This paper presents a simple and effective method to identify and quantify the existence of cracks in the teeth roots of spur gears. The problem was numerically analyzed through finite element-based simulation with SolidWorks in the first part of this work. The computed tooth in-plane bending stiffness and natural frequency decreased considerably with an increase in the crack length, while the deformation followed an opposite trend. The numerical results were experimentally validated through a convenient and straightforward test rig developed for this purpose. The experimental results obtained from the modal analysis tests confirmed the previously obtained numerical results. A graphical representation of these parameters on a polar plot shows concentric circles with no particular sign from one tooth to another. However, in the presence of cracks in the vicinity of teeth roots, these circular patterns became deformed in the neighborhood of the teeth with defect, which provides a quick and easy visual check to detect a crack and quantify its extent.
Révisé le :
Accepté le :
Publié le :
Thaer Syam 1 ; Yousif Badri 2 ; Omran Abdallah 2 ; Sadok Sassi 2 ; Jamil Renno 2 ; Omar D. Mohammed 3
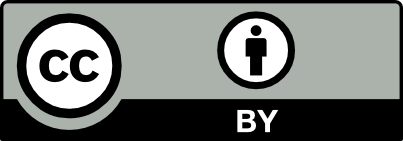
@article{CRMECA_2022__350_G3_477_0, author = {Thaer Syam and Yousif Badri and Omran Abdallah and Sadok Sassi and Jamil Renno and Omar D. Mohammed}, title = {Towards a simplified technique for crack recognition in gearing systems}, journal = {Comptes Rendus. M\'ecanique}, pages = {477--494}, publisher = {Acad\'emie des sciences, Paris}, volume = {350}, year = {2022}, doi = {10.5802/crmeca.128}, language = {en}, }
TY - JOUR AU - Thaer Syam AU - Yousif Badri AU - Omran Abdallah AU - Sadok Sassi AU - Jamil Renno AU - Omar D. Mohammed TI - Towards a simplified technique for crack recognition in gearing systems JO - Comptes Rendus. Mécanique PY - 2022 SP - 477 EP - 494 VL - 350 PB - Académie des sciences, Paris DO - 10.5802/crmeca.128 LA - en ID - CRMECA_2022__350_G3_477_0 ER -
%0 Journal Article %A Thaer Syam %A Yousif Badri %A Omran Abdallah %A Sadok Sassi %A Jamil Renno %A Omar D. Mohammed %T Towards a simplified technique for crack recognition in gearing systems %J Comptes Rendus. Mécanique %D 2022 %P 477-494 %V 350 %I Académie des sciences, Paris %R 10.5802/crmeca.128 %G en %F CRMECA_2022__350_G3_477_0
Thaer Syam; Yousif Badri; Omran Abdallah; Sadok Sassi; Jamil Renno; Omar D. Mohammed. Towards a simplified technique for crack recognition in gearing systems. Comptes Rendus. Mécanique, Volume 350 (2022), pp. 477-494. doi : 10.5802/crmeca.128. https://comptes-rendus.academie-sciences.fr/mecanique/articles/10.5802/crmeca.128/
[1] Diagnosis methodology for identifying gearbox wear based on statistical time feature reduction, Proc. Inst. Mech. Eng., Part C: J. Mech. Eng. Sci., Volume 232 (2018) no. 15, pp. 2711-2722 | DOI
[2] Pattern recognition based on-line vibration monitoring system for fault diagnosis of automobile gearbox, Measurement, Volume 114 (2018), pp. 233-242 | DOI
[3] A model for the study of meshing stiffness in spur gear transmissions, Mech. Mach. Theory, Volume 61 (2013), pp. 30-58 | DOI
[4] Gear bending fatigue failure and bending life analysis, Encyclopedia of Tribology (Q. J. Wang; Y. W. Chung, eds.), Springer, Boston, MA, 2013 | DOI
[5] Following spur gear crack propagation in the tooth foot by finite element method, J. Fail. Anal. Prev., Volume 10 (2010), pp. 531-539 | DOI
[6] Dynamic modeling of flexibly supported gears using iterative convergence of tooth mesh stiffness, Mech. Syst. Signal Process., Volume 80 (2016), pp. 460-481 | DOI
[7] Investigation of crack propagation scatter in a gear tooth’s root, Eng. Fract. Mech., Volume 75 (2006) no. 5, pp. 1266-1283 | DOI
[8] Mesh stiffness calculation of a spur gear pair with tooth profile modification and tooth root crack, Mech. Mach. Theory, Volume 62 (2013), pp. 63-74 | DOI
[9] Handbook of Loss Prevention, Springer, Berlin, 1978 | DOI
[10] Influence of cracks on dynamic characteristics and stress intensity factor of gears, Eng. Fail. Anal., Volume 32 (2013), pp. 63-80 | DOI
[11] Failure path based modified gear mesh stiffness for spur gear pair with tooth root crack, Eng. Fail. Anal., Volume 27 (2013), pp. 286-296 | DOI
[12] et al. A model for the study of meshing stiffness in spur gear transmissions, Mech. Mach. Theory, Volume 61 (2013), pp. 30-58 | DOI
[13] Guided-waves in a low velocity impacted composite winglet, Key Eng. Mater., Volume 774 (2018), pp. 343-348 | DOI
[14] Damage detection in wind turbine blades by using operational modal analysis, Struct. Health Monit., Volume 15 (2016) no. 3, pp. 289-301 | DOI
[15] Three new models for evaluation of standard involute spur gear mesh stiffness, Mech. Syst. Signal Process., Volume 101 (2018), pp. 424-434 | DOI
[16] Finite element analyses for contact strength and bending strength of a pair of spur gears with machining errors, assembly errors and tooth modifications, Mech. Mach. Theory, Volume 42 (2007) no. 1, pp. 88-114 | DOI | Zbl
[17] Effects of machining errors, assembly errors and tooth modifications on loading capacity, load-sharing ratio and transmission error of a pair of spur gears, Mech. Mach. Theory, Volume 42 (2007) no. 6, pp. 698-726 | DOI | Zbl
[18] Effects of tip relief on vibration responses of a geared rotor system, Proc. Inst. Mech. Eng., Part C: J. Mech. Eng. Sci., Volume 228 (2014) no. 7, pp. 1132-1154 | DOI
[19] An improved TVMS algorithm and dynamic modeling of gear-rotor system with tooth root crack, Eng. Fail. Anal., Volume 42 (2014), pp. 157-177 | DOI
[20] Analytical evaluating the influence of crack on the mesh stiffness of a planetary gear set, Mech. Mach. Theory, Volume 76 (2014), pp. 20-38 | DOI
[21] Effect of spalling or tooth breakage on gear mesh stiffness and dynamic response of a one-stage spur gear transmission, Eur. J. Mech. A/Solids, Volume 27 (2008) no. 4, pp. 691-705 | DOI | Zbl
[22] Analytical modeling of spur gear tooth crack and influence on gear mesh stiffness, Eur. J. Mech. A/Solids, Volume 28 (2009) no. 3, pp. 461-468 | DOI | Zbl
[23] Hertzian damping, tooth friction and bending elasticity in gear impact dynamics, J. Mech. Des., Volume 109 (1987) no. 2, pp. 189-196 | DOI
[24] Simulation of spur gear dynamics and estimation of fault growth, J. Sound Vib., Volume 317 (2008) no. 3–5, pp. 608-624 | DOI
[25] Vibration signal analysis for gear fault diagnosis with various crack progression scenarios, Mech. Syst. Signal Process., Volume 41 (2013) no. 1–2, pp. 176-195 | DOI
[26] Gear fault models and dynamics-based modelling for gear fault detection—A review, Eng. Fail. Anal., Volume 117 (2020), 104798 | DOI
[27] Dynamic simulation of spur gear with tooth root crack propagating along tooth width and crack depth, Eng. Fail. Anal., Volume 18 (2011) no. 8, pp. 2149-2164 | DOI
[28] Improving mesh stiffness calculation of cracked gears for the purpose of vibration-based fault analysis, Eng. Fail. Anal., Volume 34 (2013), pp. 235-251 | DOI
[29] Gear tooth crack detection using dynamic response analysis, Insight, Non-Destr. Test. Cond. Monit., Volume 55 (2013) no. 8, pp. 417-421 | DOI
[30] Dynamic response and time-frequency analysis for gear tooth crack detection, Mech. Syst. Signal Process., Volume 66–67 (2016), pp. 612-624 | DOI
- Contribution of friction-induced vibration to the realistic failure analysis of spur gear cracked teeth, Engineering Failure Analysis, Volume 158 (2024), p. 107956 | DOI:10.1016/j.engfailanal.2024.107956
- Modal analysis of spur gears for varied teeth root cracks characteristics: finite element analysis (FEA) simulations, Vibroengineering Procedia, Volume 45 (2022), p. 33 | DOI:10.21595/vp.2022.22936
Cité par 2 documents. Sources : Crossref
Commentaires - Politique