1 Introduction
Synthetic zeolites are normally produced as a fine crystalline powder. Prior to their use, the powder is usually formed into spheres, tablets and extrudates by the addition of non-zeolitic binders. The binding additives provide the zeolite agglomerates with high mechanical strength and attrition resistance. However, since the binders are typically present in amounts of up to 50 wt.% of zeolite, they dilute the adsorption properties of the zeolite and can block the zeolite pores. Thus, the preparation of binderless zeolite agglomerates with high mechanical stability and open structures to ensure short diffusion paths is of great technological importance. For some applications, e.g. sensors and membranes, a thin zeolite layer supported on a substrate, is beneficial. In this section, a short review over some recent developments in the preparation of supported zeolite films and self-bonded zeolite agglomerates will be made.
The continuity, homogeneity, intactness and lack of cracks and pinholes are essential for the optimal performance of supported zeolite films. Zeolite films prepared by direct hydrothermal treatment are often discontinuous, rough and their properties are difficult to control. Nevertheless, there are numerous examples in the scientific literature concerning such syntheses, but to review those works is beyond the scope of this introduction section. The contact between the support and the zeolite layer is of paramount importance for the properties of the growing zeolite films and efforts have been devoted to the development of procedures for preliminary deposition of monolayers of zeolite seeds on the supports. Upon hydrothermal treatment with synthesis mixtures these seeds induce homogeneous crystallization yielding continuous zeolite films with a good adhesion to the substrate. Methods have also been developed to deposit preformed zeolite crystals that eventually would assemble into close-packed films. However, in these latter syntheses, secondary crystal growth is normally necessary to densify the zeolite layers.
The first example of zeolite film synthesis realized by secondary growth of pre-deposited nanoseeds on the support has been reported by Tsapatsis et al. [1]. One of the most widely used method for deposition of seed crystals is the seed-film method which will be discussed in detail in the next section [2]. In brief, the substrate surface is charged modified by a cationic polymer, negatively charged colloidal zeolite crystals are then adsorbed and the seeds are induced to grow into a continuous dense film by hydrothermal treatment with a fresh synthesis solution or gel. Colloidal zeolite crystals have also been deposited on flat supports by spin-coating [3,4]. The thickness of the spin-on films can be controlled to a certain extent by increasing the spin-coating steps. However, although being smooth, the films are composed of discrete non-intergrown crystals, which might be a drawback for some applications. Continuous films of the deposited by spin-coating seeds may be obtained by a secondary crystal growth. Further, preformed zeolite crystals have been coated onto beads and silica fibers by laser ablation [5,6]. The crystals deposited are considered as seeds, which, upon post-hydrothermal treatment, grow into continuous films. In the latter reference, even hollow zeolite tubes were obtained after pulling out the silica fibers. Despite the merits of the laser ablation method, the technique is quite exotic and cannot be applied in many research laboratories. Another unconventional method to attach positively charged colloidal zeolite crystals (the zeta potential being controlled by the pH of the media) is by electrophoretic deposition [7]. Both zeolite coated carbon fibers and hollow zeolite tubes obtained after carbon fiber combustion, were obtained with smooth and uniform zeolite coating. The electrophoretic deposition has also been used to prepare self-standing zeolite Y films, unfortunately with weak mechanical stability [8]. In this work, after depositing zeolite Y using commercial zeolite powders, the films were densified by secondary crystal growth. Preformed zeolite powders have also been used to prepare zeolite layers on quartz fibers by firstly silicate coating the fibers followed by dip-coating with a zeolite slurry [9] or on cellulose fibers after pretreating the fibers with NaOH, KOH or Na2SiO3 [10]. In another work, preformed zeolite crystals have been assembled into monolayers on glass and mica supports by an independent tethered of two different functional groups onto the zeolite and the substrate, followed by covalent linking of the two tethered functional groups [11].
The electrostatic zeolite seed adsorption has been used to prepare solely zeolite structures as well. Thus, after adsorbing silicalite-1 seeds on cellulose acetate filter membrane, the composite obtained was either treated by the vapor phase method or hydrothermally treated with silicalite-1 synthesis solution to yield self-supporting zeolite membranes with sponge-like architecture [12]. Seeds have been electrostatically deposited on the surface of mesoporous silica spheres and after ordering the spheres into a three-dimensional array by sedimentation followed by hydrothermal treatment, the seeds have grown at the expense of silica from both the mesoporous spheres and the external solution resulting in macroporous zeolite monoliths with high mechanical strength [13]. The electrostatic deposition of seeds may be repeated several times (the layer-by-layer method) and ordered macroporous zeolite monoliths have been prepared by assembling seed-coated latex beads into close-packed structures and subsequent calcination [14].
Preformed colloidal silicalite-1 crystals have been used for the preparation of other all zeolite macroscopic structures with hierarchical porosity using e.g. bacterial threads, starch gels and polymers solidified in molds as templates determining the macro shape of the products and their secondary porosity [15–17]. Preformed zeolite crystals have been compressed under high pressure followed by secondary crystal growth using microwave radiation to synthesize self-standing optically transparent silicalite-1 membranes of controlled mesoporosity [18].
Finally, zeolite self-bonded structures have been prepared by direct hydrothermal synthesis in the presence of macrotemplates without any pre-treatment procedures. Preformed into various monoliths polyurethane foams have been successfully zeolitized with very high efficiency of synthesis gel utilization [19]. ZSM-5 mesoporous monoliths have been prepared using carbon aerogel as a donator of uniform mesopores and monolithic appearance of the materials [20].
This introduction review is far from being complete. Nevertheless, the large number of papers devoted to the preparation of supported and self-bonded zeolite structures that appeared during the last decade is indicative of the intense research in the area. In this account, authors’ contribution to the field will be discussed.
2 Results and discussion
2.1 Supported molecular sieve structures
Supported molecular structures are structures comprising a support on top of which a molecular sieve layer is grown. The support determines the shape and the dimensions of the zeolite layer and, as the zeolite layer is usually very thin, provides the molecular sieve coating with mechanical stability. In some of the examples that will be given (e.g. carbon fibers), the support has been removed after the zeolite synthesis by combustion and strictly the zeolite structures obtained may be termed as self-bonded. However, those materials are conceptually related to supported zeolites and therefore will be described in this section. Two types of supports for the deposition of molecular sieves will be considered, flat and fibrous, and the influence of the support type and synthesis conditions on the composite properties will be summarized. Normally, the films prepared by the seed-film method were of superior quality compared to in situ deposited films. A representation of the general procedure for preparing zeolite supported films using the seed-film method is given in Fig. 1.
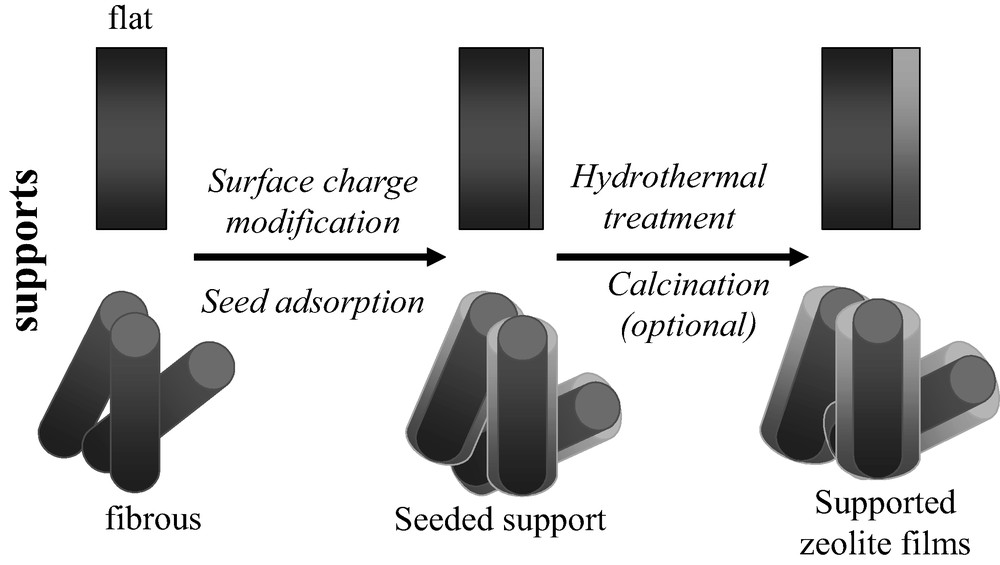
Schematic illustration of the general procedure for synthesis of supported zeolite films by the seed-film method.
2.1.1 Zeolite films on flat supports
Metal substrates are convenient supports for zeolite film deposition due to their hardness, adjustable size and thickness, resistance in zeolite synthesis solutions, etc. A systematic study of the influence of the metal substrate chemical composition on the in situ crystallization of zeolite ZSM-5 and Y films was performed in Ref. [21]. It was found that pre-cleaning of the bare supports was essential to obtain a zeolite film using some substrates (e.g. pig-iron and 08KP steel), whereas removal of surface contaminations did not result in film formation with others (4 × 18H12 steel and tin alloy). The effect of chemical composition on film formation was further studied utilizing pure metal substrates. To summarize the results, substrates with high values of surface tension (Cu, Ni and Ag) were found suitable for in situ zeolite deposition. Additional findings were that the surface imperfections were favorite locations for zeolite nucleation and the crystals on the support had a grain-like morphology with a smaller crystal size compared to bulk crystals [21,22].
To minimize the effect of the support chemical composition as well as to ensure crystallization of well-intergrown homogeneous zeolite films, the seed-film method, already mentioned in the introduction, was developed. Two examples will be considered here, the synthesis of silicalite-1 films on gold substrates [23,24] and the synthesis of template-free ZSM-5 on quartz [25]. To adsorb silicalite-1 colloidal crystals on gold substrates, the seed-film method was modified by an additional step, namely an initial adsorption of γ-mercaptopropyltrimethoxysilane followed by its hydrolysis in acidic media. This step was necessary to obtain a negative surface charge of the Au support to facilitate subsequent adsorption of either cationic polymer [23] or positively charged silicalite-1 crystals obtained by the addition of strongly acidic cation exchange resin [24]. The thickness of the silicalite-1 films grown was in the range 250–600 nm. The films were homogeneous and firmly attached to the substrate surface. The latter was verified by exposing the samples to ultrasonic treatment in water. No film detachment or peeling was observed by SEM after the treatment. The presence of the seeded substrates in the synthesis solution did not substantially influence the zeolite crystallization except that a somewhat shorter induction time was observed for the bulk crystallization in the presence of support. The adsorption of seeds was essential to obtain a continuous zeolite layer. Experiments performed using silane-modified gold substrates without subsequent seed adsorption resulted in isolated silicalite-1 crystals on the support. XRD analysis showed that the seed crystals were adsorbed on the surface with a preferred orientation of the b axis perpendicular to the surface and that the orientation was gradually lost during the film growth.
Further, ZSM-5 films crystallized from template-free synthesis were prepared on quartz substrates [25]. The seeded substrates were calcined after the adsorption step to remove the TPA cations occluded in the seed crystals. The benefit from the template-free synthesis is that the pores of the ZSM-5 films grown are already open and no subsequent calcination is required. In contrast to the syntheses from clear solutions, which resulted in thin films, this synthesis employed synthesis gels and the films formed on the substrates were thicker, up to 3.5 μm. A SEM-image of ZSM-5 film grown on quartz support is shown in Fig. 2. Thinner films were obtained by the addition of seeds in the synthesis gels with the thickness decreasing with an increase in the seeds amount. Film dissolution was observed upon prolonged exposure of the substrate after the film growth has discontinued.
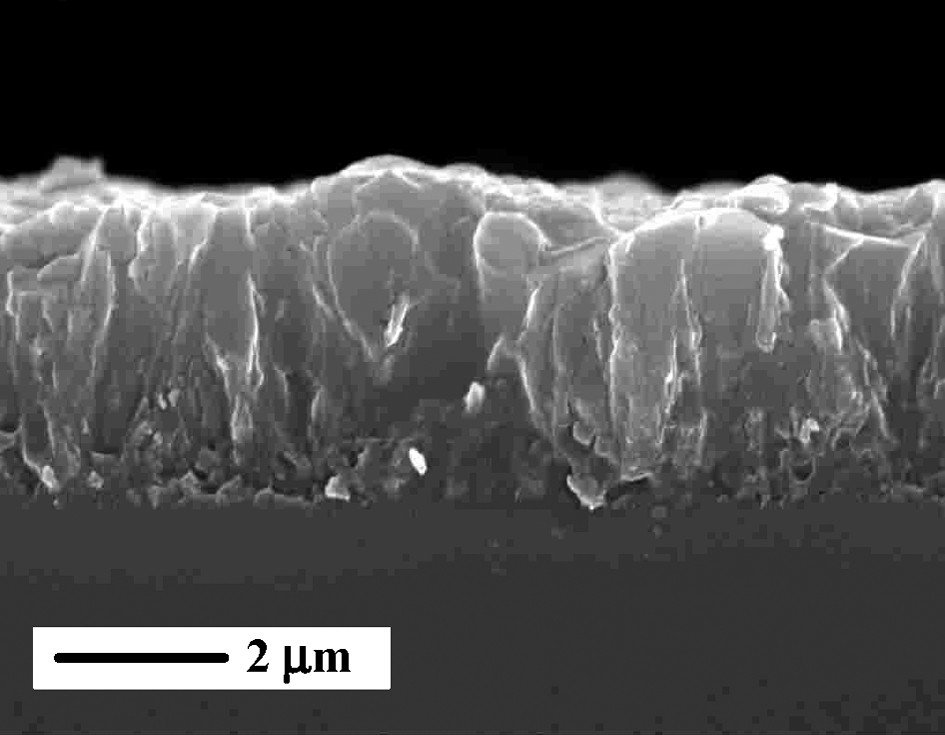
A SEM image of zeolite film on a flat support.
2.1.2 Zeolite coated fibers
The initial works on zeolite coated fibers were exploratory to collect data about the compatibility of fibers of different chemical composition in depositing zeolites by direct synthesis [26–28]. The deposition of zeolite A on vegetable fibers by direct crystallization was investigated [26,27]. It was found that high lignin content prohibits the zeolite deposition. Chemical (with diethyl ether) and mechanical (in agate planetary ball mill) pre-treatment of the fibers generally improved the zeolite coatings and deposits of up to 40 wt.% were obtained. Inorganic ZrO2 fibers were also used as a support for molecular sieve (silicalite-1) deposition [28]. Two synthesis systems were employed, a synthesis gel and a clear solution, with different viscosity and alkalinity. A few isolated crystals were observed on the fiber surfaces after the hydrothermal treatment using the gel system, whereas homogeneously distributed along the surface crystals were obtained from the solution system with a zeolite coating reaching 24.5 wt.%.
Zeolite Y was deposited on vegetal fibers by either direct crystallization after chemical or mechanical pre-treatment of the fibers or using the seed-film method [29]. The chemical composition of the fibers was found to be very important for the amount of zeolite deposited. Thus, similar results were obtained on linen fibers (ca. 20 wt.% of zeolite coatings), the amount of zeolite was 22 wt.% on cotton fibers treated by the seed-film method or chemically pre-treated and only 4 wt.% on mechanically pre-treated samples, whereas no or very small amount of zeolite was formed on CTMP-fluff fibers by in situ crystallization, whereas the seed-film method gave very good results (46 wt.%). These results indicated that the effect of the chemical composition of the support on the zeolite coating can be minimized by applying the seed-film method. This conclusion was further confirmed by the results obtained using the seed-film method for the preparation of silicalite-1 films on other fibrous supports, such as zirconia, alumina, carbon, mullite, ceramic and pyrex glass fibers [30]. It was possible to form continuous silicalite-1 films on all supports. The morphology of the crystals grown on the alumina-containing fibers was different due to alumina dissolution and crystallization of ZSM-5 rather than silicalite-1.
The procedure for preparation of fibrous zeolites was developed one step further, in which the fiber (exemplified by carbon fibers) has been combusted to leave behind hollow zeolite tubes [31,32]. The diameter of the tube hole was predetermined by the diameter of the carbon fibers, whereas the tube length can be varied by using fibers of different lengths. The tube walls were thicker and less homogeneous when synthesis gels were used compared to clear solutions. On the other hand, tubes with thicker walls showed higher mechanical strength. The possibility to prepare bilayred zeolite tubes comprising molecular sieves of different composition was studied for the silicalite-1:ZSM-5 system. The introduction of aluminum in the synthesis gels lead to less homogeneous crystallization and wall roughness increased with increased aluminum content. Also, the second zeolite layer was thicker when synthesized without intermediate seed adsorption. Fig. 3 shows SEM images of silicalite-1 coatings on carbon fibers (a) and a hollow silicalite-1 tube (b).
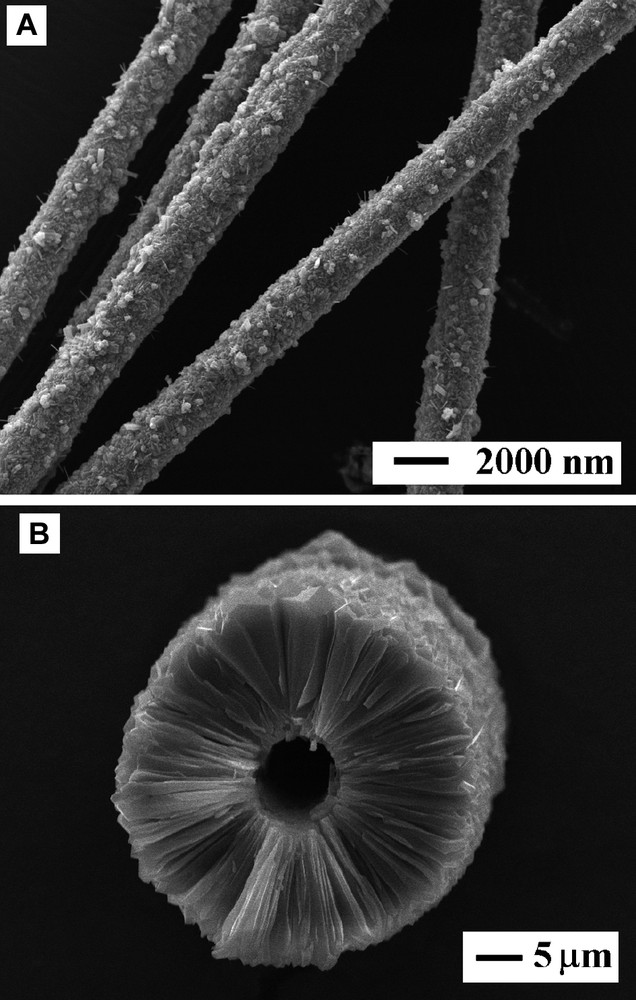
SEM images of zeolite coated carbon fibers (a) and a hollow zeolite tube.
Finally, it was possible to grow rather dense zeolite films on glass fiber supports without pre-seeding [33]. The increase in the TPAOH content of the initial gels, the temperature and the treatment time all increased the amount of silicalite-1 formed on the fibers. However, this was accompanied by deterioration of the zeolite-fiber composite mechanical stability. A two-step synthesis procedure, in which an initial treatment at a lower temperature was followed by a short treatment at high temperature, improved substantially the mechanical strength of the composite.
2.2 Self-bonded zeolite macrostructures
Despite the number of emerging applications of supported zeolite films and coatings, the traditional areas of zeolite application remain catalysis, separation and ion exchange, where the use of self-bonded zeolite macrostructures is beneficial. By macrostructures in this work is meant macroscopic structures with dimensions greater than 0.1 mm. The utilization of three types of supports, silica-containing plants, polystyrene beads and ion exchange resins, will be considered and the merits of each of the approaches will be emphasized. The approaches used to prepare the zeolite macrostructures are schematically illustrated in Fig. 4.
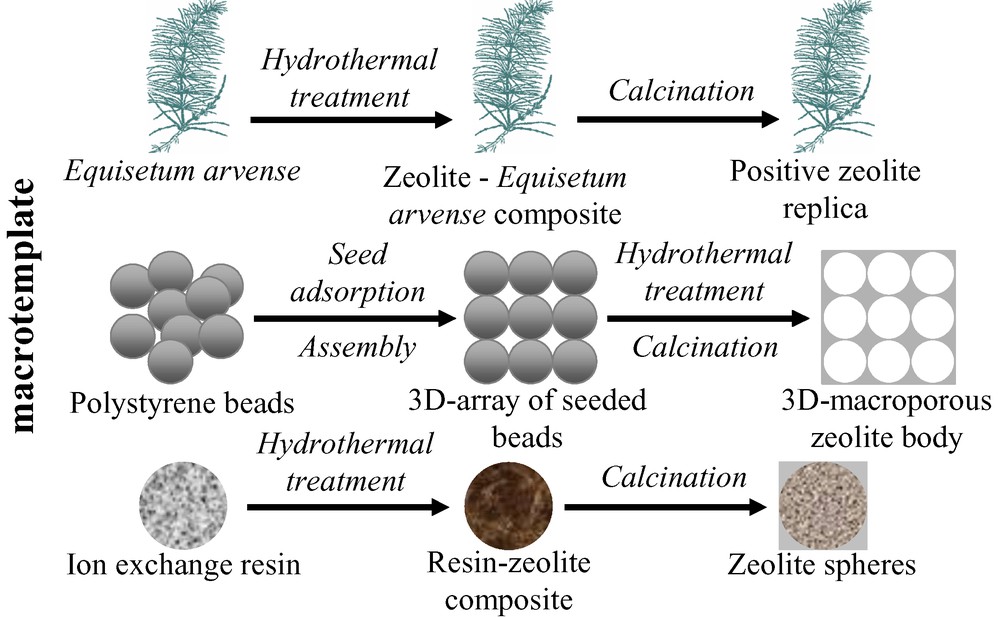
General representation of the approaches used to obtain self-bonded zeolite macrostructures.
2.2.1 Biomimetic molecular sieve macrostructures
Replicating biological templates is very challenging from scientific point of view because such templates offer beautiful architectures created by nature and the variety in their morphological features is enormous. In addition, such templates are inexpensive, easily available and environmentally benign. Equisetum arvense is a plant rich of amorphous silica (13 wt.%) deposited in descrete knobs and rosettes at the epidermal surface. Silicalite-1 and zeolite Beta replicas of both the plant leaves and stems were obtained by in situ zeolitization induced by the biogenic silica of the plant and subsequent calcination [34,35]. Fig. 5 shows typical SEM images of zeolite replicated plant leaves (a, b) and stems (c, d), from which the high fidelity of replication is evident. For both zeolites, the crystallization within the plant was faster than the crystallization in the bulk solution indicating the promoting role of the plant biogenic silica. Also, zeolite loading of up to 60 wt.% was obtained within the leaves by two times repeated synthesis. A higher zeolite loading was achieved within the stems, 74 wt.%. The mechanical strength of the calcined zeolite replicas of the plant leaves was not very high but could be improved by repeating the synthesis (increasing the zeolite loading). The zeolite formed within the plant stems showed better mechanical stability. By performing the synthesis in the absence of zeolite structure directing agent, the subsequent calcination would not be necessary and the flexible zeolite containing leaves and stems obtained could be directly utilized. Another feature of the materials prepared was the presence of mesopores emanated from the macrotemplate removal in amounts dependent on the synthesis conditions. In conclusion, the possibility to replicate even the nanometer-scale morphological details of Equisetum arvense was demonstrated. The synthesis is realized without any pre-treatment of the plant, the zeolitization being induced by the biogenic silica stored within its structure.

Typical SEM images of the positive zeolite replicas of E. arvense leaves (a) and stems (b).
2.2.2 Polystyrene bead supports
Negatively charged polystyrene beads were used as macrotemplates for the preparation of hollow zeolite spheres or millimeter sized hierarchical zeolite macrostructures with secondary porosity emanating from the removal of the pre-ordered organic beads. In some of the works, the polystyrene spheres have not been removed after the synthesis and the composite materials are not self-bonded zeolites. However, the experience gained from these studies was used to prepare the hierarchical macrostructures and they will be briefly mentioned in this section.
The seeding technique was applied to electrostatically adsorb zeolite seeds onto negatively charged polystyrene beads [36]. Seed crystals of LTA, FAU, BEA and MFI type with crystal sizes in the range 40–150 nm were employed. It was found that repeated (10–20 times) surface charge reversion-seed adsorption steps were needed to obtain zeolite coatings of high quality. However, fragile shells and broken particles were obtained upon calcination. The mechanical stability of hollow particles synthesized using polysterene beads as templates was improved by secondary hydrothermal treatment with zeolite precursor mixtures [37–39]. The mechanical strength of the hollow particles was dependent on the thickness of the zeolite shells (which can be controlled by the composition of the precursor synthesis mixture) and the size of the initial polystyrene beads, smaller beads yielded stronger hollow spheres. Millimeter sized silicalite-1 bodies with a regular system of macrocavities were obtained by seed-coated polystyrene beads assembled into three-dimensional arrays using two approaches. In the first approach, the pre-treated beads were introduced into a holder, then the synthesis solution was added and after a short ultrasonic treatment the beads were left to sediment [38]. The hydrothermal treatment was realized by transferring the holder into an autoclave. The second approach involved mixing of suspensions of polystyrene beads and silicalite-1 crystals followed by slow evaporation of the liquid phase [39]. In some experiments, the obtained composite was subjected to secondary hydrothermal treatment. Typical SEM micrographs of the macroporous silicalite-1 bodies at two different magnifications are shown in Fig. 6. Disadvantages of these procedures for preparation of macroporous ordered zeolite macrostructures are the complicated and sometimes time-consuming steps involved, the difficulties to control the macroshape and the size of the product structures and their limited mechanical strength. On the other hand, the unique micro-macropore structures of the zeolite bodies make the complex synthesis worthy.

Typical SEM images of ordered macroporous silicalite-1 bodies taken at two different magnifications.
2.2.3 Ion exchange resins as macrotemplates
The choice to use macroporous anion exchange resins as macrotemplates was determined by the fact that: (i) they are supplied in the form of spherical beads of various particles sizes and spherical shape is often preferable; (ii) they are capable of exchanging anions and anions are present in the zeolite synthesis solutions; (iii) their permanent pore structure offers a volume for the zeolite crystals to grow in; (iv) as being an organic material they can easily be removed upon completion of zeolite synthesis by calcination; and (v) their combustion would leave behind predetermined permanent pore structure in the product zeolite spheres. In brief, the synthesis procedure developed includes mixing of clear zeolite synthesis solutions and anion exchange resins, hydrothermal treatment, separation of the resin, drying and calcination. The method is simple compared to other methods because it is realized in a single step and is not burdened by complicated pre-treatment procedures. On the other hand, ion exchange resins are not chemically inert and a lot of experiments are required to adopt the synthesis conditions (synthesis solution, solution to resin weight ratio, temperature and duration of the hydrothermal treatment, etc.) as to obtain intact zeolite replicas of high quality.
Silicalite-1 and zeolite Beta self-bonded spheres of high mechanical strength were prepared with a size and shape similar to the original resin beads (Fig. 7a) [40–42]. The spheres were built up by particles with a size of ca. 100 nm which is comparable to the pore size of macroporous resins (Fig. 7b). Depending on the synthesis temperature, crystals of larger size were observed on the sphere surfaces as the growing of those crystals was not restricted by the presence of the resin polymer chains. The calcined zeolite spheres contained both microporores from the zeolite and mesopores (40–50 nm) due to the resin removal.
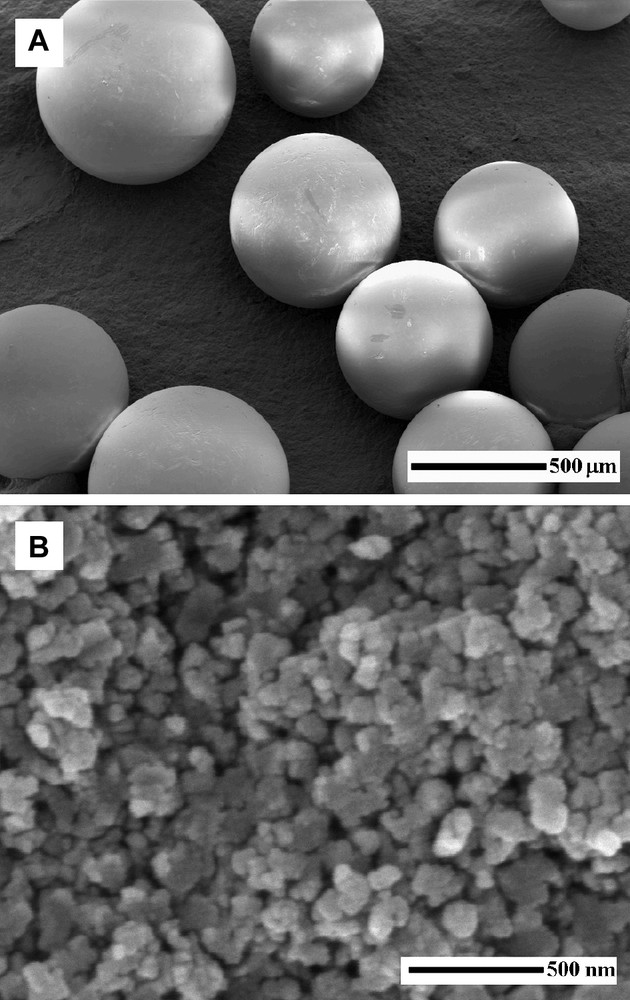
Typical SEM micrographs of self-bonded zeolite spheres (a) and the interior primary particles building up the spheres (b).
The original synthesis procedure was modified to reduce the consumption of zeolite structure directing agent and to avoid bulk crystallization and hollow silicalite-1 spheres were prepared by the modified procedure [43]. The modified synthesis involved insertion of silicate species into the resin by ion exchange, hydrothermal treatment of the resin-silicate composite with 1–5 wt.% TPAOH or TPABr solutions, separation, drying and calcination. Silicalite-1 was growing on the sphere surfaces consuming the silica stored within the resin and upon completion of the crystallization process and resin removal, hollow particles were formed.
AlPO-5 self-bonded particles with somewhat irregular spherical shapes were also synthesized by resin templating but cation exchange resins were employed as cations are present in the AlPO-5 synthesis solutions [44]. Alumina was firstly introduced into the resin by cation exchange and the resin was then hydrothermally treated with a mixture of TEAOH, H3PO4 and distilled water.
3 Conclusions
The works reviewed in this account clearly show the developments and the trends in the synthesis of supported and self-bonded zeolite structures. The initial approaches to prepare such structures were straightforward with outcomes that were difficult to predict. The later developments have been integrating interdisciplinary knowledge from other scientific areas such as colloidal and polymer chemistry and biology. The syntheses were directed towards the preparation of structures with tailored properties, often with particular applications in mind. The development and the easier access to more powerful characterization techniques will further catalyze the production of zeolite based materials of unique properties.
Acknowledgements
The authors thank CNRS-DFG bilateral program for financial support.