1 Introduction
Over the last few decades, environmental awareness found its way into chemical process engineering and much effort has been devoted to make the production of chemical commodities greener [1]. To achieve green(er) organic syntheses, it is necessary, among other requirements, to employ nontoxic starting compounds and to obtain high conversion rates while avoiding the formation waste and by-products [1]. In a landmark paper of 1999, James Clark selected Friedel-Crafts reactions as a textbook example of a process, which is (or was) both very important from an industrial point of view and extremely “ungreen” [2]. Indeed, in its initial form, the reaction was conducted by adding an, at least, equimolar amount of aluminium chloride to a solution of an alkyl chloride in a large excess of the desired aromatic compound at room temperature [3]. This resulted in the formation of more than 80 mass-% of waste products [2]. Therefore numerous ways have been investigated to reduce the amount of waste produced in this type of alkylation reactions.
Among these attempts, one can cite the use of various (true) homogeneous (based either on transition metals [3–7], on Lewis acids [8–10] or on Brönsted acids [11]) and heterogeneous catalysts (be they acidic resins [12] or molecular sieves [13]).
Some of the above mentioned works and numerous others also aim at using alcohols as alkylation agents. Indeed, alcohols are easier to synthesise than chlorides and when they are employed as alkylation agents, only water is eliminated. [14–19].
In an effort to both avoid the use of any catalyst and favour the use of alcohols as alkylation agents; Sato et al. investigated the use supercritical water as solvent for the alkylation of phenol [20–23]. Unfortunately, processes involving supercritical water impose strong requirements on the used reactors in terms of mechanical and corrosion resistance. However, water at temperatures below the critical point can also be employed, but at the expense of the yield of the reaction [24].
As the concentration, respectively the activity, of hydronium ions seems to be the main factor impacting the curse of Friedel-Crafts’ reactions in water [22], we anticipated that the use of diluted acids under hydrothermal conditions (between 150 °C and 180 °C) could allow one to overcome the technical problems caused by the use of concentrated acids on the one side and supercritical water on the other. We show here that it is possible to perform the alkylation of phenol (Scheme 1) successfully with activated alcohols under hydrothermal conditions in diluted acids at 180 °C.
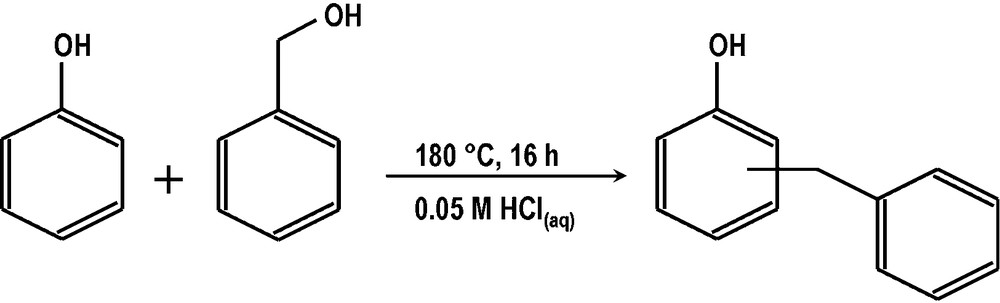
A typical example of diluted acid promoted alkylation of phenol with benzyl alcohol.
2 Experimental
2.1 Experimentation
All experiments were run in stainless steel autoclaves fitted with 21 mL PTFE inlets. The inlets were cleaned with water at 180 °C for 16 h before usage.
In standard tests, 0.5 mmoL of alcohol and 15 mmoL of phenolic derivatives were mixed with 10 mL of solvent (pure water or the acidic solutions) and heated up to the wanted temperature for 16 h. The concentration and nature of the acids, the reaction temperature and the nature of the reagents were varied to gain insights into the versatility of this reaction.
2.2 Characterisation
After the reaction, the autoclaves were cooled down to room temperature; the products of the reaction were extracted with 3 mL of EtOAc. The organic phase was prepared for GC-FID and GC-MS by addition of a standard solution of toluene in EtOAc. The results of the GC-FID were quantified using the procedure described by Jorgensen et al. [25].
3 Results and discussion
3.1 Optimization of the reaction conditions for the system phenol–benzyl alcohol
In a first step we selected HCl as a reference (inorganic) acid to promote the alkylation of phenol with benzyl alcohol, which is known to be very electrophilic. The impact of the reaction temperature on the formed products for three HCl concentrations (0, 0.5 M and 1 M, respectively) was investigated. Table 1 summarizes the obtained results.
Alkylation of phenol with benzyl alcohol in aqueous mediaa.
Solvent | Temperature (°C) | Conversion (%)b | Yield of mono-substituted Friedel-Crafts product (%)c | o/p-ratio |
Water | 125 | 0 | 0 | – |
150 | 0 | 0 | – | |
180 | 1 | 1 | – | |
200 | 7 | 7 | 61:39 | |
220 | 14 | 14 | 59:41 | |
0.5 M HCl | 125 | 100 | 89 | 50:50 |
150 | 99 | 72 | 52:48 | |
180 | 100 | 66 | 53:47 | |
200 | 100 | 67 | 53:47 | |
220 | 100 | 63 | 53: 47 | |
1 M HCl | 125 | 84 | 71 | 48:52 |
150 | 100 | 75 | 50:50 | |
180 | 100 | 69 | 51:49 | |
200 | 94 | 65 | 51:49 | |
220 | 100 | 62 | 52:48 |
a Reaction conditions: 0.5 mmoL of benzyl alcohol, 15 mmoL of phenol, 10 mL of solvent heated up to the wanted temperature for 16 h.
b Conversion rates were determined as the ratio between the initial and final amount of benzyl alcohol.
c Yields were determined as the ratio between the amount of mono alkylation products and the initial amount of benzyl alcohol.
As can be seen, the use of pure water is not sufficient (at such moderate temperatures) to yield high amounts of the expected alkylation products, which is compatible with the results reported by Katritzky et al. [24]. In presence of HCl however, high conversion rates are observed at any temperatures and the yields of mono alkylated products range from about 60 up to 90%. By-products of the reaction are mainly diakylation products.
Actually, our initial aim was to use the lowest possible concentration of acid in order to ease corrosion constrains on possible reactors for such alkylations. We, thus, decided to perform our following test at 180 °C and to try decreasing the concentration of acid or to employ weaker acids. Figs. 1–3 report the results we obtained for the alkylation of phenol with benzyl alcohol at 180 °C for 16 h for increasing acid concentrations with HCl, acetic acid and formic acid.

Alkylation of phenol with benzyl alcohol in HCl. Percentages of non-converted starting material and formed mono alkylation product (both: on the left axis) as well as the ortho/para-ratio (right axis) as a function of the concentration of HCl after reaction at 180 °C for 16 h.
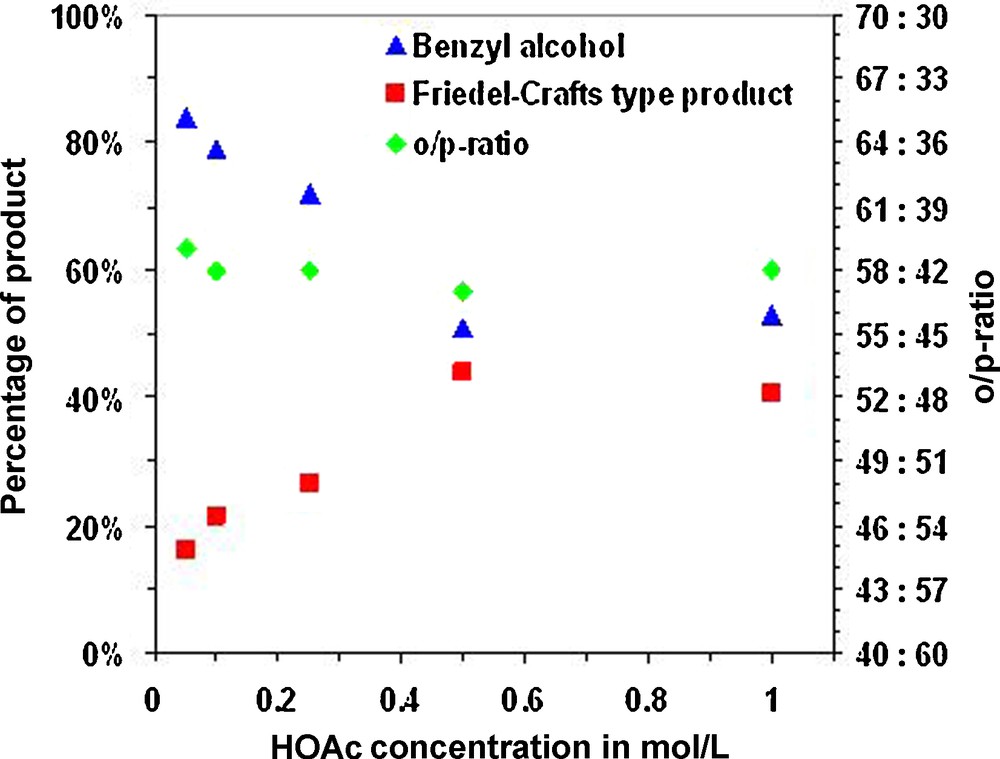
Alkylation of phenol with benzyl alcohol in CH3COOH. Percentages of non-converted starting material and mono alkylation product (both: on the left axis) as well as the ortho/para-ratio (right axis) as a function of the concentration of HCl after reaction at 180 °C for 16 h.
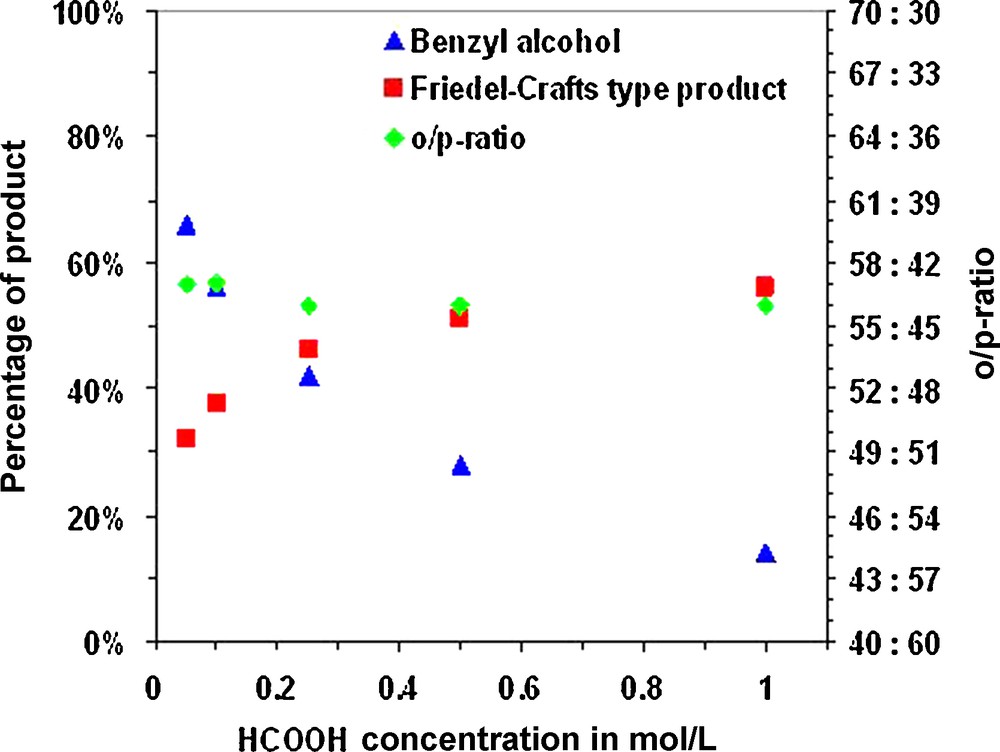
Alkylation of phenol with benzyl alcohol in HCOOH. Percentages of non-converted starting material and formed mono alkylation product (both: on the left axis) as well as the ortho/para-ratio (right axis) as a function of the concentration of HCl after reaction at 180 °C for 16 h.
As can be seen on Fig. 1, with HCl being the acid, it was already possible to achieve high yields of the expected alkylation products at very low acid concentrations (60% at 0.03 M HCl, for example, which corresponds more or less to the pH of gastric acid), while the ortho to para-ratio was not significantly impacted by acid concentration. Interestingly, a complete conversion of benzyl alcohol is obtained with 0.05 molar HCl, i.e. when the benzyl alcohol and proton are in equimolar amounts at room temperatures. As previously mentioned by-products of these reactions are mainly diakylation products.
Unfortunately weaker, organic, acids proved to be insufficient to promote the alkylation of phenol to the same extent, even at higher concentration. This is probably a consequence of their weaker acidic character, but also of competing esterification and decarboxylation reactions.
We, thus, decided to employ 0.05 M hydrochloric acid as the medium of choice for our next set of experiments. It is worth noticing that under these reaction conditions, the HCl to alcohol ratio is 1, which means that HCl cannot be considered as a catalyst but as a promoter.
3.2 Phenol with different alcohols
In the next step, we investigated the versatility of our approach by varying the nature of our electrophiles. The obtained results are summarized up in Table 2.
Friedel-Crafts type alkylation of phenol with different alcoholsa.
Entry | Agent | Yield (%)b | ortho/para-ratioc |
1 | Benzyl alcohol | 78 | 56: 44 |
2 | sec-phenethyl alcohol | 93 | 34: 66 |
3 | 4-hydroxybenzyl alcohol | 68 | 18: 82 |
4 | Cinnamyl alcohol | 47 | − |
5 | Cyclohexanol | 3 | 59: 41 |
6 | n-hexanol | 0 | − |
7 | 2-propanol | 3 | 64: 36 |
a Reaction conditions 0.5 mmoL of alcohol, 15 mmoL of phenol, 10 mL of solvent heated at 180 °C for 16 h.
b The yield of the reaction was determined as the percentage of formed mono addition product with respect to the initial amount of alcohol, as determined by CG-FID with toluene used as an internal standard.
c The ortho/para-ratio what determined by GC-FID
As could be expected [26], only strongly activated alcohols yielded substantial amounts of the awaited alkylation product (up to 93% for phenylethanol, Table 2, entry 2). Interestingly, cinnamyl alcohol formed the expected Friedel-Crafts type product (molecule A in Scheme 2) in a first step, but underwent a ring-closure yielding flavan in a second time (molecule B in Scheme 2). Crude NMR data of the reaction product indicates that 35% of flavan derivatives and 13% of the awaited Friedel-Crafts products were formed. This observation opens up new opportunities for the production of biologically relevant flavonoids.
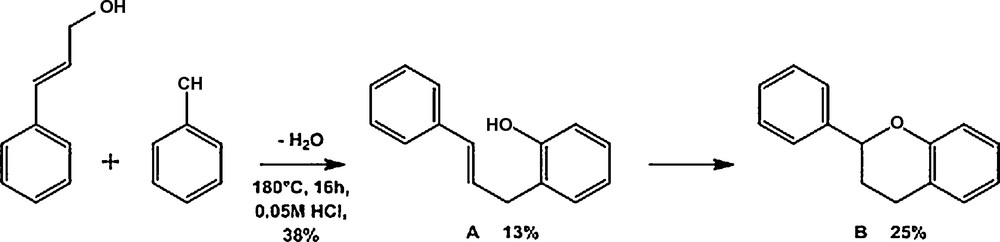
Reaction scheme with ring-closure for cinnamyl alcohol with phenol.
Cyclohexanol and isopropanol (Table 2, entries 5 and 7, respectively), which are typical activated aliphatic alcohols, only gave very limited amounts of alkylation product (3% in both cases).
3.3 Phenolderivatives with benzyl alcohol
In a further step we studied the reactions of other phenolic derivatives with benzyl alcohol. The obtained results are displayed in Table 3.
Alkylation of hydroxyl aromatic derivatives with benzyl alcohola.
Entry | Aromatic compound | Yield (%)b | Selectivity (%)c |
1 | Catechol | 66 | 3-benzyl catechol (44) 4-benzyl catechol (56) |
2 | p-cresol | 89 | 2-benzyl-4-methyl phenol (82) 3-benzyl-4-methyl phenol (18) |
3 | 4-hydroxybenzoic acid | < 1 | – |
4 | 4-hydroxyphenyl acetic acid | 41 | 4-hydroxy-3-benzylphenyl acetic acid(> 98) |
a Reaction conditions 0.5 mmoL of benzyl alcohol, 15 mmoL of phenolic compounds, 10 mL of solvent heated at 180 °C for 16 h.
b The yield of the reaction was determined as the percentage of formed mono addition product with respect to the initial amount of benzyl alcohol, as determined by CG-FID with toluene used as an internal standard.
c The selectivity was determined by GC-FID as the percentage of the mentioned isomers among the formed mono addition products.
Catechol (Table 3, entry 1) yielded a moderate (66%) amount of alkylation product. Due to its symmetry, catechol could not yield real ortho and para products. We thus obtained a mixture of 3 and 4-benzyl catechol (products C and D on Scheme 3, respectively). A slight excess of 4-benzylcatechol is detected. P-cresol (Table 3, entry 2) yielded a high amount of mono alkylation product (89%). A high excess of 2-benzyl-4-methyl phenol is observed (with a 73% overall yield in this compound).
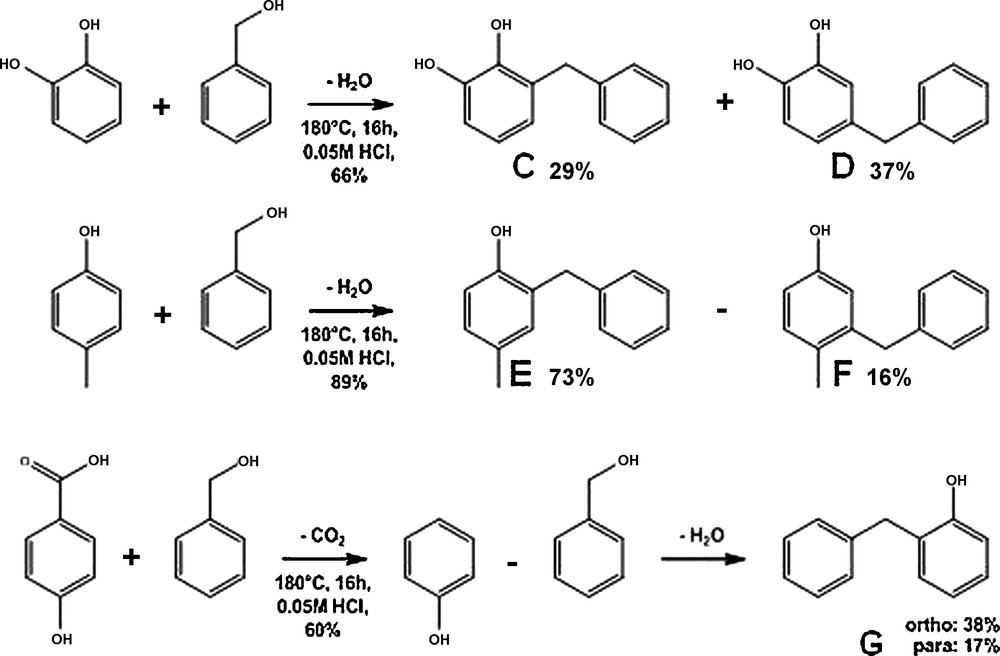
Alkylation of catechol, p-cresol and 4-hydroxy-benzoic acid with benzyl alcohol.
4-Hydroxybenzoic acid (Table 3, entry 3) appeared to be a very week electrodonor for the Friedel-Crafts reaction, probably because of the electron attracting properties of the carboxylic group. Thus, the molecule could not react until it lost this carboxylic group (via an already observed decarboxylation reaction [27]) to yield phenol in a first step, and the usual benzylphenol isomers in a second step (Scheme 3, molecule G).
4-Hydroxybenzoic acetic acid (Table 3, entry 4), on the contrary, proved more reactive, yielding 41% of monoalkylation product. Interestingly the alkylation was very selective towards the addition in the ortho position (with respect to the OH group).
4 Conclusion
Obviously, numerous other methods exist to perform this Friedel-Crafts’ type alkylation of aromatic compounds and only tests at larger scale and detailed life-cycle assessments may allow to determinate whether hydrothermal synthesis competes with these other approaches. Anyhow, hydrothermal synthesis definitely is an elegant way to perform Friedel-Crafts’ type alkylations as it employs very cheap starting materials, works under relatively mild conditions and does not impose too strong requirements and the materials to be used (in this study Teflon inlets were employed, but, for example, Hastelloy® reactors work as well). In addition, this study is of academic importance helping to understand the chemical process involved in the, nowadays, very popular hydrothermal carbonisation (HTC) of biomass [28–32]. Lignin, one of the main constituents of biomass, is constituted of polymerised, weakly cross-linked, hydroxyaromatic species and features a high density of benzyl alcohol moieties (Fig. 4). It is relatively straightforward to assume that intra- and intermolecular Friedel-Crafts’ type alkylations are part of the processes accounting for the stiffening and cross-linking observed when lignin is submitted to hydrothermal treatments. Our observations can thus contribute to a better understanding of HTC and open new possibilities for the valorisation of lignins.

Alder's structure of softwood lignin (adapted from ref. [33]).
Acknowledgements
The authors acknowledge the financial support of the CEA (Commissariat à l’énergie atomique et aux énergies alternatives, France) and the region of Languedoc-Roussillon (France).