1 Introduction
The growing concern about the environment is leading the chemical industry to develop clean processes, which are based on the principles of the so-called Green Chemistry or Sustainable Chemistry [1]. The main goals of Green Chemistry are the efficient use of feedstocks, preferentially renewable resources, waste minimization, and the substitution or elimination of toxic or dangerous reactants and solvents. In this context, the replacement of the conventional “several-steps” industrial processes by the catalytic “one-pot” ones is an important challenge. This is the case of the “one-step” synthesis of methyl isobutyl ketone (MIBK) from acetone over bifunctional solid catalysts.
MIBK is one of the most important products obtained from acetone (Ac). It is used mainly as a solvent for paints, inks, lacquers and protective coating systems [2,3]. It is also used in the extraction and purification of metallic ions [4–7], in the dewaxing mineral oils [8], and as initiator of polymerization processes. Its commercial production goes through a three-step process in the liquid phase:
- • aldol condensation of acetone to diacetone alcohol (DAA) over basic (Ba(OH)2, NaOH, KOH, Ca(OH)2) or acidic catalysts;
- • acid (H3PO4, H2SO4)-catalyzed DAA dehydration to mesityl oxide (MO);
- • selective hydrogenation of the MO olefinic double bond to MIBK over nickel or copper chromite or over noble metal catalysts [2,4,9–11].
The two first steps are conventional homogeneous processes and are usually equilibrium-limited and the third one may yield a relatively large amount of less useful methyl isobutyl carbinol (MIBC) and 2-methyl pentane (2MP). A one-step process using a bifunctional catalyst that could perform condensation, dehydration and reduction simultaneously would reduce the high operational costs associated to the conventional process due to the reduction/elimination of many separation and neutralization steps, of the corrosion problems associated to liquid base and acid catalysts, and of the large amount of waste, making the process more environmentally friendly. Moreover, hydrogenating MO to MIBK simultaneously with the other two previous steps would favorably shift their equilibrium and prevent the formation of high-boiling products from additional condensation [12].
In the recent years, gas-phase single-step processes operating at atmospheric pressure have been investigated by several authors using different catalytic systems that consist of Pd, Pt, Ni and Cu supported on various oxides and zeotypes such as: SAPOs [10,13], AlPO [10], calcined hydrotalcites [13–19], ZSM-5 [11,20–27], MCM-22 [28,29], MCM-56 [30,31], MCM-49 [32] hydroxyapatite [33], NaX [34,35], MgO [4,8,36,37], ALPON [38] and Al2O3 [39,40]. The results show that selectivities to MIBK in gas phase are usually below 80 %, especially due to the parallel hydrogenation of acetone leading ultimately to propene. Catalyst stability, whenever reported, is always very poor over acidic supports, since on these supports coke formation leads to fast deactivation of the catalyst [22,23,38]. On mildly acidic or basic supports, the reported catalyst stabilities [7,9,13,16] were somewhat better, but still limited. The only exception seems to be the work of Chikán et al. [4], who reported a reasonably constant MIBK yield during 24 h TOS (conversion decrease was counterbalanced by increasing MIBK selectivity along the run) at 553 K on Cu/MgO catalyst.
As to the reactions conditions, the temperature of reaction is usually kept below 473 K so as to minimize further condensation reactions that lead to the formation of high-boiling point products and catalyst deactivation. Increasing the hydrogen/acetone molar ratio reduces the deactivation but increases the hydrogenation of acetone to isopropyl alcohol, so reducing the yield of MIBK. On the other hand, a low hydrogen/acetone ratio not only contributes to catalyst deactivation but also limits acetone conversion. The production of MIBK requires one mole of hydrogen for two moles of acetone (not taking into account the direct hydrogenation of acetone) so that hydrogen is the limiting reactant for hydrogen/acetone molar ratios below 0.5.
In this work, Ni-containing mixed oxides derived from hydrotalcites are studied as bifunctional (metal + base) solid catalyst for the one-step synthesis of MIBK from acetone at atmospheric pressure. The influence of the Ni content and of its introduction method (coprecipitation or impregnation) was investigated as well as the effect of the hydrogen/acetone ratio on the catalytic performance.
2 Experimental
2.1 Catalyst preparation
Two Ni,Mg,Al-hydrotalcite like samples were prepared by coprecipitation at room temperature, as previously described [41]. While stirring vigorously, an aqueous solution (solution A) containing Ni(NO3).6H2O, Mg(NO3)2.6H2O and Al(NO3)3.9H2O (1.5 M in (Ni + Al + Mg) with an Al/(Ni + Al + Mg) atomic ratio of 0.25 and a Mg/Ni atomic ratio of 5 or 15) was slowly dropped into a highly basic carbonate solution (solution B), prepared by dissolving appropriate amounts of Na2CO3 and NaOH in distilled water so as to give a carbonate concentration of 1.0 M and a final pH of 13. The gel was aged at 333 K for 18 h. The solid obtained was then filtered and washed with distilled water (363 K) until pH 7. The Ni,Mg,Al-hydrotalcites so obtained were then dried at 353 K overnight. They were named NiHTX, where X is related to the Mg/Ni molar ratio.
The Ni,Mg,Al-mixed oxides were produced by calcination of the synthesized samples under dry air, using a heating rate of 10 K/min, from room temperature to 1023 K and keeping at this temperature for 2 h. The calcined samples were named NiMOX.
The third catalyst was obtained by wet impregnation of a Mg,Al-mixed oxide (Al/(Al + Mg) = 0.25), prepared as described above, with a 0.10 M nickel acetate solution (theoretical amount to obtain a Mg/Ni molar ratio of 5) in a rotavapor at 353 K. The solid was then dried at 353 K overnight. It was named Ni/HT5Imp. After, it was calcined at 1023 K as previously described producing the catalyst Ni/MO5Imp.
2.2 Physico-chemical characterization
The chemical composition of the synthesized samples was determined by X-ray fluorescence using a Rigaku spectrometer. X-ray powder diffraction patterns were recorded in a Rigaku X-Ray generator diffractometer with a graphite monochromator using CuKα radiation, 40 kV, 40 mA, and varying 2θ values from 5 to 80°.
The textural characteristics of the mixed oxides, such as BET specific surface area, external area (t-plot method) and pore volume (BJH method), were determined by N2 adsorption–desorption at 77 K in a Micromeritics ASAP 2000.
2.3 Catalytic tests
The gas phase reaction was carried out in a fixed-bed reactor at atmospheric pressure and 523 K during 4 h. The reactants were fed to the reactor by bubbling hydrogen through a saturator held at the desired temperature. Three different H2/Ac molar ratios (0.5, 2.0 and 6.2) were investigated and the space velocity was varied in order to obtain isoconversion close to 10%. The exit stream was analyzed by on-line gas chromatography with a CP-Sil 5 CB column and a flame ionization detector. CG-MS analyses were also used for proper product identification, in addition to the comparison with the retention time of standard compounds. Before the catalytic tests, the mixed oxides (obtained by calcination under the conditions mentioned on item 2.1) were treated “in situ”, under N2 (25 mL/min) from room temperature to 673 K, using a heating rate of 5 K/min, and kept at this temperature for 2 h. Then, nickel species present in the catalysts were reduced under H2 (20 mL/min) at 873 K for 2 h.
The conversion of acetone (XA) and the selectivity to the various products (Si) were defined on the basis of converted acetone [9,12]:
(1) |
(2) |
(3) |
(4) |
(5) |
Accordingly, the activities were also defined on the basis of converted acetone (mol acetone/h/gcat), as follows:
(6) |
(7) |
(8) |
The MIBK yield was defined as:
(9) |
Conversion, selectivity and activity values reported for each run refer to those taken at steady conditions, typically at 70 min time on stream. MIBK yield was taken at the beginning and at 70 and 240 min time on stream.
3 Results and discussion
3.1 Physico-chemical characteristics of the samples
The chemical composition of the catalyst samples is presented in Table 1. They are similar to those of the synthesis gels, indicating a near complete incorporation of the cations in the HTLC layered structure.
Chemical composition. textural characteristics, and reducibility (from TPR analysis) of the studied catalysts.
Sample | Mg/Ni | Al/(Al + Mg + Ni) | Al/(Al + Mg) | SBET (m2/g) | Vmeso (cm3/g) | % Ni reduced |
NiMO5 | 5.4 | 0.24 | - | 223 | 0.667 | 58 |
NiMO15 | 15.1 | 0.24 | - | 220 | 0.650 | 64 |
Ni/MO5Imp | 5.0 | - | 0.24 | 181 | 0.629 | 95 |
The XRD patterns of NiHT5 and NiHT15 samples are shown in Fig. 1. They exhibit sharp and symmetrical reflections for (003), (006), (110) and (113) planes and broad and asymmetric reflections for (102), (105) and (108) planes, characteristic of a well-crystallized HTLC in carbonate form. No other phase was detected, suggesting that both Ni2+ and Al3+ have isomorphically replaced Mg2+ cations in the brucite-like layers. For sample Ni/HT5Imp, hydrotalcite diffraction pattern was also observed indicating that the lamellar structure of hydrotalcite was restored upon the wet impregnation process. Moreover, the presence of two peaks at 11.00° and 21.40° (×) can be probably associated to the insertion of nickel acetate into part of the lamellar structure causing the shifting of planes (003) and (006), as suggested by Rietveld refinement analysis.
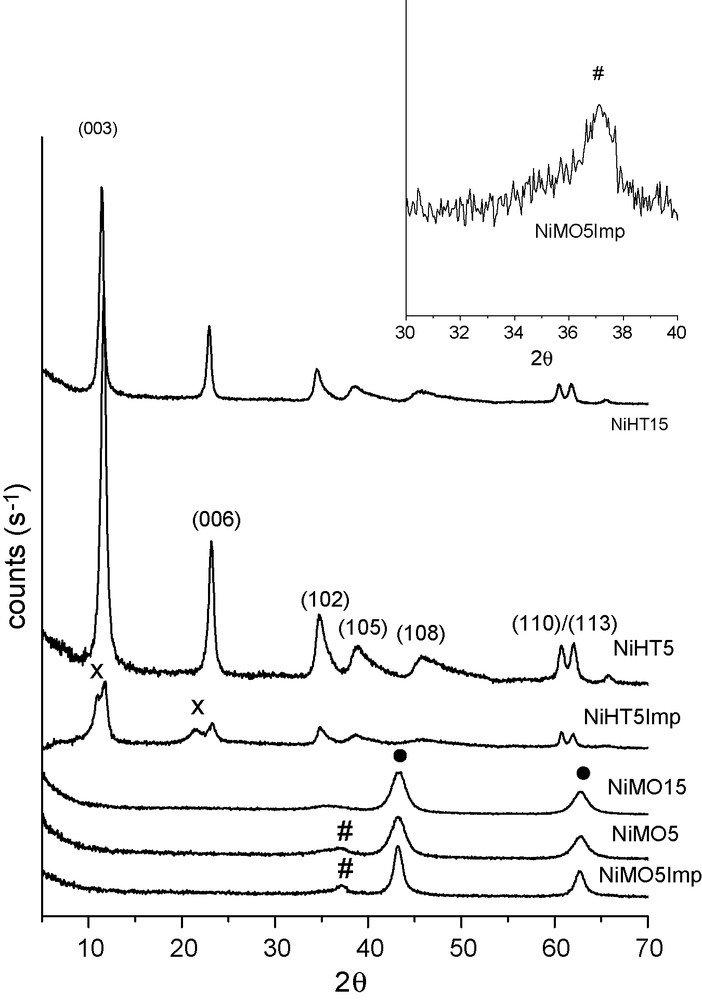
X-ray diffractograms for the as-synthesized and the calcined Ni,Mg,Al-HTLC samples.
For the three samples (NiHT5, NiHT15, and Ni/HT5Imp), the characteristic lamellar structure disappears after calcination up to 1023 K and X-ray diffractograms show the presence of a poorly crystallized Mg(Ni,Al)O periclase-type phase (•) (peaks at 2θ equal to 35.70o, 43.40o and 62.90o) (Fig. 1). These results indicate a good dispersion for both nickel and aluminum oxides in the MgO matrix. For samples NiMO5 and Ni/MO5Imp, the presence of a low-intensity peak at 36.90° suggests the segregation of a low-crystallinity NiO bunsenite-type phase (#) along with the Mg(Ni,Al)O phase.
Inspection of the N2 adsorption/desorption results indicated that all samples presented IUPAC type IV isotherms, confirming that the thermal decomposition of the HTLC samples at 1023 K produced mesoporous mixed oxides. Their main textural characteristics are also shown in Table 1. It can be observed that for samples in which nickel was incorporated by coprecipitation, the nickel content does not influence the textural characteristics whereas sample Ni/MO5Imp (nickel incorporated by impregnation) showed a slightly lower specific surface area and mesopore volume, which should be related to the presence of the NiO bunsenite-type phase.
The reducibility of nickel species present in the studied samples was previously investigated by TPR analysis [41,42]. Two reduction peaks were observed in the TPR profiles being associated to nickel species with different interaction with the Mg(Al)O matrix. The first and small one, in the range 420–700K was associated to the reduction of NiO weakly interacted with the Mg(Al)O-phase. The increase in the Ni content promoted a weakening of this interaction, resulting in lower reduction temperatures. The decrease in NiO reducibility with the decrease in Ni content was also reported on literature [43] and may be attributed to the increase in the effect of the presence of foreign ions (Mg2+ and/or mainly Al3+) inside the NiO phase.
The second peak, observed at 1050–1100 K was related to the reduction of nickel species strongly interacted with the matrix [44]. The temperature range for reduction of NiO in Ni,Mg,Al mixed oxides is higher than that reported for the reduction of supported NiO [14], confirming that the homogeneous interdispersion of the elements in HTLCs gives rise to a strong interaction among them in the correspondent mixed oxide.
The TPR results also show an incomplete reduction of the nickel species (Table 1), particularly for the samples prepared by coprecipitation, and confirm the lower reducibility of nickel on the Ni,Mg,Al mixed oxides with low Ni content, when compared to that observed for Ni-rich similar materials [45]. As to the influence of the method of preparation of the sample, the incorporation of nickel through impregnation increases the reducibility of nickel species, as indicated by both the higher fraction on nickel reduced and the slightly lower reduction temperatures observed for sample Ni/MO5Imp.
3.2 Catalytic tests
The products identified from acetone (Ac) transformation were propane (C3), isopropyl alcohol (IPA), methyl isobutyl ketone (MIBK), methyl isobutyl carbinol (MIBC), 2-methyl pentane (2MP), mesithyl oxide (MO), mesithyl oxide isomer (iMO), diisobutyl ketone (DIBK), 4,6-dimethyl-heptan-2-one (iDIBK), 1,3,5-trimethyl benzene (TMB), isophorone (IPH), and 2,6-dimethyl-2-hepten-4-ol (DMHA). Their formation can be explained by means of the reaction scheme suggested in Fig. 2. DAA formed by the aldol condensation of acetone on basic sites is dehydrated to MO and iMO, which are hydrogenated to MIBK on metallic sites or condensed further to trimers (TMB, IPH). MIBK may go through additional condensation and hydrogenation steps ultimately leading to DIBK, iDIBK, DMHA, and a compound with 12 carbon atoms (C12) (not identified, due to the low molar fraction on the reactor stream) or may be hydrogenated to MIBC, which after further hydrogenation can lead to the formation of 2MP. Along a parallel reaction, acetone can also be directly hydrogenated to IPA, which is dehydrated and hydrogenated to propane. Therefore, acetone transformation occurred by two main routes: (H) hydrogenation of acetone, producing IPA and C3 and (C) aldol condensation of acetone, forming MIBK and other condensation products (Fig. 2).

Main reactions observed during acetone transformation.
In this work, DAA, MIBC, and 2MP were not observed among the products and those products whose seletivities were lower than 1% were not shown in the figures. The absence of DAA confirms its rapid dehydration, whereas the absence of MIBC and 2MP suggests that MIBK undergoes preferentially condensation on basic sites than hydrogenation on the metallic ones.
3.2.1 Effect of Mg/Ni molar ratio (coprecipitated samples)
The influence of the Mg/Ni molar ratio on mixed oxides was studied at 523 K, with an H2/Ac ratio of 2.0 and isoconversion of 10%. The increase in the Mg/Ni molar ratio from 5 to 15 (decreasing the nickel content) changed significantly the activity and the selectivities to the products. As shown in Table 2, the decrease of the nickel content led to the decrease of both overall and hydrogenation activities with a slightly increase in condensation activity. These trends were reflected in the product selectivity (Fig. 3), since for NiMO15 only heavier condensation products (DIBK, TMB, IPH, DMHA and C12) were observed, MIBK, IPA and C3 being absent. On the other hand, for sample NiMO5, MIBK, DIBK, C12 and mainly IPA were the products formed.
Effect of Mg/Ni ratio and of nickel incorporation on the total activity (At), on the activity for acetone hydrogenation (Ah) and on the activity for aldol condensation of acetone (Ac) (reduction temperature = 873 K, reaction temperature = 523 K, H2/acetone ratio = 2.0).
Sample | X (%) | WHSV (h-1) | Ao (× 103) (mol/h gcat) | Ah (× 103) (mol/h gcat) | Ac (× 103) (mol/h gcat) |
NiMO15 | 9.7 | 48 | 80 | 0 | 80 |
NiMO5 | 10.6 | 89 | 162 | 92 | 70 |
Ni/MO5Imp | 13.2 | 162 | 368 | 165 | 203 |
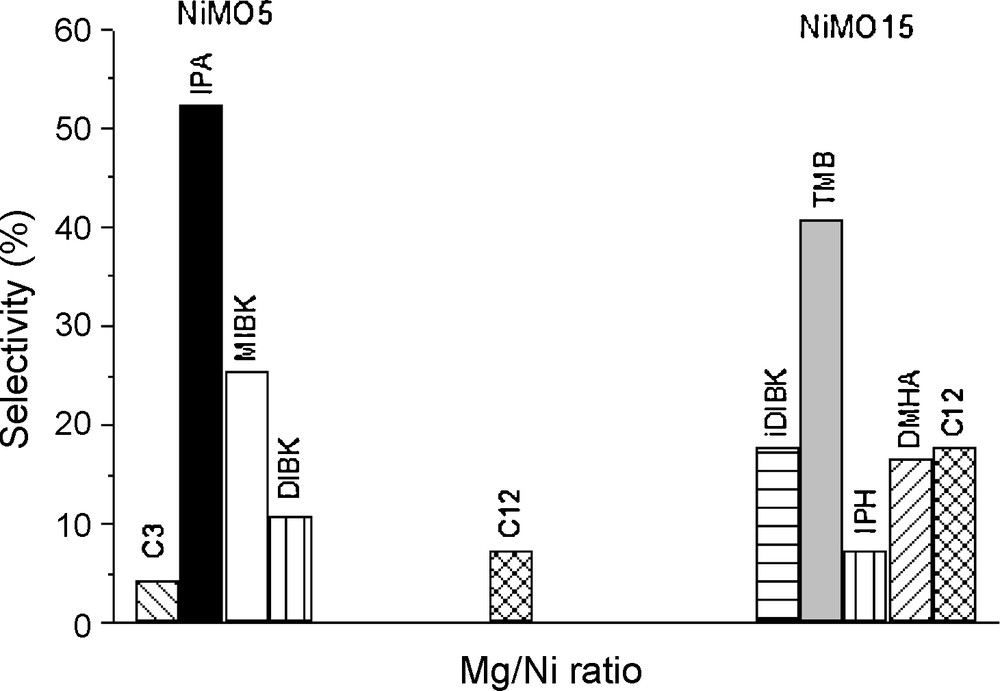
Effect of Mg/Ni ratio on selectivities for NiMO5 and NiMO15 (reaction temperature = 523K, reduction temperature = 873K and H2/acetone ratio = 2.0).
These results reflect not only the lower nickel content on sample NiMO15, but also the strong interaction between nickel oxide and the Mg(Al)O phase, which increases as nickel content decreases, making its reduction more difficult. The decrease in NiO reducibility with the decrease in nickel content (Table 1) was also reported in the literature [14,41,43] and may be attributed to the increase on the effect of the presence of MgO that favors the dispersion and diffusion of Ni2+ ions in the mixed oxide lattice, thus restricting easy accessibility of the NiO surface to the reducing gas [17,43]. This effect occurs in addition to the metal–alumina interaction and was higher on the sample with lower nickel content. Thus, the deficiency of metallic sites in the NiMO15 catalyst hinders the hydrogenation steps favoring MO condensation catalyzed by basic sites.
From these results, the atomic ratio Mg/Ni equal to 5 was selected to investigate the influence of the nickel incorporation methodology on the catalytic performance.
3.2.2 Effect of nickel incorporation procedure
The effect of the nickel incorporation procedure was also studied at 523 K, with a H2/Ac ratio of 2.0 and isoconversion of 10%. In these conditions, sample Ni/MO5Imp (obtained by impregnation) showed higher total (At), hydrogenating (Ah) and condensation (Ac) activities (Table 2), which can be associated to an increase in the number of metallic sites leading to a more adequate balance between basic and metallic function. As previously shown, the reduction of nickel species on the Ni-Mg-Al mixed oxides occurs at lower temperatures for samples in which nickel species were introduced by impregnation [42].
Fig. 4 shows that the same products are formed in both catalysts (NiMO5 and Ni/MO5Imp) but their selectivities are different. For sample in which nickel was incorporated by impregnation, the selectivity to MIBK and to DIBK was favored at IPA's expense.
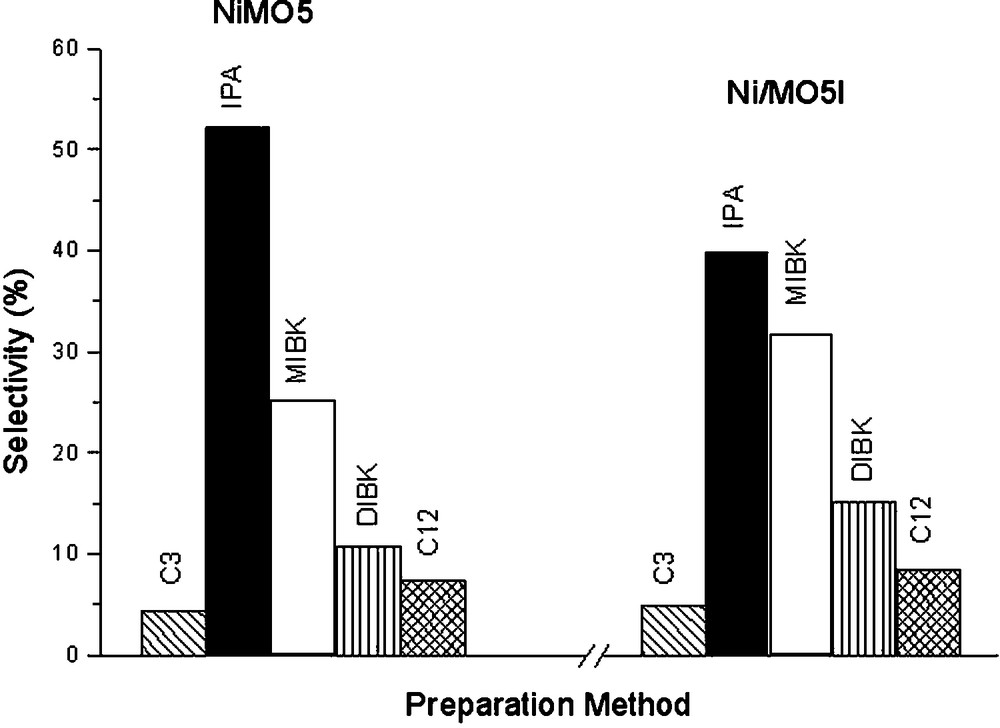
Effect of the preparation procedure of the samples on selectivities for NiMO5 and Ni/MO5Imp (reaction temperature = 523K, reduction temperature = 873K and H2/acetone ratio = 2.0).
The high values of IPA/C3 ratio suggest that, in the studied conditions, the desorption of IPA from the hydrogenation sites is favored with respect to its conversion to C3 on the dehydration sites (Fig. 2).
3.2.3 Effect of H2/Ac ratio
The influence of H2/Ac molar ratio was studied over sample Ni/MO5Imp at 523 K and isoconversion (10–13%). As expected, increasing H2/Ac molar ratio in the range 0.5 to 6.2 had a negative effect on the aldol condensation activity while the direct hydrogenation of acetone increased significantly (Table 3). Concerning the product selectivities, shown in Fig. 5, the increase in H2/Ac from 0.5 to 2.0 increases the hydrogenation of MO to MIBK and of acetone to IPA. The increase of MO hydrogenation seems to prevent the formation of some aldol condensation trimers and tetramer such as TMB, IPH and C12. Further increase in H2/Ac to 6.2 virtually inhibits route (C) (MIBK selectivity decreases significantly) and selectivity to IPA exceeds 80%. Taking into account the total activity, the apparent reaction order with respect to hydrogen was –0.6.
Effect of the H2/acetone molar ratio on the total (At), on the acetone hydrogenation (Ah) and on the aldol condensation (Ac) activities for sample Ni/MO5Imp (reduction temperature = 873 K, reaction temperature = 523 K).
H2/acetone ratio | X (%) | WHSV (h-1) | Ao (× 103) (mol/h gcat) | Ah (× 103) (mol/h gcat) | Ac (× 103) (mol/h gcat) |
0.5 | 10.4 | 301 | 540 | 87 | 453 |
2.0 | 13.2 | 162 | 368 | 165 | 203 |
6.2 | 11.4 | 127 | 307 | 281 | 26 |
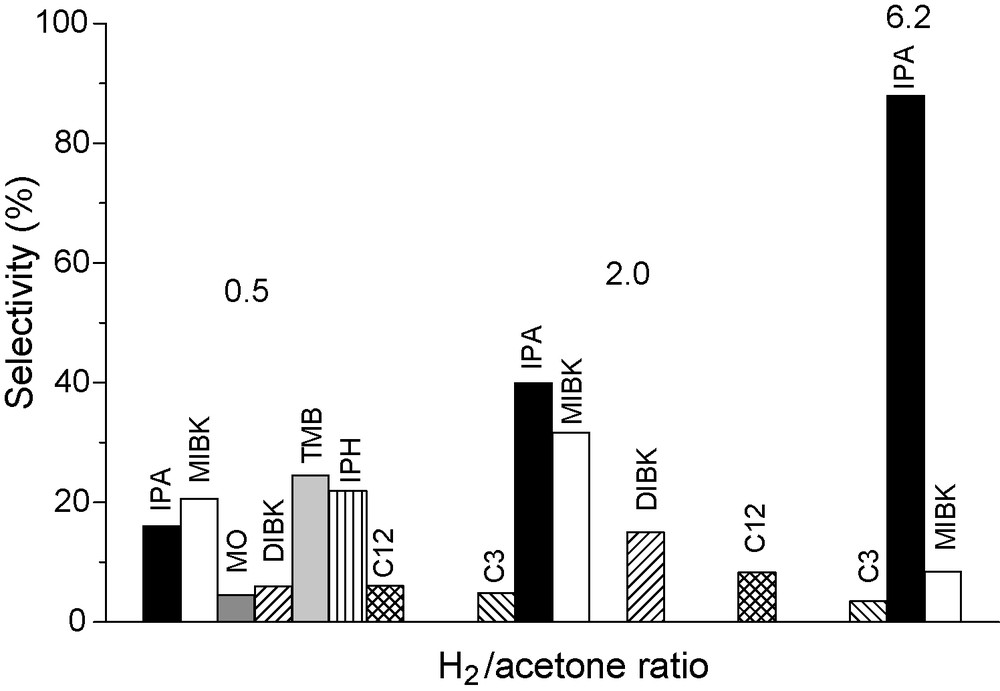
Effect of the H2/acetone ratio on selectivities for Ni/MO5Imp (reaction temperature = 523K and reduction temperature = 873K).
3.2.4 Stability
The catalytic stability, expressed by the variation of acetone conversion with time on stream, of samples NiMO5 and Ni/MO5Imp was evaluated at 523 K with H2/Ac molar ratio of 2.0. Both catalysts were rather stable up to 4 h after an initial transient period of about 40 min, as shown in Fig. 6 for sample Ni/MO5Imp. On the other hand, when sample NiMO15 (lower nickel content) was evaluated at the same conditions, it showed strong deactivation, which can be attributed to the formation of heavier products. These results can be associated to the inadequate balance between basic and metallic sites on sample NiMO15 with a predominance of the former. As reported in the literature, a too basic support induces additional condensation reactions, creating the heavier products responsible for catalyst deactivation [4,8].

Stability of Ni/MO5Imp (reaction temperature = 523K, reduction temperature = 873K and H2/acetone ratio = 2.0).
3.2.5 MIBK yields
Table 4 shows the MIBK yield (mmol MIBK.h−1 gcat−1) along the reaction (10, 70, and 240 min time on stream) for the studied catalysts, at 523 K, using different H2/Ac molar ratio. At 70 min time on stream, the highest productivity (close to 60 mmol MIBK.h−1 gcat−1) was obtained for Ni/MO5Imp sample when using H2/acetone ratio of 2.0, although good results were also observed for this catalyst using a lower H2/acetone ratio. By comparing the MIBK yields at different reaction times, it can be observed that for sample Ni/MO5Imp, this parameter did not change significantly during 240 min time on stream, confirming the better stability of this catalyst.
MIBK yield (mmol MIBK h−1 gcat−1) at 523 K.
Sample | H2/acetone ratio | Yield (10 min) | Yield (70 min) | Yield (240 min) |
NiMO5 | 2.0 | 38.6 | 20.5 | 12.1 |
NiMO15 | 2.0 | 0.0 | 0.0 | 0.0 |
Ni/MO5Imp | 2.0 | 56.0 | 58.3 | 52.5 |
Ni/MO5Imp | 6.2 | 20.9 | 13.0 | 8.4 |
Ni/MO5Imp | 0.5 | 106.9 | 55.8 | 10.4 |
These results seem to confirm that Ni/MO5Imp is a promising catalyst for the one-step synthesis of MIBK. However, they are poorer than those reported by Chen et al. [14], who investigate the influence of the reduction temperature and of the nickel content impregnated on Mg,Al-mixed oxides and reported MIBK and IPA selectivities of 61.5 and 11.3%, respectively, at 413 K and H2/acetone of 0.20, for the catalyst containing 3 wt% of Ni and reduced at 823 K.
However, the comparison between our results and those of Chen et al. [14] must be made carefully since there are some differences among the catalytic systems such as the Mg/Al molar ratio, the calcination temperature of the hydrotalcite precursor, the Ni content and the reduction temperature. Particularly for the latter, our catalytic system seems to require reduction temperatures higher than 873 K to optimize the amount of metallic sites to promote an adequate balance between these sites and the metallic ones. The effect of Ni content must also be investigated. Thus, additional studies must be carried out on our catalytic system in order to increase not only the catalytic activity but mainly the MIBK selectivity.
4 Conclusions
The results obtained in this work show that mixed oxides containing nickel with a Mg/Ni ratio of 5 and reduced at 873 K can perform the one-step synthesis of MIBK in gas phase at atmospheric pressure with good activity, selectivity and stability at 523 K and H2/Ac molar ratio in the range 0.5–2.0. The absence of both strong acidic and strong basic sites and a proper balance between the metallic and the basic properties seems to be responsible for this promising behavior. However, additional studies must be performed aiming at improving MIBK selectivity.