1 Introduction
The hydrotreatment of petroleum aims to produce clean gasoline and diesel with low sulfur, nitrogen and aromatics contents. More stringent environmental regulations require increase of the efficiency of these processes. Among the possible solutions, using more active catalysts would be less expensive for the refineries, because it would allow avoiding modifications for the plant installations.
Conventional HDS catalysts contain molybdenum sulfide MoS2 (10–20 wt%) promoted with cobalt or nickel (3–5 wt%) and supported on alumina. Recently, new types of catalysts appeared, which contain very high amount of MoS2 and can be considered as unsupported systems. Development of such unsupported systems possessing advantageous textural properties and bearing very high density of active sites seems to be a promising research direction.
Earlier, unsupported hydrotreating catalysts have been prepared by different methods, including comaceration [1], homogenous sulfide precipitation [2–6], thiosalt decomposition [7–9], hydrothermal and solvothermal processes [10–14], and solution reactions [15,16]. Thus prepared molybdenum sulfide can be further promoted by cobalt or nickel [17–19].
Thiometallates are used for many applications spreading from biological systems [20–23] to catalyst precursors [7–9,24–29]. Several works have reported the use of thiometallates to generate MoS2 and WS2 catalysts with high surface area and high catalytic activity [30–32].
The goal of this work was to prepare highly active unsupported Ni–W sulfides, which actually are somewhat less studied than the molybdenum counterparts. In this study, unsupported Ni–W–S catalysts were prepared using ammonium oxothiotungstate (NH4)2-WO2S2 as precursor.
2 Experimental
2.1 Preparation of W oxothiosalt precursor
The precursor (NH4)2WO2S2 was prepared by ammonium sulfide precipitation as follows. Ammonium metatungstate (20 g, ca 0.1 mol W) was dissolved in 50 mL of concentrated NH4OH and 40 mL H2O. The mixture was stirred for 1 h (to depolymerize polytungstate species to get monomeric WO42−, which can be a slow process). Then 100 mL of (NH4)2S (50 wt%) were rapidly added to the solution at ambient temperature. The yellow precipitate was recovered by filtration and dried under nitrogen flow at room temperature. It was identified by XRD and chemical analysis.
2.2 Preparation of Ni–W–S catalysts
Amorphous W oxysulfide pre-catalysts WOxSy were prepared either by solution acid condensation of WO2S22− anions (protonation followed by water splitting) or by thermal decomposition of the (NH4)2WO2S2 salt at different temperatures (heating rate: 4 °C/min). The oxysulfide amorphous solids were kept and handled under nitrogen. To prepare the Ni–W–S catalysts, the oxysulfide solids were impregnated with appropriate amounts of aqueous Ni(NO3)2, eventually in the presence of ethylene glycol and/or polyethylene oxide-based organic surfactant Triton 114 (50 vol% ethylene glycol, 15% surfactant). The technique applied and the molar quantities of the reactants were similar to those used earlier for molybdenum [33,34]. The black solids after nickel impregnation were sulfided under 15 vol% of H2S/H2 at 400 °C for 4 h.
2.3 Characterizations
The X-ray diffraction patterns were obtained on a BRUKER diffractometer with the Cu Kα radiation. Standard JCPDS files were employed to identify the present phases. Chemical analyses were performed using the atomic emission method with a spectroflame ICPD device. The surface areas and pore volumes were determined by nitrogen adsorption at 77 K using, respectively, the BET and the BJH equations. High-resolution transmission electron microscopy (HREM) and energy-dispersive X-ray analysis (EDX) were done on a JEOL 2010 device.
2.4 Catalytic test
Thiophene hydrodesulfurization (HDS) was carried out in the vapor phase in a fixed microreactor operated in the dynamic mode at atmospheric pressure of hydrogen (thiophene pressure: 2.4 kPa, obtained by saturation at 0 °C; total mass flow: 6 L/h). A catalyst charge of about 0.07 g was employed. The reaction rate was measured at 340 °C in steady-state conditions after 16 h of stream. The reaction products were analyzed chromatographically, using an online gas chromatograph HP5890 equipped with a flame ionization detector and a 30 m × 0.53 mm capillary column. The PLOT (Porous Layer Open Tubular) column is a fused silica capillary column coated with a homogenous layer of particles of Al2O3 deactivated by Na2SO4. The analysis was performed with a temperature program: 80 °C for 1 min, then heating to 190 °C at 20 °C/min and dwell at 190 °C for 28 min.
3 Results and discussion
3.1 Synthesis and characterization of the WOS2 precursor
Earlier, we described solution preparations of highly loaded or unsupported Mo-based catalysts [33,34]. Thiooxomolybdate (NH4)2MoO2S2 was successfully used in Ref. [33] to prepare at first high-surface-area MoOS2 amorphous oxosulfide, then to promote it with cobalt. In this work, we used a (NH4)2WO2S2 salt because it is much easier to prepare than completely sulfided thiotungstates such as WS42− salts. The (NH4)2WO2S2 salt can be obtained at ambient conditions by addition of aqueous ammonium sulfide to the metatungstate solution, whereas the thiotungstate preparation requires H2S bubbling through a solution with thorough control of temperature. At the same time the oxothiotungstate contains two sulfur atoms per tungsten, hopefully sufficient to produce WS2 with the following reactions.
In the proposed method, we first obtained a high-surface-area amorphous solid by decomposition of the crystalline precursor, then promoted this solid with nickel, and further reactivated it. The decomposition step is therefore of primary importance.
The DTA–TGA analyses were used to characterize the thermal decomposition of ammonium oxothiotungstate. From thermal decomposition curves (Fig. 1), three endothermic peaks could be clearly distinguished, and the total mass loss was 22.60% (from ambient temperature to 763 K). Small weight loss (1.06%) was observed at low temperature (412 K), and may be attributed to the elimination of absorbed water. The second step of decomposition occurred in the 423–613 K temperature range with an endothermic peak, and is supposed to be due to the reaction (1):
(NH4)2WO2S2 → 2NH3 + WS2O + H2O | (1) |
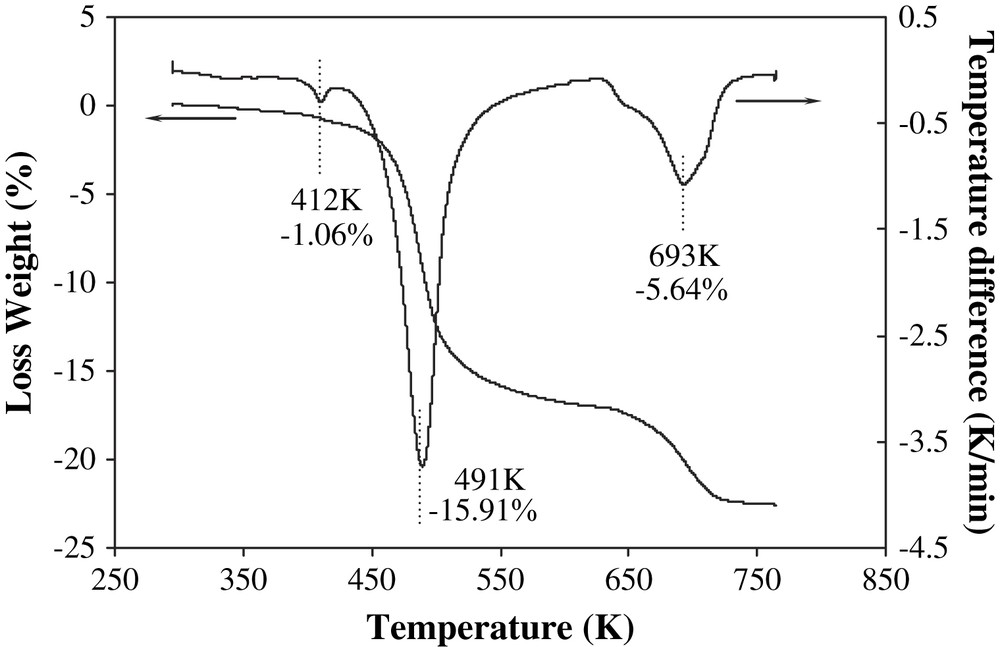
DTA–TGA curve of the decomposition of ammonium oxothiotungstate precursor.
The third decomposition step occurred from 613 to 763 K with a weight loss of 5.64%. No further mass loss was observed under nitrogen flow. According to the XRD pattern (not shown), the product after the decomposition at temperatures as high as 973 K contained WO3 and WS2 phases. It might therefore be related to the rearrangement of the amorphous tungsten oxosulfide structure to crystalline phases with partial expulsion of sulfur according to reaction (2):
3WOS2 → WO3 + 2WS2 + ¼S8 | (2) |
Alternative to the thermal decomposition, the oxysulfide solid was synthesized by acid condensation of a (NH4)2WO2S2 solution. Using this method, the yield of the solid product with respect to tungsten input was low (only 17%), and the properties of the oxysulfide solid were not very good (Table 2), so the decomposition by heating in an inert gas such as N2 or 15 vol% H2S/H2 was further preferred. In the last case, we could not carry out the DTA–TGA analysis, but analyzed the composition and XRD patterns of solids after heating at different temperatures. The chemical compositions of tungsten oxosulfide products are shown in Table 1. Their diffraction patterns are shown in Fig. 2.
Properties of the Ni–W–S catalysts as a function of preparation mode
Catalysts | Pre-catalyst | Solvent for nickel salt | R | S (wt%) | C (wt%) | S (m2/g) | V (cm3/g) | HDS rate (10−8 mol/(g s)) | ||
573 K | 593 K | 613 K | ||||||||
NiW/Al2O3 | NiW/Al2O3 | Reference | 187 | 285 | 434 | |||||
NiW-ac | W-ac | H2O | 0.5 | 30.19 | 1.75 | 0.52 | – | 13 | 24 | 39 |
NiW-n | W-n | H2O | 35.99 | 1.26 | 29.0 | 0.11 | 31 | 40 | 45 | |
NiW-ne | W-n | H2O + EG | 38.59 | 2.98 | 19.27 | 0.06 | 116 | 170 | 205 | |
NiW-hs150e | W-hs-150 | H2O + EG | 0.43 | 39.43 | 1.51 | 23.7 | 0.06 | 125 | 243 | 415 |
NiW-hs200e | W-hs-200 | H2O + EG | 0.33 | 33.48 | 1.66 | 16.21 | 0.05 | 118 | 224 | 374 |
NiW-hs400e | W-hs-400 | H2O + EG | 0.35 | 34.34 | 2.48 | 6.25 | – | 6 | 9 | 14 |
Evolution of W and S contents in the solids obtained by decomposition of ammonium oxothiotungstate
Solid | Heating temperature (°C) | W (wt%) | S (wt%) | S/W (mol) |
Initial (NH4)2WO2S2 | RT | 57.54 | 20.25 | 2.02 |
W-n-150 | 150 | 58.88 | 22.68 | 2.21 |
W-hs-150 | 150 | 58.18 | 23.86 | 2.35 |
W-hs-200 | 200 | 62.03 | 26.96 | 2.49 |
W-hs-400 | 400 | 66.81 | 21.16 | 1.82 |
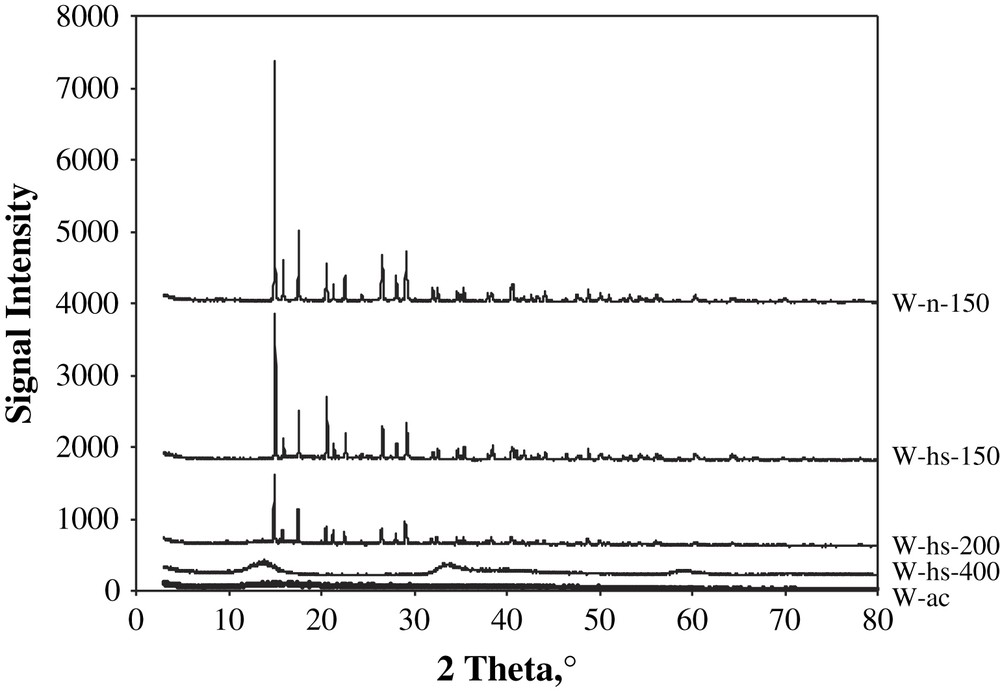
XRD patterns of tungsten solid prepared with different conditions. The intense diffraction lines are all those of (NH4)2WO2S2 phase, broad peaks – WS2 phase.
Chemical analysis shows that under H2S/H2 flow the S to W ratio increases slightly up to the temperature of the second peak of mass loss (but note that this temperature was measured under nitrogen flow). Apparently it happened due to some sulfidation of the W oxospecies by hydrogen sulphide. Then at 400 °C the S-to-W ratio drops, due to sulfur release. XRD patterns confirm progressive decrease of the intensity of sharp initial salt peaks. They are present even after 200 °C heating. Probably, the remaining oxothiosalt is located in the solid particles core and the products form amorphous exterior shell. The decomposition under hydrogen sulphide is therefore smooth and allows gentle control of the solids' properties.
After 400 °C the peaks of XRD reflections are very broad and approximately correspond to tungsten sulphide WS2 (Fig. 2). The chemical composition of this solid is, however, sulfur deficient compared to WS2 stoichiometry, due to the presence of some oxide formed by the reaction (2).
3.2 Properties of the Ni-promoted catalysts
The solids heated at different temperatures were thereafter impregnated with nickel nitrate, then dried and re-sulfided at 400 °C and tested in thiophene HDS. The properties and activities of the catalysts prepared are shown in Table 2. In this table, the catalysts (NiW-xxx) designated in the first column were derived from the amorphous precursors (W-xxx) listed in the second column. The impregnation with nickel nitrate was carried out either in aqueous solution or in the mixture water–ethylene glycol (in the last case the NiW catalysts names contain the letter e at the end).
From Table 2 it follows that the as-prepared Ni–W–S catalysts had moderate specific surface areas and HDS activities, though their specific HDS performance was relatively high compared to the industrial reference NiW/Al2O3. Positive effect of ethylene glycol addition into the nickel nitrate impregnation solution can be clearly seen. Only the solids obtained by heating of the oxothiotungstate at 150–200 °C provided some reasonable activities. The W-ac preparation obtained by acid condensation and the W-hs400 solid obtained by heating at 400 °C both showed low surface areas and HDS performances. The X-ray diffraction patterns of the catalysts listed in Table 2 were almost the same and they all showed only broad peaks of a tungsten disulfide compound.
Earlier we demonstrated for the MoS2-based catalysts [33,34] that the composition of the solvent plays a crucial role in the preparation of unsupported sulfide systems, since it determines the precursor's solubility, and also the parameters of nucleation and growth of the precipitate particles.
In the present work, we dealt with porous amorphous WOxSy solids insoluble in water or any organics. However, we impregnated them with the Ni(NO3)2 solutions containing the same type of organics as in Refs. [33,34]. It appeared that the influence of the impregnation solution's composition is strong and that qualitatively it has the same trend as was described for the precipitations. Indeed, only the addition of the nonionic surfactant Triton 114 allowed the obtaining a highly active system with increased specific surface area (Table 3).
Comparison of the properties of the catalysts prepared using impregnation by Ni(NO3)2 dissolved in different solvents
Catalysts | Solvent | R2 | C (wt%) | S (m2/g) | V (cm3/g) | Rate (10−8 mol/(g s)) | ||
573 K | 593 K | 613 K | ||||||
NiW/Al2O3 | Reference | 1.26 | 220 | 187 | 285 | 434 | ||
NiW-w | H2O | 9 | 0.11 | 31 | 40 | 45 | ||
NiW-we | H2O + EG | 0.43 | 1.51 | 23.7 | 0.06 | 125 | 243 | 415 |
NiW-wet | H2O + EG + triton | 0.4 | 1.76 | 58.23 | 0.12 | 289 | 554 | 879 |
From the diffraction patterns (Fig. 3), it seems that no great difference of WS2 phase crystallinity was caused by the variations of the solvent. The intensity of the (002) peak at 2θ = 14.3°, characteristic of the layer stacking along the c direction, decreased with the addition of EG and Triton. The stacking sizes calculated by line-broadening analysis were 2.97 nm (5 layers), 2.26 nm (4 layers) and 2.05 nm (3 layers), respectively, for the NiW-w, NiW-we and NiW-wet catalysts. So, after organic compound and surfactant addition, the slabs in the NiW-wet sulfide catalyst became smaller and might be more divided. However, the differences observed in XRD are not very strong and do not explain the almost tenfold difference in the HDS activity.
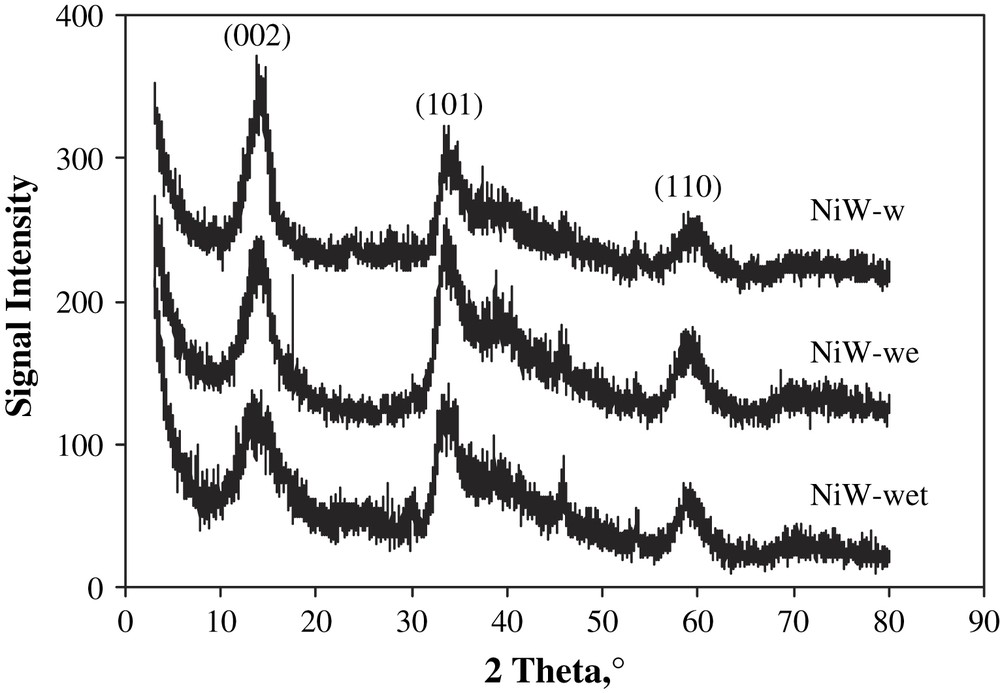
XRD patterns of the Ni–W–S catalysts prepared with different solvents. All peaks correspond to the WS2 phase.
Summarizing the influence of the impregnation solvent composition, it seems clear that it acts on the step of crystallization of WS2, improving its textural properties, but particularly it helps to optimize the Ni–W interaction. At the same time, the influence of mixed solvent on the precipitation step, as discussed earlier, [34] appears to be less important, since here we introduced the solutions into the porous amorphous solids and no precipitation occurred.
The properties of the unsupported catalysts may be further improved by adjusting the final activation (sulfidation) temperature (Table 4).
Properties of the catalysts obtained using different sulfidation temperatures
Catalysts | Sulfide temperature (°C) | R1 | R2 | C (wt%) | S (m2/g) | V (cm3/g) | Rate (10−8 mol/(g s)) | ||
573 K | 593 K | 613 K | |||||||
NiW/Al2O3 | Reference | 187 | 285 | 434 | |||||
NiW-400 | 400 | 0.37 | 0.4 | 1.76 | 58.23 | 0.12 | 289 | 554 | 879 |
NiW-450 | 450 | 0.37 | 2.60 | 64.14 | 0.14 | 307 | 610 | 1038 | |
NiW-500 | 500 | 0.37 | 1.15 | 46.69 | 0.11 | 180 | 358 | 623 |
From Fig. 4, the specific surface area and thiophene HDS activity as a function of sulfiding temperature passed through a maximum at 450 °C. Apparently, at the lower temperatures, the sulfidation was not complete, as it is known that tungsten species are rather difficult to transform to sulfide [35]. A maximum of the catalyst's surface area, pore volume, and thiophene HDS activity was observed at the middle 450 °C sulfiding temperature. It might suggest that the NiW pre-catalyst was just totally sulfided at 450 °C and temperatures higher than 450 °C provoked sulfide sintering.
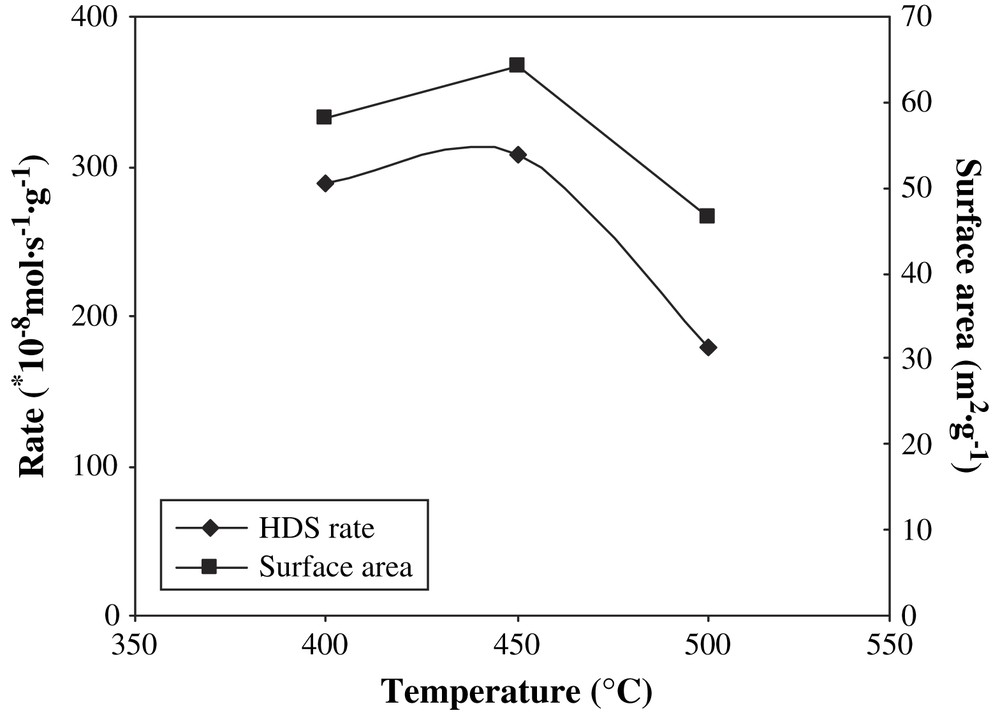
Surface area and HDS rate as a function of sulfiding temperature.
A high-resolution image of the optimized catalyst is represented in Fig. 5. We can see a porous structure constituted by the bent stacks of WS2 slabs with approximate length 7–10 nm and the stacking degree of 3–5 slabs in each stack. No bulk NiS particles were observed by TEM in this specimen, suggesting good dispersion of nickel species, smeared over the tungsten sulfide.
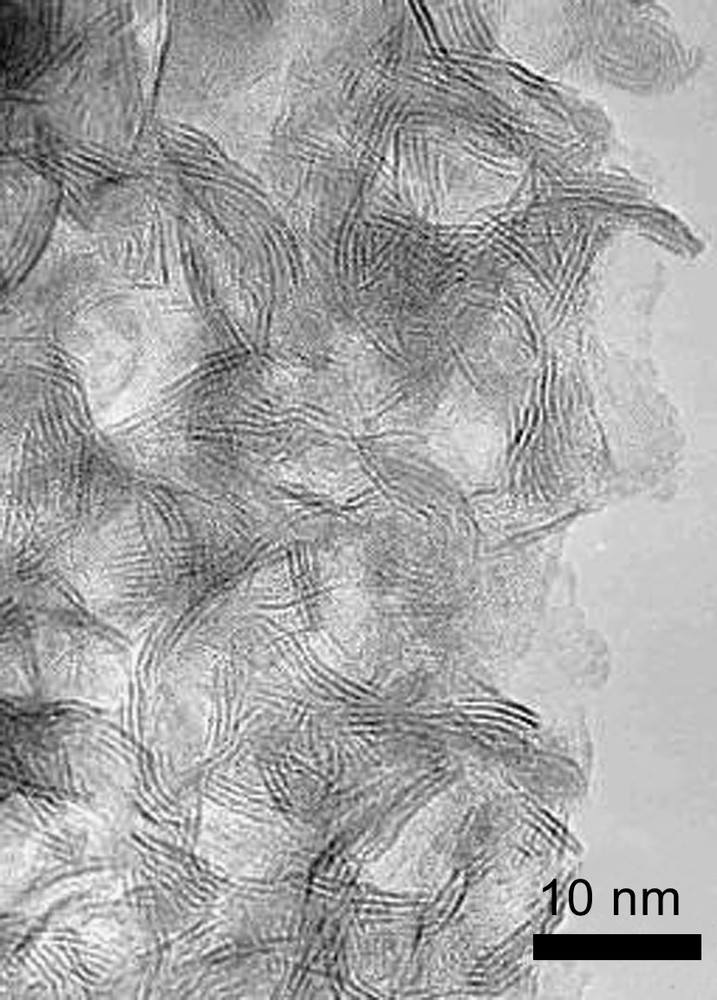
HREM image of the Ni–W-450 catalyst.
4 Conclusion
A new technique has been developed in this work to obtain highly active Ni–W–S unsupported catalysts from the (NH4)2WO2S2 oxothiosalt. In this method, the parent salt was first decomposed to the state of amorphous oxosulfide and then the amorphous solid was impregnated with Ni salt. Conditions to obtain high specific surface area and HDS activity of the final sulfide solid were found. They include decomposition of the precursor salt at 150 °C and further impregnation with nickel salt dissolved in the ternary (water–ethylene glycol nonionic surfactant) medium. Optimal sulfidation temperature was found to be 450 °C.