1. Introduction
Coated textiles emerge through the application of a polymer coating onto a textile substrate, resulting in a symbiotic fusion of materials.The different components of a coated textile are important for the overall properties of the final product [1, 2, 3, 4, 5, 6, 7]. The choice of polymer exerts a direct impact on the textile’s robustness, longevity, and suppleness, shaping its fundamental properties. Concurrently, the quantity of plasticizer integrated plays a pivotal role in determining the textile’s pliability. Additionally, the selection of filler material wields authority over the textile’s mass and volume, contributing to its structural profile [4, 5, 6, 7, 8]. The harmonious integration of these constituents culminates in the creation of a plastisol, achieved through meticulous blending. PVC-coated textiles are one of the most common types of coated textiles. Renowned for their economical nature and adaptability, PVC-coated textiles exhibit a remarkable resistance to moisture, chemicals, and wear-induced abrasion. These textiles usually comprise a tri-layered composition, as illustrated in Figure 1:

Different layers of PVC coated fabrics.
- A thin PVC superficial layer, called the skin layer or superficial layer, serves for aesthetic or technical enhancements.
- A PVC expanded layer (foamed layer) that functions as a sponge-like middle layer.
- A textile substrate layer composed of PET fabric, which imparts strength and durability to the material.
The different layers of a PVC-coated textile work together to provide the material with its desired properties [4, 5, 6, 7, 8, 9, 10]. This makes PVC-coated textiles a versatile material that can be used in a variety of applications, such as footwear, automobiles, floorcovering and wall coverings, upholstery, clothing, and many more. Tailoring the manufacturing process to suit the requirements of the final product, the polymeric layer is affixed directly (via direct coating) or indirectly (via transfer coating) onto one or both surfaces of the fabric [7, 8].
The polymer coating must adhere to the textile, and a doctor blade controls the thickness of the viscous polymer. The coated fabric is then heated and the polymer is cured (that is, polymerized). This is a non-reversible process, which means that it is impossible to recover plastisol from a PVC part after full fusion and complete curing has taken place [11].
The post-consumption disposal of PVC-coated fabrics as solid textile waste is an environmental pollution source that is becoming a serious problem recognized by society [11, 12]. Manufacturers and consumers of coated fabrics have suffered from the rise of this serious problem. Recycling of PVC-coated fabrics is a solution that can help to reduce the depletion of raw materials and energy, and eliminate or reduce waste [11, 12, 13, 14].
Numerous studies [15, 16, 17] have underscored the preference for mechanical recycling, particularly in managing identifiable PVC waste since it ensures the consistent quality of reclaimed PVC and mitigates the release of hazardous substances into the environment. However, despite these inherent benefits, a noticeable gap in available literature remains evident. Comprehensive data crucial for implementing large-scale recycling strategies tailored to PVC-coated fabrics is strikingly scarce, necessitating specialized approaches for recycling.
The challenges stem from the distinct properties of PET fabric and plasticizer PVC, encompassing differences in melting temperatures, densities, and hardness. As a result, conventional methods effective for pure PVC cannot be seamlessly applied to PVC-coated fabric waste. The amalgamation of PET fabric and plasticizer PVC during the recycling process compromises their original properties and practical utility. Consequently, the primary hurdle in recycling PVC-coated fabric waste lies in efficiently separating the PET fibers from plasticizer PVC [18]. By adopting circular principles, the conversion of PVC-coated fabric waste into powder expands the possibilities for recycling [19]. It can provide an alternative route to reutilize the material by incorporating it into new products or processes, thereby reducing the overall environmental impact of PVC waste. Nevertheless, the handling of powders can be challenging, particularly during processing, owing to the general presence of particles that are frequently non-spherical and exhibit diverse shapes. To be able to study the powder behavior properly, it is necessary to know the characteristics of the particles, as well as the powder as a whole.
Understanding the particle size distribution (PSD) in powder systems forms the bedrock of most manufacturing processes [20, 21, 22, 23]. Numerous studies [24, 25, 26, 27] have emphasized the significance of analyzing particle morphology to glean insights into powder behavior across processing stages—compaction, flow, and dissolution. Edward et al. [28] extensively investigated the impact of particle size and distribution on viscosity, especially concerning shear rate and time-dependent behavior. Their findings highlight that the presence of coarse particles significantly alters paste flow, reducing viscosity at low shear rates. Rasteiro et al.’s study [29] conducted a comparative analysis of various plastisol pastes, revealing higher viscosities and modulus values with smaller PVC particles. Additionally, Fischer et al. [30] emphasize the Gaussian distribution of PVC powder size and stress the need to narrow this distribution. Coarse fractions (>250 μm) led to dispersion defects, while fines (<60 μm) caused powder flow issues.
Rasteiro’s research [31] underlines how particle characteristics, particularly aggregate strength, significantly impact PVC plastisol paste rheology. The type of aggregates in PVC powder determines the particle size dynamics within the plastisol, directly influencing aging behavior and viscoelastic properties.
Similarly, Daniels [32] pointed out that optimizing the rheological behavior of plastisol relies on meticulous selection of the appropriate PVC distribution and shapes, as well as the type and quantity of plasticizer, since this distribution is based on two interactions. The first interaction occurs between the plasticizer and PVC particles [20]. An effective plasticizer should adeptly forge robust connections with the polymer. These connections wield influence over various aspects of the plastisol formulation—such as size, structure, distribution profile, and the agglomeration tendencies of the PVC particles. The second interaction, known as the inter-particulate PVC interaction, significantly impacts flow characteristics [33, 34]. Powders characterized by inadequate flow often stem from heightened interparticle interactions [35], originating from cohesive bonds between particles. Typically, elongated shapes like rods or needles, deviating from spherical forms, tend to exhibit inferior flow behavior [36].
Mehdipour et al. [21] highlight that an increase in K-value (indicative of molecular weight) correlates with heightened tensile strength and elongation but also amplifies defect occurrence due to reduced polymer chain mobility. Conversely, lower K-values lead to better spreading and homogeneous plastisol with weaker mechanical properties. Balancing defect mitigation and required mechanical properties is crucial in tailored coating pastes [1].
Marceneiro et al. [20] identified K-values ranging from 64 to 80 as optimal for automotive interiors and floorcoverings. Moreover, Pepperl [37] highlights how varying resin blends with diverse K-values can effectively attain desired product properties, particularly when the perfect resin is not accessible. This approach proves successful, as long as the discrepancy between K-values remains within a 10-unit range.
Other studies [3, 4, 5, 38, 39] have explored filler (calcium carbonate CaCO3) diameter and content impact on the mechanical properties of PVC foam layers in coated textiles. Stambouli et al. [5] observed negative structural impacts with excessive CaCO3 content (100 parts filler to 100 parts pure PVC resin) but noted that smaller filler particle diameters improve mechanical properties.
While prior research has delved into the rheological properties of plastisol and its impact on the mechanical characteristics of PVC-coated fabrics, the valorization of PVC-coated fabric waste through incorporation into the plastisol formula, following its conversion into powder and separation from the textile substrate, as a replacement for PVC resin, has yet to be explored.
This study is dedicated to advancing current knowledge by pioneering a specialized mechanical process tailored to convert PVC-coated fabric waste into distinct PVC powder, effectively separated from PET fibers. The primary goal is to not only develop this process but also delve deeper into the characteristics of the derived PVC powders, meticulously examining particle morphology and size distribution.
Within this research scope, our strategic direction was carefully chosen following extensive consultations with the company’s leadership. Our focus lies within the domain of floorcoverings, aiming to integrate this repurposed PVC material into the plastisol formula, replacing the traditional PVC resin. This substitution aims to create a floorcovering article that embodies sustainability without compromising quality. The core of our endeavor revolves around investigating how the recycled PVC content and particle size influence crucial mechanical properties such as Break Strength (BS), Elongation at Rupture (ER), and Tear Resistance (TR) of the expanded layer, essential in floorcovering production.
2. Materials and methods
2.1. Raw materials
For articles intended for floorcovering, the formulations used to produce PVC sheets (surface and expanded layers) are shown in Table 1. The different ingredients were kindly provided by the PLASTISS company (Sayada, Monastir, Tunisia).
Superficial and expanded layer formulations
Layer | PVC resin (g) | Plasticizer (g) | Stabilizer (g) | Calcium carbonate (g) | Kicker (g) | Azodicarbonamide (g) |
---|---|---|---|---|---|---|
Superficial | 100 | 80 | 1.5 | 25 | - | - |
Expanded | 75 | 50 | - | 50 | 2 | 4 |
The plastisol formulation relies on ingredient proportions, measured in parts per hundred of resin (phr). In the superficial layer, 100 parts of PVC resin (with particles sized at 100 μm and a K-value of 66) are combined with 80 parts of plasticizer (DINP), 25 parts of filler (CaCO3), and 1.5 parts of stabilizers (Ca/Zn). Conversely, the expanded layer presents a distinct composition, integrating a chemical blowing agent (azodicarbonamide) and a kicker expansion accelerator (potassium–zinc K/Zn), both pivotal in shaping the foam structure. These elements undergo meticulous blending using a mechanical stirrer to ensure homogeneity, meeting the company’s specified viscosity standards. At PLASTISS, the targeted viscosity for the surface layer stands at around 27,000 (±900) Pa⋅s, while the expanded layer aims for 25,000 (±500) Pa⋅s.
2.2. Preparation of PVC-coated fabric
To prepare the samples, we used the lab-coaters method that operate discontinuously. Samples with a maximum size of DIN A 4 can be produced with this method because such a machine is only the size of a common stove. But it enables us to get a first idea and to give a general statement regarding the raw material and its temperature reaction [4, 5, 6].
We used the transfer coating technique for the production of PVC-coated textiles. On the first coating head, the plastisol is spread on the transfer paper using a blade while controlling the thickness (Figure 2a). The formed layer, superficial layer, is then dried at 140 °C for 20 s and cooled. On the second coating head, the plastisol is spread on the first formed layer using a blade at a given thickness. This second layer forms a foam after being dried at 200 °C for 80 s and is called the expanded layer (Figure 2b). Later, the textile substrate layer is laminated to the resulting PVC layers (Figure 2c), and the complex thus formed is passed through the main furnace where gelling and expansion of the cellular plastisol take place. After cooling, the paper and the formed PVC-coated textile are detached and rolled up separately (Figure 2d).
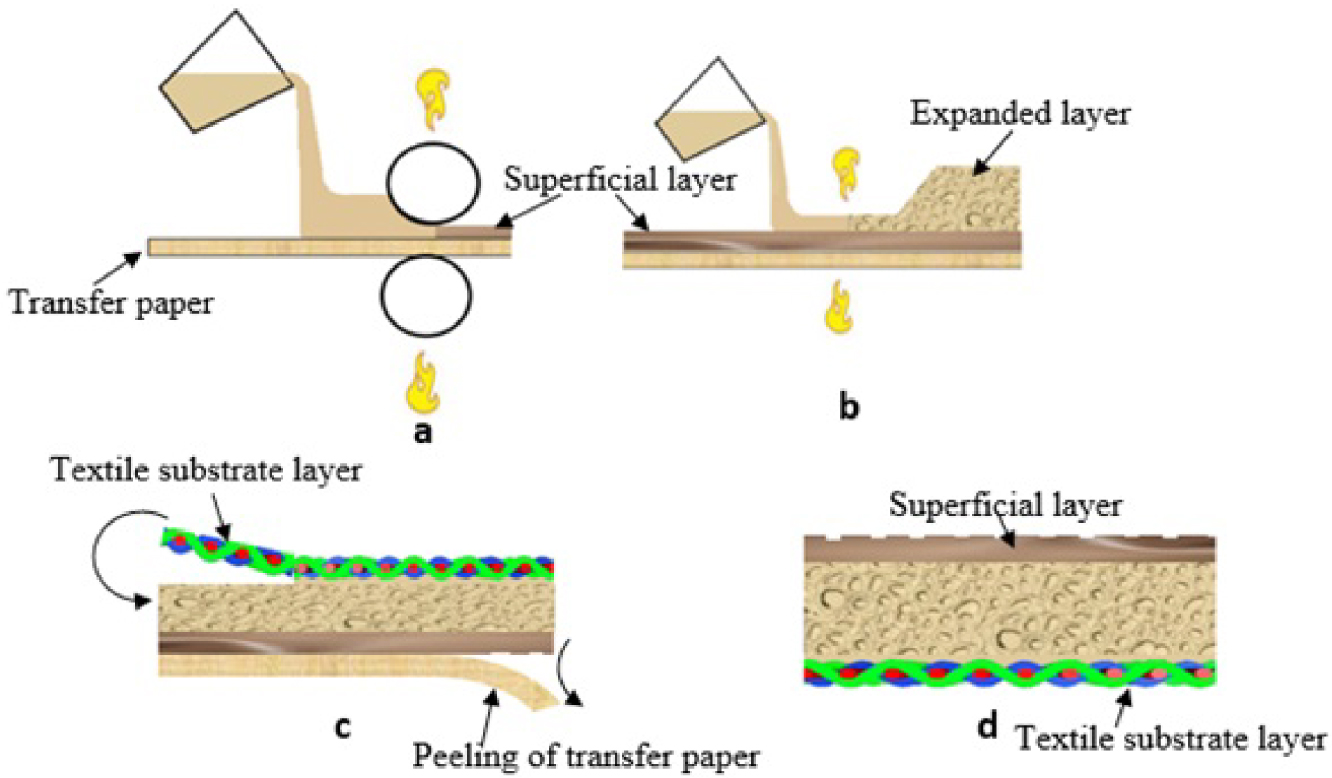
Depicts a typical coating process.
2.3. SMF plastic pulverizer
Carthage Plastique company’s pulverizer (Kaala Seghira, Soussa, Tunisia) was used during this study. The plastic pulverizer machine is chiefly designed to grind PVC and fibers in micronized form. This pulverizer uses a high-speed rotor. This rotor, consisting of several sections of discs and several blades, is responsible for grinding PVC waste into a fine powder. Its output can reach 70–350 kg/h (20–120 mesh). In this process, the utilization of a vibrating sieve is crucial to ensure the desired output size. The vibrating sieve comprises two outlets: the fine powder outlet “7” and the coarse powder outlet “6” (Figure 3). The fine particles that successfully pass through the sieve mesh are collected at the fine powder outlet “7”. On the other hand, the coarse powders that are retained by the sieve are directed to the milling chamber for further grinding, utilizing the coarse powder outlet “6”.
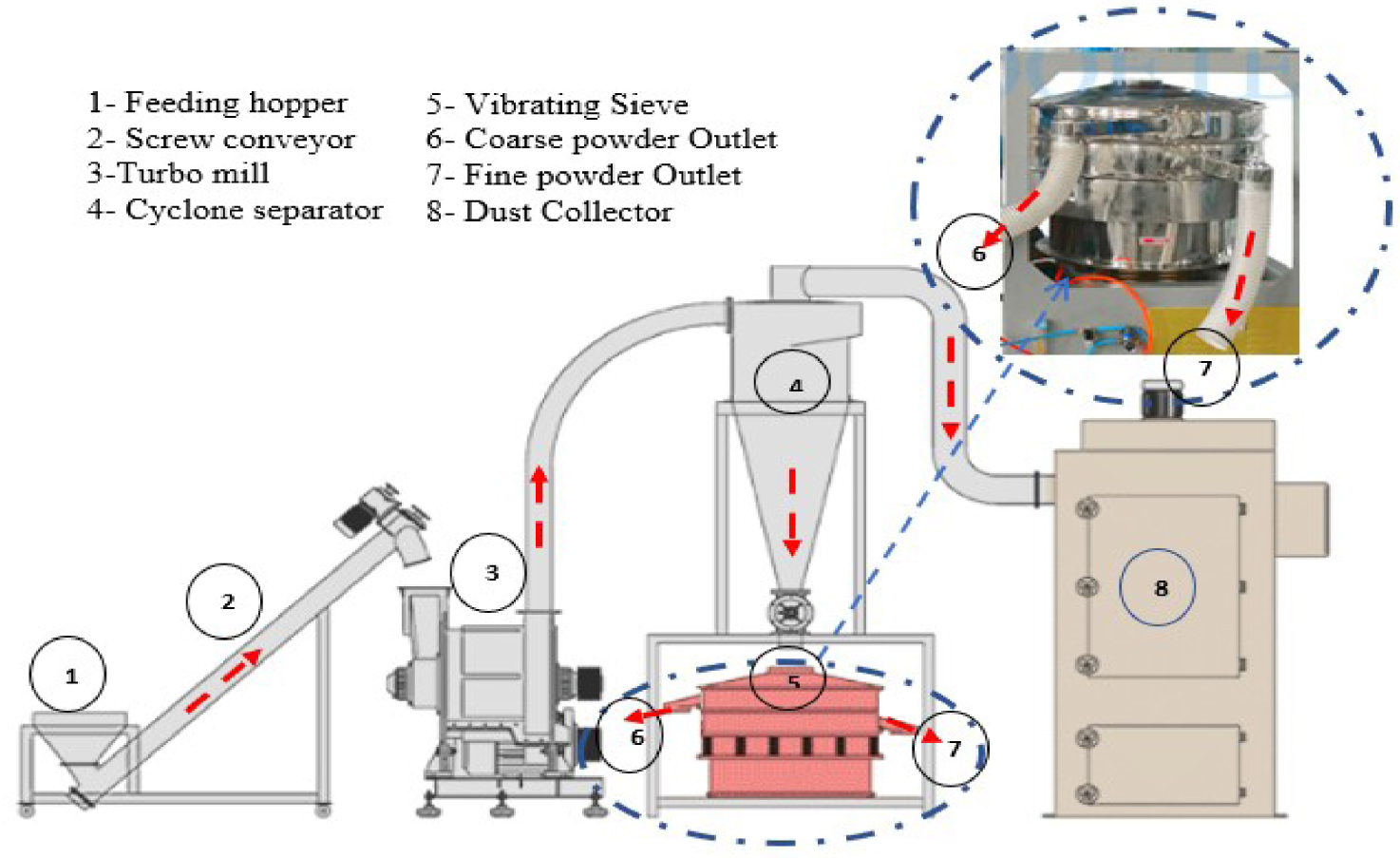
Plastic Pulverizer.
Regarding the PVC-coated fabric scraps, the fine powder particles are directed through the vibrating sieve with the assistance of air flow and collected in the product collector located at the fine powder outlet “7”, designated as outlet P. However, the PET fibers, which are retained by the sieve, are vacuumed and subsequently recovered in a cloth bag connected to the coarse powder outlet “6”, identified as outlet F (Figure 4).
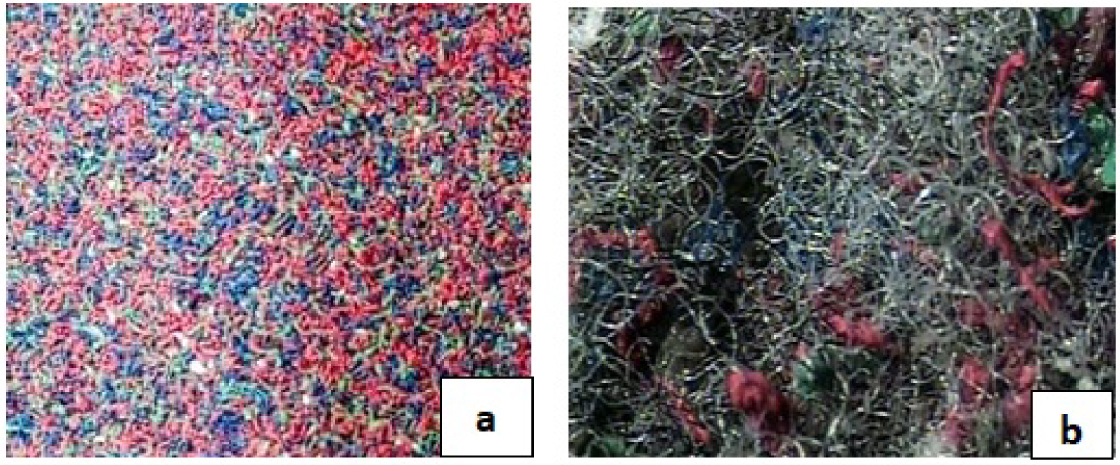
Pulverizer outlets: (a) Recovered PVC powders (outlet P). (b) Recovered fibers (outlet F).
2.4. Desirability function
The desirability function approach is one of the most widely used methods in industry for the optimization of multiple-response processes [40]. For each response Yi(x), a desirability function di(Yi(x)) assigns numbers between 0 and 1 to the possible values of Yi [40, 41, 42, 43, 44, 45].
Different functions may be built, depending on the optimization criteria adopted, within an acceptable range of response values given by (Ui − Li), where Ui is the upper acceptable value for the response and Li is the lower. Thus, if the response has to be maximized, di(Yi(x)) is described by the following equation [43, 44, 45]:
(1) |
When it has to be minimized, the equation for di(Yi) is [43, 44, 45]:
(2) |
Finally, when a target value Ti (with Li⩽Ti⩽Ui) is the most desirable response, the function is given by [43, 44, 45]:
(3) |
The overall desirability function D is defined as the geometric average of the individual desirability functions of each response di(Yi):
(4) |
The weighting coefficients (ri) are used to emphasize certain parameters over others, depending on their significance in determining the overall quality [43, 44, 45].
2.5. Test sieves shaker
Machine sieving is carried out by stacking the sieves in ascending order of aperture size and placing the powder on the top sieve.
Results are usually expressed in the form of a cumulative percentage of the nominal sieve aperture. The sieves used for the analyses are RETSCH standard sieves.
A sample (100 g) of the powder is placed on the top sieve. This sieve set, containing openings of various sizes (1, 0.8, 0.6, 0.4, 0.3, 0.2, 0.09, 0.02 mm), is fixed to the mechanical shaker apparatus and shaken (amplitude 1.2 mm) for 20 min. The powder retained on each sieve is weighed. Then, the loss of mass was monitored every 1 min by measuring the weight until no significant change was detected (less than 0.1% of the total feed) between two consecutives measurements. After the sieving process, the data are evaluated, the sample material is recovered and the sieves are thoroughly cleaned.
2.6. Tensile and elongation tests
Tensile and elongation tests have been carried out according to NF EN ISO 1421-2017 standards utilizing a testing machine (Zwich GmbH, Ulm, Germany) with a crosshead speed of 100 mm/min. Test specimens had dimensions of 50 mm ± 0.5 in width with a sufficient length to obtain a distance of 200 mm ± 1 between the jaws of the testing machine. For the reproducibility of the results, the test was replicated three times.
2.7. Tearing strength
Tearing strength test has been performed according to NF EN ISO 4674-1-2017 using an ELMENDORF dechirometer. Tests have been run in triplicate to avoid experimental error.
2.8. Optical microscopy
Morphology and structure of the expanded PVC layers have been observed using Leica DM 500 optical microscope equipped with different objectives connected to a camera and controlled by analysis software. The materials have been observed in reflected light under different magnifications of the objective.
To ensure accurate characterization of the particle images, it was necessary to utilize magnification and numerical aperture settings that provided sufficient resolution. The magnification factors employed ranged from 6.3× to 40×, with the commonly used eyepieces typically set at 10×–40×.
3. Results and discussion
3.1. Mechanical recycling process
3.1.1. Grinding process of PVC-coated fabric scraps
The process of obtaining PVC powder from PVC-coated fabric scraps involves several stages of cutting and grinding. Initially, the waste PVC-coated PET fabric is cut into small pieces using a band saw, ensuring that their dimensions are suitable for the subsequent steps and equipment, with a maximum dimension of 1 m2.
Subsequently, a first grinding process is conducted using a plastic waste grinder machine to crush the PVC-coated fabric component and generate a bulk mixture, typically ranging between 10 and 15 mm in size. During this stage, the PVC remains combined with the PET knit, and they are not yet separated from each other.
Next, a second grinding process is employed using a pulverizer. This process further shreds the plasticized PVC component, resulting in the production of fine PVC powders that are effectively separated from the PET fabric. An additional advantage of this grinding process, particularly with the involvement of a pulverizer, is its capability to not only grind the coated fabric scraps into PVC powder but also to separate them from PET fibers.
The following section presents a comprehensive quantitative analysis conducted to investigate the effectiveness of separation between PET fibers and PVC powder.
3.1.2. Quantitative analyses using chemical separation
To determine the average weights of PET fibers and plasticized PVC in each outlet (PVC powder outlet P and fiber outlet F) after pulverization, the chemical separation method, which involves solubilizing the PVC in Tetrahydrofuran (THF), was employed [46]. To ensure accuracy, the experiments were conducted three times.
According to the chemical separation results (Table 2), the quantity recovered from outlet P primarily comprises PVC powder, accounting for approximately 92%. On the other hand, outlet F contains a percentage of residual PVC, reaching 25.08%, while the quantity of PET fibers amounts to approximately 72%.
Different amounts of PET fibers and PVC powder after pulverizations
![]() |
CV: Coefficient of variation.
Therefore, it can be concluded that the separation between PET fibers and the PVC powder recovered from both pulverized outlets (outlet P and outlet F) is not perfect, even though the PET fibers’ percentage in the powder does not exceed 6.15% for outlet P. The presence of PVC alongside PET fibers significantly compromises the quality of the recycled material due to the distinct properties of these two components. Consequently, the grinding process alone is insufficient for reusing PVC-coated fabric scraps.
3.1.3. Sieving separation
To achieve complete separation between PVC powder and PET fibers, a supplementary mechanical sieving using a 1 mm aperture sieve was implemented. This efficient separation was corroborated by the chemical analysis, which demonstrated that approximately 90% of the PVC powders were successfully recovered through sieving, while all the PET fibers were retained by the sieve. These results provide strong evidence of achieving a complete separation of PVC powder (Figure 5).
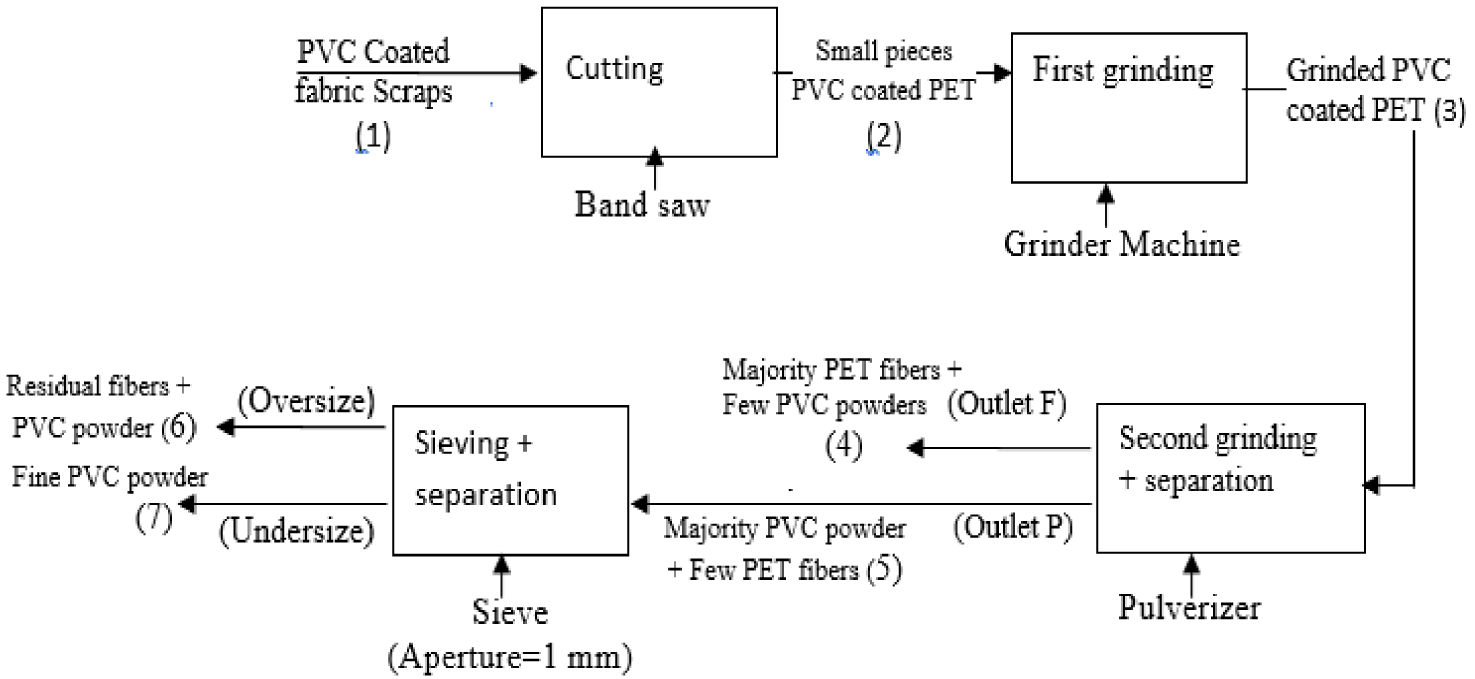
Process map of grinding supplemented by sieving.
The combination of the mechanical process (cutting, grinding, pulverization) along with sieving (Figure 5) proves to be a straightforward, cost-effective, environmentally friendly, and potentially profitable approach.
The results obtained compellingly substantiate mechanical recycling as a practical methodology for safeguarding the intrinsic value of PVC-coated fabric, while simultaneously upholding the material’s chemical structure and compositional integrity (especially the K-value of PVC).
3.2. Particle morphology of recycled PVC powders
3.2.1. Particle shape
Particle shape influences the bulk properties of powders, such as flow behavior and the viscosity of suspensions [33, 34, 47]. Through initial microscopic observations, a clear differentiation among various non-spherical particle shapes was achieved, as depicted in Figure 6.
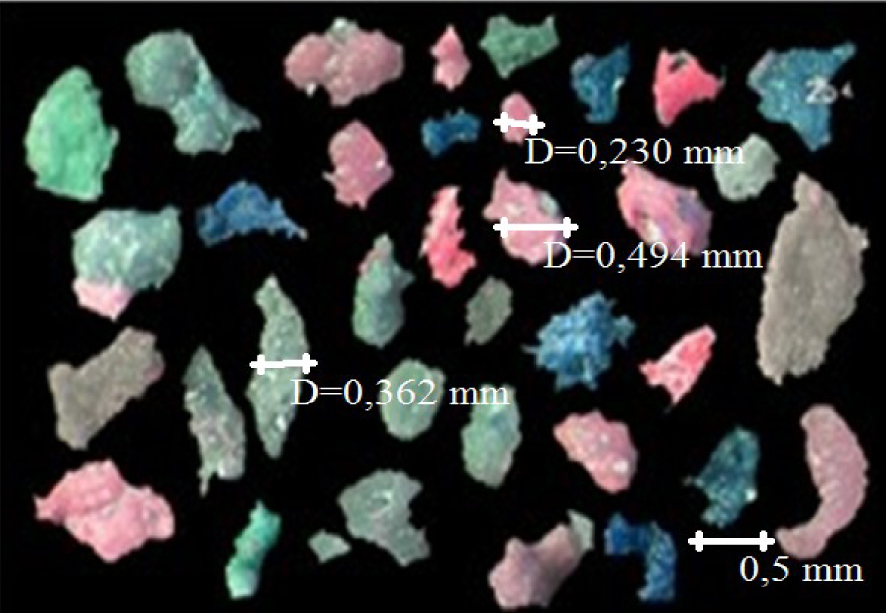
Particle images acquired by optical microscopy (magnification 10×).
As stated by Hamilton [27], powders comprising flat and elongated particles frequently display elevated porosity and reduced flow characteristics due to heightened inter-particle friction, leading to the development of shear surfaces. Consequently, as highlighted in previous studies [20, 21, 22, 23, 24, 25], powders exhibiting inadequate flow properties are susceptible to cluster formation, hindering the effective dispersion of these powders.
3.2.2. Particle size distribution
Understanding the distribution of particle sizes across different dimensions [24, 26] is of crucial importance. Firstly, these characteristics exert substantial influence over the physical behavior of the powder, particularly affecting its flowability—a crucial factor that signifies the powder’s ability to move uniformly and consistently. Simultaneously, the impact of PVC particle distribution extends beyond the rheological properties of plastisols, playing a pivotal role in establishing the necessary processing conditions to achieve the desired characteristics in the final product [29].
Sieve analysis stands as a traditional and extensively employed technique for particle size determination. In this method, the sieves are weighed empty and then with the oversize PVC particles after the sieving process. The difference between these measurements represents the weight of the individual fractions. The PSD was measured in triplicate and is reported in Table 3.
Summary for particle size distribution (PSD) study
Sieve size (mm) | 1 | 0.8 | 0.6 | 0.4 | 0.3 | 0.2 | 0.09 | 0.02 | Pan | Total |
---|---|---|---|---|---|---|---|---|---|---|
Average | 0 | 0.4 | 3.2 | 23.7 | 32.8 | 26.6 | 12.65 | 0.25 | 0 | 99.6 |
CV% | 0 | 10 | 9.75 | 1.98 | 2.47 | 2.85 | 2.87 | 14.42 | 0 | |
Cum. Weight retained | 0 | 0.4 | 3.6 | 27.3 | 60.1 | 86.7 | 99.35 | 99.6 | 99.6 | |
%Weight retained | 0 | 0.40 | 3.21 | 23.80 | 32.93 | 26.71 | 12.7 | 0.25 | 0 | |
% Retained | 0 | 0.40 | 3.61 | 27.41 | 60.34 | 87.05 | 99.75 | 100 | 100 | |
% Finer | 100 | 99.6 | 96.39 | 72.59 | 39.66 | 12.95 | 0.25 | 0 | 0.00 |
Table 3 offers a comprehensive overview of a PSD analysis via the sieving process. It encompasses multiple essential elements crucial for characterizing the PSD, including individual and cumulative percentages. By graphically depicting these two integral components, a coherent and structured portrayal of the PSD study is achieved, enhancing clarity and facilitating interpretation.
These graphs (see Figure 7) offer a rapid and intuitive means to comprehend the distribution of particle sizes within the sample. They facilitate the discernment of underlying trends and the derivation of overarching conclusions regarding the particle size characteristics as a whole.
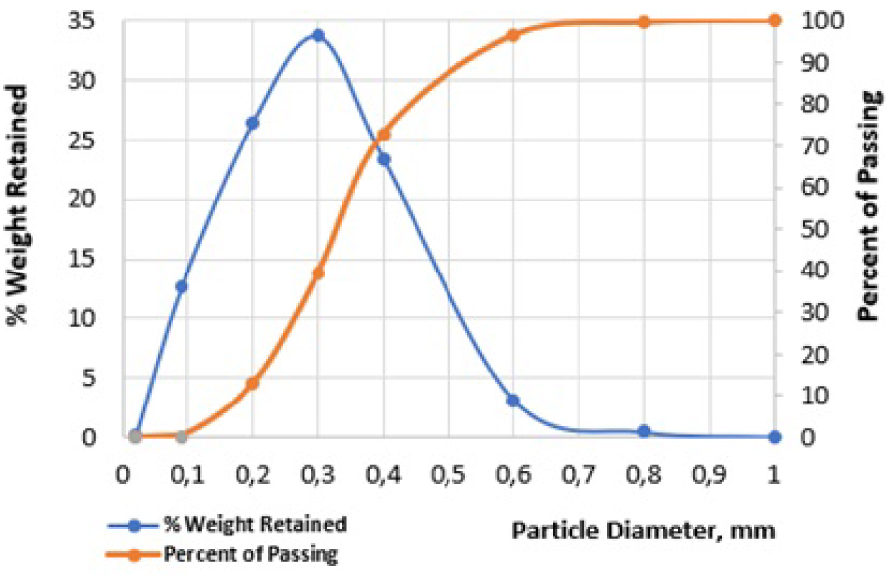
Frequency distribution curve and Cumulative distribution curve.
The individual percentages (weight retained) denote the proportion of particles retained at each specific sieve aperture. By analyzing these percentages, one can glean profound insights into the size distribution across different sieve openings. As illustrated in Figure 7, the preeminent percentages are evident for values such as 0.2, 0.3, and 0.4 mm. This observation signifies that the majority of particles possess sizes falling between these values, with respective proportions of 26.71%, 32.93%, and 23.80%.
The cumulative distribution curve (percent of passing) is obtained by adding up the individual fractions and interpolating between the points of measurement (Figure 7). The cumulative percentages provide a broader perspective on the overall PSD within the sample. They indicate the total percentage of particles retained up to a specific sieve aperture, enabling a comprehensive assessment of the particle distribution across various sizes within the entire sample. Figure 7 shows that the majority of particles are smaller than 600 μm, representing 96.39% of the total. The greatest fraction (83.44%) is in the size range between 200 and 600 μm.
3.3. Quality characterization of the floorcovering product
3.3.1. Parameter selection
In this study, we aim to comprehensively characterize the quality of floorcovering products by assessing various properties that determine their performance and user satisfaction. To achieve this, we have gathered valuable information from client requirements and specifications, and collaborated closely with PLASTISS company executives. Through this collective effort, we have successfully identified the essential properties that define the specific PVC-coated fabric used for floorcoverings. Among these distinctive requirements, the mechanical facets hold paramount significance, with a particular focus on pivotal parameters like BS, ER, and TR. As we advance toward the incorporation of recycled PVC powder as a sustainable alternative to conventional PVC resin for the fabrication of floorcoverings, it is imperative to maintain the same high-quality standards expected from this finished product. Therefore, particular attention will initially be devoted to preserving the quality of the expanded layer after incorporating the recycled PVC powder. The surface layer, which is more demanding in terms of mechanical properties, will retain the same standard recipe.
3.3.2. Upper and lower limits for each parameter
In order to convert product quality parameters to a common scale, the upper and lower limits of each parameter must be identified. The lower and upper limit useful for the product quality parameters are based on the experimental results, the theoretical knowledge and the opinion of the experts who participated in the survey. For the experimental study, 20 samples of the expanded layer were produced using the standard PLASTISS formulation. Subsequently, various mechanical tests (BS, ER, and TR) were conducted. Among the results obtained, the smallest value was considered as the minimum threshold, while the average value was considered as the target value. The results found are illustrated in Table 4.
Classification of expanded layer
Parameters | Minimum value | Target value | Maximum value |
---|---|---|---|
Break strength (N) | 15 | 20 | - |
Elongation at rupture (%) | 75 | 100–125 | 150 |
Tear resistance (N) | 0.5 | 0.8 | - |
Upon reviewing Table 4, it becomes evident that the expanded layer’s ER must fall within the range of 75% to 150% for optimal performance. Striking a balance is crucial, as excessive flexibility could undermine the quality of the final product. Our target values for this parameter are set between 100 and 125%. On the contrary, both BS and TR are parameters that warrant maximization. We establish 15 N as the minimum acceptable value for BS and 0.5 N as the minimum acceptable value for TR. By adhering to these guidelines, we can ensure the enhanced quality and durability of the end product.
3.3.3. Desirability functions for individual parameters
Figure 8 visually illustrates the desirability functions for each parameter, namely BS, TR, and ER. These functions provide a comprehensive understanding of how each parameter performs in relation to its ideal value. By incorporating the desirability function, we can make informed decisions, striking an optimal balance between the different parameters to achieve an overall high-quality product.
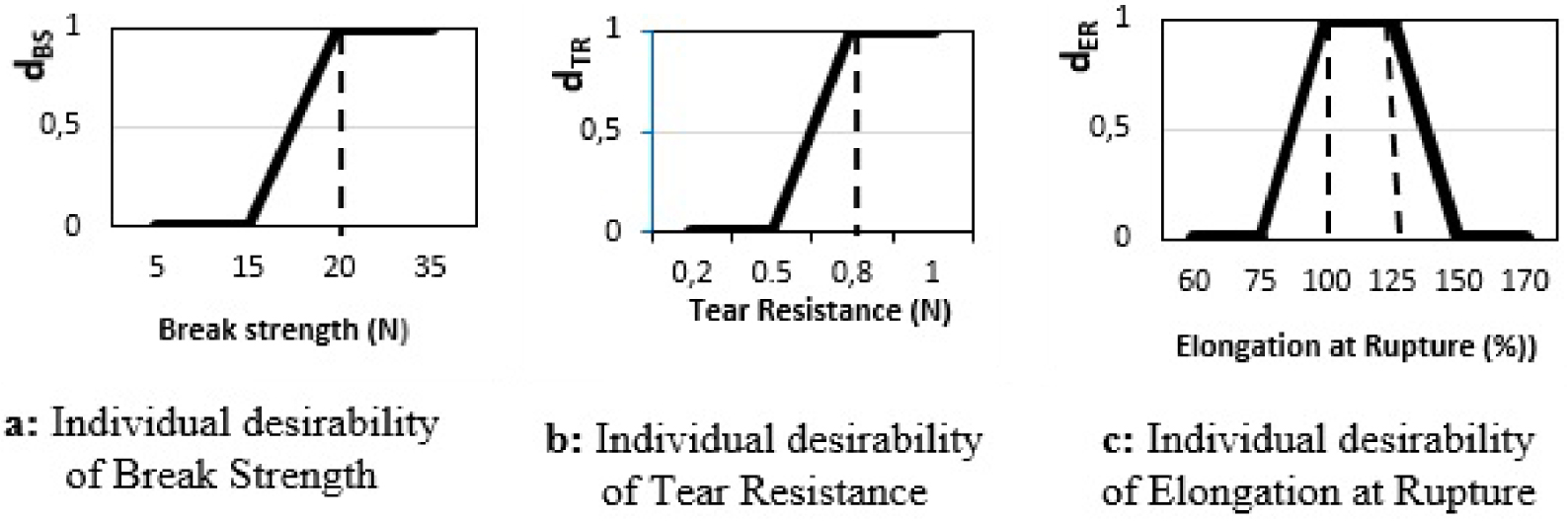
Graphical representation of Individual desirability functions.
3.3.4. Weighting coefficients
In order to assess the importance of attaining the target value, a comprehensive weighting scale should be implemented [44]. According to Candioti [45], the importance, established by the analyst, may vary from 1 for the least important variable to 5 for the most important one.
This research, carried out at PLASTISS, greatly benefited from the invaluable expertise of the company’s specialists who meticulously assigned these weightings. Notably, they placed particular emphasis on two vital factors: BS and TR, ranking these aspects above ER. Table 5 summarizes the weights assigned to the various properties of the expanded layer.
Assignment of weights to the various properties studied
Properties | Weights (ri) |
---|---|
Break strength (N) | 5 |
Elongation at rupture (%) | 3 |
Tear resistance (N) | 5 |
3.3.5. The overall desirability function D
In order to identify the most high-performing product, we have established specific criteria, drawing on the valuable insights of PLASTISS experts:
denotes unacceptable product quality (rejected product).
indicates a considerable deviation from the target value of 1, suggesting one or more properties in need of improvement (can be accepted as Second-quality article).
can be accepted as First-quality article.
signals Premium quality product.
The D value closest to 1 reflects the utmost desirability in terms of quality.
By adhering to these well-considered conditions, we can effectively identify and promote the most desirable products in our evaluations.
3.4. Reuse of recycled PVC to produce floorcovering products
The cumulative distribution curve shown in Figure 7 is used for this initial study.
3.4.1. Preparation of expanded layer formulations
In order to uphold the exacting standards requisite for the final product’s quality and achieve a consistent benchmark across all floorcovering articles, it is imperative that we maintain specific properties of the expanded layer. These properties, including viscosity (25,000 ± 500 Pa⋅s) and thickness (1.5 mm), play a pivotal role in ensuring the desired performance and characteristics of the end product.
The formulations used to produce the expanded layers are presented in Table 1. All ingredients were thoroughly blended using a mechanical stirrer until achieving a homogeneous mixture with the targeted viscosity of 25,000 (±500) Pa⋅s.
The optimization process will focus on the formulation of the expanded layer, involving variations in the quantity of recycled PVC particles (5, 15, 25, 35 and 45 g).
However, incorporating recycled PVC particles into the expanded layer’s formulation results in a decrease in viscosity. The viscosity of the plastisol is primarily influenced by the plasticizer content [24]. Consequently, to attain the desired viscosity level of approximately 25,000 (±500) Pa⋅s, which facilitates effortless handling of the mixture, adjustments to the plasticizer content (z) is necessary when increasing the proportion of recycled PVC particles (x) in the expanded layer’s composition. In fact, the quantity of recycled PVC particles is directly correlated with the quantity of plasticizer required to maintain the desired viscosity. Table 6 summarizes the various tests carried out.
Expanded layer formulations
Test | PVC (g) | Plasticizer (z) (g) | Calcium carbonate (g) | Kicker (g) | Azodicarbonamide (g) | |
---|---|---|---|---|---|---|
Recycled PVC (x) | PVC resin (y) | |||||
Test 1 | 0 | 75 | 50 | 50 | 2 | 4 |
Test 2 | 5 | 70 | 50 | 50 | 2 | 4 |
Test 3 | 15 | 60 | 55 | 50 | 2 | 4 |
Test 4 | 25 | 50 | 60 | 50 | 2 | 4 |
Test 5 | 35 | 40 | 70 | 50 | 2 | 4 |
Test 6 | 45 | 30 | 80 | 50 | 2 | 4 |
When 5 g of recycled PVC (equivalent to 6,67% of the total PVC added) was added (Test 2), the amount of plasticizer needed to maintain a viscosity of 25,000 (±500) Pa⋅s was the same as Test 1 (50 g). However, upon introducing quantities exceeding 15 g of recycled PVC, a progressive augmentation of plasticizer amount by 5 g was noted. This incremental rise escalated to 10 g as the recycled PVC quantity reached 35 g (46.67% of the total PVC).
The increase in the plasticizer quantity can be attributed to the insufficient flowability of the recycled PVC powder, which emanates from the distinctive shape and dimensions of its particles, hindering smooth movement [20]. These findings are confirmed by Daniels [32], who proves that plastisols inadequately dispersed often exhibit agglomerated resin particles, leading to higher-than-anticipated viscosities due to robust interactions among the PVC particles.
These interpretations align with microscopic observations (Figure 6) that unveiled the presence of flattened and elongated particles within the powder, leading to pronounced porosity and restricted flowability due to heightened inter-particle friction.
The same phenomenon was observed by Stambouli et al. [5], who showed that an excessive quantity of CaCO3 (100 parts filler to 100 parts pure PVC resin) led to insufficient dispersion within the plastisol, thereby compromising the adhesion between the PVC matrix and the filler.
3.4.2. The effect of recycled PVC content
3.4.2.1. Using microscopic observation
The microscopic images presented in Figure 9 offer valuable insights into the impact of recycled PVC on the foam structure of the expanded layer.
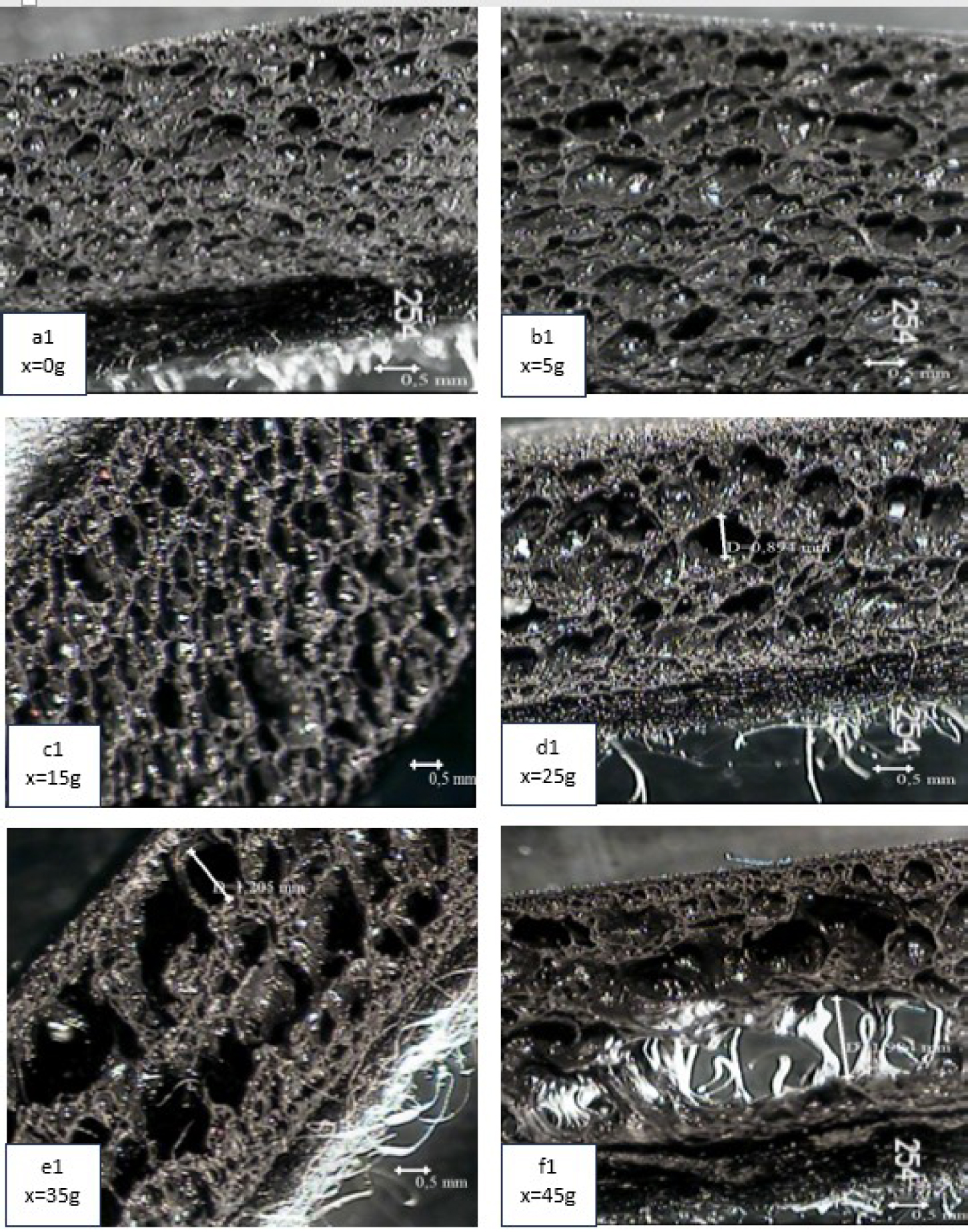
Effect of recycled PVC content on the structural properties of the expanded layer: (a) without recycled PVC; (b) with 5 g; (c) with 15 g; (d) with 25 g; (e) with 35 g; (f) with 45 g. (Magnification 6.3×).
Figure 9a illustrates the cross-section of expanded layer prepared at optimum conditions (without recycled PVC), displaying a sponge-like micropore structure characterized by uniform bubbles. These bubbles form through two key stages of the foaming process: bubble nucleation and growth [8, 9].
As the quantity of recycled PVC increases, noteworthy changes occur within the foam. The bubbles grow larger, and the structural integrity begins to suffer. Notably, when the recycled PVC reaches 35 g, the foam structure experiences significant degradation, which worsens with 45 g, revealing the emergence of micro defects such as inclusions, microcracks, macropores, etc [37]. This degradation can be attributed to the inadequate dispersion of the recycled PVC within the plastisol, which leads to poor adhesion. Moreover, excessive amounts of recycled PVC tend to clump together to form clusters that prove challenging to adequately incorporate into the plastisol. These clusters induce heterogeneities and non-uniform stress transfer within the plastisol, which lead to the formation of defects, notably microvoids and cracks (Figure 9e,f).
Interestingly, these findings corroborate the observations of various independent studies [24, 25, 26, 27, 28, 37, 40]. As a result, it is unfortunate that an excess of recycled PVC will not yield the desired dispersion within the foam structure, despite employing a highly effective mixing technique in PLASTISS.
3.4.2.2. Using mechanical properties
Figure 10 illustrates the results of BS (N), TR (N) and ER (%) measurements for expanded layer samples at different amounts of recycled PVC.
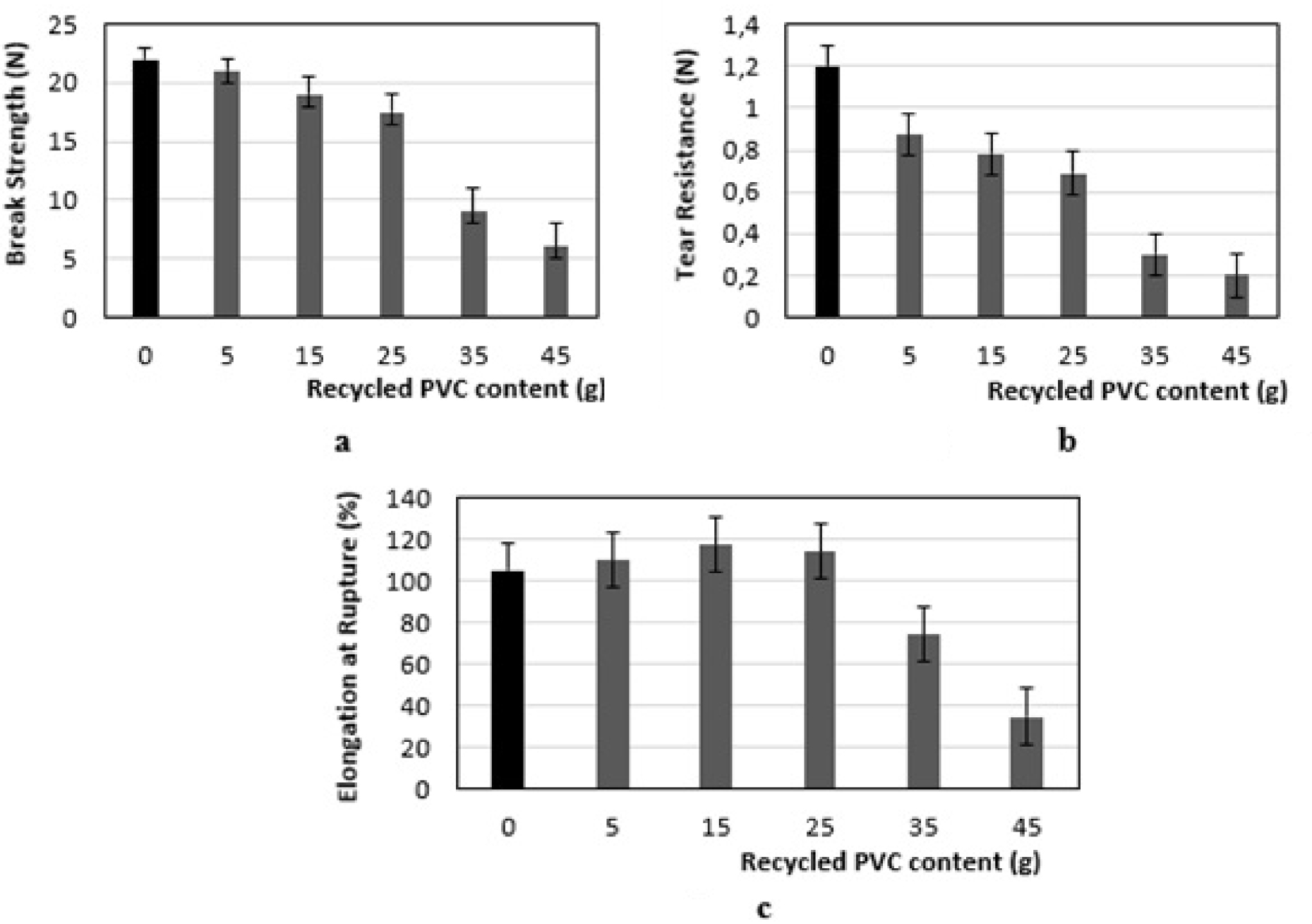
Effect of Recycled PVC content on the mechanical properties of PVC expanded layer (a) Break Strength (N), (b) Tear Resistance (N), (c) Elongation at Rupture (%). Black scale bar: without recycled PVC and representing the reference value (at 100%) to compare the evolution after incorporation of recycled PVC.
Black scale bar: without recycled PVC and representing the reference value (at 100%) to compare the evolution after incorporation of recycled PVC.
The mechanical results demonstrate that adding a quantity of recycled PVC not exceeding 25 g (33.34%) leads to a tolerable decrease in BS (17.5 N, which represents 79.5% of reference without recycled PVC) and TR (0.69N, which represents 57.5%) since these values remain within acceptable ranges and exceed the minimum required values (15N for BS and 0.5N for TR). However, a slight increase in ER was observed for the samples with 15 g (20%), and 25 g (33.34%) of recycled PVC. This slight increase could be attributed to the additional plasticizer amount, which enhances flexibility and elasticity by affecting the polymer’s initial structure [26].
These mechanical properties, however, deteriorate rapidly as the added quantity of recycled PVC exceeds 25 g (Figure 10). More critical, when the amount of recycled PVC reaches 45 g (60%), all three mechanical properties drop dramatically, recording very low values of 6 N (27.3%), 0.2 N (16.7%) and 35% (33.3%), respectively, for BS, TR and ER.
Saffert [11] proved the same point when he used PVC particles inseparable from the textile backing after grinding the tarpaulins. This ground material was used as a “filler” in plastisol. The results revealed a rapid deterioration in the mechanical properties of the resulting plastisolized PVC as the proportion of regrind increased. Even with a ratio of 10 parts regrind to 100 parts virgin material, tear strength decreased by around 10%.
These results perfectly align with the microscopic observations (Figure 9), which clearly reveal the presence of microvoids and cracks, particularly in the sample with 45 g of recycled PVC. These defects weaken the material and make it more susceptible to failure.
3.4.3. Overall desirability function D
In the context of this study, the overall desirability function was used to determine the maximum amount of recycled PVC that could be used in the plastisol formulation while still meeting the quality requirements of the floorcovering application.
These requirements include the BS (dBS), TR (dTR) and ER (dER) of this floorcovering application. The overall desirability for each sample is shown in Table 7.
Based on the findings presented in Table 7, only expanded layers P2 and P3 successfully adhere to the established criteria for acceptable quality (with D > 0.5). Notably, the assessment of the P4 sample reveals its alignment with predetermined limit of acceptability as a second-quality article. These deductions gain additional validation through meticulous evaluation carried out by experts hailing from the esteemed PLASTISS company, renowned for their profound proficiency within the floorcovering industry. The study’s outcomes incontrovertibly demonstrate that the optimal quantity of recycled PVC particles within a plastisol formulation, while upholding exacting quality requisites, stands at 15 g (equivalent to 20% of the total PVC added). This determination arises from the intricate interplay between the morphology of the recycled PVC particles, encompassing both their configuration and size distribution, and the resulting quality of the end product.
These mechanical results are in good agreement with previous work by Syabanı et al. [22] who highlighted that internal defects, such as micropores, can significantly compromise the product’s integrity, leading to damage, fractures, and failures. Therefore, coating pastes necessitate specific rheological properties to ensure optimal performance. This finding is confirmed by additional studies [1, 10, 37, 48, 49], which corroborate that the enhancements in the mechanical properties of PVC-coated fabric stemmed from the enhanced fluidity of PVC resin and the increased homogeneity of plastisol during the mixing of PVC resin.
3.5. Optimization
The results attained have already highlighted the substantial influence of both the quantity and size distribution of recycled PVC particles on the eventual product quality. To further investigate this relationship, we performed a refined analysis by narrowing down the PSD of recycled PVC through a series of three distinct sieving operations:
- In the first sieving operation, we used a 600 μm aperture sieve to exclude particles larger than 600 μm (distribution “1”).
- In the second sieving operation, we used a 400 μm aperture sieve to exclude particles larger than 400 μm (distribution “2”).
- In the third sieving operation, we used a 200 μm aperture sieve to exclude particles larger than 200 μm (distribution “3”).
This methodical approach allowed us to precisely control the PVC particle sizes and better understand their impact on the final product’s properties and performance.
The cumulative distribution function (CDF) illustrated in Figure 11 underscores the retrieval percentages achieved during sieving processes (distribution “0”). Notably, when employing a 600 μm aperture sieve (distribution “1”), an exceptional recovery percentage of 96.44% for recycled PVC particles is evident. Similarly, the use of a 400 μm aperture sieve (distribution “2”) yields a remarkable recovery percentage of 73.01%. However, only a recovery percentage of 12.81% was obtained when sieving using a 200 μm aperture sieve (distribution “3”).
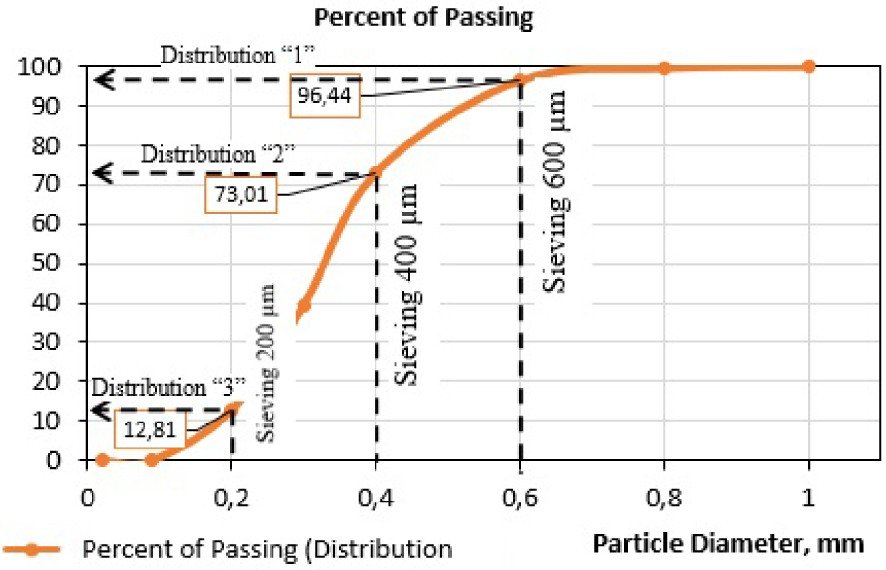
Cumulative distribution curve.
3.5.1. Optimization according to the different distributions
3.5.1.1. Preparation of expanded layer formulations
Preliminary tests, coupled with microscopic examinations, enabled the identification and exclusion of samples exhibiting cracks in the expanded layer, akin to those portrayed in Figure 9f. Employing this methodology, we effectively streamlined the testing protocol, thereby curtailing the requisite number of tests—each mechanical evaluation necessitates three individual samples—conducted for every distribution (“1”, “2” and “3”).
The ensuing table succinctly encapsulates the exhaustive array of tests undertaken for each distribution (“1”, “2” and “3”), specifying the plasticizer quantities incorporated within each respective formulation. Table 8 summarizes all the tests to be carried out.
Correlating the plasticizer quantity in each distribution with the amount of recycled PVC incorporated
![]() |
Table 8, shows that, for the same quantity of recycled PVC added, the plasticizer amount required to achieve the targeted viscosity of 25,000 (±500) Pa⋅s diminishes following each successive sieving stage. To illustrate, when 45 g of recycled PVC is employed, the plasticizer requirement drops from 80 g (distribution “0”, no sieving) to 75 g (distribution “1”, after sieving 600 μm), and further decreases to 65 g (distribution “2”, sieving 400 μm).
The incorporation of flattened and elongated recycled PVC particles, ranging from 400 to 600 μm in size, into plastisol formulations containing pure PVC resin particles (typically 100 μm) hinders uniform particle dispersion. This issue can be mitigated by increasing the plasticizer content to de-agglomerate the PVC particles. Conversely, smaller recycled PVC particles (200 μm), closer to the 100 μm size of pure PVC resin, promote the formation of a more uniform and compact coating, leading to enhanced stress distribution, reduced deformation, and consequently, a lower plasticizer requirement to achieve the desired viscosity.
Evidently, this phenomenon underscores that the best distributions stem from the finest recycled PVC particles.
3.5.1.2. Mechanical properties
Table 9 summarizes the results of the mechanical tests, including BS, TR, and ER, corresponding to each distribution (“1”, “2” and “3”) in relation to the incorporated quantities of recycled PVC. Additionally, individual desirabilities (dBS, dTR and dER) and overall functions (D) are also presented.
Impact of the quantity and size distribution of recycled PVC particles on mechanical properties
![]() |
The results shown in Figure 12 unequivocally establish a discernible enhancement in mechanical properties subsequent to a meticulous “600 μm” sieving process (distribution “1”), when juxtaposed with distribution “0” that underwent no such sieving. This improvement is particularly pronounced for the expanded layers originating from 45 g of recycled PVC, as evidenced by substantial increments in the ensuing parameters: a remarkable 190% surge in BS, an impressive 210% surge in TR, and a striking 162.86% surge in ER.
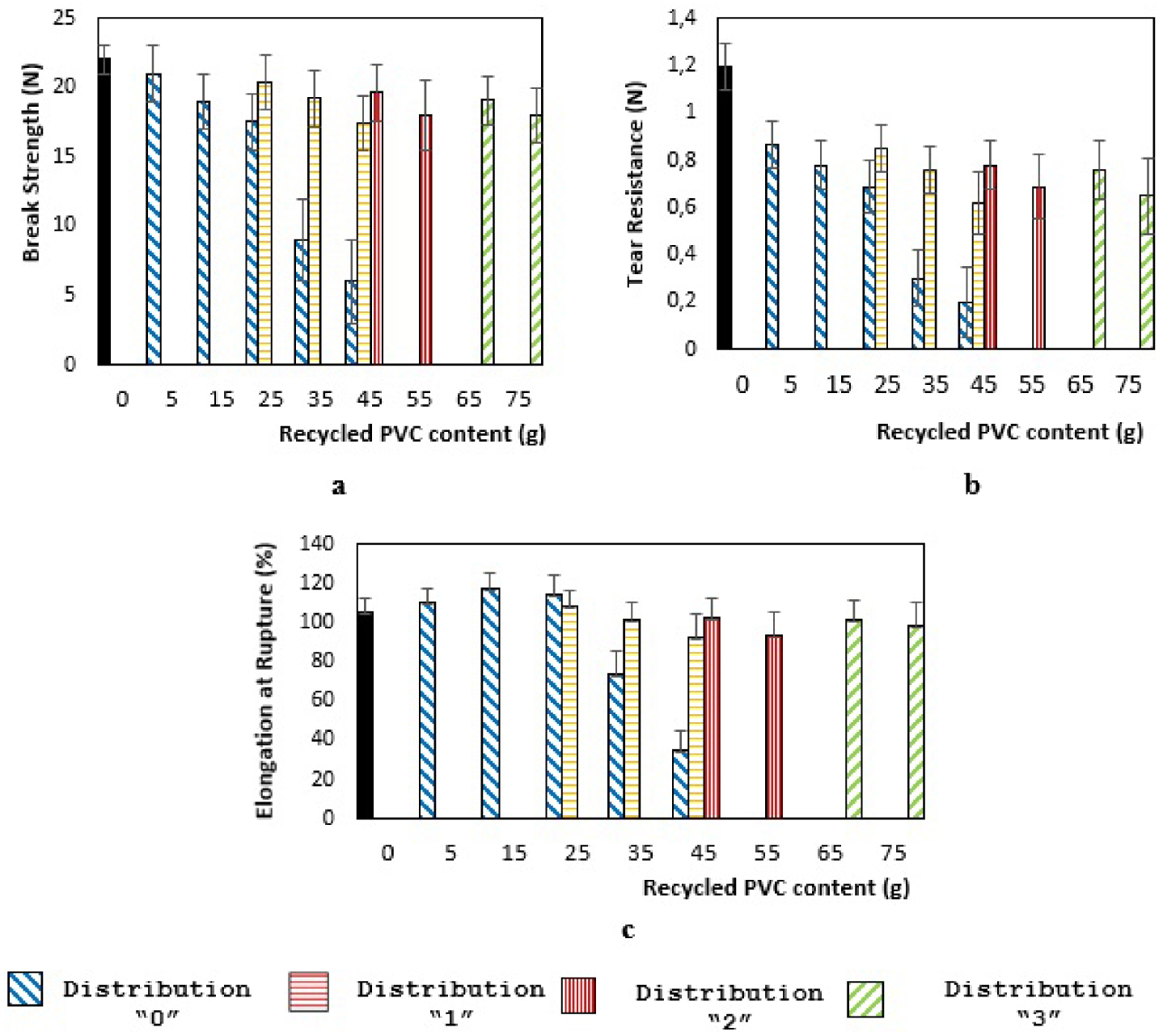
Effect of Recycled PVC content on the mechanical properties of PVC expanded layer after sieving, (a) Break Strength (N), (b) Tear Resistance (N), (c) Elongation at Rupture (%), Black scale bar: without recycled PVC and representing the reference value (at 100%) for comparing the evolution after the incorporation of recycled PVC.
These significant percentage increments can be traced back to the notable degradation, vividly exemplified by the emergence of discernible fissures, within the expanded layers obtained through distribution “0” while utilizing a 45 g quantity of recycled PVC (Figure 9f).
Utilizing distribution “2” (400 μm sieve aperture), the expanded layers produced with 45 g of recycled PVC exhibited notable enhancements compared to distribution “1” (600 μm sieve aperture). This translated to significant increments of 12.6% in BS, 25.8% in TR, and 10.8% in ER. However, when the same distribution “2” was employed with a quantity of 55 g recycled PVC, reductions were observed, with BS decreasing by 8%, TR by 11.54%, and ER by 8.82%.
It was only through distribution “3” (200 μm sieve aperture) that we achieved a successful formulation for expanded layers utilizing quantities of recycled PVC up to 65 g (86.67%) and 75 g (100%). With these two quantities (65 g and 75 g), we were able to document the following respective values: BS of 19.1N and 18N, TR of 0.76N and 0.65N, and ER of 101% and 98%.
Finer recycled PVC particles yield a more consistent foam structure with smaller pores compared to larger recycled PVC particles. This occurs because finer particles boast a larger surface area, fostering greater interaction and contact among the particles. Marceneiro et al [20] validated these findings in their study, which encompassed three distinct PVC powders distinguished by density, PSD, surface charge, and microstructure. Their study elucidated the pivotal role of interactions between PVC and plasticizer in characterizing the mechanical properties of plastisols and the resulting PVC films. Moreover, their findings highlighted the significant impact of structural defects, emphasizing their role in hastening PVC degradation, thus significantly impacting its long-term performance. Stambouli et al. [4, 5] also observed a similar phenomenon where the incorporation of fine calcium carbonate particles resulted in substantial improvements in mechanical properties. This enhancement was attributed to the strengthened van der Waals interaction forces between the plastisol and these particles.
3.5.1.3. Overall mechanical qualities
The results of the overall functions, summarized in Table 10, are critically important as they provide in-depth insight into the acceptability of each expanded layer. These insights are contingent upon the size distribution (distributions: “0”, “1”, “2”, and “3”) and the quantity of recycled PVC employed (5 g–75 g) in the plastisol recipe formulations.
Overall Desirability values for expanded layer samples based on distribution and incorporated recycled PVC quantity
![]() |
Based on the outcomes highlighted in the aforementioned table, satisfactory overall mechanical qualities are attained through varying amounts of recycled PVC—15 g (20%), 35 g (46.67%), 45 g (60%), and 65 g (86.67%)—corresponding to distribution 0 (No Sieving), distribution 1 (600 μm sieve aperture), distribution 2 (400 μm sieve aperture), and distribution 3 (200 μm sieve aperture), respectively. These conclusions are robustly endorsed by PLASTISS experts.
The results deduced from the overall functions facilitate the choice of expanded layers that align with the necessary mechanical criteria. More precisely, to decide and finalize the optimal plastisol recipe formulation from these chosen expanded layers, additional factors must be taken into account, notably including the percentage of particle recovery for each distribution and the amount of plasticizer introduced to attain the prescribed viscosity.
3.5.2. Final decision
This finding has significant implications for ensuring a balance between sustainability and achieving desired quality standards. On the one hand, using large quantities of recycled PVC particles can help to reduce the environmental impact of the floorcovering industry. Conversely, an overreliance on plasticizers, which are known to be deleterious substances with the ability to migrate to the surface of floorcoverings, raises concerns about adverse health effects on individuals exposed to them.
After extensive consultations among experts at PLASTISS company, the decision was made to embrace the C2 conditions (Table 11), as the company prioritizes the maximization of PVC waste valorization. In fact, this distribution C2, with particle sizes below 0.6 mm, yields an acceptable quality (global function value of 0.59) for the expanded layer while using less amount of plasticizer (60 g vs 65 g for C3) and efficiently utilizing 96.44% of the total recycled PVC, in contrast to C3, which only recycles 73.01% since only particles smaller than 0.4 mm are used.
However, an improved pulverization process favoring a distribution primarily comprising PVC particles with sizes under 0.4 mm would make C3 the preferred distribution.
By effectively managing the amount of both recycled PVC and plasticizer, we can not only create a more sustainable floorcovering but also ensure a safer environment for consumers and industry workers alike.
4. Conclusion
The findings from this research indicate the feasibility of utilizing a significant amount of recycled PVC particles in plastisol formulations to replace conventional PVC resin in the expanded layer of floorcoverings. As an initial exploration, a meticulous analysis of the quality standards expected from the final product, particularly the expanded layer after integrating recycled PVC powder, proves imperative.
Simultaneously, a profound comprehension of morphology and PSD takes on paramount significance in exploring the impacts of recycled PVC content and particle dimensions on both the mechanical (including BS, ER, and TR) and the morphological properties of the PVC expanded layer intended for floorcoverings.
Morphology studies, using microscopic observation, allowed us to distinguish the different flat and elongated shapes of particles making up recycled PVC powder. These shapes of non-spherical particles frequently display elevated porosity and reduced flow characteristics which hinder the effective dispersion of the recycled PVC powder. This behavior resulted in an augmentation of the plasticizer quantity, which contributes to the flexibility and elasticity of the PVC material. As a result, the amount of plasticizer required to produce an expanded layer increases as the amount of recycled PVC powder increases. This plasticizer quantity reaches 80 g for a 45 g quantity of recycled PVC.
As the proportion of recycled PVC increases, noticeable alterations manifest within the foam structure. It is noteworthy that the incorporation of 35 g of recycled PVC distinctly precipitates a degradation of the foam structure, which becomes even more pronounced at 45 g. This transition unveils the emergence of microvoids and cracks, exacerbating the structural issues observed.
Mechanical outcomes, which align with microscopic observations, validate that the mechanical properties deteriorated rapidly when the amount of recycled PVC powder exceeded 25 g.
To further optimize the utilization of recycled PVC within this specialized floorcovering application, a meticulous analysis was conducted. This involved refining the PSD through a sequence of three distinct sieving operations: distribution 1 (using a 600 μm sieve aperture), distribution 2 (employing a 400 μm sieve aperture), and distribution 3 (utilizing a 200 μm sieve aperture). The outcomes present commendable overall mechanical characteristics across various quantities of recycled PVC—15 g (equivalent to 20% of the total added PVC), 35 g (46.67%), 45 g (60%), and 65 g (86.67%). These quantities correspond to distribution 0 (No Sieving), distribution 1, distribution 2, and distribution 3, respectively.
In our forward-looking approach, we remain dedicated to enhancing the grinding process, aiming to attain an optimized PSD. Our goal is to increase the proportion of fine particles, rendering them suitable for utilization within both expanded and superficial layers.
Declaration of interests
The authors do not work for, advise, own shares in, or receive funds from any organization that could benefit from this article, and have declared no affiliations other than their research organizations.
Acknowledgements
The authors gratefully acknowledge the use of the services and facilities at PLASTISS as the case study company.