1 Introduction
The use of controlled radical polymerization, CRP, is becoming more and more popular, largely because of its mild reaction conditions and the large scope of polymerizable monomers [1]. Emulsion polymerization is a widely used process to carry out conventional radical polymerization. However, the practice of CRP in emulsion is not straightforward [2, 3]. For example, stable free radical polymerization (SFRP) in emulsion is often poised by temperatures higher than 100 °C [4, 5] or inhibition periods corresponding to the time necessary to establish a persistent radical effect equilibrium [6–8]. Early experiments by Gaynor et al. [9] have demonstrated that butyl methacrylate can be polymerized in emulsion by atom transfer radical polymerization (ATRP). Careful elucidation of the polymerization mechanism by Qiu et al. [10] revealed that the partitioning of the catalyst between the non-polar organic phase and the aqueous phase is crucial. Despite the hydrophobicity of the ligand, the catalyst, both in its CuI and CuII form, is partially soluble in water under the polymerization conditions indicating that catalyst diffusion through the aqueous phase is possible. As the choice of ligand hydrophobicity is crucial, the choice of surfactant is also critical. In general, non-ionic surfactants were found to be efficient for colloidal stabilization of the polymer particles [11]. This is to be expected, as, due to the ionic nature of the catalyst and the corresponding ionic strength, electrostatic stabilization is likely to be poor. Adequate hydrophilic/lipophilic (HLB) balance is also a necessary criterion to insure latex stability in ATRP emulsion polymerization [12]. For the controlled polymerization of MMA, catalyzed by CuBr/dNbpy, an HLB of 17 was found to be optimal, and for the polymerization of BMA, stabilization was optimal with non-ionic surfactants Brij98 and Tween80. Nevertheless, colloidal stability of the formed latex is usually poor, even at low solid contents (15%) and in the presence of large amounts of surfactant (10%).
RAFT polymerization potentially offers the best opportunity for the development of an emulsion process, as it is applicable to a wide range of monomers, at temperatures below 100 °C and it is not based on a persistent radical scheme. In a preliminary report, we described the emulsion polymerization of styrene using S-(thiobenzoyl)thioglycolic acid as chain transfer agent (CTA) [13]. Because the carboxymethyl moiety is a poor leaving group, the level of control was found to be moderate, as shown by high polydispersity indices, PDI. In addition, it was not possible to reach high solids because of the poor colloidal stability of the system. Emulsion polymerization of styrene using dithiobenzoates as RAFT agents was studied in details by Monteiro et al. [14]. It was found that the rate of polymerization was significantly retarded by the presence of the RAFT agent, and radical exit from the particle was invoked to partly account for this phenomenon. Similar results were reported in miniemulsion polymerization by Lansalot et al. [15], illustrating the influence of entry and exit events and the presence of initiator derived chains on the outcome of the polymerization. In emulsion polymerization, a conspicuous red layer, consisting of low molecular weight dormant species swollen with monomer, was observed at the beginning of the polymerization [14]. Several strategies were employed to get rid of this red layer. Prescott et al. [16] reported that using acetone as co-solvent to assist the transport of the RAFT agent into seed particles allowed the formation of a latex in controlled fashion. Miniemulsion polymerization, whereby the hydrophobic RAFT agent is dispersed into nanosize droplets prior to polymerization, was also investigated by several groups. Butte et al. [17] described the RAFT miniemulsion of styrene and MMA using pyrrole-1-carbodithioic acid-phenylethyl ester as CTA. In both Butte [17] and Lansalot [15]’s papers, little is reported about the colloidal stability. However, it is clearly demonstrated that RAFT polymerization in comparison to other CRP techniques is the best approach for the production of controlled polymers in an emulsion process. Vosloo et al. [18] recently reported the miniemulsion polymerization of styrene using, inter alia, a dithiobenzoate terminated oligomer as hydrophobe. If the approach is very similar in essence to the one we used, the results are somewhat different. In Vosloo’s case, renucleation does not seem to be a significant problem, and there is no information about the aspect of the final dispersion. In our case, we observed the formation of unusual particles containing untouched macro chain transfer agent and hexadecane. This inconsistency might be attributed to an intrinsic difference in the colloidal stability of the initial miniemulsion. Careful evaluation of the colloidal stability of the miniemulsion polymerization by Tsavalas and De Brouwer [19, 20] indicates that the red layer is present for ionically stabilized miniemulsions and absent for miniemulsions stabilized with non-ionic surfactants. This behaviour, although not fully explained, is attributed by the authors to the in-situ formation of oligomers, whereas high molecular weight polymers are instantaneously formed in conventional radical miniemulsion polymerization. The initial idea underlying our work was to bypass the stage during which oligomers are produced by starting the polymerization with a macro RAFT agent. The addition of polymer in a miniemulsion [21, 22] has been reported to improve the nucleation, thus generating one-to-one copy between emulsion droplets and polymer particles. This technique was used with success in nitroxide mediated polymerizations by Pan et al. [23], and was also reported, in the case of RAFT, by Butte et al. with a pyrrolide-based macroCTA [17].
2 Results
2.1 RAFT polymerization of styrene in batch and in emulsion
For the sake of comparison, we first report bulk polymerization results. Using chain-transfer agents, CTA, 1 and 2 (Scheme 1 ), the RAFT polymerization of styrene was found to be controlled, as shown by a linear evolution of molecular weight with conversion, narrow molecular weight distribution (Fig. 1 ). At low conversion, Mw/Mn, PDI, is lower with 2 than 1 because the phenylethyl radical is a better leaving group than the carboxy methyl radical. Consequently, transfer between a propagating radical and 2 is faster than for 1.
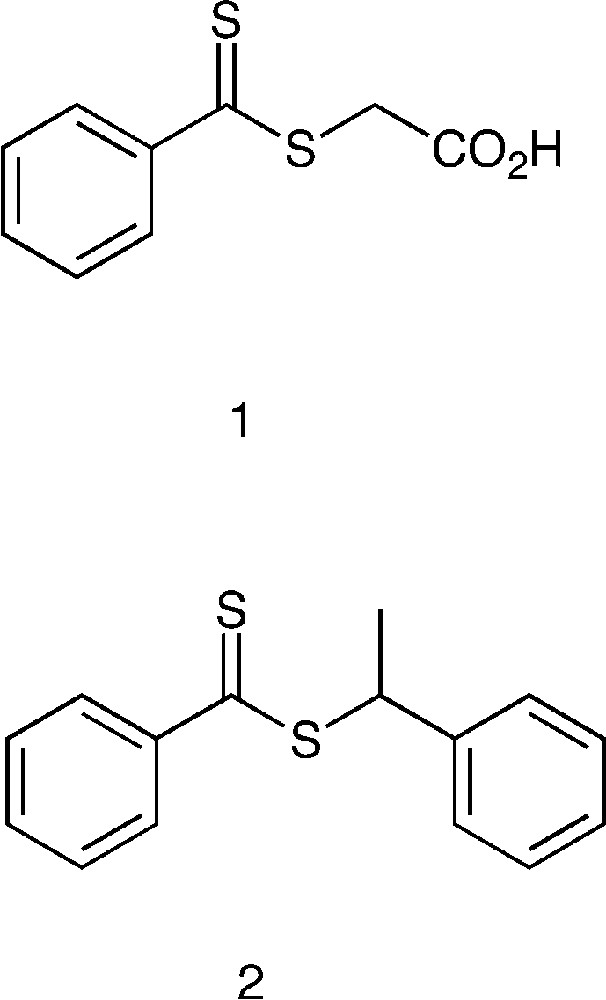

Bulk polymerization of styrene with CTA 1 (Mn: □, PDI: ) and 2 (Mn: ▴, PDI: △) at 110 °C. [Styrene] [1]: [AIBN] = 300:10:1.05; [styrene] [2]: [AIBN] = 300:10:0.98. The straight line corresponds to theoretical Mn, calculated from Mn = (104 [MON] × conversion)/[CTA].
The polymerization is relatively slow in both cases. At 110 °C, after 45 h of reaction, only 74% conversion is reached with 1 and 93% conversion with 2. There are two main reasons for this slow rate of polymerization. Rate decrease in RAFT polymerization is usually explained by the stability of the intermediate radical during the addition fragmentation process [24–26]. The rate was also slow because the radical initiator (AIBN) decomposed very fast at the polymerization temperature (t1/2 = at 110 °C). Therefore, very rapidly the radical flux was only sustained by the production of thermal radicals. We chose AIBN as polymerization initiator because we also used it in miniemulsion polymerization (see below). The RAFT polymerization of styrene conducted in bulk at lower temperature was even slower than at 110 °C.
CTA 2 could not be used in emulsion polymerization, as it is highly water insoluble. In contrast, CTA 1 could be used provided the polymerization was conducted in a basic medium in which the carboxylic group was ionised. The results for these polymerizations were already reported [13], and it was found that an intermediate chain transfer agent was probably formed in situ upon reaction of 1 with the initiator used in the polymerization (2,2′-azobis(2-methyl)propionamidine) dihydrochloride. However, all efforts to isolate, fully characterize or separately synthesize this intermediate chain transfer agent failed.
2.2 Oligomer synthesis for miniemulsion polymerization
For a miniemulsion polymerization to be stable, a hydrophobic compound is often added [27]. This hydrophobe prevents the Ostwald ripening of the miniemulsion droplets. A polymer, later referred as macroCTA, was prepared with CTA 1 in batch polymerization in order to be used as hydrophobe. The macroCTA was purified by three cycles of dissolution in toluene and precipitation in methanol in order to remove unreacted styrene, initiator and 1. After purification, the polymer molecular weight was Mn = 2800 g mol–1 (PDI = 1.1), whereas it was Mn = 2400 g mol–1 (PDI = 1.2) before purification. Short oligomers were also separated during the purification process. Before using this polymer as hydrophobe in the miniemulsion polymerization, it was necessary to check that the polymer could be extended by starting a new bulk polymerization of styrene (Table 1 and Fig. 2 ). The presence of around 10 wt% low molecular weight chains in the chromatogram (Fig. 2) is an indication of the presence of dead chains that cannot be avoided in a reversible transfer process. In general, the experimental molecular weight is below the theoretical one (Table 1), however a linear relationship in regards to conversion is still observed. This is not surprising, as in the calculation of theoretical molecular weight, the contribution of initiator derived chains and thermally generated chains become significant. The PDI for the final samples is quite large because it integrates both the contribution of the low molecular weight dead chains and the growing high molecular weight chains.
Chain extension of the macro CTA in bulk
Time (h) | Conversion (%) | Mn theor.a (g mol–1) | Mn exp. (g mol–1) | PDI |
0 | 0 | 2800 | 2800 | 1.1 |
1 | 32 | 8800 | 6000 | 1.4 |
4.5 | 58 | 13 600 | 9700 | 1.7 |
9 | 63 | - | - | |
24 | 80 | 17 500 | 12 100 | 1.8 |
a Theoretical Mn calculated from (104 × conversion × [styrene])/[macro chain transfer agent].
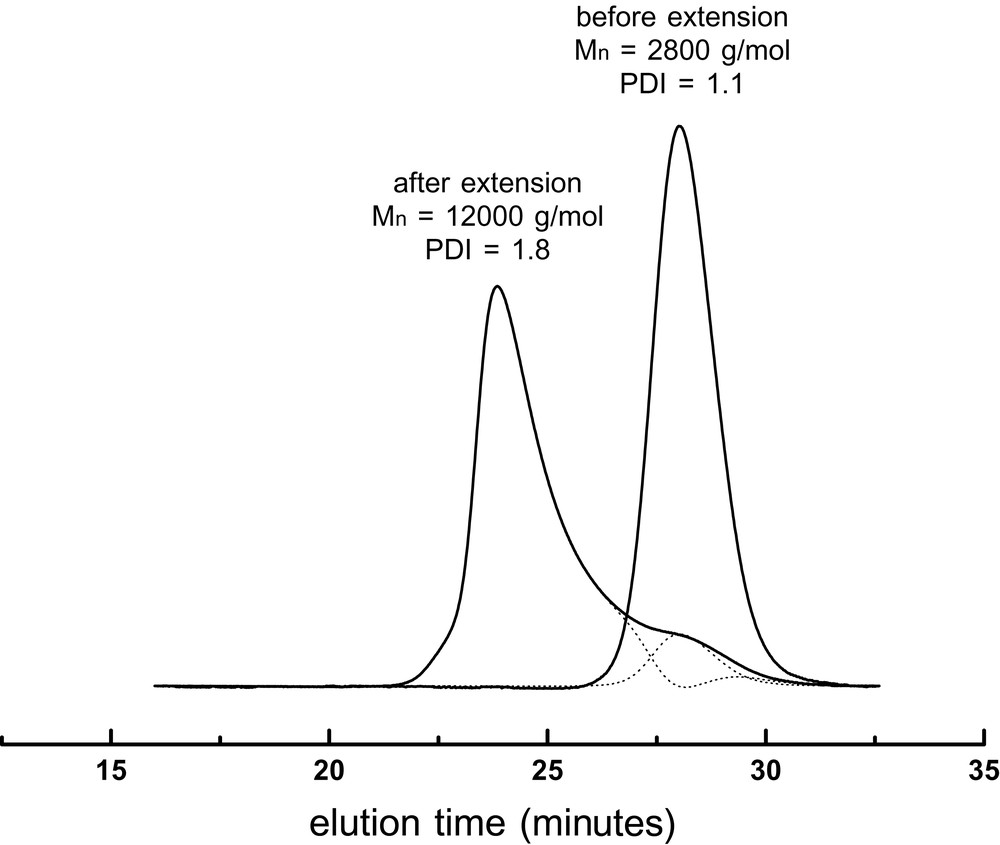
SEC traces of the polymers before and after extension. After extension, the trace could be deconvoluted into two peaks (dotted lines), one of which corresponds to 9.6% of the initial peak.
2.3 RAFT polymerization of styrene with 1 in miniemulsion
With miniemulsion polymerization, it is possible to polymerize in the presence of highly hydrophobic compounds such as 1 (under its acidic form) or 2. The chain transfer agent 1 is commercial therefore its use was initially favoured over the use of 2, as there was only few differences between both in bulk polymerization. The polymerization reached 87% conversion after 24 h at 85 °C therefore the polymerization proceeded at a significant higher rate than bulk polymerization, as expected for a dispersed polymerization. Mn linearly increased with conversion however it was systematically above its theoretical value and above 10 000 g mol–1 (Table 2 and Fig. 3 ). This behaviour can be explained by a low efficacy of CTA 1, and a low (initial) chain transfer constant for CTA 1. Extrapolating Mn versus conversion to zero conversion gives access to the molecular weight at zero conversion, which is equal to (104 × [styrene])/(Ctr* [1]), where Ctr is the chain transfer constant to the initial chain transfer agent (and not to the macrochain transfer agent) and [Sty] is the initial styrene concentration. From this expression, we found that the apparent Ctr ~ 2. Such a low value for the apparent chain transfer constant is not observed in the case of the bulk polymerization (see above: the molecular weight at 0 conversion is close to 0) even when the polymerization is conducted at 85 °C, and this phenomenon should be attributed to the presence of physical limitations to the RAFT process in dispersed medium. For example, Monteiro et al. [14] proposed that radical exit after fragmentation is responsible for strong retardation, which is likely considered the hydrophilicity of the carboxymethyl radical. In terms of colloidal stability, our results differ from those reported by Monteiro et al., in the sense that no red layer was observed in these polymerizations. This is probably due to the large amount of hexadecane used (> 5%), because when less hexadecane was used (1–3% relative to monomer), a red layer was observed concommitantly to high amounts of coagulum. Instability in controlled radical polymerization in miniemulsion has also been attributed to superswelling by Luo et al. [28].
RAFT miniemulsion polymerization of styrene, using 1 as CTA. [styrene]: [1] [init] = 200:1:0.1. Styrene: 103 g l–1, hexadecane 10% (wt:wt, relative to monomer), SDS 5 g l–1, NaHCO3 = 0.3 g l–1. Init.: 4,4′-azobis(4-cyanovaleric acid), T = 85 °C
Time (h) | Conversion | Mn theor.a | Mn exp | PDI | dpb (nm) | s.c.c (%) |
(%) | (g mol–1) | (g mol–1) | ||||
0 | 0 | 0 | 0 | — | 284 | 0.53 |
0.5 | 5.2 | 1200 | 12 200 | 1.8 | 314 | 1.03 |
1.75 | 21.2 | 4900 | 15 900 | 1.9 | 304 | 2.57 |
15 | 44.9 | 10 200 | 23 500 | 1.8 | 314 | 4.84 |
17 | 56.2 | 12 900 | — | — | 312 | 5.92 |
19 | 73.5 | 16 800 | 25 500 | 1.8 | 274 | 7.58 |
21 | 80.7 | 18 500 | — | — | 274 | 8.27 |
24 | 86.8 | 19 900 | 32 300 | 1.7 | 274 | 8.86 |
a Theoretical Mn calculated from (104 × conversion × [styrene])/[macro chain transfer agent].
b Hydrodynamic particle diameter.
c Solid content, determined by gravimetry.

Miniemulsion polymerization of styrene using 1 as RAFT agent (Mn: ■, PDI: □) at 85 °C. [Styrene] [1]: [AIBN] = 200:1:0.1. The straight line corresponds to theoretical Mn, calculated from Mn = (104 [MON] × conversion)/[1].
2.4 RAFT polymerization of styrene with 2 in miniemulsion
The RAFT polymerization of styrene in miniemulsion is controlled, and occurs at rates significantly higher than with 1 (Fig. 4 , Table 3). The rate increase has been attributed by others as the decrease of the probability of radical exit with the enhanced hydrophobic character of the phenethyl radical [14, 15]. Experimental molecular weights are slightly lower than predicted ones because of the contribution of the initiator derived chains. This is also seen in the chromatograms (Fig. 5 ), where the peak is displaced toward higher molecular weights as conversion increases, but the peak tails toward low molecular weights, indicative of the presence of terminated chains and new radical chains generated continuously in the reaction.

Miniemulsion polymerization of styrene using 2 as RAFT agent (Mn: ■, PDI: □) at 80 °C. [Styrene] [1]: [AIBN] = 500:1:0.1. The straight line corresponds to theoretical Mn, calculated from Mn = (104 [MON] × conversion)/[2].
RAFT miniemulsion polymerization of styrene, using 2 as CTA. [Styrene]: [2] : [init] = 500:1:0.1. Styrene: 94 g l–1, hexadecane 11% (wt:wt, relative to monomer), SDS 5 g l–1, NaHCO3 = 0.2 g l–1. Init.: 4,4′-azobis(4-cyanovaleric acid), T = 80 °C
Time | Conversion | Mn theor. a | Mn exp. | PDI | dp b | s.c. c |
(min) | (%) | (g mol–1) | (g mol–1) | (nm) | (%) | |
0 | 0 | 0 | 0 | — | 136 | 0.71 |
15 | 1.70 | 900 | 1000 | 1.1 | 130 | 0.87 |
40 | 11.9 | 6200 | 4973 | 1.3 | 112 | 1.83 |
60 | 18.4 | 9600 | — | — | 107 | 2.44 |
100 | 34.5 | 18 000 | 14 000 | 1.4 | 103 | 3.96 |
160 | 50.2 | 26 500 | — | — | 108 | 5.44 |
220 | 59.9 | 31 500 | 25 000 | 1.5 | 106 | 6.36 |
280 | 66.2 | 34 500 | — | — | 108 | 6.95 |
340 | 68.5 | 36 000 | 30 000 | 1.5 | 105 | 7.17 |
405 | 70.7 | 37 000 | — | — | 108 | 7.37 |
460 | 73.8 | 38 500 | 31 000 | 1.5 | 110 | 7.66 |
a Theoretical Mn calculated from (104 × conversion × [styrene])/[macro chain transfer agent]).
b Hydrodynamic particle diameter.
c Solid content, determined by gravimetry.

SEC traces of the polystyrene prepared in miniemulsion polymerization with 2 (see Table 3). The number above each peak indicates the corresponding conversion.
In this case, as in the case of 1, no red layer or flocculation was observed as the amount of hydrophobe (hexadecane) used to stabilize the miniemulsion is high (11% relative to monomer). Lower amounts of hexadecane also resulted in latex destabilization. The particle size, as measured by dynamic light scattering, decreased when conversion increased, seemingly indicative of renucleation. However, this result must be treated with cautiousness since the miniemulsion droplets might be affected by the dilution required by the light scattering experiment. We further confirmed this phenomenon using transmission electron microscopy of the latex (Figs. 6 and 7 ). At 11% conversion, the latex is constituted of a monodisperse assembly of particles. The number average diameter, calculated from 300 measurements, is 83 nm (σ = 12 nm). The particle size is significantly smaller than the one measured by light scattering, as the particles are not anymore swollen by styrene in the TEM instrument. At 74% conversion, the latex is polydisperse, with an average diameter of 101 nm (σ = 47 nm). A quite large population of small particles is present indicative of renucleation or of droplet coalescence and scission. However, the polymerization is controlled; therefore the chain transfer agent was able to be transported from the original droplets to these newly generated droplets. To further investigate this point, we devised an experiment where the CTA is polymeric, and cannot diffuse through the aqueous phase.

TEM picture of a latex made by miniemulsion polymerization with 2 (11% conversion, third entry in Table 3).
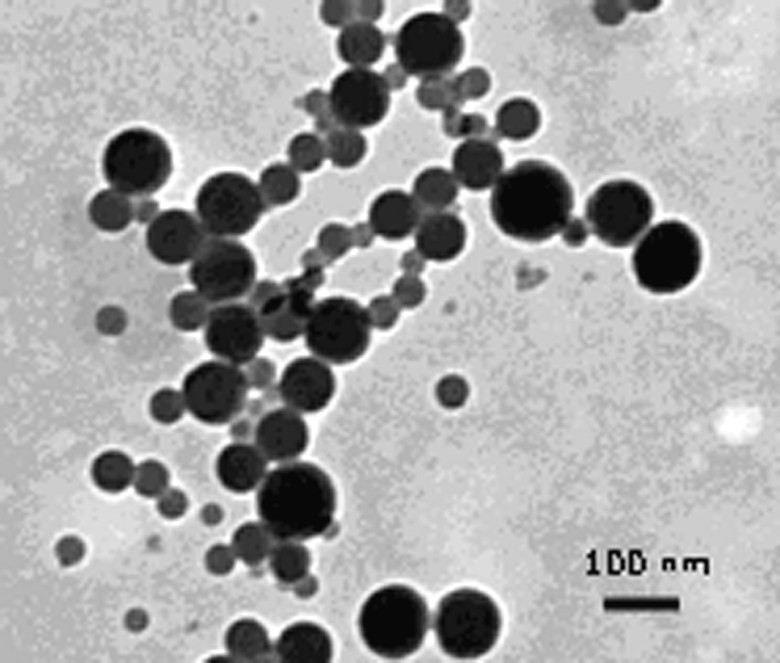
TEM picture of a latex made by miniemulsion polymerization with 2 (74% conversion, last entry in Table 3).
2.5 RAFT polymerization of styrene with a macroCTA in miniemulsion
The macroCTA used for this set of experiments is the one that was chain extended (see Table 1, first entry). Prior to polymerization experiments, we prepared a styrene miniemulsion (10% v:v) using the macroCTA as hydrophobe (5.1% w:w relative to styrene) and SDS as surfactant (5 g l–1). The miniemulsion was prepared by sonicating for 2 min with a high-power probe (see experimental section). The miniemulsion was destabilized (by a freeze-thaw cycle), the water was separated and the bulk polymerization of the organic phase was then triggered with AIBN. The chain extension process occurred similarly in the absence and in the presence of the miniemulsion step, indicating that the sonication does not adversely affect the integrity of the macroCTA.
All SDS-stabilized miniemulsions were initially stable, even those formed in the presence of V50 (2,2′-azobis(2-methylpropionamidine)dihydrochloride), a cationic initiator. The amount of initiator used in RAFT polymerization is small in order to limit the generation of dead chains; therefore, the cationic initiator concentration was only 45 mg l–1, too low to destabilize the anionically stabilized emulsion. With V50, the polymerization was not controlled (entry 9, Table 4): size-exclusion chromatography, SEC, indicated that the macroCTA was unreacted, and very high molecular weight polystyrene was produced (see the bimodal distribution in Fig. 8 ). At the end of the polymerization, a significant amount of floc of pink colour was obtained (around 10%), which was analysed as being unreacted macroCTA. With AIBN and V501, the latexes were stable, and the SEC chromatograms were constituted of three peaks: untouched macroCTA, high-molecular-weight polystyrene and an intermediate peak (Fig. 9 ). The intermediate peak is shifted toward lower elution time as conversion progresses, seemingly indicating that it corresponds to extended macroCTA. It should also be noted that in all cases, the particle size decreased with conversion. This set of observations all point out toward the presence of renucleation during the polymerization. Renucleation is predominant with a cationic water-soluble initiator and less pronounced with AIBN. Renucleation was observed because the concentration of SDS used was quite high (5 g l–1). This high concentration was selected to improve the stability of the miniemulsion. When lower amounts of SDS were used (entries 14–27 in Table 4), the renucleation was less pronounced, as expected, but the polymerization became very slow and the yields very low (26% conversion in 30 h for entry 27). There is a competition between the particles containing RAFT agents where the polymerization is slow and the uncontrolled particles where a fast polymerization occurs. One should ask what happens to the macromonomer droplets when they are not nucleated. The TEM pictures showed that the latexes where constituted of polydisperse particles with an average size of around 150 nm. It is conceivable that the smallest particles of this distribution are in fact containing only untouched macromonomers. To further investigate this issue, polymerizations were conducted with hexadecane in addition to the polystyrene macroCTA. A miniemulsion was prepared by adding 5% w:w of hexadecane to the recipe described in entry 10 of Table 4. There was no difference between the reactions performed with and without hexadecane. However, the TEM pictures indicated the presence of two types of particles (Fig. 10 ). The first type includes plain polystyrene spherical particles, whereas the other one consists of nanocapsules. We believe that these nanocapsules are in fact untouched macroCTA containing particles, in which the hexadecane and the polystyrene are phase separated [29]. This unusual morphology is obtained because the ratio hexadecane:macroCTA is high (close to 1:1 in weight) and the macroCTA is terminated by a carboxylic group which should be in the aqueous phase at the slightly basic pH at which the polymerization is conducted. This indicates that the polymerization is clearly compartmentalized in between controlled and uncontrolled nanoreactors, but that the monomer diffuses wherever reaction depletion occurs. Therefore, when using RAFT agent 2 in miniemulsion, it is likely that diffusion of the agent through the aqueous phase, albeit very slow, is enough to ensure that all particles, even those generated by renucleation, contain the RAFT agent.
RAFT miniemulsion polymerization of styrene, using a macroCTA. [Styrene]: [macroCTA]: [Init] = 555:1:0.5. Styrene: 103 g l–1, K2CO3 = 0.25 g l–1, T = 85 °C
Entry | Time | SDS | Init. | Conversion | Mn theora | Mn exp. | PDI | dpb | s.c.c |
(h) | (g l–1) | (%) | (g mol–1) | (g mol–1) | (nm) | (%) | |||
1 | 0 | 5 | V5014 | 0 | 2800 | 2800 | 1.2 | 182 | 0.92 |
2 | 0.5 | 5 | V5014 | 4 | 5400 | 5900 | 1.2 | 180 | 1.32 |
3 | 1.75 | 5 | V5014 | 27 | 19 000 | 24 000 | 1.9 | 134 | 3.46 |
4 | 3 | 5 | V5014 | 47 | 28 000 | 37 000 | 3.0 | 120 | 5.27 |
5 | 4 | 5 | V5014 | 57 | 33 000 | 45 000 | 3.5 | 126 | 6.21 |
6 | 5 | 5 | V5014 | 67 | — | — | — | 122 | 7.11 |
7 | 7.5 | 5 | V5014 | 77 | 43 500 | 58 500 | 3.3 | 127 | 8.03 |
8 | 0 | 5 | V505 | 0 | 2800 | 2800 | 1.2 | 234 | 0.80 |
9 | 91 | 5 | V505 | 91 | 51 200 | 611 000 | 2.0 | 96 | 9.36 |
10 | 0 | 5 | AIBN | 0 | 2800 | 2800 | 1.2 | 168 | 0.88 |
11 | 1 | 5 | AIBN | 16 | 11 500 | 12 000 | 8.2 | 164 | 2.43 |
12 | 3 | 5 | AIBN | 53 | 31 000 | 33 000 | 9.4 | 119 | 5.83 |
13 | 5 | 5 | AIBN | 92 | 56 200 | 94 000 | 12.1 | 101 | 9.9 |
14 | 0 | 2.5 | V5014 | 0 | 2800 | 2800 | 1.2 | 175 | 0.56 |
15 | 3.5 | 2.5 | V5014 | 20 | 13 000 | 16 800 | 1.7 | 159 | 2.39 |
16 | 22 | 2.5 | V5014 | 51 | 28 700 | 43 700 | 2.0 | 152 | 5.16 |
17 | 30 | 2.5 | V5014 | 71 | 39 200 | 48 900 | 2.6 | 153 | 7.00 |
18 | 0 | 2.05 | V5014 | 0 | 1800 | 1800 | 1.2 | 175 | 0.56 |
19 | 3.5 | 2.05 | V5014 | 20 | 13 000 | 17 000 | 1.7 | 159 | 2.39 |
20 | 22 | 2.05 | V5014 | 51 | 28 700 | 44 000 | 2.0 | 152 | 5.16 |
21 | 30 | 2.05 | V5014 | 71 | 39 100 | 48 900 | 2.6 | 153 | 7.00 |
22 | 0 | 1.5 | V5014 | 0 | 2800 | 2800 | 1.2 | 222 | 0.57 |
23 | 1.25 | 1.5 | V5014 | 4 | 4400 | 4800 | 1.2 | 222 | 0.90 |
24 | 3.5 | 1.5 | V5014 | 10 | 7600 | 7700 | 1.2 | 231 | 1.45 |
25 | 6 | 1.5 | V5014 | 13 | 9300 | 10 200 | 1.2 | 222 | 1.76 |
26 | 24 | 1.5 | V5014 | 18 | 11 600 | 23 000 | 1.3 | 244 | 2.16 |
27 | 30 | 1.5 | V5014 | 26 | 16 800 | 26 000 | 1.4 | 261 | 2.90 |
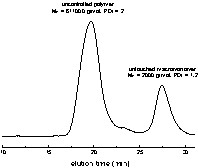
SEC chromatogram of the miniemulsion polymerization initiated by V50 (entry 9, Table 4).
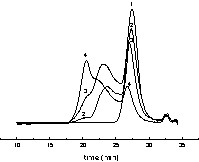
SEC chromatogram of the miniemulsion polymerization initiated by AIBN in the presence of macromonomer. 1: 0% conversion (entry 10, Table 4), 2: 16% conversion (entry 11, Table 4), 3: 53% conversion (entry 12, Table 4), 4: 92% conversion (entry 13, Table 4).
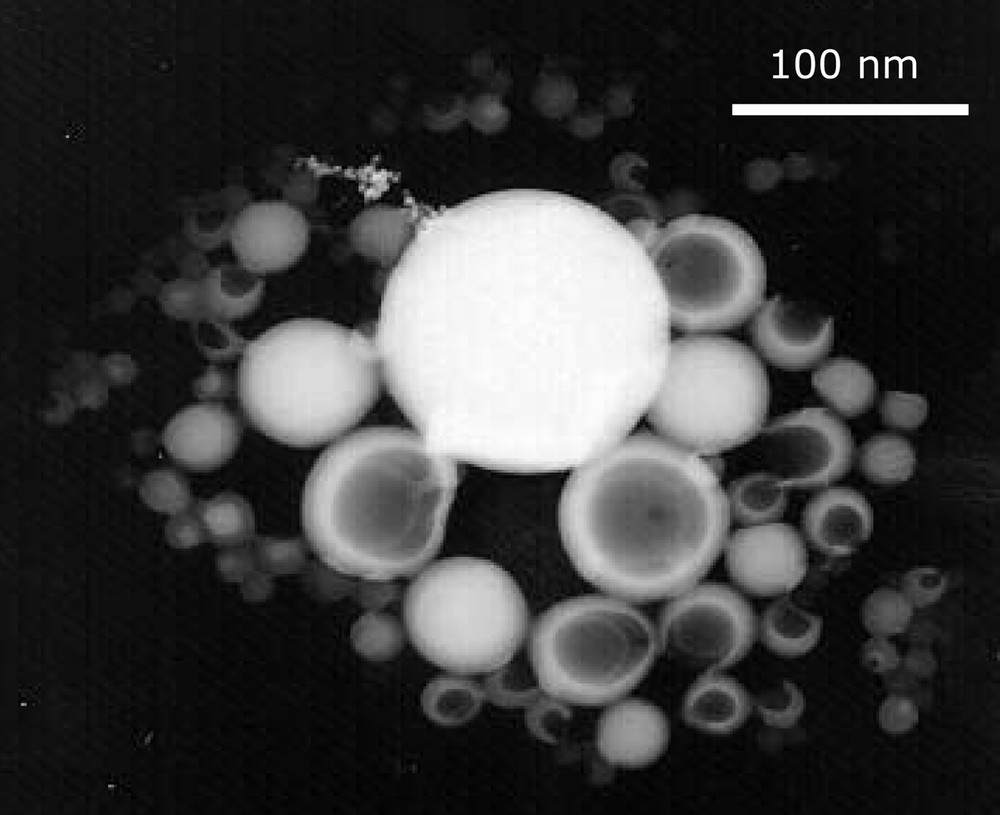
TEM picture of a latex made by miniemulsion polymerization at 43% conversion. [Styrene]: [macroCTA]: [AIBN] = 512:1:0.1, styrene = 124 g l–1, SDS = 5 g l–1 and K2CO3 = 0.25 g l–1, T = 85 °C.
3 Conclusion
In this paper, miniemulsion polymerizations of styrene in the presence of two reversible addition-fragmentation chain-transfer (RAFT) agent were studied. By comparing the polymerization in bulk to the polymerization in miniemulsion, the polymerization rates are higher in the miniemulsion process, and the level of control is lower. Best results were obtained with RAFT agent 2 (compared to 1) because of the stabilization of the leaving radical in the addition-fragmentation step. It was possible to use a macroCTA as hydrophobe to stabilize the miniemulsion. The polymerization is devoid of floc, but a competitive process occurs between RAFT polymerization in miniemulsion droplets and generation of new particles where uncontrolled polymerization occurs.
4 Experimental section
4.1 Materials
Styrene (Aldrich, 99%) was distilled under argon and stored at –40 °C. The water was ultrapure grade (Purite Analyst 25, ρ = 18.2 MΩ cm). Radical initiators (4,4′-azobis-4-cyanovaleric acid (V501), 98%, Fluka; azobisisobutyronitrile, AIBN, 98%, Aldrich; 2,2′-azobis(2-methylpropionamidine)dihydrochloride (V50), Wako chemicals), radical inhibitor BHT (2,6-di-tert-butyl-4-methylphenol, 99%, Sigma) and RAFT agent 1 (98%, Aldrich) were used without further purification.
Conversion was followed by gravimetry, and particle sizes were measured using a Malvern Autosizer 4800 light scattering instrument equipped with a 50-mW laser. Particle size distribution was also followed on a FlowFFF from FFF Corp, equipped with a static light scattering detector, MiniDawn from Wyatt Technology. Floc amount was obtained as the percent amount of polymer left in the reactor after drainage of the latex, plus the percent amount of polymer that could not pass through a quartz-wool filter. TEM pictures were made on a Philips CM 120 instrument and CryoSEM pictures on a Philips XL 30 FEG instrument equipped with a Cryotransfer CT 1500 from Oxford instruments. SEC measurements were carried out on a Waters instrument equipped with two linear mixed bed Shodex columns and a RI. The SEC was calibrated with PS standards.
4.2 Raft Agent 2
1.06 g (5.0 mmol) of RAFT agent 1 is dissolved in 40 ml of an aqueous solution of NaOH (10 g l–1). 0.76 g (5.5 mmol) of 1-phenylethyl thiol is added to this solution at room temperature. After 2-h reaction, RAFT agent is separated from the solution. The product is extracted with ether (1 × 60 ml, 1 × 30 ml). The organic phase is washed with an aqueous solution of NaOH 0.1 N (3 × 30 ml) and water (3 × 30 ml). The organic phase is dried over MgSO4 filtered and evaporated. 1.14 g (88%) of RAFT agent 2 is obtained, under the form of red oil.
4.3 Miniemulsion polymerization with 1
0.204 g of 1, 2.0 g of hexadecane are dissolved in 22 g of styrene. 1.0 g of SDS is dissolved in 190 g of water, and this solution is added to the organic phase. The mixture is stirred magnetically for 20 min and is then emulsified with a sonicator (Branson 600W) for 3 min. The dispersion is then degassed by nitrogen bubbling for 30 min, and initiator (V501, 0.13 g) and NaHCO3 (0.05 g) are added. The polymerization is triggered by heating at 85 oC, under mechanical stirring (300 rpm).
4.4 Miniemulsion polymerization with 2
0.100 g of 1, 3.0 g of hexadecane are dissolved in 20 g of styrene. 1.5 g of SDS are dissolved in 18 g of water, and this solution is added to the organic phase. The mixture is stirred magnetically for 20 min and is then emulsified with a sonicator (Branson 600W) for 3 minutes. The dispersion is then degassed by nitrogen bubbling for 30 min, and initiator (V501, 0.1 g) and NaHCO3 (0.008 g) are added. The polymerization is triggered by heating at 85 oC, under mechanical stirring (300 rpm).
4.5 Miniemulsion with a macroCTA
1.0 g of macroCTA is dissolved in 20 g of styrene. 0.3 g of SDS are dissolved in 190 g of water, and this solution is added to the organic phase. 0.3 g de SDS are dissolved in 190 g of water and are added to the styrene solution. The mixture is stirred magnetically for 20 min and is then emulsified with a sonicator (Branson 600W) for 3 min. The dispersion is then degassed by nitrogen bubbling for 30 min, and initiator (V501, 0.1 g) and NaHCO3 (0.005 g) are added. The polymerization is triggered by heating at 85 oC, under mechanical stirring (300 rpm).