1 Introduction
Coal fly ash (FA) is an industrial by-product which is generated during energy production through coal combustion. FA mainly consists of SiO2, Al2O3 and Fe2O3, but also contains potentially toxic elements such as heavy metals from coal and polyaromatic hydrocarbons that condense from the flue gas. The large-scale disposal and storage of FA is a source of air, soil and water pollution [1]. In order to minimize its disposal as wastes, FA has been used to treat acid mine drainage [2,3], to synthesize zeolites [2,4,5], as construction materials [1], or to recover valuable metals [6,7]. Two processes for alumina recovery from FA were developed in the seventies in Poland [8]. Nowadays, many processes such as sintering, acid leaching and HiChlor for alumina recovery from FA have been developed [9]. Regarding coal FA, Liu et al. reported the recovery of 70–90 % of the total alumina content from coal fly ash using acid sintering-leaching process with concentrated sulphuric acid [7]. Iron oxides can also be recovered from FA through magnetic extraction upon acidic treatment with aqueous sulphuric acid or hydrochloric acid [10,11].
Fly ash has been used as a low cost source of SiO2, Al2O3 in the synthesis of zeolites [12]. For such syntheses, the conventional alkaline hydrothermal process could be applied, but after fusion or pectization of the raw material [4,13]. Under such conditions, A, X, NaP1 and cancrinite zeolites have been successfully prepared from South African coal FA by Musyoka et al. [4,12].
The extraction of alumina from FA obviously leads to an increase in the Si/Al ratio of the solid residue, which might be a good starting material for the synthesis of high silica containing zeolites such as ZSM-5 (Si/Al ≥ 11) [14]. ZSM-5 zeolite, having the MFI topology with high silica content, exhibits a three-dimensional medium-sized pore structure, high temperature stability and strong acidity. It is a well-established catalyst for several petrochemical processes such as cracking, alkylation, acylation, disproportionation, isomerisation, etc. ZSM-5 zeolite is conventionally synthesised using various types of organic structure-directing agents [14–17]. However, Narayanan et al. reported that ZSM-5 could be synthesised without templates [18]. Chareonpanich et al. prepared ZSM-5 zeolite using lignite FA and rice husk ash as feedstocks, with tetrapropylammonium bromide (TPABr) as a template [5]. Kalyankar et al. obtained ZSM-5 zeolite using FA obtained from a thermal power station in India [19].
The conversion of methanol into hydrocarbons (MTH) for producing high-octane gasoline was discovered in Mobil laboratories in the 70s. This process now represents a valuable technology, based on acid-catalysed reactions, which is commercialised: for instance, the Topsøe integrated gasoline synthesis (TIGAS) process, the Lurgi methanol to propene (MTP) process and the Norsk Hydro/UOP's methanol to olefins (MTO) process [20]. For the latter process, Chang et al. [21c] reported that an increase in the Si/Al ratio led to an enhancement of the MTO catalyst activity. Furthermore, other key parameters that affect an MTO catalyst need to be controlled: crystal size, crystallinity and, as aforementioned, the intrinsic acidity in terms of density as well as strength [21]. It is therefore a challenge to transform a very complex waste material into a heterogeneous catalyst with tailored properties. Lastly, an interesting perspective for the study is the potential applicability of FA ZSM-5 zeolite, for instance, in China where Coal-To-Methanol processes are industrialized [21e]. Indeed, it is desirable that FA generated by the latter processes could be valorised in the design of an MTO catalyst.
Our study aims to show the potential use of South African coal fly ash as a cheap source for the extraction of metals and the synthesis of ZSM-5 zeolite, which is tested as an acid catalyst in the MTO reaction.
2 Experimental
2.1 Materials
Sulphuric acid (H2SO4, 95–99%) was purchased from Merck. Tetrapropylammonium bromide (TPABr), methanol (99.8%), chloroform-d (CDCl3, 99 atom % D), chloroform (CHCl3, ≥99.9%), oxalic acid (H2C2O4, ≥99%) and fumed silica were obtained from Sigma-Aldrich. Sodium hydroxide (NaOH, pearls, 97%) was purchased from Kimix Chemical and Laboratory Supplies. Ammonium nitrate (NH4NO3) was obtained from Sigma–Aldrich. A commercial ZSM-5 zeolite (H-ZSM-55524) was purchased from Zeolyst. Fly ash (FA) was obtained from the Arnot coal power plant located in the Mpumalanga province of South Africa.
2.2 Acid leaching of fly ash and iron extraction
The acid leaching method used in this study was adapted from the method proposed by Liu et al. [7]. Fly ash (30 g) was mixed with 60 mL of concentrated sulphuric acid in a digestion vessel, which was placed in a pre-heated oven at 250 °C for 4 h. Scheme 1 summarizes the different steps involved in the chosen strategy. Thereafter, the obtained acid slurry was mixed with 180 mL of deionised water in a 500 mL beaker. The mixture was heated at 85 °C under stirring for 30 min, hot filtered and the FA residue was washed three times with 100 mL boiling deionised water. The filtrate was retained to recover Al. The black magnetic extract (magnetic extract) that accumulated onto the magnetic bar during stirring was collected and dried overnight at 60 °C. The solid FA residue, named PL, was dried overnight in an oven at 80 °C and used in the synthesis of ZSM-5 zeolite.

From fly-ash to valuable alumina or zeolite materials.
2.3 Extraction of aluminium
All the filtrates obtained during the washing of PL were transferred to a beaker and heated for 15 min at 115 °C. Thereafter, the mixture was allowed to cool down overnight at room temperature, during which a precipitate (precipitate 1) was formed, which was filtered out of the solution, air dried overnight at 70 °C and then calcined at 850 °C for 2 h. The remaining filtrate was allowed to stand for 48 h. During this time, a second white precipitate (precipitate 2) was formed, which was filtered, dried overnight at 70 °C and then calcined at 850 °C for 2 h in order to ensure the total transformation of Al2(SO4)3 to Al2O3.
2.4 Synthesis of ZSM-5PL2 zeolite from the solid residue of acid treated fly ash (PL)
PL (0.75 g) was mixed with 1 g of TPABr, 0.75 g of fumed silica, and 0.25 g of NaOH in 20 mL of deionised water. The obtained gel mole ratio was as follows: Si: 5.8; Al: 1.0; Na: 1.7; TPABr: 0.9; H2O: 306.9. The latter gel was first aged at room temperature for 2 h and then submitted to a hydrothermal synthesis at 160 °C for 72 h. The obtained solid product (Na-ZSM-5PL2) was filtered, washed with deionised water, dried in an oven at 70 °C and calcined at 550 °C (heating ramp 15 °C/min) for 3 h. Thereafter, Na-ZSM-5PL2 was ion-exchanged in 0.5 M NH4NO3 solution (zeolite: NH4NO3 ratio 1:10) at 80 °C for 1 h. The treatment with NH4NO3 was repeated four times with a fresh NH4NO3 solution each time, the solid sample obtained was dried overnight at 100 °C and calcined at 550 °C for 3 h. The so-obtained H-ZSM-5PL2 was characterised and used as the catalyst in the Methanol-to-Olefin (MTO) reaction.
2.5 Oxalic acid post-treatment of the as synthesized H-ZSM-5PL2
One gram of the as-obtained orange-brownish zeolite (H-ZSM-5PL2) from the process described in Section 2.4 was suspended in 20 mL of a 1 M oxalic acid aqueous solution. This suspension was refluxed (95 °C) for 1 h. The mixture was then cooled and filtered over a nylon membrane. An orange-brownish liquid fraction and a white powder were obtained. The latter H-ZSM-5PL2-OA was then calcined at 550 °C for 4 h to burn out any retained oxalic acid molecules.
2.6 BrØnsted acid site titration of H-ZSM-5PL2 using the H/D exchange isotope technique
The acidity of H-ZSM-5PL2 was determined according to the method developed by Louis et al. [22]. H-ZSM-5PL2 (200 mg) was activated under N2 flow (60 mL/min) at a heating rate of 15 °C/min and held at 450 °C for 1 h to desorb water. The temperature was lowered to 200 °C, to allow D2O vapour to pass through the solid for 1 h under N2 flow. Dry N2 flow was then applied to sweep away the excess of D2O for 1 h. The titration of O-D sites was performed by back-exchanging deuterium (D) present on the surface of H-ZSM-5PL2 with H2O vapour saturated N2 stream for 1 h. Partially deuterated HxODy was collected in a cold trap at −78 °C, weighed and mixed with 0.6 mL of trifluoroacetic anhydride. A CHCl3/CDCl3 reference (10:1 in weight) was prepared to determine the BrØnsted acid site density using a Bruker UltraShield 300 MHz/54 mm spectrometer.
2.7 Methanol to olefins (MTO) catalytic reaction
The zeolite catalyst (H-ZSM-5PL2, H-ZSM-5PL2-OA or H-ZSM-55524), 60 mg, was placed in a fixed bed quartz reactor and heated at 400 or 450 °C (heating ramp 15 °C/min). After desorption of physisorbed water for 1 h, the reactor was connected to a stripper, kept at 0 °C, containing methanol. Methanol was fed to the reactor by N2 flow (20 mL/min), resulting in a WHSV of 1.12 h−1. Gas product samples (1 mL) were collected regularly during 24 h and analysed using a Hewlett Packard 5890 Gas Chromatograph (GC) equipped with a PONA column and a FID. The percentages of methanol conversion and the selectivities toward the different alkenes, alkanes and aromatics were determined as already reported elsewhere [20,21].
2.8 Characterisation techniques
The X-ray fluorescence (XRF) analysis, used to determine the elemental composition of the samples, was carried out on a Philips 1480 X-ray spectrometer. A PANanalytical X-ray diffractometer with a PW3830 generator was used for X-ray diffraction (XRD). The ZSM-5 phase purity (or % XRD crystallinity) was estimated by using the formulation suggested by Nicolaides [32], based on the seven most intense reflections:
The morphology of the samples was investigated using a Hitachi X-650 Scanning Electron Micro-analyser (SEM) with a CDU-lead detector. The specific surface areas of the samples were determined using Autosorb IQ Automated Gas Sorption Analyser. 27Al solid state MAS NMR was performed to distinguish between the framework and extra-framework aluminium using Bruker Ascend TM 500.
3 Results and discussion
3.1 Elemental composition and morphological analysis of fly ash and acid treated FA
The elemental composition of pristine coal fly ash (FA) and after acid treatment (PL) was determined by XRF (Fig. 1). Likewise, the SEM micrographs of FA and PL are shown in Fig. 1. Sulphuric acid extracted metal oxides from FA; which caused the mass percentage of Al2O3, Fe2O3, CaO and MgO in the fly ash to decrease from 28.00 ± 0.15 % to 24.59 ± 0.06%, from 5.03 ± 0.06 % to 1.61 ± 0.01%, from 4.01 ± 0.06 % to 2.87 ± 0.10%, and 1.20 ± 0.01 % to 0.44 ± 0.00%, respectively. From these results, it can be deduced that 12% and 68% of Al2O3 and Fe2O3 were extracted from their total available content in FA, whilst Lai-Shi et al. reported that 87% of Al2O3 extraction from FA could be achieved after concentrated sulphuric acid (ratio acid/FA 5:1) harsh treatment at 210 °C for 80 min [23]. However, several studies are in disagreement with this former report. For example, Vassilev et al. [24] showed that sintering, hydrothermal, acidic and alkaline treatments and some physical separation technologies for bulk FA processing were commonly ineffective, expensive or harmful to the environment. Furthermore, Liu et al. [7] and Yao et al. [9] reported that the sintering of FA with CaO at temperatures ranging between 1000 and 1200 °C, prior to acid treatment, was necessary to recover 70–90 % of Al2O3. These results seem to be corroborated by a study done by Shemi et al. showing that a temperature of 1150 °C was required during the sintering stage in order to extract 85% of Al from FA [25]. The important decrease in Fe2O3 mass percentage from 5.03 ± 0.06 % to 1.61 ± 0.01% corroborated what was reported in the literature about the recovery of iron from FA that was relatively simple and could be performed by magnetic separation [26].
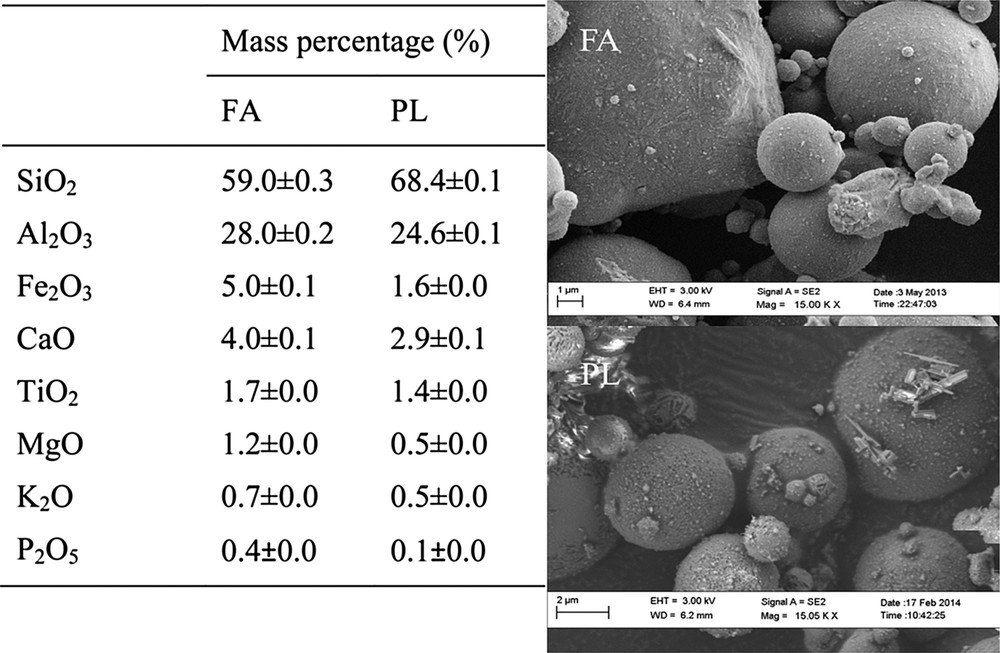
Elemental composition (n = 3) and SEM micrographs of pristine fly ash (FA) and sulphuric acid treated FA (PL).
The SEM images showed that there was no remarkable difference between FA and PL particles. The acid treatment could not alter the large, spherical glassy particles of coal FA which seemingly contained most of the aluminium. This might explain why only 12% of the total available Al2O3 content was extracted from FA under applied conditions.
3.2 Characterisation of extracted metals
Fig. 2 shows the SEM micrographs and elemental compositions of FA extracted fractions containing metals: precipitate 1, precipitate 2 and magnetic extract. It could be observed that precipitate 1 and magnetic extract were made of particles with different shapes and sizes, whilst precipitate 2 was mainly composed of homogeneous micron-sized cubic crystals.

Elemental composition by EDS (n = 6) and SEM images of precipitate 1, precipitate 2 and magnetic extract.
Precipitate 1 and magnetic extract are composed of more than one metal oxide, which might derive from different mineral phases and explain the lack of homogeneity in the particles. In contrast, precipitate 2 contains aluminium as the sole metal. Shcherban et al. extracted aluminium and iron from coal FA and reported that the aluminium extract contained 86% of Al2O3, while the magnetic extract contained 58–66 % of Fe3O4 and Fe2O3 whereas the non-magnetic residues contained 2.6–3.6 % of Fe2O3 [26]. Therefore, the magnetic extract of the present study has been enriched with iron oxides by applying further separation steps during the magnetic extract and precipitate 1. One may suggest a potential use of Fe and Al extracts in the synthesis of doped Fe-zeolites and high aluminium content zeolites, respectively [27,28].
Fig. 3 shows the XRD patterns of precipitate 1, precipitate 2 and magnetic extract. It could be seen that the precipitate 1 pattern exhibits mainly CaSO4, Fe2O3 and mullite crystalline phases. The precipitate 2 pattern exhibits the sole presence of the quasi-amorphous Al2O3 phase.

XRD patterns of precipitate 1, precipitate 2 and magnetic extract (M = mullite).
In the magnetic extract, characteristic reflections of Fe2O3, Fe3O4 and a small fraction of the residual mullite phase were detected. These results are in line with the SEM analysis as well as elemental composition analyses (Fig. 2).
3.3 Characterisation of H-ZSM-5PL2 zeolite
The elemental composition obtained by XRF analysis and SEM image of H-ZSM-5PL2 are given in Fig. 4. Si and Al were the main elements found and Si/Al = 6. Besides, H-ZSM-5PL2 also contains other elements such as Na, Ca, Fe, K and Mg. The SEM image shows that the H-ZSM-5PL2 morphology was mixed size range of spherulitic particles of ZSM-5 zeolite and the amorphous phase. Petrik et al. reported that tetrapropylammonium bromide could direct the formation of ZSM-5 particles with a spherulitic shape [15]. This is in agreement with the shape of ZSM-5 particles found in the present study. Na-ZSM-5PL2 zeolite was transformed to H-ZSM-5PL2 by carrying out ion exchange four times in 0.5 M of NH4NO3 solution followed by calcination at 550 °C for 3 h. The concentration of exchangeable cations (Na+, Ca2+, K+ and Mg2+) in the supernatants obtained after each sequential treatment with a fresh NH4NO3 solution was determined by ICP analysis (Fig. 5). It is noteworthy that sodium was the most abundant cation, followed by calcium and potassium. The ion-exchange efficiency was extremely high for the latter cations, while magnesium could not be easily exchanged. Kirov and Filizova investigated the influence of extra-framework cations (Na+, K+, Ca2+ and Mg2+) and water in the zeolitization process. They concluded that Ca2+, Na+ and Mg2+ governed the stability of large channels in ZSM-5 thanks to their high hydration capacity and their location in the channels [29]. In parallel, Petrik reported that K+ is a structure-breaking cation and hinders the zeolitization process [30]. However, the complexity of the bulk composition of coal FA renders it difficult to relate anything significantly to a particular component [24], except to note that the as-made ZSM-5 zeolite is not in Na-form only but has divalent cations present as well.
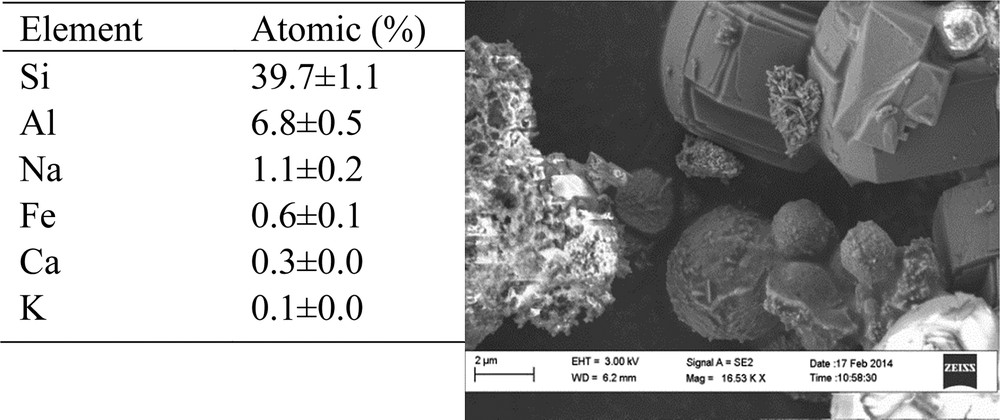
Elemental composition by XRF (n = 3) and SEM image of H-ZSM-5PL2.
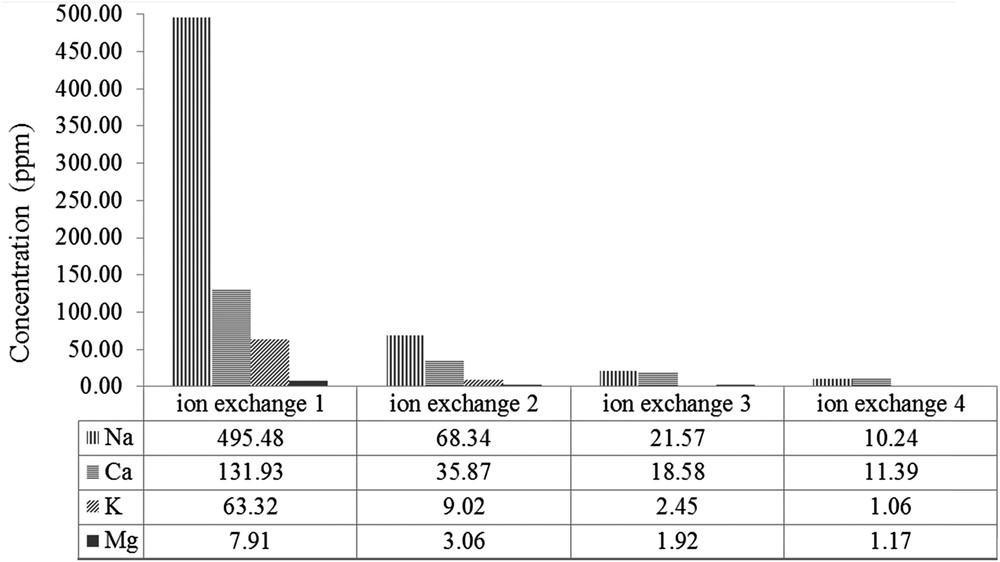
Concentration of cations exchanged from Na-ZSM-5PL2 in 0.5 M NH4NO3 solution.
The XRD patterns of pristine fly ash (FA), acid treated FA (PL), fly ash-based ZSM-5 zeolite (H-ZSM-5PL2) and commercial ZSM-5 zeolite (H-ZSM-55524) were compared in Fig. 6. FA is mainly composed of mullite, quartz and hematite phases (Fig. 6). The amorphous glassy phase in FA was identified as a hump in the background observed between 2θ 18 and 33°. Mullite, quartz and haematite phases are still present after the treatment with sulphuric acid as shown in the PL pattern. Some calcium sulphate phases could also be detected at 2θ = 25.4°. Characteristic reflections of the ZSM-5 zeolite phase are present in H-ZSM-5PL2 at 2θ: 7.7, 8.9, 13.8, 14.6, 15.8, 23, 23.9, 24.4, 29, 29.7, 44.9 and 45.4°, as shown in the simulated XRD powder patterns [31].

XRD patterns of FA, PL, H-ZSM-5PL2 and commercial H-ZSM-55524 (M = mullite, Q = quartz, H = haematite and (*) = calcium sulphate).
The zeolite phase purity in H-ZSM-5PL2 was found to be 62% with respect to H-ZSM-55524, set as a reference based on ZSM-5 peaks at 7.7, 8.9, 23, 23.9, 24.4, 29.7, 44.9 and 45.4°. As shown in the XRD patterns, a small amount of mullite, quartz and haematite phases were still present in the H-ZSM-5PL2 composite material. Querol et al. reported that the conversion efficiencies of FA into zeolites depend on the content of non-reactive phases such as haematite and resistant aluminium-silicate phases such as mullite and quartz. The dissolution rate of Al- and Si-bearing phases is as follows: glass > quartz > mullite [33,34]. Chareonpanich et al. produced a 43% containing ZSM-5 from lignite FA plus roughly 20% of unreacted Al2O3 [5].
The location of aluminium in H-ZSM-5PL2 was investigated by comparing the 27Al MAS NMR spectrum to commercial H-ZSM-55524 (Fig. 7). Two signals were observed in H-ZSM-5PL2 and H-ZSM-55524 zeolite spectra: a weak signal at 0 ppm corresponding to non-framework Al (octahedral coordination) and an intense signal at 55 ppm corresponding to tetrahedral framework Al. The tetrahedral Al signal of H-ZSM-55524 was narrower than of H-ZSM-5PL2. Similar results about the location of Al in MFI zeolite were reported by Triantafyllidis et al. and Sazama et al. [35,36].
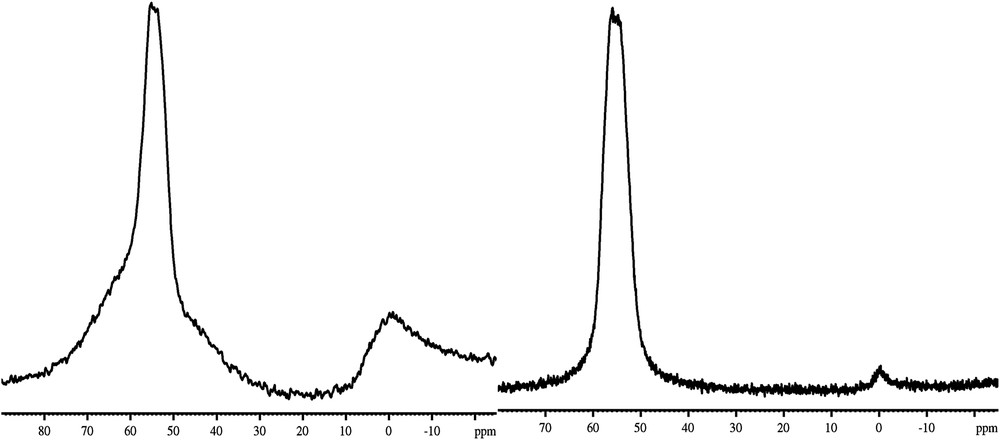
27Al MAS NMR spectra of H-ZSM-5PL2 (left) and H-ZSM-55524 (right).
Louis et al. developed a relation between the acid site density (mmol H+/gzeolite) and the theoretical Si/Al mole ratio in ZSM-5 [23], which allowed an estimation of H-ZSM-5PL2 and H-ZSM-5PL2-OA acidities. Indeed, the zeolite phase present in the H-ZSM-5PL2 sample has a predicted Si/Al = 22. This is one of the main reasons why it was selected to compare the catalytic behaviour of FA-converted materials with the commercially available, reportedly active MTO catalyst exhibiting roughly the same Si/Al = 25 [21b–e].
As mentioned earlier, the Methanol-to-Olefin (MTO) reaction was mainly used as the probe reaction to validate the synthesis of ZSM-5 zeolite catalyst starting from acid treated FA. Table 1 presents the chemical and physical properties (Si/Al ratio, number of acid sites, BET surface area) of PL, H-ZSM-5PL2 and H-ZSM-55524 zeolites. It could be seen that the Si/Al molar ratio and BET surface area of PL were 2 and 3 m2/g, respectively. This starting material exhibited a low activity in MTH; and was able to convert methanol only into aromatics as no olefins could be detected (Table 2). This unusual aromatization behaviour might be related to the presence of traces of different metals in PL. The Si/Al ratio of H-ZSM-5PL2 is roughly 6 which remain far below the lowest Si/Al of 11 found in ZSM-5 zeolites [14]. Beside the Si/Al molar ratio, the presence of mullite and other unreacted FA phases affected the number of acid sites, BET surface area and methanol conversion (Tables 1 and 2). H-ZSM-5PL2 is less active than H-ZSM-55524 (which exhibits full methanol conversion) and also deactivates after 5 h on stream with a methanol conversion drop from 60% (after 1 h) to 52% (after 2.5 h) (Fig. 8). The increase in reaction temperature in the case of H-ZSM-5PL2 from 400 to 450 °C initially led to a higher conversion and rapid catalyst deactivation (Fig. 8). The deactivation of H-ZSM-5PL2 is probably due to the low Si/Al molar ratio and BET surface area [37,38]. An easy and cheap post-synthetic treatment using oxalic acid was used in order to optimize the MTO performance of the fly ash-based ZSM-5 zeolite. Oxalic acid has been chosen since it is a potent chelating agent, broadly used in zeolite post-synthesis treatments to extract extra-framework aluminium species (EFAl) or to generate a certain mesoporosity [39]. Herein, it is reasonable to assume that oxalic acid will mainly chelate and extract residual non crystallised metal cations, since the latter are probably responsible for catalyst instability; removing them would improve the catalyst performance of FA-derived zeolites.
Si/Al ratio, number of acid sites and BET surface area for PL, H-ZSM-5PL2, H-ZSM-5PL2-OA and H-ZSM-55524.
PL | ZSM-5PL2 | ZSM-5PL2-OA | ZSM-55524 | |
Si/Al ratio | 2 | 5.8 | 6.3 | 25(*) |
Number of acid sites (mmol H+/gzeolite) | / | 0.61 | 0.31 | 0.86 |
BET surface area (m2/g) | 3 | 328 | – | 480 |
MTO conversion and selectivity data for the different catalysts.
Zeolite | Conversion [%] | Selectivities [%] | |||||
CH4C4H10 | C2= | C3= | C4= | C5= | C6+ – aromatics | ||
PL | ≈5 | 0 | 0 | 0 | 0 | 0 | 100 |
H-ZSM-5PL2 | 58 | 50 | 17 | 20 | 4 | 4 | 5 |
H-ZSM-5PL2-OA | 100 | 5 | 17 | 35 | 14 | 15 | 14 |
H-ZSM-55524 | 100 | 20 | 12 | 19 | 13 | 14 | 22 |
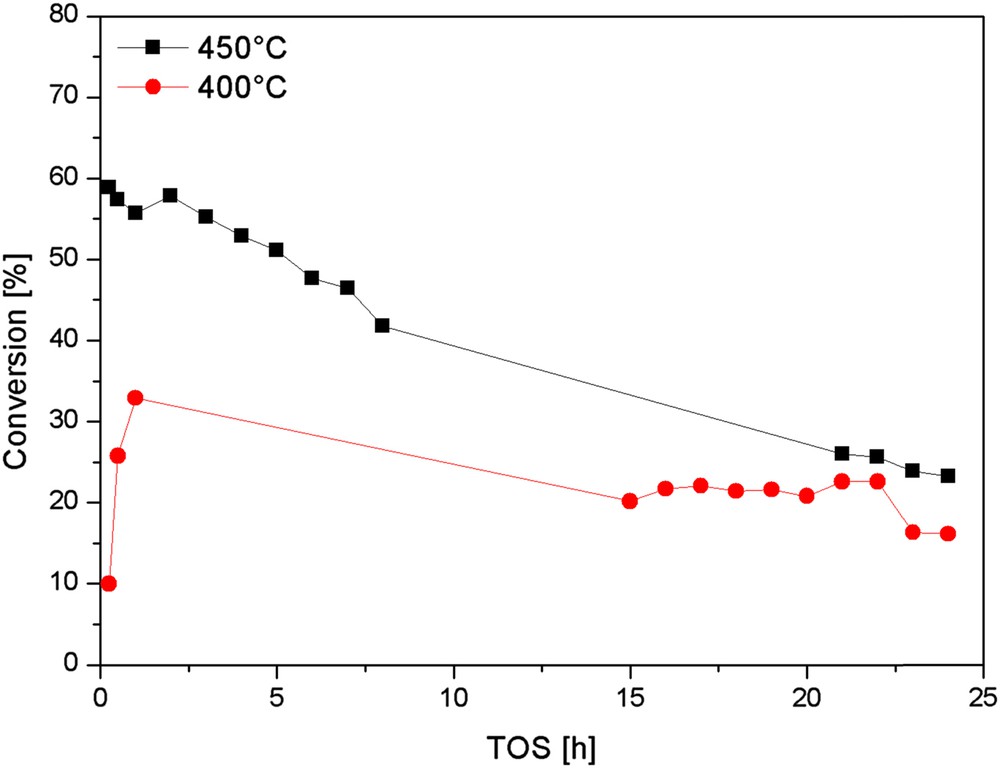
H-ZSM-5PL2 behaviour in the MTO reaction at 400 and 450 °C.
Fig. 9 shows the preliminary MTO results comparing acid-treated H-ZSM-5PL2-OA with H-ZSM-5PL2 and H-ZSM-55524 catalysts. The catalyst activity was significantly improved and full methanol conversion could now be achieved and kept during 20 h on stream (Xmethanol > 95%). This enhancement of FA-prepared zeolite catalyst viability is accompanied by extremely promising selectivities toward light olefins (Table 2). Indeed, 35% of propylene and 66% of C2C4 olefins were produced over H-ZSM-5PL2-OA, whilst only 19% and 44% were obtained over H-ZSM-55524 catalyst.

Comparison between ZSM-5 zeolites in the MTO as a function of time on stream at 450 °C.
The strategy to design FA-prepared ZSM-5 zeolites for acid-catalysed purposes appears valid and promising. The conversion of methanol into hydrocarbons is depicted in Table 3. In spite of improving the cumulative methanol conversion capacities from 30 g to 71 g depending on H-ZSM-5PL2 or H-ZSM-5PL2-OA catalyst, it is still not competing with the 212 g converted over H-ZSM-55524 catalyst. Further work is therefore required to improve the FA-prepared ZSM-5 catalyst life time by optimisation of the post-treatments.
4 Conclusion
This study highlights a strategy to valorise South African coal fly ash (after metals extraction which might be recovered and valorised as well) as a feedstock for the synthesis of ZSM-5 zeolite. From raw fly-ash, a FA-zeolite composite was successfully prepared, containing 62% of pure ZSM-5 phase and 0.61 mmol BrØnsted acid sites per gzeolite. Interestingly, this FA-ZSM-5 composite successfully behaves as a catalyst in the MTO reaction. In order to enhance its activity and stability, a cheap oxalic acid post-treatment has been undertaken to achieve full-methanol conversion during 15–20 h on stream. In addition, H-ZSM-5PL2-OA led to reach a 35% propylene selectivity and 66% light olefins (C2–C4) selectivity.
Acknowledgements
The financial support of the NRF Protea program, the technical and material supports of the Environmental and Nano Sciences (ENS) are gratefully acknowledged. PL would like to thank the National Research Fund Luxembourg for his PhD Grant (5898454).