1 Introduction
Crosslinking of saturated elastomers is a complex process. These polymers do not possess double bonds in the macromolecule. Therefore, they can be vulcanised with organic peroxides. The disadvantages of elastomer peroxide vulcanisation are, first of all, long vulcanisation time and weak mechanical strength of vulcanisates. These disadvantages are very difficult to overcome and reduce the industrial application of saturated elastomers [1]. To improve the physical properties and processing of peroxide crosslinked elastomers, coagents are applied. Coagents are multifunctional vinyl monomers, highly reactive towards free radicals formed during peroxide vulcanisation. Due to the presence of double bonds in their molecules, coagents are able to undergo addition and polymerisation reactions. However, functional groups of coagents are used to form ionic or complex crosslinks in the elastomer network. In this way, coagents are incorporated in the elastomer [2].
Coagent application allows one to obtain the material with higher tensile and tear strength, higher modulus and hardness, and better abrasion resistance and adhesion to metal [3]. Moreover, coagents like acrylates, methacrylates and maleimides increase the vulcanisation rate of rubber compounds and may lead to scorching [4,5]. These coagents possess easily accessible double bonds without allyl hydrogen. Therefore, the crosslinking reaction follows an addition mechanism and the distraction of the hydrogen atom from polymer chain is not observed [6]. Some coagents (diallyl phthalate, triallyl cyanurate and isocyanurate) increase the efficiency of crosslinking without scorching or increasing the vulcanisation rate. Due to the presence of easily abstractable hydrogen atoms and easily accessible unsaturated bonds, these coagents undergo addition reactions and are attached to the polymer macromolecules [6]. Coagents react readily with peroxide radicals as well as polymer radicals. According to Class [3] and Murgic et al. [7], during the crosslinking process, a coagent reacts directly with polymer radicals and is grafted to the polymer chain forming a more stable radical, which reacts with next polymer radical and forms a network crosslink. Another mechanism of peroxide crosslinking assumes that radicals from peroxide decomposition cause the homopolymerisation of coagent. Despite the fact that polymerised coagent molecules are not grafted to the elastomer chain, they improve the vulcanisate's mechanical properties, as they act as a reinforcing filler formed in situ during vulcanisation [4]. Moreover, polymerised coagent domains can act as centres of stress redistribution in vulcanisates upon external strain.
Most coagents are relatively polar compounds, difficult to mix with non-polar polymers [6]. Despite a homogeneous dispersion in a polymer matrix, coagent molecules can agglomerate again, form domains and then homopolymerise [8]. The polymerised coagent domains are probably covalently bonded with surrounding polymer matrix [9]. In this case, the equilibrium between coagent homopolymerisation and its grafting to the polymer chain depends on the coagent concentration, the difference between the coagent and polymer polarity and the degree of their mixing [7].
Commonly known is the application of diacrylate derivatives as coagents of elastomer peroxide crosslinking [10]. Coagents like zinc diacrylate are used to form ionic crosslinks in the elastomer network, which lead to improvements in the mechanical properties of rubber products (tear strength, elongation) and increase the adhesion between metal and elastomer. These coagents increase the crosslinks density of vulcanisates [11]. Costin et al. [12–14] confirmed that metal acrylates as multifunctional salts can support peroxide crosslinking of elastomers. Nomura et al. [15] proved that zinc dimethacrylate (ZDMA) created the structure in the hydrogenated acrylonitrile-butadiene elastomer (HNBR), composed with aggregates of in situ polymerised ZDMA during elastomer vulcanisation. The structure was deformed upon external stresses, improving the mechanical strength of material. Lu et al. confirmed that interactions between a polar elastomer and zinc dimethacrylate as well as the stretching induced crystallisation during deformation of the material were also responsible for the improvement of the composite's mechanical properties. This was confirmed by the character of the stress/strain curve in tensile tests. The stress was low during the initial stage of deformation and then increased rapidly in the narrow deformation range just before sample destruction [16]. However, radical ZDMA polymerisation during the crosslinking process and formation of ionic clusters with the contribution of zinc ions from coagent molecules was also important. Lu et al. proposed a model of elastomer/ZDMA interactions [11]. According to this model, nanoparticles of poly(zinc dimethacrylate) can be physically adsorbed on elastomer chains, attach to them and form crosslinks or create ionic clusters due to electrostatic interactions. Moreover, some covalent crosslinks were formed in the elastomer network as a result of peroxide crosslinking. Elastomer composites with this kind of morphology reveal the ability for stress relaxation, due to elastomer chain slippage on the ionic cluster surface and reformation of ionic bonds upon external deformation of the sample. The high elongation at break is also observed [17].
In this work, we applied nanosized calcium and magnesium oxide and layered minerals (boehmite, hydrotalcite) in combination with unsaturated itaconic acid as coagents for crosslinking of HNBR. Itaconic acid containing easily abstractable hydrogen atoms and a readily accessible double bond was grafted onto the powder surface during the modification process. It is believed that these coagents, due to their multifunctionality, are able to react with the elastomer directly and form effective covalent bonds. Moreover, they can form ionic crosslinks, that lead to the increase of vulcanisates crosslinks density and an improvement in tensile strength [16,18]. We studied the influence of the obtained coagents on the rubber compounds’ vulcanisation kinetics, crosslinking efficiency, vulcanisates’ crosslinks density and tensile strength. The application of such coagents in vulcanisation of saturated elastomers has not yet been reported.
2 Methods
2.1 Materials
HNBR (Therban 3407) containing 34 wt % acrylonitrile and 0.9 wt % of residual double bonds after hydrogenation was obtained from Bayer C.O. The Mooney viscosity was (ML1+4 [100 °C]:70). It was vulcanised with dicumyl peroxide (DCP) (Aldrich). Nanosized calcium oxide (CaO) (Aldrich), and magnesium oxide (MgO) (Aldrich) as well as layered minerals: boehmite (BM) (Disperal, SASOL) and hydrotalcite (HTA) (Aldrich) together with itaconic acid (IA) (Fluka) were applied as coagents. The chemical composition of boehmite (AlO(OH)) was: 77% of Al2O3 and 0.002% of Na2O, whereas the synthetic hydrotalcite had the linear formula Mg6Al2(CO3)(OH)16 · 4H2O. The structural formula of itaconic acid was given in Scheme 1.
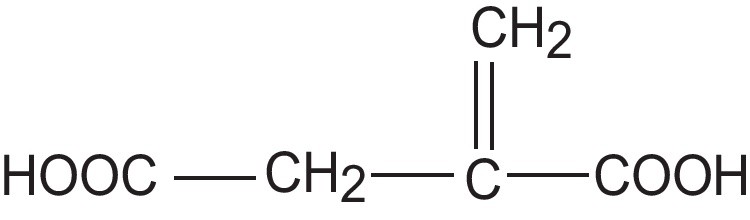
Structural formula of itaconic acid.
2.2 Preparation of coagents
Nanosized metal oxides and layered minerals were mixed with a solution of modifying agent (itaconic acid) in acetone for 30 min during ultrasonic treatment (BANDELIN DT 255) with a frequency of 35 kHz. The mixture was left for 24 h. Then the solvent (acetone) was evaporated using a vacuum evaporator at 50 °C. The coagents obtained were dried in a vacuum drier at 60 °C for 96 h. The quantity of itaconic acid was 8 g/100 g of metal oxide or layered mineral. The efficiency of preparation process was evaluated based on results of elementary and thermogravimetric analysis and zeta potential measurements.
2.3 Thermogravimetric analysis of coagents
The thermal decomposition of coagents was performed using TGA/DSC1 (Mettler Toledo) analyzer. Samples were heating from 25 °C to 700 °C in argon atmosphere with the heating rate 10 °C/min.
2.4 Coagent aggregate size
The size of the coagent aggregates was determined using a Zetasizer Nano Series S90 (Malvern Instruments) apparatus. The size of the coagent particles in a water dispersion was measured based on the DLS (Dynamic Light Scattering) method. The concentration of the dispersion was 0.1 g/L. To estimate the tendency of the coagents to agglomerate in the elastomer, the size of their agglomerates in paraffin oil (model of elastomer matrix) was determined. Before measurement, the dispersions were stabilized upon ultrasonic treatment (BANDELIN DT 255) for 30 min to reduce the size of agglomerates.
2.5 Preparation and characterization of rubber compounds
Rubber compounds, with the formulation given in Table 1, were prepared using a laboratory two-roll mill in the temperature about 40 °C. The samples were cured at 160 °C until they developed a 90% increase in torque, measured by an oscillating disc rheometer according to ASTMD 2084-81. The criterion for the scorch time determination was the 20% of torque increase over the minimum torque value.
Composition of the hydrogenated acrylonitrile-butadiene elastomer (HNBR)-based rubber compounds (phr).
HNBR | 100 | 100 | 100 | 100 |
Coagent | 3 | 5 | 7 | 9 |
DCP | 2 | 2 | 2 | 2 |
The crosslink density (νT) of the vulcanisates was determined by equilibrium swelling in toluene, based on the Flory-Rehner equation [19]. The Huggins parameter of the elastomer-solvent interaction χ was calculated from the Eq. (1) [18],
(1) |
To determine the amount of ionic crosslinks in the elastomer network, samples were swollen in toluene in a desiccator with saturated ammonia vapour (25% aqueous solution). The content of ionic crosslinks (Δν) was calculated from Eq. (2), where νA is the crosslink density determined for samples treated with ammonia vapour:
(2) |
The tensile properties of the vulcanisates were determined according to ISO-37, with a ZWICK 1435 universal machine.
The dispersion of coagent particles in elastomer matrix was estimated using Scanning Electron Microscopy with a ZEISS SEM microscope. Vulcanisates were broken down in liquid nitrogen, and the surfaces of the vulcanisate fractures were examined. Prior to measuring, the samples were coated with carbon.
2.6 Dynamic-mechanical analysis
Dynamic-mechanical measurements were carried out in tension mode using a DMTA V viscoanalyser (Rheometric Scientific). Measurements of the dynamic moduli were performed over the temperature range (–60 ÷ 100 °C) with a heating rate of 2 °C/min, at a frequency of 1 Hz and a strain amplitude of 0.02%. The temperature of the elastomer glass transition was determined based on the maximum of tanδ = f(T), where tanδ is the loss factor and T is the measurement temperature.
3 Results and discussion
3.1 Efficiency of metal oxides and layered minerals modification
To estimate the effectiveness of modification with itaconic acid, the elementary analysis of coagents was performed. The content of carbon was determined. Based on these results, the amount of itaconic acid in the coagents was evaluated. Results are given in Table 2.
Efficiency of metal oxides and layered minerals modification.
Coagent | C content (%) | Itaconic acid content (mmol/100 g of modified powder) | Modification efficiency (%) |
CaO/IA | 2.93 | 48.8 | 79.4 |
MgO/IA | 1.24 | 20.7 | 33.6 |
BM/IA | 2.70 | 45.0 | 73.2 |
HTA/IA | 2.73 | 45.5 | 74.0 |
The highest reactivity towards itaconic acid revealed the CaO. The efficiency of CaO modification was 79.4%. The content of itaconic acid determined for BM was lower than for CaO (45.0 mmol/100 g of BM) and the modification efficiency was 73.2%. Similar results were obtained for HTA. The content of itaconic acid bonded to this mineral was 45.5 mmol/100 g of HTA, whereas the efficiency of modification was 74%. The lowest reactivity towards itaconic acid revealed MgO. The efficiency of modification process was only 33.6%. Probably, low activity of MgO in modification process resulted from a small content of hydroxyl groups on MgO surface, which are used to react with itaconic acid or limited accessibility of these groups in the MgO crystals.
The presence of IA in coagents was confirmed by thermogravimetric analysis (Fig. 1, Table 3).
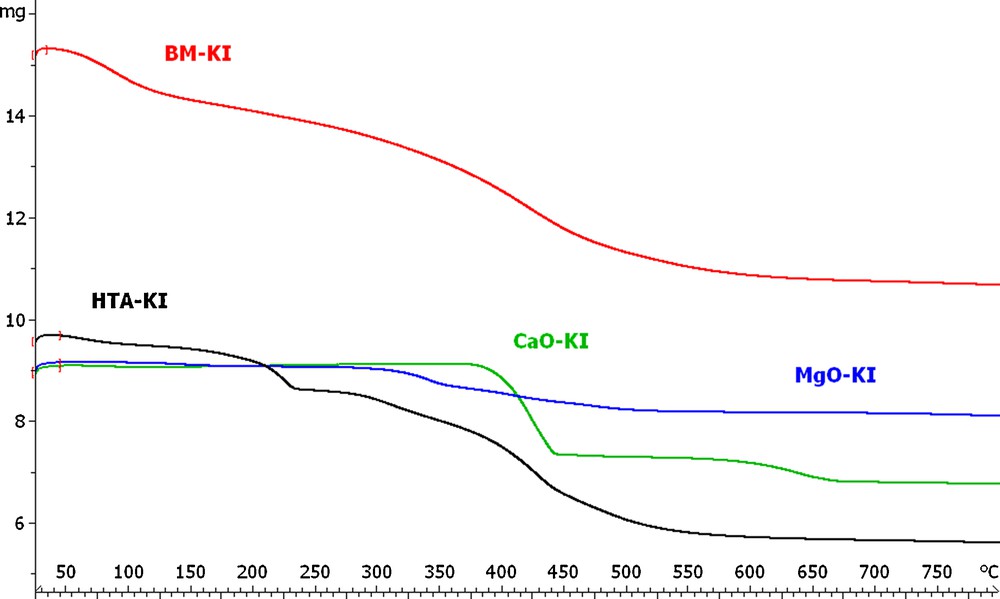
TGA thermogram for metal oxides and layered minerals modified with itaconic acid.
Thermogravimetric analysis of coagents.
Coagent | Total weight loss (%) |
CaO/IA | 25.0 |
MgO/IA | 9.6 |
BM/IA | 18.6 |
HTA/IA | 32.4 |
The TGA curves of CaO/IA showed two loss weight steps resulting mainly from the decomposition of modifier. The first step in the temperature range of 250 to 500 °C was due to decomposition of organic acid and yielded weight loss of 20.3%. The second step of thermal decomposition was within the temperature range of 550 °C to 700 °C with the weight loss from 4.7%. In the case of MgO/IA, the decomposition process occurred in the temperature range of 150 to 700 °C and the total weight loss was about 9.6%. The TGA curves of BM/IA showed two weight losses. The first step of thermal decomposition yielded weight loss about 3.6% and occurred in the temperature range of 50 to 200 °C. It was probably due to dehydration, that is the loss of water remaining after drying process or adsorbed from environment (moisture) or dehydroxylation process of BM surface. Itaconic acid decomposed from 200 to 750 °C with the weight loss 15%. Two steps of thermal decomposition were observed for HTA. The first step, probably dehydration and dehydroxylation of HTA surface, was in the temperature range of 150 to 250 °C and yielded weight loss of 5.9%. The second step of thermal decomposition (probably decomposition of organic modifier) was within the temperature range of 250 to 700 °C with the weight loss 26.5%.
The results of elementary and thermogravimetric analysis confirmed that the reaction between metal oxide or layered mineral and itaconic acid occurred. Although, it could not be excluded that a small amount of salt was also formed during modification process and coagents were a mixtures of metal oxide or layered mineral coated with itaconic acid with the small amount of its salt.
3.2 Coagents particles size and their dispersion in elastomer
The particle size of the coagents is a very important parameter that has a great influence on their activity. A reduction in particle size increases the coagent specific surface area, providing better contact between its particles and the elastomer chains. Therefore, we studied the effect of modification on mineral oxides and layered minerals particle size. The sizes of the coagent particles measured in water are presented in Table 4.
Coagents particle size measured in water.
Coagent | Aggregate size (nm) | Size of the aggregate main fraction (nm) | number % |
CaO | 36–3000 | 46 | 50 |
>2000 | 10 | ||
CaO/IA | 41–3000 | 41 | 50 |
>2000 | 8 | ||
MgO | 130–3000 | 165 | 27 |
>2000 | 1 | ||
MgO/IA | 104–208 | 131 | 30 |
BM | 131–185 | 147 | 41 |
BM/IA | 104–147 | 116 | 37 |
HTA | 234–331 | 262 | 38 |
HTA/IA | 208–295 | 234 | 43 |
Modification of the CaO with itaconic acid did not affect the particle size significantly. In the case of pure CaO, two particle fractions were observed: 46 nm in size (50%) and about 2 μm in size (10%). CaO modification reduced microsized fraction by about 2% in comparison with the unmodified powder. A reduction of the main particles fraction size to 41 nm was also observed.
The sizes of the magnesium oxide particles, as measured in water, were within the range of 130 to 3000 nm, with the size of the main number fraction being 165 nm (27%). A small fraction (1%) of particles over 2 μm in size was also observed. The size of the particles was reduced upon treatment with itaconic acid to a range of 104 to 208 nm with the size of the main particles fraction being 131 nm (30%).
Modification with itaconic acid resulted in the reduction of boehmite and hydrotalcite particle size. The layered minerals aggregates were reduced in the water dispersion to particles with sizes ranging from 104 to 147 nm (BM/IA) and 208 to 295 nm (HTA/IA).
Elastomers are hydrophobic in nature. Therefore, the size of the coagent particles was measured in a liquid hydrophobic medium — paraffin oil, which was chosen as the model for an elastomer matrix (Table 5). The aim of this study was to estimate the tendency of coagent particles to agglomerate in elastomer.
Coagents agglomerate size in paraffin oil.
Coagent | Agglomerate size (μm) |
CaO | 9.5 |
CaO/IA | 5.4 |
MgO | 9.6 |
MgO/IA | 7.3 |
HTA | 10.0 |
HTA/IA | 7.5 |
BM | 1.7 |
BM/IA | 1.0 |
Unfortunately, pure mineral oxides and layered minerals exhibited a high tendency towards aggregation or agglomeration in paraffin oil. Primary particles formed microsized clusters with sizes ranging from 1.7 μm (boehmite) to 10 μm (hydrotalcite). Therefore, it could be assumed that coagent particles will agglomerate the elastomer matrix.
The dispersion of coagent particles in the elastomer was estimated based on vulcanisates SEM images. The results are presented in Fig. 2a–d.
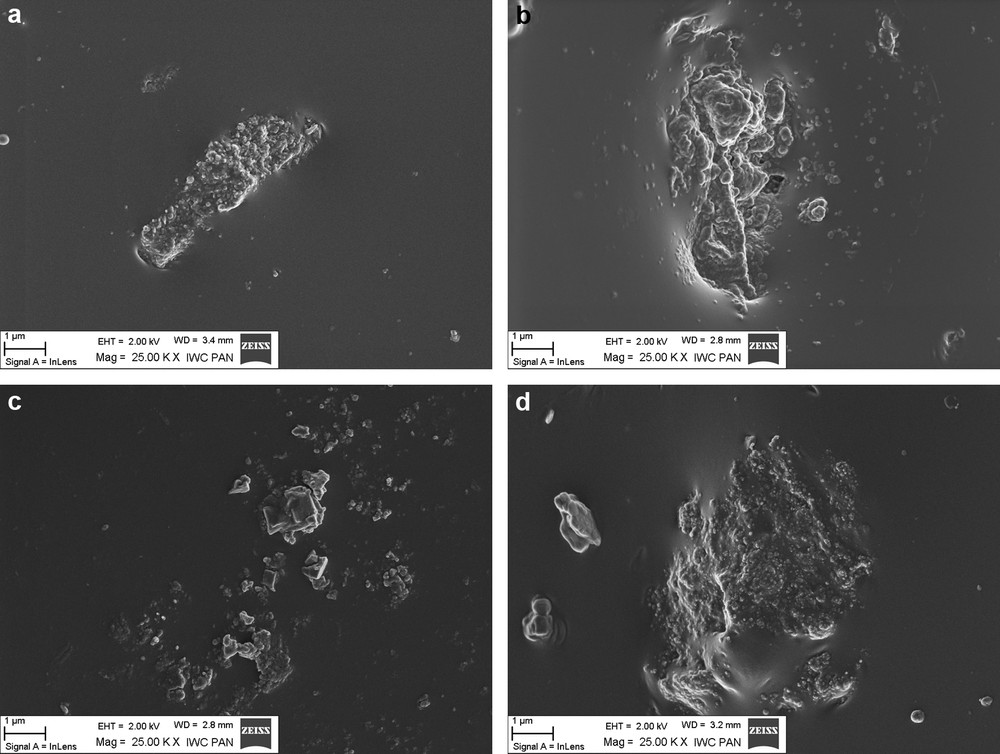
SEM images of vulcanisates containing 3 phr of: a: CaO/IA; b: MgO/IA; c: BM/IA; d: HTA/IA.
Dispersion of coagent in the elastomer was heterogeneous. Coagent particles revealed a high ability to agglomerate in elastomer matrix. They formed agglomerates several micrometers in size, which have a complex structures. However, these agglomerates were surrounded with elastomer film and especially in the case of hydrotalcite, tightly bound to the elastomer matrix. Probably, wetting of hydrotalcite agglomerates with elastomer contributed to good mechanical properties of the vulcanisates, despite poor dispersion of modified hydrotalcite particles.
3.3 Cure characteristics and crosslink density of vulcanisates
The main goal of coagent application is to reduce the vulcanisation time of rubber compounds because it is important from an economical and technological point of view. Moreover, coagents should increase the crosslinks density of vulcanisates and the efficiency of the crosslinking process. The influence of coagents was estimated based on rheometer measurements. The cure characteristics of HNBR compounds are given in Table 6.
Cure characteristics of hydrogenated acrylonitrile-butadiene elastomer (HNBR) compounds (ΔG: increment of torque in the rubber compound during vulcanisation; t90: optimal vulcanisation time; tp: scorch time).
Coagent | Coagent amount (phr) | ΔG (dNm) | t90 (min) | tp (s) |
– | – | 46.8 | 50 | 174 |
CaO/– | 3 | 48.0 | 45 | 193 |
CaO/IA | 3 | 45.6 | 25 | 168 |
5 | 52.0 | 30 | 151 | |
7 | 52.4 | 30 | 182 | |
9 | 47.2 | 25 | 151 | |
MgO/– | 3 | 50.8 | 40 | 178 |
MgO/IA | 3 | 56.9 | 35 | 114 |
5 | 50.4 | 32 | 175 | |
7 | 53.5 | 30 | 141 | |
9 | 54.1 | 26 | 135 | |
BM/– | 3 | 46.1 | 40 | 172 |
BM/IA | 3 | 41.5 | 33 | 191 |
5 | 41.4 | 33 | 175 | |
7 | 44.8 | 33 | 198 | |
9 | 45.9 | 30 | 175 | |
HTA/– | 3 | 44.5 | 45 | 188 |
HTA/IA | 3 | 52.6 | 32 | 175 |
5 | 51.0 | 37 | 162 | |
7 | 61.9 | 37 | 178 | |
9 | 52.9 | 35 | 163 |
Applying CaO, MgO and layered minerals (BM, HTA) coated with itaconic acid resulted in a considerably shorter vulcanisation time for rubber compounds compared to the conventional peroxide system. It confirmed that these powders act as coagents of HNBR peroxide vulcanisation. The shortest cure times were exhibited by rubber compounds containing CaO/IA, whereas the longest vulcanisation times were observed for rubber compounds with HTA/IA. Generally, coagents had no significant effect on the scorch time of rubber compounds. Only the MgO/IA reduced the scorch time considerably, from 174 s for rubber compound without coagent to 114 to 141 s for composites containing MgO/IA.
The application of coagents as well as pure powders did not significantly affect the torque increment of rubber composites during vulcanisation; an increase in ΔG values was observed for elastomer compounds containing MgO/IA or HTA/IA. The amount of coagent seemed not to have a significant impact on the torque increment.
Apart from the reduction of vulcanisation time, coagents are used to increase the crosslinks density of rubber compounds. The effect of CaO, MgO and layered minerals with itaconic acid on the crosslinks density was estimated based on the results of the vulcanisates’ equilibrium swelling in toluene and toluene upon ammonia vapour (presence of ionic crosslinks). The results are given in Figs. 3 and 4.
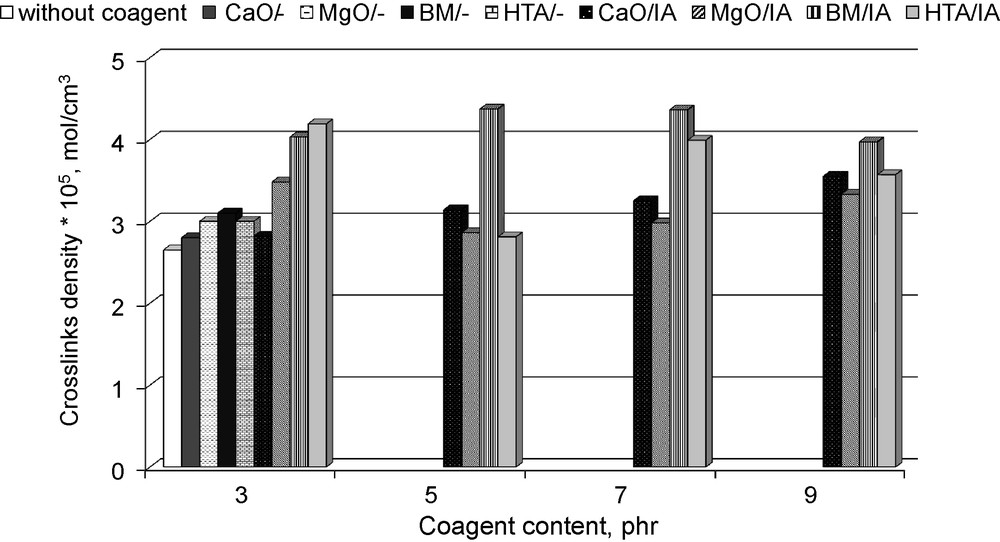
Crosslinks densities of hydrogenated acrylonitrile-butadiene elastomer (HNBR) vulcanisates containing coagents.
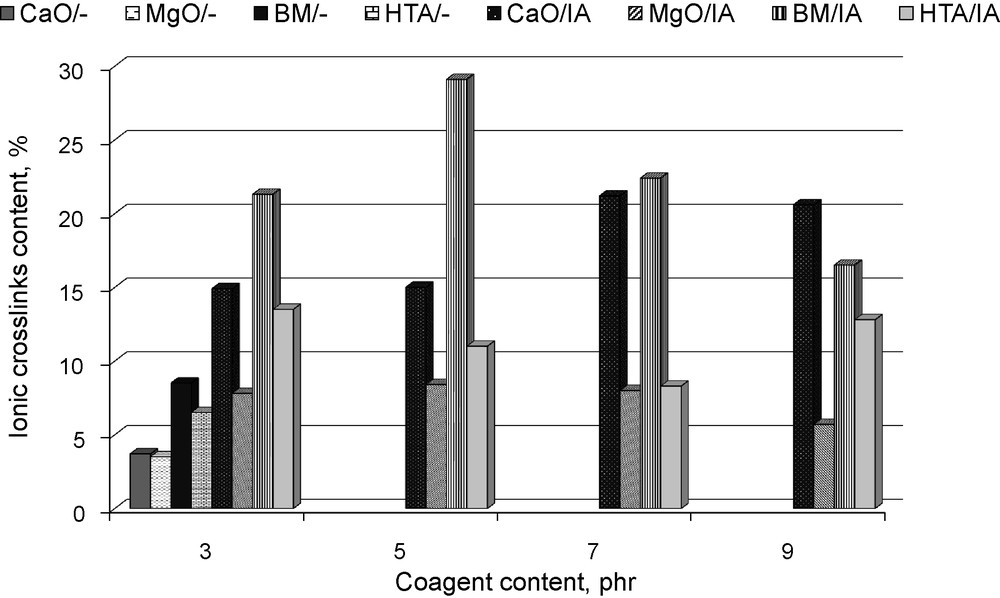
The content of ionic crosslinks in hydrogenated acrylonitrile-butadiene elastomer (HNBR) vulcanisates containing coagents.
From the data presented in Fig. 3, it follows that the application of pure powders did not affect the crosslink density, whereas coagents increased the amount of crosslinks in the vulcanisates, as compared to those produced using only dicumyl peroxide. The highest crosslink densities were obtained for vulcanisates containing BM/IA or HTA/IA. Results of these studies confirmed that unsaturated acid contributes to the increase of vulcanisation efficiency. However, the kind of powder coated with itaconic acid is also very important. There was not a simple relation between the amount of coagent in the composites and their crosslink density. It could be supposed that the effect of coagents’ amount on the crosslinks density was dependent on the tendency of their particles to agglomerate in the elastomer matrix. It is commonly known that agglomeration decreases the activity of coagents in the vulcanisation process.
Swelling of vulcanisates in toluene upon ammonia vapour allows one to determine the content of crosslinks in the elastomer network, which do not have a covalent character. In the case of vulcanisates containing unmodified powders, the content of crosslinks determined based on swelling in toluene upon ammonia vapour (about 4 to 8%) could be a measure of the content of physical bonds formed on the interface between metal oxide (layered mineral) and elastomer. It should be noted that the crosslinks density of HNBR vulcanisates was improved probably due to the formation of coagent bridges — additional ionic crosslinks in the presence of metal oxide or layered mineral with unsaturated itaconic acid (Fig. 4). The highest content of ionic crosslinks in the elastomer network was achieved for vulcanisates crosslinked with BM/IA (16 to 29%) or CaO/IA (15 to 21%). HTA/IA and MgO/IA were less active in the crosslinking process. The content of ionic crosslinks determined for vulcanisates containing these coagents was in the range of 8 to 14% for HTA/IA and only 5 to 9% for MgO/IA. The lower activity of HTA and MgO is probably due to agglomeration of their particles in the elastomer. Agglomeration decreases the surface of contact (the interface) between elastomer chains and coagent particles during the crosslinking process. As a result, a smaller amount of ionic crosslinks is formed during the reaction between the elastomer and coagent functional groups. In the case of magnesium oxide, low activity of this coagent in the vulcanisation process was also due to a small amount of itaconic acid bonded to MgO surface. It should be noted that the highest amount of ionic crosslinks was formed in vulcanisates with CaO/IA and BM/IA, which revealed the lowest tendency to agglomeration (see in Fig. 2a and c).
Considering the results, a possible reaction mechanism of coagents could be suggested (Scheme 2).
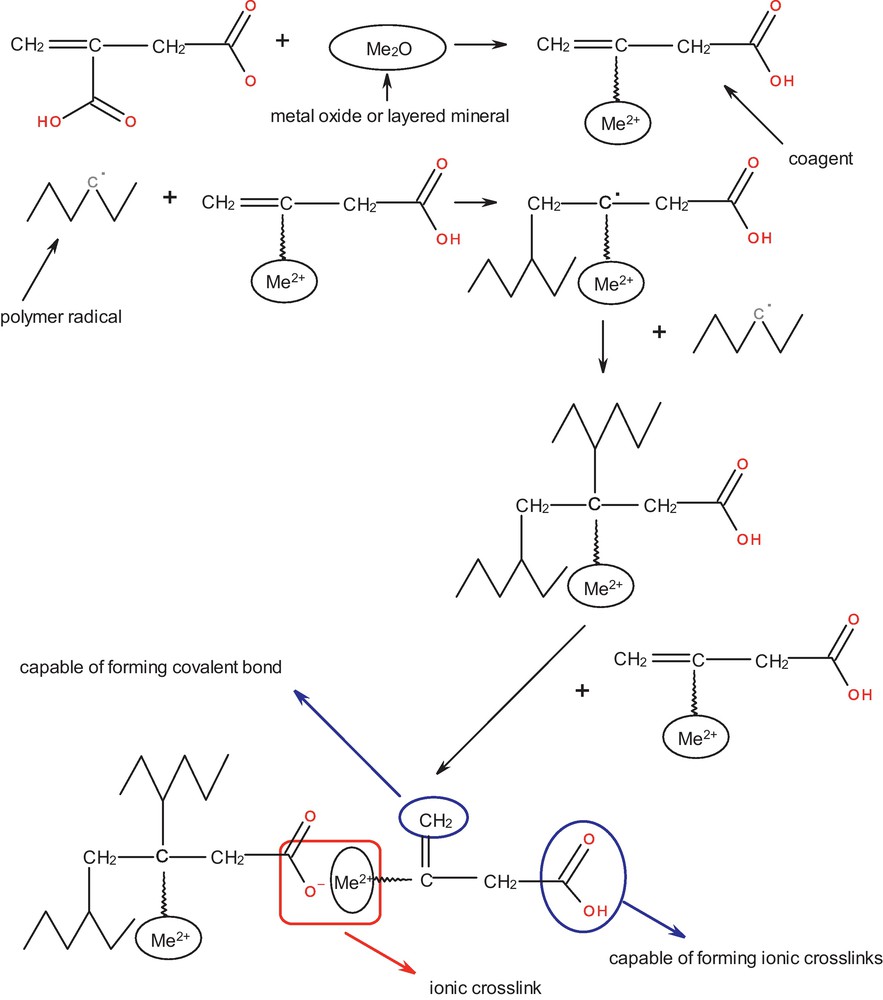
Possible mechanism of coagent reactions.
This mechanism explains how the coagents based on metal oxide or layered mineral coated with allyl-containing acid could be incorporated into the elastomer network. Itaconic acid has two carboxylic groups in the molecule. It could be supposed that during the modification process one of these groups is consumed to attach the itaconic acid to the metal oxide or layered mineral surface. The resulting coagent has three functional groups reactive in the crosslinking process: an unsaturated bond, which can react with polymer macroradical forming covalent bond (in this way coagent molecule is incorporated into polymer chain), a carboxylic group and a metal cation which can be used to form ionic crosslinks. Similar mechanism was proposed by Guo et al. for stearic acid/zinc oxide/dicumyl peroxide system applied in the vulcanisation of nitrile rubber [20].
3.4 Mechanical properties of vulcanisates
Having established the influence of coagents on the vulcanisation process and crosslinks density of vulcanisates, we then examined their mechanical properties. We believed that formation of coagent bridges, labile ionic crosslinks inside the elastomer network, would improve the tensile properties of vulcanisates. The results are given in Fig. 5 and Table 7.
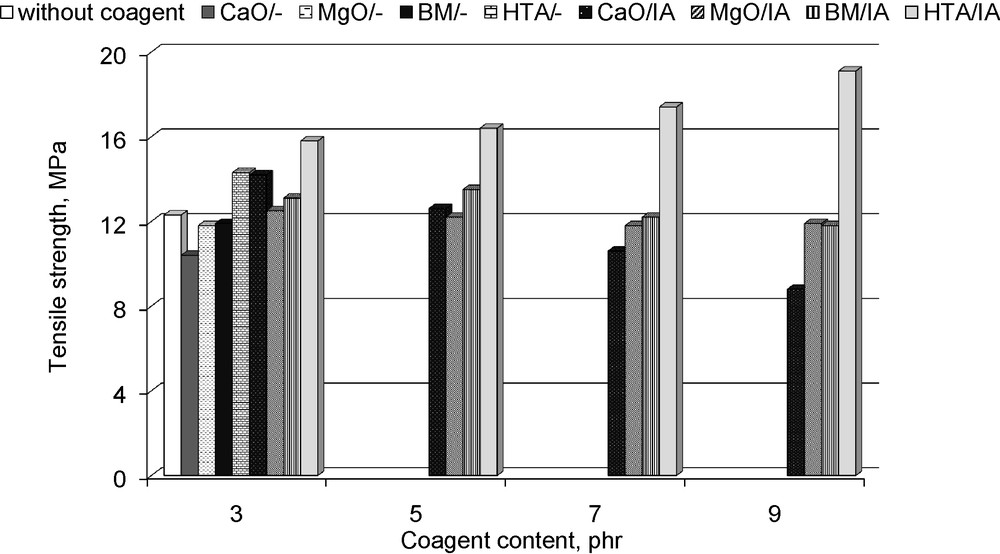
Tensile strength of hydrogenated acrylonitrile-butadiene elastomer (HNBR) vulcanisates containing coagents.
Mechanical properties of hydrogenated acrylonitrile-butadiene elastomer (HNBR) vulcanisates (SE300: modulus at 300% vulcanisate relative elongation; EB: elongation at break).
Coagent | Coagent amount (phr) | SE300 (MPa) | EB (%) |
– | – | 0.98 | 819 |
CaO/– | 3 | 0.96 | 815 |
CaO/IA | 3 | 0.95 | 845 |
5 | 1.02 | 821 | |
7 | 1.03 | 831 | |
9 | 1.07 | 814 | |
MgO/– | 3 | 1.00 | 793 |
MgO/IA | 3 | 1.05 | 704 |
5 | 0.97 | 755 | |
7 | 1.04 | 747 | |
9 | 1.18 | 733 | |
BM/– | 3 | 0.83 | 853 |
BM/IA | 3 | 0.85 | 847 |
5 | 0.86 | 864 | |
7 | 0.87 | 882 | |
9 | 0.94 | 883 | |
HTA/– | 3 | 0.93 | 818 |
HTA/IA | 3 | 0.98 | 776 |
5 | 0.95 | 827 | |
7 | 1.14 | 744 | |
9 | 1.09 | 811 |
HNBR vulcanisate crosslinked without coagent revealed a tensile strength about 12.3 MPa and an elongation at break of 819%. Application of pure CaO, MgO and BM did not improve the tensile strength of vulcanisates, whereas HTA increased the tensile strength by 2 MPa. Application of CaO/IA increased the tensile strength to 14.2 MPa for vulcanisate containing 3 phr of coagent. Further increase in the coagent content deteriorated vulcanisate tensile strength, probably due to coagent particles agglomerating in the elastomer. Large agglomerates could act as critical sites that may generate microcracks and initiate breaking of the sample under external stress. Moreover, the agglomeration of coagent particles may cause the surface area to decrease, followed by a decrease in the size of the interface between the coagent and rubber chains. The presence of coagent and its amount in the elastomer had no significant impact on the modulus at 300% elongation or the vulcanisate elongation at break (Table 7).
MgO/IA did not affect vulcanisate tensile strength. One of the reasons is probably the heterogeneous dispersion of particles in the elastomer matrix and their tendency for agglomeration (see in Fig. 2b). However, the other reason is the relatively low activity of magnesium oxide during the crosslinking process that leads to the smallest number of labile ionic crosslinks in the elastomer network. It is known that the presence of ionic clusters, which are able to rearrange inside the elastomer matrix upon external stress, contributes in the enhancement of the tensile strength of vulcanisates. Increasing the coagent content did not affect the vulcanisates’ tensile strength or elongation at break (Fig. 5, Table 7). However, a decrease in vulcanisate elongation at break as compared to vulcanisate without coagent was observed.
BM/IA increased the tensile strength of vulcanisates containing 3 and 5 phr of coagent. Further increase in the coagent content deteriorated vulcanisates tensile strength. Application of BM/IA increased the elongation at break and decreased the modulus at 300% relative elongation as compared to pure peroxide vulcanisate (Table 7).
Among the coagents studied, the highest tensile strength was observed for vulcanisates with HTA/IA. The tensile strength of vulcanisates increased with the amount of coagent and was within the range of 15 to 19 MPa. Considering the fact that vulcanisates containing CaO/IA or BM/IA did not reveal such high tensile strengths, despite the high content of ionic crosslinks, it could be supposed that the improvement in vulcanisate tensile strength did not result only from the presence of labile ionic clusters in the elastomer network. Possibly, the enhancement in tensile strength was due to the reinforcing effect of HTA as well [21–23]. The particles of hydrotalcite formed the structure, meaning their own network penetrated through the elastomer network and contributed to the stress distribution.
3.5 Dynamic-mechanical properties of vulcanisates
A dynamic-mechanical analysis was performed to confirm the existence of ionic clusters in the elastomer network. The loss factor tanδ, as a function of temperature, for the vulcanisates containing 5 phr of coagents is presented as an example in Fig. 6. The values of the glass transition temperature were compiled in Table 8.
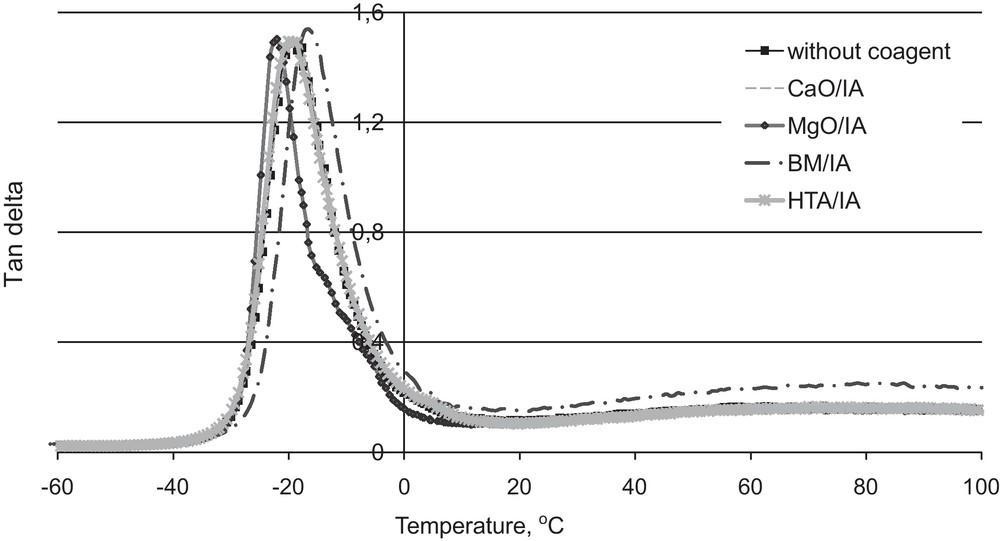
Tanδ versus temperature for hydrogenated acrylonitrile-butadiene elastomer (HNBR) vulcanisates containing coagents.
Glass transition temperature of hydrogenated acrylonitrile-butadiene elastomer (HNBR) vulcanisates.
Vulcanisate | Tg (°C) |
Uncrosslinked HNBR | –21.3 |
Without coagent | –19.0 |
CaO/IA | –18.5 |
MgO/IA | –22.1 |
BM/IA | –16.6 |
HTA/IA | –20.0 |
The glass transition temperature of pure uncrosslinked HNBR was (–21.3 °C). Crosslinking of HNBR increased the glass transition of elastomer as could be expected. The existence of two transitions can be observed. The first transition is the glass transition of the elastomer at low temperatures, with a maximum that represents Tg. The determined glass transition temperatures for the vulcanisates with CaO/IA and HTA/IA were (–18.5 °C) and (–20.0 °C), respectively. Therefore, it can be concluded that these coagents did not affect the Tg value of elastomer crosslinked with peroxide considerably. MgO/IA shifted the glass transition temperature of the vulcanisate towards lower temperatures (–22.1 °C), whereas BM/IA increased the Tg value to (–16.6 °C) due to the highest crosslinks density of these vulcanisate. The different impact of the coagents on the vulcanisates glass transition temperature was probably due to the existence of differently immobilised elastomer phases on the coagent particle surfaces.
The second transition (the fuzzy peak) is the ionic transition, occurring at high temperatures (50 to 100 °C), resulting from the occurrence of a hard phase due to ionic associations — ionic clusters or aggregates. The second transition is the most noticeable for vulcanisates with BM/IA, which revealed the highest content of ionic crosslinks in the elastomer network.
4 Conclusions
We studied new coagents for HNBR peroxide crosslinking. These coagents were based on nanosized calcium and magnesium oxide and layered minerals (boehmite, hydrotalcite) in combination with unsaturated itaconic acid. Such a heterogenic system was applied to achieve additional ionic crosslinks in the elastomer network and multifunctional and labile ionic clusters which are able to slip on the surface of solid particles.
Application of the coagents caused a decrease in rubber compounds’ vulcanisation time as compared to the conventional peroxide system. Moreover, these coagents increased the crosslinks density of vulcanisates due to formation of additional ionic crosslinks in the elastomer network in the reaction of the coagent functional groups with the elastomer chains. The crosslinks density of the vulcanisates usually increased with the amount of coagent in the composite. The highest crosslinks densities were obtained for vulcanisates containing HTA/IA or BM/IA. Coagents increased the tensile strength of vulcanisates. The highest tensile strength was exhibited by vulcanisates containing HTA. We concluded that the presence of strong and multifunctional labile ionic clusters, which are able to move on the surface of the solid coagent particles, should result in a high ability of vulcanisates for stress relaxation, and as a consequence, an improvement in mechanical strength was achieved. Moreover, coagent particles could form the structure in the elastomer matrix, which contributes to the reinforcement effect. Application of these coagents allowed for replacing the traditional coagents: zinc salts. It is very important from an ecological point of view. The European Union requires that zinc compounds to be reduced or eliminated, as they were found to be toxic to aquatic species.
Acknowledgements
The authors wish to acknowledge the Polish Ministry of Science and Higher Education as well as the National Centre of Research and Development for supporting this study.