1 Introduction
The combination of excellent properties and availability has made alumina (Al2O3) an attractive material for various applications. In particular, alumina is widely used in soft abrasive, wear-resistant coating, catalyst support, adsorbent, electrical component, and a large variety of other industrial applications. The synthesis of alumina and related materials is achieved either by traditional ceramic methods or by wet chemical methods like sol–gel, hydrothermal, precipitation, spray drying, spray pyrolysis, and so forth. Most of these methods generally require numerous synthetic steps, special equipments, and energy-demanding protocols. To overcome these drawbacks, a technically simpler and less costly effective chemical synthetic route has been developed in the mid-1980s [1,2]: the so-called “solution combustion” (SC) or “solution combustion synthesis” (SCS). This process was accidentally discovered by Kingsley and Patil [3] when they reacted aluminum nitrate hydrate (Al(NO3)3·9H2O) and urea (CH4N2O) (as fuel). On the basis of this unlooked-for experiment, the SC method was explored and a large number of oxides were prepared [4–8]. Combustion is an exothermic redox reaction that requires an oxidizing agent (Ox) and reducing agent (Red). Metal nitrates are used at a large scale and considered as essential oxidizing agents for this SCS. Other products as glycine and citric acid can also be used as reducing agents (fuels). The SC method involves applying the thermochemical concepts of propellant chemistry developed by Jain et al. [9]. These concepts are based on the estimation of the elemental stoichiometric coefficient (ϕe). According to Jain et al. [9], ϕe is determined by the following Eq. 1:
(1) |
The combustion reaction is greatly influenced by several parameters such as the chemical precursors, the elemental stoichiometric coefficient (ϕe), the pH value, and the method for the reaction initiation. The influence of these parameters on the SC process is explored in terms of combustion sustainability, reaction exothermicity, and propagation rate of the reaction front. The properties of the SC synthesized materials, such as crystalline phase, particle size, morphology, surface area, and agglomeration degree are mainly governed by the combustion enthalpy and the volume of gases generated during the combustion process. These two factors operate in a synergetic way on the physicochemical properties of the SC products, and they can be varied to modulate and obtain the desired material properties. Typically, a high combustion temperature results in a high crystallinity, large particle size, extensive agglomeration, and low surface area, whereas the rapid generation of a large volume of gases contributes to the effective dissipation of the heat from the bulk of the material, limiting the interparticle contact, and enhancing the porosity and the surface area of the products. The possibility of tuning the combustion parameters offers remarkable opportunities for the synthesis of a wide variety of technologically useful materials. However, the exothermic reaction characteristics such as high combustion temperature and fast heating/cooling rate are the key parameters to obtain materials with improved morphological and structural properties.
A wide range of advanced Al2O3-reinforced materials with interesting magnetic, dielectric, electrical, mechanical, catalytic, luminescent, and optical properties were obtained by the SC process [10–14]. In particular, the SC preparation method has been successfully applied for the synthesis of advanced solid catalysts, because the combustion reaction leads to products characterized by a chemical composition homogeneity, high sintering ability, fine-particle size distribution, and enhanced textural properties. Al2O3-based catalysts can be divided into two categories: bulk and supported catalysts. In the first group, Al2O3-based bulk catalysts include mixed oxides. In the second group, an active phase (generally a metal or metal oxide) is deposited onto the alumina support. Compared to the conventional catalyst preparation routes, the deposition of the active phase on a support by the SC method is characterized by low temperature and consequently by a slow kinetics, which seems to promote a good dispersion of the metal/metal oxide species on the support surface. Al2O3-based catalysts are particularly used in gas-phase catalytic reactions, including methane or alcohol reforming, hydrogenation and oxidation reactions, and automotive exhausted gas emissions treatment [13,14].
The interest in combustion synthesis has been on a steady increase and several research articles on the synthesis of alumina-based materials have been published over the last 30 years. However, there are still some issues concerning the management of the reaction products during the synthesis, the request of a calcination step after the synthesis, and the lack of fundamental modeling studies on the existing combustion synthesis processes and their applicability to small-scale synthesis. Many efforts have been made to overcome these encountered limitations and new approaches based on the SCS method are currently being developed.
The objective of this work was to help an easy identification of the more adapted modus operandi to prepare alumina-based materials with the required proprieties and composition by the SC method. The remainder of this review article reported on the most relevant research articles related to the combustion synthesis. A brief summary on alumina and related materials synthesized by the SC method is presented, along with summaries of their properties and applications. The process details, the reaction parameters, and the recent advances of this method are discussed.
2 SCS of alumina
SC has been used to prepare Al2O3 nanopowders using aluminum nitrate as an oxidizing agent. The characteristics of the SC-derived products (crystalline phase, particle shape, surface area, and crystallite size) depend on the starting fuels, the elemental stoichiometric coefficient (ϕe), the pH of the solution, and the method applied for the reaction initiation. In this section, the SCSs of pure alumina performed during the last 30 years are reported in Table 1.
SC approaches for preparation of Al2O3 in the past 30 years, listed in a chronological order.
Author | Composition of the combustion mixture | Method of reaction initiation | Process | Phase/particle shape/size/surface area | Major findings |
Kingsley and Patil [3] |
|
|
|
|
|
Chick et al. [21] |
|
|
|
|
|
Bhaduri et al. [15] |
|
|
|
|
|
Pathak et al. [26] |
|
|
|
|
|
Ozuna et al. [19] |
|
|
|
|
|
Chen and Haung [20] |
|
|
|
|
|
Toniolo et al. [22] |
|
|
|
|
|
Freitas et al. [16] |
|
|
|
|
|
Peng et al. [28] |
|
|
|
|
|
Li et al. [27] |
|
|
|
|
|
Chandradass and Kim [25] |
|
|
|
|
|
Meng et al. [17] |
|
|
|
|
|
Sharma et al. [23] |
|
|
|
|
|
Laishram et al. [29] |
|
|
|
|
|
Zhuravlev et al. [18] |
|
|
|
|
|
Farahmandjou and Golabiyan [24] |
|
|
|
|
|
Kingsley and Patil [3] have reported the first investigation on the preparation of fine particles of α-Al2O3 by combustion method. In their synthesis procedure, the stoichiometric amounts of aluminum nitrate hydrate and urea were dissolved in water, then the solution was heated in a muffle furnace at 500 °C for less than 5 min. On the basis of this experiment, a large number of studies were successively performed on the synthesis of the single-phase α-Al2O3 powders using urea [15–18], hydrazine (N2H4) [19], or carbohydrazide (CH6N4O) [20] as fuels, without any postsynthesis thermal treatments. At the same time, other authors have showed that by using glycine (C2H5NO2) [21–24], acetylacetone (C5H8O2) [25], or citric acid (C6H8O7) [26,27] an amorphous powder could be produced, and that, after annealing above 1100 °C, it could be transformed into α-Al2O3. Zhuravlev et al. [18] have used thermal analysis and IR spectroscopy methods to measure the reaction temperature reached during the combustion reactions of the aluminum nitrate–urea mixtures. The temperature in the reaction zone was recorded by a special program using a Pt/Pt – 10 Rh thermocouple. The formation of α-alumina was detected at temperatures ranging between 600 and 800 °C. In particular, the combustion temperature of the aluminum nitrate–urea system was higher than the one for aluminum nitrate–glycine mixtures (Fig. 1), and thus urea seems to be the most convenient fuel to be used for the combustion synthesis of α-Al2O3.
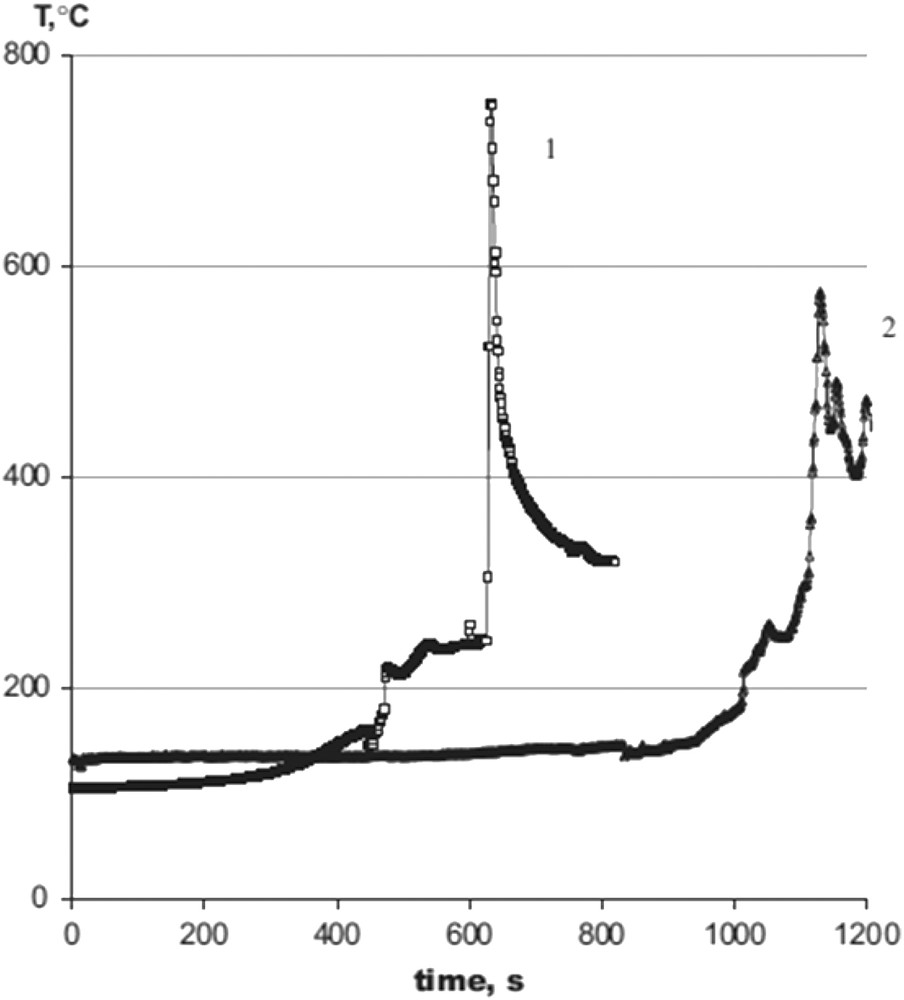
Adiabatic combustion temperature evolution in (1) aluminum nitrate–urea mixture and (2) aluminum nitrate–glycine mixture in stoichiometric proportions. Reprinted from Ref. [18].
The morphological and textural properties of SC-derived products (particle shape, surface area, and crystalline size) vary depending on the fuels nature (Fig. 2). In the presence of urea, well-crystallized α-Al2O3 powders with a surface area ranging from 5 to 115 m2/g were obtained. α-Al2O3 powders were characterized by nearly hexagonal platelet particles (Fig. 2a) [3,18,19] with sizes ranging from 200 to 800 nm [3,19]. Other fuel-types produce amorphous powders with different nanoparticle morphologies; the aluminum nitrate–glycine combustion product presents spherical-shaped particles [23,24] (Fig. 2b) with a diameter size in the range of 35–80 nm [24], and the nitrate–citric acid combustion product displays particles with irregular shapes (Fig. 2c) [27].

Transmission electron microscopy (TEM) and scanning electron microscopy (SEM) micrographs of Al2O3 powders prepared by SCS from (a) aluminum nitrate–urea solutions, (b) aluminum nitrate–glycine solutions, and (c) aluminum nitrate–citric acid solutions calcined at 1050 °C for 2 h. Reprinted from Refs. [3,24,27].
As previously reported, a wide variety of fuels are available for the combustion synthesis method. However, the ignition characteristic of various fuels differs in relation to the chemical activity of the ligand groups of the fuel molecule. The ignition character of a fuel can effectively affect the exothermicity of the combustion reaction (enthalpy and flame temperature), the burning rate, and the amount of gases generated during combustion. Depending upon the fuel used, the combustion reaction will be flaming type (volume combustion), nonflaming type (smoldering or layer-by-layer combustion), or explosive type. In case of the use of urea, the combustion reaction is flaming type, manifests with a high flame temperature (>1000 °C) and high burning rate. The observed high flame temperature is due to the exothermic reaction between the gaseous decomposition products of aluminum nitrate solutions, as nitrogen oxides (NOx) and urea, as isocyanic acid (HNCO), ammonia (NH3), and carbon dioxide (CO2) species. Because of the high flame temperature, the particles undergo slight sintering resulting in larger agglomerated particles. Although the particles are agglomerated, the crystallite sizes will be in the submicron/nanosized range because of the short duration of heating. By changing the fuel from urea to glycine, the combustion reaction is much controlled, follows a smoldering type and propagates slowly from one layer to another. In this case, the combustion reaction is characterized by a reduced flame temperature (<1000 °C), slow burning rate, and a large amount of gas. Alumina prepared by the combustion of glycine has larger surface areas and smaller particle sizes, mostly in nanosize, as compared with the one prepared by the combustion of urea. Other fuels like hydrazine and carbohydrazide that burn at lower temperatures than urea were also found to be suitable for alumina synthesis and to produce finer particles.
As general behavior, the low combustion temperature favors small particle sizes and prevents the particles from agglomeration, but leaves behind higher levels of impurities in the final products (carbon particles, hydroxides, carbonates, etc.). It is interesting to note that urea is still among the most attractive fuels studied for the combustion synthesis of alumina and related oxides, resulting in the formation of highly thermally stable, pure, and homogeneous powders, contrary to others fuels that need further thermal treatments at high temperatures to reach a high purity of the final products.
Bhaduri et al. [15] have examined the effect of a fuel/oxidizing agent ratio on the phase formation using different compositions of aluminum nitrate–urea solutions, in stoichiometric and off-stoichiometric proportions. They reported that the molar ratio is crucial in the nucleation of the alumina crystalline phases. Furthermore, Freitas et al. [16] have used an infrared pyrometer to measure the reaction temperature during the combustion of different aluminum nitrate–urea composition mixtures. The authors showed that by diminishing the urea amount a decrease in the combustion temperature was observed, and consequently, particles with smaller size that easily agglomerate were produced.
Meng et al. [17] have studied the effect of the fuel composition on phase stability, morphology, and crystallites size of the synthesized alumina. In this investigation, aluminum nitrate and urea were the main reagents used; starch ((C6H10O5)n) or ammonium nitrate (NH4NO3) was added as a fuel additive. By adding ammonium nitrate, the authors obtained well-crystallized α-Al2O3 powders with fine particles in the size range from 20 to 800 nm. However, the addition of starch led to an amorphous powder, which was transformed into well-crystallized α-alumina with a small crystalline size (∼30–50 nm) after heat treatment in a muffle furnace at 1100 °C for 1 h.
Pathak et al. [26] have showed that the morphology of the synthesized powder could be affected by varying the pH of the parental solutions. They suggested that the increase in nitrate ion concentration at low pH (2, 4, and 6) leads to a slow decomposition of the precursors, thus resulting in flaky powders. At a high pH value (10), a rapid decomposition of the precursors takes place and a powder consisting of well-divided nanoparticles is produced. The same result was obtained by Peng et al. [28] during their study on the effect of the precursor solution pH for the aluminum nitrate–glycine combustion route.
Ignition is also an important step of the SCS. Different devices, such as muffle oven [3,15,17,23,25], hot plate [16,20,21,28], aluminum open cylindrical reactor [18], and pressure reactor [19] have been used for supplying the required energy for the preparation of SC-alumina–based materials. In recent investigations [29,30], an alternative strategy for SC-reaction ignition based on microwave heating has been developed. Laishram et al. [29] have compared two ignition methods. In the first, a stoichiometric aluminum nitrate–urea solution was heated in a domestic microwave oven working at 900 W, 2.45 GHz, whereas in the second, a similar solution was heated in a preheated muffle furnace at 700 °C. The authors have identified the microwave combusted nanoparticles as α-Al2O3 with fine particle size, ranging from 18 to 20 nm, and a quite uniform spherical morphology (Fig. 3a). However, the well-known furnace combustion method has produced particles of bigger size (50–90 nm), with a polyhedral morphology (Fig. 3b). During this investigation, it was demonstrated that heating by microwave favors a continuous emission of the evolving gases all along the process. Furthermore, the consequent well-controlled dissipation of the heat from the material core generates finer and more uniform particle size and smaller agglomerates.
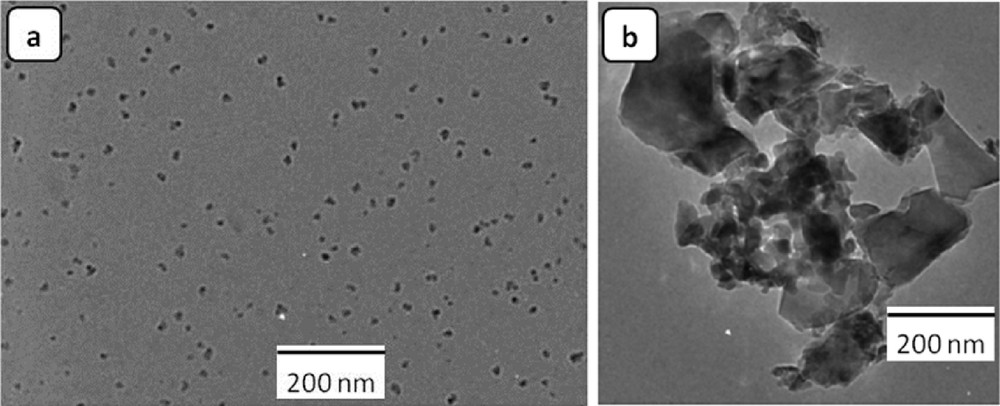
TEM images of α-Al2O3 nanopowder prepared by SCS using (a) microwave heating and (b) furnace heating at 700 °C. Reprinted from Ref. [29].
3 SCS of alumina-based materials
SC is a very promising method for the preparation of alumina composites, alumina composites/nanocomposites, alumina-supported catalysts, and metal aluminates (MAl2O4). In this section, a list of alumina-derived materials prepared by SC is presented. In addition, their properties and applications are described, focusing on the preparation procedures and the influence of the synthesis parameters (composition of initial solutions, ignition method, etc.) on the physicochemical properties of the final materials. Details of various hybrid processes based on combustion synthesis are also presented.
3.1 Alumina composites/nanocomposites
3.1.1 Alumina/zirconia
Zirconia (Zr2O3) exhibits higher mechanical properties as compared with alumina. Therefore, zirconia is often added to the alumina matrix to enhance certain mechanical properties such as toughness, strength resistance, and hardness. Zirconia-toughened alumina (ZTA) finds applications in heat engines, rocket nozzle cutting tools, and biomedical implants [31–33]. The Al2O3/ZrO2 system can be easily prepared by the combustion of aqueous solutions containing stoichiometric amounts of aluminum nitrate, zirconium nitrate (ZrO(NO3)2), and carbohydrazide [34] or urea [35]. The combustion-derived powders, obtained by using carbohydrazide as fuel, showed improved mechanical properties such as toughness and hardness. A modified SC approach has been adopted by Aruna and Rajam [36] in the preparation of nanosized ZTA composite, using the corresponding metal nitrates as oxidizing agents and a mixture of fuels consisting of ammonium acetate (C2H7NO2), urea, and glycine. Tahmasebi and Paydar [37,38] have reported different strategies for the preparation of Al2O3/20 wt % ZrO2 nanocomposite powder. In a first approach, different fuel mixtures including urea, ammonium acetate, and starch were used. The authors suggested that an excess of starch, used as fuel, could diminish the exothermicity of the combustion reaction carried-on with conventional heating methods, thus producing a nanostructured ZrO2/Al2O3 powder with well-dispersed alumina and zirconia nanoparticles and small crystallite size (<20 nm) (Fig. 4a,b) [37]. In a second approach, a microwave-assisted SC technique, using urea as fuel, was proposed. This process resulted in finer crystallites as compared with the previous case [38], with a narrow particle size distribution and a well dispersion of zirconia nanoparticles in the alumina matrix (Fig. 4c).

TEM images of ZTA powder prepared by SCS using (a) urea + conventional heating method, (b) urea + 5% starch + conventional heating method, and (c) urea + microwave heating method. Reprinted from Refs. [37,38].
3.1.2 Alumina/ceria
The alumina/ceria (Al2O3/CeO2) system is currently receiving great attention in the field of catalytic converters for the treatment of vehicle exhaust gases [39,40]. The ability of CeO2 to reversibly exchange oxygen is a key feature in this application. Moreover, the Al2O3/CeO2 system can act as an excellent support system for acid catalysis [41,42]. An active Al2O3/CeO2 catalyst for carbon monoxide (CO) oxidation was obtained [43] in a one-step microwave-induced SC from metal nitrate mixtures with urea as fuel. By using the fuel mixing approach and tuning the ratio between glycine, urea, hexamine (C6H12N4), and oxalyldihydrazide (C2H6N4O2), Deshpande et al. [44] were able to selectively produce CeO2–Al2O3–CeAlO3 mixed oxide for CO oxidation. Similarly, the CeO2–Al2O3–CeAlO3 system was prepared by Venâncio and de Miranda [45] as a solid oxide fuel cell functional anode material. The CeO2–Al2O3–CeAlO3 electrocatalyst was obtained starting from metal nitrates mixed with citric acid, as fuel. Ngoc Nhiem et al. [46] have prepared nanostructured Al2O3/CeO2 catalyst with Ce/Al molar ratio of 1:9, 2:8, 3:7, 4:6, and 5:5, then calcined at 850 °C, for the oxidation of CO, by gel combustion method, using polyvinyl alcohol ((C2H4O)n) and metal nitrates as starting materials. A conversion of 99.7% was achieved for CO oxidation at 160 °C with a catalyst with Ce/Al molar ratio of 1. This conversion temperature was significantly lower than the reported value for Al2O3/CeO2 system prepared by the classical combustion method, using urea as fuel [43], or a fuel mixture containing glycine, urea, hexamine, and oxalyldihydrazide [44].
3.1.3 Copper/alumina
Copper exhibits excellent electrical and thermal conductivities. Pure copper has, however, low tensile strength and elastic modulus. The addition of nanoscale alumina particles to copper matrix can improve the mechanical properties of copper without affecting its electrical conductivity [47–49]. Therefore, copper/alumina (Cu/Al2O3) nanocomposites have attracted attention for their potential use as high-performance electrode materials for industrial spot welding [50]. A Cu/Al2O3 nanocomposite was obtained in one-step SCS from an aqueous solution mixture of copper nitrates (Cu(NO3)2), aluminum nitrates, urea, and graphite [51]. Graphite was initially added to prevent oxidation of copper into copper oxide after the completion of the combustion reaction. It was noted that the combustion led to a good dispersion of the nanosized alumina on the copper matrix. Park et al. [52] have prepared bulk Al2O3 with well-dispersed Cu phase, using combustion of metal nitrates and urea solutions, followed by a reduction treatment, to reduce CuO to Cu. Also in this case, the combustion route showed good results in the efficient dispersion of fine Al2O3 particles.
3.1.4 Other alumina composites
Similarly, a variety of alumina composites, like the Al2O3–SiO2 mullite system, have been prepared by the SCS method [53]. Additives like MgO, ZrO2, TiO2 (0–5 wt %), and rare earth metal oxides like Y2O3, La2O3, and CeO2 were investigated to examine their effect on the mullite sintering [54]. The mullite–cordierite composites (MgO–Al2O3–SiO2) have also been prepared by the combustion of aluminum nitrate, magnesium nitrate (Mg(NO3)2)/magnesia (MgO), fumed silica (SiO2), and urea heterogeneous mixture at 500 °C [55]. Ajamein and Haghighi [56] have recently studied the microwave-assisted SCS of various CuO–ZnO–Al2O3 nanocatalysts. These synthesized materials were applied for the steam reforming of methanol, using metal nitrates, and sorbitol (C6H14O6), ethylene glycol (C2H6O2) [57], or urea [58], as fuels. The schematic representation of the microwave-assisted SCS of CuO–ZnO–Al2O3 nanocatalysts is shown in Fig. 5. Nasiri et al. [59] have studied the effect of the alumina content on the superparamagnetic properties of a Ni/Al2O3 nanocomposite synthesized starting from Al(NO3)3·9H2O, Ni(NO3)2·6H2O, graphite, and urea gel. Graphite is added to the solution to prevent the oxidation of metallic nickel at high temperature. By increasing the alumina content from 3 to 45 wt %, smaller nickel particles and higher superparamagnetic properties could be obtained. Naemi et al. [60] have produced Ag/Al2O3 nanocomposite, containing 1–10 wt % of metallic Ag, using metal nitrates–ammonium carbonate ((NH4)2CO3) solutions, ignited in a preheated furnace at 400 °C, followed by an annealing stage at 900 °C for 2 h.

Preparation of CuO–ZnO–Al2O3 nanocatalysts by SCS using sorbitol, ethylene glycol, or urea as fuels. Reprinted from Ref. [56].
3.2 Alumina-supported catalysts
3.2.1 Nickel/alumina
Several research groups have used combustion synthesis to prepare a series of Al2O3-supported nanoscale Ni catalysts. These catalysts were used in various industrial catalytic processes, including reforming reactions and ethanol decomposition. Roy et al. [61,62] have studied the effect of preparation methods and surface treatment of an SC alumina support on the performance of nickel/alumina (Ni/Al2O3) catalysts for ethanol reforming. First series of Ni/Al2O3 catalysts with different Ni loadings (2, 5, and 10 wt %) were prepared by the sol–gel method. For the second series, the Al2O3 support was prepared by the SCS method. Then, Ni (2, 5, and 10 wt %) was dispersed on the support by a standard wet impregnation method. Before the catalytic run, the free NiO particles on the support surface were reduced under hydrogen flow. The Ni/Al2O3 catalysts synthesized by the combustion method presented a higher metal dispersion and ethanol conversion, as compared with those prepared by the sol–gel method [61]. To study the effect of surface modification, 10 wt % of Ni was dispersed on both modified and unmodified SC powders using the standard wet impregnation method, and then the samples were thermally treated at 350 °C. The surface modification of Al2O3 carried out by plasma pretreatment led to a Ni catalyst with enhanced catalytic activity and selectivity [62]. Similarly, Cross et al. [63] have prepared dispersed Ni nanoparticles on γ-Al2O3 support for ethanol decomposition reactions. In a typical experiment, γ-Al2O3 pellets with a ring geometry were immersed into a reactive solution of nickel nitrate hydrate (Ni(NO3)2·6H2O) and glycine for 1 s to 30 min, and then placed on a hot plate maintained at 500 °C to initiate the combustion. To keep the metal dispersion, the catalyst pellets were reduced with hydrogen at 300 °C. The authors have reported that short impregnation times lead to a nonuniform distribution of Ni into the pellets, thus negatively affecting the catalyst selectivity to hydrogen, during ethanol decomposition. Zhao et al. [64] have prepared Ni/Al2O3 catalysts with various Ni contents (from 10 to 50 wt %) by the SC method, and 30 wt % Ni/Al2O3 catalyst by the impregnation method, for CO methanation. Before the reaction, the catalysts were heated under H2 flow to reduce NiO to metallic Ni. SCS-derived catalysts exhibited a higher catalytic activity than that of 20 wt % Ni/Al2O3 catalysts obtained by the classical impregnation. The SC catalysts displayed good temperature stability and total CO conversion already at 320 °C. Zeng et al. [65] succeeded in further improving the catalytic activity of Ni/Al2O3 catalysts up to 100% conversion of CO, in the 300–320 °C range, by adding titanium (Ti) species with loadings varying from 1 to 5 wt %.
In the same context, Gao et al. [66] have prepared Ni/Al2O3 catalysts (with 20 wt % Ni loading) by microwave-assisted SC using urea, glycine, ethylene glycol, or citric acid as fuels as illustrated in Fig. 6. The catalysts were then tested in CO methanation. The microstructure and performance of the reduced Ni/Al2O3 catalysts seem to strongly depend on the type of fuel used during the synthesis. Further studies were carried out by Gao et al. aiming to evaluate the influence of the urea quantity [67] and fuel additives (ammonium acetate, starch, and polyethylene glycol) [68] on the combustion process, the microstructure, and the intrinsic catalytic activity of Ni/Al2O3 catalysts. They found that the combustion enthalpy increased with the urea/metal nitrates ratio. The presence of high urea amounts leads to a high combustion temperature, facilitating NiO migration into the Al2O3 matrix to form the NiAl2O4 spinel and that displays a low activity (Fig. 7). If ammonium acetate is used as a fuel additive the nanostructure and activity of the Ni/Al2O3 catalysts are higher than those obtained for the catalysts prepared with starch and polyethylene glycol, as illustrated in Fig. 8.
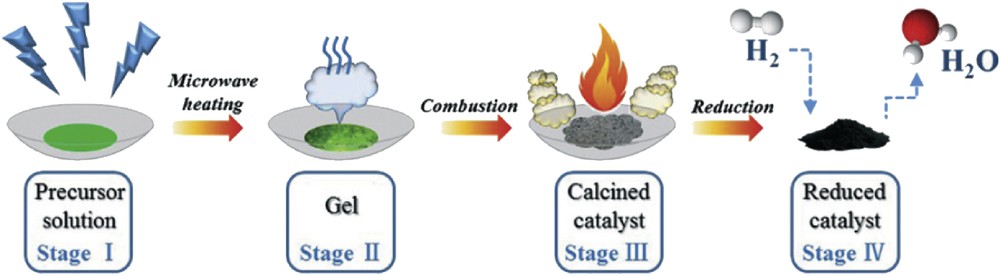
Schematic illustration for the synthesis process of Ni/Al2O3 catalyst by microwave-assisted SC. Reprinted from Ref. [67].

Schematic representation of the influence of complexation in precursor solution and combustion energetic on dispersion and migration of NiO particles into Al2O3 matrix. Reprinted from Ref. [67].
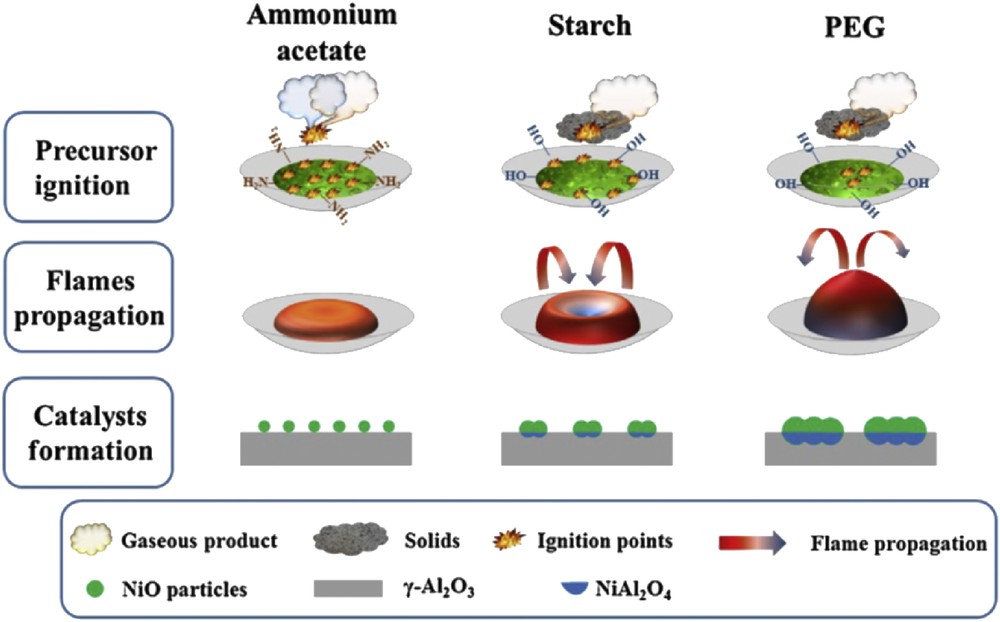
Schematic representation of precursor ignition, flames propagation, and catalysts formation during combustion process: influence of fuel additives in the urea–nitrate SCS of Ni/Al2O3 catalyst. Reprinted from Ref. [68]. Abbreviation: PEG, polyethylene glycol.
3.2.2 Cobalt oxide/alumina
Highly active supported Co oxide catalysts for methane oxidation were prepared by Zavyalova et al. [69] using a combination of wetness impregnation and combustion method. γ-Al2O3 supports impregnated with aqueous solutions of various reactive mixtures (cobalt acetate (Co(CH3COO)2), cobalt nitrate (Co(NO3)2)/cobalt acetate, and mixtures of cobalt nitrate with urea, citric acid, glycine, and glycerine (C3H5(OH)3)) were dried at 110 °C and ignited on a hot plate preheated in the 230–250 °C range. For comparison purposes, a 10 wt % Co3O4/γ-Al2O3 catalyst was prepared by the conventional impregnation method. The catalysts obtained with the combination of impregnation and combustion method from equimolar redox mixtures of cobalt nitrate/glycine or cobalt nitrate/cobalt acetate were found to have the highest activity in methane oxidation (complete conversion of methane at 400–425 °C). Another example of cobalt oxide/alumina (Co3O4/Al2O3) catalyst was obtained by SC using α-Al2O3 supports instead of γ-Al2O3 supports and tested for phenol decomposition. Activated α-Al2O3 supports were mixed with nitrate–urea mixtures, stirred for 30 min, and heated in furnace at 500 °C for 30 min [70]. The physicochemical characterizations showed that crystallites of Co3O4 and α-Al2O3 were present as two distinct chemical phases, with bigger particle size than those obtained with γ-Al2O3 supports, as reported in previous works [69] (Fig. 9).

SEM images of supported Co oxide catalysts prepared by SCS with nitrate–urea mixtures using (a) γ-Al2O3 and (b) α-Al2O3 supports. Reprinted from Refs. [69,70].
3.2.3 Pt, Pd, Ag, or Au/alumina
The SC approach was also successfully used to prepare highly dispersed noble metal such as Pt, Pd, Ag, and Au on alumina. Bera et al. [71] were the first authors to report on the synthesis of supported Pt, Pd, Ag, and Au catalysts by the combustion method. In a typical synthesis, an aqueous solution of aluminum nitrate, noble metal salts, and urea was introduced into a furnace preheated at 500 °C. The combustion process brought about spherical nanometal particles (∼7–15 nm in diameter) uniformly dispersed on large surface area α-Al2O3 powder (Fig. 10). These catalytic materials displayed a good activity in CO oxidation and NO reduction. Greca et al. [72] conceived three different methods for the preparation of Pd/Al2O3 catalysts with 0.5 and 1 wt % Pd for the selective oxidation of ethanol. In a first experiment, they used the conventional wetness impregnation method. In a second experiment, the simultaneous combustion synthesis of the support and active phase was performed. In a third experiment, the independent combustion synthesis of the support, followed by impregnation with the active phase, was applied. In particular, the alumina obtained by combustion synthesis and impregnated with 1 wt % Pd showed a high ethanol conversion (∼90%) and selectivity to acetic acid (>60%), at reaction temperatures between 180 and 200 °C.

TEM images of (a) 1% Pt/Al2O3 and (b) 1% Pd/Al2O3 catalysts prepared by SCS using aluminum nitrate, noble metal salts, and urea precursors. Reprinted from Ref. [71].
3.3 Metal aluminates
Kingsley et al. [73] reported for the first time the preparation of metal aluminates MAl2O4 (where M = Mg, Ca, Sr, Ba, Mn, Fe, Co, Ni, Cu, and Zn), using the corresponding metal nitrate and urea/carbohydrazide redox mixtures.
Metal aluminates MAl2O4 (where M = Mn, Cu, and Zn) have been produced from SC using aluminum nitrate, ammonium nitrate, metal acetate precursors, and different fuels such as urea, carbohydrazide, oxalyldihydrazide, hexamine, or glycine. The spinels obtained were nanosized (15–65 nm) oxides with a surface area varying from 40 to 180 m2/g, depending on the kind of fuel [74]. Cobalt aluminates (CoAl2O4) were prepared by an SC process using cobalt nitrate, aluminum nitrate, and urea [75], citric-acid [76], or glycine [77] as fuels. Recently, Ragupathi et al. [78] have proposed a novel green SCS to produce cobalt aluminate powders using Aloe vera plant extract as fuel. Two reaction ignition methods, microwave heating and conventional furnace heating, were applied. The authors noted that the microwave ignition provided smaller nanoparticles and a more uniform particle size distribution than those obtained in the furnace (Fig. 11). A similar approach was adopted for the synthesis of NiAl2O4 [79], CuAl2O4 [80], and ZnAl2O4 [81]. Nanoscale powders of nickel aluminates were also produced from SC using nickel and aluminum nitrates as oxidizers and urea [82], glycine [83], Sesamum indicum leaves [84], or Opuntia dillenii haw plant extract [85] as fuels.
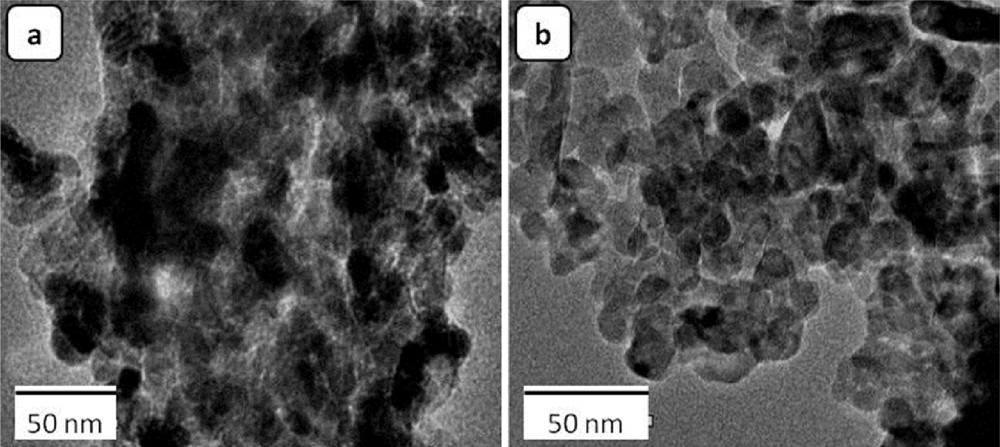
TEM micrographs of CoAl2O4 powder produced from metal nitrates–Aloe vera system prepared by (a) furnace ignition, calcined at 650 °C for 3 h and by (b) microwave heating. Reprinted from Ref. [78].
4 Conclusions
This review showed how the SCS offers a versatile tool for the formulation and preparation of a wide variety of technologically useful alumina and related oxides with improved properties.
However, despite the large number of SCSs reported and the wide variety of SC-obtained compounds, information on the reaction mechanism of combustion synthesis, the mechanism of nanocrystalline particle formation, and the modeling of combustion synthesis processes is still scarce. Also, it is clear that further research is required to better understand the thermal regime of the combustion reactions.
The rapid combustion reaction and complex nature of the SC process makes it difficult to control the nucleation and growth steps of products. In the light of these observations, researchers have developed alternative strategies for inhibiting the agglomeration and enabling the tuning of the microstructure properties in a conventional SCS. One solution is to use microwave energy in the so-called “microwave-assisted solution combustion synthesis.”
In microwave-assisted SCS, the heat is generated by the rapid change in dipole moments or dielectric polarizations of the precursor molecules, which leads to a uniform heating from the core to the surface of the material. This controlled heating brings about a fine particle size distribution, ultimate good phase dispersion, and a uniform morphology of the nanoparticles of the final material.
Another fundamental issue is related to environmental impacts of hazardous (NO2, NO, N2O, and N2O5) gases that might be released during large-scale applications of SC processes. Recently, sustainability issues have emerged, urging the need for improving the methodologies used in the SCS. The sustainability concept requires the consumption of less toxic precursors, in water or more environmentally benign solvents, using the smallest number of reagents and synthetic steps, as well as minimizing the energy consumption and the generated byproducts and waste quantities. In this context, researchers have developed an environmentally friendly approach “green SC” using plant extract (Aloe vera, Sesamum indicum leaves, Opuntia dillenii haw plant extract), as a bioreducing agent in the preparation of metal oxide precursor powders.
Following the recent improvement in the SC chemistry, the combination of the microwave-assisted SC and the green SC approaches appears to meet the demands of materials science engineering in making materials with interesting proprieties and environmental friendly.
Thanks to the joint efforts of researchers, the SC has become a promising synthesis route in modern material science and technology. Looking into the future, many promising improvements and technological developments in the nanocombustion synthesis can be expected.