1 Introduction
The polymer industry is permanently facing significant economic, environmental and societal challenges. Major driving forces for the changes are increased globalization of markets, strive for improved profitability, societal demands for improved environmental performance, as well as ever increasing demands of end users on properties of plastics products. The challenges of polymer industry are naturally transferred into all material streams used in polymer production, including additives and polymer stabilizers.
In this respect, constant re-evaluation of the existing know-how together with performance improvements targets are necessary elements of any developmental activity in this field.
The area of polymer degradation and stabilization is still an area of appreciable industrial interest—supported by corresponding research activities in several universities and industrial laboratories. At present time, the generally accepted understanding of polymer degradation is based on an original scheme for autocatalytical oxidation of hydrocarbons proposed several decades ago [1,2]. Those base principles are presently often used for explanation of stabilization mechanisms of chemical substances—i.e. additives, which are able to slow down degradation processes of organic and particularly of polymeric materials (as e.g. depicted in Scheme 1). The theory has been over the years many times reviewed, extended and supplemented [3,4].
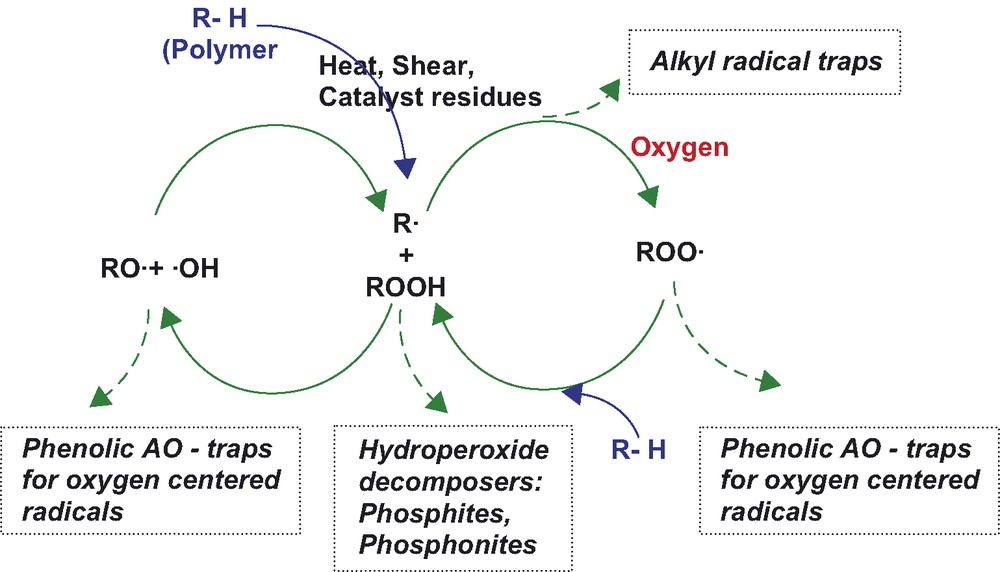
As a matter of fact—present theory allows for rather comfortable classification of different stabilizer groups—primary antioxidants (hindered phenols, aromatic amines, etc.), secondary antioxidants—hydroperoxide decomposers (phosphites, phosphonites, thio-costabilizers,), etc. But, on the other hand—this existing theory does not seem sufficient to explain in full a number of data and facts related to polymer degradation and stability.
By closer examination of the presently accepted stabilization theories, several inconsistencies can be easily outlined.
As an example it can be mentioned the stabilization function of trivalent phosphorous based secondary antioxidants (typically phosphites or phosphonites). According to the accepted theory, these secondary antioxidants act as “hydroperoxide decomposers” during polymer melt processing. It should be noted, that common alkyl-hydroperoxides decompose rapidly at temperatures significantly lower (see e.g. [5]) than typical polyolefin processing temperatures (e.g. above 200 °C for HDPE or PP). So one can hardly expect sufficient reaction time and conditions for polyolefin hydroperoxides to be effectively decomposed by phosphorous secondary antioxidant during polymer melt extrusion. Already several years ago, Neri et al. [6,7] suggested that the stabilization mechanism of phosphites in polyolefin stabilization was probably in direct interaction of activated phosphite with molecular oxygen, but no principal corrections in the scheme of polymer stabilization are seen in relevant literature.
Another question on the stabilization role of trivalent phosphorous secondary antioxidants is coming from a practical industrial experience—those secondary antioxidants are effective and important processing stabilizers for polyolefins such as PP, HDPE and LLDPE, whereas their role and stabilization effect in melt stability of radically polymerized LDPE is almost negligible. In other words, polymer industry is typically not using phosphites for processing stabilization of LDPE.
Fig. 1 shows comparison of melt flow stability of LDPE and LLDPE at different temperatures in presence of phenolic antioxidant (Hostanox O 16) and phosphite stabilizer (Hostanox PAR 24). While in the case of LLDPE, the contribution of phosphite to melt stability of the resin is well seen, at the same time—the contribution of the phosphite stabilizer to the melt stability of LDPE at two different temperatures is quite negligible, and stabilization is in principle assured by phenolic antioxidant (AO) only.
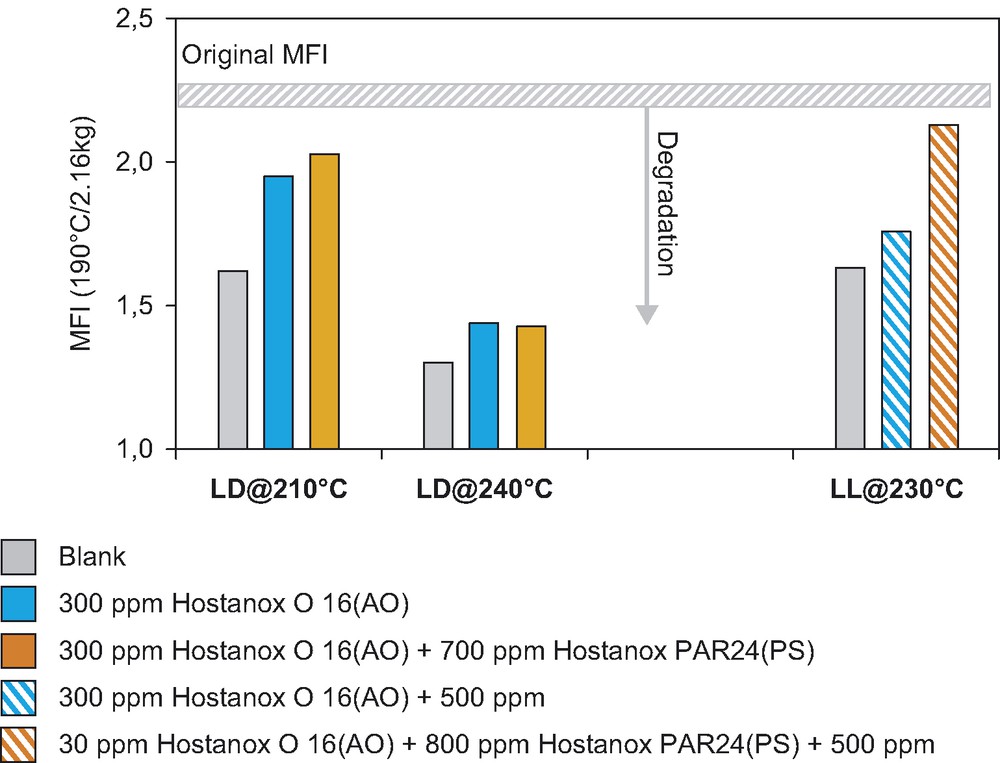
Processing stabilization of LDPE (LD) and LLDPE (LL) at different temperatures.
Melt Flow Index (MFI) results after three extrusion passes.
These results as well as the existing industrial experience give rise to a simple logical question—is it possible that only PP, HDPE and LLDPE degrade via the mechanism depicted in the Scheme 1, whereas the role of hydroperoxides is not important in the degradation of LDPE? Does it mean that for LDPE the Scheme 1 is not fully applicable?
Obviously, more probable explanation is that the presently accepted theory (as in Scheme 1) does not correctly attribute the stabilization role of trivalent phosphorous antioxidants in polymer stabilization during melt processing.
Analogously it can be investigated a potential stabilization role of other stabilizers depicted in the Scheme 1. For example benzofuranone derivatives (lactones) were shown to have a potential to act as carbon centered radicals (alkyl radicals) traps [4]. Therefore, nowadays in several publications the lactones are almost automatically placed in the Scheme 1 as alkyl radical traps.
Nevertheless, a closer examination of stabilization performance of lactones reveals, that their stabilization efficiency in polyolefins is observed especially at elevated processing temperatures—e.g. 240 °C and higher. Stabilization effect of lactones in polyolefins at lower temperatures is not significant.
Fig. 2 documents that the addition of lactone to a standard additive package (phenolic antioxidant Hostanox O 10 with phosphonite processing stabilizer Sandostab P-EPQ) does not have any positive effect on melt stability of HDPE resin processed at 210 °C, whereas for polymer processing at 240 °C the improved melt stability in presence of lactone 472 is clearly observed.
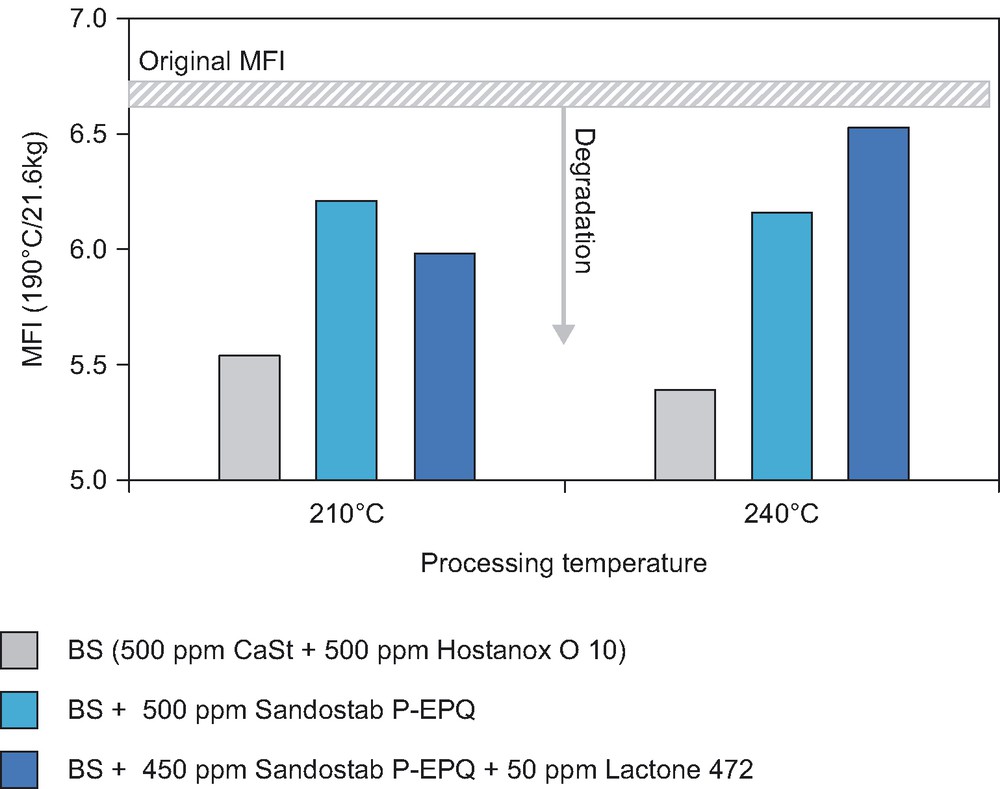
Processing stabilization of HDPE (Cr) at different temperatures.
MFI results after five extrusion passes.
A simple study of thermal behavior of lactone under inert atmosphere (nitrogen) and under oxygen atmosphere (as shown in Fig. 3) shows that the lactone rapidly oxidizes at higher temperatures—above 220 °C.
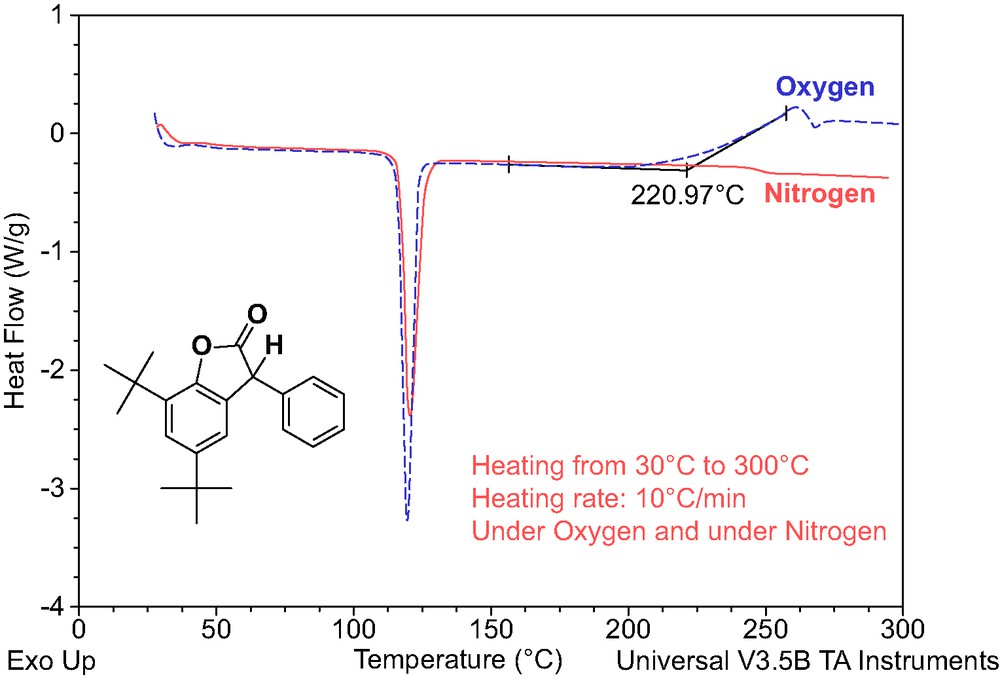
DSC records for lactone 472 under nitrogen and under oxygen atmosphere.
Comparison of the stabilization efficiency data in Fig. 2 with the thermal behavior of lactone under oxygen (Fig. 3) suggests that that the oxygen scavenging potential of lactones might play very important role in polymer stabilization. Therefore, the oxygen (and oxygen containing species) trapping stabilization action of lactone derivatives are probably more important polymer protective mechanisms than simple radical trapping—as shown in the general Scheme 1.
The tendency of lactones to an easy oxidation was already documented previously. Earlier investigations [8] showed that lactones reacted rapidly with oxygen, preferentially at elevated temperatures being stepwise converted into hydroxy-benzophenones (Scheme 2).
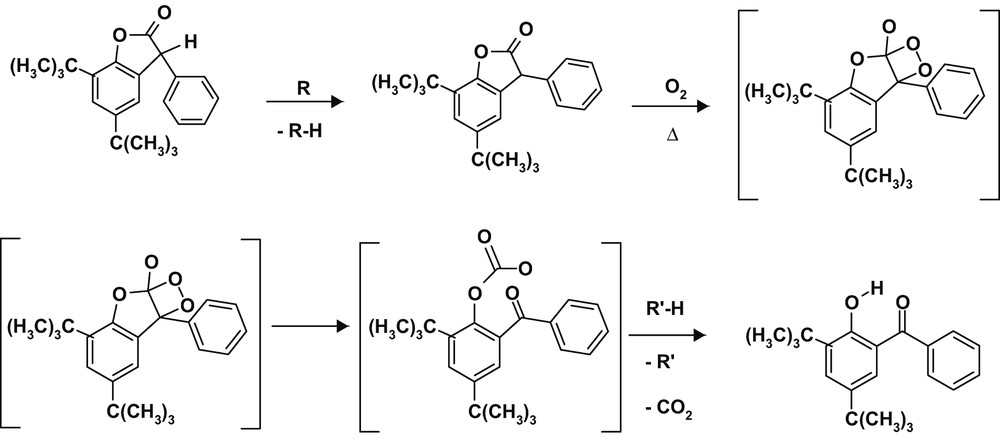
Conversion of lactones in the presence of oxygen at elevated temperatures into hydroxy-benzophenones.
In a similar way as to the polymer stabilization role of P(III) stabilizers and lactones, it is possible to examine different published information on stabilization mechanism of other polymer stabilizers—as e.g. Hindered Amine (Light) Stabilizers (HA(L)S), Ni-quenchers, etc. where additional questions to the Scheme 1 could be formulated.
With the today’s available information obtained from complex studies and tests in polymer degradation and stabilization, the generally accepted Scheme 1 does not seem to be sufficient to support further understanding and development in the field.
The principal risk connected with the continuous utilization of this scheme in general teachings on polymer degradation and stabilization processes is especially the fact, that the scheme presents the degraded substrate as homogeneous hydrocarbon environment (for which it was really originally proposed more than 50 years ago). In reality, various inhomogeneities, catalysts residues, etc. in real polymer substrate play substantial role in initiation, kinetics, and also reaction extend of the substrate oxidative degradation. Figs. 4 and 5 give a very simple comparison of oxidative behavior of decaline (homogeneous hydrocarbon substrate) and the unstabilized HDPE melt (realistic industrial ‘substrate’) exposed to oxygen atmosphere at 175 °C.

DSC record for decaline at 175 °C under oxygen atmosphere.

DSC record for unstabilized HDPE at 175 °C under oxygen atmosphere.
Whereas no measurable exothermic oxidative degradation processes are seen for decaline (Fig. 4), the degradation of unstabilized HDPE starts in very early stages of exposition to oxygen (Fig. 5).
Obviously, any continuous use of the Scheme 1 in various degradation and stabilization kinetic studies presents an oversimplification with potential misleading hints for further development of new stabilizers and stabilization technologies. The discussed scheme is certainly well applicable for homogenous liquid systems, but real industrial polymers are clearly more complex systems with different degradation and stabilization kinetics.
In the view of those facts, the estimation of future trend is polymer stabilization can be outlined better on a basis of empirical and industrial know-how instead of relying on outdated theoretical backup.
2 Potential future trends in polymer stabilization
As indicated above, for future development of polymer stabilization it will be necessary to investigate the whole subject of polymer degradation and stabilization—outside the present limits and frames imposed by the generally accepted Scheme 1.
It is especially important to gain better understanding on degradation mechanisms in the very first steps of those processes—i.e. on the “initiation reactions” that subsequently lead to deterioration of polymer properties.
From a pragmatic point of view, in present situation the estimation and assessment of future trends in the development of polymer additivation and stabilization could be based on analysis of existing situation in plastics industry, as well as on the understanding of driving forces in this field (often determined by the needs of society and market).
Nowadays in a field of polymer stabilization following principal driving forces can be identified as those having the impact on running development in the field:
- ● continuing economical pressure related to ongoing ‘commoditization’ in the additive market;
- ● ever-growing ecological awareness resulting in new needs to meet increased requirements by environmental-, safety- and health-related regulations;
- ● systematization and needs for improvement in complex stabilization packages for e.g. pigmented, filled and/or flame retarded plastics (i.e. system solutions); and also search for stabilization systems for new engineering resins.
These driving forces (depicted in Scheme 3) do influence, and it can be expected that they will continue to influence developments in the field of polymer stabilizers in a near future.

More detailed estimation of the above trends is given in following paragraphs.
2.1 Commoditization/economical pressure
2.1.1 Price/performance optimizations
These are standard concerns which belong to everyday tasks in polymer industry. In can be expected that various empirical and/or statistical methods on optimization of stabilization systems and processing conditions will be increasingly and more systematically used.
2.1.2 Additional studies
Additional studies should continue for better and more profound understanding of degradation and stabilization principles—i.e. investigate outside the frame of Scheme 1. Further analysis of active of chain ends, structural defects in polymer chains, and also remaining activity of catalyst residues are necessary to draw additional relevant polymer degradation pathways [9]. Use of sophisticated and sensitive analytical methods is mandatory for these purposes.
2.1.3 More effective ways of additives application
A potential use of active stabilization functionalities in the resin preparation process. In this way it would be possible to achieve target properties (e.g. stability, dyeability, etc.) at significantly lower additive concentration. At the same time there is additional potential to obtain new properties of such ‘in situ’ modified polymer (e.g. improved processability, etc.).
In the field of “more effective ways of additive application” (as Section 2.1.3)—a novel approach has been recently published for polyamides (PA). A specially designed aromatic HALS (Nylostab S-EED) , originally developed to improve dyeability of PA resins [10], was found to be significantly more effective by applying directly into caprolactame polymerization, when compared to the additive in-mixing via standard melt homogenization steps. By direct application into caprolactame polymerization it was possible to significantly reduce necessary additive loading to achieve the expected effect (dyeability) and moreover, the modified polyamide resin exhibited new and better properties, such as improved melt processing and improved long term heat and light stability.
Figs. 6 and 7 show rheological comparison of melt process stability for standard PA 6 (Fig. 6) and for PA 6 prepared in presence of Nylostab S-EED (Fig. 7). As it is seen, the modified PA 6 (Fig. 7) shows clearly improved melt pressure stability—i.e. gives smoother melt flow and less variation in the melt extrusion process—the fact which under industrial spinning conditions leads to significant reduction of filament breakage at high spinning speeds.

Melt process stability of standard PA 6.
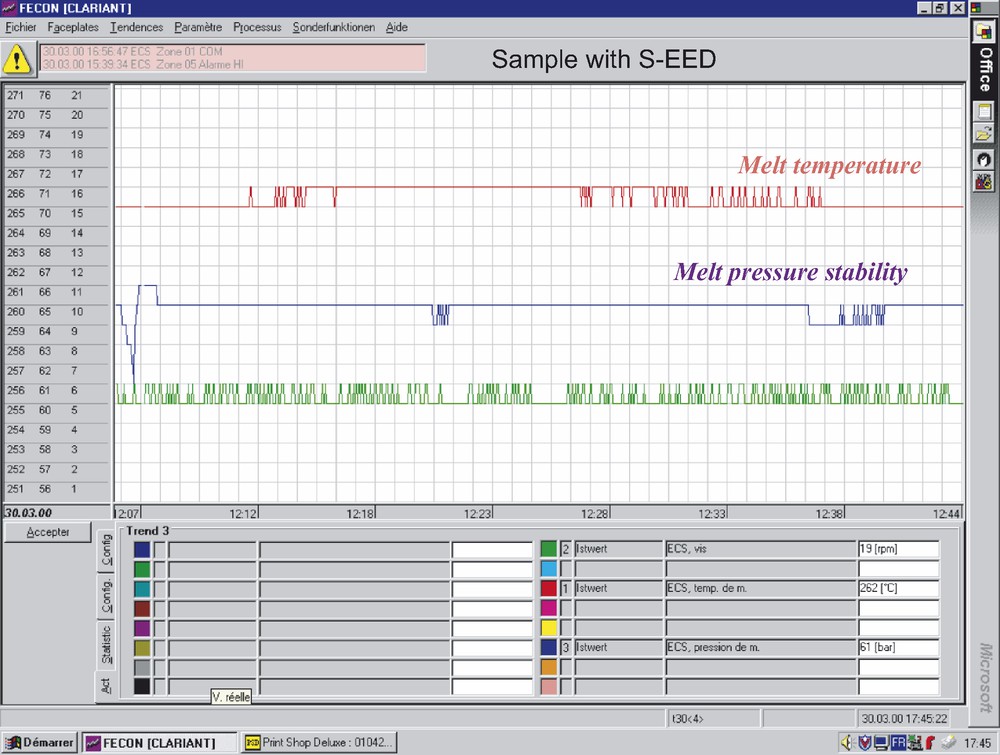
Melt process stability of standard PA 6.
Similar process improvements were reported also for PA resin prepared in presence of a chain stopper system containing 4-amino-2,2,6,6-tetramethyl piperidine [11].
As another promising example in this field, it can be mentioned an “in-reactor modification” of LDPE by a properly functionalized HALS [12] which enabled to prepare modified PE films with higher light stability compared to PE films stabilized by conventional HALS additives via compounding steps.
Another interesting work in this respect was published also for in-reactor additive incorporation in polypropylene—by using alkyl-aluminum co-catalyst modified with phenolic antioxidant functionality [13]. The reported data indicated that the obtained PP resin showed higher oxidative and long term heat stability. However, industrial application of this last approach is still not seen.
2.2 Ecological awareness/ESH
Most of the additives presently used in plastics industry were broadly tested according to respective eco-toxicological standards. Therefore, for every particular case any additive is properly sanctioned for a respective application, e.g. for food packaging purposes additives have to be approved for indirect food contact applications, etc.
Nowadays, however, apart of standard approval procedures for original additive molecules, also the additive reaction products from stabilization reactions (i.e. the additive metabolites) are becoming under scrutiny.
In order to exclude or minimize potential concerns of an average consumer, following potential trends in the field of polymer stabilizers can gain more importance.
2.2.1 GRAS and ‘green’ additives
Application of compounds available in nature for stabilization of plastics. In general, this trend is quite popular, and for example, applications of Vitamin E as antioxidant for plastics are well known [14]. With ‘natural antioxidants’—often their thermal stability is a limiting factor for the use polymer stabilization, as for the natural compounds often decompose under typical polymer processing conditions. Therefore studies to analyze [15], better understand and mimic the high efficiency of natural products for polymer processing conditions are of high value (see, e.g., [16]).
Apart of antioxidative protection, recently—out of natural compounds, the DNA bases and especially DNA-based combinations [17] were shown to be effective UV stabilizers for HDPE and PVC. Such additive types can present also an interesting future potential in stabilization of plastics containers for food packaging.
2.2.2 Development and industrial introduction
Development and industrial introduction of new highly effective polymer stabilizers—with a goal to minimize overall loading of the additives. In principle, this is one of the most common development efforts in the field of polymer stabilizers, and recently the advantages of a new highly effective secondary antioxidant were documented [18]. By use of a new phosphine stabilizer, the concentration of secondary AO can be reduced from present typical levels 700–1500 ppm (0.07–0.15 phr) of standard phosphite or phosphonite, down to 100–200 ppm (0.01–0.02 phr) of phosphine (Fig. 8). This reduction of the necessary stabilizer concentration can present an interesting ‘eco’ potential in the future.

Processing stabilization of HDPE at 240 °C.
MFI results after five extrusion passes.
2.3 Complexity/system solutions
Further developments of complex additive systems have to continue in parallel to the theoretical and environmental trends in polymer additivation, as outlined above in paragraphs 1 and 2. The developmental efforts in this last paragraph would be driven by the needs to use existing theoretical and empirical know-how to further improve stability of complex polymer systems (e.g. flame retarded polymer resins, pigmented polymers, etc.), as well as to gain extended empirical basis which would help in additional understanding of structure–property relationships in polymer additivation.
Following developmental efforts can be expected in this part.
2.3.1 Additional and continuing systematic studies on combined packages
Recently presented work on stabilization of pigmented Polyethylene articles [19] showing an impact of different HALS and UV absorbers on color stability and mechanical integrity during long term stability tests. The work clearly indicated that there is still a lot of space for a deeper and systematic understanding of potential interactions of light stabilizers and pigments. Future works can provide more information on structure–properties relationships, which would enable to design additive systems more economically and more effectively.
2.3.2 Use the available data and estimations on structure–property relationships
Use the available data and estimations on structure–property relationships to synthesize new, inherently stable polymer additives—such as flame retardants or pigments, etc. As a trend example, one can mention a yellow organic pigment modified in synthesis by tetramethylpiperidine (HALS) functional groups [20]—giving then significantly better long term stability in PP fibers than other similar yellow pigments stabilized by with corresponding commercial light stabilizers in conventional compounding way.
3 Conclusions
Polymer stabilization is and will continue to be an important technical field attracting corresponding industrial and scientific attention.
Further developments in the field of polymer stabilization in a near future will be to a large extent determined by growing economical and ecological requirements.
Presently used theoretical understanding of polymer degradation and stabilization principles does not seem to sufficiently cover the full chemical and physical complexity of polymer stabilization, and therefore it can be expected that most of new developed stabilizers and stabilization systems in near future would be based on accumulated practical experience and existing empirical know-how.