1 Introduction
Quaternary ammonium cationic surfactants are diffusely applied in many fields, such as textile, cosmetic, and petrochemical industries [1–3]. In comparison with other cationic surfactants, prepared cationic surfactants exhibit superior aqueous solution properties, such as the minimum surface tension, lower critical micelle concentration (cmc), higher foaming ability, better emulsifying performances, and higher corrosion inhibition efficiency [4–6]. To identify effective different surfactant structures, great efforts have been made in seeking different surfactants and their relative properties have been found [4]. Previously different kinds of surfactants have been studied, but almost all of them focus on the ammonium part. It was reported that increase or decrease in the alkyl chain can adjust the performances of quaternary ammonium cationic surfactants [7], but the effect of the anion on the property of cationic surfactants was scarcely discussed. To develop a better surfactant, we used cetyltrimethylammonium chloride (CTAC), octadecyltrimethylammonium chloride (OTAC), and glycine to prepare two new surfactants, cetyltrimethylammonium glycine (CTAG) and octadecyltrimethylammonium glycine (OTAG), and then the surface activities were evaluated and compared with the two raw materials, including surface tension, foaming ability, emulsification, and corrosion inhibition.
2 Experimental section
2.1 Materials
CTAC, OTAC, and glycine were purchased from the China National Pharmaceutical Group. Other chemicals were purchased from Xi'an Chemical Reagent Factory and used without further purification.
2.2 Synthesis of CTAG and OTAG
Using methanol as a solvent, sodium hydroxide reacted completely with CTAC and OTAC, respectively, (at a molar ratio of 1:1) at room temperature. The supernatant and glycine (at a molar ratio of 1:1) were refluxed for 2 h with stirring, and the mixture was evaporated and dried. Finally, two new surfactants, CTAG and OTAG were obtained. Fig. 1 shows the synthetic chemical equations for CTAG and OTAG.
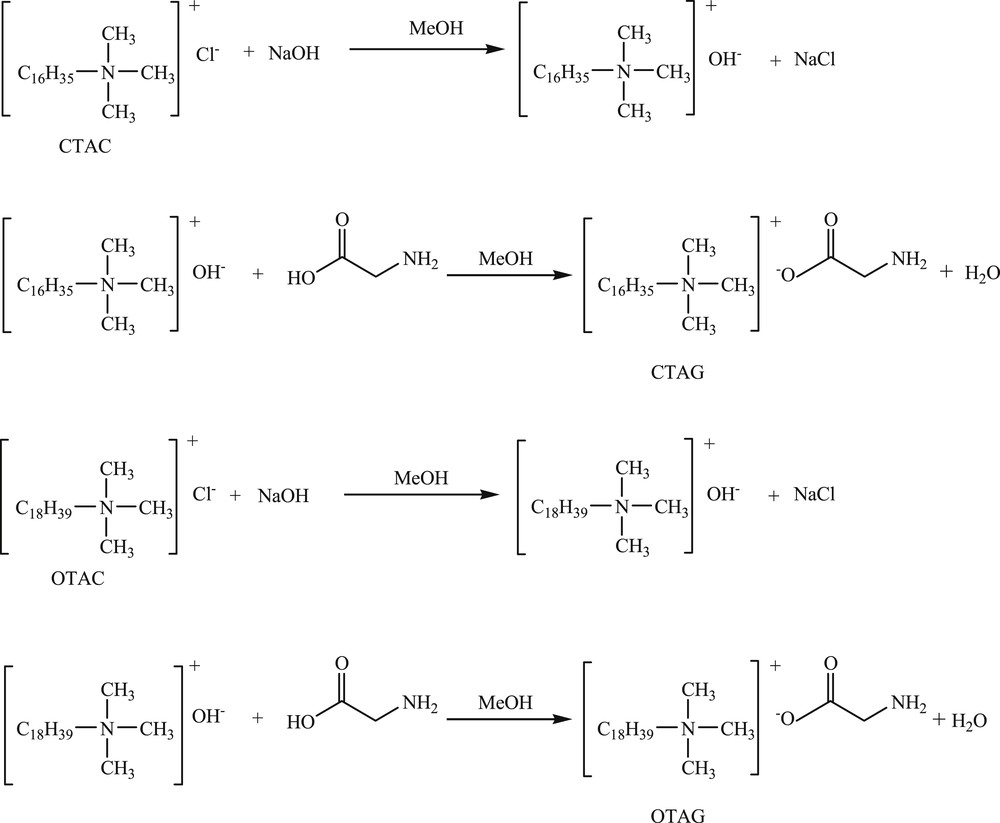
Synthetic chemical equations for CTAG and OTAG.
2.3 Surface tension measurement
The hanging ring method is one of the most used methods to measure the surface tension of different surfactant solutions. At room temperature, the different surfactant solutions prepared with a concentration range of 100–5000 mg/L had surface tension measurement using a Krüss-K6 tensiometer (Krüss K100, Germany) [7]. The platinum ring was frequently washed with distilled water to obtain the standard surface tension value of the distilled water. All measured values of surface tension were repeated three times to reduce the error [8].
2.4 Foaming ability measurement
Foaming ability was generally measured using the Waring Blender method. A 100 mL solution was poured into a 1000 mL container with a high speed stirrer, in which the stopped foam height represents the foaming ability of the foam. The stability of the foam is determined by the foam half-life time (t1/2) values, which means the time needed for the collapse of the foam to half of the foam height. Each test was repeated three times to check repeatability, and the maximum errors of the product distribution fell within a reasonable range of ±2.0%. Only the average data were reported hereafter [9,10]. In this article, a polarizing microscope (DM4500P LFD, Germany) was used to observe the aggregation state of foam films of different surfactant solutions at a concentration of 0.2%.
2.5 Emulsification
To determine the emulsification power of different cationic surfactant solutions, 10 mL of surfactant solution and 10 mL of crude oil were placed in a plug test tube with 20 mL capacity, which was placed in a regulated temperature instrument at 60 °C [11]. Subsequently the tube was vibrated for 2 min and allowed to settle [12]. The stabilization of the four emulsions was estimated by means of periods demanded for the separation of different volume of the four surfactant solutions. The dehydrated crude oil used to evaluate the emulsifying ability of the surfactant was from Yanchang Oilfield with the viscosity of 115 mPa s at 50 °C.
2.6 Corrosion inhibition measurement
A weight loss technique was adopted to evaluate the inhibiting efficiency of the four surfactant solutions with some concentration in HCl solution at 60 °C for 4 h [13]. The experiments were performed with mild steel specimens of 40 mm × 13 mm × 2 mm, and these specimens were polished to smooth plans with 360#, 600#, 1200# sandpapers before the experiment, then polished specimens were cleaned with distilled water, washed with absolute ethanol, and finally with acetone. They were dried by degreasing cold air and placed in the dryer, weighed 5 min before the experiment with an electronic balance, and the length, width, thickness, and the diameter of hole were measured with a vernier caliper. These specimens were immersed in 5% HCl solution with different surfactants at 60 °C for 4 h [14].
3 Results and discussion
3.1 Surface activity
As can be seen from the surface tension–concentration curve of the surfactant solution (Fig. 2), because the concentration of surfactant solution is lower than that of cmc, it is difficult for individual surfactant molecules to form micelles with each other, which makes the surface tension to be drastically reduced. As the concentration of surfactant solution is higher than the cmc, the surface tension will remain balanced or slightly decreased. This is because when the concentration of the solution continues to increase, the individual molecular concentration of the surfactant does not change, and the micelle increases. The surface tension method is used to measure the performance of the surfactant in the gas–liquid dispersion by comparing surface tension and dynamic stability [15]. As shown in Table 1, the surface tension of the four kinds of surfactants (CTAC, CTAG, OTAC, OTAG) at the cmc is 36.1, 37.2, 34.1, and 35.4 mN/m, respectively. The surface tensions of both CTAG and OTAG are lower than the traditional surfactants CTAC and OTAC.
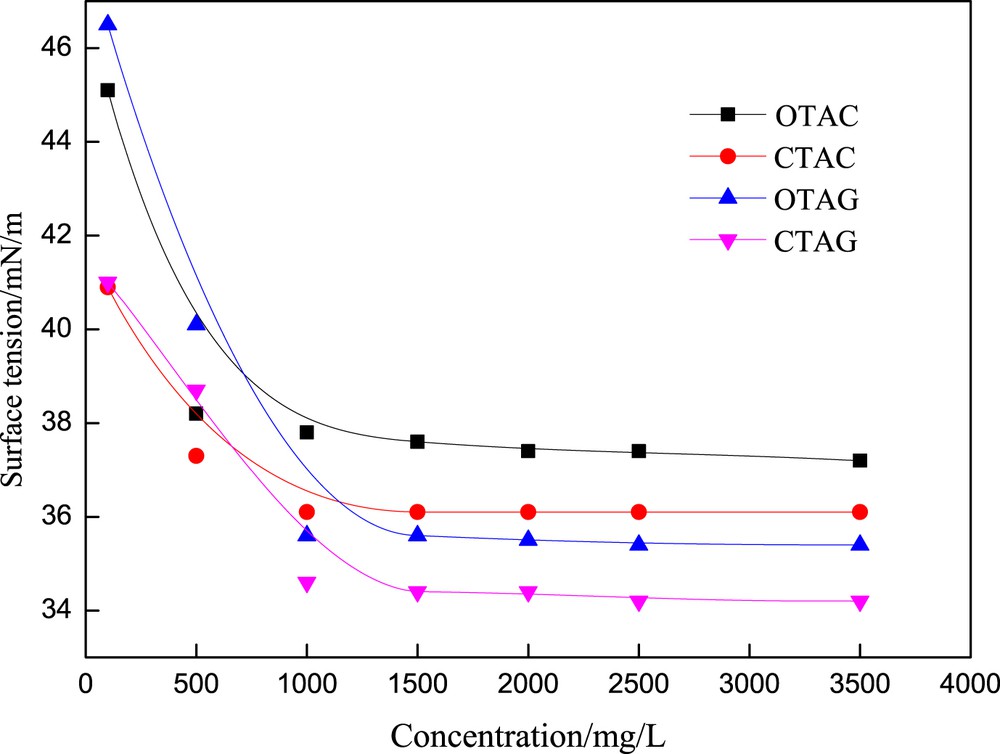
Surface tension–concentration curve of different surfactants at 25 °C.
The cmc and surface tension of different surfactants with concentrations less than 1000 mg/L.
Surfactant | cmc (mg/L) | Minimum surface tension (mN/m) |
CTAC | 98.9 | 36.1 |
CTAG | 93.3 | 34.2 |
OTAC | 81.4 | 37.2 |
OTAG | 79.9 | 35.4 |
3.2 Foaming ability
Many articles have reported that the foaming ability and foam stability were associated with the properties of the interfacial film and the interfacial tension [16–18]. When foam is generated from the same total surface area, the low surface tension is conducive to produce foam, nevertheless, the foam is likely to rupture as well. Foam stabilization is primarily by virtue of elasticity of the interface film that separates the two phases. Some studies have provided an account of the fact that foaming stabilization is well linked to the high-limit interfacial elasticity of the interface film [19,20]. The findings of Sonin et al. [21] indicated that high-frequency interfacial elasticity has a significant effect on the thin film thinning process. At room temperature, the cationic surfactants assimilate to form a bilayer with the hydrophilic head groups forming a hydration layer with the liquid film. Some researchers measured the stability according to the initial foam height (H0) and the foam height after 5 min (H5) after the mechanical agitation was stopped at room temperature; the results are shown in Table 2. The foaming ability of the four surfactants is different, and the foaming height of same surfactant increases with the increasing concentration and reaches a maximum H0 and H5 at the concentration of around 2000 mg/L. Beyond this concentration, H0 and H5 remained almost stable. Hence, 2000 mg/L is referred to as the optimal concentration of different surfactant solutions. The CTAG exhibits the optimal foaming ability, the H0 is reached 22.8 mL, and H5 is attained 22.5 mL; likewise, the OTAG exhibits the optimum foaming ability, when H0 reaches 21.8 mL and H5 attains 21.5 mL. Therefore, OTAG exhibits excellent foaming ability. To better understand the stability of the surfactants, different surfactants with concentration 2000 mg/L were measured by means of the Waring Blender method, using a 100 mL solution and distilled water as solvent with an agitation speed of 7000 rpm for 3 min. Then, the foam height and the half-life of the same concentration of different surfactant solutions were observed. Fig. 3 shows that OTAG presents an eminent foaming ability, which is consisted with the results of stirring method [22].
Foaming performance at different concentrations of different surfactants.
Concentration of surfactant (mg/L) | Foam height of Ross–Miles (mL) | |||||||
CTAC | CTAG | OTAC | OTAG | |||||
H0 | H5 | H0 | H5 | H0 | H5 | H0 | H5 | |
40 | 12.7 | 11.6 | 13.5 | 12.8 | 12.8 | 11.9 | 14.5 | 13.9 |
60 | 14.0 | 13.1 | 15.9 | 15.5 | 15.2 | 14.8 | 16.5 | 16.0 |
100 | 16.8 | 15.7 | 17.5 | 17.2 | 16.9 | 16.2 | 18.2 | 18.0 |
200 | 18.2 | 17.8 | 20.3 | 19.5 | 19.7 | 19 | 21.5 | 19.9 |
300 | 18.3 | 18.2 | 21.8 | 21.5 | 20.5 | 20.2 | 22.5 | 22.4 |

The foaming performance of different surfactants with same concentration.
3.3 Microstructure of foams
Optical microscopy is used to characterize the microstructures of a large amount of foam produced by the four surfactant solutions with an agitation speed of 7000 rpm for 3 min [23]. The result is shown in Figs. 4–7. It can be seen from the figures that the foam produced from different surfactant solutions has different shapes and volumes. The foam of CTAC and OTAG obviously exhibits a spherical shape, whereas the OTAG foam is still irregular polygon, which illustrates that nonsurface active anions exert a different influence on the foam microstructure. This can be attributed to the fact that the foam stability is controlled by the process of draining the liquid film. In comparison with other surfactants, the drainage process of the CTAC is the fastest. For this reason, the foam produced by OTAG can have a high stability. CTAG and OTAG have two hydrophilic groups, one is an amino (NH2) group and the other is carboxy (CH2COO−) group, such that the molecular structure makes CTAG and OTAG more hydrated than cationic and anionic surfactants. When adsorbed at the gas–liquid boundary, the molecules of the liquid film can be hydrogen-bonded or entwined with each other, so that the surface film has certain strength, thus giving a better foaming ability and foam stability.
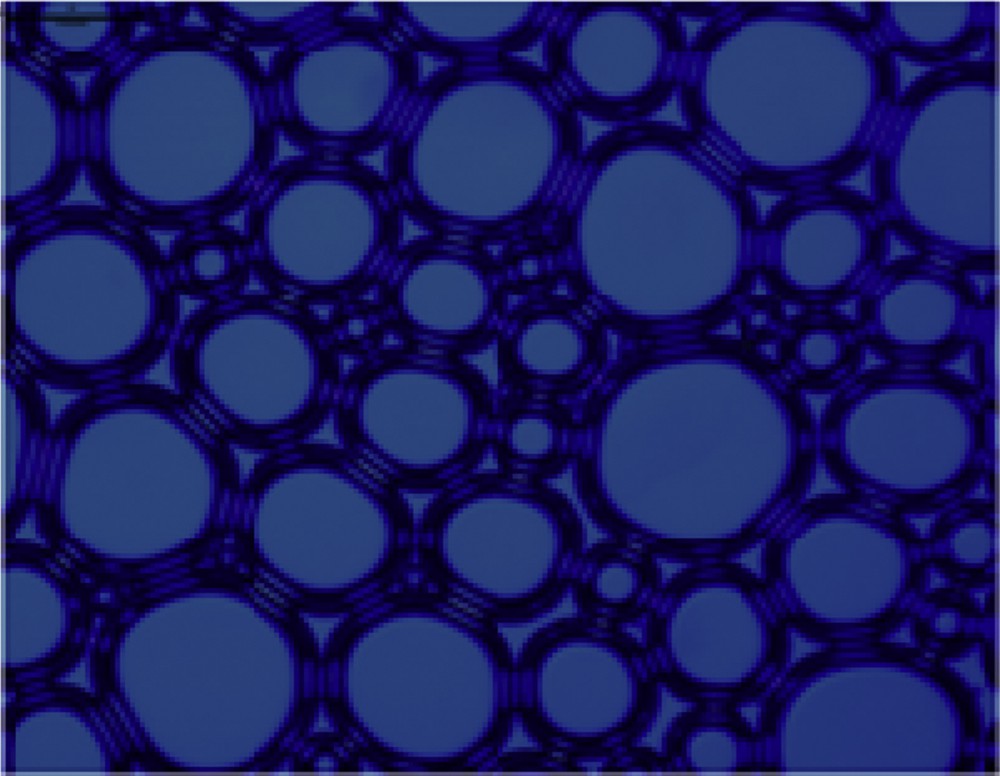
Microscope morphology of CTAC.
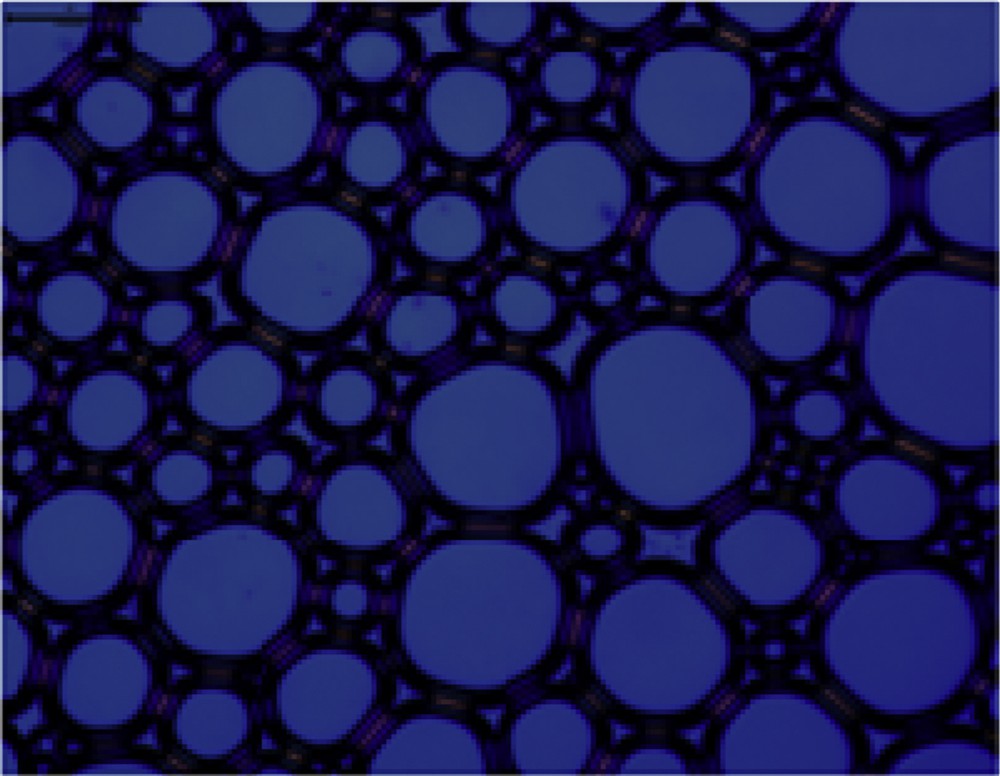
Microscope morphology of CTAG.
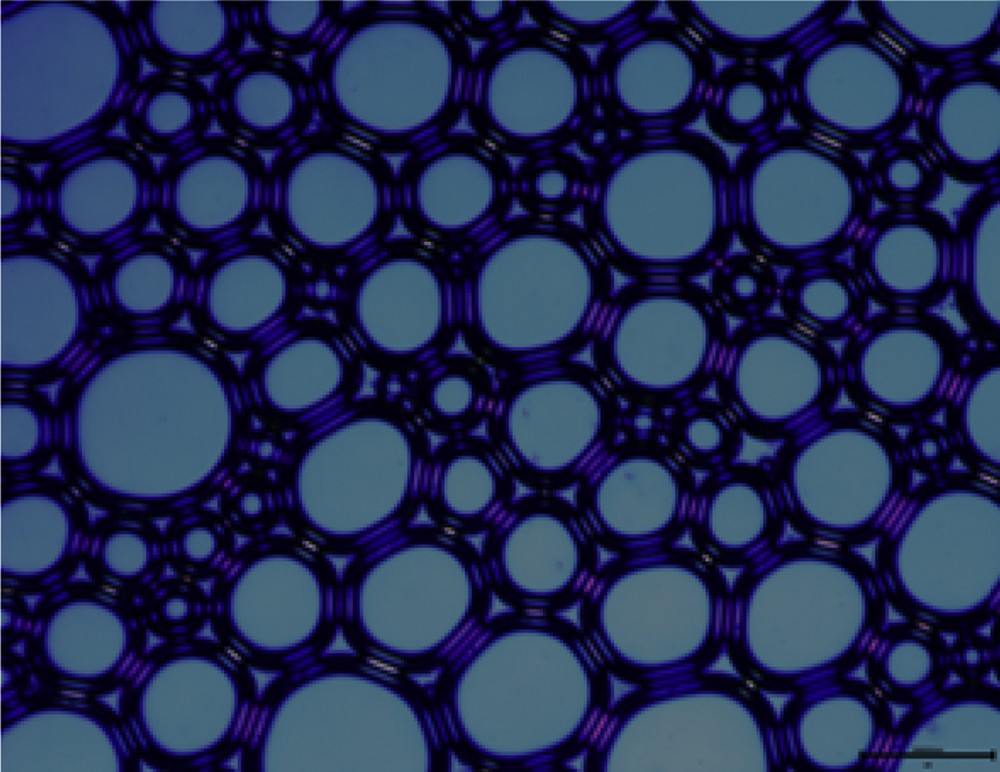
Microscope morphology of OTAC.
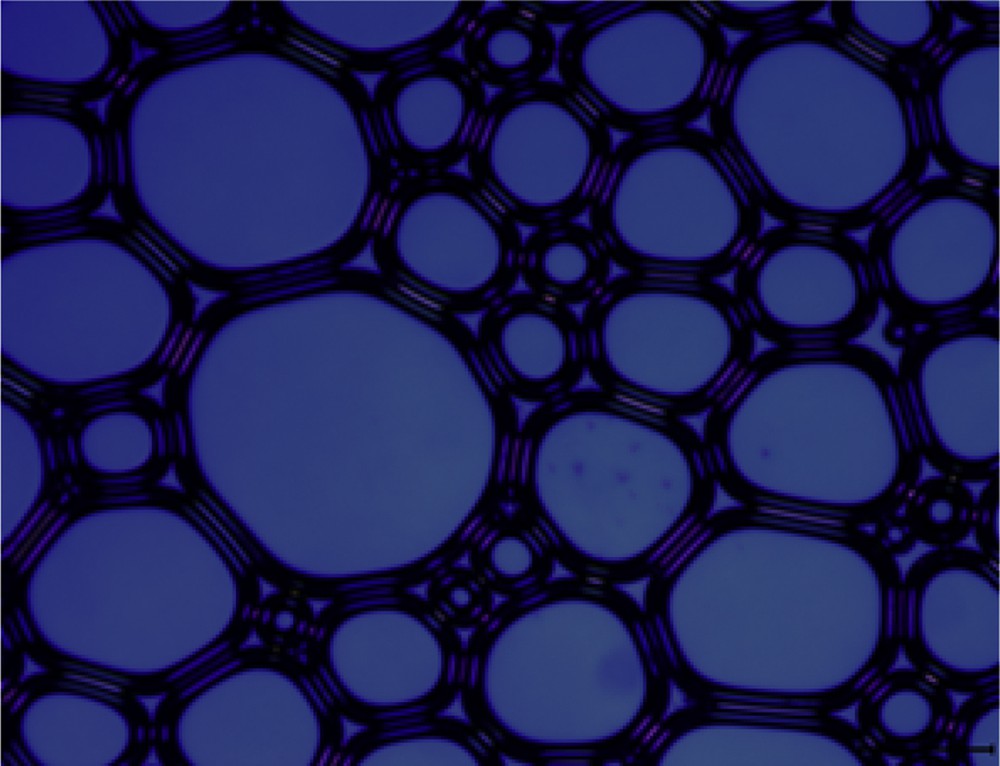
Microscope morphology of OTAG.
3.4 Emulsification power
Emulsification power is also a significant aspect of evaluating the performance of different surfactant solutions in the presence of the oil phase. The stabilization of the shaped emulsion between the surfactant solution and the oil phase depends on the chemical structure of the cationic surfactant and the oil; moreover, the emulsification power is also related to the surface activity [24]. Cationic surfactants strengthen stabilization by means of rendering an electrostatic charge on the droplet surface, thereby reducing contact between the droplets [25]. To some extent, the amount of surfactant adsorbed at the oil–water interface in oil/water emulsion depends on the extent to which the hydrophobic group of the cationic surfactant damages the structure of the aqueous phase. At the micellar concentration, the concentration of surfactant and its emulsifying ability is the strongest. Consequently, we researched four kinds of surfactants in the respective micelle concentration of emulsifying ability as shown in Fig. 8. In comparison with other surfactants, CTAG obtained the highest emulsifying ability, with the half-life time of 41.57 min. CTAG and OTAC led to 18.12 and 30.01 min, respectively. CTAC showed the lowest emulsification ability, with the shortest half-life time of 13.45 min. Compared with the four surfactants, the OTAG molecule had the largest weight, which can effectively prevent combination [26]. For the emulsification capacity, the longer time for water precipitation shows that the emulsifying ability of the surfactant is enhanced. Mainly with the introduction of an amino acid, hydrophilicity increases, the adsorption becomes saturated, the water/oil interface that forms a dense film is increased, and the interfacial film strength is large, so that the trap and emulsifying ability, which makes the time longer, becomes stronger.
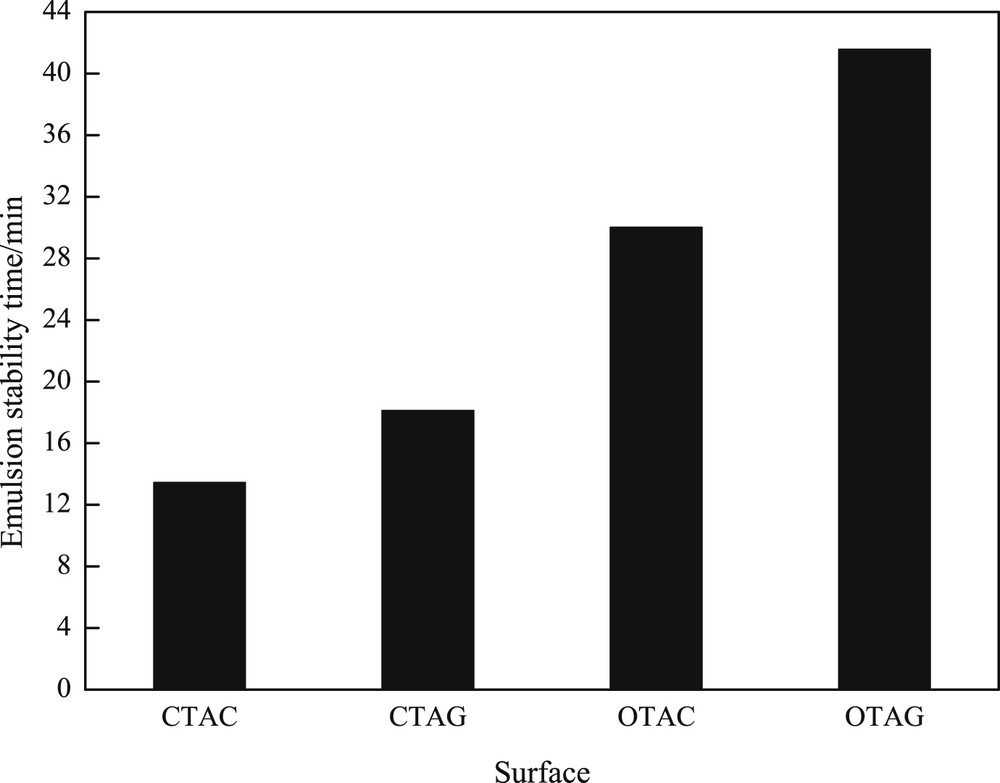
The emulsion capability of surfactants in the cmc with same concentration.
3.5 Corrosion inhibition
Corrosion of steel alloys is an extremely critical issue emerging in virtue of the corrosive surroundings, which not only affects the original metallic luster but also brings about a great deal of economic costs in many technical fields. Accordingly, some researchers have solved this issue as well as its prevention through the use of corrosion inhibitors [27]. There are many types of corrosion inhibitors, including cationic, anionic, nonionic surfactants, and so forth. [10]. In the present study, four different surfactants were estimated as corrosion inhibitors at 0.5 mg/L and reported the different efficiencies and corrosion rates in 5% HCl at 60 °C. As shown in Table 3, the maximum inhibition efficiency was observed for OTAG, followed by OTAC, CTAG, but the minimum was attained for CATC. The CTAG and OTAG surfactants have a glycine structure, which has a better corrosion inhibition effect than CTAC and OTAC. The corrosion inhibition efficiencies of CTAG and OTAG are 91.12% and 97.89%, respectively. The CTAG and OTAG corrosion inhibitors contain not only nitrogen atoms but also amino acid structures. The NH2 group can be adsorbed on the surface of the metallic materials to form a film, change the state of the metal surface and the electric double layer structure, increase the activation energy of the corrosion reaction, and generate a negative catalytic effect. The nonpolar group forms a hydrophobic protective film on the surface of the metal, which hinders the exchange of substances in the corrosion reaction, thereby reducing the corrosion rate of the metal. At the same time, the lowest empty orbital energy level of glycine is close to the highest occupied orbital energy level of the Fe interface. Electron transfer occurs between the two species, resulting in chemisorption. The amino acid molecules are adsorbed on the Fe interface, which separates the H+ and Fe interfaces. Amino acids act synergistically to achieve corrosion inhibition [28].
Corrosion inhibition efficiency and corrosion rate of the four surfactants at 20 mg/L.
Surfactants | Wcorr (g·m−2·h−1) | Ew (%) |
Blank | 17.07 | – |
CTAC | 1.93 | 88.70 |
CTAG | 1.51 | 91.12 |
OTAC | 0.96 | 94.38 |
OTAG | 0.36 | 97.89 |
4 Conclusions
In this study, we synthesized two new surfactants CTAG and OTAG using CTAC and OTAC. Because CTAG and OTAG contain amino (NH2) and carboxyl (COO−) groups, CTAG and OTAG are more hydrated than common cationic surfactants and anionic surfactants. When adsorbed at the gas–liquid interface, the molecules of the liquid film act through hydrogen bonding and electrostatic forces, so that the surface film has certain strength, thereby providing better foaming ability. The foaming ability of synthesized CTAG and OTAG surfactants is greater than those of CTAC and OTAG, and the foam half-lives of synthetic CTAG and OTAG surfactants increased by 43 and 15 s, respectively. With the structure of glycine, CTAG and OTAG have more potent corrosion inhibition effect than CTAC and OTAC, and the corrosion inhibition efficiencies of CTAG and OTAG are 91.12% and 97.89%, respectively.
Acknowledgments
The work was supported financially by the National Science Foundation of China (21808182), Scientific Research Program of the Shaanxi Provincial Education Department (18JC025) and Graduate Innovation and Practice Ability Training Project of Xi'an Shiyou University (KCS17111011).
Vous devez vous connecter pour continuer.
S'authentifier