1 Introduction
Adhesive bonding is nowadays a technology used in all fields of industry to assemble two substrates. Technology uses processes that often have no sound scientific basis. A process includes a surface treatment, the choice of adhesive and curing conditions. All these steps are selected empirically. Industry is interested in strong, ‘structural’ bonds. Bonding with adhesive is very specific to each industry and it is difficult to generalise from one application to another. There is a complex exchange between the substrates and the adhesive which is still undefined. Once a process has been validated by the market, it is normalised and factories stick to it. Scientific studies have shown that strong bonds occur when the adhesive is firmly anchored into the substrate and dissipates much energy. While scientific results shed light on the mechanical behaviour of adhesive bonded joints, the anchoring step remains uncertain.
It is clear that adhesion is the result of some chemical bonds between the substrate and the adhesive. In the absence of interpenetration between the substrate and the adhesive, the thermodynamical energy of adhesion, Wa, can be reduced to the energy of intermolecular interactions at interfaces [1,2].
When a chemical reactions occurs between the adhesive components and the substrate the energy of the reaction contributes to the energy of adhesion by Wareac = – f Σ·ΔH [3].
where Σ is the number of reactive sites per surface unit, ΔH the enthalpy of reaction and f a conversion factor. This increases the value of Wa.
The energy needed to separate bonded substrates, their ‘adherence’ is expressed by the fracture energy, G. It is measured by peeling or cleavage. Peel test allows measurement at controlled speed which shows that G, depends upon the peeling speed in the case of assemblies made with visco-elastic polymers(1)
It has been thought that the visco-elastic dissipation could explain the high fracture energy of structural bonding. However, in Eq. (1), when the speed v tends toward zero, G tends toward Wa, which has a very low value of the order of 0.1 J m–2. Cleavage is the only way for measuring very strong bonding. The cleavage at constant displacement is a measure of G at zero speed (G0). In the case of an assemblies made with structural commercial adhesives, values that are three to four order of magnitude higher than Wa are measured [8].
The high value of G0 comes from the dissipation of energy by the adhesive before it breaks. This has been well explained in the case of bonding of plastics.
2 Progress in the bonding of plastics
2.1 Energy dissipation during the fracture of polymers
The fracture of a polymer occurs either by chain pullout or bond rupture. Chain extraction dissipates little energy, about 5 J m–2. Rupture of chains requires more energy. Because when a polymer chain is under tension, the N monomers of the chain have to be extended to their limit of rupture before the chain breaks. Thus the energy required is N times the energy, uξ, of the weaker covalent bond in the polymer chain. The fracture energy is(2)
In adhesives, energy dissipation occurs by cavitation, fibrillation, crazing or in the case of cross-linked network croiding – an intermediate damage between crazes and voids [11]. Ahead of the fracture tip there is a region of deformed material over a large volume that consumes the energy G = σy · δ (σy is the yield stress and δ the crack opening displacement).
In order to dissipate energy the adhesive chains have to be anchored with bond energy at least equal to uξ. A covalent bond has an energy of ca. 340 kJ mol–1, whereas acid–base interactions are at most 50 kJ mol–1. Thus the polymer chains of the adhesive have to be attached either trough multiple van der Waals bonds or covalent bonding. In computerised simulation of the rupture of polymers [12] the anchorage is simulated by an interaction potential 1.6 times higher than that of the carbon–carbon bond. How anchorage is produced between an adhesive and the substrate is still uncertain. In the case of polymeric materials it has been shown that interdiffusion of the adhesive into the polymer and chain entanglement is required.
2.2 Interdiffusion of polymeric chains
Long ago has the autoadhesion of soft polymers as polyisobutylene (PIB), or the adhesion between PIB and cellophane, been explained by interpenetration of chains from both side. The ‘diffusion theory of adhesion’ [13] accounted for the time and temperature dependence of the adherence between miscible, soft, polymers. More recently, it was shown that amorphous or semi-crystalline, immiscible, polymers could be stitched together by a film of copolymer having lateral chains interpenetrating in both materials. Studies of the bonding of polystyrene (PS) and polymethylmethacrylate (PMMA) by the lateral chains of a copolymer of PS—PMMA allowed the study of the conditions of energy dissipation. Using copolymers with a fixed length of PMMA, long enough to anchor the polymer in the PMMA, and varying the length (N) and specific density (Σ) of the PS chains, it could be shown that when the chains are short they are easily pulled out. When they are sufficiently long but of low specific density, the PS chain break. When they are both long and dense the threshold for plastic deformation is overpassed and the fracture energy, due the deformation process during the fracture process is high [14]. Significant adherence is measured as soon as the PS lateral chains molecular weight is equal or greater than the average molecular weight between entanglements of the PS. The transition between a weak and a strong bonding was shown to occur when the length of the interphase reaches 10 nm (Fig. 1) [15].
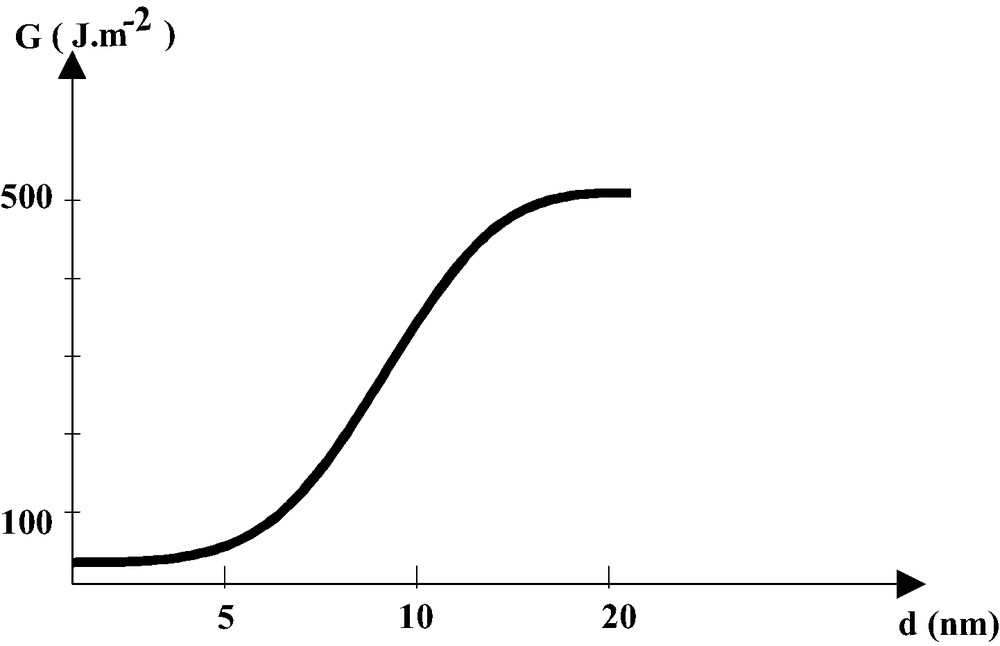
Transition from weak to strong bonding as the interphase depth increases due to interdiffusion. (adapted from [15]).
These studies suggest that strong bonding of plastics occurs when polymer chains diffuse at a given depth (the length of entanglement for PS) in both substrates and the anchorage density is equal or greater than a threshold Σc.
2.2.1 Interdiffusion requires sufficient chain mobility
In practice this is realised by heating, solvent plasticisation or the use of liquid reactive adhesives.
The diffusion of the adhesive into a plastic depends of the components, their glass transition temperature, the duration of cure and processing temperature.
In the case of reactive adhesives, which have two components, as epoxy-amine, both components diffuse some microns in the plastic substrates and form inside a connecting network upon reaction of the components, to give strong bonds. There is a competition between the diffusion of the adhesive into the plastics and its kinetic of polymerisation. For instance the bonding of the amorphous thermoplastic polysulphone (PSU) with a DGEBA-4,4′aminodiphenylmethane is insured by an interpenetrated network 3 μm thick. The interphase so created is dissymmetric as it is essentially the epoxy-amine which diffuses in the PSU, the penetration of PSU in the adhesive being much lower [16]. When a polyimide is bonded with an epoxy-amine (DGEBA-diaminodiphenylsulphone) cured 4 h at 130 °C and annealed 4 h at 220 °C, the interpenetrated network extends over 80 μm [17].
2.3 Specific interactions
That adhesive has to penetrate into the plastic substrate to form a bond seems well established however which is the adhesive composition that will achieve it is not known. Despite intensive researches the interaction between a fluid and a polymer is unpredictable. Solubility parameters (δ) are of limited values. This is because molecules are pulled together by localised attractive forces known as ‘specific intermolecular interactions’ which operate between specific functional groups. They have been evidenced in miscible polymers. For instance PVDF (δ = 11.2) and PVC (δ = 11.0) have the same solubility parameter. PVDF is fully miscible with PMMA (δ = 9.3). The blend of PMMA and PVDF shows a shift of the IR band of the ester group of PMMA indicating strong interactions but PVC is miscible with none of them.
This makes that the choice of the right adhesive for gluing a given plastic has to be made after experimentation. The behaviour of two epoxy-amine differing only in their curing agent used to bond polyphenylene ether (PPE) is an example: the mixture of DGEBA and MCDEA (methylene bis[o-chloro-diethyle aniline]) diffuses in PPE and forms an interphase of 200 μm producing a strong bond between them. On the contrary if the hardener is diaminodiphenylsulphone, a smaller molecule, the mixture is incompatible with PPE. When the adhesive is applied to the PPE and cured even under pressure only a thin (< 50 nm) interphase forms without insuring the bonding [18].
2.4 Primers for bonding plastics
Another practical way to favour the interpenetration between the plastic and the adhesive is the use of solvents or solutions in solvents that penetrate into the plastic, swells it and facilitate the diffusion of the adhesive. Polyimide may be bonded to itself, if the polymer is swollen with N-methyl-pyrrolidone. Then the polymer chains interpenetrate over 200 nm [19]. However, when the intercrossing of chains is not realised this may lead to the de-anchoring of the two parts. For instance a polypropylene (PP) foam cannot be attached to a stainless-steel plate with a two-side PSA film because the film does not adhere to the PP. Rubbing the foam with acetone leads to the formation of a very good bond with peel energy 800 J m–2. Acetone allowed the penetration of the acrylate adhesive in the felt promoting the anchorage. However the film debonds overnight. The acetone either has diffused deeper in the felt or evaporated and the polymer chains came back at their original place.
A special case is the use of so called ‘primers’ that will help the penetration of the adhesive in the plastic material. The correct choice of a molecule is a matter of experience. Let give an example: cyanoacrylics are a class of reactive adhesives which polymerise rapidly in contact with a nucleophilic molecule, even water induces the curing. They do not bond to polyethylene (PE) or PP. If a solution of an amine in an organic solvent (or a mixture) is deposited over the PE surface, it will diffuse inside the PE. The cyanoacrylic adhesive deposited afterward allows for bonding the PE to itself or to another substrate. As the adhesive penetrates at his turn in the polymer, the amine which is already there, initiates the cyanoacrylate polymerisation inside the PE realising the interpenetration of both network over some microns. Commercial primers are based on this effect. Their use is complicated by the volatility of the solvent and the fact that the bonding has to be made after sometimes to allow the penetration of the primer but not too long after because the primer disappears inside the PE. Triphenylphosphine and cobaltacetylacetonate have also been reported as effective initiators [20]. What is amazing is that the solvent penetrates the PE although it does not wet it. It is the difference in chemical potential that drives it inside. Even an aqueous solution of 2,4,6-tri(dimethylaminomethyl)phenol, 0.5% allows also the penetration of a cyanoacrylic adhesive in HDPE and its bonding to another substrate.
2.5 Plasma treatment
The treatment of plastics surfaces in a plasma greatly improve the adherence of adhesives [21]. Cold plasma, generated by microwave discharge has brought one of the most spectacular advances in plastic bonding or painting. In the automobile industry huge oven are used to treat car bumpers before painting. Nowadays plasmas at atmospheric pressure are used. It is one example of a technology that has not received any satisfying scientific explanation. Our experience is that it works with all the thermoplastic materials, amorphous, semi-crystalline or crystalline we have had to bond. This is astonishing as normally semi-crystalline and crystalline polymers are difficult to bond. Plasma treatment provides strong and durable bonds with many adhesives. Scientific studies insist on the surface oxidation of the polymers [22,23]. Actually plasma treatment increases the measured surface polarity and XPS shows an increase of oxygen content but this is comparable to other oxidative treatments with flame or corona discharge. A unique property of microwave plasma treatment of thermoplastics is its long term efficiency. Once treated, the plastic surface may be bonded 2 or 3 months after the treatment providing the same high resistance as a freshly treated surface. It is suggested that the polymer chains at the surface are immobilised by cross-linking which would ease the diffusion of the adhesive inside the polymer [24].
3 Progress in the bonding of inorganic materials
That the anchorage of two plastics materials or a plastic and an adhesive is due to interdiffusion is well established. What is occurring between an adhesive and inorganic materials is not known for sure. There are two aspects of the problem the first one is the state of the inorganic surface, the second is the reaction that give the bond between the adhesive and the surface.
3.1 The surface of inorganics
3.1.1 The ‘atmospheric layer’
Surfaces are formed either by the solidification of a liquid or by cleavage or by extension. The latter two processes imply the breaking of chemical bonds. Inorganics should have a high surface energy as suggested by the extrapolation of their surface tension in the liquid state. However when a chemical bond breaks the atoms are left in a state of very high energy. That disturbs the surface at a depth of many atomic layers. The excited atoms will react with all the elements present in their environment. It is for that reason that they form not only oxides but also carbides, hydroxides and sulphides. Modern surface analysis shows the presence of C1s carbon embedded in the surface. Its origin is not clear; it probably comes from reaction with atmospheric carbon dioxide. Upon the resulting layer, water makes a contact angle of 45° as on a low energy plastic surface of 40 mJ m–2 [25]. That layer is not, as often considered, the result of adsorbed contamination but an embedded layer over some nm. Neither solvent extraction nor nitric acid oxidation are able to modify it significantly. It seems that the way surface are formed makes a difference in their behaviour. Evaporated metallic layers, injected zirconia or alumina give easily strong and durable adhesive bonds despite their smoothness. Difficulties arise with the gluing of metals that have been rolled, machined, chemically etched etc. and are covered with an inhomogeneous atmospheric layer. In that case surface energetic is irrelevant as interactions come from active sites which undergo chemical reactions with the adhesive.
3.1.2 Surface treatment
Metallic surfaces require a proper surface treatment to give durable and reproducible bonding. Great deals of research have been devoted to ways of treating surfaces in order to improve the durability of adhesive bonding. Some surface treatments promote a tremendous increase of the resistance to fracture and durability of adhesive bonds. The preparation of the surface determines the bond properties and fatigue resistance. Same bonding of substrates with different surface treatment gives different mechanical properties.
This is a problem in standard tests. Even if the surface treatment is described in the procedure, which is rarely the case, serious discrepancies are found from one laboratory to an other [26].
One of the many difficulties in a scientific approach of surface treatment is the heterogeneity of the surfaces of the materials used in practice. Surfaces are ‘chemically rough’. The search for such a treatment is highly empirical despite the development of new methods of surface analysis. Different ways have been explored:
- • increase of the roughness of the surface;
- • electrochemical anodisation;
- • plasma treatment.
Increase of surface roughness is thought to increase the effective surface of contact between the substrate and the adhesive. Also some think that it will improve the mechanical anchorage of the adhesive. No relation has been proven however. The increase of surface roughness increases the surface of contact by a factor from 2 to 10 [27] which is much lower than the energy dissipated trough plastic deformation. The incidence of roughness on the plastic deformation is not known but seems to exist. In some cases roughness increases the fracture energy. Roughness also allows for displacing surface impurities, as silicon oil, providing a reservoir in which the adhesive displace them. Furthermore, it facilitates the expulsion of interfacial air bubbles. These are two important factors of good adherence. Formation of a rough surface is associated with a modification of surface chemistry. Grit blasting which is often used before bonding aluminium sheets gives an example of the modification of surface chemistry accompanying the increase of roughness. A comparison of an aluminium–magnesium alloy (EN-AW 5754) surface, chemically etched only or chemically etched and grit blasted, with glass beads or alumina grit, shows variation in the carbon content of the utmost (<10 nm) layer and the formation beneath it of an oxide layer of composition Al2O3, Al2O2.9 and Al2O1.3, respectively. The latter two are very reactive [28].
Anodisation of metals is the most effective treatment for durable bonding of stainless steel, aluminium or titanium. The electrochemical reaction of stainless steel in nitric acid removes a superficial atmospheric layer and reveals the grain boundaries. The conditions depend of the type of stainless steel. Application of a difference of potential of 5 V between the substrate and a counter electrode of stainless steel 316 L, for 1 min, gives good results.
Phosphoric or chromic acid anodisation of aluminium and titanium forms a thick porous oxide layer on the surface which facilitates the interpenetration of the adhesive and the substrate.
In order to avoid the use of toxic or corrosive liquid bath and the retreatment of the wastes, adhesion promoters are proposed.
Plasma treatment of the surface is the magic solution for most plastics bonding but is rarely effective over metals. Some authors [29,30] report good results on stainless steel showing how the atmospheric layer thickness is reduced, however we could not reproduce their results.
3.2 Anchoring the adhesive to inorganic substrates
If everyone agrees that adhesives have to be bound to the surface, most works consider it as granted and discuss the behaviour of the polymer under stress. However these interactions are the key of successful assemblies. The goal of surface treatments is to increase the anchorage density Σ. A common point of view is that the oxo-hydroxides present on the metal surface are the sites of adhesive binding.
OH groups are either acidic : –OH → O– + H+ or basic : –OH + H+ → OH2+, so they could react with acidic or basic functions of the adhesive components forming ionic bonds that would explain their sensitivity to water. Adhesive bonds with aluminium alloys which are just grit blasted have poor durability in moist atmosphere indeed. However, the weakening of the hypothetical ionic bonds is associated with superficial oxide hydrolysis and rupture in that layer. That explanation could be too simple.
3.2.1 Adhesion promoters
In order to facilitate the connection between a solid inorganic surface and the adhesive, functional alkoxy-silanes are used. Of general formula:
Silanation of glass with amino propyle trimethoxy silane, NH2–C3H6–Si–(OCH3)3, before bonding is widely used, mainly for glass fibres reinforcement of composites.
On metals, the behaviour is much more complicated and it is difficult to obtain reproducible results. The aminosilane used for glass bonding is unstable on aluminium and its alloys.
Recent publications propose to replace the anodisation of aluminium alloys used in the aircraft industry by wetting with γ glycidoxypropyle tri methoxy silane (GPS). Much work have been devoted to find the optimum conditions. A 1% solution at pH 5 gives the best results if it is used before 8 h after its preparation [31]. Aluminium has to be pretreated before silanation. In practice, a first degreasing with acetone or detergent is followed by abrasion with a ‘scotch brite®’ scouring pad or grit blasting and the silane treatment. As the aluminium oxide composition changes in moist atmosphere, previous immersion in warm water is advised. In these conditions the behaviour of GPS treated surfaces compares with anodisation. 3 mercaptopropyltrimethoxysilane is also reported to give comparable resistance of adhesive bond to aluminium [32].
3.3 Interaction between the substrate and the curing of adhesives
The substrate interacts with the adhesive curing. Ions coming from the dissolution of the inorganic substrate modify or promote adhesive cure. Iron or copper ions are necessary to induce the curing of anaerobic acrylic adhesives. They initiate the formation of radicals by decomposition of peroxides which are added to the formulation:
Fe2+ + R–O–O–H → Fe3+ + OH– + RO° and the polymerisation reaction ensues. A solution of organo copper derivatives is added to surfaces which lack from these ions in order to insure the curing of the adhesive.
When two copper rods bonded with a two component epoxy-amine adhesive are separated the adhesive appears coloured in blue by copper ions coming from the solid substrate. Sometimes microcomposite structures form leading to an interphase between the solid surface and the first adhesive layer. In the case of titanium and aluminium bonded with epoxy-amines, the superficial oxide dissolve in the amine, forming organocomplexes which precipitates in the interphase [33].
Whether the interphase will have or not a positive influence upon the adhesive bond is not known in advance. Its formation comes from interplay between the surface and the adhesive. It is inhibited by the atmospheric layer and favoured by roughness in a range of 2–20 μm. We have seen previously the importance of the pores aspect ratio. Pits have to be four times there depth to increase the fracture energy. It is not so much the initial roughness of the surface which realises the anchorage of the adhesive but often the reaction of the adhesive with the surface. On smooth surfaces, the adhesive dissolve the surface, creates pits and mounts to which it bonds, forming anchors. They realise a kind of interdiffusion between the solid substrate and the adhesive. Some ions, coming from the surface, will diffuse in the adhesive and realise an electrostatic bonding; some will catalytically react with the adhesive forming carboxylic acid which bond to the surface through salt formation, some will form dendrites which retain the cured adhesive. A good example is the bonding of rubber on metallic reinforcement in tyres where an interplay between the formation of dendritic sulphides and rubber vulcanisation creates a strong interphase [34]. Similar process occurs in aluminium bonding. SEM observation of the surface treated with sulphochromic acid shows, after debonding, “fingers”, not uniformly spread, coming out from the adhesive. By place they are broken. On the Al side some holes that were present initially, due to the etching, have disappeared. The fingers have penetrated inside and broke. Whether they are made of oxide, adhesive or a mixture of both could not be determined [35].
4 Progress in adhesives chemistry
4.1 Modified thermoset
As the key of strong bonding is the dissipation of energy chemists have sought how to increase it. Reactive adhesives may be modified by:
- • addition of thermoplastic powder or liquid rubber
The latter are reactive polymers, initially soluble in the resin, which separate upon curing and form elastomeric inclusions bound to the polymer chains. Their dimension depend from the temperature curing program. Epoxidised polymer or carboxyl terminated rubber (CTBN) are mainly used. To increase their solubility in the DGEBA resin, they are first partially condensed with epoxy. A typical composition is DGEBA 72.7%, adduct DGEBA-CTBN 19.8, DiCy 7.5. A few 2-methyle imidazole is added to decrease the temperature of cure. Both surface treatment and cure conditions affect the value of G0;
- • interpenetrated networks
Mixture of epoxy and polyurethanne or acrylics form their own network which interpenetrate and increase the fracture energy;
- • nanoparticles
The nanoparticles fashion has led many formulators to study their possible influence on fracture toughness. These particles are difficult to disperse in the viscous resins and few positive results have been obtained. An important increase in toughness has however been reported when small quantities of a commercial dispersion of nanoparticles of silica in DGEBA were added to an epoxy formulation [36].
4.2 New curing agent: organoborannes
Surprisingly the choice of the hardener has a great influence upon the bonding as we saw in the paragraph devoted to plastic bonding. In the course of a study aimed to compare the resistance of various dental adhesive, we have been surprised of the excellent behaviour of an acrylic adhesive using a partially preoxidised tri-n-butylboranne (TBB) as a curing agent. The descriptive sheet explains the initiation of polymerisation through a reaction between air and TBB leading to a boron peroxide which discomposes into radical:
(n butyl)3 B + O2 → (n butyl)2 B O2 ° + (n butyl)°(n butyl)° + O2 → (n butyl) O2 °(n butyl) O2 ° + (n butyl)°3 B → (n butyl) O2 B (n butyl) 2 + (n butyl)MMA + (n butyl)° → (MMA) (n butyl) |
The organoborannes are difficult and dangerous to manipulate. Their complexes with amines are easier to use. Complexes of amine and trialkyleborannes as, N,N,N′,N′, tetramethylguanidine and triethylboranne, are useful initiators for compounds which polymerise under free radical polymerisation conditions as the acrylates [37,38]. They have to be associated with a component that will liberate the boranne. A composition made of:
- • an organoboranne;
- • a polymerisable monomer;
- • and a metal salt complex [39] gives a product that is able to bond low energy polymers as POM, PP, PE or even PTFE that are not bondable with the classics acrylic adhesives polymerising with benzoylperoxide.
Although they have the same surface tension, the hardener promotes the penetration of the adhesive in the polymer and realises the required interpenetration.
5 Progress in durability
Durability and fiability of adhesive bonded parts is of great concern in engineering. The influence of water on the stability of metal/adhesive interface is well proven. A joint cleaved by a wedge, in which the adhesive polymeric chains are at their maximum extension, appears indefinitely stable in room conditions. We have in our laboratory such assemblies, the length of fracture of which has not varied over 25 years. If that device is exposed to humidity, the length of fracture will increase and eventually lead to complete separation. A combination of stress and humidity is necessary to induce the failure. A joint made with a structural adhesive does not separate in water unless stressed. The level of stress determines the speed of delamination.
5.1 The role of water
Most adhesives are made of polar polymers and absorb water. Water penetrates into the adhesive by diffusion either in the bulk or along the interface when it is not densely attached to the polymer. As long as the quantity of water is lower or equal to the free volume of the polymer, it has no effect nor on the polymer nor on the bond. The absorbed quantity, w (% weight) depends upon the relative humidity: w = RHb. There is a threshold in relative humidity below which there is no bond degradation. In this first step water absorption is reversible. Once the free volume has been filled, further absorption of water leads to hydrogen bonds displacement and swelling. The glass transition temperature (Tg) and the elastic modulus (E) decrease. Although some great variation have been reported, we have never observed a decrease of more than 10 °C in Tg and 0.5 GPa in E. It is not the effect of water on the polymer which causes the debonding of structural adhesives which are insoluble in water.
At saturation water condenses in the voids of the polymer. With a “good” surface treatment the adhesive joint is stable, even when saturated with water, although it is weaker than a dry bond. At low density of anchorage there are microcavities at the interface. These let water to condense and/or diffuse along the interface. Water will dissolve some soluble elements from the substrate surface or the adhesive which increase the osmotic pressure and lead to the growth of the voids until the adhesive separates from the substrate. We could show this process during the debonding of glass adhesive joints in hot water [40] and similar observations have been made on aluminium [41].
Corrosion occurs at the surface of aluminium and its alloy. The superficial alumina is transformed into brittle crystallites of boehmite, AlOOH. Fracture then occurs in the oxide layer [42].
The superior resistance of the oxides formed anodically may be due to absorption of phosphates or chromates from the solution. It has actually been shown that the process of hydration is lowered on aluminium oxides with adsorbed phosphates or chromates layers.
Metal-adhesive joints are more sensitive to disbonding in moist environments than are those made on ceramics or plastics which do not corrode.
In a joint under stress, water causes a displacement of the locus of fracture from cohesive in the adhesive to the interface (Fig. 2). On joints made with an EVA hot melt between a stainless steel plate and sapphire, cleaved in ambient conditions, one observes cavitation in the plastically deformed zone ahead of the crack tip, in high humidity the cavities disappear and the fracture proceed along the interface (Fig. 3). In the case of an epoxy nylon, the fracture is cohesive in the ambient atmosphere but cavities form along the sapphire surface (Fig. 4). In the absence of water, they maintain the adhesive bond, with no growth. This suction effect is known in the case of ‘pressure-sensitive’ adhesives [43]. When water is present at the interface, it lowers the fracture energy (probably water vaporises in the cavities) and the cavities grow laterally along the interface. This process explains the mysterious transition of the locus of fracture and also why joints in compression are insensitive to water as they do not cavitate. It also explains why when a joint saturated with water is cleaved the fracture length upon cleavage is hardly higher than that of a dry joint [44].
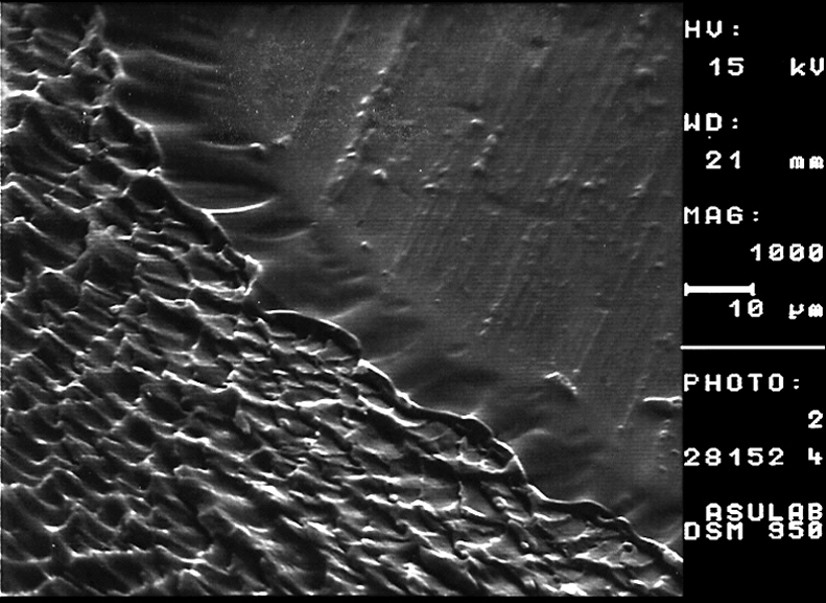
Transition from cohesive to adhesive fracture in a bonded joint cleaved and exposed to humidity (epoxy-CTBN—stainless steel).
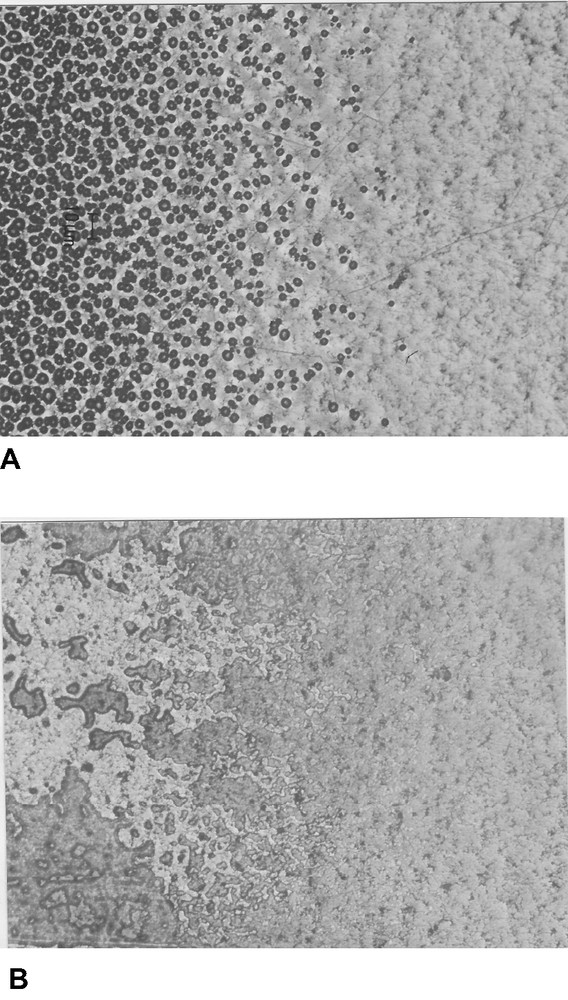
(A) Cavitation at the fracture tip of an adhesive bonded joint; (B) in the presence of humidity, the cavities expand laterally. (EVA-sapphire.)
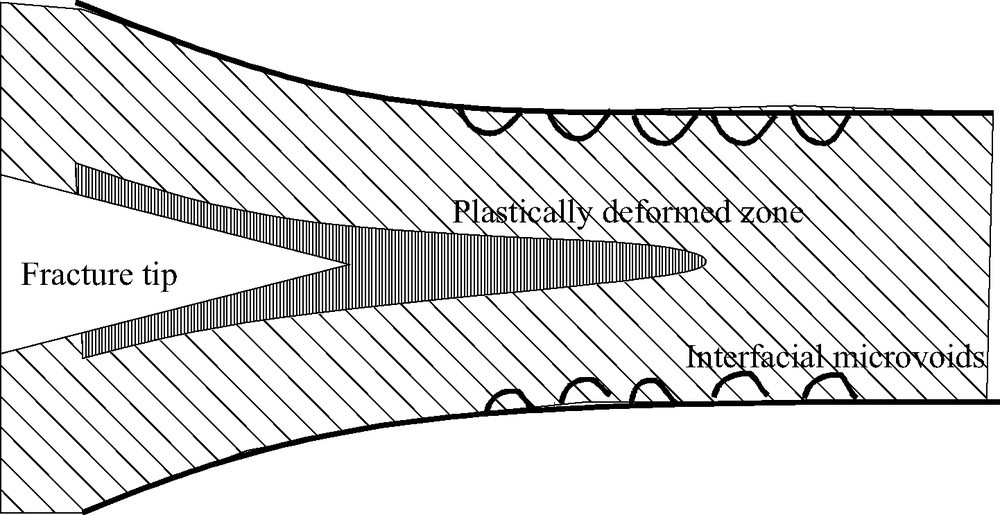
Schematic description of deformation of the adhesive at the fracture tip. Cavities appear along the interface while the adhesive whitens.
One of the functions of surface treatments is to increase the anchorage density and reduce the size and the number of micro voids at the interface. The quality of a surface treatment is usually deduced from the evolution of the fracture of cleavage in a ‘wedge test’.
5.2 The fake of fracture energy measured in ambient conditions
In many cases an adhesive gives a bond that appears reasonably strong in laboratory tests. It is only latter during use that the debonding of the substrates may appear.
Fracture energy measurements characterise the adhesive but not the bond. This is so because as soon as a fraction of adhesive chains are bound to the substrate the fracture energy reaches its maximum values. The bound chains pull all the other in the neighbourhood and the ‘cooperative effect’ produces the same resistance independently of Σ. Measurement on silica wafer covered with a layer of octadecyl trichloro silane [45] or a metallic surface covered with silicon oil [46] indicate that at a value of 20% of the maximum anchorage the adhesive bond reaches its maximum resistance . If mechanical tests do not see the variation in anchorage density, the evolution of the bond in humid environment is very sensitive to it, as water condenses in the voids between the sites of anchoring. In a series of 50 specimens bonded with an adhesive cured in different conditions or prepared in different way, the fracture length of a wedge test is the same. However, when the cleaved assembly is placed in an oven at 40 °C 94% RH some test debonded after 50 days while other where stable for 450 days. Fig. 5 shows the increase in the length of fracture of four samples which have initially the same fracture length at 40 °C in ambient conditions. When placed at 40 °C 95% RH, their fracture length either remains stable or increase leading rapidly to the separation of the two plates. This is why durability studies are always made in humid conditions.
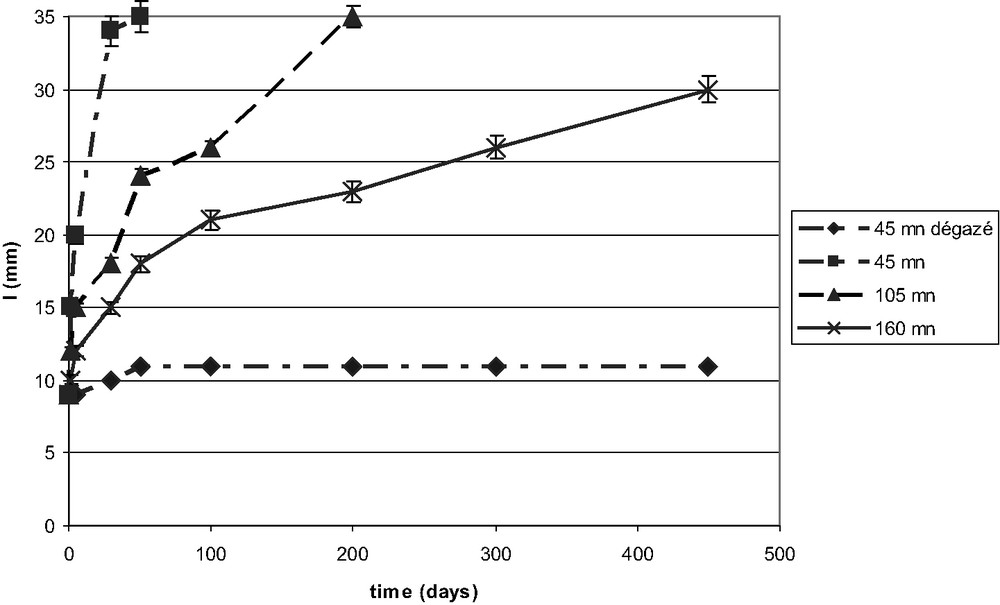
The increase of fracture length in a wedge test, in humid atmosphere, depends of the adhesive curing time and its outgassing (epoxy-CTBN—stainless steel).
5.3 Debonding under stress in humid conditions
What is used to characterise the durability is the extension of the wedge test fracture length after some time of exposition in humid conditions. The standard being 50 °C, 100% RH, 1 h. Usually, the fracture length increases when the cleaved joint is exposed to humidity. A surface treatment is considered as ‘acceptable’ if the progression is below a threshold (6.3 mm in the standard). That there is a correlation between the increase in fracture length and joint durability was proven by a comparison of tests made with parts machined in pieces of airplanes which had or not debonded in service. However, this correlation is surprising. The standard dimensions do not allow the water to penetrate deep in the adhesive (the diffusion coefficient of water in the adhesive at 50 °C is around 10–12 m2 s–1). In 1 h the penetration of water occurs mainly in the plastically deformed zone ahead of the crack tip. It causes the destruction of that region by what is known as ‘environmental-stress cracking’ (ESC) of the polymer. Why would the surface treatment influence the ESC? Probably because the anchorage density of the adhesive being higher, the tension imposed to the polymer chains is lower or the cavities being smaller water do not diffuses along the interface or both. The wedge test indicates the density of defects along the interface.
Despite the sensitivity to water of two parts epoxy-amine adhesives observed in laboratory, the Abu Simbel statues were cut and reassembled with epoxy-amine adhesive in large joints, compression insure their reliability.
For long, cracked bridges were reinforced with steel sheets bonded with epoxy-amine without any signs of degradation over 30 years (nowadays composite films, that are lighter are used). This apparent discrepancy comes from the difference in dimensions of the bonded parts and the differences in the temperature and humidity of the environment. Test parts are 2.5 cm wide and submitted to continuous warm and humid environment. The reinforcement of bridges are at least 20 cm wide and are occasionally exposed to humidity, so water does not have time to saturate the adhesive bond and condense at the interface. Only some millimetres at the edges are irreversibly debonded. The edge degradation may be observed on the edges of the glass of the ‘pyramide du Louvre’. That is the reason why it is advised to build joints large enough to have a core that is not submitted to mechanical or environmental stresses—when possible.
The use of high temperature as an accelerating factor introduces side reactions which do not occur in the field. Often the variation in weight of a disk made of epoxy exposed to humidity at high temperature (>60 °C) shows a first increase due to water absorption then a decrease due to the dissolution of some undetermined species in the adhesive and a further increase due to hydrolysis which increases the weight by 18 g mol–1. These latter two do not occur at 60°C or below(Fig. 6). This is the reason why “Reliability tests on optical connectors are in poor agreement with field observation based on more than 20 years experience” [47].

Variation of the weight of a disk of epoxy-nylon exposed to 100% relative humidity at high (90 °C and moderate (60 °C) temperature.
It must be noted that standard procedure, if it allows for characterising water resistance, does not give indications on the fiability of the process and only replication of measurements may give the lower limit of resistance of bonded joints because it is very variable.
6 Conclusion
A scientific approach of adhesive bonding is a formidable task. Among the results we have presented many are difficult to rationalise. For instance: Why is the role of the hardener so important for the penetration of an adhesive into a plastic? Why do the polymerisation by borannes change the behaviour of acrylic adhesives? And so on. The purpose of that paper is to attract attention on these intriguing aspects of the technology.