Fatigue crack propagation can considerably reduce the life of components, leading to sudden failures. This paper provides a method for fatigue life prediction based on ultrasonic non-destructive inspection applied on Al 2024 T3 material.
A new crack quantification model based on ultrasonic waves features is developed. To analyse the performance and efficacity of the model, the probability of detection is determined using the “signal response” technique.
The Paris model is used to predict the fatigue life taking into consideration the initial crack distributions, the dispersion of the parameters underlined by the Least-squares method and Monte-Carlo simulations.
Reliability evaluation is discussed later for two cases: Detection and No-detection case.
If no indication is presented, an inspection detection threshold is determined and optimized. This proposed indicator will be helpful for industrial environments whenever the inspection machine does not have any indication.
Considering the ultrasonic inspection data, an updating reliability via the Bayesian approach is suggested. The results of this approach can lead to a gain in the life span or a gain of the costs generated by the failure of the part.
Révisé le :
Accepté le :
Publié le :
Iheb Chouikh 1 ; Chokri Bouraoui 1
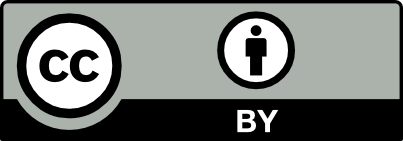
@article{CRMECA_2023__351_G1_105_0, author = {Iheb Chouikh and Chokri Bouraoui}, title = {A fatigue-reliability approach using ultrasonic non-destructive inspection}, journal = {Comptes Rendus. M\'ecanique}, pages = {105--124}, publisher = {Acad\'emie des sciences, Paris}, volume = {351}, year = {2023}, doi = {10.5802/crmeca.179}, language = {en}, }
Iheb Chouikh; Chokri Bouraoui. A fatigue-reliability approach using ultrasonic non-destructive inspection. Comptes Rendus. Mécanique, Volume 351 (2023), pp. 105-124. doi : 10.5802/crmeca.179. https://comptes-rendus.academie-sciences.fr/mecanique/articles/10.5802/crmeca.179/
[1] Pitch-catch active sensing methods in structural health monitoring for aircraft structures, Struct. Health Monit., Volume 7 (2008), pp. 5-19 | DOI
[2] State-of-the-art in structural health monitoring for aeronautics, Proceedings of International Symposium on NDT in Aerospace, Fürth/Bavaria-Germany (2008)
[3] Structural health monitoring and damage prognosis in fatigue, Struct. Health Monit., Volume 7 (2008) no. 1, pp. 37-49 | DOI
[4] A review of non-destructive testing techniques for the in-situ investigation of fretting fatigue cracks, Mater. Des., Volume 196 (2020), 109093 | DOI
[5] et al. Assessment of existing steel structures: recommendations for estimation of remaining fatigue life (2008) (Technical report)
[6] et al. Lamb wave interaction with a fatigue crack in a thin sheet of Al2024-T3, EU Project Meeting on Aircraft Integrated Structural Health Assessment (AISHA), Leuven, Belgium (2007)
[7] Ultrasonic sensing and life prediction for the DARPA structural integrity prognosis system, Rev. Quant. Nondestruct. Eval., Volume 894 (2007), pp. 1453-1460 | DOI
[8] Probability of Detection (PoD) Curves Derivation, Applications and Limitations, Health & Safety Executive, Norway, 2006
[9] Crack inspection using guided waves (GWS)/structural health monitoring (SHM), Rev. J. Appl. Sci., Volume 17 (2017), pp. 415-428 | DOI
[10] A model assesment method for predicting structural fatigue life using Lamb waves, Ultrasonics, Volume 84 (2017), pp. 319-328 | DOI
[11] A fatigue crack size evaluation method based on lamb wave simulation and limited experimental data, Sensors, Volume 17 (2017), 2097
[12] et al. A probabilistic crack size quantification method using in-situ Lamb wave test and Bayesian updating, Mech. Syst. Signal Process., Volume 78 (2016), pp. 118-133 | DOI
[13] Modelling of lamb wave interaction with open and closed fatigue cracks for damage detection, IOP Conf. Ser.: Mater. Sci. Eng., Volume 10 (2010), 012059
[14] Structural health monitoring and propagation of lamb waves to identification of crack, 4th International Conference on Materials Processing and Characterization, Materials Today: Proceedings, Volume 2 (2015), pp. 1833-1840
[15] et al. Probabilistic fatigue life prediction and structural reliability evaluation of turbine rotors integrating an automated ultrasonic inspection system, J. Nondestruct. Eval., Volume 33 (2014), pp. 51-61
[16] et al. Toward optimal updating time inspection based on reliability approach of fatigue crack propagation, Appl. Mech. Mater., Volume 146 (2012), pp. 96-111 | DOI
[17] Model uncertainty and Bayesian updating in reliability-based inspection, Struct. Saf., Volume 22 (2000), pp. 145-160 | DOI
[18] Reliability-based inspection planning of the ship structure exposed to fatigue damages, Brodogradnja-Shipbuilding, Volume 69 (2018) no. 2, pp. 119-134 | DOI
[19] Inspection scheduling based on reliability updating of gas turbine welded structures, Adv. Mech. Eng., Volume 11 (2019) no. 1, pp. 1-20 | DOI
[20] Optimal inspection and repair scheduling for mitre lock gates, Proc. Inst. Civ. Eng.: Marit. Eng., Volume 172 (2019) no. 3, pp. 95-103
[21] An integrated probabilistic approach for optimum maintenance offatigue-critical structural components, Mar. Struct., Volume 68 (2019), 102649
[22] Probabilistic optimization framework for inspection/repair planning offatigue-critical details using dynamic Bayesian networks, Comput. Struct., Volume 198 (2018), pp. 40-50 | DOI
[23] Advanced ultrasonic “probability of detection” curves for designing in-service inspection intervals, Int. J. Fatigue, Volume 86 (2016), pp. 77-87 | DOI
[24] Issues in estimating probability of detection of NDT techniques—a model assisted approach, Ultrasonics, Volume 87 (2018), pp. 59-70 | DOI
[25] Detection and monitoring of hidden fatigue crack growth using a built-in piezoelectric sensor/actuator network: I. Diagnostics, Smart Mater. Struct., Volume 13 (2004), pp. 609-620 | DOI
[26] Nondestructive Evaluation System Reliability Assessment, Department of Defense of the US, 2009
[27] et al. A multi-feature integration method for fatigue crack detection and crack length estimation in riveted lap joints using Lamb waves, Smart Mater. Struct., Volume 22 (2013), 105007
[28] Reliability analysis and inspection updating by stochastic response surface of fatigue cracks in mixed mode, Eng. Struct., Volume 33 (2011) no. 12, pp. 3392-3401 | DOI
[29] Fracture Mechanics: Fundamentals and Applications, CRC Press Taylor & Francis Group, 2005 | DOI
[30] Probability of detection (POD) determination using ultrasound phased array for considering NDT in probabilistic damage assessments, 18th World Conference on Nondestructive Testing, Durban, South Africa (2012)
[31] A probabilistic fatigue approach for riveted joints using Monte Carlo simulation, J. Constr. Steel Res., Volume 110 (2015), pp. 149-162 | DOI
[32] Overview of structural reliability analysis methods-part I: Local reliability methods, OpenScience, Volume 10 (2016), 21494
[33] Target Levels for Reliability-based Assessment of Offshore Structures During Design and Operation, Health & Safety Executive, Norway, 1999 (ISBN 0 7176 2303 3)
[34] et al. Fatigue damage diagnosis and prognosis using bayesian updating, Structures, Structural Dynamics, and Materials and Co-located Conferences, Boston, Massachusetts, Volume 6 (2013), p. 1652
Cité par Sources :
Commentaires - Politique