1 Introduction
NOx and soot are the two major pollutants released from diesel engines. Future environmental standards will lead to the integration of depollution systems for these two pollutants in all types of vehicles (light, heavy, or off-road). To reduce weight and volume of the aftertreatment devices assembled along the exhaust line, and minor the production and installation costs, integrating DeNOx and DeSoot functions into a single monolith is under investigation. In this direction, Toyota has developed the diesel particulate NOx reduction system that is composed of a diesel particulate filter (DPF) coated with a NOx storage reduction catalyst [1]. This system, however, suffered of sulfur poisoning, higher fuel consumption, and low durability of efficiency. Choi and Lee [2] investigated the efficiency of a lean NOx trap catalyst associated with a DPF. Although simultaneous DeNOx and DeSoot phenomena were observed, the NOx conversion did not exceed 60%. A NOx selective catalytic reduction (SCR) process using NH3 was developed for on-road and off-road vehicles and is now well introduced in the market. In this context, several researchers have assessed the effectiveness of a wall-flow DPF treatment with an SCR catalyst washcoat [3–5]. Such a system is referred as SCR on filter. According to Guan et al. [3], SCR on the filter system is considered as one of the most promising concepts for future diesel NOx exhaust aftertreatment. Kang et al. [4] studied the simultaneous removal of soot and NOx on a DPF substrate coated with a copper-based zeolite catalyst. The SCR on filter system coated with a CuNb–ZSM-5 catalyst displayed comparable NOx conversion in the whole temperature range (150–600 °C) before and after loading the DPF substrate with 2 g/l of Printex U, used as simulated soot. Using Cu–ZSM-5 catalyst, NOx conversion of the catalyst was decreased by 5% over the entire temperature range after soot loading. According to Cavataio et al. [6], a soot inhibition effect in DeNOx activity was observed using a Cu-based zeolite-coated SCR on filter during laboratory and engine testings. This behavior is dependent on the NO2/NOx ratio: for low ratios no inhibition occurred, whereas for NO2/NOx = 0.5 the SCR on filter showed a reduced activity. At higher ratios an increase in DeNOx activity has been observed. In a recent review, Guan et al. [3] concluded that controversy results have been reported for soot loading impact on DeNOx performance of the SCR on the filter system that may be associated with various factors, including SCR catalyst formulation, soot loading level, NH3/urea injection strategies, and the range of temperature under investigation. However, it is generally acknowledged that soot on a DPF helps the DeNOx functionality if the NO2 content is greater than 50% of the overall NOx.
The effect of the SCR catalyst coating on a DPF on soot oxidation was widely investigated [7–13]. These corresponding experiments were all performed under an oxidative atmosphere (air or x% O2/N2) and have demonstrated that some oxides such as CeO2, V2O5, MoO3, or CuO exhibit a high activity. Neeft et al. [10] found that the contact between soot and oxide catalyst is a key factor of soot catalytic oxidation. A loose contact leads to a lower oxidation activity than a tight contact. Among the different single oxides that have been tested, V2O5 is one of the best catalysts for promoting oxidation of carbon by O2. According to Liu et al. [13], its high activity is attributed to its low melting point leading to migration of the active phase across the soot surface. The high mobility of the catalyst could thus form a wet phase that improves the contact with soot by covering its surface [12].
V-based catalysts are widely used as DeNOx components because of their high activity against NOx reduction in the medium temperature range 300–450 °C and their high resistance to sulfur poisoning [3]. The commercial V-based SCR catalysts consist of V2O5 and WO3 supported high surface area anatase form of titania. Japke et al. [5] observed that under temperature-programmed oxidation the coating of the ceramic cordierite DPF, with a commercial vanadia-based SCR catalyst (2 wt % V2O5–9 wt % WO3–TiO2), allows a significant diesel soot oxidation in two low-temperature regions (150–250 and 350–500 °C), whereas on the noncatalytic DPF soot oxidation starts at temperatures greater than 500 °C.
Despite these numerous studies, few investigations were performed on the simultaneous DeNOx and DeSoot on vanadia-based SCR catalysts coated on a DPF support under realistic exhaust conditions, that is, in the presence of a gas flow composed of NH3, NOx, and O2 [14,15]. The reason is probably that, as SCR on filter combines both SCR and DPF functions, the thermal resistance of an SCR catalyst has to be taken into account, as DPF regeneration leads to an increase in the exhaust temperature. Beside their interesting DeNOx activity, V-SCR catalysts, when placed downstream of a DPF, present a deactivation of DeNOx function because of release of toxic vanadium compounds, such as V2O5, which occurs beyond 675 °C [16–20]. However, full body type V-SCR catalysts were recently developed and demonstrated higher temperature tolerance [16], thus suggesting an interesting potential for simultaneous DeNOx and DeSoot using SCR on filter composed of a V-based catalyst.
The purpose of the present work is to investigate simultaneous NOx reduction and soot combustion over a commercial full body type V-based SCR catalyst used in off-road exhaust gas conditions. Experiments were performed at a laboratory scale in a fixed bed reactor, with carbon black (CB) used as model soot. The impact of the contact between soot and catalyst is assessed. The effect of calcium addition in the catalyst is also investigated as this element, produced from oil consumption, can depose in the engine and provoke SCR deactivation [21,22]. Indeed, in a recent study [23], a poisoning effect of a commercial full body type V-based SCR catalyst with 0.24 wt % of Ca and Zn was observed. These loadings are representative of the poisoning of catalysts after several thousand hours of operations of an off-road vehicle, which impact the activity of the catalyst at low temperatures (<300 °C). The decrease in DeNOx performance was attributed to a poisoning process of active sites involved in the redox cycle.
2 Experimental section
2.1 Materials and characterization
The catalyst studied in this work is a commercial full body type vanadia-based SCR catalyst with a density of 300 cpsi. The matrix of the catalyst is TiO2 with a global vanadia and tungsta composition around 2 and 8 wt %, respectively. As mentioned in Section 1, the use of vanadia-based catalysts is critical because V2O5 can sublime at temperatures greater than 650 °C and significant aggregation of active and selective well-dispersed VOx species into less selective agglomerates can take place at temperatures greater than 400 °C. The stability of the SCR catalyst used in the present study was previously investigated [16]. It was shown that when a monolith sample (with 72 channels) is exposed to a gas flow composed of 5% of O2, 5% of H2O, 500 ppm of NO, and 500 ppm of NH3, in the temperature range 550–750 °C, no significant vanadium sublimation occurred at temperatures less than 675 °C. Moreover, it was observed that the DeNOx activity of the monolith sample remains stable at 550 °C during 10 h of exposure. In the present study, the monolith was crushed and sieved to retain the fraction having a particle diameter ranging from 250 to 350 μm. This sample was referred to as “undoped SCR”.
Incipient wetness impregnation was used to dope the catalyst with 2 wt % of Ca. This deposition technique was preferred to those consisting in spraying submicrometer aerosol particles in view of the literature data [21,22,24], which revealed that this latter seems to be more realistic but less controllable. Some authors [21,25,26], who compared different approaches for catalyst poisoning, observed a better uniform distribution of the inorganic compound and consequently a better reproducibility using the impregnation procedure. The powder was impregnated by an aqueous solution of Ca(NO3)2 under agitation and heating until the water was evaporated. Then it was dried at 110 °C overnight and calcined in a muffle furnace at 450 °C for 6 h. This sample was referred to as “Ca2%”.
A commercial CB, Vulcan 6 from Cabot with a specific surface area equal to 106 m2/g was used as a model of soot particles.
Surface areas were determined by nitrogen physisorption at −196 °C on a Micromeritics ASAP2020 device.
Elemental composition of Ca was analyzed by flame atomic absorption spectroscopy using a Perkin Elmer PinAAcle 900F Absorption Spectrometer after microwave digestion with HF (0.5 ml/100 mg) and HNO3 (5 ml/100 mg).
X-ray diffraction (XRD) patterns were recorded on a Bruker D8 powder diffraction system using a Cu Kα radiation source equipped with a graphite monochromator. The diffraction patterns were collected under ambient conditions over the range 10–90°2θ. The phases were identified comparing the measured set of interplanar distances, d, and the corresponding intensities of the diffraction maximum, I, with those found in the Joint committee on powder diffraction standards (JCPDS) database.
2.2 Reactivity tests
Catalytic experiments were performed in a fixed bed reactor. All gases were injected via different mass flow meters. The water vapor was introduced using a liquid mass flow meter followed by an evaporator. The temperature was measured by a thermocouple located within the bed of catalyst.
Before experiments, the catalytic sample placed in the reactor (1.3 g) underwent a degreening at 450 °C for 4 h with injection of a synthetic gas flow containing 1000 ppmv of NO and 15% of O2. Then, the catalyst was cooled under N2 flow. It was sketched that this degreening procedure allows a stabilization of the catalytic surface, hence leading to repeatable results (results not shown here).
Two different configurations of catalyst/soot mixtures were tested. The first one consisted introducing 120 mg of soot (CB), as a layer, directly on the SCR catalytic bed (1.3 g), after the degreening of the latter. This configuration is supposed to be representative of soot accumulation in the channels of a coated SCR catalyst on a DPF monolith. The contact between soot and catalyst is thus small (“loose contact”). This configuration is named “SCR–CB layer”. In the second configuration, 120 mg of CB and 1.3 g of a degreened catalyst sample were physically mixed with a spatula. In that case, the contact between carbon and catalyst is tighter than the one developed in the SCR–CB layer samples. This second configuration, named “SCR–CB mixture”, is supposed to simulate soot and catalyst interactions occurring in a full body SCR on filter monolith. In this process, the catalyst is included in the composition of the monolith structure and the soot migrates into the pores of the filter.
The SCR–CB layer and SCR–CB mixture samples were placed in the reactor and heated under N2 flow up to 190 °C. Subsequently, the reactive gas flow, containing 1000 ppmv of NOx (100 ppmv NO2 + 900 ppmv NO), 1000 ppmv of NH3, 15% of O2, and 8% of H2O to mimic real conditions, was injected through the reactor. The total flow rate was 90 Nl h−1, leading to a space velocity of 55,000 h−1. Concentrations of NO, NO2, CO, and CO2 were measured in the outlet gases by a NO/NO2/CO/CO2 analyzer (Rosemount X-stream) and a NO/NO2 analyzer (Rosemount NGA2000). After stabilization of the concentration signals, the NOx reduction conversion rate and carbon oxidation rate (rc) were calculated from the following equations:
(1) |
(2) |
- • (XNO)out, , (XNO)in, and are the outlet and inlet mole fractions of NO and NO2
- • Mc is the molar carbon mass (g/mol)
- • mcr is the carbon mass remaining in the reactor (g)
- • Dv is the flow rate (m3/s)
- • Vmol is the molar volume (m3/mol)
- • (XCO) and are the mole fractions of CO and CO2 measured at the outlet of the reactor.
Then, the temperature was raised to 225 °C under the reactive feed gas. At this temperature, after stabilization of the concentration signals the NOx reduction conversion rate and carbon oxidation rate were calculated again to measure steady-state conversions. This procedure was repeated, with a progressive increase in temperature by steps of 25–100 °C, up to 550 °C. Some experiments with SCR–CB layer samples were performed by lowering the temperature from 550 °C (by heating under N2 flow) to 250 °C by steps of 25–100 °C. In the following sections, experiments performed with SCR–CB layer samples by rising and lowering the temperature are named “SCR–CB layer R” and “SCR–CB layer D”, respectively.
3 Results and discussion
3.1 Characterization of undoped and impregnated SCR catalysts
The elemental composition of calcium of the catalyst samples and their specific surface area measured after the calcination step are presented in Table 1. Surprisingly, the undoped SCR sample, that is, fresh commercial sample without any calcium poisoning, contains a significant amount of Ca ((1.79 ± 0.33) wt %). The standard deviation measured for this element, from eight measurements, is large. The material thus presents a lack of homogeneity that reduces the possibility to precisely check the amount of Ca introduced during the poisoning procedure. It is noteworthy that impregnation of divalent cations (Ca2+) did not affect the specific surface area of the catalyst.
Concentration of calcium (wt %) and specific surface area (SBET) of the catalytic samples.
Catalytic sample | %Ca (wt %)a | SBET (m2/g) |
Undoped SCR | 1.79 | 52.6 |
Ca2% | 3.37 | 50.6 |
a Standard deviation: 0.33%.
XRD patterns of both undoped SCR and Ca2% samples are presented in Fig. 1. Both catalysts showed well-defined XRD peaks because of well crystallized anatase TiO2 phase. In the catalyst poisoned with calcium (Ca2%), a single peak referring to CaCO3 phase (*) was observed at 29.3°2θ (JCPDS 29-305) on XRD patterns.

X-ray diffractograms obtained with undoped SCR (a) and Ca2% (b) samples.
3.2 Reactivity of undoped SCR catalyst
3.2.1 Impact of soot on NOx reduction activity
NOx reduction activity of the undoped SCR catalyst and the different configurations of catalyst/soot mixtures, depending on the temperature, are shown in Fig. 2. Whatever the sample tested, the maximum efficiency of the vanadia-based SCR catalyst reached in the temperature range between 300 and 400 °C. In this temperature range, a loose contact between CB and the SCR catalyst (SCR–CB layer samples) does not influence the NOx reduction conversion rate equaling 99.1 ± 0.5%. Considering the SCR–CB mixture sample, for which a tighter contact between CB and catalyst is obtained, a slight decrease in NOx reduction conversion rate equaling 97.4% is observed.

NOx reduction conversion rate (%) of the different samples (undoped SCR (●), SCR–CB layer R (▲), SCR–CB layer D (■), and SCR–CB mixture (◆)) versus temperature (900 ppmv NO; 100 ppmv NO2; 1000 ppmv NH3; 15% b.v. O2; 8% b.v. H2O; 90 Nl h−1; space velocity, 55,000 h−1).
At temperatures less than 250 °C, SCR–CB mixture, SCR–CB layer R, and undoped SCR samples present similar NOx reduction activities. The slightly enhanced conversion observed with the SCR–CB layer D sample may be attributed to the heating mode (decrease in temperature from 550 to 190 °C). This small enhancement of NOx reduction activity, when catalytic tests are carried out at steady state with a progressive decrease in temperature (from 550 to 200 °C) compared with an increase in temperature, was already observed with SCR catalyst samples (without the presence of soot) in previous tests (not shown here). On the basis of the literature data [8,10,12,13], this behavior could be attributed to a melting of the vanadium oxide at 550 °C leading to the formation of a wet phase that slightly improves the contact between carbon particles and the catalyst.
At temperatures greater than 400 °C, the NOx reduction activity significantly decreases. As reported elsewhere, for the undoped SCR sample [23], this behavior is in agreement with the observed production of N2O. Such a behavior can be then related to the oxidation reaction of NH3 with O2, reaction that is directly affected by the temperature. Beside this phenomenon, one may observe an impact of the presence of CB on NOx reduction activity of the SCR catalyst. Results obtained with the different samples reveal that, whatever the type of contact with CB and the catalyst, the presence of CB in the catalytic bed leads to a decrease in NOx conversion. However, the extent of the decrease in NOx reduction activity does not seem to depend on the contact between the two materials. Indeed, at 500 °C, 92.5% of NOx were reduced in the presence of the SCR–CB layer D sample, whereas a lower conversion (90.2%) is obtained with the SCR–CB layer R sample. Conversely, the NOx conversion obtained with the SCR–CB layer D sample is the same as the one measured, in the same conditions of temperature, using the SCR–CB mixture sample. With regards to the mass of CB remaining in the reactor when experiments were performed at 500 °C (Table 2), one may observe that this mass is equal to 55.7 ± 0.6 mg for both SCR–CB layer D and SCR–CB mixture samples, whereas a higher amount was remaining with the SCR–CB layer R sample (90.2 mg). On the other hand, results presented in Fig. 2 and Table 2 reveal that although almost all CB was consumed when experiments were performed at 550 °C in the presence of the SCR–CB layer R and SCR–CB mixture samples, a NOx reduction activity close to the one measured with the undoped SCR sample was observed. Conversely, the NOx reduction conversion rate obtained at 550 °C with the SCR–CB layer D sample was particularly weak (70%) because of the high amount of CB in the reactor (76.8 mg). It is possible to conclude that, when the SCR catalyst is in contact with soot, the mass of carbon remaining in the reactor is the critical parameter that affects the NOx reduction activity of the catalyst and the presence of soot does not impair the catalyst that regains its initial activity after complete combustion of the soot.
Mass of CB remaining in the reactor at each temperature step.
Catalysis sample | Mass of carbon (mg) | |||||
190 °C | 255 °C | 297 °C | 402 °C | 506 °C | 550 °C | |
SCR–CB layer R | 119.9 | 119.1 | 118.2 | 115.2 | 90.2 | 0 |
SCR–CB layer D | 50.0 | 50.1 | 50.4 | 50.9 | 55.3 | 76.8 |
SCR–CB mixture | 100.6 | 100.3 | 99.9 | 97.3 | 56.1 | 0 |
Ca2%-CB layer R | 111.8 | 111.1 | 109.6 | 106.8 | 90.7 | 37.5 |
Ca2%-CB layer D | 72.6 | 72.9 | 73.2 | 74.0 | 77.8 | 94.4 |
Ca2%-CB mixture | 96.2 | 95.9 | 95.5 | 93.8 | 77.9 | 3.4 |
3.2.2 Catalytic soot combustion
The evolution of the specific oxidation rate of CB and the different configurations of catalyst/soot mixtures as a function of temperature is shown in Fig. 3 and Table 3.

Specific oxidation rate of carbon for the different samples (CB (●), SCR–CB layer R (▲), SCR–CB layer D (■), and SCR–CB mixture (◆)) versus temperature: (a) T < 400 °C; (b) T > 400 °C (900 ppmv NO; 100 ppmv NO2; 1000 ppmv NH3; 15% b.v. O2; 8% b.v. H2O; 90 Nl h−1; space velocity, 55,000 h−1).
Carbon oxidation rate (mg/s g) of the different SCR samples for each temperature.
Catalysis sample | C oxidation rate (mg/s g) | ||||
190 °C | 255 °C | 297 °C | 402 °C | 506 °C | |
SCR | / | / | / | / | / |
CB | 5.40 × 10−4 | 2.03 × 10−3 | 3.10 × 10−3 | 6.10 × 10−3 | 3.70 × 10−2 |
SCR–CB layer R | 5.70 × 10−4 | 1.67 × 10−3 | 2.32 × 10−3 | 6.50 × 10−3 | 7.06 × 10−2 |
SCR–CB layer D | n.d | 8.03 × 10−4 | 1.61 × 10−3 | 6.62 × 10−3 | 7.90 × 10−2 |
SCR–CB mixture | 1.47 × 10−4 | 4.40 × 10−4 | 7.79 × 10−4 | 7.33 × 10−3 | 1.76 × 10−1 |
Whatever the sample, the carbon oxidation rate increases, as expected, with the temperature. Experiments performed on CB alone under SCR conditions of the present study show that the NOx reduction occurs with a conversion of almost 12% at 190 °C (Table 4). This NOx reduction activity decreases with an increasing temperature. A slightly higher carbon oxidation rate is obtained in the absence of NH3 in the feed gas (results not presented here) as NO2 is consumed by the SCR reaction. These results are in agreement with those obtained by Mehring et al. [27], who studied SCR of NOx on Printex U without any catalyst in the presence of NO2 or (NO2 + NO) together with NH3, O2, and H2O in the temperature range 200–350 °C. These authors observed that no SCR activity occurred in experiments with NO and NH3 in the feed gas, whereas when NO2 was introduced in the gas flow, the model soot was able to remove NOx. It is noteworthy that at this temperature, the NO2/NO ratio experimentally obtained is very low compared with the thermodynamic one. Considering the soot combustion, these authors argue that only a minimal coupling of the carbon oxidation rates and the NOx SCR reaction occurs on soot particles. Therefore, they concluded that NOx involved in the SCR reaction on soot do not form strong bonds with soot and have a more physisorbed nature. The decrease in NOx conversion on CB with an increasing temperature, also observed by Mehring et al. [27], is attributed to a higher oxidation of NH3.
NOx reduction (%) on CB sample as a function of temperature.
Catalysis sample | NOx reduction (%) | ||||||
190 °C | 225 °C | 255 °C | 297 °C | 402 °C | 506 °C | 550 °C | |
CB | 11.9 | n.d. | 9.8 | 8.8 | 7.5 | 3.7 | 2.8 |
Fig. 3 shows the impact of the SCR catalyst on CB oxidation. As observed for the impact of CB on NOx reduction activity, this impact is different as a function of temperature and two temperature ranges can be distinguished. At temperatures less than 400 °C (Fig. 3a), the SCR catalyst partially inhibits the carbon oxidation. The stronger the contact between CB and catalyst, the lower the carbon oxidation rate in the presence of the SCR catalyst. At 255 °C, the carbon oxidation rate obtained with the SCR–CB layer R sample is nearly 1.2 times lower than the one measured without the presence of the catalyst, whereas this ratio reaches a value of 5 with the SCR–CB mixture sample. Moreover, the CB oxidation rates obtained with the “SCR + CB layer R” are higher than the one measured using “SCR + CB layer D” samples (Table 3). This result could be attributed to the experimental procedure adopted and therefore to the closeness between the CB and catalyst particle. As observed previously, the SCR + CB layer D sample exhibits, at low temperatures, a slightly higher NOx reduction activity. In agreement with results presented in the literature [8,10,12,13], this behavior could be attributed to an improvement in the contact between carbon particles and catalyst, probably because of a melting of the vanadium oxide when exposed to high temperature (550 °C). Considering results presented in this study, it appears that at temperatures less than 400 °C, the impact of the SCR catalyst on the carbon oxidation depends on the contact between the two materials, whereas the presence of soot only affects very weakly the activity of the SCR catalyst.
In the literature, mechanisms of model soot oxidation, without any catalyst, under oxidative conditions, that is, with NO2 and O2 in the feed gas, are well documented [28–31]. It was established that carbon–O2 is the major reaction at temperatures greater than 450 °C. At temperatures less than 450 °C, NO2 is a better oxidant than O2. A direct reaction between NO2 and soot (1a) with a cooperative mechanism occurs (2a). The latter first involves NO2 interactions with active carbon sites, formed by oxygen adsorption, leading to NO production. Hence, the formed functional groups will react with NO2, resulting in CO2, CO, and NO production [28,31,32]. A direct (1a) and a cooperative (2a) reaction are adopted to summarize the overall process of soot oxidation by NO2 and O2:
(1a) |
(2a) |
On the other hand, investigations on NOx SCR over V-based catalysts revealed that three reaction equations describe the overall results obtained under different conditions:
(3) |
(4) |
(5) |
The “standard SCR” reaction (3) is the main reaction. However, at low temperatures and in the presence of NO2 in the gas mixture, several studies [33–35] agree that the “fast” reaction (4) proceeds faster than the standard SCR and “NO2 SCR” (5) reactions.
On the basis of the previously described mechanisms, one may conclude that in this temperature range, both carbon oxidation by NO2 and the fast SCR reaction occur simultaneously, and the inhibition of CB oxidation by the SCR catalyst is the consequence of a lack of available NO2. The fast SCR reaction is less impacted than the carbon oxidation reaction as it is kinetically faster [3].
At temperatures greater than 400 °C (Fig. 3b), contrary to the trends observed at low temperatures, an improvement in the specific carbon oxidation rate is obtained when the SCR catalyst is present in the reactor. The contact between CB particles and the SCR catalyst seems again to be a key factor for the impact of the catalyst. At 500 °C, a layer configuration between CB and the SCR catalyst doubles the CB specific oxidation rate compared to the one measured without catalyst in the reactor, whereas the CB and SCR catalyst mixture configuration leads to a five-fold increase in CB specific oxidation rate.
Overall, at temperatures greater than 400 °C, experiments carried out on the soot mixtures with the vanadia-based SCR catalyst lead to the observation of two main behaviors: a catalytic effect of the V-based SCR catalyst on carbon oxidation rate and an inhibition of soot on the NOx reduction by the SCR catalyst. It has been demonstrated that the extent of the catalytic effect of the SCR catalyst on the soot oxidation rate is directly related to the strength of the contact between the two materials, whereas those of the inhibition of NOx conversion is more related to the amount of carbon remaining in the fixed bed. Therefore, it seems that competitive reactions occur. It is admitted that the SCR standard reaction (3), which is the main reaction in our experimental conditions at high temperatures, proceeds according to a redox mechanism in which V5+=O catalytic species are reduced into V4+–O–H species by the reaction between NO and NH3. Gaseous oxygen then proceeds to the reoxidation of these reduced catalyst sites [37–39]. On the other hand, several authors underlined the potential of vanadium oxide catalysts for soot combustion [8–13,36]. Neri et al. [9] observed that the activity of oxide and mixed oxide catalysts is related to their reducibility: the most reducible catalysts, the most active. According to these authors, the first step of the mechanism involves the combustion of carbon particles with the reduction of active species. It can be therefore assumed that, when soot and vanadia-based SCR catalyst are mixed, carbon particles in tight contact with the SCR catalyst are catalytically oxidized by vanadyl sites (V5+=O) in the presence of NOx, O2, and H2O in the feed gas. This step would lead to a reduction in vanadyl sites, which would then be reoxidized by gaseous oxygen. Such a mechanism may explain the observed competition between carbon oxidation and NOx reduction at temperatures greater than 400 °C and is summarized in Scheme 1. However, surface characterizations are now necessary to confirm these hypotheses.
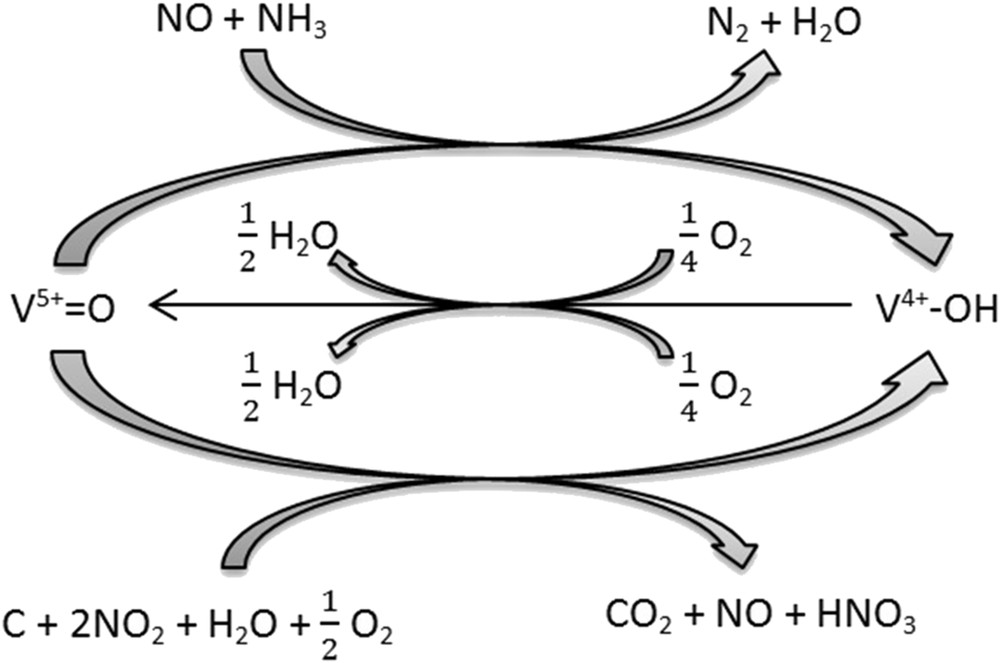
Competition paths between carbon oxidation and NOx reduction above 400 °C.
3.3 Poisoning effect of Ca
Fig. 4 presents the NOx reduction activity of the SCR catalyst doped with Ca in the absence or presence of CB in the reactor. Compared to Fig. 2, it can be noted that doped SCR catalyst with 2 wt % of Ca dramatically decreases the NOx conversion in the whole temperature range. The NOx conversion of Ca2% sample does not exceed 60%. According to the literature [23,40,41], the decrease in NOx reduction performance of V-based SCR catalysts by alkali and alkali-earth divalent cations is rather attributed at low temperatures (<300 °C) to a decrease in the ability of reduced V surface species to be reoxidized. Thus, an impact of the redox cycle is observed. On the basis of the redox mechanism governing the SCR of NOx by ammonia, NO2 at temperatures less than 250 °C is the oxidizing reactive agent of V surface species, via the buildup of adsorbed nitrates [39]. Conversely, at higher temperatures the regeneration of V5+=O mainly occurs through the action of O2 [24].
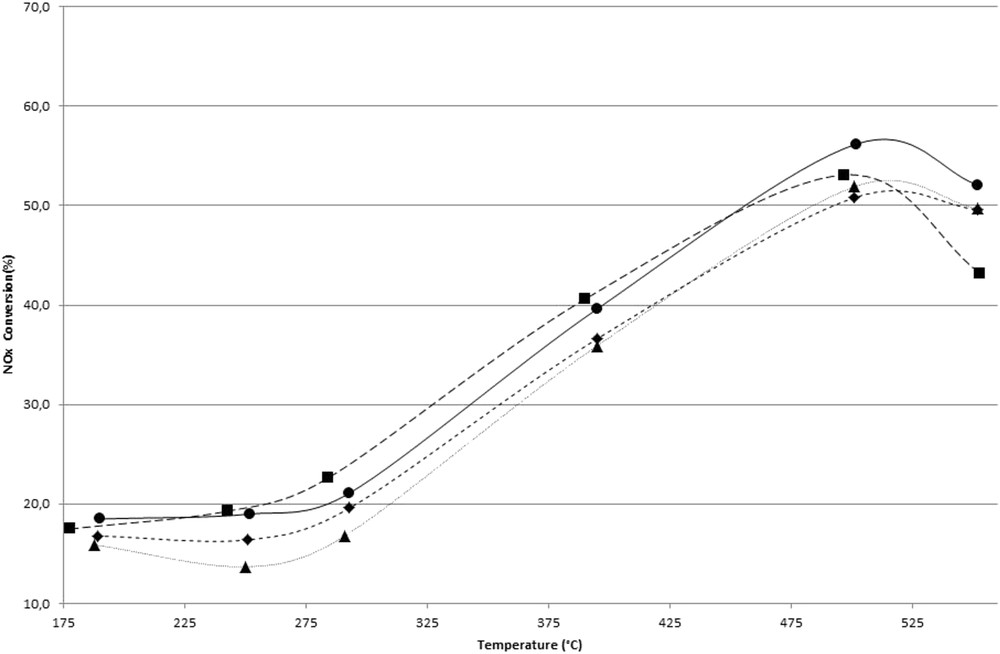
NOx reduction conversion rate (%) of the different samples (Ca2% (●), Ca2%-CB layer R (▲), Ca2%-CB layer D (■), and Ca2%-CB mixture (◆)) versus temperature (900 ppmv NO; 100 ppmv NO2; 1000 ppmv NH3; 15% b.v. O2; 8% b.v. H2O; 90 Nl h−1; space velocity, 55,000 h−1).
In contradiction with what was observed with the undoped catalyst, the presence of CB in contact with Ca2% sample leads to a slight decrease in the NOx reduction activity in the whole temperature range (Fig. 4).
Although the global impact of the SCR catalyst on carbon oxidation rate is still present after the doping procedure of the catalyst, as shown in Fig. 5, the extent of the latter is weaker. For example, when the temperature reaches 400 °C and beyond, the carbon oxidation rate measured in the presence of the Ca-doped catalyst is overall half of the one measured with the undoped catalyst. Similarly, although a tighter contact between CB and the undoped catalyst (SCR–CB mixture sample) leads, at 255 °C, to a five-fold decrease in the specific carbon oxidation rate, only a reduction by 30% is observed for the same contact with the Ca-doped catalyst (“SCR-Ca mixture” sample). As it is emphasized previously, this low effect of the doped catalyst on the carbon oxidation rate at low temperatures suggests that calcium inhibits the fast reaction. Reoxidation of V4+–OH sites in the presence of NO2, through the formation of nitrate adsorbed species, seems to be affected. Such a phenomenon limits the consumption of NO2 in the NOx SCR reaction and then increases the availability of NO2 for CB oxidation. The presence of CaCO3, observed by XRD (Fig. 1), acts as a barrier layer or through the formation of strong bonds between surface oxygen centers and the Ca metal doping. This observation was found already by Nicosia et al. [41] using XPS and thus can explain the results obtained in this study. Similarly, the low catalytic effect observed at temperatures greater than 400 °C with the Ca-doped catalyst compared with results obtained with the undoped catalyst reveals a lower proximity of V and carbon sites. This behavior agrees with the aforementioned propositions.

Specific reaction rate of carbon oxidation versus temperature of the different samples (CB (●), Ca2%-CB layer R (▲), Ca2%-CB layer D (■), and Ca2%–CB mixture (◆)): (a) T < 400 °C; (b) T > 400 °C (900 ppmv NO; 100 ppmv NO2; 1000 ppmv NH3; 15% b.v. O2; 8% b.v. H2O; 90 Nl h−1; space velocity, 55,000 h−1).
4 Conclusion
Catalytic SCR experiments in off-road conditions were performed using a commercial V-based SCR catalyst. The effect of the presence of CB in loose or tight contact with the catalyst was investigated. No significant impact of the presence of CB on NOx reduction activity was observed in the SCR operating temperature range 250–400 °C. However, in the same conditions, the catalyst exhibits a negative effect on the carbon oxidation rate attributed to a lack of NO2, consumed by the fast SCR reaction. At temperatures greater than 400 °C, the presence of carbon in the reactor leads to a decrease in NOx conversion. The extent of this inhibition of soot on NOx reduction was related to the amount of carbon present in the reactor. On the contrary, in the same temperature range (T > 400 °C), the vanadia-based SCR catalyst exhibits a catalytic effect on carbon oxidation rate. A redox mechanism, which competes with the redox cycle of the SCR mechanism, was proposed.
The impregnation of 2 wt % of calcium on the V-based SCR catalyst led to a dramatic deactivation of the SCR catalyst, linked to a poisoning of the regeneration step of V surface species by NO2. Doping of the SCR reduced the overall effect of the contact between carbon and catalyst for both NOx conversion and DeSoot processes.