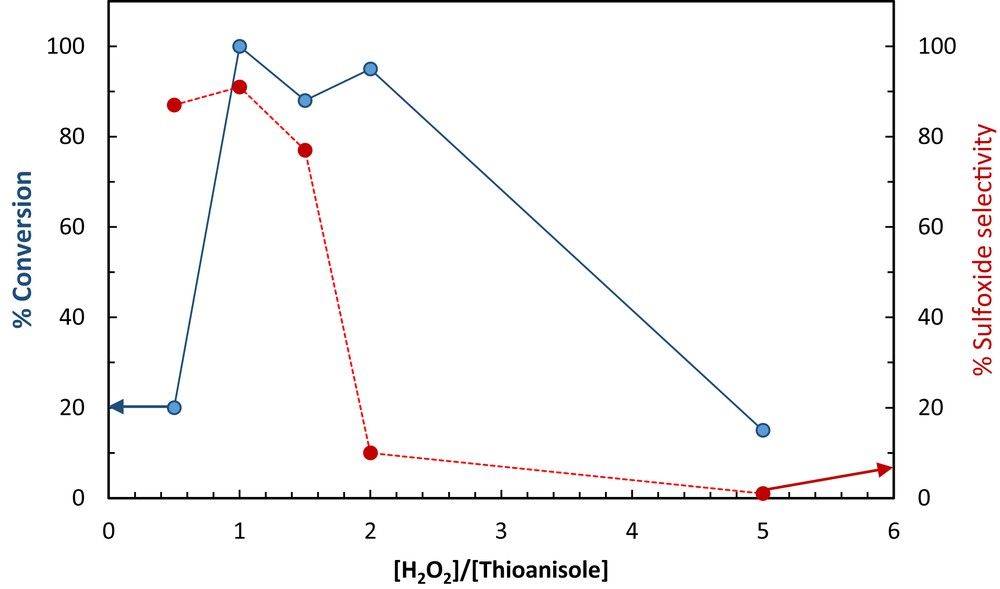
Effect of a [H2O2]/[thioanisole] ratio on sulfoxidation conversion (left axis) and sulfoxidation selectivity (right axis), catalyst (3.8 × 10−4 mmol), solvent-free conditions, 3 min, 50 °C.
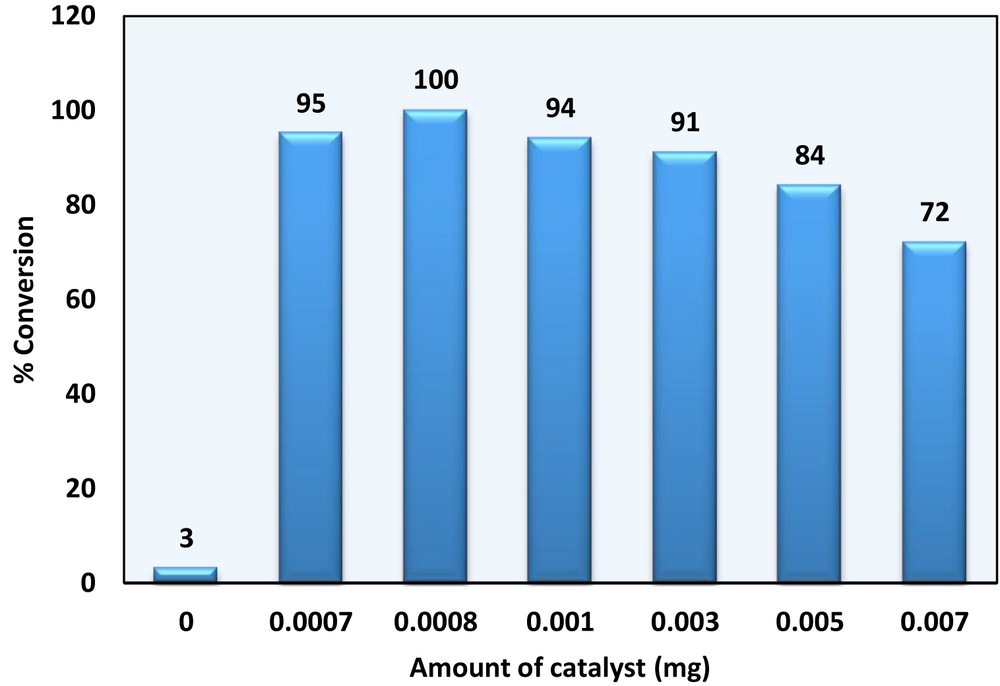
Effect of a catalyst amount on sulfoxidation conversion under solvent-free conditions, thioanisole (10 mmol), H2O2 (10 mmol), T = 50 °C, reaction time = 3 min.
Results of catalytic oxidation of various sulfides with H2O2 (30% aqueous) catalyzed by Fe3O4@SiO2–(CH2)3–PBSB/MoO2.a
Sulfides | Sulfide (mmol) | %Conversionb | TOF (h−1)c |
Image 1 | 10 | 100 | 526,000 |
Image 2 | 10 | 100 | 526,000 |
Image 3 | 10 | 100 | 526,000 |
Image 4 | 10 | 99< | <521,000 |
Image 5 | 10 | 95 | 500,000 |
Image 6 | 1 | 2 | 1052 |
Image 7 | 1 | 12 | 6300 |
Image 8 | 1 | 20 | 10,520 |
Image 9 | 1 | 15 | 7890 |
a Catalytic reaction condition: solvent free; [sulfides]/[H2O2] (1:1), catalyst = 0.00038 mmol, reaction temperature = 50 °C, reaction time = 3 min.
b Conversion were determined by GC-FID (flame ionization detector), conversion = [(mole of SO) + (mole of SO2)]/(mole of initial sulfide).
c Calculated as (mmol of product)/(mmol of catalyst) × hours.
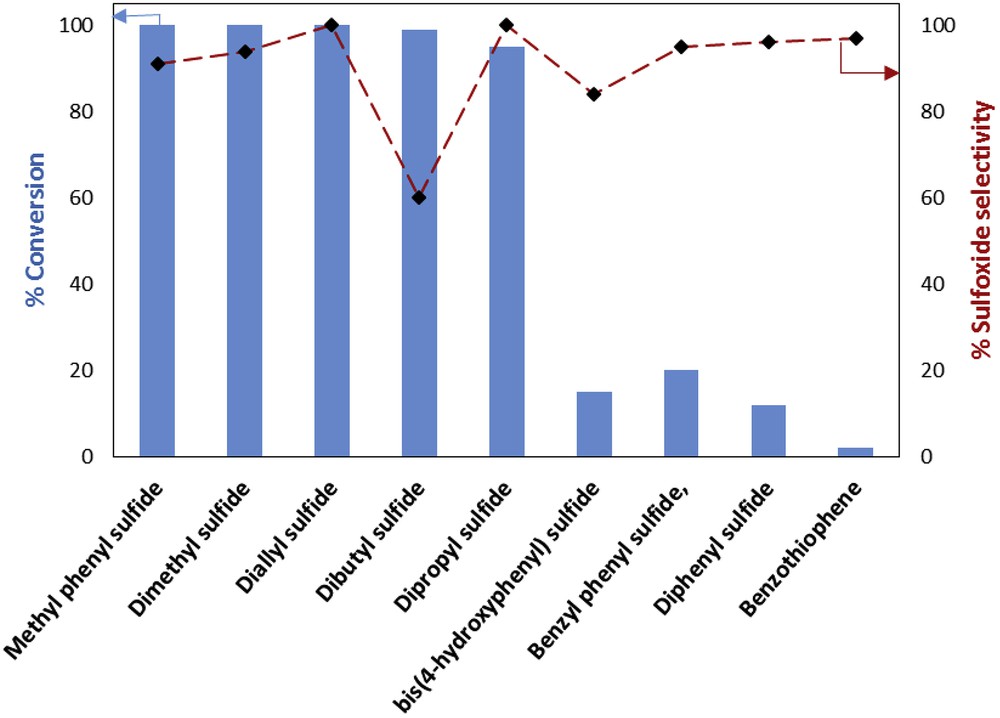
Conversion and selectivity for oxidation of sulfides by the catalyst, solvent-free conditions, H2O2 (30%), 50 °C, 3 min.
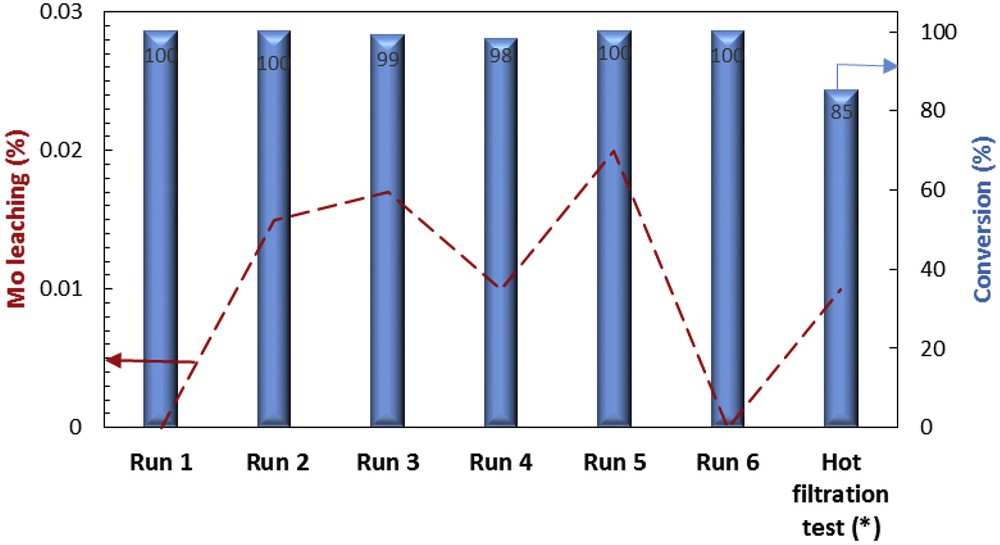
Running of the catalyst several times, reaction conditions: solvent-free; thioanisole (10 mmol), H2O2 (10 mmol), catalyst (3.8 × 10−4 mmol), 3 min, 50 °C, ∗Hot filtration test: after 1 min, the catalyst was removed from the reaction mixture (83% conversion) and the conversion was calculated after next 6 min (85% conversion).
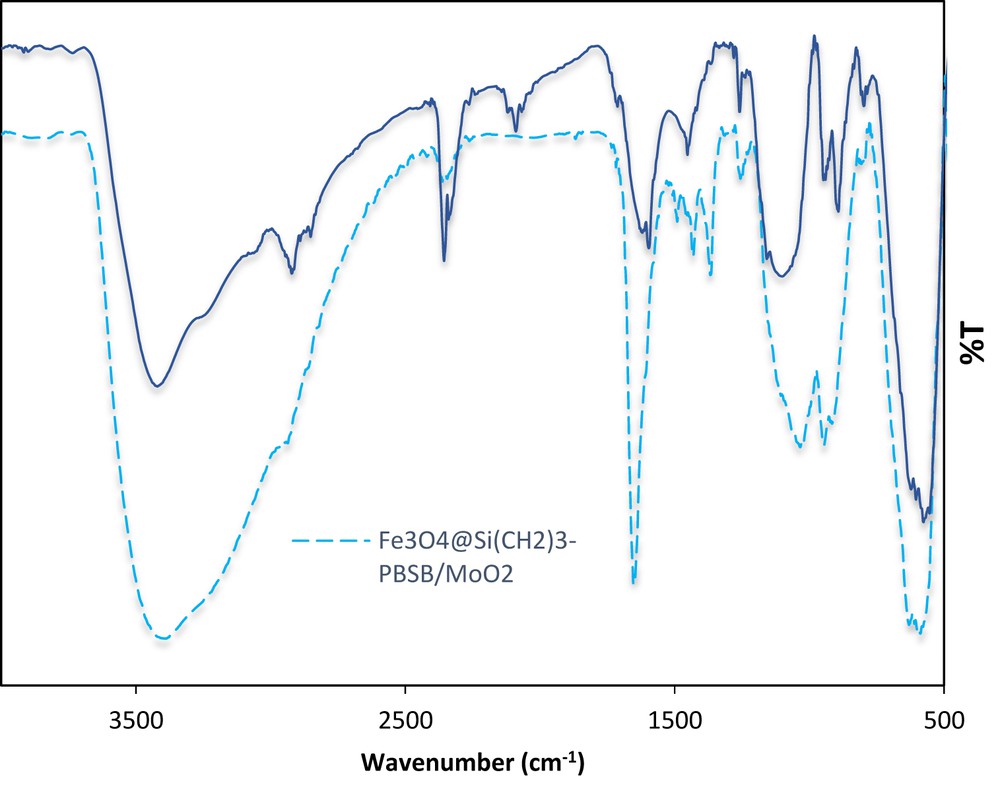
FT-IR spectrum of Fe3O4@ SiO2–(CH2)3–PBSB/MoaO2 before the catalytic reaction (solid line) and after the sixth run (dashed line).
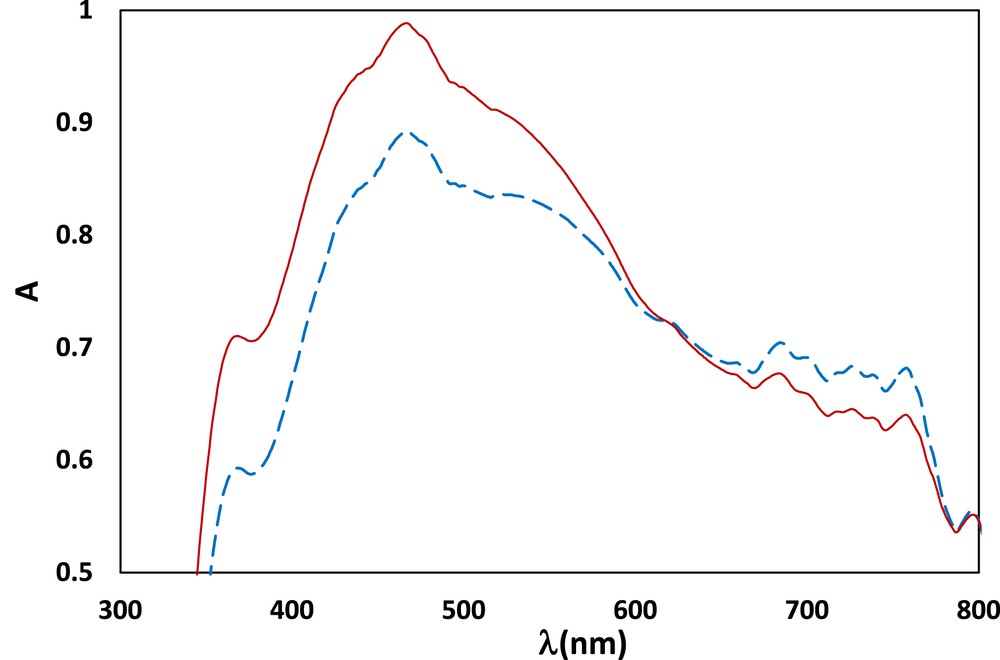
DRS spectrum of Fe3O4@ SiO2–(CH2)3–PBSB/MoaO2 before the catalytic process (solid line) and after the sixth run (dashed line).
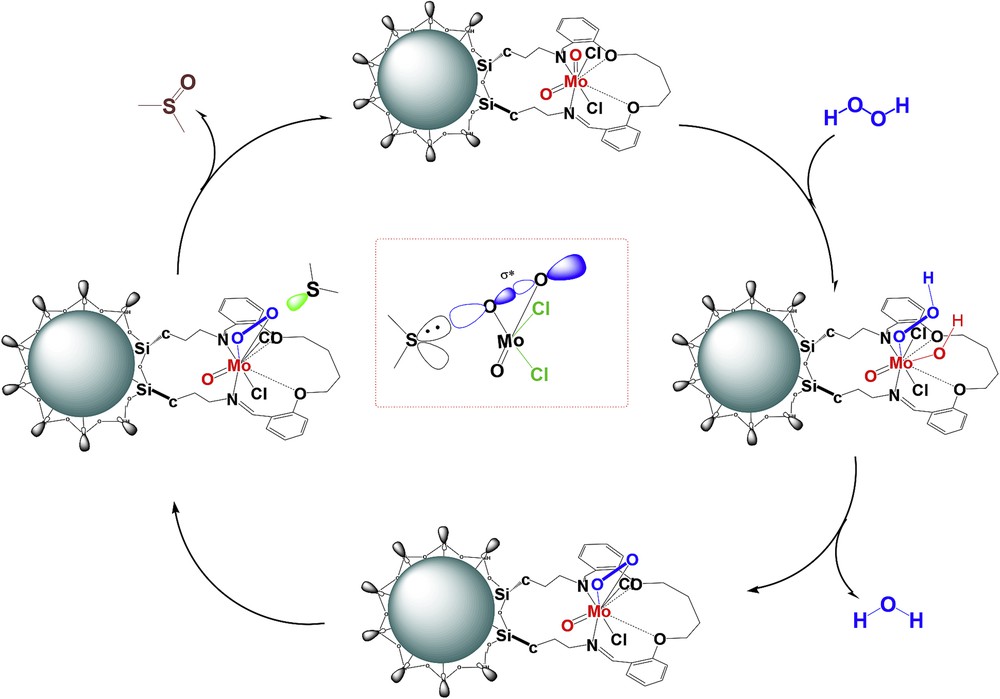
Proposed catalytic cycle for oxidation of sulfides by Fe3O4@SiO2–(CH2)3–PBSB/MoO2 with H2O2.
Table 2 shows the comparison between the novel presented catalyst and literature reports. The Fe3O4@SiO2–(CH2)3–PBSB/MoO2 indicated higher oxidation catalytic activity of thioanisole with excellent TOF (TOF: turnover frequency) (<526,000 h−1). Finally, by comparing the catalytic reaction time of the reported works in the literature (Table 2), 90 min [54], 180 min [55], 120 min [56–58], 60 min [14], 85 min [59], 30 min [60,61], and 15 min [62,63] with Fe3O4@SiO2–(CH2)3–PBSB/MoO2 (3 min), it is found that the presented catalyst is efficient, time saving, and paramount.
Comparison of literature reports on the oxidation of thioanisole under various conditions.
Catalyst | Oxidant | Solvent | Time | %Conversion | Ref. |
SBA-15 + ImCl + MoO5 | H2O2 (30%) | Methanol | 60 min | 95 | [14] |
TiO2/AA/MoO2 | H2O2 (30%) | Ethanol | 30 min | 100 | [60] |
[(n-C4H9)4N]4(α-Mo8O26) | H2O2 (30%) | Methanol | 10 min | 98 | [64] |
ML2(Cu, Co Zn, Pd) | H2O2 (30%) | Solvent-free | 180 min | 80 | [55] |
Ti-MCM-41 | H2O2 (30%) | Solvent-free | 120 min | 89 | [56] |
[PO4{WO(O2)2}4]@PIILP | H2O2 (30%) | Methanol | 15 min | 95 | [62] |
[MRAMoO2(O2)] | H2O2 (30%) | Methanol | 15 min | 99 | [63] |
VO-2A3HP-MCM-41 | H2O2 (30%) | Solvent-free | 120 min | 96 | [57] |
Ti-IEZ-MWW | H2O2 (30%) | Solvent-free | 120 min | <99 | [58] |
Fe3O4@chit-based Cu complex | H2O2 (30%) | Solvent-free | 90 min | 97 | [54] |
p-TsOH | H2O2 (30%) | Solvent-free | 85 min | 90 | [59] |
e3O4@APTMS/fluorene-SBeMoO2 | H2O2 (30%) | Solvent-free | 5 min | 99 | [61] |
Fe3O4@Si-APFSB-MoO2 | H2O2 (30%) | Solvent-free | 3 min | 100 | This work |
4 Conclusions
In the present study, following our previous researches on the catalytic activity, we found successful covalent anchoring of a phenoxy butane-based Mo(VI) tetradentate Schiff base complex on magnetite NPs. The novel paramagnetic recoverable catalyst has been studied as nanocatalyst for oxidation of methyl phenyl sulfide, diphenyl sulfide, benzyl phenyl sulfide, dipropyl sulfide, dibutyl sulfide, dimethyl sulfide, bis(4-hydroxyphenyl) sulfide, diallyl sulfide, and benzothiophene. The catalyst was recovered successfully using the magnet from the catalytic reactor and reused as a catalyst for six times without decrease in conversion and selectivity. Fe3O4@SiO2–(CH2)3–PBSB/MoO2 catalyst illustrated excellent catalytic activity and remarkable short catalytic time (3 min) than the other reported catalysts. The Fe3O4@SiO2–(CH2)3–PBSB/MoO2 catalyst indicated a remarkable high TOF (<526,000 h−1).
Acknowledgments
The authors would like to thank and appreciate Research Deputy of Mohaghegh-e-Ardabili University, Iran, for financial support under the project (Grant number: 281).