1 Introduction
Pervaporation (PV) is a membrane-based separation system by the condensation process. PV operates at mild conditions, with no emission to the environment and no involvement of additional species into the feed stream, which make this method more desirable than the traditional method of distillation [1,2]. PV is commonly used for three applications, including (1) dehydration of organic solvents, (2) removal of dilute organic compounds from aqueous streams and (3) organic-organic mixture separation [2], among which, dehydration of organic solvents has been largely using PV scientifically and commercially. Membrane Technology and Research (MTR) is one of the companies that commercialises the PV technology for recovery of organic components from waste streams. Dehydration of isopropanol (IPA) from waste has received great attention from industries because of the high price of IPA and its uses in various industries. Separating water and alcohol using PV is an excellent idea in the chemical industry, especially in obtaining liquid fuel from biomass sources.
Pristine dense polymeric membranes for a PV system in the laboratory are commonly used to characterise the intrinsic properties of the materials. However, the limitations of these membranes, such as relatively low transmembrane flux and low mechanical strength when in contact with the solvent and high temperature, make them unfavourable to be applied in PV processes [3]. Asymmetric membrane structure, also known as thin-film composite (TFC), has been introduced to minimise the issues when dealing with dense membranes and pristine polymeric membranes. TFC membranes possess a thin selective layer supported by a relatively thick microporous substrate. TFC membranes are produced by a simple step of interfacial polymerisation (IP) reaction between aqueous and organic monomers.
IP and postmodification techniques are among the methods used by many researchers to enhance membrane performance [4,5]. IP is a simple, rapid, and easy process for depositing an ultrathin layer composite on a microporous membrane for overall performance improvement. TFC membranes are widely used in PV processes and contribute to major escalation in the separation factor [6,7]. Mohan and Kullová [8] produced TFC membranes using m-phenylenediamine (MPD) and piperazine (PIP) to react with trimesoyl chloride (TMC) and found that the MPD-TMC membranes were more stable and performed better than TFC membranes produced using PIP-TMC. Since then, numerous studies have used MPD as an aqueous monomer to fabricate more stable structures because of the chemical nature of MPD and the final physical structure of the active skin layer [9–11]. It is important to not only choose appropriate monomer pairs to produce effective TFC membranes but also support membrane properties which plays an important role. The interaction between two layers must be strong to ensure a good deposition of the TFC layer on the support membrane. Huang and McCutcheon [12] introduced TFC membranes using nylon 6,6 (N66) for reverse osmosis application. N66 has a unique balance between hydrophilicity and great mechanical strength, which are appealing properties for a support membrane to achieve high performance and robust TFC membranes.
This work aims to prepare TFC flat-type membranes using N66 as a substrate. In this work, TFC membranes were produced by the IP process via the reaction between TMC and MPD. We investigated the effect of immersion time in aqueous and organic monomer on the membrane morphology, chemical structure, hydrophilicity, and swelling.
2 Experimental
This research consisted of experimental steps to carry out the IP reaction on a substrate flat sheet between TMC and MPD monomer. The membrane coating membranes were characterised by scanning electron microscopy (SEM), energy-dispersive X-ray spectroscopy (EDX), FTIR, water contact angle, and swelling analyses.
2.1 Materials
Commercial flat sheet N66 membrane (SKU: NY013001) was obtained from Sterlitech Co. (WA, USA). Aqueous (MPD) and organic (TMC) monomers were purchased from Sigma-Aldrich, Malaysia. Hexane was procured from Merck. All chemicals were used as received without further purification. Deionised water and distilled water were used as the nonsolvents for TFC preparation.
2.2 Preparation of TFC membranes
Support membranes were dried in a vacuum oven at 60 °C for 10 min before PA thin-film deposition process. The support membranes were exposed with 1–2 wt % aqueous phase for 2–5 min at 25 °C (Table 1). After removing excess amine solution using an air blower, the membranes were immersed in a 0.1 wt % organic solution containing TMC phase solution for the IP reaction for 1–2 min. Fabricated TFC membranes were immersed in hexane solution and then in distilled water to wash away excess acyl chloride and amine solutions, respectively. The membranes were dried at 70 °C for 10 min in a circulation oven. Then, the fabricated TFC membranes underwent posttreatment by immersing in methanol for a couple of minutes.
The experiment parameters for preparing TFC membranes.
Type | Aqueous MPD solution (wt %) | Immersion time in MPD solution (min) | Organic TMC solution (wt. %) | Reaction time (min) |
Pristine | 0 | 0 | 0 | 0 |
TFC1 | 2.0 | 2.0 | 0.1 | 1.0 |
TFC2 | 2.0 | 3.0 | 0.1 | 1.0 |
TFC3 | 2.0 | 5.0 | 0.1 | 2.0 |
2.3 Scanning electron microscopy
The surface and cross section views of pristine and fabricated membranes were examined using a scanning electron microscope (Carl Zeiss EVO50) attached with an EDX unit. Cross sections of the TFC membranes were prepared by fracturing the membranes using liquid nitrogen. All samples were dried in a vacuum oven and then coated with a conductive layer, Au (400 Å) of sputtered gold before photographing.
2.4 Fourier-transform infrared spectroscopy
The formation of the TFC layer by IP reaction on the support membrane was confirmed by FTIR spectrometry (Nicolet Avatar 370 DTGS). All the TFC membrane samples were ground to make membrane pellets under hydraulic pressure. The FTIR wavelengths were recorded in the range of 4000–500 cm−1.
2.5 Contact angle
Hydrophilicity of the fabricated TFC membranes was evaluated by using a contact angle instrument known as JY-82 video contact. A droplet of 5 μl of distilled water was deposited on the surface of membranes for 10 s at room temperature. Angles were measured in five replicates at different sites of each membrane to minimise error.
2.6 Swelling measurements
Membranes were dried in an oven at 120 °C overnight before being preweighed. Membrane swelling was measured by immersing dried membranes in isopropanol mixtures of 90, 80 and 60 wt % for 24 h at room temperature. The swollen samples were taken out and wiped with a tissue paper, and the film was weighed. The degree of swelling is defined in Eq. 1 [13]:
degree of swelling (g/g of dry membrane) = (Mwet − Mdry)/Mdry | (1) |
3 Results and discussion
3.1 SEM and EDX studies
Fig. 1(a) i and 1(a) ii demonstrate the surface and cross-sectional SEM images of the pristine. The pore distribution of the pristine membrane was distinguished as a uniform structure. The uniform structure and small pore size average of 1.15 μm offer a high surface area for IP process, making the membrane an appropriate substrate for this study [14].
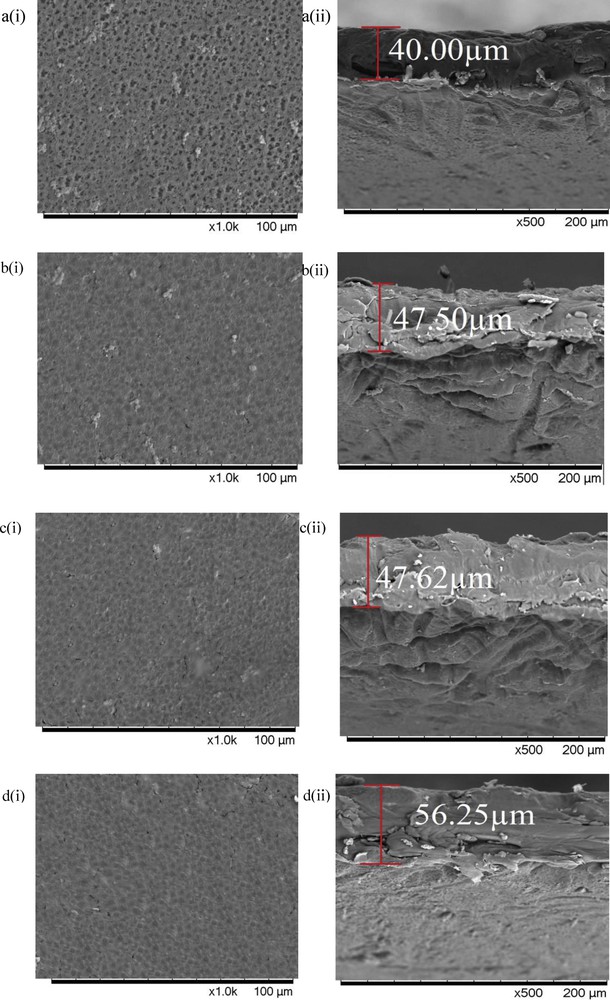
SEM images of (a) pristine, (b) TFC1, (c) TFC2 and (d) TFC3 membranes prepared from 2.0 wt % MPD and 0.1 wt % TMC solutions. (i) Top surface and (ii) cross-sectional views. SEM, scanning electron microscopy; MPD, m-phenylenediamine; TMC, trimesoyl chloride; TFC, Thin-film composite.
Fig. 1(b–d) present (i) surface and (ii) cross-sectional SEM images of the pristine and TFC membranes prepared under various immersion times in 2.0 wt % MPD (2, 3 and 5 min) and 0.1 wt % TMC solution (1 and 2 min). The thin-film thickness increased linearly with increasing contact time in MPD solution. Longer contact time between MPD and TMC enhanced the availability of MPD monomer on the surface. The degree of cross-linking reaction was also improved because there was more interaction between MPD with TMC [4]. Thus, this leads to thicker and denser TFC active layer being developed on the pristine membrane as seen from the increase in thickness from 40.0 to 56.3 μm. The polymer substrate pores must be effectively wetted during contact with the aqueous MPD solution. Impurities defect on the TFC membrane could occur if the membrane is not properly wetted in the amine solutions because of the low MPD concentration.
The polyamide thin layer successfully deposited on substrate revealed in the SEM images when the pores seem to be covered and individual pores no longer can be identified. Tsuru et al. [15] mentioned that the TFC forms a ridge-and-valley structure, and this is favourable for enhancing the permeation area. More importantly, the TFC produced must be thin and have a strong cross-linked PA layer [16]. When the immersion time in the aqueous MPD solution was increased from 2 to 3 min, more MPD species were deposited on the surface of the membranes. Eventually, during reaction, more organic monomer can react with MPD and subsequently increase the thickness of the membranes. As the membrane produced becomes thicker, the mass-transfer coefficient also escalates, which attributes to increasing selectivity of the membrane.
Fig. 2 shows the main elements of the N66 membrane and produced TFC membranes as seen from the EDX spectrum. Carbon (C) and oxygen (O) are the main elements in the N66 and TFC membranes. The highest C peak can be observed in the control group. After the PA TFC deposition, the C content of the processed sample gradually declined. Meanwhile, O content increased markedly. This result corresponds well with the results obtained by Al-Hobaib et al. [17]. The percentage of C was decreased (O increased) as the thickness of membrane increased, which confirms that TFC layers are present on the top of the membrane.
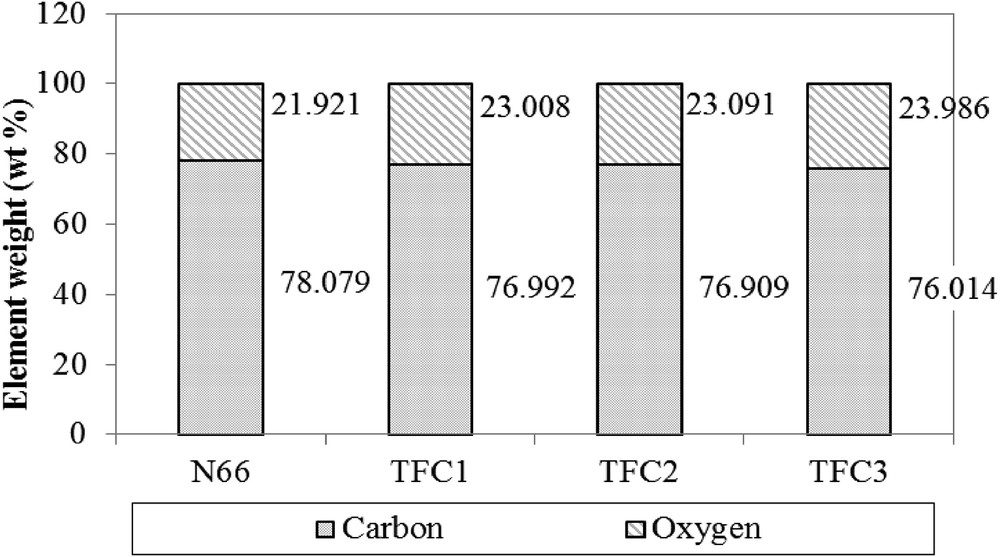
Percentage of element weight of N66 and TFC membranes using energy-dispersive X-ray spectroscopy.
3.2 Fourier-transform infrared spectroscopy studies
Fig. 3 shows the comparison between the FTIR spectra for pristine and TFC membranes (TFC1, TFC2 and TFC3). These absorption wavelengths indicate the existing nitro compound which consists of nitro functional groups inside the fabricated TFC membranes. These peaks were observed in all TFC membranes but not in the pristine membrane. The absorption band of C-N stretching at 1537–1540 cm−1 represents the amine group [18]. However, these peaks cannot distinguish between the aliphatic ring owned by a pristine membrane or fully aromatic polyamide group of TFC membranes. Aromatic breathing ring, C6H6 peaks, was identified at the 1609–1610 cm−1 where hydrogen bond of C–O and N–H stretching of amide is identified [19]. In the case of TFC3, the amine solutions may diffuse back into TMC solutions because of the longer exposure time with the TMC solution. At the wavelength of 3300 cm−1, a strong carboxylic acid displayed which indicate a strong intensity within the pristine with the TFC3 sample. These bonds are stronger than the rest of TFC membranes where they were presented by a weak O–H stretching [20]. The peak at 1250 cm−1 is attributed to the MPD introduced onto the substrate, which does not exist in the pristine membrane. More TFC formation can be observed at the peaks of 768 and 1450 cm−1. The peak at 768 cm−1 is attributed to the C–Cl stretching, while the peak at 1450 cm−1 indicates CO stretching and O–H bending of carboxylic acid.
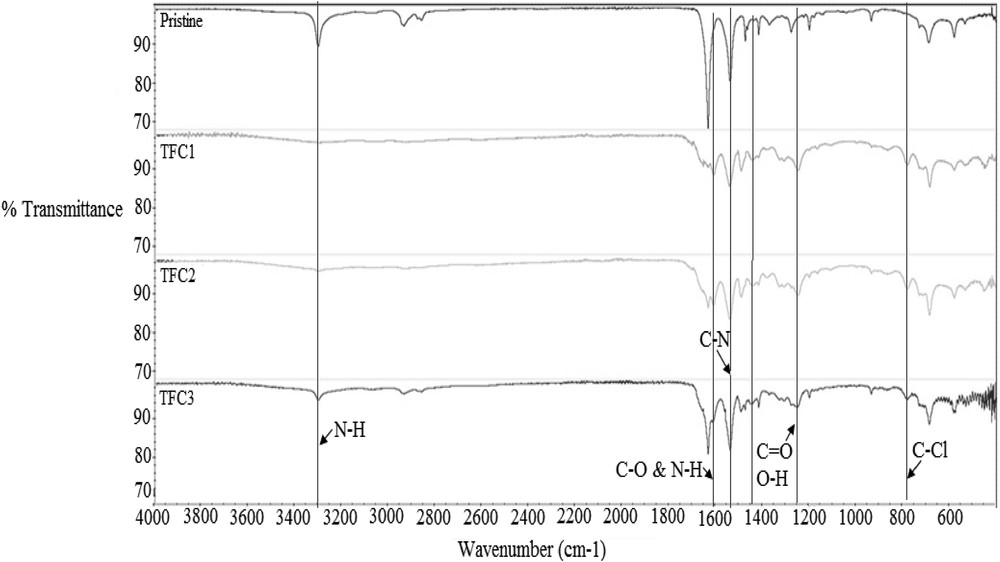
FTIR spectra of N66 and TFC membranes. FTIR, Fourier-transform infrared; N66, nylon 6,6; TFC, thin-film composite.
3.3 Contact angle measurement studies
Table 2 shows that as the immersion time in the MPD solution increased, the contact angle measurement of the TFC membranes also increased. All the membranes in this study showed a contact angle below 90°, which indicates that all the membranes are hydrophilic. Hydrophilic membranes are more selective toward water molecules rather than the solvent [21]. N66 membrane showed higher contact angle than TFC1, TFC2 and TFC3 membranes. The contact angle for pristine membrane is 60°, which is consistent with the standard contact angle of commercial membranes reported by Huang and McCutcheon [22]. This is because when the N66 substrate was coated with the TFC, the membrane surface became smoother and the pores were covered. This also indicates that the amount of amide groups formed on the membrane surface is getting higher. The hydrophilicity of the fabricated membrane not only depends on the immersion time but also the reaction time. The hydrophilicity enhancement of the TFC membranes is due to the pendant carboxylic acid groups inside the main chain. As the IP reaction time increased, the TFC membranes thickened, which contributed to the dense TFC especially for TFC2 and TFC3. This also explains the decrease in contact angle values. This result is in accordance with the results obtained by Gorgojo et al. [23]. A hydrophilic substrate is expected to hold MPD in the pores, and eventually some of the MPD may be trapped inside the substrate pores, which will reduce the interfacial reaction rate [24].
Contact angles of water for all fabricated TFC membranes at room temperature.
Type of membrane | Average contact angle value (°) |
Pure N66 | 59.2 ± 6.8 |
TFC1 | 40.3 ± 6.9 |
TFC2 | 37.9 ± 3.5 |
TFC3 | 34.9 ± 5.6 |
3.4 Effects of feed composition on membrane swelling
To study the sorption characteristics of N66 and TFC membranes, the degree of swelling of all membranes was plotted with respect to different mass percentage of water in the feed solution at room temperature. Sorption is important in PV mechanism to understand the penetration of molecules resulting from the driving force of gradient in chemical potential [25]. Chemical gradient is also expressed using partial pressure differences of the molar flux [26]. As shown in Fig. 4, the degree of swelling increased for all membrane samples with the increasing mass percentage of water in the solution. This trend is similar with those of previous studies by Thorat et al. [27] and Sajjan et al. [13] because of the strong interaction between water molecules and the membranes, which is consistent with their hydrophilic properties. The pristine membrane showed a significant degree of swelling compared with TFC membranes. This indicates that the pristine membrane has higher affinity towards water than other membranes, which can be correlated to the membrane structure. The microstructures cause the water molecules to penetrate into the membrane when the membrane is exposed for certain duration and the liquid is trapped inside the membrane's pores, which leads to a higher degree of swelling than that of the TFC membranes [28].
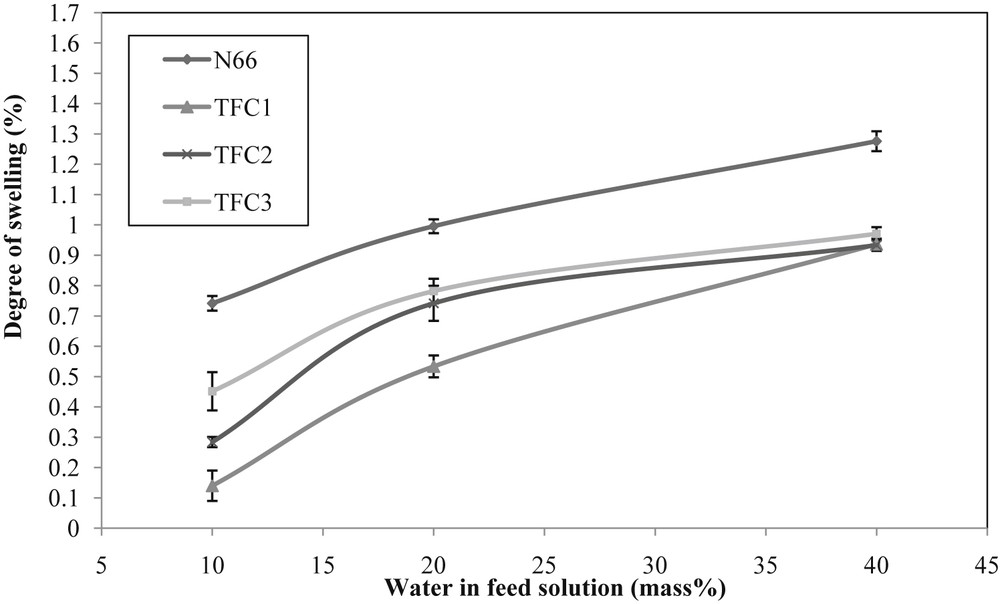
The degree of swelling of pristine and TFC membranes fabricated in various water composition in the feed solution. N66, nylon 6,6; TFC, thin-film composite.
4 Conclusion
The chemical and physical properties of pristine and fabricated TFC membranes were characterised by SEM, FTIR, contact angle and swelling analyses. Using SEM, the fabricated TFC membranes were defined by a dense structure. Increasing the immersion time from 2 to 5 min in 2 wt % MPD and immersion for 1 min in 0.1 wt % TMC solution increased the thickness of the membranes from 40.0 to 56.3 μm. Fully aromatic polyamide groups were detected at 1609–1610 cm−1 via FTIR analysis. The contact angles decreased significantly from 50° to 35° by the modification, which indicates better hydrophilic properties of the TFC membranes. In addition, continuous IPA sorption experiments for up to 24 h were carried out for pristine N66 and TFC membranes, using 40, 20 and 90 wt % water in IPA-water solutions. As a consequence, the thicker the TFC layer, the greater the swelling degree obtained.
Acknowledgements
The authors would like to thank the sponsor for the financial support for this research through grants PGRS180323 and RDU1803113.