1 Introduction
Methylaluminoxane (MAO) is the most commonly used activator for olefin polymerisation catalysed by metallocene catalysts in homogeneous conditions [1]. It is synthesised by the partial hydrolysis of trimethylaluminum (TMA) in the presence of hydrated salts like Al2(SO4)3·16 H2O, ice or water vapour. The reaction between TMA and water is highly exothermic and hence severe experimental conditions have to be followed to prevent runaway reactions. It is also reported that some amount of TMA is lost during the synthesis due to excess hydrolysis[2]. Due to the high cost of TMA as well as stringent experimental conditions to be maintained, MAO is an expensive material. In addition, large amounts of MAO with respect to transition metal complex are needed to obtain satisfactory catalytic activity in olefin polymerisation. For instance, a minimum Al/Zr ratio of 3000 is required to get an optimum catalytic activity for hex-1-ene polymerisation catalysed by racEt(Ind)2ZrCl2 [3]. For all these reasons, it is highly important to lower the expense due to MAO (aluminium) activator in olefin polymerisation for industrial applications. In the last few years, we have been conducting a systematic research in this regard. We approached the problem in two different ways, namely exploring routes to reduce the Al/Zr ratio required for obtaining the optimum catalytic activity and by exploring new cost-effective synthetic routes to MAO.
The role of MAO in the activation process of metallocene is now well established. It first substitutes at least one X ligand linked to the metal by a methyl group (alkylation step) then abstracts one X ligand (X = Cl, Me…) to form the zirconocenium active species. As shown in Fig. 1, the active species possesses one vacant site allowing the monomer co-ordination prior to its insertion into the metal–carbon bond.

Mechanism of polymerisation.
We have recently shown that the abstraction of chloro-ligands by MAO yields [MAO–Cl]– counteranions that strongly interact with the zirconocene coordinating vacant site and hence impede olefin polymerisation [4]. One way to reduce the MAO content required to form ionic active species is to use zirconocene bearing easily extractable X ligand such as methyl, benzyl or amido groups. Indeed, the activation of racEt(Ind)2ZrMe2 by MAO allows 1-hexene polymerisation with a maximum of activity at Al/Zr ratio as low as 150 [5]. More directly linked to this study, we have also recently shown that the use of ‘TMA-depleted MAO’ enables to reduce considerably the amount of MAO required for dichloro zirconocene activation [6].
Other routes allowing the reduction of concentration and cost of expensive MAO using alternate, cost-effective and less stringent experimental procedure for its synthesis have been explored. It has been recently disclosed and patented that heating aromatic ketones with TMA results in the direct formation of MAO structures (MAOb), efficient to activate transition metal complexes for olefin polymerisation [6–8]. This led us to undertake a deep study of these new approaches to MAO synthesis. This paper mainly focus on MAOb preparation through the reaction of TMA with benzoic acid and its use for racEt(Ind)2ZrCl2 activation towards ethylene polymerisation.
2 Experimental
2.1 Synthesis of MAO
In a 100 ml round bottom flask fitted with a reflux condenser, 1.35 g (11·10–3 mol) of benzoic acid was taken under nitrogen atmosphere. 5 ml of dry toluene was then added into it and was cooled to 0 °C. 14 ml of 2 M TMA solution (28.0·10–3 mol) was then slowly added over a period of 10 min. Brisk evolution of methane gas was observed. The whole solution was heated at 80 °C for 2 h. 0.4 ml of 10% MAO commercial solution was then added and the solution was heated at 80 °C. After 5 h, the heating was stopped and the solution was cooled slowly to room temperature with continuous stirring.
2.2 Polymerisation
The procedure used for the polymerisation of ethylene/α-olefins using racEt(Ind)2ZrCl2 / MAO system is described elsewhere [4,8].
3 Results and discussion
Use of TMA as alkylating agent for aromatic acids is reported in the literature. For instance TMA when heated at 130–150 °C for 24 h with benzoic acid forms t-butyl benzene [9]. The conversion of benzoic acid to t-butyl benzene involves at least three steps. First, TMA reacts with benzoic acid to remove the active labile hydrogen to form Ph(CO)OAl(CH3)2 with the evolution of methane gas. Alkylation of the carbonyl group occurs in a second step together with elimination of –O–Al– containing moiety followed by further alkylations to form t-butyl benzene (Fig. 2).
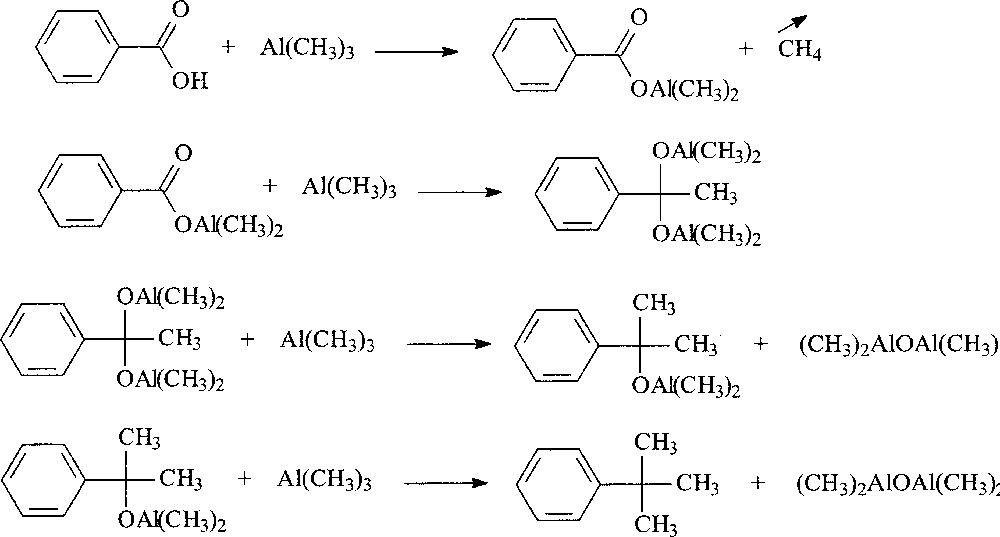
Reaction between TMA and benzoic acid.
A benzoic acid:TMA ratio of 1:5 is considered to be the optimum ratio required for the complete alkylation of benzoic acid yielding t-butyl benzene. We have found that the solution thus obtained, containing –Al–O– moieties (MAO-type) was inefficient in activating metallocene catalysts.
Following the observation that full alkylation of benzophenone occurs at a lower TMA ratio in presence of catalytic amount of MAO and that the resulting solution could activate metallocene catalysts towards olefin polymerisation [7,8], we explored the possibility of using benzoic acid as the organic compound. When a mixture of benzoic acid and TMA in a 1:2.5 ratio is heated at 80 °C for 2 h, PhCMe2OAl(CH3)2 is formed along with compounds containing –O–Al– moieties. We could recover a product identified as PhCMe2OH after the organic work-up of the mixture; its 1H NMR spectrum is shown in Fig. 3.
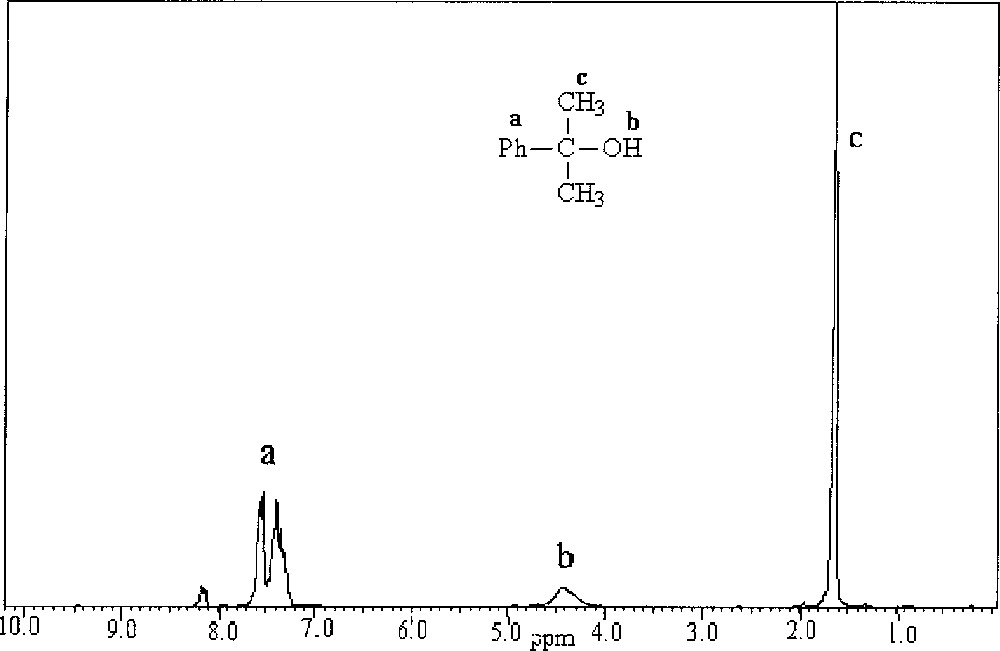
1H NMR spectrum of reaction product of benzoic acid and TMA (1:2.5 ratio) mixture heated at 80 °C for 2 h.
Further heating of the mixture does not result in any change. The O[Al(CH3)2]2 product formed during this organic reaction may be considered as a model of MAO structure. Nevertheless, it failed to activate metallocene catalysts in olefin polymerisation. However, the addition of catalytic amount (2%) of commercial MAO followed by heating at 80 °C for 5 h was found to yield a powerful metallocene catalyst activator for olefin polymerisation, as indicated in Fig. 4.
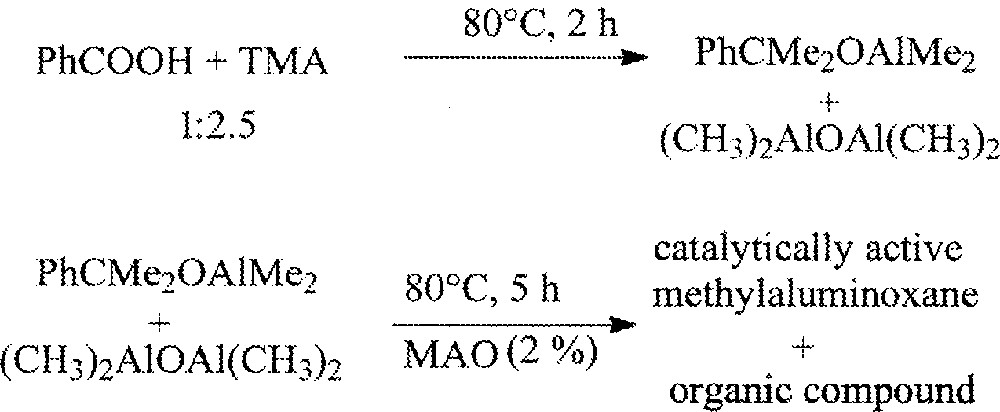
The formation of MAO from benzoic and TMA.
In the Table 1, the results of ethylene polymerisation studies with commercial MAO and MAOb obtained by this method are presented. The catalytic activity and the molar mass are nearly the same as with commercial MAO. The advantage of using such a method for the synthesis of MAO is highlighted by the fact that the recovery of aluminium in this method is 100%. In other words, loss of aluminium by over-hydrolysis is completely absent in this method.
Ethylene polymerisation studies with racEt(Ind)2ZrCl2/MAO system.
Activator | Activity | Mw (g mol–1) | MWD | Tm (°C) |
MAOb | 3 800 | 330 000 | 3.54 | 132 |
Commercial | 4 300 | 380 000 | 3.61 | 132 |
4 Conclusion
Thermal treatment of TMA with benzoic acid in the presence of a catalytic amount of commercial MAO turns out to be a very efficient method for the synthesis of methylaluminoxane, MAOb. The use of this MAOb as activator for late transition metal complexes in ethylene polymerisation will be the subject of our forthcoming paper.