1 Introduction
Hydrogen is increasingly regarded as an ideal clean and alternative energy source and vector for the near future [1,2]. Methane is one of several fuel candidates that can be used for the production of hydrogen and synthesis gas via the catalytic steam reforming reaction [3].
Two major reactions are considered in the methane steam reforming (MSR) process. The methane steam reforming Eq. (1) and the water gas shift reaction WGS Eq. (2).
(1) |
(2) |
Combining these two reactions gives Eq. (3):
(3) |
Catalysts for hydrogen production processes are mainly based on noble metals and nickel. Rh-based catalysts are highly active, but their elevated cost makes them unsuitable for use on the industrial scale, unless it is possible to reduce the quantities used without impairing catalytic performances. The advantage of using Ni-based catalysts is that they are cost-effective, but they are prone to form carbon [4]. However, studies have proven that catalysts obtained via hydrotalcite-type precursors are resistant to carbon deposition, and therefore could be applied to the MSR process [5]. These compounds gain increasing importance as catalyst precursors for MSR due to their high specific surface area, basic character, and memory effect [6,5].
Several authors showed that the presence of copper as an active metal can suppress carbon formation in the syn-gas production step and can improve water gas shift activity in MSR [7–10]. They claimed that Cu played a role in promoting the gasification of deposited carbon, and its addition to Ni led to the enhancement of the WGS reaction activity in the overall MSR process and decreased the coke deposit [7–10].
In this study, the x Cu/Co6Al2 catalysts were prepared via the hydrotalcite route, were characterized using several physicochemical techniques, and their reactivity was tested in the MSR reaction.
2 Experimental
The Co–Al layered double hydroxides were prepared by precipitating ions in an aqueous solution with appropriate quantities of Co(NO3)2·6H2O (Sigma-Aldrich, 98%) and Al(NO3)3·9H2O (FLUKA, 98%) into a 1 M sodium carbonate Na2CO3 (HIMEDIA, 98%) aqueous solution at 60 °C. The pH of the solution was maintained constant (pH ∼ 10). The resulting slurry was heated at 60 °C for 2 h and then placed in a drying oven for 24 h. The precipitate was filtered, washed with hot deionized water (until its pH reached 6–7), dried for 48 h at 60 °C and then grinded to obtain fine powders. Thermal stabilization was performed under an air flow (2 L·h−1) up to 500 °C (1 °C·min−1), with a dwell of 4 h at the final temperature. The latter temperature was chosen since thermo-gravimetric analysis (TGA) revealed that at this temperature, stable oxides are obtained with no further weight loss.
x Cu/Co6Al2 catalysts (x represents the Cu weight percentage) were prepared by adding an adequate quantity of copper (II) nitrate Cu(NO3)2·3H2O (Prolabo, 99%) solution to the calcined support and mixing for 2 h. The excess of water is then slowly eliminated in a rotary evaporator. The obtained solid was then dried at 100 °C overnight and then thermally stabilized under the same conditions as those used for the support.
X-ray diffraction (XRD) experiments were performed at ambient temperature on a Bruker D8 Advance diffractometer using the Cu Kα radiation (1.5405 Å). The diffraction patterns were indexed by comparison with the JCPDS files. Temperature-programmed reduction experiments (TPR) were carried out on a Zeton Altamira apparatus with a hydrogen flow of 30 mL·min−1 (5 vol.% H2 in Ar). The sample was heated (5 °C·min−1) at atmospheric pressure, and the amount of H2 consumed was monitored with a thermal conductivity detector (TCD).
The MSR test was carried out under atmospheric pressure in a catalytic reactor (internal diameter = 6.6 mm) coupled with a micro GC (Varian CP-4900) equipped with a TCD. Two hundred milligrams of the catalyst were introduced into the reactor and reduced in situ under an H2 flow (15 mL·min−1) at 400 °C for 1 h to activate the catalyst. Next, the catalyst was purged with an Ar flow to assure that the reaction started in a hydrogen-free feed. The catalytic reactivity was studied in the 600–800 °C temperature range, in which the MSR reaction is thermodynamically possible under the test conditions. The reactant gas flow consisted of a stoichiometric ratio of steam to methane (3:1) and the total flow was 50 mL·min−1 (GHSV = 1,5000 mL·g−1·h−1).
3 Results and discussion
Fig. 1a shows the XRD patterns obtained for freshly calcined solids. The obtained patterns present diffraction lines corresponding to the three cobalt oxide spinel phases, which are difficult to differentiate by this technique – Co3O4 (JCPDS No. 42-1467), CoAl2O4 (JCPDS No. 44-0160) and Co2AlO4 (JCPDS No. 38-0814). The diffraction lines of CuO in the tenorite phase (JCPDS No. 45-0937) are observed for impregnated catalysts. These lines became more intense when the copper content was increased to 15 wt.% and 25 wt.%, respectively. This indicates that a copper quantity exceeding 5 wt.% leads to the formation of agglomerated CuO species at the surface of the solid. However, the formation of Cu–Co mixed oxides phase with diffraction lines at 31.2°, 36.7° and 44.7° (JCPDS N°37-0878) cannot be excluded, as these latter may be present but masked by the more intense diffraction lines of the mixed cobalt oxides spinel phase.
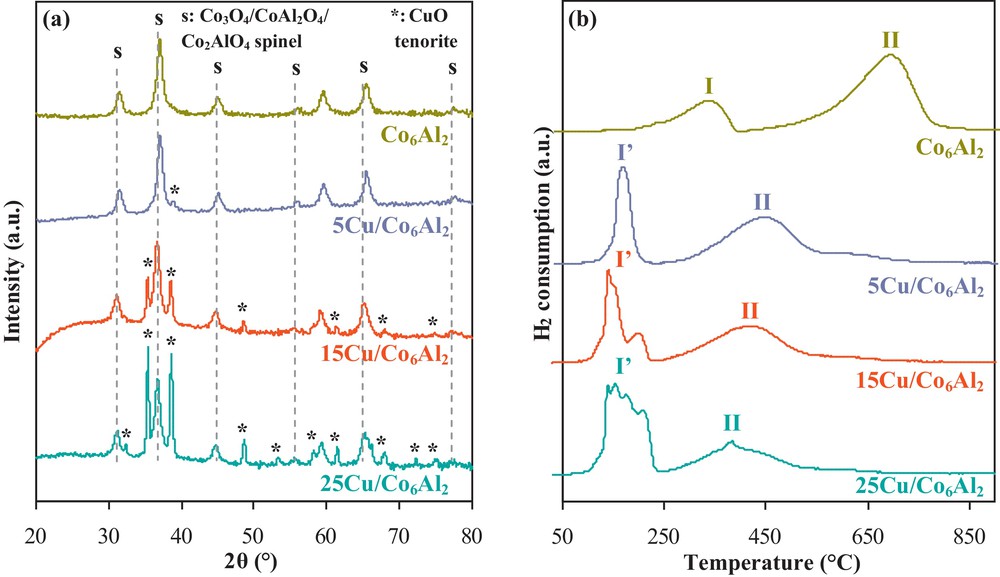
(a) XRD patterns and (b) H2 consumption profiles of the freshly calcined x Cu/Co6Al2 solids.
Fig. 1b presents the TPR profiles of different freshly calcined solids. The Co6Al2 TPR profile showed two reduction peaks. Peak I is attributed to the reduction of the Co3O4 species and peak II is due to the reduction of a cobalt aluminate Co3+–Al3+ or Co2+–Al3+ species [11]. The TPR profiles corresponding to copper-impregnated catalysts present reduction peaks in the 150–230 °C temperature range (peak I’). These latter are associated with the reduction of different copper oxide species. In fact, CuO is reduced into Cu2O and then into metallic Cu. Moreover, different Cu (II) species may exist in the freshly calcined catalyst: isolated Cu2+ ions, Cu2+ clusters, small well dispersed CuO particles, CuO agglomerates and even bulk CuO [12]. The presence of these different species is demonstrated by the different reduction peaks obtained at low temperatures, especially for the 25Cu/Co6Al2 solid. Differentiation is impossible using the TPR technique; however, the peak at the lowest temperature probably corresponds to the reduction of a well-dispersed small CuO species, while the one at the highest temperature is most probably due to the reduction of bulk CuO.
Table 1 presents experimental (peaks I, I’ and II) and theoretical (CuO → Cu) hydrogen consumption values for the different solids. While consumption corresponding to peak I’ was attributed to the reduction of the copper oxide species, it is clear that there is a hydrogen over-consumption compared to theoretical predictions. Therefore, it is suggested that the presence of copper facilitates the reduction of some cobalt oxide species by the hydrogen “spill-over” phenomenon. This is confirmed by the lowering of peaks I, I’ and II at the maximum temperature with the increase of copper content. It seems that the two metals, cobalt and copper, react synergistically with hydrogen, making the reduction of their corresponding oxide species (CuO, Co3O4, Cu–O–Co…) possible at lower temperatures compared to that of those obtained for the non-impregnated support.
Theoretical hydrogen consumption values for the different calcined solids.
H2 consumption [μmol H2·g−1 catalyst] | |||
Experimental | Theoretical | ||
Peak I or I’ | Peak II | CuO → Cu | |
Co6Al2 | 2568 | 9132 | – |
5Cu/Co6Al2 | 3302 | 8378 | 787 |
15Cu/Co6Al2 | 4831 | 7500 | 2360 |
25Cu/Co6Al2 | 6035 | 5940 | 3934 |
Fig. 2 displays methane conversion in the MSR reaction in the presence of the calcined solids. It is observed that once 5 wt.% of copper are impregnated on calcined Co6Al2, methane conversion reached 100% at 700 °C, whereas it did not exceed 3% for Co6Al2 at the same temperature [13].
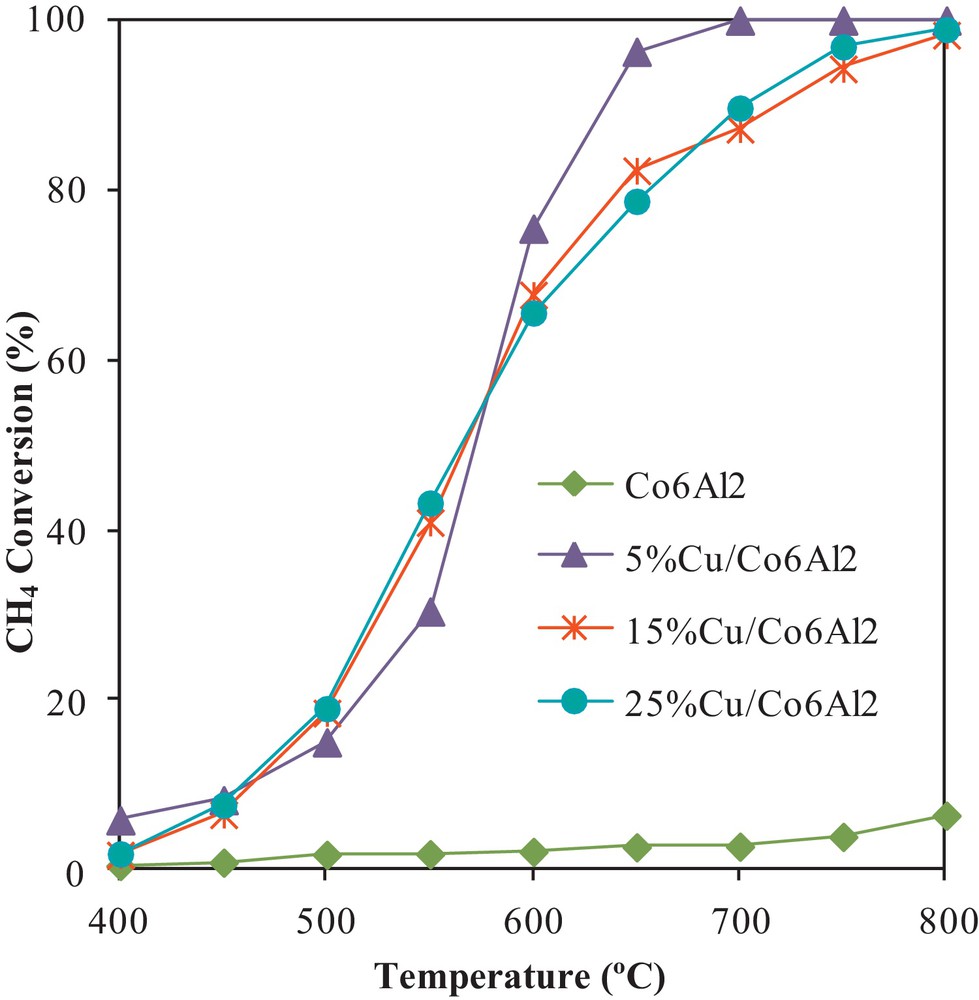
Methane conversion in the MSR reaction over the different calcined solids.
When copper loading was increased, the conversion of methane was negatively affected. In fact, 15Cu/Co6Al2 and 25Cu/Co6Al2 exhibited comparable catalytic performances in the considered temperature range. However, they presented lower methane conversions compared to the 5Cu/Co6Al2 catalyst (82% and 79% methane conversion at 650 °C for 15Cu/Co6Al2 and 25Cu/Co6Al2 respectively compared to 96% for 5Cu/Co6Al2). As shown from the XRD and TPR results, an increase in metal loading resulted in copper oxide species agglomeration and therefore in a decrease of its dispersion. Consequently, this would decrease catalytic reactivity. In addition, the hydrothermal atmosphere at high temperature resulted in sintering of copper clusters dispersed on the surface of the catalyst with high copper loadings. This reduces the dispersion of the active metal, leading to a decrease in the catalytic reactivity. In addition, the presence of both Cu0 and Cu+ species in Cu/ZnO catalysts during the water-gas shift reaction was reported in the literature [14]. It was concluded that Cu+ was the actual active species under the reaction conditions, and this might influence the catalytic activity via a reduction–oxidation mechanism between Cu0 and Cu+, in which the Cu+ sites oxidize chemisorbed CO to CO2 to form Cu0, whereas the reduced Cu0 sites were reoxidized by H2O to form Cu+ and H2.
Molar flow rates of the produced gas as a function of the reaction temperature for the different calcined solids are reported in Table 2. As the temperature is raised from 600 to 800 °C, H2 concentration increases. And the significant increase in the CO concentration should be expected as a result of the thermodynamic equilibrium of the water gas shift (WGS) reaction and the reverse carbon gasification reactions where a temperature rise would not favor them, thus causing more CO formation. The CO2 concentration showed a gradual decrease with a temperature increase. This is probably due to the contribution of the reversed water gas shift (RWGS) reaction favored at higher temperatures. The 25Cu/Co6Al2 catalyst showed the highest CO molar flow rate with the lowest CO2 production, indicating the greater importance of the RWGS reaction over this catalyst. As the surface of this catalyst is covered with copper oxide clusters, it can be assumed that these types of species favor the RWGS reaction. On the other hand, the 5Cu/Co6Al2 catalyst produced the highest quantities of H2 and CO2, emphasizing that this solid favors the WGS reaction. An intermediate behavior is observed for the 15Cu/Co6Al2 catalyst.
Molar flow rates (mol·min−1·g−1cata) of H2, CO and CO2 as a function of temperature over the different calcined solids.
400 | 450 | 500 | 550 | 600 | 650 | 700 | 750 | 800 | |
Co6Al2 | |||||||||
H2 | – | 0.01 | 0.01 | 0.01 | 0.01 | 0.01 | 0.02 | 0.05 | 0.1 |
CO | – | – | – | – | – | – | – | 0.01 | 0.01 |
CO2 | – | – | – | – | – | – | 0.01 | 0.02 | 0.03 |
5Cu/Co6Al2 | |||||||||
H2 | 0.05 | 0.08 | 0.28 | 0.73 | 2.02 | 2.60 | 2.82 | 2.84 | 2.81 |
CO | – | – | – | – | 0.19 | 0.26 | 0.34 | 0.43 | 0.47 |
CO2 | 0.01 | 0.02 | 0.07 | 0.23 | 0.66 | 0.82 | 0.54 | 0.73 | 0.67 |
15Cu/Co6Al2 | |||||||||
H2 | 0.08 | 0.17 | 0.52 | 1.17 | 1.89 | 2.23 | 2.34 | 2.49 | 2.56 |
CO | – | – | 0.01 | 0.04 | 0.19 | 0.33 | 0.38 | 0.46 | 0.46 |
CO2 | 0.01 | 0.05 | 0.15 | 0.36 | 0.42 | 0.39 | 0.37 | 0.35 | 0.40 |
25Cu/Co6Al2 | |||||||||
H2 | 0.07 | 0.21 | 0.54 | 1.27 | 1.88 | 2.16 | 2.39 | 2.56 | 2.60 |
CO | – | – | – | – | 0.23 | 0.44 | 0.60 | 0.67 | 0.74 |
CO2 | 0.01 | 0.06 | 0.16 | 0.36 | 0.49 | 0.42 | 0.36 | 0.15 | 0.09 |
In order to check the oxidation state of the different species and the possible formation of coke after catalytic testing, the XRD pattern of the used 5Cu/Co6Al2 was recorded (Fig. 3).
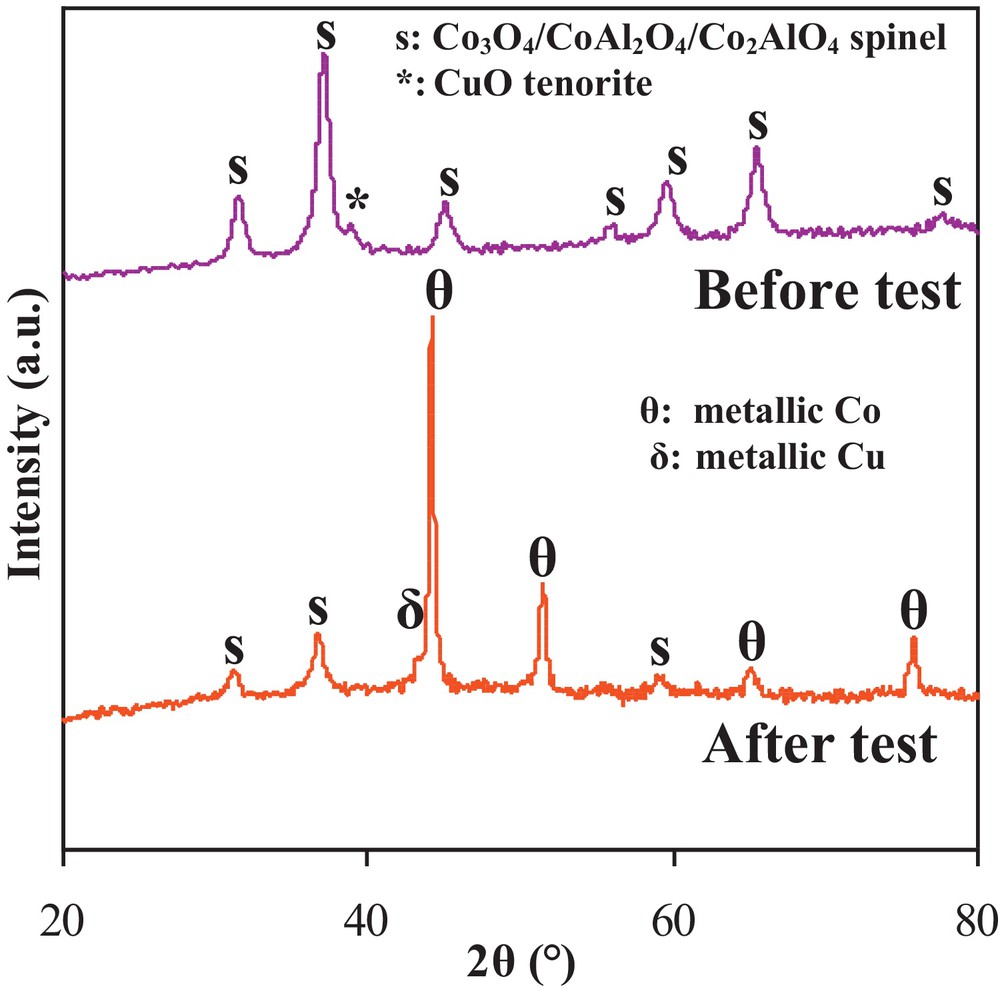
XRD patterns recorded before and after MSR reaction over the 5Cu/ethane conversion in the MSR reaction over the different calcined solids.
The XRD pattern corresponding to the 5Cu/Co6Al2 catalyst after its use in the MSR reaction presents diffraction lines attributed to Cu0, marked with the symbol “δ” (JCPDS No. 04-0836) in Fig. 3. The CuO diffraction lines were absent, indicating an advanced reduction of copper oxide species during the catalytic test. The cobalt oxide spinel phase diffraction lines were still present after the test, but their intensities were decreased. Intense diffraction lines attributed to Co0, marked with the symbol “θ” (JCPDS No. 15-0806), were identified, indicating that a part of the cobalt oxide species were reduced during the catalytic test. It is worth mentioning that DSC/TG analyses done on catalysts after the tests showed that no carbon species or coke were deposited on them, which can be promising for the development of stable catalysts for the SRM reaction.
4 Conclusion
In this study, the catalytic behavior of Co6Al2, 5Cu/Co6Al2, 15Cu/Co6Al2 and 25Cu/Co6Al2 was studied in the MSR reaction. It was demonstrated that, depending on the copper content, different types of copper oxide species were present in the impregnated solids after calcination at 500 °C. The addition of a small amount of copper (5 wt.%) increased dramatically the catalytic reactivity of the Co6Al2 support. Increasing the copper loading did not enhance the catalytic performance of the solids. The addition of copper did not contribute to the enhancement of the reactivity of the different solids. A higher copper loading led to the formation of clusters of copper oxide species that are less reactive in the MSR reaction. Compound 5Cu/Co6Al2 exhibited the best catalytic performance, with no coke deposition after the catalytic test. It appeared that this catalyst favors the WGS reaction, leading to the transformation of CO into CO2.
Acknowledgments
The authors thank the AUF-CNRS-L and the BRG 4/2010 for financial support.