1 Introduction
The utilisation of biomass is getting increased attention as a prospective source of renewable energy [1]. Among all biomass conversion processes, gasification [2,3] is one of the most promising thermochemical process carried out at high temperatures in order to optimize the gas production. In presence of steam, a quite clean synthesis gas is formed: syngas (H2 and CO) along with CO2 and CH4. However the main drawback in gasification technologies is the formation of solid residues consisting of char, ash, volatile alkali metals and a complex mixture of condensable single to multiple ring aromatic compounds known as “tar” [4,5]. It is necessary to remove tar from the syngas before further applications because it leads to various problems as polymerisation and condensation and the carbonaceous structure formed can plug the processing equipment. In the other hand, for the commercial use of biomass gasification as a source of hydrogen for fuel, of syngas and of electricity production with fuel cells (SOFC), tars are a brake technology. Anyway, tar contains a significant amount of potential energy and can be converted by catalytic steam reforming in H2, CO and CO2 gases that improve gas production. This represents a challenge for the development of gasification technology.
Among the various gasification processes studied, the fast internally circulating fluidized bed (FICFB) or the dual fluidized bed process (DFB) demonstrated good performance in biomass steam gasification and in a hydrogen rich gas production [6–8]. One of the most adapted catalysts for this process was olivine, which revealed good efficiency in tar removal [9–11]. Olivine is an iron and magnesium orthosilicate and is attractive for fluidized bed process due to its attrition resistance. Knowing that iron is present in olivine structure [12,13], is effective in tar decomposition [14,15] and in water gas shift reaction (WGSR) [16,17], an iron/olivine catalyst up to 20 wt% of iron has been designed by impregnation method in order to improve olivine activity in tar reforming [18].
A range of studies considers phenol [19], naphthalene [20] or toluene [23] as tar model compound. Toluene has been chosen as tar model compound because it is one of the major tar species formed during wood gasification with high-temperature processes [4,5] and its presence in class 3 of the established tar protocol [4,21].
The aim of this work was to study 20% Fe/olivine catalyst in toluene steam reforming reactivity. Operating conditions have been studied to optimize the catalyst activity (temperature, H2 to steam ratio). The catalyst was compared to Ni/olivine, a previously developed catalyst [22], which showed good efficiency [23]. Characterization techniques such as X-ray diffraction (XRD), temperature programmed reduction (TPR), and Mössbauer spectroscopy were used to understand the physicochemical properties of the Fe/olivine catalysts before and after test and their activity in toluene steam reforming.
2 Experimental
2.1 Catalyst preparation
The olivine used as catalytic support came from Austria (Magnolithe GmbH) and have been calcined at 1600 °C over 4 h. It is a silicate mineral in which magnesium and iron cations are embedded in the tetrahedral silicate. The elemental analysis performed by ICP-MS on this mineral permitted us to write the global formula of the olivine structure: (Mg0.93Fe0.07)2SiO4. The present iron is about 50% in the olivine structure as Fe (II) and the other half as Fe (III) due to the oxidation of Fe (II) during the calcination [13].
The Fe/olivine catalysts were synthesized by olivine impregnation (400–600 μm grain size) with an iron nitrate aqueous solution (Fe(NO3)3.9H2O). The water excess was evaporated by rotary evaporator at 100 °C during 1 h, leading to 20 wt% Fe/olivine. The samples were dried overnight at 100 °C and calcined at 400 °C, 900 °C, 1000 °C, 1100 °C or 1400 °C over 4 h after an increasing temperature rate of 3 °C/min [18].
2.2 Characterization techniques
XRD patterns were acquired with a Brucker AXS-D8 Advanced using CuKα radiation to identify the crystalline phases. Spectra were obtained in a 2θ range of 20–90°. The diffraction spectra have been indexed by comparison with the Joint Committee on Powder Diffraction Standards (JCPDS) files.
The Mössbauer spectra measurement was carried out in the transmission mode with 57Co diffused into an Rh matrix as a source moving with constant acceleration. The spectrometer (Wissel) was calibrated by means of a standard α-Fe foil, and the isomer shift was expressed with respect to this standard at 293 K. The fitting of the spectra was performed with the help of the NORMOS program.
To quantify the amount of reducible iron, TPR was performed on 50 mg of sample, in a flow of 3.85% of hydrogen in argon (total flow of 52 mL/min). The temperature was increased at a speed of 15 °C/min from room temperature to 900 °C and the hydrogen consumption of the samples has been determined by a thermal conductivity detector.
2.3 Catalytic tests
The steam reforming of toluene was carried out in a fixed-bed quartz reactor (inner diameter 8 mm), which was placed in a furnace in which the heating is monitored by means of a thermocouple. Water and toluene were introduced by syringe pumps into a vaporization furnace (250 °C) and then were carried to the reactor by a flow containing a mixture of argon (carrier gas) and nitrogen (internal standard).
The catalyst bed (400 mg, 8 mm height) was supported by quartz wool and a total flow of 3L/h (GHSV: 7500/h) passes thought it and the temperature range from 750 to 850 °C is chosen to cover all possible conditions that may occur in practice in a gasifier.
Toluene concentration (0.8% vol of the total flow) was fixed at 30 g/Nm in order to perform catalytic tests in more sever conditions than the average tar concentration (5 –15 g/Nm) in the gas produced by the wood biomass gasification [4,7]. The water concentration (12% vol of the total flow) was fixed to be in the stoichiometric conditions as in Eq. (1):
C7H8 + 14H2O → 18H2 + 7CO2 | (1) |
Further toluene steam reforming has been performed in presence of hydrogen because hydrogen is formed in the real conditions of biomass gasification.
The gaseous effluent was analysed by two gas chromatographs (Delsi Instruments Di200 and Delsi Nermag Instruments) equipped by TCD. A set of two traps located at the reactor outlet was used to recover the toluene fraction unconverted and/or the possible aromatics compounds heavier than toluene in order to prevent condensation in the gas chromatograph lines.
3 Results
3.1 Catalysts characterization
3.1.1 X-ray diffraction
XRD patterns (Fig. 1) revealed that the olivine structure ((Mg,Fe)2SiO4) was maintained after iron impregnation and thermal treatments. The rays intensities of the α-Fe2O3 and spinel phases (which could be either MgFe2O4, Fe3O4, γ-Fe2O3) less intense in the olivine sample increased with an increase in calcination temperature until 1100 °C whereas the enstatite phase initially present in olivine (MgSiO3 at 2θ = 28.2°) decreases in the iron/olivine catalysts. After calcination at 1400 °C, the intensity of the iron phases in the 20% Fe/olivine catalyst decreases while the enstatite phase increases significantly.
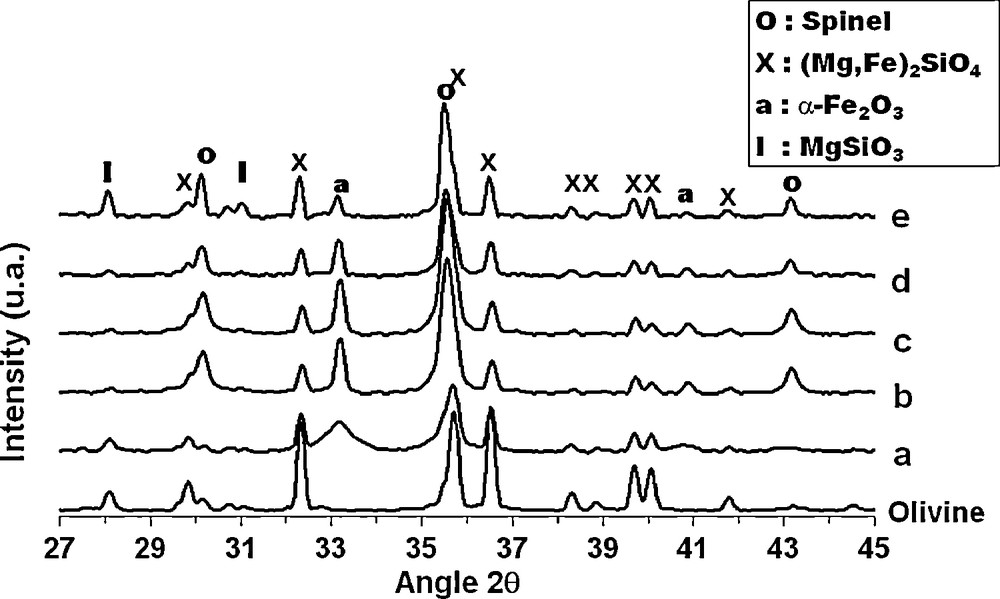
XRD patterns for the olivine and 20% Fe/olivine calcined at different temperatures: (a) 400 °C, (b) 900 °C, (c) 1000 °C, (d) 1100 °C and (e) 1400 °C.
Following Eq. (2) Swierczynski et al. [13] concluded from XRD and Mössbauer studies that between 400 °C and 1100 °C, iron (II) from the olivine structure is rejected by oxidation into iron (III) oxide (Fe2O3, MgFe2O4). Amorphous silica (not seen in XRD) and MgO have been observed by TEM (x 160000) and EDX analysis. For temperature between 1100 °C and 1400 °C, the amorphous silica reacts with olivine to form the enstatite phase (Eq. (3)).
(Mg,Fe)2SiO4 + O2 → xMg2SiO4 + (1-x)SiO2 + (2x-1)Fe2O3 (α) + 2(1-x)MgFe2O4 | (2) |
Mg2SiO4 + SiO2 → 2MgSiO3 | (3) |
MgSiO3 + Fe2O3 → MgFe2O4 + SiO2 | (4) |
In our case, between 400 °C and 1100 °C enstatite already present in olivine support may also react with the added iron oxide in order to form magnesioferrite spinel phase (MgFe2O4), which explains the decreases enstatite phase ray (MgSiO3) in the Fe/olivine catalysts (Eq. (4)). At 1400 °C iron oxide is reintegrated in olivine structure, which explains the decrease of the magnesioferrite and iron oxide phases [13].
3.1.2 Mössbauer spectroscopy
Mössbauer spectroscopy was performed on the 20% Fe/catalyst calcined at different temperatures in order to determine the iron oxidation state. The doublet present in the Mössbauer spectra with an isomer shift ISFe ≈ 1.15 mm/s and a quadrupole splitting QS ≈ 2.8 mm/s is attributed to Fe2+ of the olivine structure. The three others components are magnetic sextets. Two of them with hyperfine parameters (IS ≈ 0.26–0.36 mm/s, QS ≈ 0 mm/s and hyperfine field Heff ≈ 466–495 kG) can be attributed to Fe3+ located at the tetrahedral and octahedral sites of MgFe2O4 spinel structure, respectively. The parameters of the third sextet (IS ≈ 0.37 mm/s, QS ≈ 0 mm/s and Heff ≈ 516 kG) corresponds to the Fe3+ of α-Fe2O3. Fig. 2 resumes the 20% Fe/olivine catalysts iron phase distribution after various calcination temperatures. Between 400 and 1100 °C, the Fe (II) is extracted from the olivine structure and is oxidized to form “free” iron (III) oxides, which were also observed by the phase increase of iron oxide observed by XRD. Between 1100 to 1400 °C, a few parts of Fe (III) reintegrates the olivine structure as Fe (II) and therefore iron (III) is less present in free oxides.
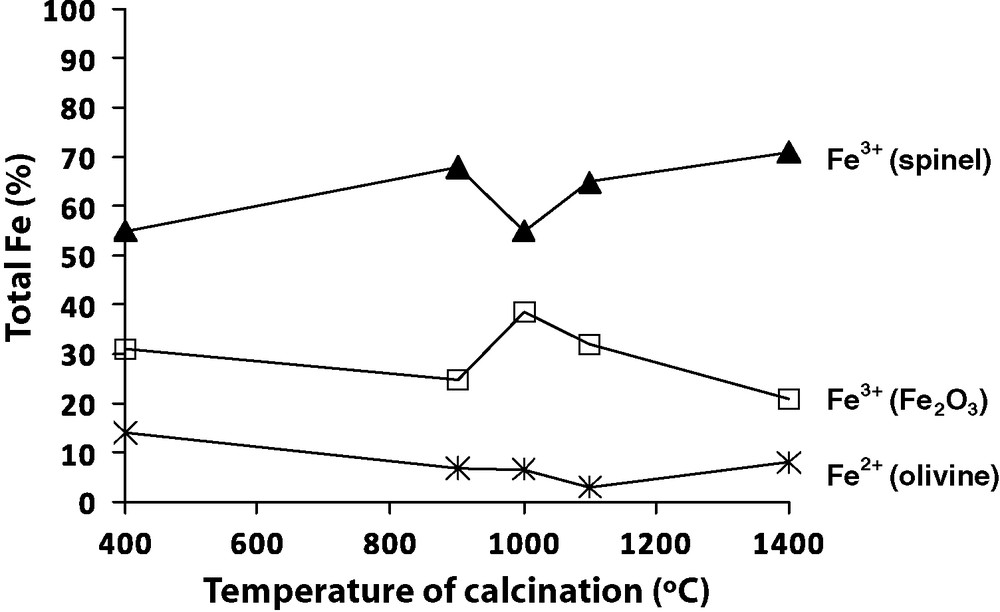
Iron distribution for 20% Fe/olivine catalyst calcined at 400 °C, 900 °C, 1000 °C, 1100 °C and 1400 °C.
3.1.3 Temperature programmed reduction
The 20% Fe/olivine reducibility has been studied in order to evaluate the metallic iron quantity accessible for the reactivity. The TPR curves showed two reduction zones. The first reduction zone, between 335 and 515 °C (mainly present for the catalyst calcined at 400 and 900 °C), is associated with the reduction of iron oxides present on olivine surface (α-Fe2O3 formed during the calcination). α–Fe2O3 is easily reduced into Fe0, which leads to sintering and possibility of carbon fouling on the surface, which deactivates the catalyst [24]. This is the reason why 20% Fe/olivine calcined at 400 °C and 900 °C were not selected for reactivity test. The second reduction zone is a broad peak between 605 and 790 °C. The iron oxides of olivine support are reduced at 660 °C. This range of reduction temperature can be associated to reduction of various iron phases present inside the olivine grain in precipitates form (as oxides Fe3O4) or iron in the spinel structure MgFe2O4.
To prevent free iron oxides at olivine surface, calcination needs to be performed at least 1000 °C. The percentage of metallic iron available after reduction (Table 1) has been calculated from the hydrogen consumption given by the TPR profiles and compared to the olivine support. After calcination at 1000 °C, almost the totality of the iron amount impregnated on the olivine is reduced and available for tar steam reforming. At 1100 °C, a lower amount of reducible iron is observed (16%). After calcination at 1400 °C, metallic iron available (21%) is not fully improved. The Fe/olivine calcined at 1000 °C seems to be the best compromise between the amount of metallic iron available after reduction and the lower energy required for the calcination.
Percentage of metallic iron available after reduction.
Calcination at 1000 °C | Calcination at 1100 °C | Calcination at 1400 °C | |
Olivine | 3 | 3 | 4 |
20% Fe/olivine | 19 | 16 | 21 |
3.2 Toluene steam reforming
The results were given in terms of toluene conversion, which was calculated as the fraction of the carbon contained in the gas products (CO, CO2, CH4) to the carbon contained in the toluene inlet feed (C2, C3 hydrocarbons have not been observed).
Hydrogen yield is expressed as the percentage of the stoichiometric potential corresponding to the total conversion of toluene into H2 according to the reaction (1):
3.2.1 Effect of reaction temperature
Steam reforming of toluene was performed in a temperature range of 750–850 °C according to Eq. (1), toluene and water was introduced in the flow in stoichiometric conditions. Neither olivine nor 20% Fe/olivine catalyst have showed a significant activity in toluene steam reforming (less than 20% of toluene conversion). Even with an iron added of 20%, the iron olivine catalyst was not able to enhance the activity of the olivine support.
Therefore to increase the iron efficiency, hydrogen, which is produced during gasification was introduced in the flow for the toluene steam reforming with a hydrogen to water ratio of 1:1. Toluene conversion with 20% Fe/olivine and olivine (both calcined at 1000 °C) is shown Fig. 3. At 750 °C, the iron catalysts showed a moderate activity in toluene conversion (10 and 23% for olivine support and 20% Fe/olivine catalyst, respectively). The hydrogen yield is almost the same (20 and 25% of hydrogen yield for olivine and 20% Fe/olivine, respectively). At 850 °C, about 85% of toluene has been converted by the iron catalyst, close to the thermodynamic value, whereas olivine support converted about 28% of toluene which is comparable to the 20% Fe/olivine activity at 750 °C.
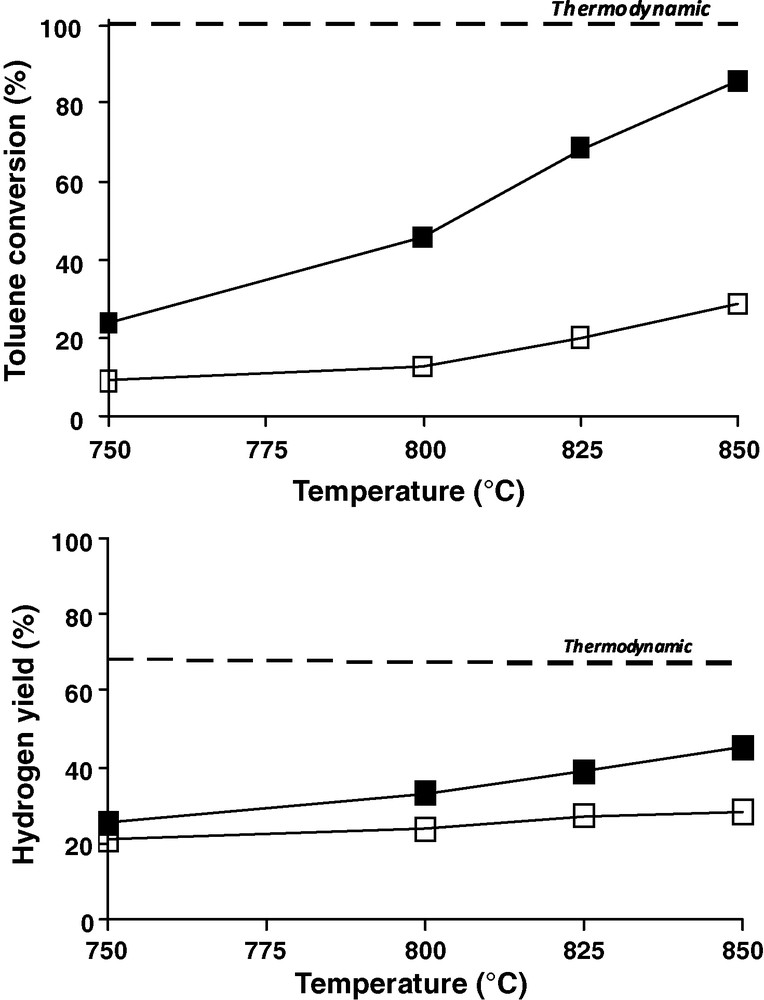
Comparison of (■) 20% Fe/olivine, (□) olivine and (- - -) thermodynamic equilibrium in toluene conversion (left) and hydrogen yield (right) in presence of H2:H2O = 1:1.
An improvement in hydrogen yield is observed for the iron catalyst compared to olivine support (yield of 45% for the 20% Fe/olivine catalyst versus 28% for olivine) is obtained. Nevertheless the 20% Fe/olivine catalyst hydrogen yield is away from of the thermodynamic value (about 66%).
As the real gasifier temperature is kept around 800–850 °C, the upcoming tests were performed at 825 °C.
3.2.2 Hydrogen effect at 825 °C
The previous results have showed that hydrogen is necessary during reactivity test for toluene conversion, therefore a hydrogen to water ratio variation have been studied in order to find the optimized conditions of toluene steam reforming. Water and toluene concentration were kept constant in the total flow at 12% vol and 0.8% vol, respectively. Hydrogen varies from 14% vol (hydrogen to water ratio of 1:1) to 21% vol (hydrogen to water ratio of 1.5:1). Fig. 4 shows that the added hydrogen in the flow enhances the toluene conversion (from an average of 60% of toluene conversion for H2 to H2O ratio of 1:1 to 95% of toluene conversion for H2 to H2O ratio of 1.5:1) and improves clearly the catalyst stability. This tendency was also observed for the hydrogen yield. With a 1:1 ratio, the hydrogen yield is 40% and with a 1.5:1 ratio, the hydrogen yield is stable (about 60%), close to the thermodynamic value (66%).
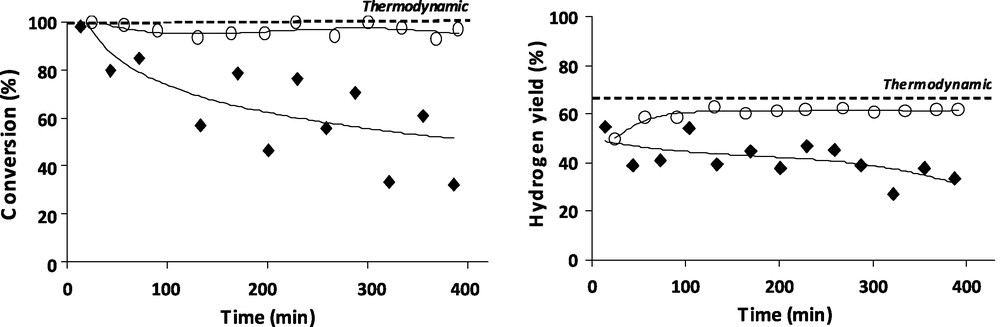
Influence of hydrogen/water ratio (○ratio = 1.5:1; ♦ratio = 1:1) on toluene conversion (left) and hydrogen yield (right) at 825 °C.
With a hydrogen to water ratio of 1.5:1, toluene conversion is almost twice more important and stable which indicates that the hydrogen addition counterbalances the pronounced oxidative character due to the presence of water. Thus, the catalyst in reduced form showed high activity toward toluene reforming. Tamhankar et al. [25] has also found that the presence of hydrogen plays a critical role in the overall reaction of benzene removal and in suppressing catalyst deactivation. The characterization performed after tests did not show high amount of carbon deposit which implies that the differences of activity are not due to a carbon deactivation although the state of iron oxidation. In presence of water iron is present as iron oxide and is not active in toluene reforming whereas with a high hydrogen to water ratio iron is kept on its metallic form, which can be the reforming active metal.
Therefore, the optimized condition at 825 °C is a hydrogen to water ratio of 1.5:1. The catalyst has been tested during 30 h in these conditions and shows similar efficiency (95% of toluene conversion) and hydrogen yield (about 60%) which tend toward thermodynamic values. The toluene concentration passes from 30 to about 1,5 g/Nm, which is still a high value for a SOFC [26]. Nevertheless, this value is sufficiently low to add inside the reactor a ceramic candle filter [27].
3.2.3 Comparison with an effective catalyst
Ni/olivine designed by Courson et al. [22] presented good performances in methane steam reforming [28,29] and also for toluene steam reforming in laboratory [23] and pilot scale [30]. The challenge for the 20% Fe/olivine catalyst is to realize a similar activity to the 3.9% Ni/olivine. Afterward these two catalysts have been tested in the optimized conditions (0.8% vol of toluene, hydrogen to water ratio of 1.5:1 at 825 °C) (Fig. 5). The 20% Fe/olivine (dashed line) presents similar activity and stability than the 3.9% Ni/olivine catalyst (solid line) with a toluene conversion around 90% and a hydrogen yield about 60%.
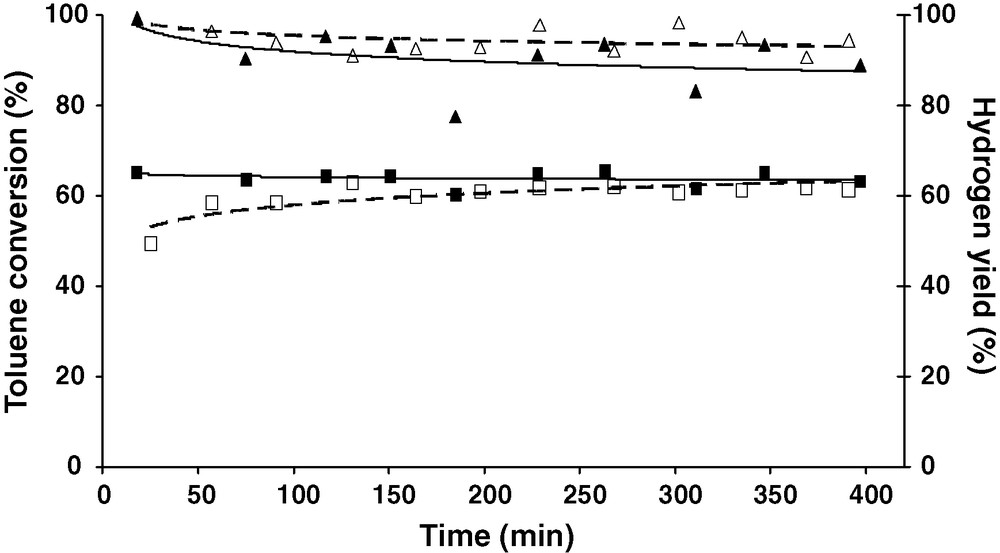
Toluene conversion for (▵) 20% Fe/olivine compared to (▴) 3.9% Ni/olivine and hydrogen yield for the (□) 20% Fe/olivine compared to (■) 3.9% Ni/olivine.
Hence, the iron olivine catalyst is equivalent to Ni/olivine catalyst and can be used in biomass gasification without environmental nuisance due to nickel catalysts toxicity especially in fluidized bed.
3.3 Characterization after test
The elemental analysis performed by ICP-MS on 20% Fe/olivine after 7 and 30 h of test indicates a small carbon content (< 0.30 wt%), which implies that the operating conditions permit to avoid carbon deposition on the actives sites catalyst.
The XRD patterns (Fig. 6) compare the catalysts before and after the reactivity tests with various hydrogen to water ratios. The rays of the oxide phase α-Fe2O3 and the spinel phase initially present in the before test catalyst (Fig. 6a), decreased significantly after reactivity with a hydrogen to water ratio of 1:1 (Fig. 6b). It can be observed a ray of FeO oxide (2θ = 42.19°) and small ray of metallic iron Fe0 (2θ = 44.66°). After reactivity with a hydrogen to water ratio of 1.5:1, the FeO peak disappears while an intense metallic iron phase ray is mainly observed (Fig. 6c). The iron particle size is around 43 nm for 20% Fe/olivine tested during 7 h as well as after 30 h. This indicates that the high calcination temperature is able to maintain the iron particles and to guarantee the absence of agglomeration of actives sites during toluene steam reforming.
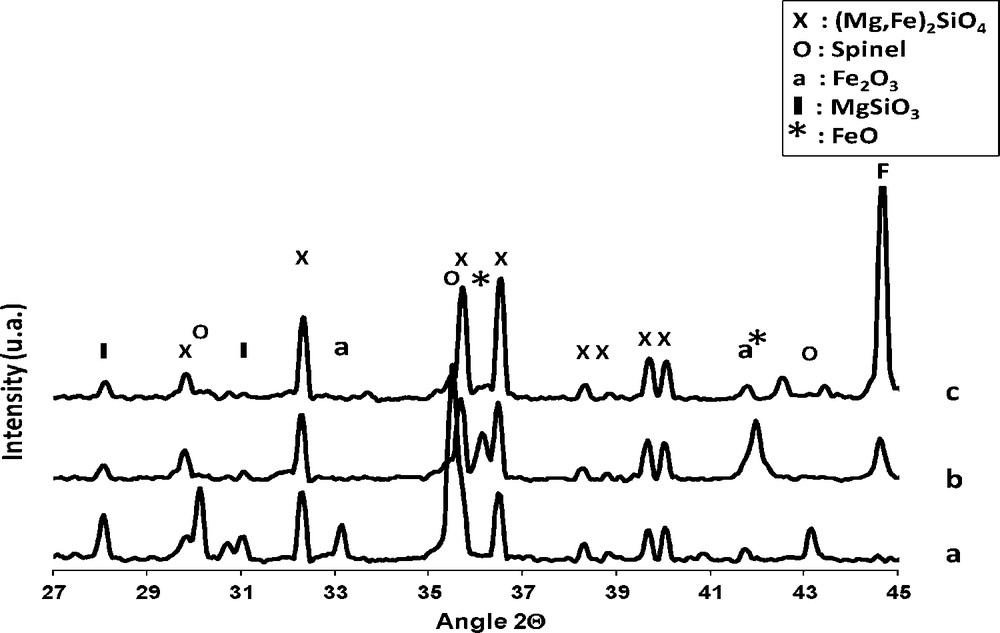
Comparison of the 20% Fe/olivine XRD patterns: (a) before test, (b) after test with hydrogen/water ratio of 1:1, (c) after test with hydrogen/water ratio of 1.5:1.
The presence of an intense peak of metallic iron Fe0 (XRD) can explain the high value of toluene conversion and the absence of sintering can explain the stability of toluene conversion.
The 20% Fe/olivine catalysts iron distribution in different phases (Table 2) obtained by Mössbauer spectroscopy confirmed the XRD observations after optimized test: a decrease in the hematite and MgFe2O4 spinel phases instead of a high metallic iron percentage. However Table 2 gives two complementary information. A magnetite phase (Fe3O4) not clearly seen by XRD (Fig. 6c) is present in the catalysts after test. Further a considerable amount of Fe2+, higher than for the catalysts before reactivity, is observed. The Fe (II) is reintegrated inside the olivine structure. This may be an explanation of the olivine peak shift from 2θ = 35.50° to 2θ = 35.69°.
Iron distribution obtained by Mössbauer spectroscopy in the 20% Fe/olivine catalyst before and after 400 min of toluene steam reforming with hydrogen to water ratio of 1.5:1.
Catalyst | Iron species | (%) |
20% Fe/olivine calcined at 1000 °C | Fe2+ (olivine) | 6 |
Fe3+ (MgFe2O4) | 55 | |
Fe3+ (α-Fe2O3) | 39 | |
20% Fe/olivine after test | Fe2+ (olivine) | 14 |
Fe3+ (MgFe2O4) | 5 | |
Fe3+ (α-Fe2O3) | 1 | |
Fe2+/Fe3+ (Fe3O4) | 20 | |
Fe0 | 59 |
Moreover TPR shows that the 20% Fe/olivine catalyst after the optimized test presented a low reducibility (around 3%) compared to the fresh one (19% in Table 1). This data confirms the XRD and Mössbauer data, which indicated the presence of a reduced iron form after test. A small reduction peak around 405 °C reveals the presence of a small iron oxide amount (α-Fe2O3, spinel MgFe2O4 or Fe3O4), which can be attributed to Fe3+ → Fe2+ reduction. Another small reduction peak around 920 °C might be associated to Fe2+ → Fe0 reduction. It may be more probably due to the magnetite phase reduction because of the difficulty to reduce iron present inside the olivine structure. Then iron is mainly present in metallic forms after test.
4 Discussion and conclusion
Olivine structure (silicate of magnesium and iron) is a very flexible structure. Even with a very low specific surface area (< 1 m2/gcat) it was demonstrated that it can be a host for transition metal (Ni or Fe). It was able to impregnate at least up to 4% of nickel or 20% of iron in order to enhance the olivine activity. The characterization techniques performed permit to conclude that the calcination temperature of iron olivine catalyst has a real influence on the iron distribution and on the phases present in olivine. The XRD indicated the olivine structure was not deeply modified even after calcination at 1400 °C. However minor modifications that occur during calcination will have important influences for the reactivity.
The XRD and Mössbauer spectra indicated that the main iron phases present after various temperature of calcination were hematite (α-Fe2O3) and spinel (MgFe2O4). Thus at calcination temperature lesser than 1100 °C, MgO, SiO2 and iron oxides (iron (II) oxidized into iron (III) which has been characterized as α-Fe2O3 or spinel MgFe2O4) live the structure. Addition of a high amount of iron (III) does not deeply modify this process but participates and amplifies some of the modifications. After 1400 °C, the Fe2+ can reintegrate the olivine structure, and SiO2 reacts with MgSiO4 to form an enstatite phase.
The TPR result demonstrated the ability of reduce the iron impregnated. At calcination temperature limited at 900 °C, TPR shows clearly two iron reduction zones. Beyond 515 °C, not well integrated, iron is reduced. The well-integrated iron as α-Fe2O3 (present as precipitates) or MgFe2O4 dispersed inside the olivine grain is reduced only between 600 and 900 °C. To avoid any problems of deactivation due to iron easily reduced, it will be better to perform the reactivity test after calcination as high as 1000 °C. However, TPR data shows that the calcination at higher temperature has no real influence on the samples reducibility. This is in relation to the thermodynamic stability of olivine. So after calcination at 1000 °C, then reduction, the 20% Fe/olivine catalyst possesses sufficient amount of metallic iron available for the reactivity without iron reducible at low temperature.
In reactivity conditions, steam reforming of toluene required a large amount of water according to the stoichiometric conditions (14 mol H2O:1 mol C7H8). Reactivity tests show clearly the inactivity of the catalyst in such conditions. However, it has been demonstrated that the presence of hydrogen could counterbalance the negative effect of water and enhance the iron olivine catalyst activity. Tests have been performed in most close to gasifier conditions in presence of hydrogen. At 825 °C, with a ratio H2:H2O = 1.5:1, toluene conversion (95%) and hydrogen yield (60%) tend to thermodynamic values. Metallic iron is well known in CC and CH bond breakdown and justifies the high toluene conversion [25,14]. Moreover, 20%Fe/olivine catalyst is very stable (30 h) with few carbon formation.
However with a ratio H2:H2O = 1:1, the catalyst is less active, less stable but few carbon is formed too. This indicates that catalyst deactivation is not related to the amount of deposited carbon. XRD and Mössbauer data shows presence of Fe2+/Fe3+ during reactivity. With a ratio H2:H2O = 1.5/1, hydrogen concentration prevents such oxidation by maintaining the iron on its metallic form and water concentration is sufficient to oxidize the surface carbon. We could also indicate that the presence of metallic iron is important to improve the WGSR with hydrogen and CO2 formation.
So, we could propose that metallic iron is the active state for the toluene conversion and that water is important to oxidize carbon.
More, a significant amount of iron (II) reintegrates the olivine structure during the reactivity. We can conclude that an exchange Fe2+/Fe3+ occurs when the mixture is enough reductive or oxidant, and olivine is a valuable support of iron storage. The XRD confirmed the same particles size after 7 h and 30 h of reactivity. The 20% of iron impregnated catalyst calcined at 1000 °C present a good interaction with olivine which leads to such efficiency in toluene stream reforming.
Compared to Ni/olivine which already improved highly the toluene steam reforming and showed good activities during gasification in pilot plant, Fe/olivine seems to be able to substitute it in more safety conditions for environment even if the used amount of iron is quite to much important compared to the nickel amount.
Acknowledgements
This work was carried out under EC Project (Contract UNIQUE N° 211517–ENERGY FP7–2008/2011). We thank the European Commission for its financial support.