1 Introduction
The growing request for building materials motivated many researchers to identify materials that promote sustainable development. The manufacturing of Portland cement (PC; the type of cement in common use today) is an energy-intensive and resource demanding transaction process resulting in a considerable release of the CO2 gas [1]. More polluting gases, such as SO3 and NOx, are released and drive into acid rains and more severe greenhouse effects [2]. Therefore, many researches are being carried out to create new hydraulic binders, which not only could replace PC but could also be manufactured in a way to protect our live environment. Among these hydraulic binders, inorganic polymer (geopolymer) shows attractive potentials [3–5]. The term “geopolymer” was coined by Davidovits in the 1970s, originally referring to the investigations on the reaction of metakaolin in alkaline media forming aluminosilicate polymers [6]. Products given by geopolymerization reactions have some advantages, namely, higher mechanical strength, resistance to firing, limited degradation under chemical agents, and low shrinkage [3,7]. The inorganic polymer is obtained by mixing alkaline solution with aluminosilicate materials. The alkaline liquids (NaOH, KOH, etc.) at high concentrations could be used to react with silicon (Si) and aluminum (Al) in a source material of natural minerals or in byproduct materials such as fly ash and rice-husk ash to produce binders. The alkaline activation of materials can be defined as a chemical process that provides a prompt modification of some specific structures, partial or totally amorphous, into compact cemented frameworks [8]. The crude mineral sources that are commonly used are usually rich in aluminosilicate. Examples include natural pozzolan, fly ash, blast-furnace slag, and metakaolin. For the production of geopolymer binders, several researchers use calcined kaolinitic clay at diverse temperatures [9–11]. Illite, smectite, and other clay minerals are rarely used for geopolymer preparation. The variation in chemical composition of clay minerals and the parameters of thermal activation complicate the decision about whether it remains adequate to use clay resources to produce geopolymers [12,13]. It is worth noting that recently the uses of construction and industrial wastes for geopolymer fabrication received great attention. Mineral waste recycling can reduce the need for natural resources and energy, and the benefit from these recycled materials is to improve the performance of synthesized geopolymer binders [14]. Therefore, the use of waste minerals like Bayer red mud and granulated blast-furnace slag was reported in many research works [15,16].
In this work, we propose a new experiment to test whether phosphogypsum (PG) and waste brick (WB) can be used as raw materials to produce geopolymer binders.
The present investigation focuses on the suitability of mixing a Tunisian red clay mineral with different ratios (4%, 8%, 12%, and 16%) of PG to form geopolymer cements. We emphasize that it is novel to use Tunisian PG preparation. The used clay was calcined at 850 °C and characterized by X-ray diffraction (XRD) and infrared spectroscopy. The geopolymer samples were activated by NaOH solution (10, 14, and 17 M). The compressive strength of the hardened geopolymer binder paste samples preserved for 28 days was determined. At the optimal condition a geopolymer sample was prepared by replacing heated red clay with the WB powder and its mechanical properties were determined, and then confirmed the suitability of use of WB and PG for geopolymer fabrication. The use of PG and WB is a very innovative and attractive alternative considering the low cost and availability of these materials.
2 Materials and experimental methods
2.1 Materials
The clay mineral sample used in this study was collected from Tejra region (Medenine, South East of Tunisia). The main fraction is kaolinite associated with illite, hematite, and quartz [4]. This clay is mainly used as a raw material in the red brick industry. The dried clay fractions were crushed in a mortar and then sieved through 150 μm sieve.
The temperature of 850 °C is very suited to synthesize a good geopolymer binder. This hypothesis is based on a previous study by four who tested the effect of thermal activation of raw clay on the geopolymerization reaction. We calcined the clay sample at 850 °C in a programmable electric furnace (Nabertherm, Mod. L5/11) for 2 h at a heating rate of 10 °C/min. In this experiment we used other materials, namely, the PG and the WB. We obtained PG from the chemical industry of Gabès, whereas WB was available at the brick industry of Medenine. The PG powder was washed three times with fresh water and dried at 100 °C for a night. The WB was crushed and grounded using a crusher and a ball mill. Subsequently, all materials were sieved through 150 μm sieve and characterized by XRD and Fourier transform infrared (FTIR) spectroscopy. We dissolved dried pellets of 99% purity in distilled water to obtain three concentrations of sodium hydroxide (10, 14, and 17 M). The sodium hydroxide was supplied by Sigma–Aldrich (St. Louis, MO).
2.2 Experimental methods
The preparation of the geopolymers consists of mixing the raw material powder with solutions of alkali hydroxide, NaOH, using a mass ratio solid/liquid of 3 at room temperature. The mixture was homogenized for 3–5 min. The paste samples were casted in PVC cylindrical molds (diameter 2.1 cm; height 4.0 cm) and were vibrated for 5 min to eliminate trapped air bubbles. We used plastic sheets to cover the geopolymers and avoid water evaporation and carbonation. The geopolymers were maintained for 48 h before the demolding stage. The dried samples remained for 28 days at room temperature in the laboratory.
We measured the compressive strength of geopolymers using a traction machine (EZ 50 lloyd), that is, enslaved on a trip of 5 mm/min. The chemical analyses of the raw clay and waste materials were carried out using an atomic absorption spectrometer (AAS vario 6, Analytik jena). The mineral crystalline phases were determined by X-rays diffractometry using a PANalytical X'Pert-V diffractometer, which functions by reflection of Cu kα radiation (30 mA and 40 kV) of 5°/min scanning speed. The thermal study of the raw clay was completed with a coupled DTA-TG sensor oven (TA Instruments) instrument. The FTIR spectrum of the clay mineral was recorded on a KBr disk, which contains 1% sample by mass, using a Perkin–Elmer (model 783) spectrophotometer. The nuclear magnetic resonance (NMR) characterizations of the clay and geopolymer samples were carried out using an MSL 360 Bruker solid state with high-resolution NMR spectrometer. The NMR spectrometer is equipped with 7.05 T wide-bore superconducting magnets at 59.62 and 78.20 MHz for 29Si and 27A1 NMR spectra, respectively.
3 Characterization of raw materials
Table 1 represents the chemical analysis of the raw materials used in this study. We noticed that the mass ratio of Si/Al was greater than 2 in the case of raw clay and the slightly higher iron oxide (Fe2O3) confirmed the presence of hematite. As for the PG the main constituents are SO3, CaO, and SiO2. The chemical analysis of WB shows that the SiO2 is the major constituent and the loss on ignition is relatively lower if compared with the initial clay.
Chemical composition of raw minerals.
Oxides | SiO2 | Al2O3 | Fe2O3 | MgO | CaO | Na2O | K2O | SO3 | P2O5 | Loss on ignition (LOI) |
Raw clay | 55.14 | 14.22 | 8.12 | 3.65 | 1.76 | 0.53 | 2.73 | – | – | 13.11 |
PG | 10.32 | 1.54 | 0.21 | 0.64 | 24.56 | 0.98 | 0.45 | 41.12 | 1.43 | 18.31 |
WB | 61.73 | 13.56 | 8.72 | 2.85 | 2.94 | 0.42 | 2.08 | 1.43 | – | 6.73 |
The results of thermal analyses (Fig. 1) show that the red clay sample has a mass loss of 2.5% at about 133 °C attributed to evaporation of moisture content. The next mass loss at around 450–650 °C and corresponding to 5.15% is due to the elimination of the OH groups of kaolinite. The DTA curve in Fig. 1 shows three endothermic peaks: the first one appears in the range of 100–200 °C, corresponding to the moisture loss also seen with TG. The second peak appears at about 560 °C and is attributed generally to the dehydroxylation of clay mineral and corresponds mainly to transformation of kaolinite into metakaolinite [17,18]. This dehydroxylation is the removal of hydroxyl groups from Al–OH bonds [19].
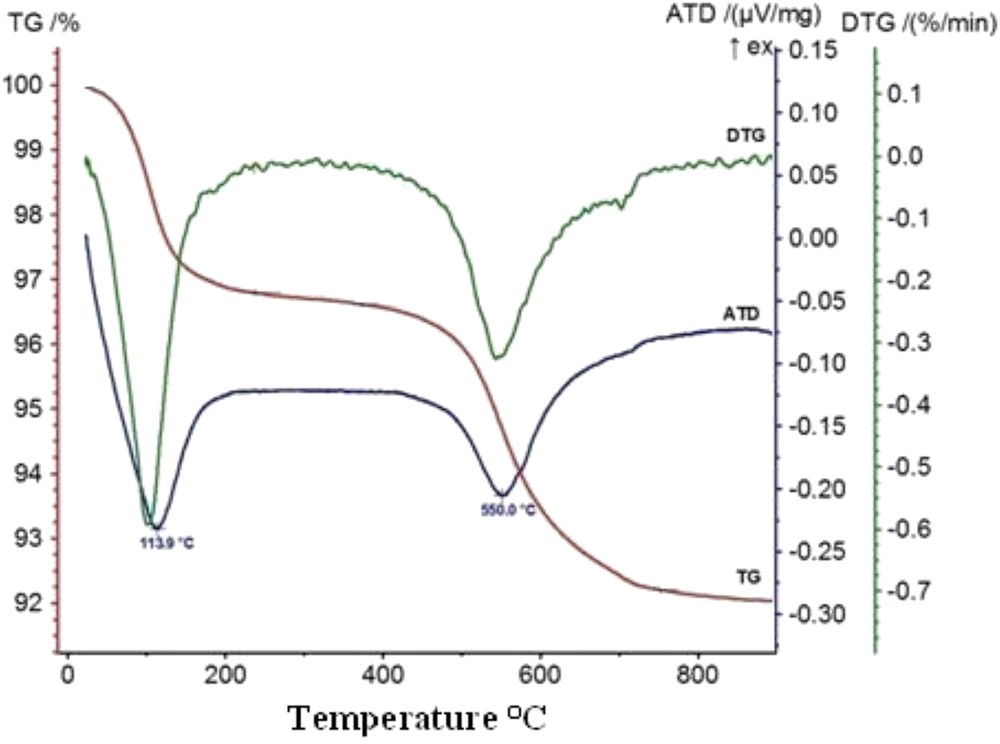
DTA-TG curves of clay mineral powder.
Fig. 2 presents the XRD patterns of raw and calcined clay, PG, and WB samples. As shown, these clay samples are essentially consisting of kaolinite and illite. The associated mineral is quartz and hematite. XRD analysis of the calcined samples showed the disappearance of the peak of kaolinite (reflection at 7.15 Å) at the temperature 850 °C. The intensity of the illite peaks (reflection at 10 Å) also decreased compared with raw clay. The same observation was found in the case of WB, the only difference is that the intensity of quartz is getting higher and it is confirmed by the higher percentage of SiO2 for the WB. Besides, the XRD diffractogram of PG reveals the presence mainly of gypsum (Ca(SO4·)·2H2O) and brushite (CaPO3(OH·)·2H2O).

XRD patterns of raw materials: PG, WB, RC850 (raw clay calcined at 850 °C), and RC (raw clay). G, gypsum; B, brushite; Q, quartz; I, illite; K, kaolinite; H, hematite.
The FTIR spectra of raw materials are presented in Fig. 3. In the case of clay spectra the bands of absorption are in the range 400–1200 cm−1. This is due to OH bending vibrations of Si–O and Al–O. Within the range of 420–500 cm−1, the band arising at 470 cm−1 refers to the bending mode of Si–O–Al vibration and was assigned to T–O bending mode (where T = Si or Al) [20]. The observed band at 1040 cm−1 refers to the asymmetric stretching mode of Si–O–Si vibration and is assigned to T–O stretching mode. The band characteristic of quartz (Si–O–Si vibrations) is located between 781 and 800 cm−1. The lowest intensity absorption band at 3697 cm−1 is assigned to stretching vibrations of octahedral OH groups of Al2OH attributed to kaolinite [21]. This band disappeared in the spectra of calcined samples. For all samples, a band arising at ∼1660 cm−1 is due to the usual bending vibrations of water. The second vibration (∼3400 cm−1) may be attributed to the hydrogen bonding of water molecules to the surface oxygen. As for the PG spectra, two bands at 600 and 669 cm−1 are attributed to asymmetric vibration mode of SO4. The stretching mode band was found at about 1100 cm−1.
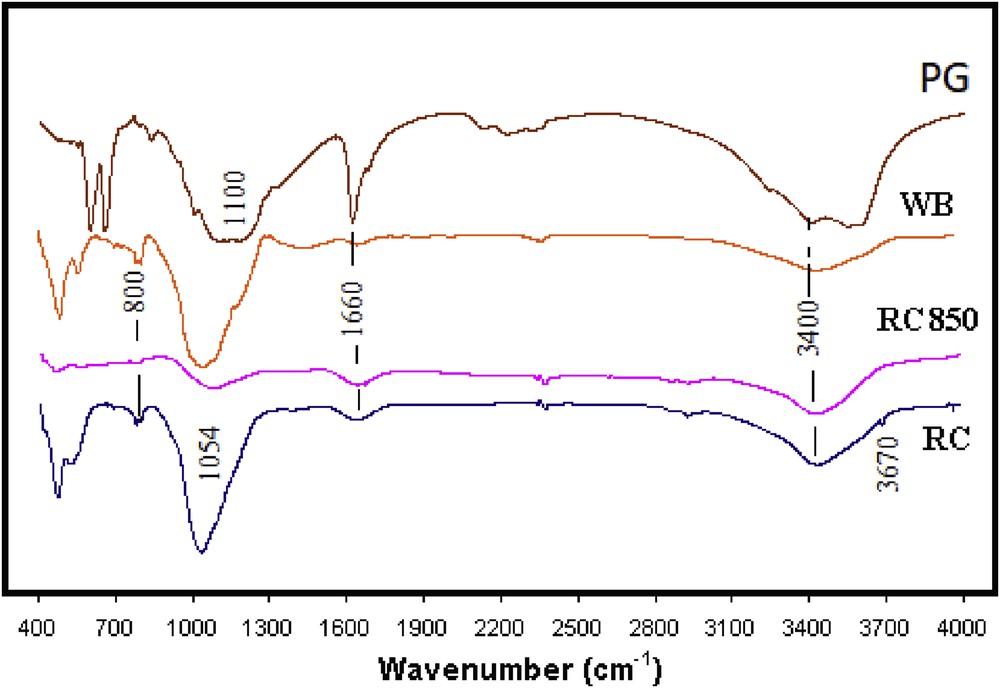
Infrared spectra of raw materials: PG, WB, RC850 (raw clay calcined at 850 °C), and RC (raw clay).
4 Characterization of hardened geopolymer binders
4.1 Compressive strength
The compressive strength of hardened geopolymer binders (cylinder form, Fig. 4) of the heated clay (850 °C) and for the other four mixtures are presented in Fig. 5. It is shown that the compressive strength increases with the addition of PG until 8%. It is observed that 14 M of NaOH is the best concentration giving the highest compressive strength, 36 MPa. The main factors that can initiate and propagate the geopolymerization reaction are alkali hydroxide in the presence of silica and alumina. The strength increases with 8% of PG better than the control mixture. The main reason is the presence of sulfate content, which enhances geopolymer formation. Consequently, both sulfate and alkalinity have an additional activation of the pozzolanic materials.
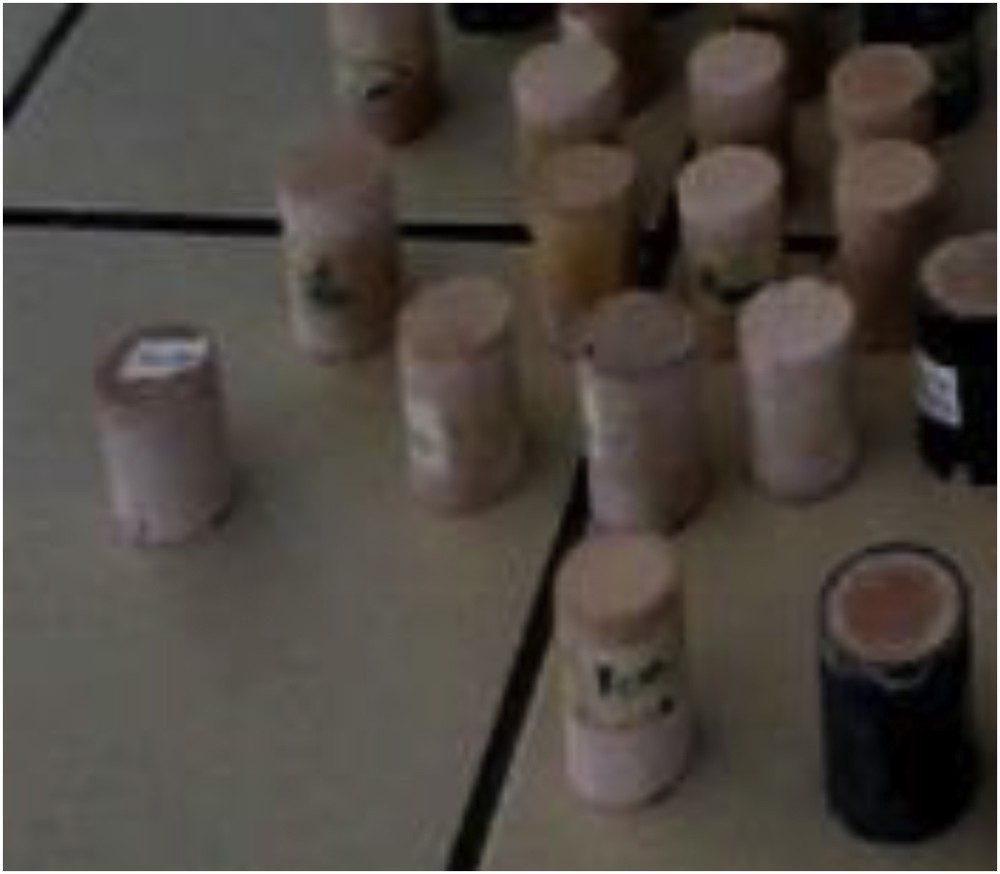
Prepared samples.
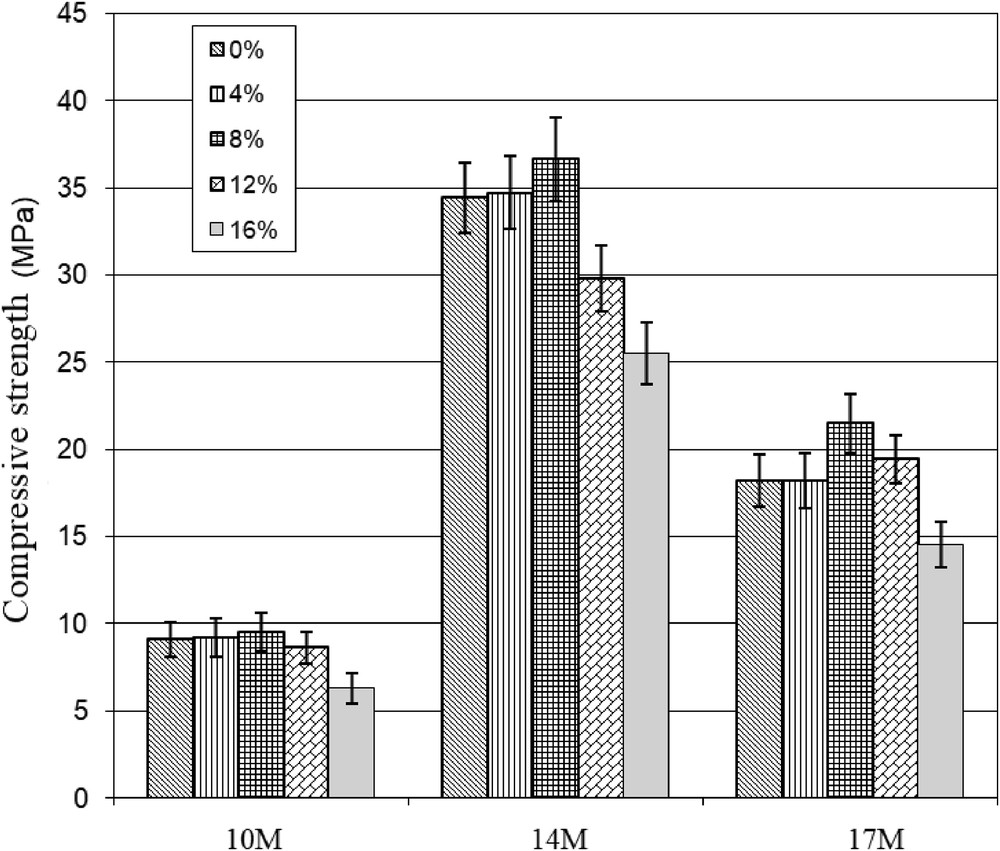
Compressive strength of the hardened geopolymer samples depending on NaOH concentrations and PG content.
The concentration of 10 M is insufficient to activate the calcined clay. The 17 M of NaOH is in excess giving rise to a less mechanical performance of geopolymer products. In addition, the increase in PG above 8% has a negative impact on the geopolymerization reaction, because sulfate disturbs the geopolymer structure by the formation of ettringite, which causes swelling. Therefore, it could absorb the moisture, and this explains the increasing of geopolymers volume to about 124% [22].
4.2 Density of hardened geopolymer samples
Each sample was dried at a temperature of 85 °C for 24 h, and the weight of each sample was measured (Wd). The sample was then immersed in water for 24 h and weighed (Ww). At the last step we determine the weight of saturated sample in air (Wa). ρw is the density of water (1000 kg/m3).
The density of hardened geopolymer is calculated as follows:
(1) |
As shown in Fig. 6, the density of synthesized geopolymers increases slightly with increasing PG content until 8%. High values of density were found for the geopolymers prepared using NaOH 14 M. According to the results of the mechanical strength, the density of the samples synthesized with clay calcined at 850 °C with 8% of PG and using 14 M of NaOH concentration has been the highest density (2296 kg/m3). This increase in density indicates the formation of a compacted structure and the closure of the open porosity. At 10 and 17 M of NaOH concentration the densities are slightly lower.
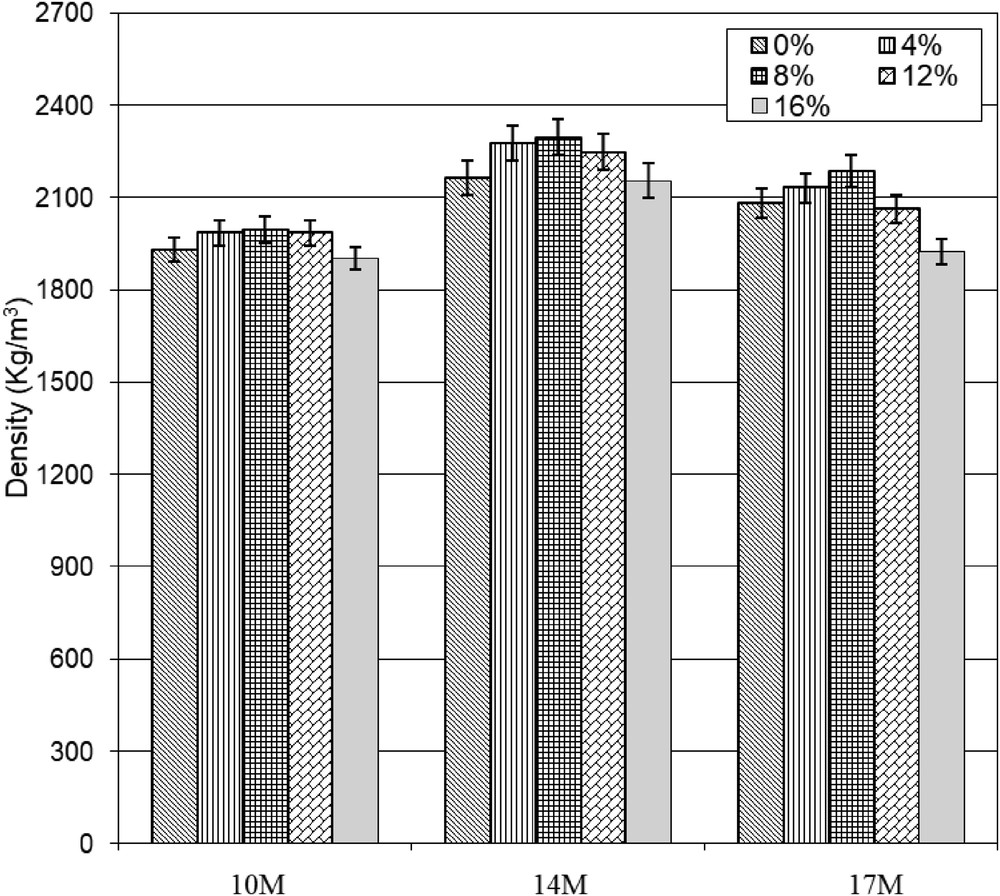
Density of the hardened geopolymer samples depending on NaOH concentration and PG content.
4.3 Nuclear magnetic resonance (NMR)
In general, several geopolymers of practical interest are noncrystalline and their structure must be studied by the NMR spectroscopy, which provides better insight into the molecular framework. The analysis of the prepared geopolymers with XRD does not show any new peaks. It indicates just a slight bump around 20° (2θ), which is characteristic of an amorphous phase. Fig. 7 shows the NMR spectra of raw clay, calcined clay (850 °C), and the best geopolymer binder (sample prepared using 8% of PG and NaOH solution of 14 M). The well-resolved resonance at −91.1 is attributed to a specific Q3 (O-Al) site. The chemical shift equal to −108 ppm identified in 29Si NMR MAS spectra of clay sample is attributed to the tetrahedral [SiO4] four-coordination Q4 characteristic of quartz [23,24]. According to the 29Si NMR MAS spectra of geopolymer binder, the main shift at −90.5 ppm indicates the presence of the both units Q4(3Al) and Q4(2Al) in the geopolymer structure [23]. The NMR spectra of geopolymer samples depict a resonance at −113 ppm, which is assigned to Q4 of the amorphous silica phase. Fig. 7 shows the 27Al NMR spectra of the raw and calcined clay and geopolymer synthesized from clay heated at 850 °C. The spectra display two dominant peaks at 2.05 and 56.6 ppm, assigned to the octahedral and tetrahedral Al-coordination, respectively. For the calcined sample, all the octahedral coordination was transformed to tetrahedral sites and the same observation for the geopolymer binder. Consequently, the six-coordinated aluminum species present in the raw material had condensed to form the three-dimensional geopolymeric network that essentially consisted of four-coordinated aluminum species [25].
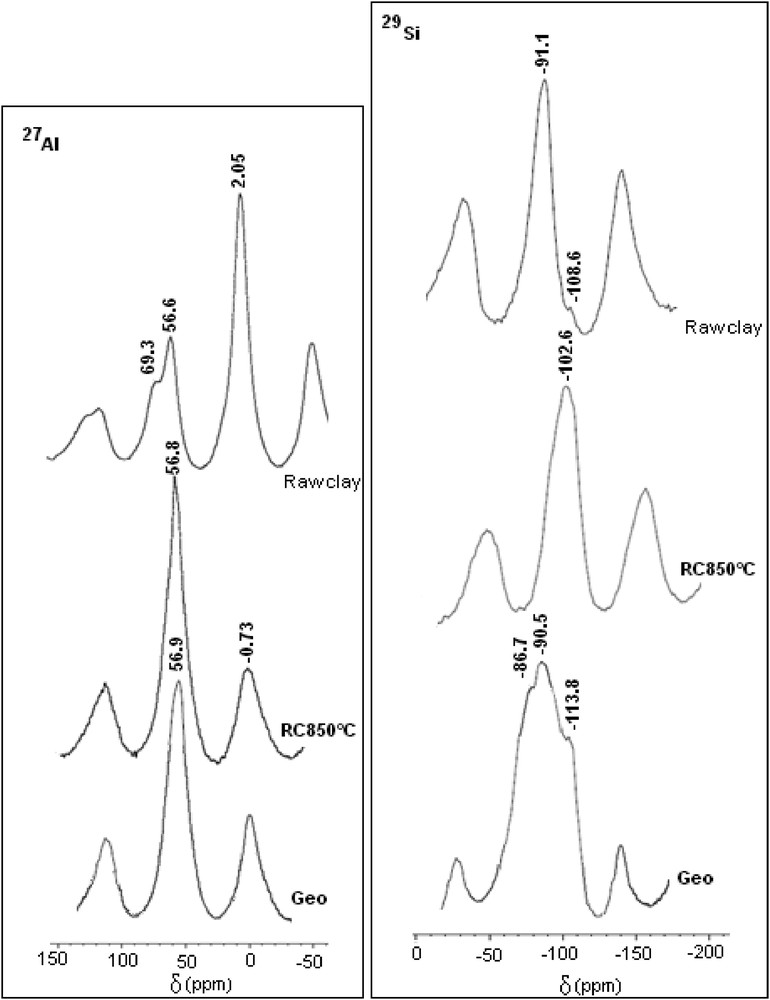
29Si and 27Al MAS NMR spectra of raw clay, calcined clay at 850° (RC 850 °C), and geopolymer using calcined clay at 850° (Geo).
However, on the basis of the best mechanical performance we found using the calcined clay and to prepare a geopolymer binder with low cost materials, the red clay was replaced by WB in the optimal condition. The geopolymer sample synthesized using WB as raw material, 8% of PG, and NaOH 14 M solution at the ratio of solid/liquid about 3 gave a compressive strength of hardened geopolymer binder of 32 MPa. This is a very interesting and promising result that can be compared with ordinary PC. This decrease in the compressive strength compared with the previous value is related to the chemical composition and the high crystallinity of the WB. Our finding confirms that WB and PG are very promising for the preparation of low cost geopolymer binders.
Table 2 summarizes the comparison of compression strength of our samples and various geopolymers produced from clay minerals and industrial wastes that were reported in previous studies. The comparison shows that our optimal samples have a higher mechanical strength than many of the other geopolymer cements. The best resistance is obtained using the metakaolinite, which is the best precursor for geopolymer production, although it is very expensive [27]. Furthermore, the variation in compression resistance can be attributed to the differences in experimental condition and the concentration of the activator.
Comparison of the compressive strength of geopolymer cements with different base materials.
Geopolymer-based materials | Compressive strength of geopolymer (Mpa) | References |
Cameroon clay | 37 | [9] |
Tabarka clay | 36.7 | [26] |
Analytical grade metakaolinite | 55 | [27] |
Medenine clay | 25 | [28] |
PG + fly ash + cement dust | 27 | [29] |
Clay + PG | 36 | This study |
WB + PG | 32 | This study |
5 Conclusions
In this study, iron-rich clay from Southern Tunisia heated at 850 °C was used for geopolymer preparation. Four mixtures of calcined clay and PG were investigated using three concentrations (10, 14, and 17 M) of NaOH. Improvement in the mechanical and microstructural properties of geopolymer was achieved, thanks to PG in the mixture. The best result was found for 8% of the PG and 14 M of NaOH. The compressive strength recorded was equal to 36 MPa. NMR study shows that all octahedral coordination was transformed to tetrahedral sites after geopolymerization reactions, which confirmed our results of the mechanical behavior. In optimum conditions, the calcined clay was replaced by WB. The geopolymer binder, in return, achieved a compressive strength 32 MPa. These results are very promising. Our findings foster the use of low cost materials (waste) like PG and WB for geopolymer binder preparation. These geopolymers can help in many construction fields and notably in several thermal insulation applications. In future studies, we seek to study in more details the strength of the geopolymers. We target to test fire resistance, the effect of chemical solution (acid attack, chloride attack, and sulfate attack) and permeability.
Acknowledgements
The authors would like to thank the National Centre of Research in Materials Sciences (CNRSM).