1 Introduction
Deactivation of acidic zeolitic catalysts during hydrocarbon transformations is due to the formation of carbonaceous molecules heavier than the reactant. These compounds, called “coke”, form inside the pores, at the outer surface of the crystallites or in both positions [1–9]. The catalytic activity of fouled catalysts can be regenerated by various techniques such as the combustion under air or diluted oxygen flow and at high temperature [10–13], ozone treatment [14,15], hydrocracking [16,17], extraction with a supercritical fluid [18], etc.
Comparing the coke oxidation rates for HY, H-Mordenite and HZSM-5 zeolites that are coked during n-heptane cracking at 450 °C, Guisnet and Magnoux [10] showed that the oxidation rate depends very little on the coke content but strongly on the zeolite structure. Similar to coking and ageing, several authors [1,2,6] concluded that oxidation is a shape selective process. Whatever the zeolite, oxidation occurs through successive steps with intermediate formation of oxygenated compounds (ketones, aldehydes, etc.). In Moljord et al. [12,13], the rate of coke oxidation of acidic zeolites is controlled by the number of framework aluminum atoms. The higher the density of Brønsted acid sites of the zeolite, the easier the combustion of the coke. Datka and Gil [19] and Gil et al. [20], showed that the strong acid sites of steamed HY zeolite in interaction with extraframework aluminum species, which were the first to be eliminated by the coke deposits during m-xylene (mx) transformation at 530 K, are the first to be restored using temperature programmed oxidation. Jong et al. [21], reported that a great part of the internal coke, located near the Brønsted acid sites, is selectively removed by air treatment during the initial oxidation stages of HZSM-5 coked during ethylbenzene disproportionation. Thereafter, both internal and external cokes are removed by oxidation. Selective removal is more pronounced with H2 stripping where internal coke is preferentially removed by cracking reactions while external coke is only partially cracked. Ozone stripping removes a large part of coke and makes easier the remaining coke to be burned [14,15], in contrast to the “harder” coke left after stripping with He, H2, N2, O2, and alkanes gases [11,14,21–25]. For a hydrogen pressure of 1 bar and a temperature up to 700 °C, coke is not completely removed from the 0.4% Pt/LaY zeolite sample which is coked during isobutene alkylation with 1-butene [14]. However, total regeneration can be achieved at 300 °C and 15 bar of H2 [16,17].
Magnoux et al. [24] showed that the coke formed over the HY zeolite during mx-transformation at 250 °C is mainly soluble in CH2Cl2. With ageing under N2 for 6 h, it becomes insoluble, hence more polyaromatic. Tsai [25] reported that at a stripping temperature of 400 °C, 26 °C higher than the reaction temperature (374 °C), toluene disproportionation coked mordenite can be completely regenerated by H2 than by N2 or He stripping. However, H2 regeneration is effective only if the coke is “soft” with an atomic H/C ratio ≥1.
The objective of the present work is to study the regeneration of the USHY zeolite that is coked during mx-transformation at 350 °C under N2 flow for 6 h. Coked zeolite samples are first regenerated via stripping at a temperature of 500 °C and under air, H2 or N2 flow. Subsequently, the sample undergoes in situ mx-transformation, which shows the effectiveness of each regeneration gas. The regeneration under H2 flow of the USHY zeolite coked for 5 min is examined.
Coke is also characterized by temperature programmed oxidation under continuous flow of O2/He and with a constant O2 pressure. The comparison of N2 adsorption isotherms of fresh coked and regenerated by TPO (O2) zeolite samples is made.
2 Experiment
2.1 Catalyst
The USHY zeolite (Table 1) is obtained from the calcination under airflow at 500 °C for 12 h of an ultrastable NH4-Zeolite (CBV500, supplied from PQ). The unit cell parameter a0 is determined via the ASTM-D 3942-80 method using the X-ray powder diffraction pattern of the USHY zeolite. The framework Si/Al ratio (Si/Al)F is calculated from a0 using the Breck and Flanigen equation [26]. The number of extraframework aluminum atoms per unit cell (NEFAl/U.C) is estimated from the values of (Si/Al)F and total ratio (Si/Al)tot calculated from chemical analysis of Si and Al.
Characteristics of fresh USHY zeolite.
Unit cell formula | Na0.4H25.3Al25.7Si166.3O384 |
a0 (Å) | 24.4142 |
(Si/Al)tot | 2.9 |
(Si/Al)F | 6.5 |
NEFAl/U.C. | 32 |
2.2 mx-Transformation: coking reaction
The transformation of m-xylene (purity >99.5% from Fluka) is carried out with m = 600 mg of zeolite in a fixed bed reactor at 350 °C, , Pmx = 0.0625 bar with a contact time of 1/WHSV = 0.347 h. Before the reaction, the fresh catalyst sample is pretreated in situ at 500 °C, under N2 flow, and for 10 h. Then, it is cooled at the reaction temperature under N2. Prior to the reaction, the reactant is percolated on a silicagel column. At the end of a run, the coked sample is always kept under N2 for 30 min at the reaction temperature before being cooled down to room temperature under N2. The analysis of the reaction products is performed online by gas chromatography using an FID detector and a 15 m × 0.02 in D Bentone 34/DNDP Scot Capillary column. The temperature is raised from 80 to 150 °C at a heating rate of 1 °C/min.
2.3 Regeneration conditions under air, H2 and N2
The catalyst coked for 6 h is regenerated in situ in the fixed bed reactor at 500 °C and during 15 h under N2 or H2 at a heating rate of 5 °C/min. The sample coked during 5 min is regenerated under H2 in the same operating conditions. With H2, and after the coking reaction, the temperature must be cooled down to the room the temperature under N2 before switching it by H2. The same caution is taken at the end of regeneration. Under air, the coked catalyst is regenerated for 5 h. The flow of regeneration gas is the same as the flow of N2 during the coking reaction (100 ml/min).
2.4 In situ mx-transformation over regenerated USHY zeolite
The regeneration treatment is performed at 500 °C and for several gases. Afterwards, the catalyst is cooled down to the reaction temperature (350 °C) with the same gas that was used for the treatment and switched by N2. The use of H2 requires additional precautions.
2.5 Coke composition
The coke present on the catalyst (%C, %H) is measured in total burning at 1020 °C under diluted oxygen/helium with a Thermoquest Analyzer. The methodology developed by Guisnet and Magnoux [6] is used for removing the coke from the zeolite. The coked zeolite is treated with a 40% HF solution at room temperature in order to dissolve the zeolite and to free the coke. The components soluble in CH2Cl2 are extracted. The yield of extraction (Y%) is defined as the fraction of the total coke that could be extracted in CH2Cl2:
The insoluble coke yield Y′% is:
2.6 Coke oxidation with pure O2
Oxidation of a coked catalyst with 19.3% C is carried out using a MTB 10−8 Setaram Microbalance with relative and absolute sensitivities of 4 × 10−8 and 4 × 10−7 g, respectively. The microbalance is linked to a computer via a cobra interface. Before introducing 200 mbar of O2, 40 mg of coked sample is pretreated at 50 °C under 10−3 Pa vacuum until stabilization of the weight. Then O2 is introduced and the temperature is raised up to 500 °C at a rate of 5 °C/min. The sample is kept at this temperature during 15 h. After the TPO, the adsorption isotherm of N2 is recorded at −196 °C. Adsorption isotherms of fresh, coked and regenerated catalysts are obtained with the same microbalance.
The residual coke (%) is defined as:
2.7 Dynamic coke oxidation
The TPO analysis is carried out in a quartz microreactor. The 300 mg coked sample is initially pretreated in situ under pure helium (N 60, 30 ml/min) at 200 °C and for 2 h. Then the coke is burned under a 2.6% (vol.%) O2/He mixture from 200 up to 900 °C with a heating rate of 5 °C/min. The CO2 formed and unconsumed O2 are analyzed online by gas chromatography using a Porapak Q molecular sieve column (2 m) and a thermal conductivity detector.
3 Results
3.1 mx-Transformation
3.1.1 Over fresh zeolite
For the acidic USHY zeolite, the mx-transformation undergoes two competitive reactions: (a) isomerization (I) into ortho (ox) and para-xylenes (px) and (b) disproportionation (D) into toluene (T) and trimethylbenzenes (TMB). At high conversion, light products (C2–C4 alkanes–alkenes), benzene (B) and tetra-methylbenzenes (TTMB) are formed (Fig. 1).

Products (molar %) formed over fresh USHY zeolite: I = px + ox (♦), TMB (□), T (▵), TTMB (×), B (*) and light products (●) vs mx-conversion.
During the reaction, owing to the initial fast coke formation, the catalyst deactivates rapidly with the time on stream (TOS), hence with increased of the coke content. Indeed, coke content passes from 2.7% for 5 min of reaction to 19.3% for 6 h. For this last time, the catalyst is almost completely deactivated (Fig. 2). The px/ox ratio is nearly not affected by the deactivation of the catalyst while D/I ratio decreases (Fig. 3).

mx-Conversion over fresh USHY zeolite vs time on stream (min).
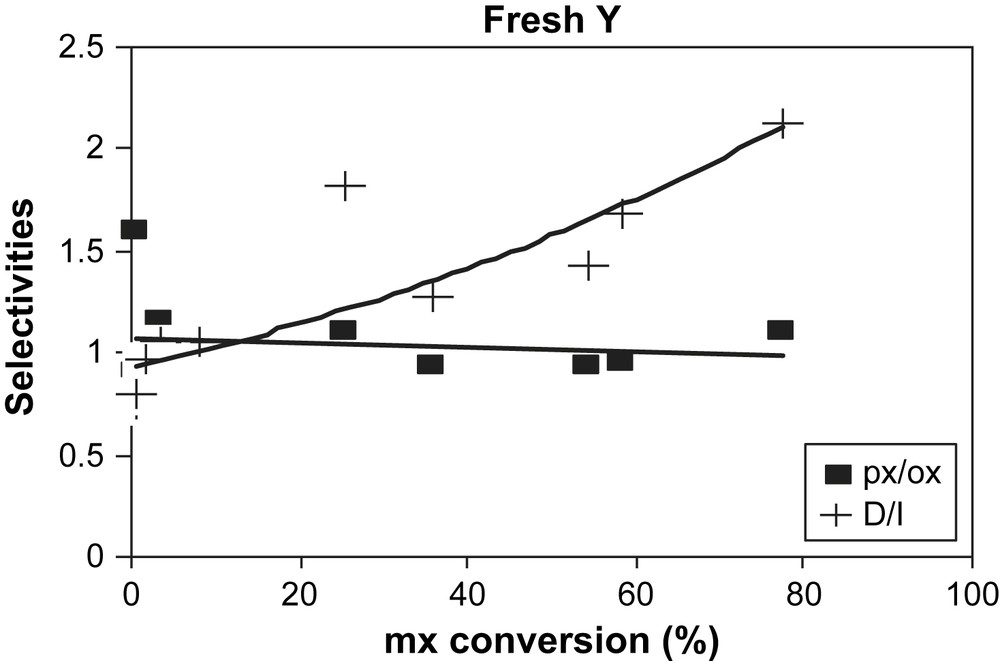
Selectivities: px/ox (■) and D/I (+) molar ratios over fresh USHY zeolite vs mx-conversion.
3.1.2 Over H2-regenerated coked samples
3.1.2.1 After regeneration of the low coked USHY
Before regeneration, the USHY sample is coked during mx-transformation at 350 °C under N2 flow and for 5 min. Coke content is then equal to 2.7%. In Fig. 4 the deactivation curves during mx-transformation of the fresh and H2-regenerated USHY samples are compared. The initial catalytic activity of the regenerated sample is quasi completely restored and the deactivation versus TOS is quite similar to that of the fresh sample. However, coke is not completely removed from the catalyst after H2 regeneration. Indeed, white color of the fresh sample becomes dark-green after coking reaction then clear grey after regeneration. The coke content decreases from 2.7%, before regeneration, to 1.74% after H2 treatment. The weak coke content could explain the similar catalytic behavior of the regenerated zeolite to that of the fresh one.

mx-Conversion over fresh (◊) and H2-regenerated USHY (▵) vs time on stream (min).
As shown in Figs. 5 and 6, compared to fresh zeolite, no particular modifications in the selectivities (px/ox and D/I ratios) are observed after H2 regeneration.
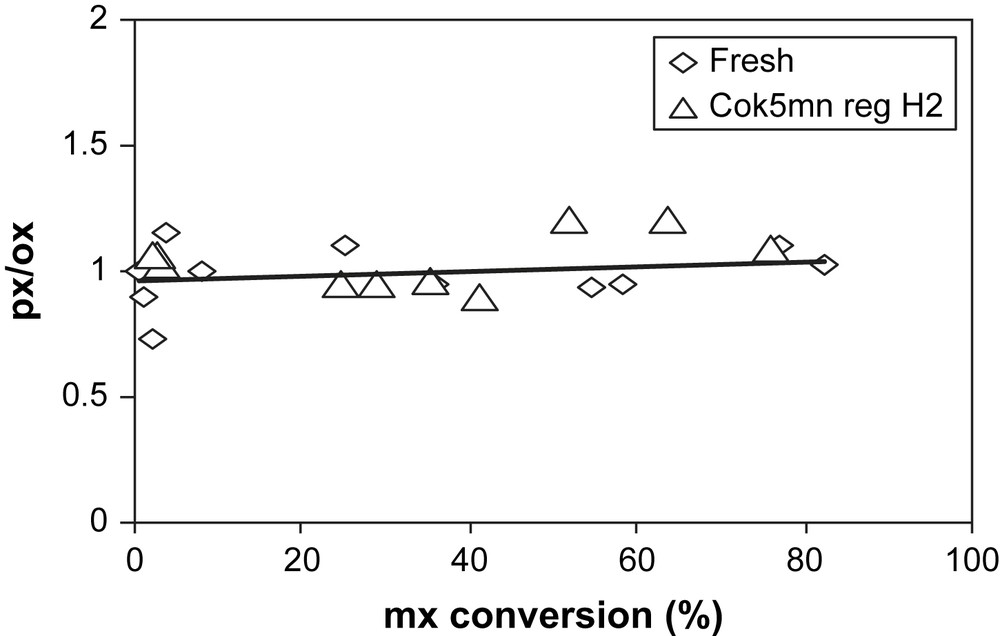
px/ox ratio vs mx-conversion over fresh (◊) and H2-regenerated USHY (▵).
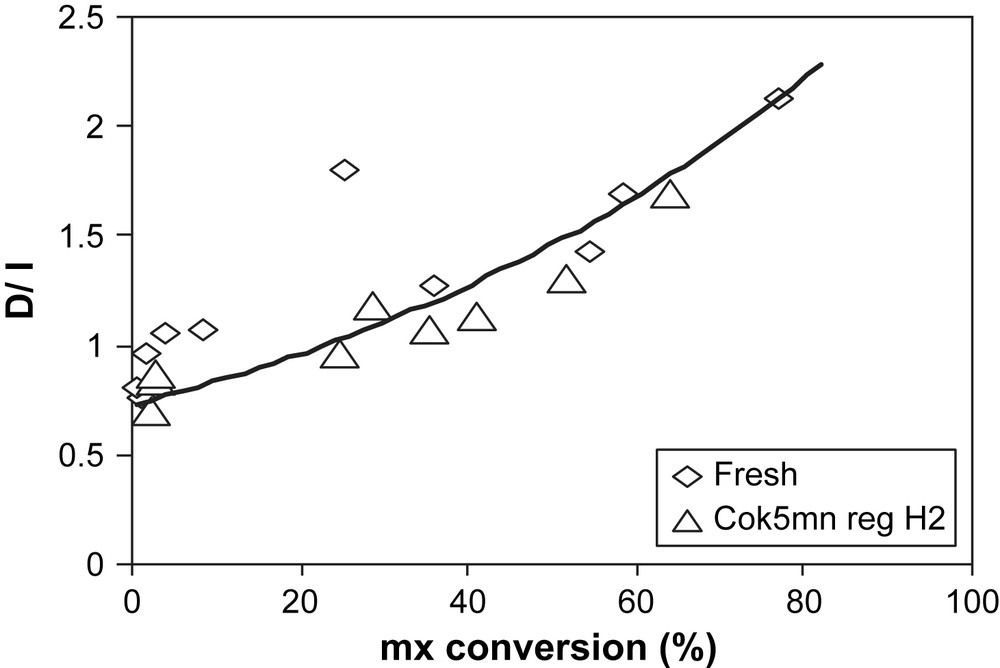
D/I ratio over fresh (◊) and H2-regenerated USHY (▵) vs mx-conversion.
3.1.2.2 After regeneration of the high coked USHY
Before regeneration, the USHY sample is coked during mx-transformation at 350 °C under N2 flow and for 6 h. The coke content of the sample is equal to 19.3%. In Fig. 7 are reported percentages of the isomerization (px, ox) and the disproportionation products (T, TMB) formed during mx-transformation over H2-regenerated sample. In Fig. 8 are compared the deactivation curves of the fresh and regenerated USHY. The initial catalytic activity of the reactivated sample is partially restored with 67% of mx-conversion instead of 82% obtained over the fresh zeolite. However, the deactivation over the regenerated sample is much more pronounced than that over the fresh zeolite. Indeed, after only 50 min of TOS, regenerated catalyst is completely deactivated, while 300 min are necessary for the fresh sample.
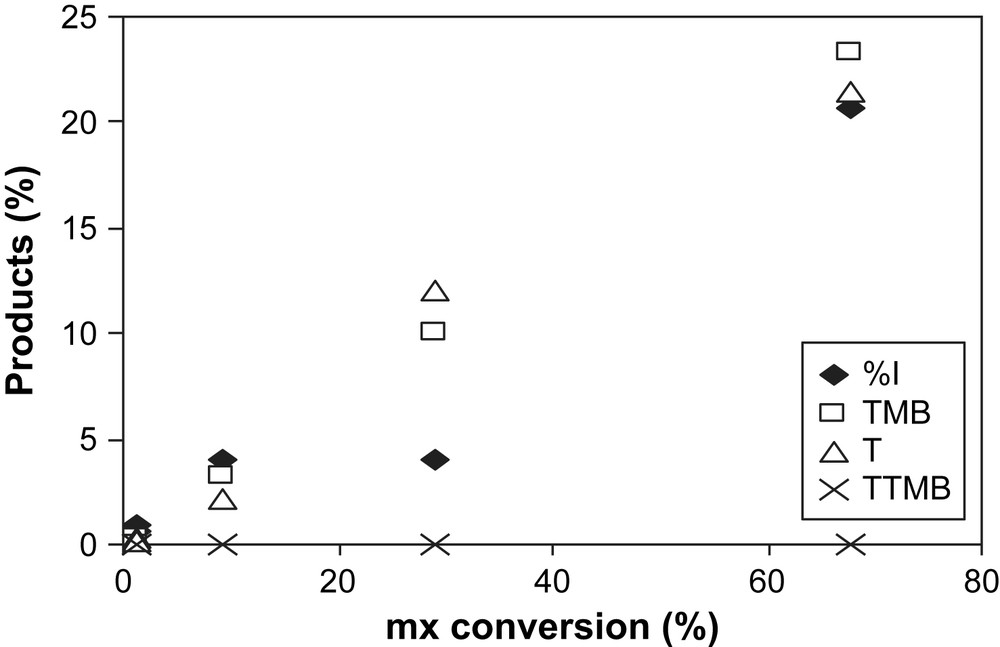
Products (molar %) formed over H2-regenerated USHY zeolite: I = px +ox (♦), TMB (□), T (▵), TTMB (×) products (●) vs mx-conversion.

mx-Conversion over fresh (◊) and H2-regenerated USHY (▴) vs time on stream (min).
After H2 regeneration, the px (the smaller isomer) is slightly more produced than that of ox. However, the px/ox ratios before and after regeneration are close (Fig. 9).
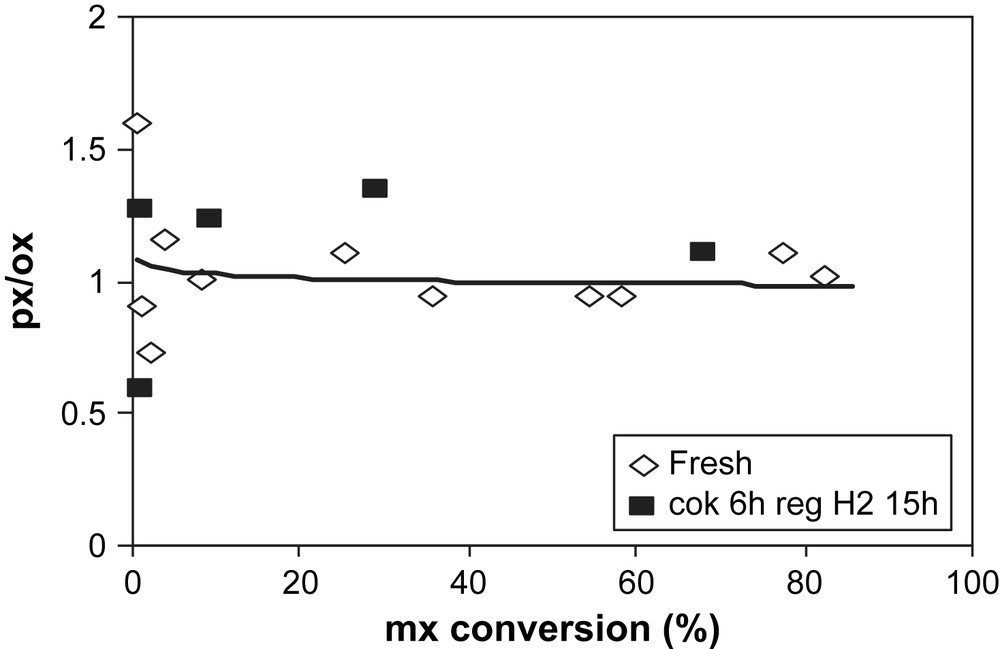
px/ox ratio over fresh (◊) and H2-regenerated USHY (▴) vs mx-conversion.
Over the fresh zeolite, the D/I ratio decreases with deactivation (Fig. 10). Over the regenerated sample, this ratio passes by a singular high value (D/I = 5.5) for the mx-conversion of 29% before decreasing. For this particular value, and as shown in Figs. 7 and 10, the disproportionation is more favorable than the isomerization.
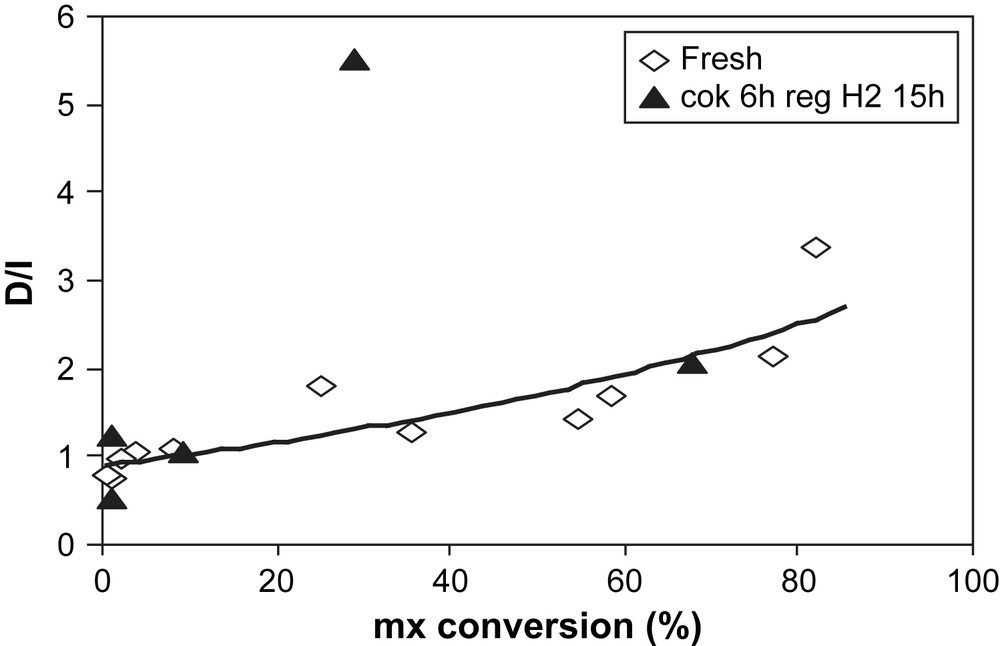
D/I ratio over fresh (◊) and H2-regenerated USHY (▴) vs mx-conversion.
3.1.3 mx-Transformation over N2-regenerated coked zeolite
The USHY sample coked with 19.3% of coke is regenerated under N2 flow at 500 °C and for 15 h. In Fig. 11 the deactivation curves obtained during mx-transformation over the fresh and N2-regenerated USHY samples are compared.

mx-Conversion over fresh (◊) and N2-regenerated USHY (–) vs time on stream (min).
The stripping of coked sample with N2 flow does not induce any significant restoration of the catalytic activity. Compared to the fresh zeolite, a loss of 93% of the initial activity is observed.
3.1.4 Over air-regenerated coked zeolite
The sample coked with 19.3% of coke is regenerated under N2 flow at 500 °C and for 5 h. In Fig. 12 the deactivation curves obtained during mx-transformation over the fresh and air-regenerated coked USHY samples are compared. Over the regenerated sample, the catalytic activity is fully restored. The initial activity is even slightly higher than that of the fresh zeolite. The isomerization and disproportionation products formed and the selectivities (Figs. 13 and 14) are quite similar to that of the fresh zeolite.
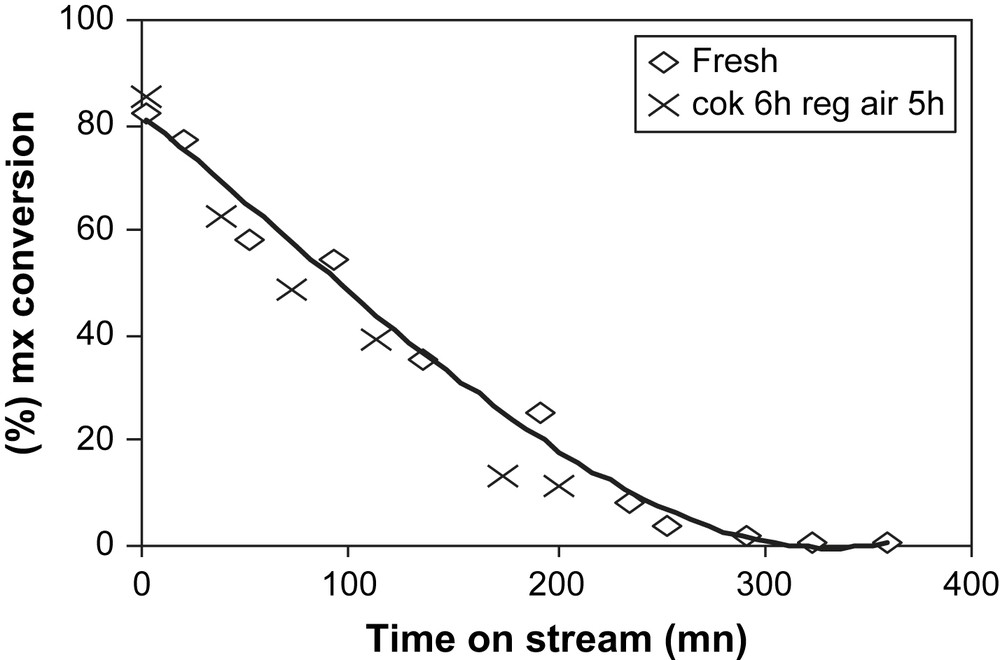
mx-Conversion over fresh (◊) and air-regenerated USHY (×) vs time on stream (min).
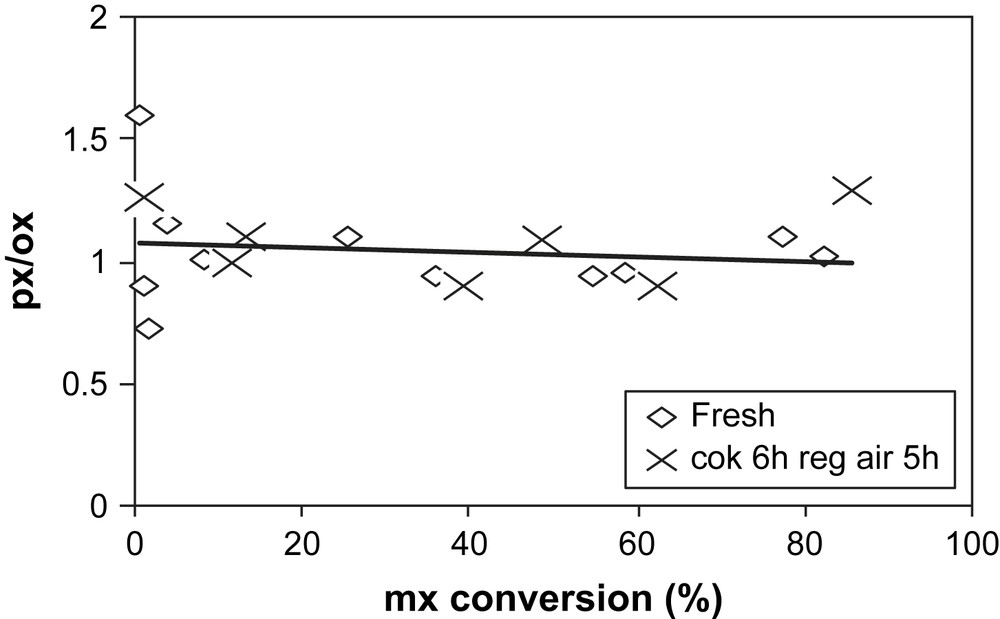
px/ox ratio over fresh (◊) and air-regenerated USHY (×) vs mx-conversion.
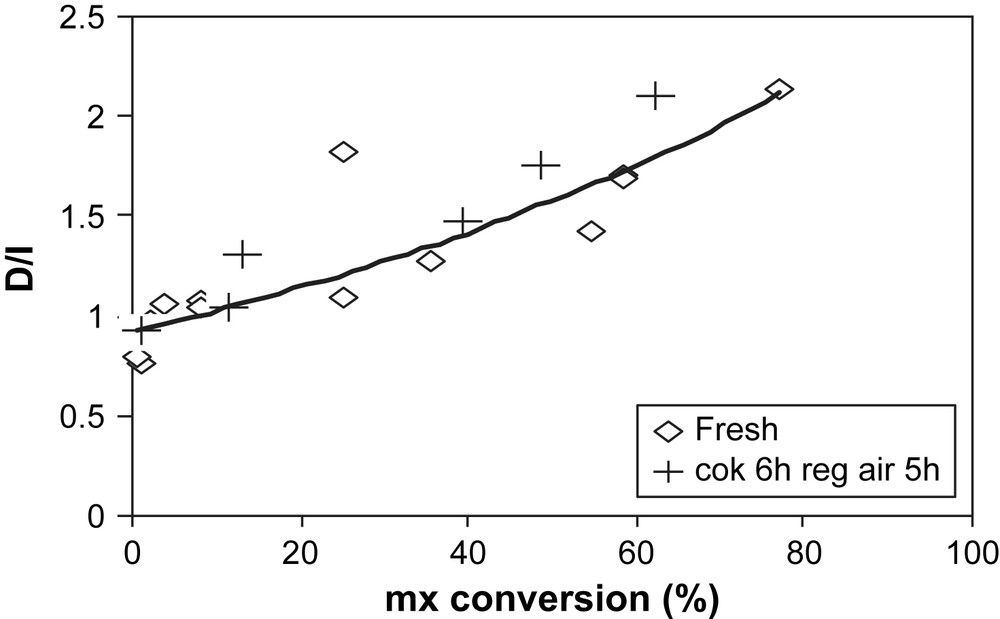
D/I ratio over fresh Y (◊) and air-regenerated USHY (+) vs mx-conversion.
3.2 Coke characterizations
3.2.1 Coke composition
After dissolution of a coked sample in acidic solution, two fractions of coke can be extracted by CH2Cl2. The results of two coked samples before regeneration are reported in Table 2. Coke content increases with TOS. We can notice that the higher the total coke content the smaller the soluble fraction. This is due to the formation of more condensed polyaromatic coke molecules.
Yields of coke extraction.
TOS (min) | 5 | 360 |
Total coke (%) | 2.7 | 19.3 |
Soluble coke (%) | 100 | 20 |
Insoluble coke (%) | 0 | 80 |
3.2.2 Temperature programmed oxidation of coke (TPO)
3.2.2.1 TPO in a microreactor under continuous flow of diluted O2/He
3.2.2.1.1 Before regeneration
In Fig. 15 are reported TPO profiles of two coked samples before regeneration with 2.7 and 19.3% of coke. The CO2 formed and the unconsumed O2 are the only products detected by TCD analysis. TPO profiles show that CO2 formation starts at 320 °C with a maximum production at 580–680 °C and the final oxidation temperature is at 725–750 °C. After TPO, the catalyst color becomes white as the fresh zeolite. No particular modification in the TPO profiles is observed with the increase of the zeolite coke content.

TPO profiles of coked zeolites before regeneration (■ 2.7% C, ◊ 19.3% C).
3.2.2.1.2 After H2 regeneration of the low coked USHY
TPO profiles of USHY coked (2.7% C) and USHY regenerated sample, under H2 (Fig. 16), show that H2 cannot remove completely the coke from the catalyst even if the initial coke content is weak (Table 3). A shift of the starting and the final temperatures of CO2 formation to higher oxidation temperatures are observed after H2 regeneration. Indeed, CO2 formation starts at 400 °C instead 320 °C for coked Y and the final temperature is shifted to 900 °C, 150 °C higher after regeneration. This confirms the more “harder” nature of remaining coke in the zeolite after H2 regeneration. However, this does not affect the catalytic activity of regenerated zeolite which is quite similar to that of the fresh catalyst.

TPO profiles of USHY samples before (♦ 2.7% C) and after regeneration under H2 (○).
Carbon content (wt%), coke loss (%) and color of the catalyst before and after H2 regeneration and TPO.
Sample | Fresh USHY | Before H2 regeneration | After H2 regeneration |
Total coke (%) | 0 | 2.7 | 1.74 |
Carbon loss (%) | 0 | 0 | 35.3 |
Color | White | Dark-green | Clear grey |
Color after TPO | White | White |
3.2.2.1.3 After N2 and H2 regeneration of the high coked USHY
In Fig. 17 TPO profiles of coked USHY samples before and after N2 and H2 regenerations are compared. After N2 treatment, the starting temperature of the CO2 formation is similar to that of the coked sample, while with H2, it shifts to a higher temperature (400 °C). Whatever the gas used, N2 or H2, the final temperature of CO2 formation shifts to a higher value of 900 °C compared to 750 °C obtained with the coked sample. The shift of TPO profiles to the higher temperatures after regeneration confirms the more “harder” nature of coke. The low loss of coke (Table 4) and its “harder” nature could explain the catalytic behavior after N2 and H2 regenerations.

TPO profiles of USHY samples before (◊ 19.3% C) and after regeneration under N2 (–) and H2 (▴).
Evolution of coke content (wt%), coke loss (%) and color of the catalyst before and after H2 and N2 regenerations.
Sample | Coked for 6 h | After N2 regeneration for 15 h | After H2 regeneration for 15 h |
Coke (%) | 19.3 | 17.4 | 16.4 |
Coke loss (%) | 0 | ≈10 | ≈15 |
Sample color | Black | Black | Black |
At high coke content (19.3% C), a loss of ≈10 and 15% of total coke are removed respectively by the use of N2 and H2 treatments (Table 4). Whatever the coke content of the catalyst after coking reaction, the regeneration is relatively more efficient under H2 than N2. It is important to notice that after TPO, the color of the samples is white.
3.2.2.2 Static TPO of high coked USHY zeolite using a microbalance
USHY zeolite having 19.3% of coke is examined by TPO using a microbalance under a fixed pressure of pure O2 (200 mbar). The microbalance system involves a 3 L vessel; this volume being large, the decrease in O2 pressure is negligible. Before the TPO, the sample is treated in a vacuum (10−3 Pa) at 50 °C until a constant weight is obtained.
In Fig. 18 the relative residual weight called ‘residual coke’ and the derivative form of the gravimetric curve upon increasing temperature from 50 to 500 °C is reported. The catalyst is maintained at 500 °C for 15 h. The weight of the coked sample decreases during oxidation treatment until stabilization.
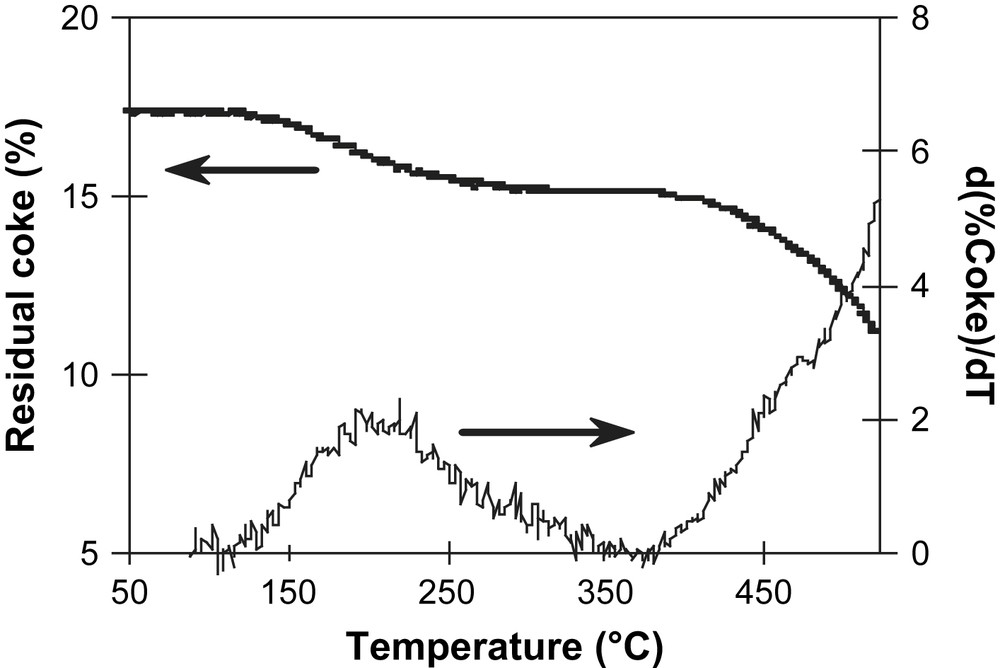
Residual coke (%) and the DTG during the TPO.
The derivative curve shows a small maximum at 250 °C due to the release of water and light products blocked in the zeolite. The initial coke oxidation temperature is close to that observed in O2/He TPO. Even a time as longer as 15 h at 500 °C, coke is not completely removed; we observe few black solid particles remaining on external surface of the sample.
3.3 Pore volume
In Fig. 19 N2 adsorption isotherms obtained with the microbalance over fresh, coked (19.3% C) and regenerated zeolite (after TPO under O2) samples are reported. As shown in Table 5, owing to the high coke content, a significant loss of the micropore (90%) and total pore (84%) volumes is observed. The regeneration of coked sample by a TPO restores a great proportion of the pore volume. Indeed, the micropore volume is completely regenerated, while only 89% of the total volume is recovered. This could be due to the presence of a little amount of “harder” coke remaining in the catalyst and to the longer time (15 h and 500 °C) which can lead to some structural modifications.

N2 adsorption capacity of fresh, coked and regenerated zeolites.
4 Discussion
The deactivation of the fresh USHY zeolite is mainly due to the rapid initial coke formation, which accompany both the isomerization and the disproportionation reactions of m-xylene. During the mx-transformation, coke content of the zeolite increases with the TOS from 2.7% for 5 min to 19.3% for 6 h. According to Cerqueira et al. [27], the deactivation of the USHY zeolite during the mx-transformation is initially due to the Brønsted acid site poisoning, pore blockage appearing at longer TOS hence at higher coke content. Our previous work [28] and those of the literature [19,20,27,29,30] showed that coke deposit leads to a decrease of the micropore volume and the Brønsted acid site density. The strong Brønsted acid sites that are in interaction with extraframework aluminum species (Si–OH–Al Al; OH IR bands at 3600 and 3525 cm−1) are the first to be eliminated by coke deposit. In the present work, 19.3% of the coke results in a decrease of 84 and 90% for the total and the micropore volumes respectively. The Brønsted active acid sites in the mx-transformation are located in the micropores.
Coke composition depends on the coke content [9,31]. This is confirmed in our study which clearly shows that coke is completely soluble in CH2Cl2 at low coke content (2.7%) and mainly insoluble in the same solvent at high coke content (19.3%). Insoluble coke molecules, which are much larger and more condensed polynuclear aromatic compounds than the soluble ones, contribute to the high deactivation of the USHY zeolite [27,31,32].
After the coking reaction, the zeolite is regenerated at 500 °C (i.e. 150 °C higher than the reaction temperature) under N2, H2 or air gases. As expected, regardless of the gas regeneration being used, the coke content of the regenerated zeolite decreases. The regeneration effectiveness of each gas is indicated by the coke loss (%) which is of 10, 15 and nearly 100% for the N2, H2 and air treatments respectively. The proportion of coke removed also depends on the initial coke content of the zeolite (before regeneration). Indeed after H2 regeneration, 35% of the coke is removed in the case of a low coke content sample against only 15% in the case of a high coke sample.
The TPO profiles for two coked samples (2.7 and 19.3%) under continuous flow of O2/He or under static oxidation with constant O2 pressure, show that the coke oxidation only starts after 300 °C and the oxidation rate is nearly independent of the coke content as reported by several authors [10,33].
The comparison of the coked and regenerated USHY TPO profiles highlights the “harder” nature of the remaining coke after the regeneration treatments. This is indicated by the shift of the final oxidation temperature towards higher values. A similar observation is reported by several authors [11,14,15,21–24] for various reactions and zeolites.
The low restoration of the catalytic properties over H2 and N2-regenerated samples can be related to the low removal of coke from the high coked samples and to the “harder” nature of the remaining coke. However, the regeneration is relatively more efficient for the H2 than for the N2 treatments. This is also reported in the literature for different reactions and zeolites [21,25].
In the present work, no significant regeneration of the catalytic activity is observed after the N2 treatment of the highly coked sample. Magnoux et al. [24] showed that the coke resulting from the mx-transformation over the USHY zeolite at 250 °C is mainly soluble in CH2Cl2. With ageing under N2 for 6 h, insoluble coke molecules appear. The deterioration of the aged zeolite activity is due to the change of the deactivation mode from site poisoning to pore blockage. Insoluble coke molecules are likely formed by dehydrogenative coupling. In our study, before the N2 treatment, 80% of the coke (19.3% C) is insoluble. So, the very low activity of the N2-regenerated sample is not surprising.
After the H2 treatment of the highly coked sample, 82% of the initial activity of the fresh zeolite is restored. However, the deactivation is faster after the H2 treatment. The partial regeneration could be due to the removal of some coke by hydrocracking reactions as reported by different authors [21–23]. Bauer et al. [22,23] explained the partial reactivation after H2 regeneration of the methanol-to-gasoline reaction coked HZSM-5 by the dissociative adsorption of H2 on a few sites of the zeolite and/or on coke molecules. Both of these facilitate the hydrocracking steps of the coke. According to Jong et al. [21], after the H2 stripping of the ethylbenzene-disproportionation coked HZSM-5, the intracrystalline coke, which is located near the Brønsted acid sites, is selectively removed by hydrocracking reactions while the extracrystalline coke is partially cracked. In our work, a partial removal of the intracrystalline coke could explain the singularly high D/I ratio obtained at 29% of mx-conversion over regenerated sample.
Our results are in agreement with those of Tsai [25], who reported that mordenite coked during the toluene disproportionation can be completely regenerated by H2 stripping, if the coke formed is “softer” than the coke of alkylpyrene with H/C > 1. The atomic H/C ratio of the coked sample (19.3% C) is less than 0.5 (coronene: H/C = 0.5). However, the total recovering of the catalytic activity over the H2-regenerated low coked USHY does not mean that the coke is completely removed from the catalyst, as shown by the TPO profiles and the carbon analysis.
All the catalytic properties (activity, selectivities) of the fresh zeolite are fully restored after air regeneration of the highly coked sample (19.3% C). This can be explained by the total regeneration of the micropore volume where the Brønsted active acid sites are located, as shown by the N2 adsorption isotherms of the fresh, coked and regenerated after TPO (O2) samples. Datka and Gil [19] showed that, upon increasing the oxidation temperature of a 9.8% C HY coked from m-xylene, the strong Brønsted acid sites (OH IR band at 3600 cm−1), which are located inside the pores and are in interaction with the extraframework aluminum, are the first to be restored. In addition, the strength of the free hydroxyl groups, which are in interaction with CO molecules, is higher for the restored zeolite than for the fresh zeolite. This last remark could explain the slightly higher initial catalytic activity observed in the present work for the regenerated zeolite.
According to Datka and Gil [19], during the regeneration, the strong Brønsted sites are first progressively restored as well as the mx-transformation activity. On the other hand, Jong et al. [21] reported that, during oxidation of ethylbenzene-disproportionation coked HZSM-5 at 500 °C under air, the rate of coke oxidation is much higher at the initial oxidation stage. A large proportion of the intracrystalline coke, located near the Brønsted acid sites, is preferentially removed than the extracrystalline coke before both cokes being burnt. In the present study, the better result obtained for the air-regenerated sample is due to the high coke removal.
5 Conclusion
During the mx-transformation, the USHY zeolite deactivates rapidly owing to fast coke formation. The catalytic properties of fresh zeolite are totally restored after air regeneration of the highly coked USHY zeolite. Through H2 treatment, partial regeneration of the initial catalytic activity is followed by a rapid deactivation. No significant reactivation in the mx-transformation is observed after the N2 treatment. If the coke is nearly totally removed from the catalyst after air regeneration, a large proportion is remaining after the N2 and H2 treatments. This residual coke is of a more “harder” nature than the original one (i.e. before N2 or H2 stripping). H2 is relatively more efficient than N2 in the catalytic activity regeneration.