1 Introduction
Atmospheric sulfur emission is a significant environmental problem and has been dealt with through regulation of sulfur in transportation fuels. Liquid fuels (crude oils) contain a large variety of sulfur compounds (thiols, sulfides, disulfides and thiophenes) which generate sulfur oxides and airborne particulate emissions during combustion. Reduction of sulfur emissions is considered a primary means of improving air quality. Sulfur removal is thus an important process in the cleanup of transportation fuels. Besides being an environmental pollutant, sulfur is a poison to reformer catalysts as well as fuel cell electro-catalysts. Standards developed by the European Committee for Standardization mandate a maximum sulfur content of 10 ppmw [1].
Hydrodesulfurization (HDS) is the most important and common industrial process for treating the fuel at high temperatures and high pressures with hydrogen to produce H2S [2–5]. However, the HDS process is expensive, thereby making the final fuel product expensive; it is also not effective in reducing refractory organosulfur compounds such as benzothiophenes (BTs) and dibenzo[b,d]thiophenes (DBTs). The oxidative desulfurization (ODS) technique is a promising and future technique for eliminating sulfur from fuels. This process operates under mild conditions. Several desulfurization studies have been reported using this technique. Over the last few years, oxidation of sulfur-containing compounds has been carried out by employing various metal complexes as catalysts: Ti [6–17], V [18–23], W [24–30], Mo [31,32], Co/Mn [33], Ag [34], Au [35], Re [36] and Mn [37].
Herein, a V(IV) metal complex immobilized on polymer microspherical beads {poly[VO(allylSB-co-EGDMA)]} [38] was employed for the oxidation of the aromatic fraction of heavy fuel oil via a batch process. The potential use of oxidative desulfurization in the aromatic fraction of heavy fuel oil was explored to understand the viability of this technique in fuel processing.
2 Experimental
2.1 Materials
A crude oil sample was provided by Nigerian National Petroleum Co-operation (NNPC), Nigeria. Total sulfur in diesel standard was purchased from Matheson Tri-Gas, Texas, USA. Hexane (99.9%, HPLC grade), methanol (99.9%, HPLC grade), acetonitrile (99.9%, HPLC grade) dichloromethane (99.9%, HPLC grade), pentane (99.9%, HPLC grade) and toluene (99.9%, HPLC grade) were procured from Merck chemicals (South Africa) and tert-butyl hydroperoxide (t-BuOOH), 97% was purchased from Sigma–Aldrich, Germany.
2.2 Instrumentation
A gas-chromatrography-flame ionization detector (GC-FID), an atomic emission detector (-AED) and a mass spectrometer (-MS) were started at an oven temperature of 45 °C ramped to 150 °C at 10 °C min−1 and then held for 5 min, and then increased to a final temperature of 320 °C at a rate of 20 °C min−1, and were further maintained at 320 °C for 2 min. The AED detector for sulfur analysis was set at a wavelength of 181 nm and the carbon analysis wavelength was 179 nm, while the transfer line temperature of 350 °C and block cavity temperature of 320 °C were used.
2.3 Column chromatography
2.3.1 Fractionation
The heavy crude oil sample was fractionated into Asphaltenes, Resins, Aromatics and Saturates (SARA). Separation of the heavy oil sample was carried out in a column packed with silica gel as reported by Jewell et al. [39], Ogunlaja et al. [40] and Shi et al. [41].
0.5 g of crude oil was dissolved in 10 mL of pentane and allowed to stand for 4 h and then centrifuged at 10 000 rpm for 30 min to separate the pentane soluble fraction from the asphaltenes. The fractionation was carried out in a column (about 2–3 cm in diameter) packed with 14 g of silica gel. For this purpose, the column was conditioned with 5 mL hexane. Elution was carried out by using 25 mL of hexane for saturates and 25 mL of dichloromethane for aromatics and 25 mL mixture of dichloromethane:methanol (1:1) was used to elute the resins. Drying of the various fractions was done in a fume hood by bubbling nitrogen gas in the sample vials. The weight percentage of each fraction eluted is presented in Table 1. The aromatic fraction of the heavy fuel oil was of interest and was analyzed using elemental analysis, Fourier transform-infrared spectroscopy (FTIR) and a gas-chromatography-mass spectrometer (GCMS).
Elemental microanalyses of the aromatic and saturate fractions of the heavy fuel oil.
Fuel oil | Fractions | wt (%) | |||
C | H | N | S | ||
Heavy | Saturates | 83.17 | 16.26 | – | – |
Aromatics | 84.50 | 12.61 | 0.03 | 1.792 |
2.4 Catalytic oxidation procedure
Equivalent mass (0.20 g) of heavy fuel oil (∼17 920 ppmw S) was dissolved in 10 mL of a solution of toluene, after which an aqueous solution of tert-butyl hydroperoxide (t-BuOOH) {oxidant:sulfur (10:1)} and poly[VO(allylSB-co-EGDMA)] (0.144 g, 0.0810 mmol) was added. The mixture was transferred into a 25 mL round bottom flask while stirring at 250 rpm in an oil bath at 70 °C. Products of the oxidation reaction were analyzed using a gas-chromatrography-flame ionization detector (GC-FID), an atomic emission detector (-AED) and a mass spectrometer (-MS).
2.5 Adsorption studies of oxidized fuel oil
The method has been reported by us previously, [42] with a slight modification. Adsorption attempts on 1 mL oxidized fuel oil (17 920 ± 100 ppmw S) were carried out by using imprinted polybenzimidazole nanofibers (150 mg) under a continuous adsorption process at a flow-rate of 1 mL h−1. Conditioning of adsorbents was carried out by pre-wetting adsorbents with solvents employed in dissolving the oxidized fuel oil.
The adsorption capacity, qe (mg g−1), was calculated from Eqn. 1.
(1) |
3 Results and discussion
3.1 Elemental analysis
Microanalysis data for the saturate and aromatic fraction of the heavy fuel oil are presented in Table 1. From the elemental analysis, a total sulfur concentration of 17 920 ppmw S is available in the heavy fuel oil. Mass spectroscopy fragmentations of some of the identified sulfur-containing compounds such as naphtho-[2,1-b]thiophene, naphtho-[2,3-b]thiophene, dibenzo[b,d]thiophene, 4-methyldibenzo[b,d]thiophene and 7-methyl-1-benzothiophene are provided in Figs. S2–S6. Prior to oxidation, the sulfur in fuel was re-quantified by employing sulfur standards in diesel produced by Matheson Tri-Gas which have direct traceability to NIST-SRM 2723a/SRM 2770. Sulfur 181 nm of the various sulfur standards in diesel concentrations is displayed in Fig. S7. Other properties and characterization of the heavy fuel oil are reported in our earlier publication [40].
3.2 Fourier transform-infrared spectroscopy (FTIR)
C–H stretch of a methyl and methylene groups was observed around 2960 and 2920 cm−1, respectively. The ν(O-H) and ν(R-NH-R) were observed in the aromatic fraction of the heavy fuel oils around 3330–3420 cm−1. Most important sets of bands for the aromatic ring vibrations are centered around 1650 to 1550 cm−1, and this usually occurs as a pair of band structures, often with some splitting. Thiol (C–S) stretching vibrations tend to give rise to strong absorptions at 721 cm−1 in the infrared spectrum. The FTIR spectrum of the aromatic fraction of heavy fuel oils is presented in Fig. S1. The vibrational region around 1450 cm−1 is ascribed to the aromatic ring stretch (CCC). A series of weak bands between the regions 1200–950 cm−1 can be attributed to the substitution patterns of aromatic –C–H (in plane deformation). The bands in the region 860–690 cm−1 can be attributed to –C–H out of plane deformation and are very useful for identifying polycyclic compounds [43].
3.3 Oxidation of the aromatic fraction of the heavy fuel oil
From the results obtained (GC-AED chromatogram, Fig. 1), most of the sulfur compounds, predominantly refractory organosulfur compounds, dibenzo[b,d]thiophene and methylated dibenzo[b,d]thiophene were converted to their respective sulfone compounds after 5 h of oxidation. A shift in the retention time of the GC-AED sulfur chromatogram of the oxidized heavy fuel oil was observed (Fig. 1). Mass spectroscopy fragmentations of some of the identified oxidized sulfur-containing compounds such as dibenzo[b,d]thiophene sulfone, 4-methyldibenzo[b,d]thiophene sulfone and 7-methyl-1-benzothiophene sulfone are provided in Figs. S8–S10. The oxidation reaction also led to the formation of stable organic peroxide, di-tert-butyl peroxide, which is an interesting fuel source as it provides oxygen for combustion. UV/Vis studies reported in our previous publication [21] showed that the catalyst oxidovanadium(IV) hosted onto a polymer support produces intermediate species during the catalytic oxidation process; the oxidation of oxidovanadium(IV) led to the formation of dioxidovanadium(V) and oxidoperoxido species followed by its protonation to form the hydroxyl-peroxidovanadium(V) species (Scheme 1). Interaction between the sulfur atom of organic compound, e.g., 4-methyldibenzo[b,d]thiophene and an oxygen atom of the hydroxyl-peroxidovanadium(V) species resulted in bond formation, therefore giving rise to the formation of 4-methyldibenzo[b,d]thiophene sulfone (Scheme 1).
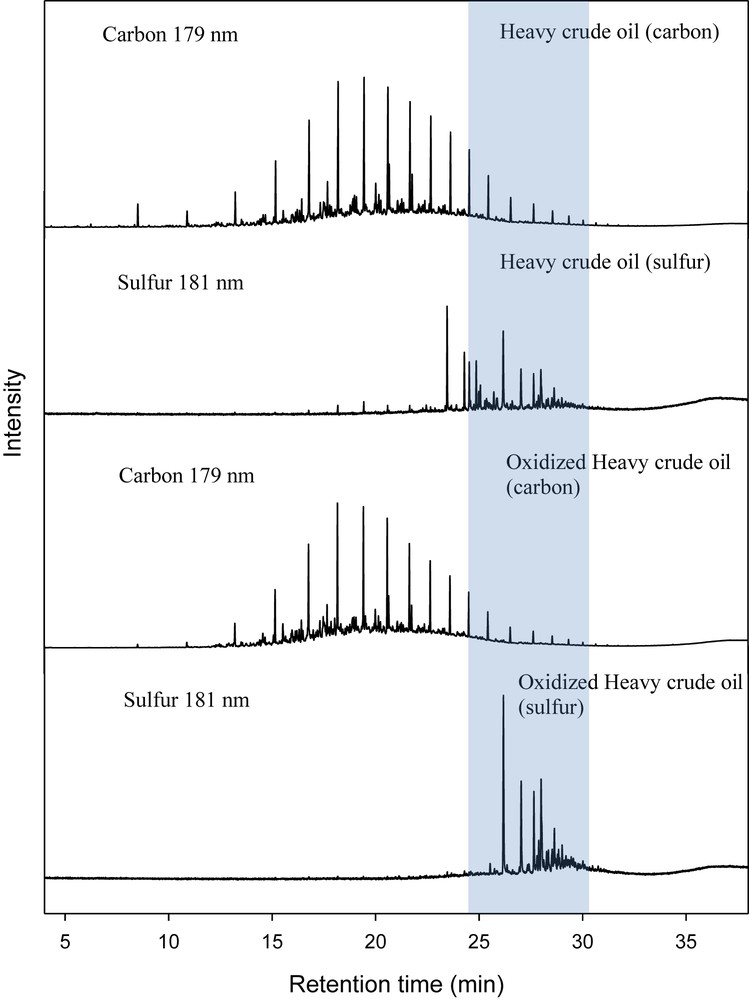
GC-AED chromatograms of carbon at 179 nm and sulfur at 181 nm for heavy fuel oil before oxidation, and carbon and sulfur chromatograms of oxidized heavy crude oil after oxidation while using poly[VO(allylSB-co-EGDMA)] as the catalyst.
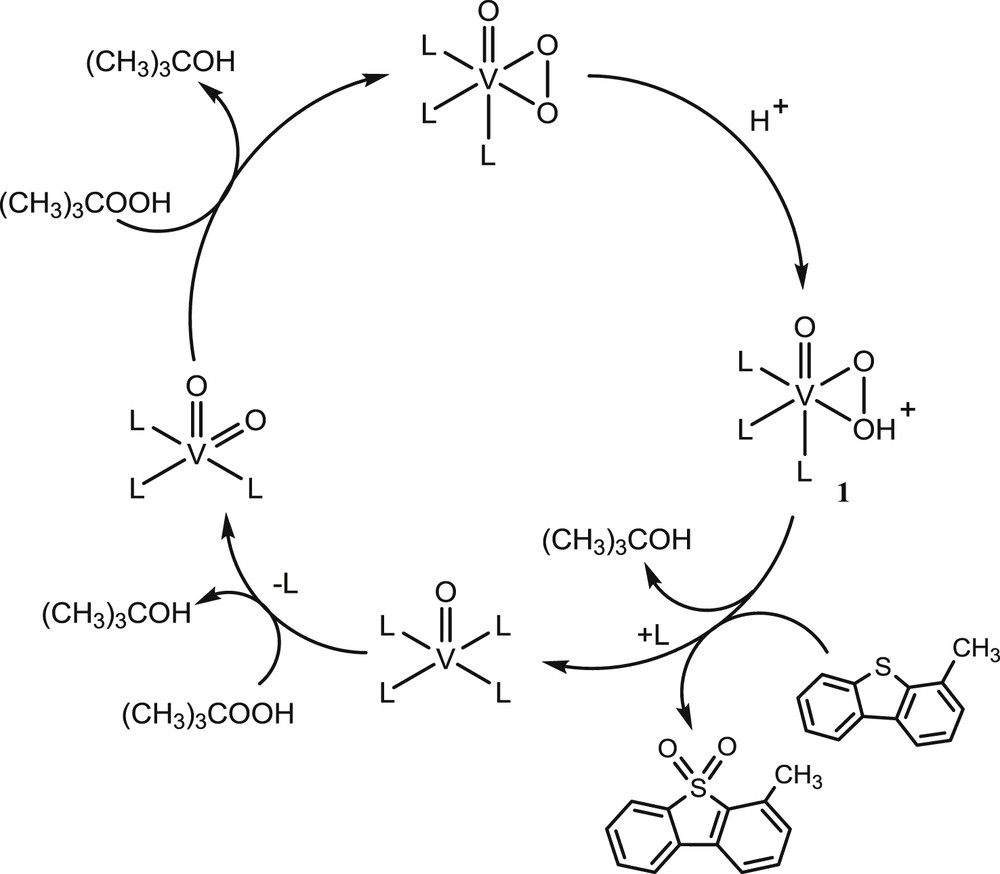
Simplified catalytic mechanism for the oxidation of 1-methyl dibenzothiophene sulfone. H+ from the alcohol (tert-butyl alcohol) may protonate peroxido to form the hydroxyl-peroxidovanadium(V) species (1). Here L may refer to the donor atom.
While a shift in the retention time of some aromatic sulfur compounds depicts oxidation, however, some sulfur compound retention time remained unchanged, confirming the presence of some un-oxidized sulfur compounds such as thiophene and its derivatives.
The oxidation of the oil also led to the formation of some undesired compounds such as carboxylic acids and peroxides which were not detected in the initial oil fraction prior to oxidation (Figs. S11–S12). Hence, the oxidant-to-sulfur ratio must be optimized to avoid the generation of undesired products.
3.4 Adsorption of oxidized heavy fuel oil using imprinted PBI nanofibers
Imprinted polybenzimidazole (PBI) nanofibers synthesized according to the method reported by Adeniyi et al. [42] were employed for the adsorption of the oxidized sulfur compounds. Molecular imprinting of polymers is originally defined as a technique employed for the introduction of recognition sites into polymeric matrices via the formation of bonds between the imprinting molecule (template) and functional groups within the polymer network [42,44].
Fabrication of imprinted polybenzimidazole nanofibers adopted for the adsorption of oxidized heavy fuel oil as reported by Ogunlaja et al. [42] is described as follows: polybenzimidazole (PBI) solution was prepared by dissolving 2.0 g of pristine PBI polymer in 10 mL N,N-dimethylacetamide containing 0.4 g (4% wt) LiBr under reflux conditions in a nitrogen atmosphere for 4 h. The resulting viscous solution was cooled, and filtered to remove any particulates. 1 mL (0.01 M) acetonitrile solution of respective model sulfone compounds containing 40 μL Triton X-114 (surfactant agent) was added to the dissolved PBI polymer, after which the mixture was further stirred at 50 °C for 5 h to form a homogeneous blend. The polymer solution was transferred into a 25-mL syringe and electrospun by using the following optimised electrospinning conditions: a voltage of 25 kV at a flow rate of 0.4 mL/h, and a distance between the needle tip and collector plate placed at 20 cm. The resulting nanofibers were subjected to an extensive washing process using a mixture of acetonitrile and methanol (1:1) via Soxhlet extraction to the remove residual solvent (DMAc) and entrapped template (model sulfone compounds). The washed nanofibers were later dried overnight at an oven temperature of 60 °C. LiBr (about 4% by weight) was employed for polymer dissolution as it increases solution electrospinability.
GC-AED chromatograms after passing through polybenzimidazole-imprinted nanofibers showed that a total of 8900 ± 200 ppmw sulfur was left in the oxidized heavy crude oil (Fig. 2). The saturated sulfur adsorption capacity of the molecularly imprinted PBI nanofibers was 60.2 ± 6.9 mg/g.
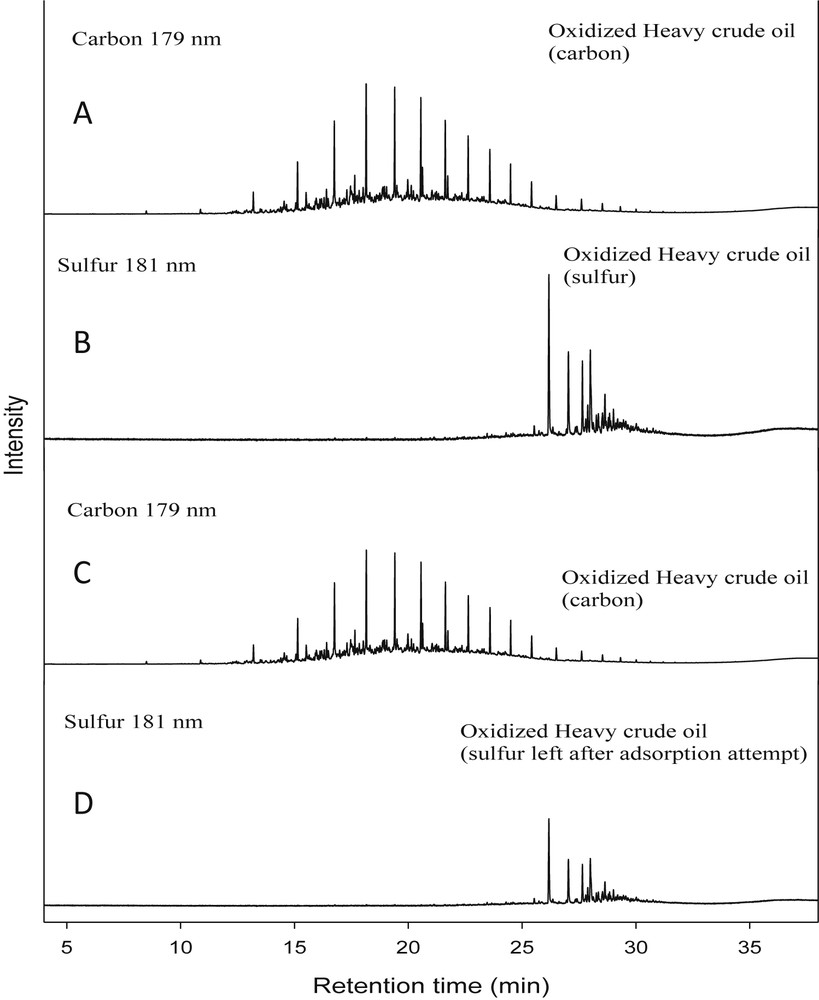
GC-AED chromatograms of carbon (A) at 179 nm, and sulfur (B) at 181 nm in oxidized heavy crude oil, and chromatograms of carbon (C) at 179 nm and sulfur (D) at 181 nm in oxidized heavy fuel oil after using imprinted-PBI nanofibers as the adsorbent.
The imprinted adsorbents exhibited conformational memory for recognizing sulfones. Adsorption via imprinted-PBI nanofibers was possible due to (i) hydrogen bond formation through the interactions between sulfone oxygen groups with NH groups of the PBI (Fig. 3) and (ii) aromatic stacking of π–π interactions between sulfone compounds and PBI [42].
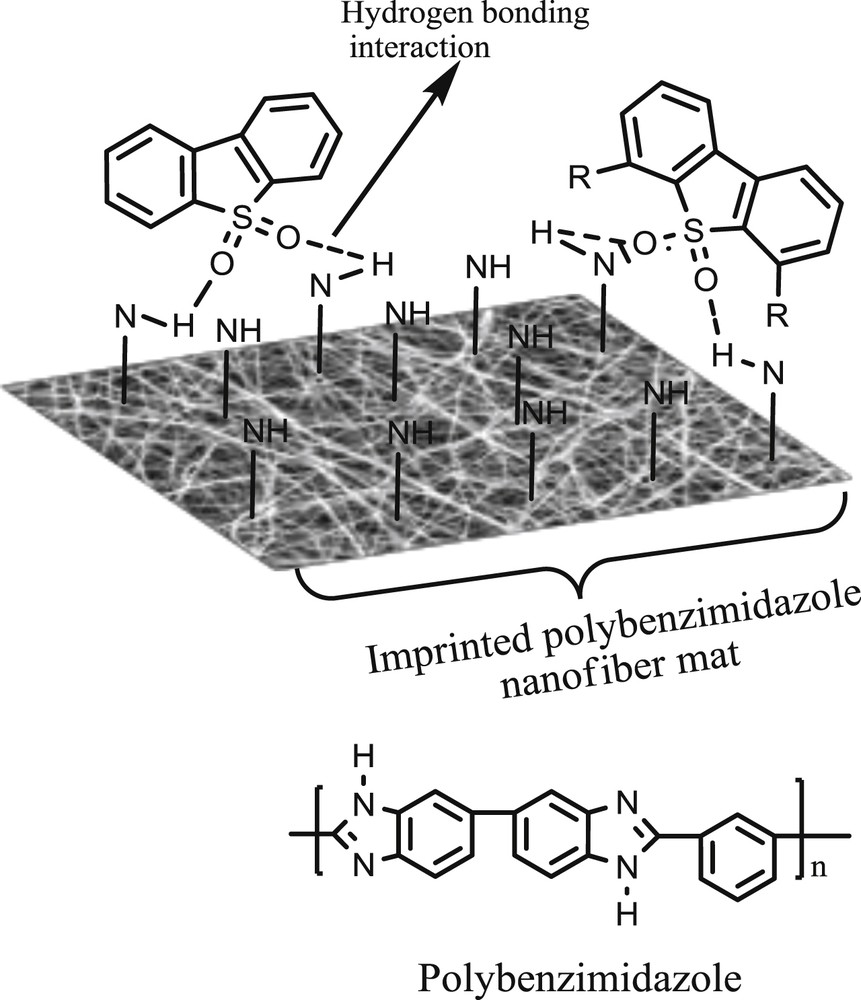
Proposed hydrogen bonding interaction between polybenzimidazole and sulfones (inset: polybenzimidazole structure).
4 Conclusions
Refractory organosulfur compounds in heavy fuel oil (aromatic fraction) were oxidized using poly[VO(allylSB-co-EGDMA)] as a catalyst to convert sulfur to polar sulfones. The resulting organosulfones were adsorbed via the use of fabricated molecularly imprinted polybenzimidazole nanofibers. The organosulfur compounds in the aromatic fraction of the heavy fuel oil after the oxidation/adsorption fell below 8900 ± 200 ppmw S from the initial value of 17 920 ± 100 ppmw S. Hydrogen bonding as well as π–π aromatic interactions between polybenzimidazole nanofibers and sulfone may be responsible for the adsorption mechanism.
Acknowledgements
We are thankful for financial support provided by Sasol (Pty) Ltd. The South African National Research Foundation (NRF) is also acknowledged for funding A.S. Ogunlaja (Green Economy Postdoctoral Scholarship).