1 Introduction
Global energy consumption continuously grows due to the increasing population and industrial development. In the context of fossil fuel abatement, environmental issues and rising waste volumes, sustainable strategies for waste management and diversifying energy production are required. The production of biodiesel from biomass is expected to increase in the European Union in order to meet the goal of replacing 20% and 30% of petroleum-based fuels with biofuels by 2020 and 2030, respectively [1, 2]. In the past few years, biomass and waste have become attractive as renewable sources that could play a major role in renewable energy [3]. Waste treatment aims to reduce landfill disposal and to minimize the environmental impact, whereas biomass seeks to diminish the dependence on fossil fuels. Various thermal processes, such as incineration [4, 5], pyrolysis [6, 7] or gasification [8, 9], have been developed for biomass/waste treatment to recover energy from the organic fraction. The thermochemical conversion of biomass/waste to energy allows generation of a combustible gas, called synthesis gas, which is mainly composed of hydrogen (H2) and carbon monoxide (CO). This synthesis gas can be used as a feedstock for liquid fuel production via the Fisher–Tropsch synthesis [10, 11], gas turbine or fuel cell for energy production [12, 13] or chemical products as ammonia, methanol and hydrogen [14]. However, the conventional methods have some limitations, such as a low energy balance, pollution, catalyst requirement and its deactivation, process control, flexibility, the compactness and size of equipment, etc., which might be overcome using plasma [15].
Thermal plasma seems to be one of the most attractive and environmentally friendly technologies for the biomass/waste treatment. High gas temperatures in plasma, reaching up to 15000 K [16], offer a possibility to advantageously contribute to the pyrolysis/gasification of organic materials by accelerating the reaction kinetics. The easiest enthalpy control by adjusting the electric power and flow rate of the plasma-forming gas allows controlling the parameters of the conversion process in situ. The production of reactive species by the plasma, such as atomic oxygen, hydrogen and hydroxyl radicals, is an additional advantage of using plasma [17]. However, the maturity of thermal plasma in terms of economic feasibility has not been proved yet because of the use of expensive electrical energy to run plasma torches.
The oxidation environment in the waste treatment process is also an important feature. Knoef [18] shows the differences obtained between two different oxidation agents used (pure oxygen and air). Pure oxygen provides a gas with a calorific value of 10.1 MJ/m3, while the use of air gives only 4.2 MJ/m3 due to the dilution of the synthesis gas with nitrogen introduced with the airflow. Water steam is generally preferred, because it produces the desired reactions including the steam reforming reaction and increases the H2 ratio in the synthesis gas. However, the steam reforming reaction is highly endothermic and needs a high temperature (1100–1700 K) [19].
Numerous investigations have been carried out employing thermal plasma (DC – direct current, AC – alternating current, RF – radio frequency, and MW – microwave) with a different type of plasma-forming gas for biomass/waste conversion to energy. References [20, 21] investigated the pyrolysis/gasification of biomass and waste for synthetic fuel production using a hybrid argon–water stabilized DC plasma torch. It was found that the synthesis gas with a high caloric value, a high content of hydrogen and CO, and a low concentration of CO2 was produced. An AC plasma torch stabilized with an air stream was used for wood gasification in [22]. The authors claim that 1 kg of wood with a moisture content of ∼20% can generate ∼13.5 MJ/kg of chemical energy with an energy consumption of ∼2.16 MJ/kg. The MW plasma gasification of glycerol was performed in [23]. It was found that, at a zero O2/fuel ratio, it is possible to produce the syngas with a high H2 and CO content of 57% and 35%, respectively. Additionally, when the steam/fuel ratio increased, the H2 content in the syngas increased, whereas the syngas heating value and gasification efficiency decreased. The pyrolysis of waste tire powder in a capacitively coupled RF plasma reactor under reduced pressure was studied in [24]. The results suggested that the pyrolysis of polymeric waste may be a feasible technique for recycling polymer waste. The gaseous product contains a large amount of H2 and CO and a small amount of methane and other light hydrocarbons. The gasification of municipal solid waste using the pilot-scale Plasma Gasification Melting (PGM) process is reported in [25]. The syngas lower heating value (LHV) varied from 6 to 7 MJ/Nm3. The production of a high-purity H2 (>99.99%) from the thermal plasma gasification of paper mill waste is shown in [26].
In this study, a thermal DC arc discharge water steam plasma was used to pyrolyze/gasify organic materials to synthesis gas. Glycerol and crushed wood were used as a source of biomass. The effects of different conversion parameters including the water steam flow rate, the treated material flow rate and the plasma torch power were studied. The modeling of chemical processes, based on a classical thermodynamic equilibrium reactor model (TER), was also proposed. Furthermore, the quantification of the plasma conversion system in terms of energy efficiency and a specific energy requirement was performed. It was found that the synthesis gas with a high content of H2 and CO could be effectively produced from glycerol and wood by the thermal water steam plasma pyrolysis/gasification process.
2 Experimental setup and methods
2.1 Design of the biomass conversion system
In this study, the conversion of glycerol and wood to synthesis gas was carried out using an entrained bed plasma-chemical reactor (PCHR). The experimental system is shown in Fig. 1.
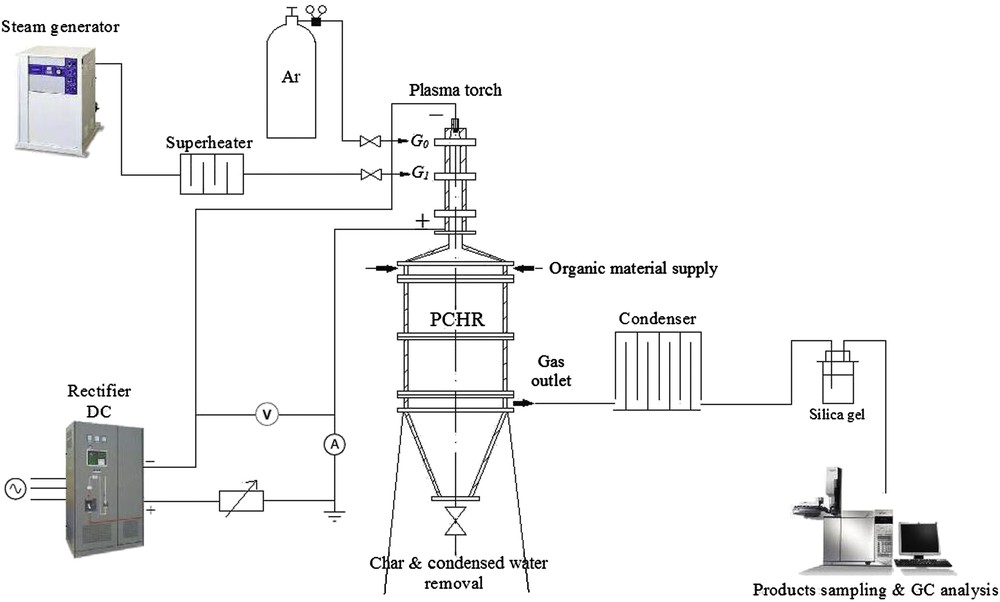
Scheme of the biomass conversion system.
It consists of an atmospheric pressure DC arc plasma torch, a power supply system, a steam generator, a super-heater, a gas supply system, a chemical reactor, an organic material supply, a condenser with silica gel (to remove moisture from the gas produced), and a gas chromatograph. The entrained bed plasma-chemical reactor used in this study was 1 m long with 0.4 m inner diameter. At the bottom of the reactor, there is a section for the removal of char and condensed water, and in the middle an outlet chamber for the produced gaseous products is installed. The residence time varied from 0.5 to 1 s, which depended on the flow rates of steam and the treated organic material, and the size of the PCHR.
Pure glycerol (99.5%) was used as a substitute for crude glycerol, which is considered a by-product of biodiesel production after the transesterification process. Glycerol was supplied to the chemical reactor at a constant rate of 2 g/s through the special spray nozzles. The optimal operating pressure of a spray nozzle is 10 bar. Therefore, the pressure in the glycerol feeding line was kept at 10 bar and regulated by nitrogen gas from a cylinder. To improve the fluidity and spray stability of glycerol, it was preheated to 343 K with a heater before supplying to the reactor.
Wood was chosen as a solid organic material because of the known chemical composition: C – 50.25%, H – 6.09%, O – 43.35%, N – 0.2%, and S – 0.1% [22]. It was supplied to the reactor by a special feeder at the flow rate of 1.2 g/s.
An atmospheric pressure DC arc plasma torch was used to generate active plasma radicals (O, H, and OH) from the water steam. The power of the plasma torch depends on the current intensity, voltage, and the flow rate of the plasma-forming gas. Argon was used as a shielding gas in order to protect the tungsten cathode of the plasma torch from erosion. During the experiments, the plasma torch power was changed from 48 kW to 56 kW (current 200 A, voltage 240–280 V, steam flow rate (at 500 K) 2.63–4.48 g/s). The mean temperature in the plasma-chemical reactor was simply calculated from the heat balance equation corresponding to the plasma enthalpy. The methodology is concisely defined in [27]. During the experiments, the mean jet temperature was 2800 K, with the maximal absolute error in the range of ±6–8%.
The gas produced after the conversion was analyzed by means of an Agylent 7890A gas chromatograph equipped with dual-channel thermal conductivity detectors (TCDs) and a valve system. The flow rates of the formed products were calculated from the mass balance equation using the known flow rates of the reactants and the product concentrations measured with a gas chromatograph. Additionally, a flow meter was used after the condenser to measure the flow rate of the outlet gas. Thus, it was easier to check whether the mass balance equation was valid for all the products after the flow rate calculation.
2.2 Main chemical reactions
Generally, the biomass/waste conversion to synthesis gas involves complex chemical reactions. The main chemical heterogeneous and homogenous reactions of pyrolysis and the gasification taking place in the reactor are described in detail in [17]. Arena [8] states that the final composition of the synthesis gas will be determined by the reaction rates and also by the effect of catalysts, which is important for tar decomposition in the reactor, rather than by the thermodynamic equilibrium. Nevertheless, the initiation of the chemical reactions in the reactor starts not only due to the high temperatures but may also be affected by the arc discharge being used. Therefore, firstly, active radicals such as O, H and OH are produced in the discharge chamber of the plasma torch under the impact of energetic electrons or the thermochemical pyrolysis of steam (where M refers to charge transfer) [28, 29]:
H2O + M → OH + H* + M, | (1) |
H2O + O* → OH* + OH*, | (2) |
H2 + O* → OH + H*, | (3) |
H2 + OH* → H2O + H*. | (4) |
The produced active radicals can considerably accelerate the pyrolysis/gasification process in the plasma-chemical reactor where the heterogeneous and homogeneous reactions mentioned in [17] take place.
2.3 Evaluation of conversion performance
In order to compare different processes and to evaluate the performance of the conversion system, it was quantified in terms of carbon conversion, H2 and CO yield, H2/CO ratio, energy efficiency and specific energy requirement. The criteria mentioned above are described in detail in [17, 23, 30, 31].
Carbon conversion writes:
(5) |
The hydrogen yield is:
(6) |
The carbon monoxide yield is:
(7) |
The energy conversion efficiency is:
(8) |
The specific energy requirement (SER) is:
(9) |
2.4 Thermodynamic equilibrium calculations
The plasma-chemical processes occurring in the plasma-chemical reactor were simulated by means of the Chemical Workbench (CWB) code [32] using a PT-type (constant pressure and known temperature) thermodynamic equilibrium reactor (TER) model. The TER is designed for calculating the chemical equilibrium of a multi-component heterogeneous system. A more detailed explanation of the model is provided in [30].
3 Results and discussion
The effects of the steam/treated material ratio and the plasma torch power on the biomass conversion are discussed below. It should be noted that at a constant arc current intensity of 200 A, the increase of the steam (H2O) flow rate from 2.63 to 4.48 g/s increases the power of the plasma torch from 48 to 56 kW due to the raise in the voltage-drop in the arc discharge channel. The concentrations of gas produced in each experimental case were measured three times, giving a relative deviation below ±5%.
3.1 Glycerol conversion
Glycerol (C3H8O3) conversion in the ambient of water steam plasma was performed under the following experimental conditions: glycerol flow rate 2 g/s, steam flow rate 2.63–4.48 g/s, and the plasma torch power 48–56 kW. The H2O/C3H8O3 ratio changed from 1.3 to 2.2, Tf = 2800 K.
The concentrations of gas produced after the conversion of glycerol are shown in Fig. 2. As the H2O/C3H8O3 ratio increased from 1.3 to 2.2, the H2 and CO2 concentrations slightly increased, whereas that of CO slightly decreased, and the concentration of intermediates (CH4 and C2H2) was below 5%. The experimentally obtained H2 and CO concentrations differed from those calculated at the thermodynamic equilibrium by 6% and 17%, respectively.
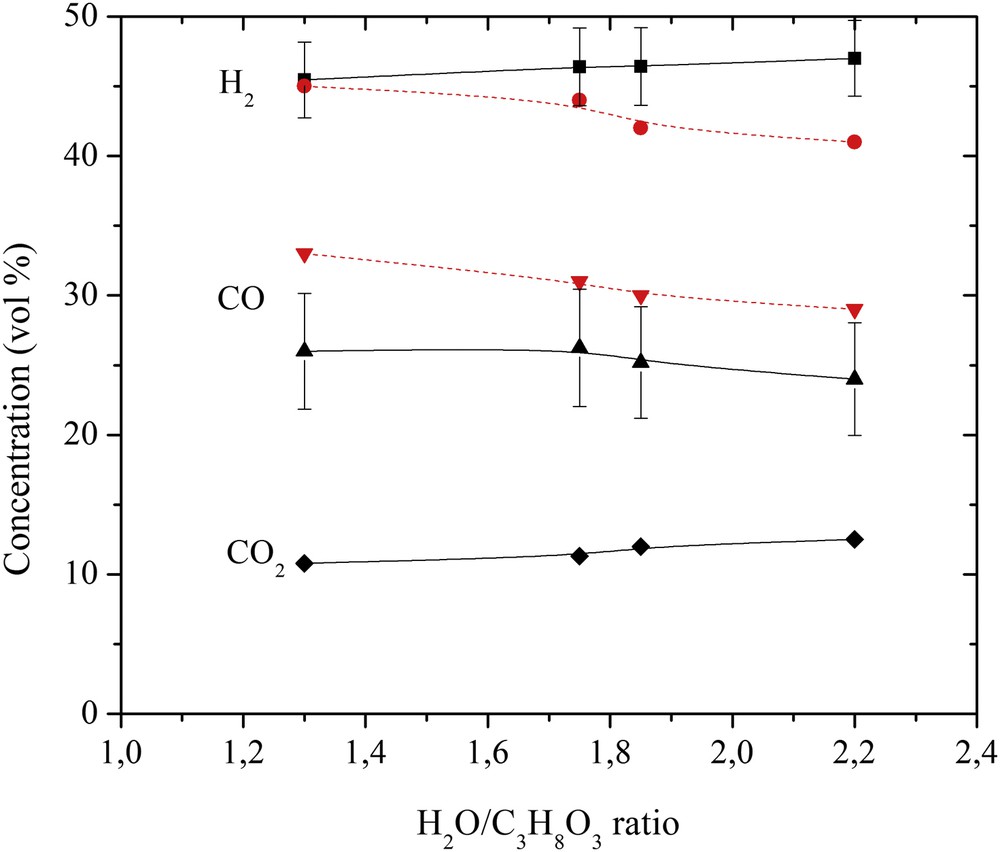
Effect of the H2O/C3H8O3 ratio on the produced gas composition. The full line represents the experimental results and the dashed red line represents the calculated results.
No traces of glycerol after the conversion were detected. It was fully decomposed into gas, liquid and a little amount of char as indicated in Figs. 3 and 4. The highest carbon conversion efficiency exceeded 88.9% at a water steam flow rate of 4.48 g/s and a plasma torch power of 56 kW. As the H2O/C3H8O3 ratio and the plasma torch power increased, the yield of gas produced in the total reaction product mass balance increased, while the yield of char decreased significantly. The yield of liquid products, mostly condensed water, increased due to the excess steam, methanation, and hydrogenolysis of glycerol. Nevertheless, the H2 yield was over 90% and increased as the flow rate of steam increased (Fig. 5). However, the CO yield was lower and increased only up to 55%, indicating that there was a potential to make the process of glycerol conversion to synthesis gas more selective in terms of the CO yield. This could be done by trying to minimize the content of intermediates such as CH4 and C2H2 by using special catalysts and/or by using the water–gas-shift reaction. The H2/CO ratio was close to stable (around 1.9), showing the ability of the produced synthesis gas to be directly used for energy/heat or chemical production.
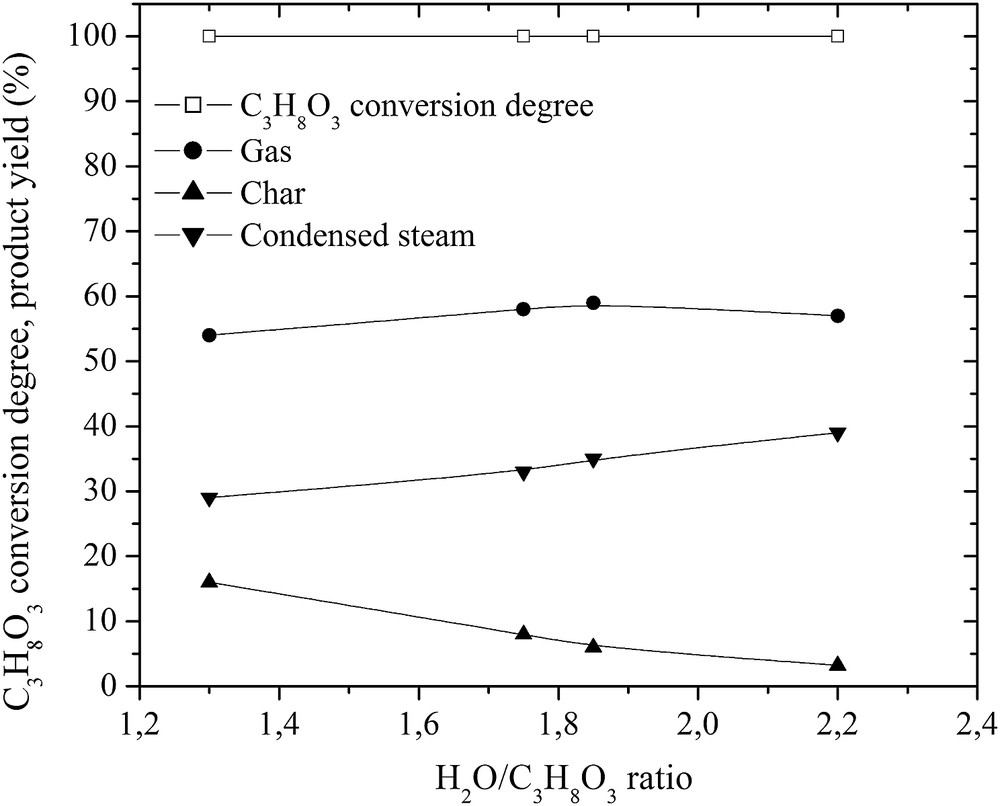
Effect of the H2O/C3H8O3 ratio on the glycerol conversion degree and product yield.
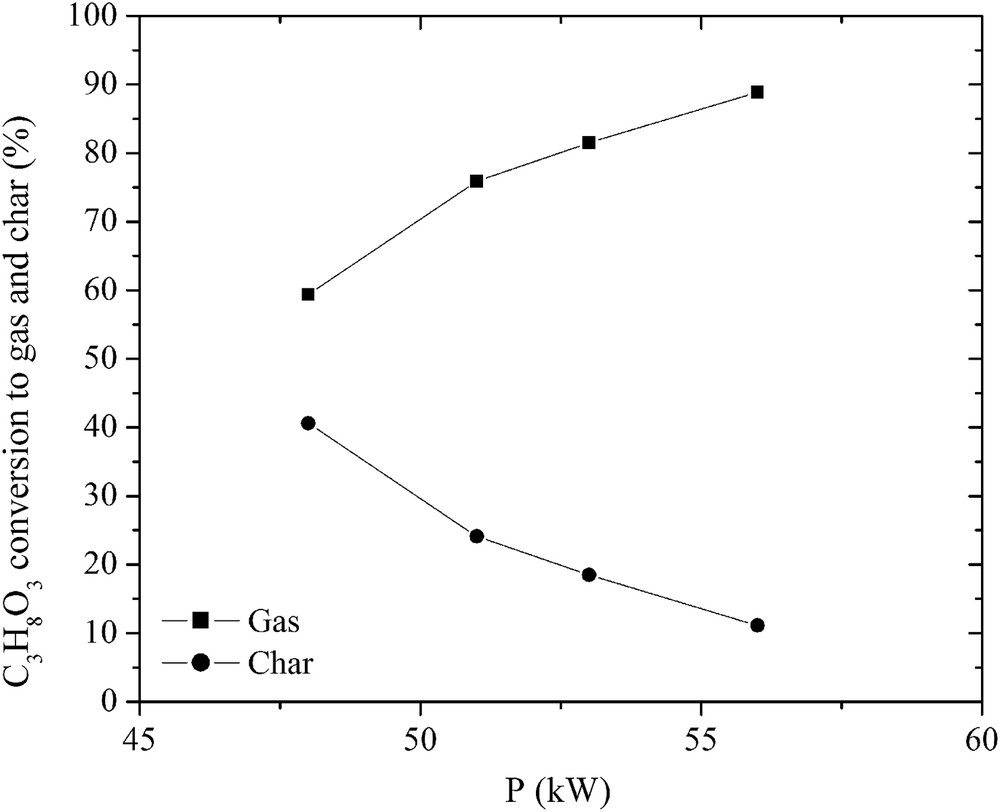
Effect of the plasma torch power on the glycerol conversion to gas and char.
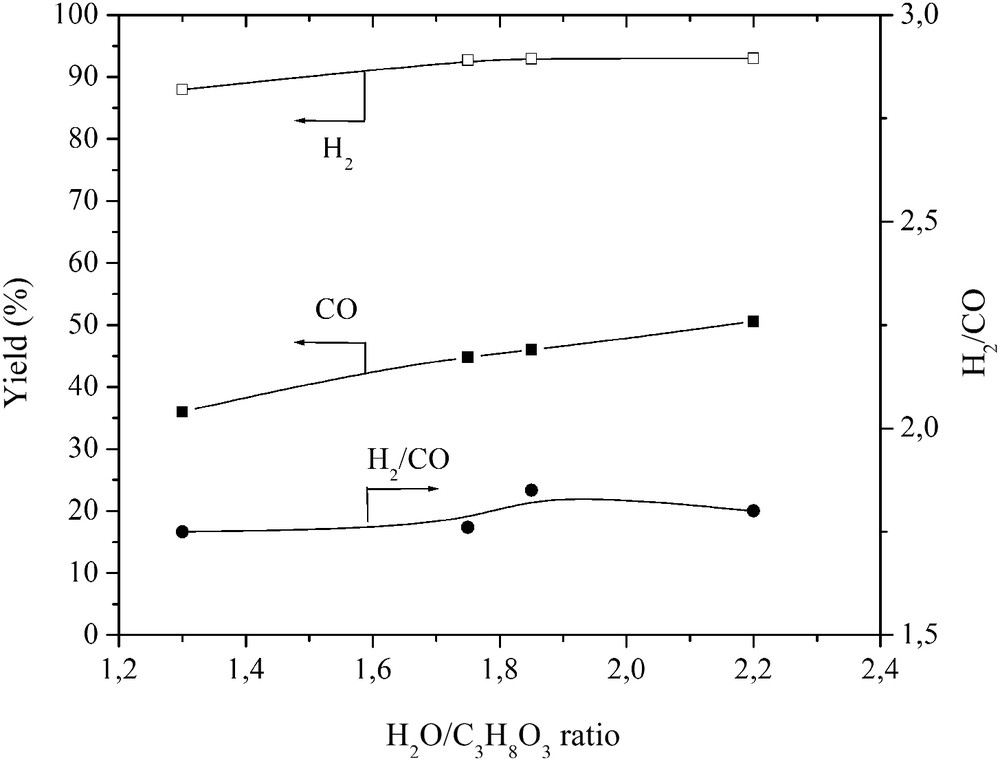
Effect of the H2O/C3H8O3 ratio on the H2 and CO gas yield and H2/CO ratio.
The best conversion process efficiency was obtained at an ηeff of 51% and SER of 59 kJ/mol (equal to 0.54 kWh/kg) when the flow rates of glycerol and steam were 2 g/s and 4.48 g/s, respectively, and the plasma torch power was 56 kW (Fig. 6).
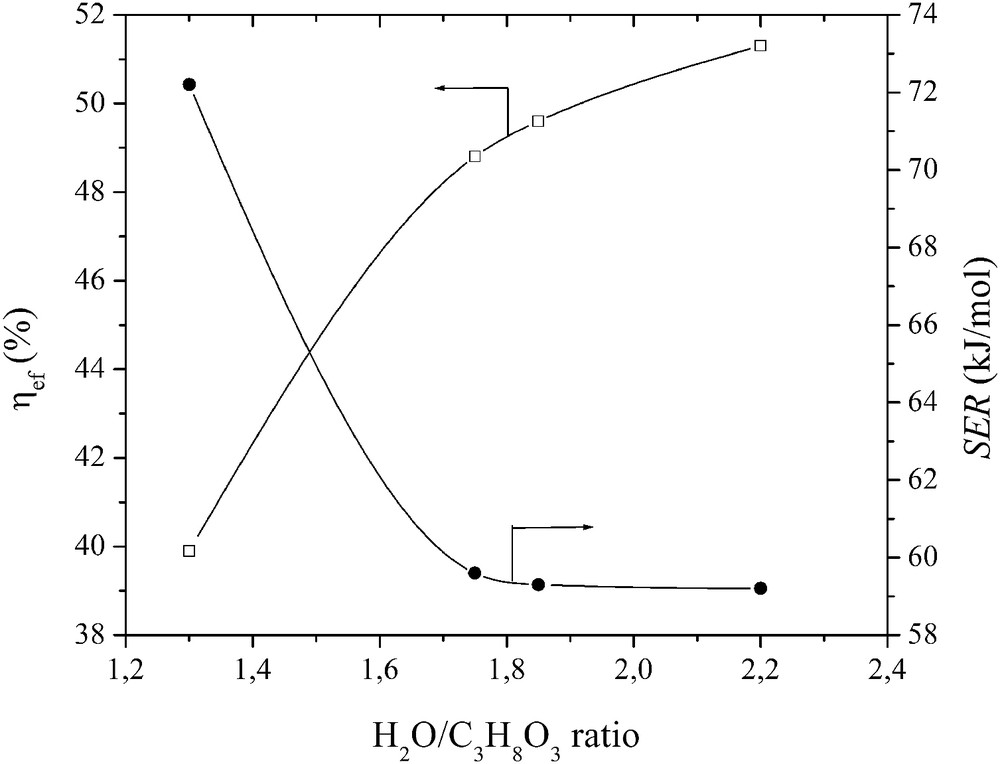
Effect of the H2O/C3H8O3 ratio on the energy expenditure.
The results suggest that there is a potential for the further increase of the flow rate of glycerol in order to achieve a better reaction performance as well as the process efficiency. However, the char formation could be minimized by improving the reactor design, i.e. installing the glycerol spray nozzles closer to the plasma jet or by increasing the reaction temperature. Hence, glycerol could be converted even much faster by a high-temperature steam plasma with a higher active radical concentration inside.
3.2 Wood conversion
Wood conversion in the ambient of the water steam plasma was carried out under the following experimental conditions: wood flow rate 1.2 g/s, steam flow rate 2.63–4.48 g/s, and the plasma torch power 49 kW–56 kW. The H2O/wood ratio was in the range of 2–3.4, Tf = 2800 K.
The concentrations of the gas produced after wood conversion are shown in Fig. 7. As the H2O/wood ratio increased from 2 to 3.4, the H2 and CO concentrations slightly decreased, whereas the CH4 content increased. The CO2 concentration decreased as the H2O/wood ratio increased to 2.7 and began to increase above the H2O/wood ratio of 2.7. This could be affected by the dominance of the exothermic water–gas-shift reaction. The experimentally obtained H2 and CO concentrations differ from those calculated at a thermodynamic equilibrium by more than 40–50% and 25–50%, respectively. In this case, the CWB code was not suitable for the modeling of the wood conversion process as it does not include the condensed solid phase formation. Wood pyrolysis/gasification in the ambient of water steam plasma is complicated and mostly based on the water–gas, Boudouard hydrogasification, water–gas-shift, and methanation reactions [8, 17].
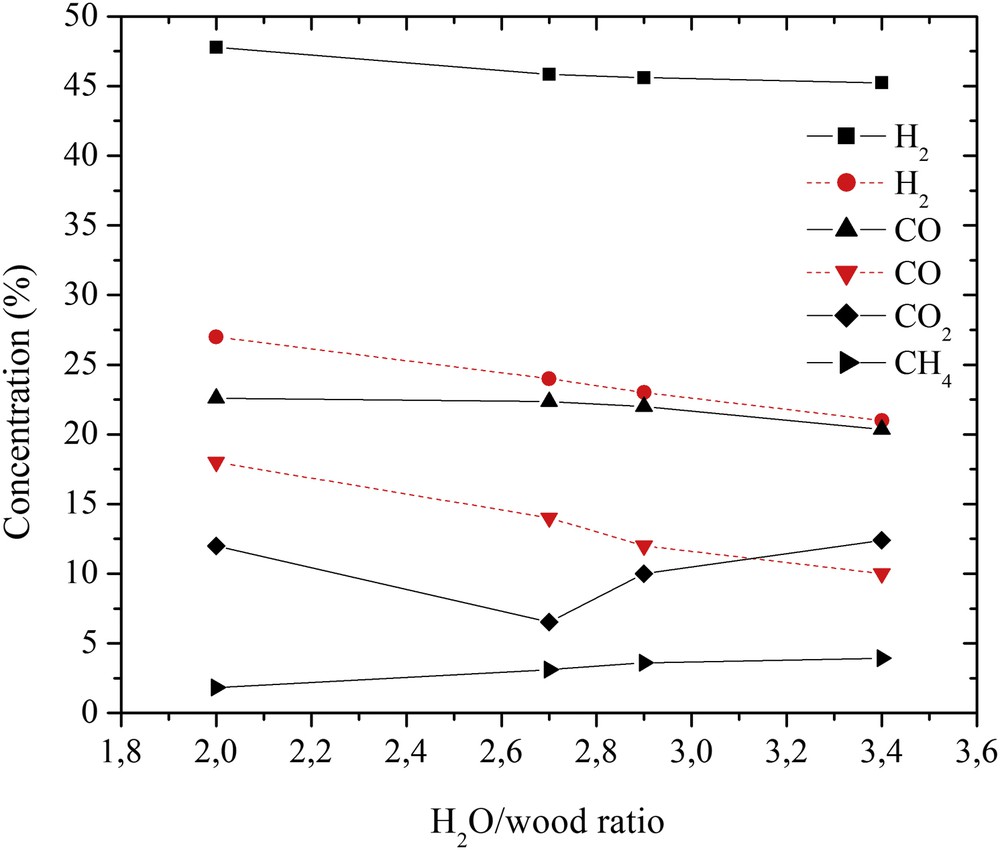
Effect of the H2O/wood ratio on the produced gas composition. The full line represents the experimental results, and the dashed red line represents the calculated data.
The wood was completely converted to gas, liquid and char, as it is shown in Figs. 8 and 9. At the plasma torch of 56 kW and the H2O/wood ratio of 3.4, the residence time was sufficient for the wood conversion to gas, liquid, and char. The yield of char in the total reaction product mass balance decreased to 0.5%, while that of gas increased to 55%, giving a carbon conversion efficiency of up to 97.5%. As wood consists of moisture (H2O) and H2, the yield of liquids, mostly condensed water, slightly increased due to the excess steam used in the process and the wood methanation reaction [8]. The H2 yield increased from 60% to 87%, while that of CO increased only from 35% to 54%, as indicated in Fig. 10. If compared with the glycerol conversion, wood consists of only ∼5–7% of H2 in the total mass, while the quantity of hydrogen in glycerol is much higher. For this reason, the H2 yield is lower in the wood conversion case. The formation of intermediates such as CH4, C2H2 and the combustion product CO2 determines the lower CO yield. This might be improved in the same way as described in the glycerol conversion case. The H2/CO ratio slightly increased at a H2O/wood ratio of 3.4. It could be explained by the dominance of the water–gas-shift, CO oxidation and methanation reactions [17]. The H2/CO ratio indicates that the produced synthesis gas was of high quality and could be used for energy/heat or chemical production [10–14, 34].
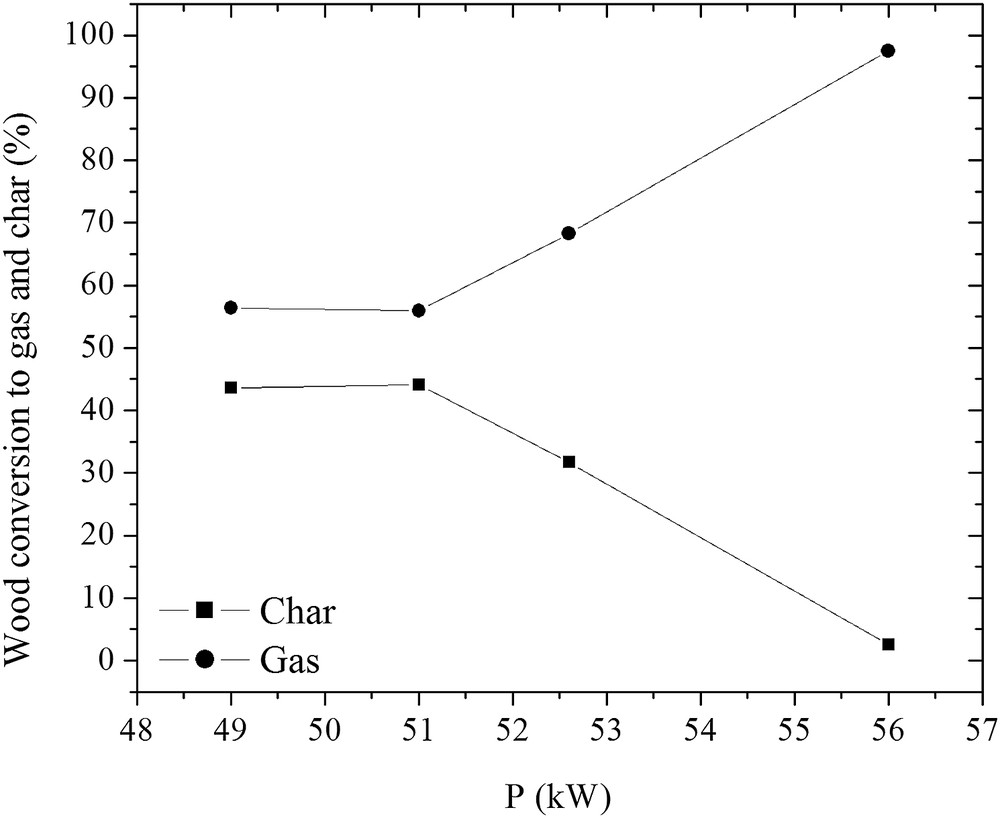
Effect of the plasma torch power on the wood conversion to gas and char.
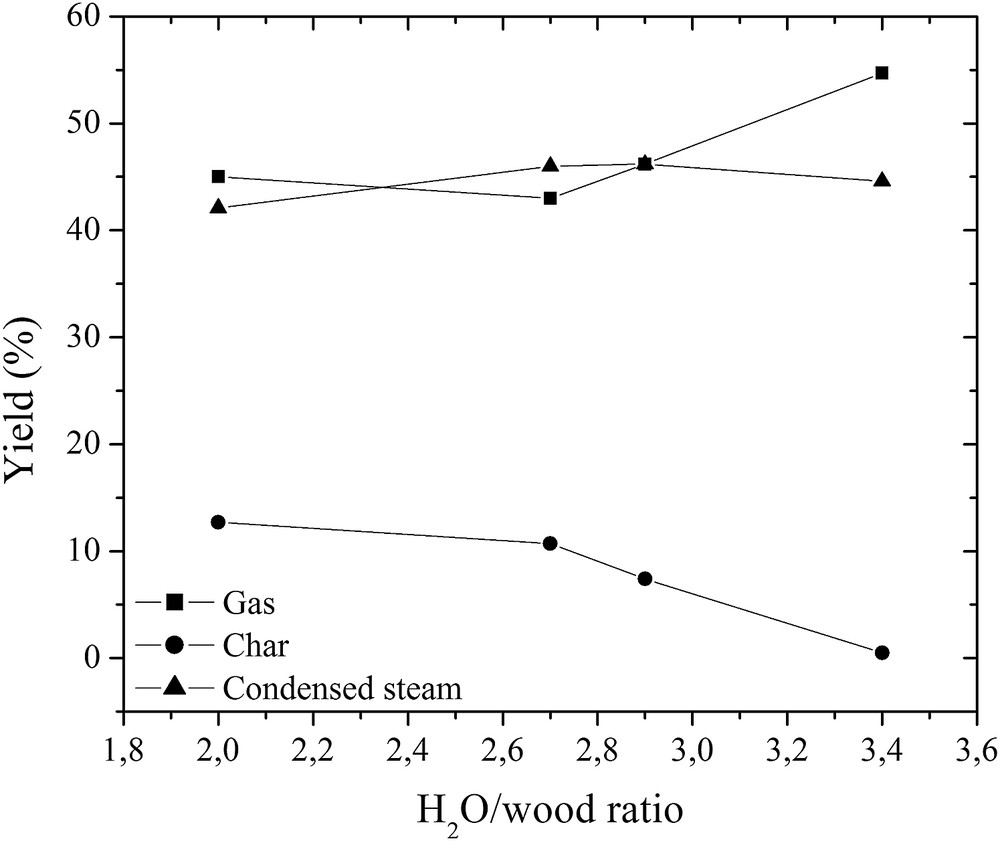
Effect of the H2O/wood ratio on the product yield.
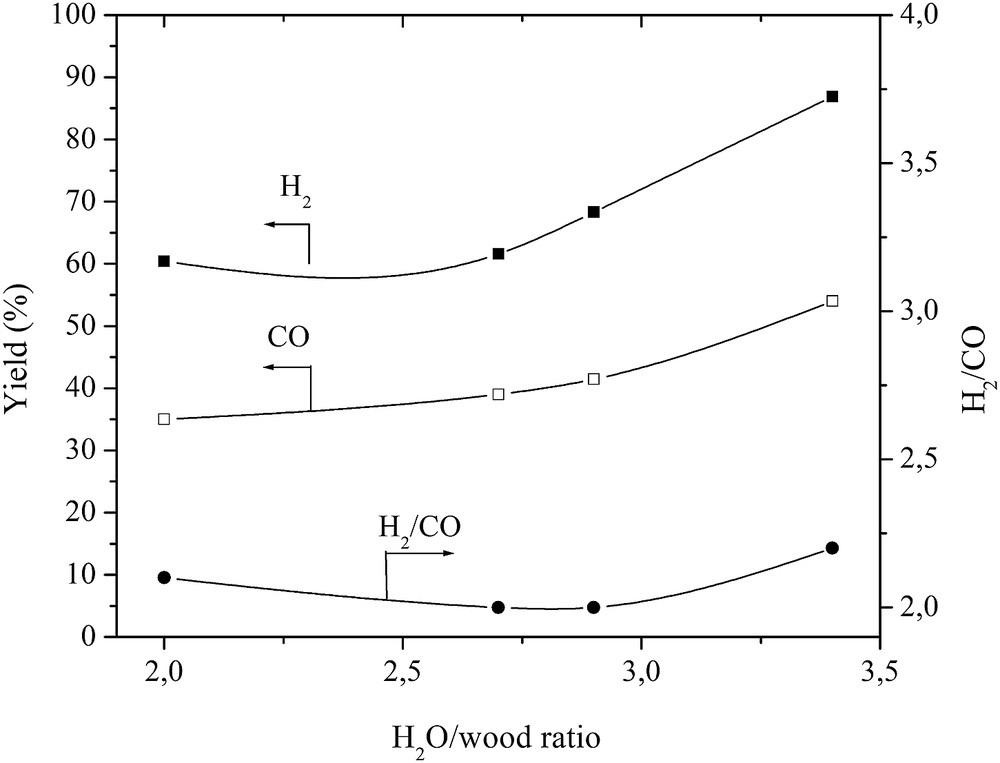
Effect of the H2O/wood ratio on the H2 and CO gas yield and the H2/CO ratio.
The highest process efficiency of the wood conversion was obtained at a ηeff of 45.6% and SER of 69 kJ/mol (equal to 0.64 kWh/kg) when the flow rates of wood and steam were 1.2 g/s and 4.48 g/s, respectively, and the plasma torch power was 56 kW (Fig. 11).
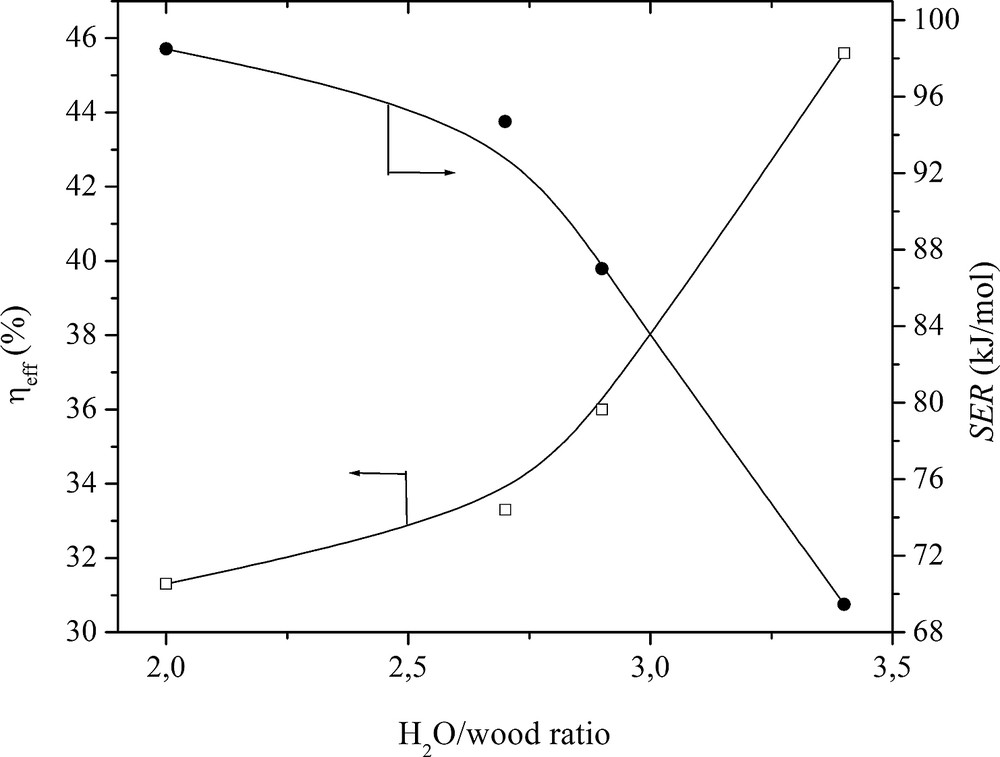
Effect of the H2O/wood ratio on the energy expenditure.
3.3 Comparison of the conversion process
The comparison of glycerol and wood conversion to synthesis gas by means of the thermal steam plasma is described in this section. The results of the conversion process under the best experimental conditions are shown in Table 1.
Comparison of the conversion processes.
Material | H2 (Yield%) | CO (Yield%) | H2/CO | ηeff (%) | SER (kJ/mol) |
C3H8O3 | 93 | 55 | 1.9 | 51 | 59 |
Wood | 87 | 54 | 2.2 | 45.6 | 69 |
Due to the physical properties and size of wood, the process efficiency was lower and the specific energy requirements were higher as compared with the glycerol conversion case. Therefore, an additional energy was required to heat, boil up, evaporate and convert wood to gas. Hence, wood required a higher energy to be converted to gaseous compounds if compared with liquid glycerol. According to the results in Table 1, the SER for converting wood to synthesis gas was 10 kJ/mol higher than that in the case of glycerol, thus leading to a 5.4% lower process efficiency. In the future, the process efficiency depending on the size of treated wood is planned to be examined. It could be stated from the above table that in both cases the decisive parameter for the effective material treatment was the steam flow rate which also influenced the power of the plasma torch at a constant arc current. As the flow rate of steam increased from 2.63 to 4.48 g/s, the best conversion process efficiency was obtained. Moreover, the presence of active radicals in the plasma stream and high plasma temperatures (reaching up to 2800 K) enabled to treat materials with a high conversion efficiency at a short residence time (varying from 0.5 to 1 s). Therefore, the main components after the conversion of glycerol and wood are H2 and CO, together representing around 55% in the total product mass balance. The concentrations of intermediate gaseous products, such as CH4 and C2H2, even with a small content exceeding 5–7% in the total mass balance should also be taken into account. This might help to increase the process efficiency converting them to H2 and CO through the complex heterogeneous and homogeneous reactions involving methanation, hydrogasification, water–gas, Boudouard and water–gas-shift chemical reactions [17]. During this experimental research, the concentrations of CH4 and C2H2 slightly increased as the steam/fuel ratio increased. In the case of glycerol reforming, the content of CH4 and C2H2 increased from 4.5% to 5.3% and from 1% to 1.65%, respectively, whereas in the case of wood conversion, only CH4 with concentrations in the range of 1%–4% was observed. This suggests that there is potential to minimize the formation of these compounds by improving the technological process.
Another constituent in the mass balance is condensed incompletely reacted water which was used as a plasma-forming gas, the heat carrier and the main reactant. Due to its physical properties, condensation is inevitable. Moreover, the flow rate of steam used to run the plasma torch stably is optimal, and thus, there is no possibility to achieve it completely reacted. Nevertheless, the increase of the flow rate of treated materials might help to increase the amount of reacted steam and to minimize its quantity in the final reaction product mass balance. Therefore, the optimal conversion process establishment is required.
The amount of char in the reaction products’ mass balance varies from 1 to 4%, showing the great potential of the thermal plasma technology to be applied for the effective treatment of organic materials. On the other hand, the low carbon monoxide yield requires making the conversion process more selective. Therefore, special catalysts supported by Cu, CuO, Cr2O3, Ni, NiO, ZrO2, Al2O3, and magnesium-containing materials might be used to reduce the content of intermediates as reported in [35, 36]. Furthermore, the increase of the plasma temperature up to 4000 K would lead to a full steam decomposition into elemental substances such as H, O, OH, O2 and H2. It will also help to increase the yields of H2 and CO, because at a mean plasma temperature of 2800 K, reached during the experiments in the reaction zone, only 25% of steam was dissociated according to the CWB calculations and [37]. However, the achievement of such a temperature is a challenging technological issue.
The H2/CO ratio was close to 2 in both cases. It implies that the produced synthesis gas is suitable for the direct energy/heat or chemical production via the Fisher–Tropsh synthesis. It is worth stating that no dangerous compounds after the glycerol/wood conversion have been detected. Only condensed water, valuable synthesis gas (H2+CO) and small amounts of solid carbon were found. This implies that the thermochemical arc plasma technology, where the overheated steam is used as a plasma-forming gas, the heat carrier and the reactant, can be an effective and environmentally friendly biomass treatment method. Moreover, the method used in this study is not limited to any kind of organic material (gaseous, liquid or solid) to be effectively treated to valuable products. However, more detailed experimental investigations are required in order to prove the economic feasibility of the technology used.
4 Conclusions
In this experimental research, a thermal DC arc discharge water steam plasma was used to convert glycerol and wood to a synthesis gas. Additionally, chemical process modeling was used to investigate the concentrations of products at the thermodynamic equilibrium. The TER model showed quite a good agreement between the experimental and simulated data only for H2 in the case of glycerol conversion, but it was unsuitable in the case of wood conversion.
After glycerol conversion, the mainly formed products were H2 and CO with concentrations of 47% and 25%, respectively. The water steam flow rate and the plasma torch power were the crucial parameters for the effective glycerol conversion. As the H2O/C3H8O3 ratio and the plasma torch power increased, the yield of gas and char produced in the total reaction product mass balance increased to 55% and 3%, respectively, giving the highest carbon conversion efficiency of 88.9%. The highest yields of H2 and CO were 93% and 55%, respectively. The best conversion process efficiency was obtained at an ηeff of 51% and a SER of 59 kJ/mol.
After wood conversion, the mainly formed products were H2 and CO with the concentrations of 45.2% and 21%, respectively. As in the case of glycerol, the increasing water steam flow rate and the plasma torch power were the decisive parameters for the effective wood pyrolysis/gasification. The yield of char in the total reaction product mass balance decreased to 0.5%, while the gas yield increased to 55%, giving the highest carbon conversion efficiency of 97.5%. The highest yields of H2 and CO were 87% and 54%, respectively. The wood conversion process required a higher SER of 69 kJ/mol compared to the case of glycerol conversion. Therefore, it determined a lower conversion process efficiency of 45.6%.
The H2/CO ratio indicates that the produced synthesis gas is of high quality and, therefore, may be further used for energy/heat or chemical production.
The thermochemical DC arc discharge water steam plasma technology could be an effective and competitive technology for biomass conversion to synthesis gas because of the high plasma enthalpy (temperature), active radicals, easy process control, and relatively high energy efficiency. The future studies will focus on the process optimization. Furthermore, a detailed comparison with different plasma technologies will be proposed.