In this paper, the orthogonal cutting process is studied using Smooth Particle Hydrodynamic (SPH) method by a kinematic rigid cutting tool and two work-piece material models: perfectly elastic-plastic (EPP) model and Johnson–Cook (JC) model. The kinematic tool means that if the cutting tool is assumed a rigid body then the horizontal component speed of work-piece particles at cutting tool region are modified to the cutting speed. The chip shapes of orthogonal cutting process using SPH method with kinematic and kinetic tool models are compared with the experimental results. The chip obtained by the simulation with kinematic tool is more similar to the experimental results. Von-Mises stress distribution at different states of the orthogonal cutting process is investigated. The maximum stress occurs at the shear plane and causes the formation of chip teeth. Comparisons between chips of work-pieces with two material models are investigated including different rake angles of 5, 10 and
Révisé le :
Accepté le :
Publié le :
Mohammad Dehghani 1 ; Alireza Shafiei 1 ; Mohammad Mahdi Abootorabi 1
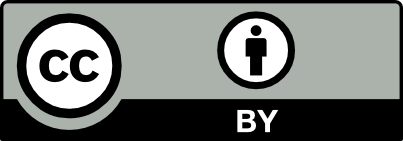
@article{CRMECA_2020__348_2_149_0, author = {Mohammad Dehghani and Alireza Shafiei and Mohammad Mahdi Abootorabi}, title = {Analyzing orthogonal cutting process using {SPH} method by kinematic cutting tool}, journal = {Comptes Rendus. M\'ecanique}, pages = {149--174}, publisher = {Acad\'emie des sciences, Paris}, volume = {348}, number = {2}, year = {2020}, doi = {10.5802/crmeca.6}, language = {en}, }
TY - JOUR AU - Mohammad Dehghani AU - Alireza Shafiei AU - Mohammad Mahdi Abootorabi TI - Analyzing orthogonal cutting process using SPH method by kinematic cutting tool JO - Comptes Rendus. Mécanique PY - 2020 SP - 149 EP - 174 VL - 348 IS - 2 PB - Académie des sciences, Paris DO - 10.5802/crmeca.6 LA - en ID - CRMECA_2020__348_2_149_0 ER -
%0 Journal Article %A Mohammad Dehghani %A Alireza Shafiei %A Mohammad Mahdi Abootorabi %T Analyzing orthogonal cutting process using SPH method by kinematic cutting tool %J Comptes Rendus. Mécanique %D 2020 %P 149-174 %V 348 %N 2 %I Académie des sciences, Paris %R 10.5802/crmeca.6 %G en %F CRMECA_2020__348_2_149_0
Mohammad Dehghani; Alireza Shafiei; Mohammad Mahdi Abootorabi. Analyzing orthogonal cutting process using SPH method by kinematic cutting tool. Comptes Rendus. Mécanique, Volume 348 (2020) no. 2, pp. 149-174. doi : 10.5802/crmeca.6. https://comptes-rendus.academie-sciences.fr/mecanique/articles/10.5802/crmeca.6/
[1] Development of a thermomechanical cutting process model for machining process simulations, CIRP Ann. - Manuf. Technol., Volume 57 (2008), pp. 97-100 | DOI
[2] Advances in material and friction data for modelling of metal machining, CIRP Ann. - Manuf. Technol., Volume 66 (2017), pp. 731-754 | DOI
[3] Improved analytical prediction of chip formation in orthogonal cutting of titanium alloy Ti6Al4V, Int. J. Mech. Sci., Volume 133 (2017), pp. 357-367 | DOI
[4] Stress distribution at the interface between tool and chip in machining, J. Eng. Ind.-Trans. ASME, Volume 94 (1972), pp. 683-689
[5] Metal Cutting, Elsevier, 2000
[6] Identification of a new friction model at tool-chip interface in dry orthogonal cutting, Int. J. Adv. Manuf. Technol., Volume 89 (2017), pp. 921-932 | DOI
[7] Investigation of temperature distribution in orthogonal cutting through dual-zone contact model on the rake face, Int. J. Adv. Manuf. Technol., Volume 96 (2018), pp. 81-89 | DOI
[8] Dry cutting study of an aluminium alloy (A2024-T351): a numerical and experimental approach, Int. J. Mater. Form., Volume 1 (2008), pp. 499-502 | DOI
[9] A new material model for 2D numerical simulation of serrated chip formation when machining titanium alloy Ti – 6Al – 4V, Int. J. Mach. Tools Manuf., Volume 48 (2008), pp. 275-288 | DOI
[10] Simulation modelling practice and theory finite element modelling of machining of AISI 316 steel: Numerical simulation and experimental validation, Simul. Model. Pract. Theory, Volume 18 (2010), pp. 139-156 | DOI
[11] Finite element modeling and simulation in dry hard orthogonal cutting AISI D2 tool steel with CBN cutting tool, Int. J. Adv. Manuf. Technol., Volume 53 (2011), pp. 1167-1181 | DOI
[12] Effects of friction conditions on the formation of dead metal zone in orthogonal cutting – a finite element study, Mach. Sci. Technol. (2018), pp. 934-952 | DOI
[13] An explicit finite element model to study the influence of rake angle and friction during orthogonal metal cutting, Int. J. Adv. Manuf. Technol., Volume 73 (2014), pp. 875-885 | DOI
[14] On the introduction of adaptive mass scaling in a finite element model of Ti6Al4V orthogonal cutting, Stimul. Model. Pract. Theory, Volume 53 (2015), pp. 1-14 | DOI
[15] Finite element modelling of 3D orthogonal cutting experimental tests with the Coupled Eulerian-Lagrangian (CEL) formulation, Finite Elem. Anal. Des., Volume 134 (2017), pp. 27-40 | DOI | Zbl
[16] Mesh influence in orthogonal cutting modelling with the Coupled Eulerian-Lagrangian (CEL) method, Eur. J. Mech. A / Solids, Volume 65 (2017), pp. 324-335 | MR | Zbl
[17] Finite element simulation and analysis of serrated chip formation during high – speed machining of AA7075 – T651 alloy, J. Manuf. Process., Volume 26 (2017), pp. 446-458 | DOI
[18] Finite element modeling of carbon fiber composite orthogonal cutting and drilling, 6th CIRP Int. Conf. High Perform. Cutting, HPC2014, Elsevier B.V., 2014, pp. 211-216
[19] Temperature measurement in orthogonai metal cutting, Int. J. Adv. Manuf. Technol., Volume 14 (1998), pp. 7-12 | DOI
[20] MPM simulations of high-speed machining of Ti6Al4V titanium alloy considering dynamic recrystallization phenomenon and thermal conductivity, Appl. Math. Modelling, Volume 56 (2018), pp. 517-538 | MR | Zbl
[21] Simulation of the orthogonal cutting of OFHC copper based on the smoothed particle hydrodynamics method, Int. J. Adv. Manuf. Technol., Volume 91 (2017), pp. 265-272 | DOI
[22] A numerical cutting model for brittle materials using smooth particle hydrodynamics, Int. J. Adv. Manuf. Technol., Volume 82 (2016), pp. 133-141 | DOI
[23] A parametric study of the modeling of orthogonal machining, Proc. ASME 2015 Int. Mech. Eng. Congr. Expo., American Society of Mechanical Engineers Digital Collection, 2015, pp. 1-10
[24] On the SPH orthogonal cutting simulation of A2024-T351 alloy, Procedia CIRP, Volume 8 (2013), pp. 152-157 | DOI
[25] (LS-DYNA Keyword User’s Manual, 2007) | DOI
[26] Modeling of orthogonal cutting process of A2024-T351 with an improved SPH method, Int. J. Adv. Manuf. Technol., Volume 95 (2018), pp. 905-919 | DOI
[27] Smooth Particle Hydrodynamics: A Mesh Free Particle Method, World Scientific, 5 Toh Tuck Link, Singapore, 2003 (ISBN 9789812384560) | Zbl
[28] Introduction to Nonlinear Finite Element Analysis, Springer, Department of Mechanical and Aerospace Engineering, University of Florida, Gainesville, FL, USA, 2015
[29] Plastic deformation of A2024-T351 aluminum plate over a wide range of loading conditions, Int. J. Solids Struct., Volume 50 (2013), pp. 1781-1790 | DOI
[30] Implementation of the smoothed particle hydrodynamics method to solve plastic deformation in metals, 10th World Congr. Comput. Mech., Blucher Mechanical Engineering Proceedings, 2014
[31] Dry machining aeronautical aluminum alloy AA2024-T351: Analysis of cutting forces, chip segmentation and built-up edge formation, Metals (Basel), Volume 6 (2016), 197 pages | DOI
Cité par Sources :
Commentaires - Politique