1 Introduction
Ester synthesis reactions are usually conducted with the aid of acid or base catalysts, so the employment of catalyst or promoters that are suitably active but also compatible with other functional groups is of great importance [1]. The protection of alcoholic and phenolic hydroxyl group is an important transformation in organic synthesis [2]. Typically, acylation of alcohols is performed with acetyl chloride or acetic anhydride in the presence of catalysts such as Et3N and pyridine [3]. A variety of catalysts such as silica gel supported sulfuric acid [4], p-toluene sulphonic acid [5], ZnCl2 [6], CoCl2 [7], Sc(OTf)3 [8], TaCl5 [9], montmorillonit K10 [10], HY zeolite [11], In(OTf)3 [12], Cu(OTf)2 [13], Yittria-Zirconia based Lewis acid [14], InCl3/Mont.K10 [15], Manganese(III) bis(2-hydroxyanil)acetylacetonato complex [16], Silica Sulfate [17], p-MeC6H4SO2NBr2 [18], DBDMH or TCCA [19], H6P2W18O62.24 H2O [20], ionic liquid based on morpholin [21] borated zirconia [22] and DMAP.saccharin [23] are also known to catalyze the acylation of alcohols. However, most of these methods suffer from at least one of the following disadvantages: vigorous reaction conditions, high cost and toxicity of the reagent, tedious work-up procedures, unsatisfactory yields, and instability and hygroscopic nature of the reagent. The most synthetically versatile methodology for (trans) esterification is provided by Lewis acids, due to their mildness, simplicity in operation and catalytic capabilities. Polymer supported catalysts and reagents have become popular in organic synthesis over the past decades. The high catalytic activity, low toxicity, stability, their recyclability, and environmentally safe conditions make the use of a polymer supported reagent attractive alternatives to conventional reagents. Also, the application of polymer supported reagents and catalysts has received special attention, due to easy work up of reaction products and some selectivity which is undoubtedly attractive features of this methodology [24]. In the course of our research on amidation of benzhydrol with nitriles via polyvinylpolypyrrolidone-bound boron trifluoride (PVPP-BF3) [25], in this work we found that PVPP-BF3 can be used as a recyclable and more efficient catalyst for acetylation of alcohols, phenols and trimethylsilyl ethers in excellent yields at room temperature (Scheme 1).
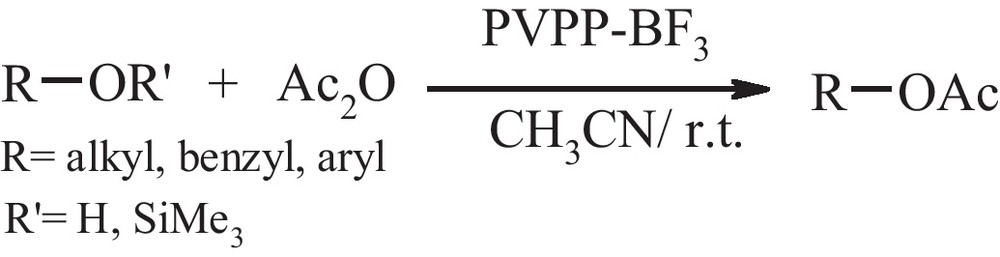
Acylation of alcohols, phenols and trimethylsilyl ethers in acetonitrile via PVPP-BF3.
2 Experimental
All chemicals were purchased from Merck chemical company. Melting points were recorded on an electro thermal melting point apparatus. The NMR spectra were recorded in CDCl3 with TMS as an internal standard on a Bruker advance DRX 400 MHz spectrometer. IR spectra were determined on a SP-1100, P-UV-Com instrument. Purity determination of the products was accomplished by TLC on silica gel poly gram SIL G/UV 254 plates. Products were identified by comparison IR and NMR spectra, with those reported for authentic samples.
2.1 Catalyst preparation
In this method, boron trifluoride etherate was immobilized on polyvinylpolypyrrolidone to give a stable polymeric Lewis acid reagent according to our previous article [25]. To a suspension of PVPP (3 g) in CH2Cl2 (25 ml), a solution of BF3.OEt2 (5 ml) in CH2Cl2 (15 ml) was added dropwise and the mixture stirred for 1 h at room temperature. The resulting resin was filtered and washed with CH2Cl2 (2 × 10 ml) and dried in a vacuum desiccator to give a stable and non-hygroscopic powder.
2.2 General procedure for acetylation of alcohols and phenols
To a stirred mixture of the alcohol (1 mmol), Ac2O (2 mmol) and CH3CN (3 ml) was added PVPP-BF3 (0.025 g) and stirring continued at room temperature. The progress of the reaction was monitored by TLC. After completion of the reaction, dichloromethane (15 ml) was added and the reaction mixture was filtered. The organic phase was washed with saturated NaHCO3 solution (15 ml), dried over anhydrous Na2SO4 and evaporated to give the pure acylated product. The isolated products were characterized by spectral studies (FT-IR and NMR). The spectra were compared with those of standard esters. The yield was calculated as mmol of purified product with respect to mmol of initial alcohol. The reaction times and yields of the products are presented in Table 3.
Acylation of different alcohols, phenols and trimetylsilyl ethers using of PVPP-BF3.
Entry | Substrate | Producta | Time (h) | Yield (%)b |
1 | C6H5CH2CH2OH | C6H5CH2CH2OAc | 0.5 | 99 |
2 | C6H5CH2OH | C6H5CH2OAc | 1 | 99 |
3 | 4-MeOC6H4CH2OH | 4-MeOC6H4CH2OAc | 1 | 98 |
4 | 4-Pri-C6H4CH2OH | 4-Pri-C6H4CH2OAc | 1.5 | 97 |
5 | 2-Cl-C6H4CH2OH | 2-Cl-C6H4CH2OAc | 1 | 97 |
6 | 4-Cl-C6H4CH2OH | 4-Cl-C6H4CH2OAc | 2 | 99 |
7 | 4-F-C6H4CH2OH | 4-F-C6H4CH2OAc | 2 | 99 |
8 | 4-NO2-C6H4CH2OH | 4-NO2-C6H4CH2OAc | 2 | 99 |
9 | 4-But-C6H4CH2OH | 4-But-C6H4CH2OH | 1.5 | 98 |
10 | 2,4-Cl2-C6H3CH2OH | 2,4-Cl2-C6H3CH2OH | 1.5 | 99 |
11 | (CH3CH2CH2CH2)2CHOH | (CH3CH2CH2CH2)2CHOAc | 2 | 96 |
12 | C6H5CH2C(CH3)2OH | C6H5CH2C(CH3)2OAc | 2.5 | 95 |
13 | C6H5OH | C6H5OAc | 2 | 85 |
14 | 4-NO2C6H4OH | 4-NO2C6H4OAc | 2.5 | 99 |
15 | 3-MeC6H4OH | 3-MeC6H4OAc | 2 | 99 |
16 | 4-MeC6H4OH | 4-MeC6H4OAc | 1 | 95 |
17 | 4-MeO-C6H4OH | 4-MeO-C6H4OAc | 0.5 | 98 |
18 | 2-Br-C6H4OH | 2-Br-C6H4OAc | 2 | 98 |
19 | 4-Cl-C6H4OH | 4-Cl-C6H4OAc | 1 | 85 |
20 | 2-Et-C6H4OH | 2-Et-C6H4OAc | 1.5 | 80 |
21 | C6H5CH2OTMS | C6H5CH2OAc | 2.5 | 96c |
22 | C6H5CH2CH2OTMS | C6H5CH2CH2OAc | 1 | 97c |
23 | C6H5OTMS | C6H5OAc | 3 | 85c |
24 | 4-Cl-C6H4OTMS | 4-Cl-C6H4OAc | 1 | 84c |
25 | 4-MeO-C6H4CH2OTMS | 4-Cl-C6H4CH2OAc | 1 | 96c |
a Reaction conditions: alcohol (1 mmol), acetic anhydride (2 mmol), PVPP-BF3 (0.025 g), MeCN, r.t.
b Isolated yields.
c PVPP-BF3 (0.05 g) was used.
2.3 General procedure for acetylation of silylated alcohols and phenols
To a stirred mixture of the silylated alcohol or silylated phenol (1 mmol), Ac2O (2 mmol) and CH3CN (3 ml) was added PVPP-BF3 (0.05 g) and stirring continued at room temperature. The progress of the reaction was monitored by TLC. After completion of the reaction, dichloromethane (15 ml) was added and the reaction mixture was filtered. The organic phase was washed with saturated NaHCO3 solution (15 ml), dried over anhydrous Na2SO4 and evaporated to give the pure acylated product. The isolated products were characterized by spectral studies (FT-IR and NMR). The spectra were compared with those of standard esters. The reaction times and yields of the products are presented in Table 3.
2.4 Selected characterization data
2.4.1 2-phenylethyl acetate (Table 3, entry 1)
Yield 99%; IR (KBr) υ: 2958, 2925, 1745, 1529, 1457, 1375, 1037, 746 cm−1. 1H NMR (CDCl3) δ = 2.06 (s, 3H), 2.95 (t, 2H, J = 7.2), 4.29 (t, 2H, J = 7.2), 7.24–7.35 (m, 5H) ppm. 13C NMR (CDCl3) δ = 170.96, 137.80, 128.85, 128.47, 126.53, 64.89, 34.07, 20.93.
2.4.2 4-isopropylbenzyl acetate (Table 3, entry 4)
Yield 97%; IR (KBr) υ: 2958, 2861, 1743, 1457, 1230, 1027, 819, 736 cm−1. 1H NMR (CDCl3) δ = 1.27 (d, 6H), 2.12 (s, 3H), 2.9 (m, 1H), 4.68 (s, 2H), 7.24 (d, 2H, J = 8.4), 7.31 (d, 2H, J = 8.4) ppm. 13C NMR (CDCl3) δ = 171.02, 151.24, 136.10, 127.32, 126.59, 72.47, 34.55, 24.85, 20.11.
2.4.3 p-nitrobenzene acetate (Table 3, entry 14)
Yield 99%; IR (KBr) υ: 2927, 2852, 1762, 1523, 1344, 1197, 1099, 858 cm−1. 1H NMR (CDCl3) δ = 2.37 (s, 3H), 7.28 (d, 2H, J = 7.2), 8.27 (d, 2H, J = 7.2) ppm. 13C NMR (CDCl3) δ = 168.46, 155.36, 146.15, 125.24, 122.48, 21.16.
2.4.4 m-tolyl acetate (Table 3, entry 15)
Yield 99%; IR (KBr) υ: 2927, 2861, 1770, 1589, 1457, 1371, 1145, 1014, 943, 784 cm−1. 1H NMR (CDCl3) δ = 2.31 (s, 3H), 2.38 (s, 3H), 6.9-7.3 (m, 3H) ppm. 13C NMR (CDCl3) δ = 169.85, 149.42, 135.53, 129.99, 125.18, 121.28, 118.63, 21.16, 20.91.
3 Results and discussion
Characterization of the Lewis acid sites present on the polymer was performed by recording the FT-IR spectrum of PVPP-BF3, which shows a strong broad absorption at 1000–1060 cm−1 for the BF bonds and a moderate absorption at 1646 cm−1 corresponds to the imine group on the backbone (Fig. 1). The capacity of the reagent was determined by titration and found to be 10 mmol/g, whereas its silica supported analogue has a loading capacity of less than 4 mmol/g [26,27]. Despite that BF3.Et2O, PVPP-BF3 is more water tolerant, non-corrosive and stable solid catalyst elevated Lewis acid property. Interestingly, this reagent gives not only excellent yields of the products but also PVPP-BF3 is easily regenerated and can be reused several times and retains its activity after several months of storage. To select the best solvent, the acylation of 2-phenylethanol was studied in a variety of organic solvents such as dichloromethane, acetonitrile, nitromethane, diethylether, and n-hexane. Among them, the reaction in acetonitrile proceeds faster than other organic solvents in the same concentration of solvent (Table 1). As seen in Table 2, the optimized stoichiometric ratio of ROH: Ac2O was found to be 1:2 using 0.025 g of the PVPP-BF3 in acetonitrile at room temperature. All reactions were carried out under the optimized conditions, and the results are summarized in Table 3. Excellent yields were obtained for a variety of primary, secondary, tertiary, benzylic alcohols, and substituted phenols. Primary alcohols were acetylated faster than secondary and tertiary alcohols (entries 1, 11, and 12, Table 3). The influence of the presence of substituents investigated and the results showed that the reactions were relatively affected by electronic and steric factors. Table 3, shows that benzylic alcohols and phenols with electron-donating groups were converted to the corresponding acetates in shorter time than those with electron-withdrawing groups. Also, a series of silylated alcohols and phenols are treated with acetic anhydride under catalysis by the PVPP-BF3 (entries 21–25, Table 3). To conclude, PVPP-BF3 is a good one-pot desilylation-acetylation catalyst for a wide range of silylated alcohols and phenols. It is reasonable to assume that the present reaction is initiated by Lewis acidity and oxophilicity of PVPP-BF3 which promotes the acylation reaction via deprotection of trimethyl silyl ether and coordination to oxygen atoms of acetic anhydride and facilitation of C-O cleavage by attacking of hydroxyl group (Scheme 2). In order to learn the catalytic activity of PVPP-BF3, we compared our obtained results for the acylation of benzyl alcohol with the best of the well-known data from literature as shown in Table 4. The advantages of the described method in comparison with other previously reported catalysts are: the reaction occurs at room temperature with good to high yield of the products, more water tolerant, non-corrosive and stable solid catalyst. To check the reusability of the catalyst, it was employed the acylation of 2-phenyl ethanol fourth cycles under the optimum conditions. The catalyst powder was recovered by filtration, washed with dichloromethane and immediately reused for acylation processes again, taking into account the partial loss of catalyst during the recovery. The second cycle was performed with the recovered catalyst and addition of two equimolecular amount of acetic anhydride gave corresponding ester in 96% yield. The third and fourth cycles were performed with the recovered catalyst similar to above method and 88% and 79% of 2-phenylethyl acetate was obtained respectively. To improve the catalytic activity of catalyst after forth cycles it is favored to separate the polyvinylpolypyrrolidone by filtration, washed carefully from dichloromethane and dried, then treated with boron trifluoride etherate again to prepared fresh polyvinylpolypyrrolidone immobilized boron trifluoride catalyst. The polymer support can be used several times for the immobilization of boron trifluoride. So, the recyclability of the polymer support together with its biocompatibility makes the method environmentally safe and friendly.
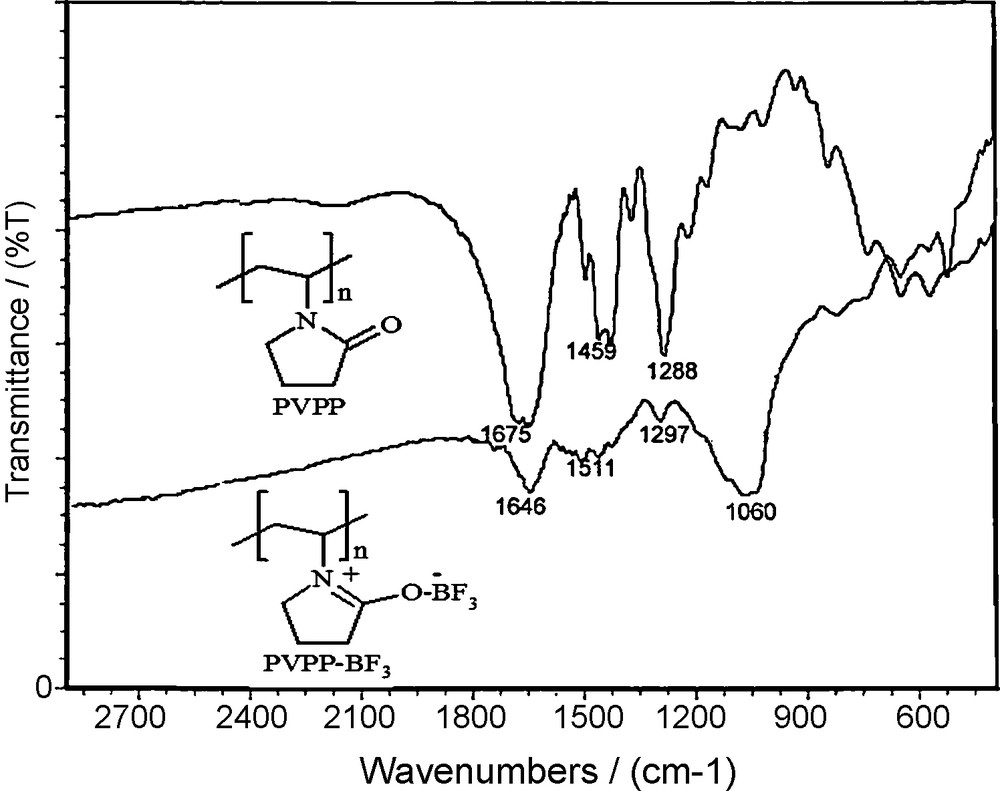
The FT-IR spectrum of polyvinylpolypyrrolidone (PVPP) and (PVPP-BF3) complex.
Effect of solvents on acylation of 2-phenylethanol (1 mmol) using acetic anhydride (2 mmol) promoted by PVPP-BF3.a
Entry | Solvent | Time (h) | Conversionb (%) |
1 | CH2Cl2 | 4 | 48 |
2 | Et2O | 2.5 | 76 |
3 | CH3CN | 0.5 | 99 |
4 | CH3NO2 | 2.5 | 68 |
5 | n-hexane | 3 | 56 |
a All reactions were carried out using 0.025 g of the polymeric reagent.
b The conversion was determined by GC analysis of the crude product.
Effect of PVPP-BF3 on acylation of 2-phenylethanol (1 mmol).a
Entry | Ac2O (mmol) | PVPP-BF3 (g) | Conversionb (%) |
1 | 1 | 0.015 | 42 |
2 | 2 | 0.015 | 68 |
3 | 3 | 0.015 | 71 |
4 | 1 | 0.025 | 76 |
5 | 2 | 0.025 | 99 |
a Reactions were carried out in acetonitrile at room temperature in 0.5 h.
b The conversion was determined by GC analysis of the crude product.
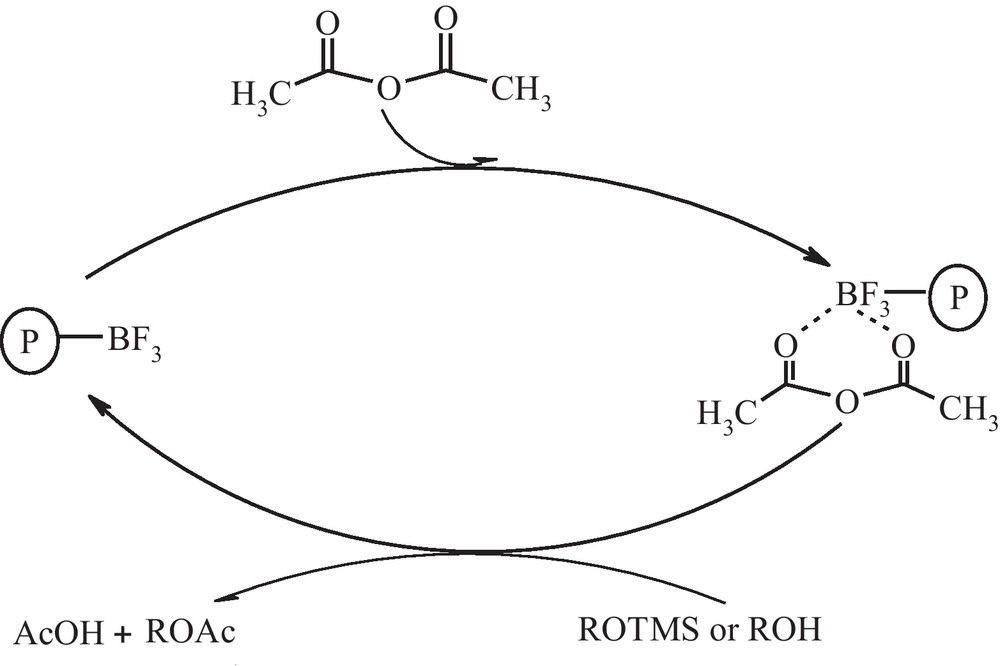
The proposed mechanism.
Comparison of our reagent with some other reagents in acylation of benzyl alcohol.
Entry | Reagent | Conditions | Time (h) | Yield (%) | Ref. |
1 | Yttria-Zirconia-based-Lewis acid | 110–125 °C | 4 | 94 | [14] |
2 | InCl3/mont.K10 | 50 °C | 0.7 | 92 | [15] |
3 | [Mn(haacac)Cl] | MeNO2, 30 °C | 5 | 97 | [16] |
4 | p-MeC6H4SO2NBr2 | CH2Cl2, r.t. | 1 | 95 | [18] |
5 | DBDMH or TCCA | CH2Cl2, r.t. | 7.5 | 97 | [19] |
6 | H6P2W18O62.24 H2O | Toluene, r.t. | 0.75 | 98 | [20] |
7 | Borated zirconia | Toluene /110 °C | 4.5 | 92 | [22] |
8 | PVPP-BF3 | MeCN, r.t. | 1 | 99 | This work |
4 Conclusions
We have developed a simple methodology for esterification reaction using PVPP-BF3 as a high loading of Lewis acid, which is stable, easy to prepared and handle, and represent effective procedure for the acylation of primary, secondary and tertiary alcohols, phenols and trimethylsilyl ethers with acetic anhydride in acetonitrile at room temperature. Excellent yields, easy work-up and reusability and stability of the catalyst are noteworthy advantages of this method.
Acknowledgements
We are thankful to Islamic Azad University, Rasht Branch and Islamic Azad University, Science and Research, Amol Branch for financial assistance in this work.