1 Introduction
Float glasses are produced worldwide in huge amounts and are among the most important technical glasses. It has long been known that tin ions can penetrate into the bath side of the float glass melt during the production process 〚1–3〛. Consequently, float glasses have two quite dissimilar sides. At the tin bath side, the performance of the glass surface is mainly determined by the in-diffused tin. At the atmosphere side, on the other hand, the surface is melt-formed (fire-polished) and displays pristine nature. Of course, both sides can be altered during further handling and/or storage.
There are especially two anomalies at the tin bath side of silicate float glasses that puzzle glass technologists since long, viz:
- • the so-called tin hump or bump, a peak in tin concentration in the micrometer region of several glasses 〚3–6〛,
- • the phenomenon of bloom, a greyish haze on other glasses after reheating in air, caused by a microscopic wrinkling at the surfaces 〚1, 7, 8〛.
Despite the many experimental and theoretical efforts to understand these interaction processes between tin and the glass melt in the float chamber, these are still largely unclear. Therefore, we initiated a joint-laboratory study on ‘tin in float glass’. Its aim was to measure precisely the in-depth profiles of all relevant species in the nanometer and the micrometer regions of the glasses, the in-depth profile of the Sn2+/Sn4+ ratio, and also the topographies of as-received and fractured glass surfaces on a nanometer scale. Based on the results, models were developed to explain the two mentioned anomalies.
2 Some experimental findings
Eight commercial float glasses with a thickness of 4 mm were investigated. Six of them were soda-lime silicate float glasses with Fe2O3 contents ranging from 0.017 to 1.80 wt%, and the two others were floated borosilicate glasses having Fe2O3 contents of ∼0.02 wt%, respectively 〚9〛. With the application of electron probe microanalysis (EPMA), Rutherford backscattering spectrometry (RBS) and Secondary Neutral Mass Spectrometry (SNMS), the complete in-depth profiles of all relevant elements from the first few nanometers to several micrometers could be obtained 〚10, 11〛. Conversion electron Mössbauer spectrometry (CEMS) was used to describe the Sn2+/Sn4+ ratio as a function of penetration depth 〚12, 13〛, and high-resolution atomic force microscopy (AFM) was applied to study the topographies of the different glass surfaces 〚14, 15〛.
3 Tin hump in the micrometer region
Fig. 1 displays the tin concentration profiles in a silicate float glass with an overall Fe2O3 content of 0.605 wt% and a Fe2+/(Fe2+ + Fe3+) ratio of 23.9. Irrespective of the method, a satellite peak in the tin profile between about 6 and 8 μm can be seen for the 4-mm float glasses. Similar peaks are found in other Fe2O3-rich float glasses, showing surface tin concentrations between 0.25 and 0.35 wt%. The borofloat glasses and the silicate float glasses with a low overall Fe2O3 content (< 0.2 wt%) did not show a tin hump within the present experimental error. A silicate float glass with 0.56 wt% Fe2O3, which had been prepared under reducing conditions (Fe2+/〚Fe2+ + Fe4+〛 = 60), did equally not show a tin hump.
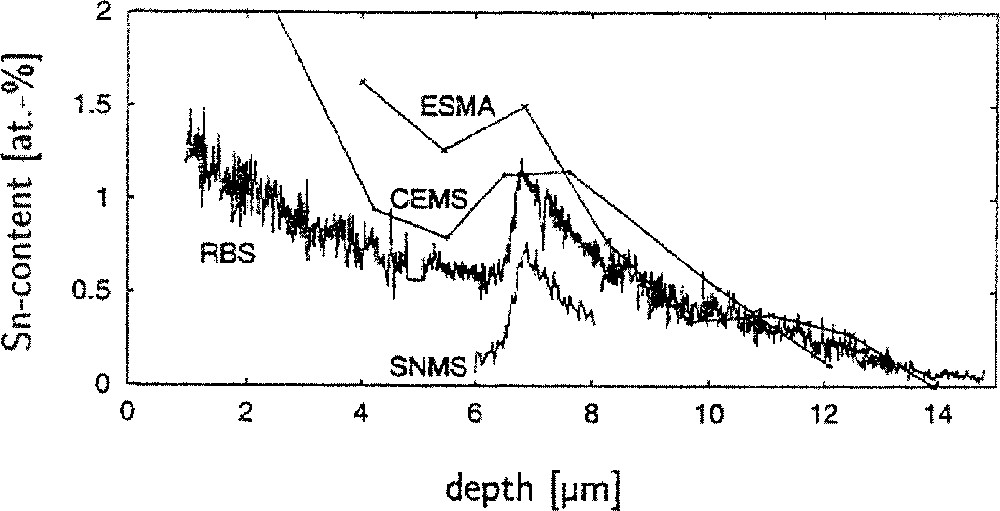
RBS, SNMS, EPMA and CEMS tin depth profiles in a float glass with 0.605 wt% Fe2O3 (the SNMS profile was shifted by –0.3 at%).
How can this anomalous peak be explained? The following conditions are assumed valid:
- • when the glass melt, which has been prepared under oxidizing conditions, enters the float chamber, a very strong and rapid change occurs in its oxidation state near the surface; this causes the redox processes
(see also the schematic in Fig. 2); - • the Fe2+ ions (possibly also ions like Na+ or Ca2+) enable an ongoing penetration of Sn2+ ions into the glass melt by an ion-exchange process
- • the formation of Sn4+ ions in the glass is possible only if Sn2+ and oxidation partners such as Fe3+ (possibly also S6+) are simultaneously available; according to Fig. 2, this is possible only in deeper parts of the melt; there this redox reaction proceeds according to
(since the Sn4+ ions act as network formers 〚16〛, they become highly immobile in the glass network); - • as a consequence, the convolution of the decreasing CSn2+ profile with the increasing CFe3+ profile, divided by the decreasing CFe2+ profile, results in a peak similar to that known for the Sn4+ profiles obtained by CEMS 〚12〛 (see Fig. 3).
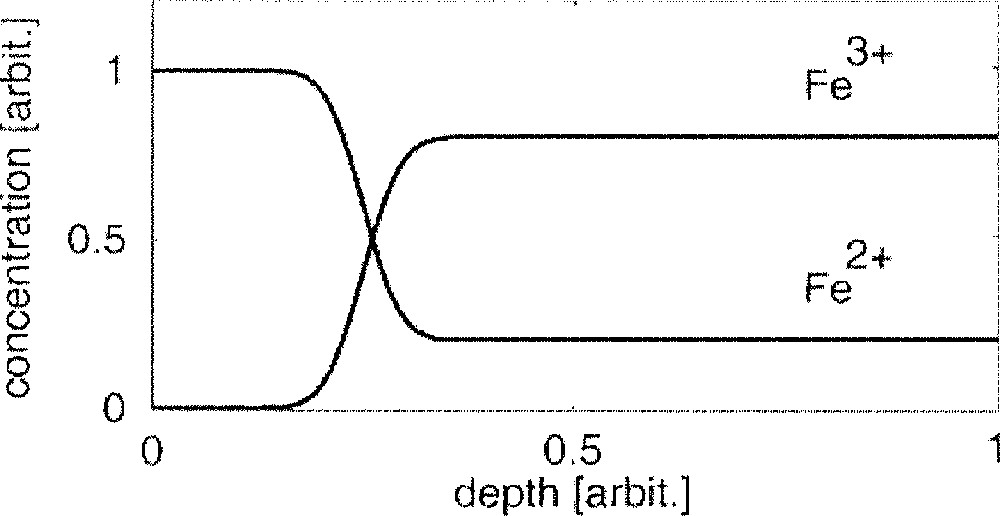
Schematic iron profiles (bath side) at t = 0 after the glass melt has entered the float chamber.
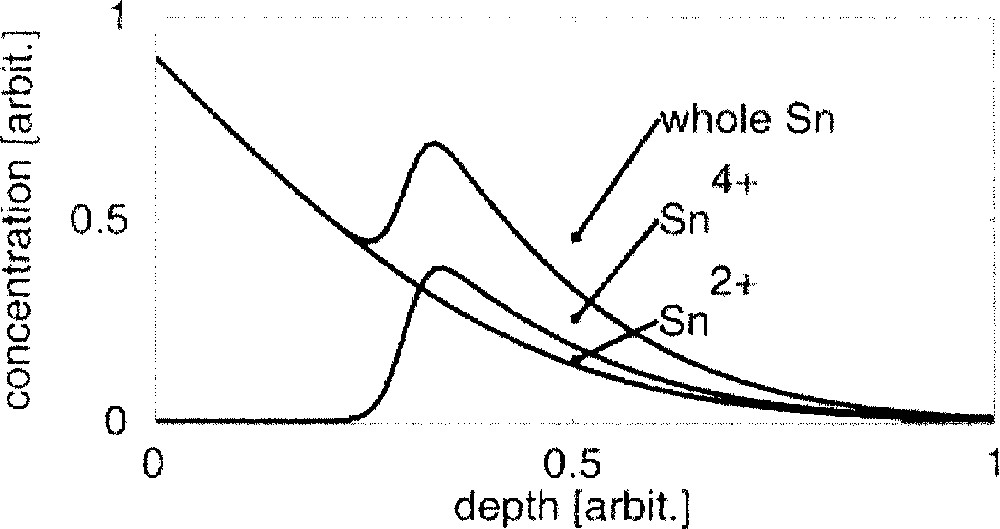
Model showing the tin hump as an interaction between diffusion and redox processes.
This diffusion-reaction model thus explains the occurrence of the tin hump in Fe2O3-rich float glasses under the assumption that the oxidation state of the glass surface changes drastically and rapidly when it enters the strongly reducing float chamber. Everything else follows as a consequence.
4 The phenomenon of bloom
It is generally accepted that the phenomenon of bloom is related to the oxidation of Sn2+ to Sn4+ during reheating of those float glasses in air, whose ‘tin count’ (determined by X-ray fluorescence spectrometry) shows a distinct value 〚1, 8〛. The Sn4+ acts as a network former in the glass structure 〚16〛, changing the glass properties in a superficial layer.
Fig. 4 shows an AFM image of a standard float glass with bloom. This glass has an overall Fe2O3 content of 0.13 wt% and had been annealed as a 100 mm × 100 mm sheet for 1 h at 670 °C, followed by a cooling with the natural furnace rate. The wave pattern produced at the surface is irregular, has a wavelength of ∼3 μm and shows an rms roughness of 65 to 75 nm. The occurrence of bloom is somewhat dependent on sample size, geometry, and the heating program. Annealing in reducing atmosphere does not produce bloom and borofloat glasses do not show this effect under any condition 〚15〛. However, within this work, bloom could be evidenced only on the surfaces of white soda-lime silicate float glasses with a low Fe2O3 content (≤ 0.13 wt%), whereas green and blue glasses with higher Fe2O3 contents (> 0.5 wt%) did not develop bloom.

AFM height mode image of a standard float glass surface (0.13 wt% Fe2O3) showing bloom after annealing for 1 h at 650 °C in air.
How can this Fe2O3-dependence be explained? Fig. 5 displays that the Sn in-depth profiles of the float glasses investigated in the as-received state are quite different in the first 100 nm from the surface. Whereas the silicate glasses with low Fe2O3 contents show SnO2 surface concentrations up to 7 wt% and a steep gradient in these profiles (curve 1: glass with 0.017 wt% Fe2O3), the SnO2 profiles of the borofloat and the silicate float glasses with high Fe2O3 contents have lower surface concentrations < 2.4 wt% and a much smoother decrease from the surface to the bulk (curve 2: glass with 1.80 wt% Fe2O3). After annealing these glasses for 1 h at 650 °C in air, this tendency becomes even stronger (curve 3: glass with 0.017 wt% Fe2O3). On the other hand, the mentioned annealing step smoothens the SnO2 profile of the Fe2O3-rich glasses even further (curve 4: glass with 1.80 wt% Fe2O3). Thus, one can conclude that during annealing in air a tin species is forced to diffuse from the interior to the surface in the case of the silicate float glasses with low Fe2O3 contents, whereas a diffusion process in the opposite direction obviously takes place in the case of the glasses with the high Fe2O3 contents.

SNMS tin in-depth profiles of two float glasses: curve 1, Fe2O3 content 0.017 wt%, as-received; curve 2, Fe2O3 content 1.80 wt%, as-received; curve 3, Fe2O3 content 0.017 wt%, 1 h at 650 °C; curve 4, Fe2O3 content 1.80 wt%, 1 h at 650 °C.
As already mentioned, a very strong and rapid change occurs in the oxidation state of the glass melt when it enters the float chamber, see also equations (1) and (2) and Fig. 2. There are mainly the Fe2+ ions that enable the penetration of Sn2+ ions into the glass melt by an ion exchange process. Since the total number of Fe2+ ions is very low in the case of a low-Fe2O3 glass, a small part of these Sn2+ ions can diffuse into the glass only. Consequently, a steep tin (mainly Sn2+) gradient is formed near the surface. In the case of a high-Fe2O3 glass, the total number of Fe2+ ions is high. This enables a far-reaching penetration of Sn2+ ions into the glass melt. A gradient in tin concentration does not occur near the surface, however, this glass tends to form an anomalous tin (Sn4+) hump in the micrometer region 〚9〛.
When a low-Fe2O3 glass is annealed in air, most of the Sn2+ ions near the surface are oxidized to Sn4+ and depletion in Sn2+ occurs there. This now causes an opposite gradient in the Sn2+ concentration with the consequence of a reversed Sn2+ diffusion from the interior to the surface. When reaching the surface region, these Sn2+ ions are also oxidized to Sn4+, finally forming a very high and steep tin (Sn4+) peak near the very surface. Since the Sn4+ ions act as network formers in the glass structure 〚16〛, they are highly immobile. When a high-Fe2O3 glass is annealed in air, the Sn2+ ions near the surface are also oxidized to Sn4+. However, the concentration of Sn2+ ions there is low and there is no steep gradient. Moreover, since also the Sn4+ hump in the micrometer region is formed, obviously most of the Sn2+ ions are trapped there as Sn4+ and a specific tin enrichment near the surface is unlikely. A tin diffusion process from the interior to the surface was also found by 〚4, 7, 17, 18〛.
The high-tin (Sn4+) hump near the very surface of the float glasses changes their properties strongly in the region < 100 nm 〚15〛. Thus, for example, the viscosity, the glass-transition temperature, and the Young’s modulus are increased, whereas the thermal expansion coefficient is decreased. In analogy to thin film technology, a simplified model was set up and a free buckling length of ∼2.3 μm could be estimated for the wrinkling of the bloom surface 〚15〛. This value is in reasonable agreement with the experiment (Fig. 4).
5 Conclusions
Different 4 mm thick commercial float glasses were investigated. A tin hump (satellite peak) between 6 and 8 μm from the glass surface could be evidenced only for Fe2O3-rich (> 0.5 wt%) silicate float glasses. To explain this anomaly, a diffusion-reaction model was developed under the assumption that the oxidation state of the glass surface changes drastically and rapidly when the oxidized glass melt enters the strongly reducing float chamber. The phenomenon of bloom, a greyish haze causing a microscopic wrinkling of the surface, was found on silicate glasses only with a low Fe2O3 content (< 0.13 wt%) after annealing them in air. In that case, a very high and steep tin (Sn4+) peak is formed near the surface (< 100 nm), mainly because of a reversed Sn2+ diffusion process from the interior to the surface. This high Sn4+ peak near the surface changes the properties strongly, leading finally to a buckling there.
Acknowledgements
The author wishes to thank the ‘Tin in float glass’ team: Drs G. Heide, C. Müller-Fildebrandt, D. Moseler, W. Meisel (Mainz) and Prof. F. Rauch (Frankfurt/Main). He also appreciates the financial support of the AiF (Köln), HVG (Frankfurt/Main), utilizing resources of the BMWi (Bonn).