1 Introduction
Currently, the world is facing a number of interdependent challenges: the excessive use of petrochemicals has created severe problems in relation to climate change, local economic dependencies, ecological impact, and sustainability [1–8]. The diminishing of petroleum reserves and growing environmental concerns have motivated researchers for newer approaches to the production of advanced biofuels from biomass as a feedstock. Biomass provides an ideal alternative to fossil resources [1,4,7]. In fact, biomass is the only sustainable source for organic molecules and has been suggested as the ideal comparable to petroleum for the production of biofuels and chemicals [1–4]. It is an abundant, widespread, and inexpensive energy resource resulting from organic substances, which include agricultural residues, forest resources, perennial grasses, woody crops, wastes, algae, etc [9–11]. As a consequence, biomass-derived fuels have attracted attention as alternatives to fossil fuels because of their environmentally benign and renewable nature. In recent years, a significant number of platform molecules have been synthesized from biomass for the production of commodity chemicals and biofuels. Glycerol is one of the most promising renewable platform chemicals for the production of a broad range of commercially significant fine chemicals and biofuel additives. Therefore, the development of new technologies for producing biofuels from sustainable resources has been encouraging biomass utilization to become an important area of research [1,12].
Consequently, glycerol cannot be added to fuel because at high temperatures its polymerization takes place and thereby blocks the engine. In addition, it is partly oxidized to form the toxic acrolein. On the other hand, a major concern of using glycerol as a fuel additive is its very hygroscopic nature and hence has a strong tendency to be contaminated with water. Conversely, glycerol oxygenate products are reported to be excellent fuel additives on the basis of their anti detonant and octane number improving properties. Glycerol can be converted to various fuel additive units through various reaction pathways like esterification, acetalization, etherification, transesterification, hydrogenolysis, and carbonylation [13–22]. The transformation of glycerol into highly oxygenated fuels by esterification and acetalization reactions is of special interest since they are economically viable for the synthesis of glycerol by-products from biodiesel processes.
Esterification of glycerol with acetic acid produces highly important oxygenated biofuel additives, which are generally called as acetins namely, monoacetylglycerol (MAG), diacetylaglycerol (DAG), and triacetylglycerol (TAG). Individually, each acetylated product has its own potential applications in various fields. MAG is used as a food additive, solvent for dyes, and as a tanning agent and is used in the manufacture of explosives [23]. Diacetyl glyceride conjugated with different amino acids shows potential applications in pharmaceutical and food formulations [24]. MAG and DAG are used in the medicine and cosmetic industry and as raw materials for the production of biodegradable polyesters [25]. TAG can be used as a fuel additive to enhance the octane number in gasoline [26]. On the other hand, glycerol esterification with levulinic acid (LA) produces acetylated products which are used as monomers for the synthesis of polymers [27]. Also, esterification with other carboxylic acids such as oleic acid, lauric acid, propionic acid, and butanoic acid with bioglycerol produces acetylated products, which are useful in several industries [28]. The acetalization of glycerol with carbonyl compounds and its derivatives produces highly oxygenated compounds, such as 5-membered and 6-membered cyclic compounds. These highly oxygenated acetals/ketals are used as versatile biofuel additives for diesel fuel. In addition, a remarkable reduction in harmful emissions, unregulated aldehydes and particulate matter can be achieved by adding the glycerol acetals/ketals to the standard diesel fuel [4,15,29].
Generally, esterification and acetalization of glycerol are performed over homogeneous mineral acids such as HCl and H2SO4 as well as other strong acids like p-toluenesulfonic acid [25]. However, the use of these mineral acids is usually limited by several technical and environmental drawbacks such as catalyst separation, use of expensive and toxic reagents, product purity, reactor corrosion, and generation of large amounts of waste [30]. In addition, the costs for the disposal of hazardous substances and related pollution are above the inflation rate in many countries. Hence, the challenge is to replace them with highly efficient heterogeneous solid acid catalysts which are easier to separate from the products, stable at high temperatures and less toxic. Additionally, they have been found to offer better selectivity towards desired products compared to homogeneous catalysts [31]. Solid acids significantly differ from homogeneous catalysts in terms of acidity, surface area, and cost of production. Also, it is economically feasible because of the reusability of the catalyst for both batch and continuous processes [32,33]. Recently, a large number of heterogeneous solid acid catalysts have been developed including hydroxylated magnesium fluorides, sulfated activated carbon, SO3H-functionalized ionic liquids, mesoporous silica with sulfonic acid groups, zeolites, Amberlyst, heteropolyacids, and promoted metal oxides for valorization of bioglycerol to value added products [4,7,15,32,34–37]. In the present article, we report the high production of biofuels by the esterification and acetalization of bioglycerol over highly effective solid acid catalysts from the literature including our catalysts. Presently, we have focused our attention on the production of glycerol esters, acetals, and ketals over various promising solid catalysts.
2 Esterification of bioglycerol with carboxylic acids
2.1 Esterification of bioglycerol with acetic acid
The esterification of glycerol with acetic acid provides three important oxygenated products, namely, MAG, DAG and TAG (Scheme 1). The esterification of glycerol with acetic acid was performed over a wide variety of heterogeneous solid acid catalysts and the obtained results are presented in Table 1. Among the reported catalysts, Amberlyst-70 exhibited a high catalytic performance of glycerol esterification with acetic acid at 378 K reaction temperature and 4 h reaction time [38]. The Amberlyst-70 catalyst exhibited 100% glycerol conversion and the product selectivities of MAG, DAG, and TAG were found to be ∼2.5, 51.7, and 45.8%, respectively (Table 1, entry 1). Zhu and co-workers [39] reported a series of silver-exchanged phosphotungstic acid (Ag1PW) catalysts for the esterification of glycerol with acetic acid at 393 K. Among them, the Ag1PW catalyst showed excellent glycerol conversion (96.8%) with 48.4, 46.4 and 5.2% selectivity of MAG, DAG and TAG, respectively (Table 1, entry 2). It is mainly due to the presence of a high amount of acidic sites and outstanding water tolerance of the Ag1PW catalyst. Recently, Reddy et al. [15] reported promising MoO3, WO3 and 2− promoted SnO2-based acid catalysts for the esterification of glycerol with acetic acid. The 2−/SnO2 catalyst exhibited superior catalytic activity and high product selectivity toward DAG and TAG compared to other catalysts (Table 1, entry 6). The high catalytic activity of the 2−/SnO2 catalyst was mainly attributed to the presence of a large amount of acidic sites with ample super acidic sites. Also, zirconia based catalysts were reported for esterification of glycerol with acetic acid and the obtained results are presented in Table 1. The un-promoted ZrO2 and TiO2–ZrO2 catalysts exhibited lower glycerol conversion than the promoted catalysts such as WOx/TiO2–ZrO2 and MoOx/TiO2–ZrO2 (Table 1, entries 7, 8, 9). The low catalytic activity of un-promoted catalysts could be explained by the less number of acidic sites associated with weak acid strength [13].
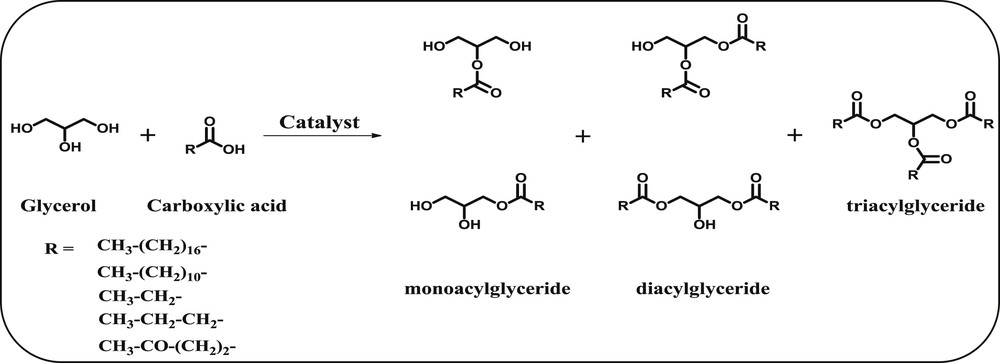
The esterification of glycerol with various carboxylic acids to yield mono-, di- and tri-glycerides.
A comparison study of different acid catalysts for the esterification of bioglycerol with acetic acid.
Entry | Catalyst | T (K) | t (h) | XG (%) | mono/di/tri (%) | Ref |
1 | Amberlyst-70 | 378 | 4 | 100 | 2.5/51.7/45.8 | [38] |
2 | Ag1PW | 393 | 0.25 | 96.8 | 48.4/46.4/5.2 | [39] |
3 | SnO2 | 373 | 2 | 41.6 | 85.2/14.1/0.1 | [15] |
4 | MoO3/SnO2 | 373 | 2 | 66.3 | 81.2/15.7/3.1 | [15] |
5 | WO3/SnO2 | 373 | 2 | 71.5 | 82.2/15.7/2.1 | [15] |
6 | SO4/SnO2 | 373 | 2 | 89 | 73/21.2/5.8 | [15] |
7 | TiO2–ZrO2 | 393 | 3 | 91.5 | 54.7/39.4/5.8 | [13] |
8 | WO3/TiO2–ZrO2 | 393 | 3 | 99 | 53.2/40/6.8 | [13] |
9 | MoO3/TiO2–ZrO2 | 393 | 3 | 100 | 52/40.4/7.6 | [13] |
10 | 2−/12ZrKIL-2 | 373 | 1 | 100 | 2.7/77.1/20.1 | [40] |
11 | HSiW/ZrO2 | 393 | 1 | 96.4 | 28.3/60.5/11.2 | [41] |
12 | HPW/ZrO2 | 393 | 1 | 90.6 | 35.2/56.8/8 | [41] |
13 | HPMo/ZrO2 | 393 | 1 | 88.3 | 37.4/55.8/6.8 | [41] |
14 | Graphene oxide | 393 | 1 | 98.5 | 15.5/60/24.5 | [42] |
15 | 2−/CeO2–ZrO2 | 393 | 1 | 100 | 25.8/57.7/16.5 | [43] |
In recent times, the glycerol acetylation with acetic acid was also studied over the mesoporous KIL-2 supported sulfated zirconia catalyst [40]. It was reported that mesoporous KIL-2 supported zirconia samples are more active when compared to that of pure zirconia. With increasing ZrO2 amount, KIL-2 supported catalysts showed enhanced catalytic performance to produce valuable fuel additives (i.e., MAG and TAG). 2−/ZrKIL-2 catalyst exhibited higher glycerol conversion and better selectivity towards the desired products when compared to ZrKIL-2 catalyst (Table 1, entry 10). This observation can be explained by the presence of 2− ions on the catalyst surface, which improves the Brönsted acidity of the catalyst as well as surface interactions between the acylium moiety of the acetic acid and the OH− ion of glycerol. This reaction was also performed on zirconia supported heteropoly acids such as HSiW/ZrO2, HPW/ZrO2, and HPMo/ZrO2 [41]. All these catalysts showed excellent glycerol conversion with better selectivity towards desired products within a short reaction time (Table 1, entries 11, 12, 13). Among these catalysts, the superior activity of the HSiW/ZrO2 catalyst could be due to the presence of a large amount of Brønsted acidic sites. Very recently, Ga et al. [42] stated that the graphene oxide (GO) is a highly efficient acid catalyst for esterification of glycerol with acetic acid to produce valuable biofuel additives. The GO showed 98.5% glycerol conversion with higher selectivity for DAG and moderate selectivity for MAG and TAG products (Table 1, entry 14). The excellent catalytic activity of GO is associated with the presence of a high amount of SO3H groups and unique morphology. Reddy et al. [43] noted that the 2−/CeO2–ZrO2 catalyst exhibits high glycerol conversion with better selectivity towards DAG and TAG (Table 1, entry 15). From the aforementioned results, we concluded that the concentration as well as the strength of the acidic sites of the catalyst has a significant influence on the esterification of glycerol with acetic acid. Generally, the selectivity of DAG and TAG products was highly influenced by the shifting of reaction equilibrium during the reaction. The shifting of reaction equilibrium towards desired products strongly depends on several factors such as the nature of the catalyst, concentration and strength of acidic sites, excess amount of acetic acid, reaction temperature, reaction time, and removal of water as the by-product in the course of reaction [44].
2.2 Esterification of bioglycerol with levulinic acid
The esterification of glycerol with levulinic acid was studied over mesoporous SBA-15 and SBA-16 materials. In this reaction, three types of products could be generated such as mono-, di- and tri-glycerides (Scheme 2). In the absence of a catalyst, esterification of glycerol with levulinic acid showed very low glycerol conversion (Table 2, entry 1). Gonzalez-Arellano and co-workers [45] reported that the Zr-SBA-16 [46] catalyst provides a moderate conversion of 70% at 393 K in 15 h time with high selectivity for monoacylglyceride and negligible selectivity for diacylglycerides and no selectivity for triglycerides (Table 2, entry 2). Notably, the conversion is improved and reached 99% under identical reaction conditions with increase in the reaction temperature to 413 K, and resulted in higher selectivity for diacylglycerides and triglycerides (Table 2, entry 3). However, the Al-SBA-15 catalyst achieved better glycerol conversion (78%) at 393 K with superior selectivity for monoacylglycerides and negligible selectivity for di- and tri-glycerides [46]. By the increase of reaction temperature to 413 K, the glycerol conversion drastically increased to 99% with excellent selectivity for diacylglyceride (85%) (Table 2, entry 4,5).

The esterification of glycerol with levulinic acid to yield mono-, di- and tri-glycerides.
A comparison study of different acid catalysts for the esterification of bioglycerol with levulinic acid and different acids.
Entry | Catalyst | ACID | T (K) | Time (h) | XG (%) | mono/di/tri (%) | Ref |
1 | Blank | Levulinic acid | 413 | 8 | 20 | 4/66/30 | [45] |
2 | Zr-SBA-16 (25) | Levulinic acid | 373 | 15 | 70 | 77/23/0 | [46] |
3 | Zr-SBA-16 (25) | Levulinic acid | 413 | 15 | 99 | 0/62/37 | [46] |
4 | Al-SBA-15 | Levulinic acid | 393 | 8 | 78 | 94/5/1 | [45] |
5 | Al-SBA-15 | Levulinic acid | 413 | 8 | 99 | 0/85/15 | [45] |
6 | Fe/Al-SBA-15 | Levulinic acid | 393 | 8 | 99 | 0/71/29 | [47] |
7 | Fe/Al-SBA-15 | Levulinic acid | 413 | 8 | 99 | 0/80/20 | [47] |
8 | STA-IL | Oleic acid | 373 | 8 | 96.4 | 96/4/0 | [48] |
9 | LDH | Lauric acid | 453 | 2 | 99 | – | [49] |
10 | LDH | Lauric acid | 373 | 2 | 25 | – | [49] |
11 | Ag1PW | Propionic acid | 393 | 0.15 | 70.9 | 55/43.1/1.9 | [39] |
12 | Ag1PW | 1-Butanoic acid | 393 | 0.15 | 64.3 | 53.9/46/0.1 | [39] |
Gonzalez-Arellano et al. [47] found that the Fe promoted Al-SBA-15 catalyst shows better catalytic activity compared to that of Al-SBA-15 under similar reaction conditions. However, with increasing the reaction temperature to 413 K, the glycerol conversion declined and there is no significant change in the selectivity of di- and tri-glyceride (Table 2 entries 6 and 7). It was also noted that the selectivity of desired products was not influenced by the reaction temperature with the Fe/Al-SBA-15 catalyst. From the above results, one can conclude that esterification of glycerol with levulinic acid is highly dependent on the nature of the catalyst, temperature, and Lewis acidic properties of the catalyst. In addition, esterification of glycerol with other carboxylic acids was also performed over a variety of solid acid catalysts. Recently, Isahak and co-workers [48] studied the esterification of glycerol with oleic acid over silicotungstic acid nanoparticles on ionic liquid (STA-IL) at 373 K for 8 h. This catalyst was found to show excellent glycerol conversion (96.4%) with 96 and 4% selectivity for mono- and di-glycerides, respectively (Table 2, entry 8). The lowest selectivity of di-glyceride could be attributed to more steric hindrance at the secondary hydroxyl group of glycerol. Hamerski et al. [49] reported that the layered double hydroxide (LDH) catalyst shows excellent conversion (99%) for esterification of glycerol with lauric acid at 453 K, whereas 25% of glycerol conversion was attained at 373 K under similar reaction times (Table 2, entries 9 and 10). Esterification of glycerol with propionic acid and 1-butanoic acid was studied by Zhu et al. [39] over the Ag1PW catalyst. This catalyst was found to exhibit better conversion with almost similar selectivity for the desired reaction products at 393 K in a short time period (Table 2, entries 11 and 12). Finally, the natural sources of the levulinic, oleic, lauric, propionic and butanoic acids are provided in Table 3.
List of natural sources of the various carboxylic acids.
Carboxylic acid | Sources |
Levulinic acid | Cane sugar, starch, or cellulose |
Oleic acid | Vegetable and animal fats and oils |
Lauric acid | Coconut oil, laurel oil, and palm kernel oil |
Propionic acid | Propionibacterium and sugars |
Butanoic acid | Milk, butter and parmesan cheese |
2.3 Proposed mechanism for esterification of bioglycerol with carboxylic acids
Zhu et al. [39] proposed a plausible reaction mechanism for the esterification of glycerol with carboxylic acid. The mechanism is preceded through different consecutive steps, firstly, the proton site derived from the Brønsted acid site readily interacts with acid molecules as a result of which protonation of the carbonyl group occurs in the acetic acid molecule and gets a higher positive charge. Subsequently, a nucleophilic attack of the –OH group of the glycerol occurs, which facilitates the formation of a new C–O bond between the carbon atom of the carbonyl group in carboxylic acid and the oxygen atom of the –OH group of glycerol resulting in the formation of an intermediate [50–53]. Hence, a new mono-glyceride molecule can be formed through the elimination of a water molecule. Due to high steric crowding at the secondary hydroxyl group of glycerol it is less feasible for a nucleophilic attack on the acid. Therefore, the formation of secondary mono-glyceride was lower than that of the primary mono-glyceride. In a similar fashion, the obtained mono-glyceride undergoes a further nucleophilic attack leading to the formation of di-glyceride. Finally, the di-glyceride molecule further attacked the carbonyl carbon of acetic acid yielding tri-glyceride.
3 Acetalization of glycerol with carbonyl compounds
Acetalization of glycerol with carbonyl compounds is an acid catalyzed reaction which is carried out by a variety of heterogeneous acid catalysts including zeolites, supported and/or promoted metal oxides or cationic resins, zeolites, SBA-15, and Amberlyst at moderate temperatures and in the presence or absence of solvents. Generally, glycerol acetalisation with simple carbonyl compounds gives two structural isomers, that is, six- (Z and E-1,3-dioxan) and five-membered (Z and E-1,3-dioxolan) cyclic acetals whose proportion depends on the properties of the catalyst, structure of the carbonyl compound and reaction parameters including the temperature, time and molar ratio of reactants (Scheme 3).

The proposed reaction mechanism of glycerol esterification with carboxylic acid.
3.1 Acetalisation of glycerol with acetone
The acetalisation of glycerol with acetone could produce two structural isomers, such as 5-membered ring acetal (Solketal) and 6-membered ring acetal, and water as a byproduct (Scheme 4). Several theoretical and experimental calculations have proposed that the solketal is thermodynamically more stable than the 6-membered isomer because of more steric repulsions provoked by the presence of one methyl group in the axial position of the 6-membered ring acetal [54]. It was proposed that the solketal can be formed selectively through a short-lived tertiary carbenium ion intermediate initiated by the Brønsted/Lewis acidic sites. Subsequently, other studies demonstrated that 6-membered ring acetals are thermodynamically favoured, while 5-membered ring acetals are kinetically favorable [55,56]. Most of the literature studies reported that the acetalization of glycerol with acetone is affected by both Lewis and Brønsted acidic sites; particularly, the Brønsted acidic sites are more active than the Lewis ones [57–60]. Among the mentioned catalysts, the Amberlyst-15 acid resin catalyst exhibited the highest glycerol conversion (95%) within 0.25 h of reaction time. The best catalytic performance is due to the higher amount of acidic sites that are exposed on the surface of the catalyst [60]. From Table 4, entries 1–11, it can be seen that these catalysts show better catalytic performance at high temperatures and less reaction times. Among them, Amberlyst-36 and S-Sn-OH catalysts were found to show higher glycerol conversion and selectivity for the solketal product, which might be due to the presence of more number of acidic sites [29,47,57,59–63]. The zeolite ZSM-5, H-ZSM-5, and zeolite beta solid acids have shown poor catalytic performance, which is explained by their narrow pore structure, which probably does not permit the acetalization to occur inside the pores (Table 4, entries 6, 18, and 19) [62]. Da Silva et al. [60] showed a glycerol acetalization with acetone over the Amberlyst-15 acid resin catalyst with 95% of glycerol conversion at 343 K for 0.25 h (Table 4, entry 22). Zeolite-beta and K-10 montmorillonite catalysts were examined under similar reaction conditions, which showed ∼60% of glycerol conversion after 1 h (Table 4, entries 19 and 20). Reddy et al. [4,7,14] reported that the superior catalytic performance of the promoted SnO2 and ZrO2 based catalysts is due to the presence of an increased amount of acidic sites, and a high specific surface area associated with the large pore volume, accompanied by notable redox properties (Table 4, entries 12–16). Interestingly, a high selectivity of solketal (>96%) was obtained irrespective of the catalyst used. From these studies, one can strongly emphasize that the better catalytic performance of various catalysts might be due to the presence of more number of acidic sites on the catalyst surface. Finally, we concluded that the glycerol conversion was strongly affected by the nature of the catalysts as well as the reaction conditions, whereas there is no significant role played by the nature of the catalyst and reaction conditions towards the selectivity of the products.
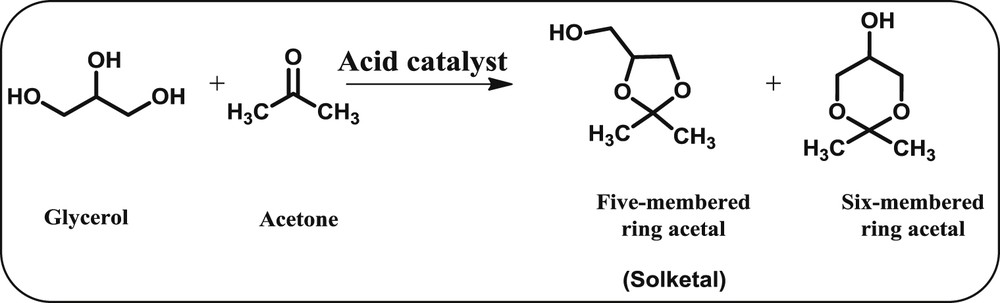
The acetalization of glycerol with acetone to yield 5-membered (solketal) and 6-membered cyclic ketals.
A comparison study of different acid catalysts for the acetalization of bioglycerol with acetone.
Entry | Catalyst | Temperature (K) | Time (h) | XG (%) | XS (%) | Ref |
1 | AC-S-18M | 323 | 6 | 65 | 98 | [62] |
2 | Sn-SBA-15 | 353 | 6 | 65 | 99 | [57] |
3 | Fe/Al-SBA-15 | 373 | 8 | 58 | 99 | [47] |
4 | Amberlyst-36 | 313 | 8 | 88 | 98 | [63] |
5 | Nb2O5 | 343 | 6 | 80 | 98 | [29] |
6 | H-ZSM-5 | 353 | 6 | 24 | 99 | [61] |
7 | HSC-SO3H | 353 | 6 | 79 | 99 | [61] |
8 | Sn-MCM-41 | 353 | 6 | 42 | 99 | [61] |
9 | SBA-15-SO3H | 353 | 6 | 44 | 99 | [61] |
10 | S-Sn-OH | 353 | 6 | 84 | 99 | [66] |
11 | Ar-SBA-15 | 343 | 2 | 80 | 99 | [57] |
12 | SnO2 | RT | 1.5 | 15 | 96 | [7] |
13 | MoO3/SnO2 | RT | 1.5 | 61 | 96 | [7] |
14 | 2−/SnO2 | RT | 1.5 | 70 | 96 | [4] |
15 | ZrO2 | RT | 1.5 | 10 | 97 | [14] |
16 | 2−/ZrO2 | RT | 1.5 | 98 | 97 | [14] |
18 | PTSA | 343 | 0.50 | 80 | 99 | [60] |
19 | Zeolite ZSM-5 | 343 | 0.6 | 20 | 99 | [60] |
20 | Zeolite beta | 343 | 1 | 60 | 99 | [60] |
21 | K-10 | 343 | 1 | 60 | 99 | [60] |
22 | HUSY | 343 | 0.6 | 60 | 99 | [60] |
23 | Amberlyst-15 acid resin | 343 | 0.25 | 95 | 99 | [63] |
3.2 Acetalization of glycerol with different carbonyl compounds
Generally, the carbonyl compounds are classified into two functional groups, which are aldehydes and ketones. In this article, we have discussed the glycerol acetalization with different aldehydes like benzaldehyde, furfural, formaldehyde, acetaldehyde, butanal and long chain alkyl aldehydes to produce oxygenate fuel additives for diesel engines (Scheme 5). A variety of homogeneous and heterogeneous Bronsted and Lewis acid catalysts have been explored to carry out this reaction with different degrees of success. Wang et al. [64] reported a better catalytic activity for the acetalisation of glycerol with acetaldehyde and butanal over the [BPy]HSO4 catalyst (Table 5, entries 5 and 6). The elevated performance of this catalyst was due to the micro water-removing system constituted by ionic liquid that benefits its solubility, in which the water could be removed from the reaction mixture, shifting the reaction equilibrium towards the products. However, the acetalisation reaction of glycerol with formaldehyde performed in the presence and/or absence of a solvent over the Amberlyst-36 catalyst achieved a maximum conversion of 77% and 56%, respectively (Table 5, entry 1) [65]. It is evident that the acetalisation of glycerol is more difficult in the absence of a solvent because of the strong adsorption of polar reactants on the catalyst surface which deactivates the active sites.
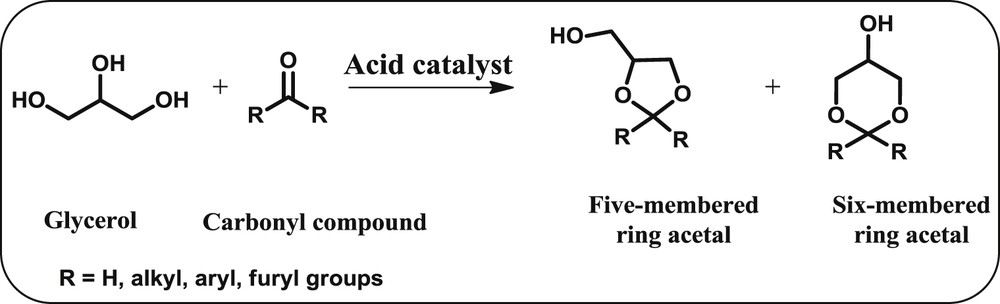
The acetalization of glycerol with different carbonyl compounds to yield 5-membered and 6-membered cyclic acetals/ketals.
A comparison study of various acid catalysts for the acetalization of bioglycerol with carbonyl compounds.
Entry | Aldehyde | Catalyst | T (K) | Time (h) | XG (%) | XS5/XS6 (%) | Ref |
1 | Formaldehyde+ CHCl3 | Amberlyst-36 | 333 | 6 | 77 | 76/24 | [65] |
2 | Formaldehyde | AuCl3 | 353 | 4 | 83 | 63/37 | [68] |
3 | Formaldehyde+ dioxane | AuCl3 | 353 | 4 | 93 | 63/37 | [68] |
4 | Acetaldehyde | [BPy]HSO4 | 298 | 2 | 95.6 | 39.4/56.2 | [64] |
5 | Butanal | [BPy]HSO4 | 298 | 2 | 96.8 | 38.7/58.3 | [64] |
6 | Heptanal+ dioxane | AuCl3 | 298 | 0.5 | 93 | 34/66 | [68] |
7 | Heptanal+H2O | AuCl3 | 298 | 0.5 | 85 | 46/54 | [64] |
8 | Benzaldehyde+ CHCl3 | Amberlyst-36 | 333 | 4 | 94 | 61/39 | [65] |
9 | Benzaldehyde+ CHCl3 | HBeta (Si/Al = 25) | 333 | 6 | 94 | 59/41 | [65] |
10 | Benzaldehyde | MoO3/TiO2–ZrO2 | 373 | 0.5 | 74 | 51/49 | [16] |
11 | Benzaldehyde+ toluene | MoO3/TiO2–ZrO2 | 373 | 0.5 | 74 | 50/50 | [16] |
12 | Benzaldehyde | 2−/SnO2 | RT | 0.5 | 77 | 41/59 | [15] |
13 | Benzaldehyde | MoO3/SiO2 | 373 | 8 | 72 | 40/60 | [66] |
14 | Furfural | MoO3/SnO2 | RT | 0.5 | 75 | 66/34 | [7] |
15 | Furfural | 2−/SnO2 | RT | 0.5 | 82 | 68/32 | [4] |
16 | Furfural | ZnCl2 | 373 | 0.5 | 75 | – | [67] |
17 | 2,4-Dimethyl-3-pentanone | [Cp*IrCl2]2 | 373 | 1 | 14 | 100/0 | [70] |
18 | Cyclohexanone | [Cp*IrCl2]2 | 333 | 1 | 76 | 97/3 | [70] |
19 | Acetophenone | [Cp*IrCl2]2 | 353 | 1 | 56 | 96/4 | [70] |
20 | Benzophenone | [Cp*IrCl2]2 | 373 | 1 | – | – | [70] |
Deutsch et al. [65] developed Amberlyst-36 and beta-zeolite to perform the acetalization of glycerol with benzaldehyde in the presence of chloroform to attain 94% of glycerol conversion. As well, Reddy and co-workers [16] also reported that the MoO3 promoted TiO2–ZrO2 catalyst shows high glycerol conversion with excellent yield of the acetal product in the presence and absence of the solvent. In the solvent-free case, the MoOx/TiO2–ZrO2 catalyst showed better glycerol conversion (74%), which is explained by the addition of MoOx species to the TiO2–ZrO2 support that improves the surface acidic properties of the catalyst. The MoO3/SiO2 catalyst was also investigated successfully for the acetalization of glycerol with benzaldehyde. The maximum glycerol conversion reached ∼78% and selectivities of 5- and 6-membered acetals were found to be 60 and 40%, respectively (Table 5, entry 14) [66]. Recently, we designed a highly efficient 2− ion promoted SnO2 solid acid catalyst for the acetalization of glycerol with furfural and benzaldehyde under solvent-free conditions at room temperature. It was found that the addition of 2− ions to SnO2 increases its activity performance mainly due to the existence of a large amount of acidic sites associated with the super acidic sites [4,7,15]. Homogeneous Lewis acids such as AuCl3 and ZnCl2 have been extensively studied for the acetalization of heptanal and furfural, respectively (Table 5, entries 7, 8, and 17). Particularly, AuCl3 showed an excellent activity for the acetalization of glycerol with heptanal in the presence of water or dioxane as the solvent [67–69].
The study of glycerol ketalization was extended to various ketones, including 2,4-dimethyl-3-pentanone, acetophenone, benzophenone and cyclohexanone and the obtained results are reported in Table 5 (entries 17–20). The reaction between 2,4-dimethyl-3-pentanone and glycerol results in lower glycerol conversion (14%) over the [Cp*IrCl2]2 catalyst [70]. There was no conversion with benzophenone, which is due to the more steric hindrance of the benzophenone molecule. Conversely, glycerol acetalization with cyclohexanone exhibited a significant glycerol conversion with excellent selectivity of 5-membered ketal (97%). In all the cases, the selectivity of five-membered ketal was more than 97%, which is comparable to those obtained in the reaction with acetone.
3.3 Reaction mechanism
Based on the reports in the literature, a plausible reaction mechanism is proposed for acid catalyzed acetalization of glycerol with acetone as given in Scheme 6 [4,57,66,69]. In the first step, the positively charged carbonyl carbon of the carbonyl compound is formed due to the existence of a strong interaction between the oxygen atom of the carbonyl group and acidic sites of the catalyst. In the second step, the formed carbocation will be immediately attacked by the –OH group of the glycerol to produce the intermediate hemiacetal, which finally affords two isomeric cyclic acetals by different pathways. Calvino-Casilda et al. [55] provided the evidence for the formation of the tertiary alcohol intermediate during the reaction. Afterwards, this intermediate undergoes cyclization by the attack of the lone pair of electrons present on the adjacent hydroxyl group to the tertiary carbon atom leading to the formation of 5-membered acetal (a). On the other hand, the attack of the lone pair of electrons on the terminal hydroxyl group to the tertiary carbon atom leads to the formation of 6-membered acetal (b) with the elimination of a water molecule in the last step.
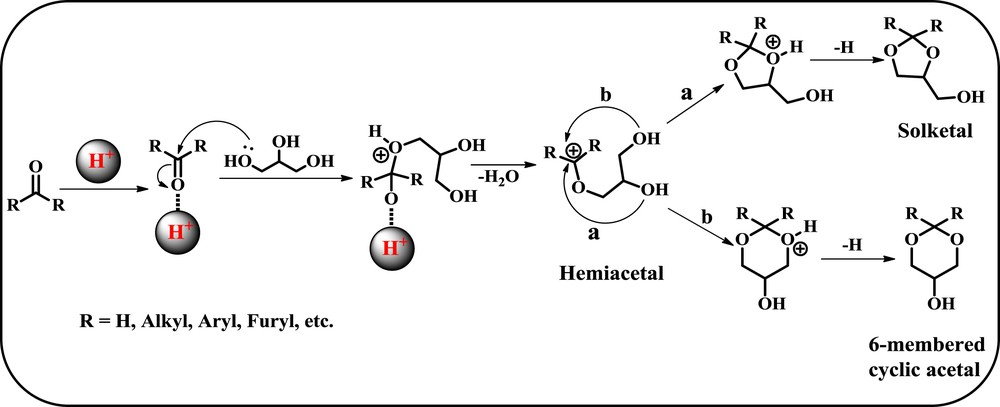
Plausible reaction mechanistic pathway of glycerol acetalization with carbonyl compounds.
4 Conclusion
The production of biofuel additives is an emerging field, which is still awaiting consolidation and rationalization. In this review, we reported the results of highly efficient catalysts for the production of highly oxygenated biofuel additives via esterification and acetalization of bioglycerol. For both the reactions, shifting of reaction equilibrium plays a key role in controlling the selectivity of the desired products during the reaction. Shifting of reaction equilibrium towards products is associated with various parameters including the nature of the catalyst, high concentration and superior strength of acidic sites, reaction temperature, reaction time, and the removal of water as a by-product in the course of the reaction. The acetalization of glycerol with acetone is highly promoted by Brønsted acidic sites than Lewis acidic sites. The high catalytic performance of reported acid catalysts for both the reactions is mainly due to the high concentration and superior strength of the acidic sites.
Acknowledgements
BM and BGR thank the Council of Scientific and Industrial Research (CSIR), New Delhi for research fellowships.