1 Introduction
With increasing concerns about non-renewable fossil energy sources, greater emphasis has been placed on the exploration of renewable energy sources, such as lignocelluloses. Among other possible dedicated energy crops, the use of Miscanthus x giganteus has received considerable attention due to its widespread availability and lack of competition with food and animal feed. Miscanthus features many favorable agronomic characteristics and leads to tremendous biomass yields [1]. An alternative use for miscanthus would be bioethanol production, which is based on the enzymatic saccharification of cellulose into fermentable sugars. Given the resistance of lignocelluloses to enzymatic degradation, saccharification generally requires physicochemical pretreatment and generates a lignin-enriched by-product [2]. Sustainable ethanol production from lignocelluloses would however imply not only a reduction in the consumption of chemicals and/or energy resources, but also reuse of the lignocellulosic by-product remaining after enzymatic saccharification. Introducing these by-products into a cementitious matrix could be useful when manufacturing a lightweight composite.
Since the 1950s, efforts to reduce concrete weight have been intensified in order to satisfy handling, transport and design constraints. A lightweight concrete displays a bulk density equal to 1800 kg.m−3 or less, while the bulk density of conventional concretes varies between 2200 kg.m−3 and 2500 kg.m−3. In addition to its low density, lightweight concrete offers other attributes as well. Research has demonstrated that such lightweight materials are thermally and acoustically advantageous [3–5]. A lightweight building material can be manufactured in two ways: introduction of lightweight aggregates, and creation of a cellular structure.
Over the past two decades, studies have been conducted on the use of lignocellulosic resources as lightweight aggregates in designing lignocellulosic cement composites. Natural fibers originating from bamboo [6], sisal [7], coconut [8], jute [8], malva [9], eucalyptus [10,11] and hemp [12] or else by-products of wood [6,13] or rice husk [6], bagasse [14] and flax shaves [15] have been employed. Such uses of lignocellulosic resources are intended to offer an attractive alternative to their disposal. In this respect, lignocellulosic resources offer a number of suitable features such as low density, limited processing equipment requirements and abundant raw material supply [16]. Since these materials are primarily composed of cellulose, hemicelluloses and lignin however, they may exert influence on the manufacturing of cementitious composites. Lignocellulosic aggregates show very high sensitivity to water. During the composite manufacturing process, aggregates compete with cement to absorb the mixing water, with water flow enhancing increase in lignocelluloses size due to its chemical composition and porous structure. This phenomenon is named the suction phase. This vegetal larger lignocelluloses aggregates then becomes a water reservoir. A number of research findings indicate that the incorporation of lignocellulosic aggregate inhibits cement setting. Weatherwax et al. [17] observed a total inhibition of setting time with a composite made of pine, whereby the composite remained indefinitely in a pasty state. Extractive compounds like starch, sugar, some phenols and even hemicelluloses and lignin cause a delay in setting time [18,19]. The consequences of this delay are a deceleration of species development and, consequently, slower strength gain and longer demolding time [20]. Some studies have shown that sugars are responsible for changes in setting time. A small sugar concentration in cement paste (0.03–0.15%) was found to be sufficient to cause a delay in setting time [21]. In fact, the work of Biblis et al. [20] reported that glucose and cellulose strongly influenced cement hydration. The influence of sugar on setting time can be explained by the capacity of sugar to absorb on products containing calcium ions, thereby preventing the hydration of tricalcic silicate (C3S) and its transformation into hydrated calcium silicate (C-S-H). However, the silicate components of Portland cement are responsible for the mechanical strengths of the composite obtained at an early age. Consequently, when tricalcic silicate hydration is disturbed, the mechanical strength of the cementitious matrix is significantly altered as well.
To overcome the disadvantages mentioned above, several solutions are possible, such as pretreatment of aggregates or the cement matrix, or modification of the manufacturing process. Various processes have been studied herein, including the extraction of soluble sugars using cold or hot water [22] or the incorporation of chemical accelerators like sodium hydroxide (NaOH), sodium silicate (Na2SiO3) [23], aluminum sulfate (Al2[SO4]3) [13] and calcium chloride (CaCl2) [24].
The present study was carried out on by-products of the enzymatic saccharification of Miscanthus x giganteus. With the intention of reusing all of the biomass, this study was undertaken in order to determine if by-products from chemical pretreatment and saccharification can be used directly in a cementitious matrix as lightweight aggregates. One of the main objectives of this original study has been to assess whether the saccharification of miscanthus, in addition to an acid or ammonia-based pretreatment, would be sufficient to overcome the aforementioned disadvantages relative to lignocelluloses incorporation in a cementitious matrix.
2 Materials and methods
2.1 Raw materials
2.1.1 Cement
The cement (C) used in this study is an artificial Portland Cement CPA CEM I 52.5 supplied by Calcia, in accordance with the EN 197-1 Standard. Its apparent bulk density equals 1000 kg.m−3 at room temperature and moisture. This cement facilitates supervision of the study, since its contents are limited to clinker and gypsum; moreover, it is being used with the aim of avoiding the formation of subsidiary compounds that can form in the presence of subsidiary components, thus avoiding excessive dispersion in the results. However, this condition in no way limits the use of mixed cements, since when performance is expected, this particular cement is favored by the profession.
2.1.2 Mixing water
The mixing water (W) is standard drinking water extracted from the public water supply network at a temperature of 20 ± 2 °C and a pH of 7.45 ± 1.
2.1.3 Raw miscanthus (RM)
Miscanthus x giganteus was introduced in April 2006 and grown for 2 years without nitrogen supplementation in experimental fields at Inra Estrée-Mons (France). The plant biomass was harvested in November 2007 (early harvest) and again in February 2008 (late harvest, once the leaves had fallen) [25]. This study has only focused on the early-harvest miscanthus. After harvesting, plant samples were dried at 40 °C in a forced air oven for 3 days and then stored under dry conditions at room temperature until their use. The dry biomass was milled using a Retsch mill equipped with a 1-mm sieve.
2.1.4 By-products from the enzymatic saccharification of miscanthus
Two different aggregate types were selected for this study, both of which are by-products of the enzymatic extraction of fermentable sugars from pretreated miscanthus [25].
After two distinct pretreatments of raw miscanthus (RM) with either acid (2% H2SO4, 121 °C, 1 hour) (with an acid/miscanthus ratio of 0.04) or 33% aqueous ammonia at a 1/6 ratio (miscanthus/ammonia: w/v, i.e. 15% NH3) for 3 days at room temperature [26], the enzymatic saccharification was carried out with an enzymatic cocktail (cellulase, β-glucosidase and xylanase) at 50 °C for 48 hours, as previously described [25]. The enzymatic residues were then collected prior to incorporation into the cementitious matrix, and ultimately designated AER (for enzymatic residues pretreated with acid prior to saccharification) and NER (for enzymatic residues pretreated with aqueous ammonia prior to saccharification).
The composition of both the raw material and enzymatic residues after chemical pretreatment was determined as previously [25]. The water absorption capacity of aggregates was determined before developing the composite in order to saturate the aggregates and counter the effects of the suction phase. If aggregates are not saturated, they can indeed absorb water from the mixture and cause modifications in composite properties in both the fresh and hardened states. Naik et al. observed a decrease in the workability of fresh composite [27]. Water absorption by aggregates also leads to a significant presence of water near the aggregates. The result of this condition is greater porosity in the interfacial zone once the composite has dried. From a mechanical standpoint, this zone is thus considered as a weakness in the composite [7]. Moreover, during composite hardening, water flows in the opposite direction, which results in dimensional variations of the composite [8]. The level of water absorption by aggregates was determined on dry aggregate after their immersion in water at 20 °C. Their residue mass was monitored until reaching constant mass.
2.2 Experimental technique
2.2.1 Concrete mixing conditions
A reference cement mortar with water/cement (W/C) ratio equal to 0.3 was prepared. Mixing was performed in accordance with the standard for normalized mortars (EN 196-3), as stated in the requirements to obtain optimal strength development conditions.
In order to verify that the saccharification would be sufficient to overcome the aforementioned disadvantages of lignocellulosic concrete, a mortar was produced with the raw material and designated as the reference composite. A mass percentage of 5% between the dry raw material and the cement was respected. This raw material quantity represents 12% of the total mortar volume. The mixing conditions were optimized on the basis of a set of demolding criteria (Fig. 1).
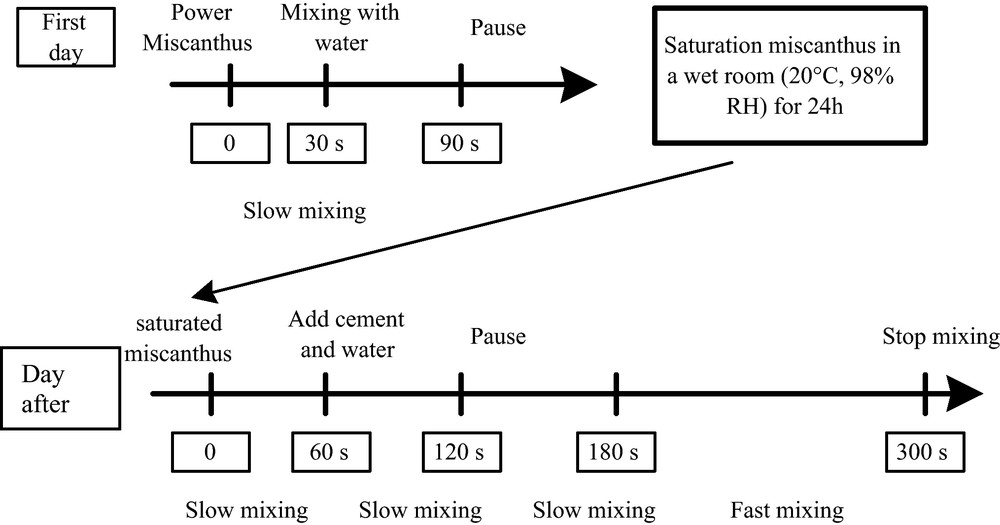
Optimized mixing conditions for the elaboration of lignocellulosic composites.
After the crushing step, the quantity of water required for aggregate saturation was added. Aggregates were then stored in a wet room for 24 hours to ensure complete saturation of plant samples, which is necessary to avoid competition for water between aggregates and cement during the next step. Following this curing period, the aggregates were mixed again at low speed (140 rpm) for 1 min in a standard mixing machine (EN 196-1). Next, the cement and water combined at a 0.3 W/C ratio were gradually added to the saturated aggregates. Mixing was continued for another 2 min at low speed and then 2 min at a faster speed (285 rpm) to obtain a homogeneous mixture. The fresh paste was poured into 40 mm × 40 mm × 160 mm prismatic molds and the samples were stored in a room controlled for both relative humidity and temperature (98% relative humidity and 20 ± 2 °C). It was prohibited to demold the samples after 24 hours, in contradiction with recommendations stated in the standard. To preserve samples, the wet curing period was extended: samples were demolded after 72 hours. Following demolding, the test specimens remained in a storage room for another 28 days. At the end of this curing period, the composites were dried in an aerated oven at 50 °C until achieving constant mass prior to the characterization step.
The mixing conditions described for mortars, including raw miscanthus, can be applied to the manufacturing of mortars with by-products. After saccharification, the wet by-products, which had just been separated from the aqueous phase by filtration under vacuum without extracting water contained in the particles, were directly used to produce the composites. These materials were not dried in order to save energy during the process of manufacturing mortars with by-products. A mass percentage of 5% between dry by-products and cement had been respected since the mortars had been produced using raw miscanthus. This ratio represents 15% of the total mortar volume. To ensure compliance with the (Wtt/Dry matter) ratio determined for the reference composite, the quantity of water added during manufacturing was calculated once again to account for the fact that the lignocelluloses by-products have a different water absorption rate. The amounts of the various constituents used in manufacturing mortars are summarized in Table 1. A cement paste with a Wtt/Dry matter ratio equal to 0.43 was also prepared as the reference composite.
Amount of various constituents used for the manufacturing of mortars (RM: raw material; AER: enzymatic residues pretreated with acid prior to saccharification; NER: enzymatic residues pretreated with ammonia aqueous prior to saccharification).
Dry aggregates (g) | Cement (g) | Water absorption (g) | Water added during manufacturing (g) | Water/Cement | Water/total dry matter | |
RM | 50 | 1000 | 160 | 300 | 0.46 | 0.43 |
AER | 50 | 1000 | 290 | 170 | 0.46 | 0.43 |
NER | 50 | 1000 | 284 | 176 | 0.46 | 0.43 |
2.2.2 Characterization of the composites
The workability of each fresh mortar was determined according to French Standard NF P 18–451. The tests were conducted with a workability meter to measure the time required for the mortar to reach a reference mark in the apparatus under the effect of vibration.
Generally speaking, hardening refers to a process whereby the set mortar gradually strengthens. The initial setting time measurement of fresh mortar is therefore an important parameter for both the manufacturing process and final strength. In our study, the setting time of each fresh composite was determined according to Standard EN-196-3; the corresponding tests were conducted using a Vicat apparatus.
The real bulk density of aggregates was determined gravimetrically by applying the following expression:
The apparent bulk density of the composite was determined from an average of three weighings on a scale accurate to within 0.01 g. Geometric measurements were taken on 40 mm × 40 mm × 160 mm prismatic test samples using the shifting method to within 0.01 cm.
Mechanical properties were assessed on 40 mm × 40 mm × 160 mm prismatic test samples, in compliance with European Standard EN 196-1. Flexural and compressive strengths were evaluated on a standard hydraulic machine with 25 and 250 kN of capacity.
The microstructural morphology of various samples was studied by means of scanning electron microscopy (SEM); this analysis enabled visualizing the macroporosity of the various composites while providing an observation of the paste-aggregate adhesion. The micrographs were derived using a Philips FEG XL 30 microscope. To facilitate these observations, the samples were initially dried and then covered with a thin layer of spray-on gold, which acted as conductor.
3 Results and discussion
3.1 Characterization of the lignocellulosic aggregates
The NER and AER residues obtained from saccharification of ammonia- or acid-pretreated miscanthus represented less than 37% and 42% respectively of the raw miscanthus dry matter. When expressed as initial dry matter, the chemical composition revealed that the treatments had eliminated the soluble components and a portion of the structural components as mainly cellulose and hemicelluloses. When the data were expressed as a percentage of dry matter after saccharification, the proportion of lignin and polysaccharides increased in comparison with raw miscanthus (Table 2). Both aggregates display an irregular shape and rough surface texture that may facilitate matrix-aggregate adhesion (Fig. 2). The real bulk densities of NER and AER residues are low (respectively 291.71 ± 7.25 and 299.87 ± 8.71 kg.m−3), which makes it possible to lighten the cementitious composites. A gap grading analysis of the aggregates revealed an aggregate particle size of up to 1 mm (Fig. 3). As observed by scanning electron microscopy, the amount of small particles between 0.2 and 1 mm decreased after pretreatments and saccharification. This decrease was slightly more pronounced in the case of ammonia pretreatment followed by saccharification.
Composition of enzymatic residues in comparison with raw material (RM) expressed as % initial dry matter and % dry matter of by-products (AER: enzymatic residues pretreated with acid prior to saccharification; NER: enzymatic residues pretreated with ammonia aqueous prior to saccharification).
RM | AER | NER | |
(% initial dry matter) | |||
Cellulose, hemicelluloses | 57.6 | 32.2 | 28.4 |
Lignin | 14.4 | 11.0 | 9.5 |
Soluble compounds | 23.6 | 0 | 0 |
(% dry matter) | |||
Cellulose, hemicelluloses | 74.0 | 76.0 | |
Lignin | 21.2 | 22.0 |
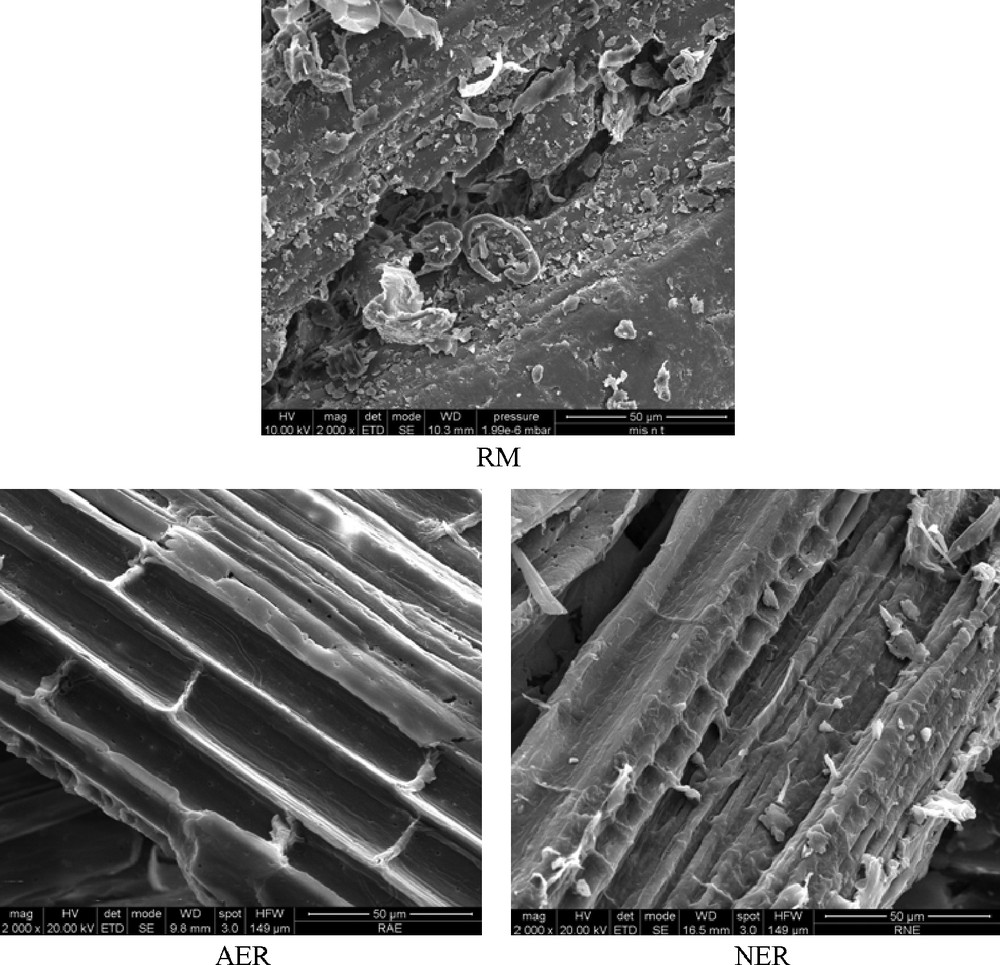
Scanning electron micrographs of lignocellulosic aggregates (magnification = 2000) (RM: raw material; AER: enzymatic residues pretreated with acid prior to saccharification; NER: enzymatic residues pretreated with ammonia aqueous prior to saccharification).
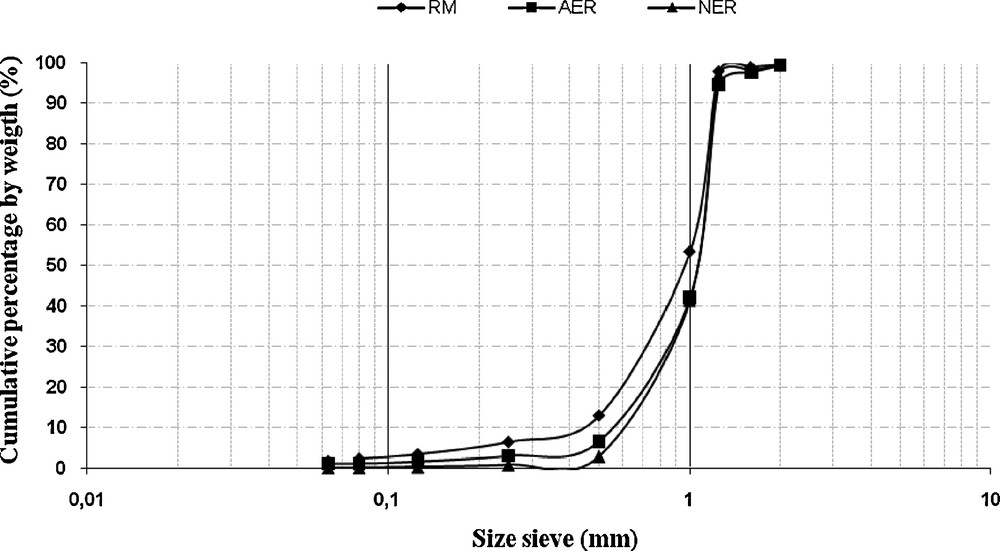
Gap grading analysis of various aggregates (RM: raw material; AER: enzymatic residues pretreated with acid prior to saccharification; NER: enzymatic residues pretreated with ammonia aqueous prior to saccharification).
The lignocelluloses by-products had a water absorption almost double that of raw miscanthus (Fig. 4). The chemical and enzymatic treatments disrupted part of the lignocelluloses, thus opening the cell wall network. The by-products would have a more porous structure, and this may facilitate water penetration. The water absorption of these by-products was higher compared to values reported for other raw plant fibers (bagasse, coconut coir, etc.), which range between 34% and 400% [28]. Regarding the composition of enzymatic by-products, the cellulose and hemicelluloses amounts were greater than other natural vegetable fiber or lignocellulosic by-products reported in the literature [28] and relatively lower than flax fiber, which accounts for approximately 78% of cellulose [29].
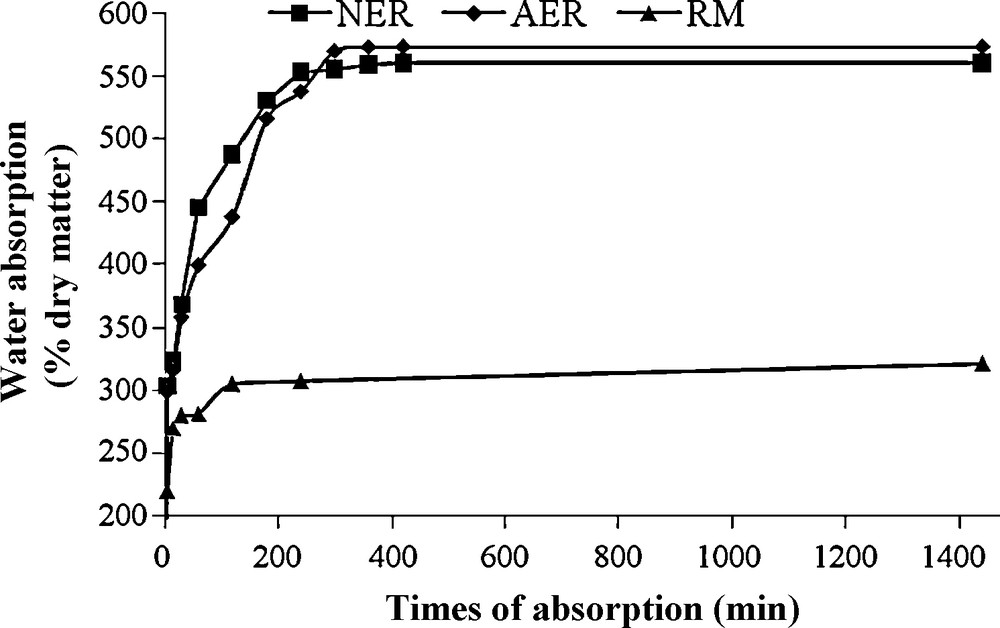
Water absorption of raw miscanthus and by-products (RM: raw material; AER: enzymatic residues pretreated with acid prior to saccharification; NER: enzymatic residues pretreated with ammonia aqueous prior to saccharification).
3.2 Influence of by-products on workability of mortars
The results of mortar outflow time are reported in Table 3 and indicate that flow time is practically cut in half between a standard cement paste and mortars with lignocellulosic aggregates. This decrease may be explained by a significantly higher W/dry matter ratio for lignocelluloses-cement composites. However, in comparison with the workability of cement paste, which features the same water/dry mater ratio (W/C = 0.43), the workability of the composites remains better. Electrostatic interactions between aggregates and cement might enhance this deflocculation and, consequently, improve the flowability of composites [30].
Outflow times and setting beginning time of various mortars (RM: raw material; AER: enzymatic residues pretreated with acid prior to saccharification; NER: enzymatic residues pretreated with ammonia aqueous prior to saccharification).
Mortars | Wtt/Dry matter | Outflow times (s) | Initial setting time (h) |
Cement paste | 0.3 | 5s12 | 2.75 |
Cement paste | 0.43 | 3s28 | 3.5 |
Mortar prepared with RM | 0.43 | 1s94 | 3.75 |
Mortar prepared with AER | 0.43 | 2s5 | 22.75 |
Mortar prepared with NER | 0.43 | 2s2 | 22.25 |
Mortar prepared with AER and CaCl2 | 0.43 | 3s20 | 7 |
Nonetheless, these results contradict the findings of Naik et al. [27], who demonstrated that the presence of plant aggregates increases mortar viscosity. The saturation of by-products before manufacturing could explain these contradictions. Saturated by-products were unable to absorb the water present in the mortar. This improved flowability is an attractive quality for masonry works.
3.3 Influence of by-products on initial setting time of mortar and cement hydration
A determination of the composite setting time proves to be very important since the addition of lignocellulosic aggregates has been previously reported to cause a delay in setting time [18,20,31,32]. Savastano et al. [33] noted that acid compounds released from plant fibers reduced the setting time of the cement matrix and fiber sugar components, hemicellulose and lignin can all contribute to preventing cement hydration [34].
The time when setting actually begins, which depends on the type of mortar being used, is presented in Table 3. In the case of a mortar prepared with raw material, the mortar setting time did not change. This result may be due to the fact that the aggregate had been water saturated. This study shows however that concrete formulated with these by-products requires setting times of 6.5 and 8 times longer than that of standard Portland cement paste, in assuming W/C ratios of 0.43 and 0.3, respectively. These results are in agreement with a previous study, in which the composite was produced using bagasse [34]. Yet, the time required to produce mortar with the by-product was also considerably higher than that when using raw miscanthus. Such findings have been corroborated by the work of Biblis et al. [20].
The composition of lignocellulosic aggregates may explain this additional setting time. The amount of lignin and polysaccharides actually increased in the enzymatic residues, as opposed to raw miscanthus (Table 2). These constituents, which are still present in by-products, may be partially altered under the alkaline conditions of a cementitious matrix [18]. The enzymatic residual cellulose could in fact contain reducing terminal groups that could serve as the starting point for a peeling reaction under alkaline conditions, as observed in a cementitious matrix. This degradation produces isosaccharinic acid and low molecular weight compounds, which are associated with a setting retarding effect in cement paste [35,36]. Moreover, the hemicelluloses and lignin could be altered. Several authors have shown that the products released from the decomposition of cellulose, hemicelluloses and lignin are more effective in retarding hydration than native polymers [37,38]. Also, hydroxyl groups (–OH) from the lignin have chemical properties related to those of sugars, and some even promote the retardation of cement hydration to the same extent as sugars [39].
SEM observation of the composites indicates that the presence of by-products causes a modification in species development (Fig. 5). The water competition between cement and aggregate is not the cause of this difference given that by-products had previously been saturated. As observed by Aggarwal [18] and by Yue et al. [40], C-S-H development is modified due to the presence of insolubles. Alkali moieties released during cement hydration may in fact alter the hemicelluloses and lignin present in aggregates, thus giving rise to the formation of calcium salts of lignin, polysaccharides and certain reducing sugars. These dissolved or precipitated salts interfere, either physically or chemically, with the subsequent hydration of cement and can even change the composition and morphology of the hydrated products [18].
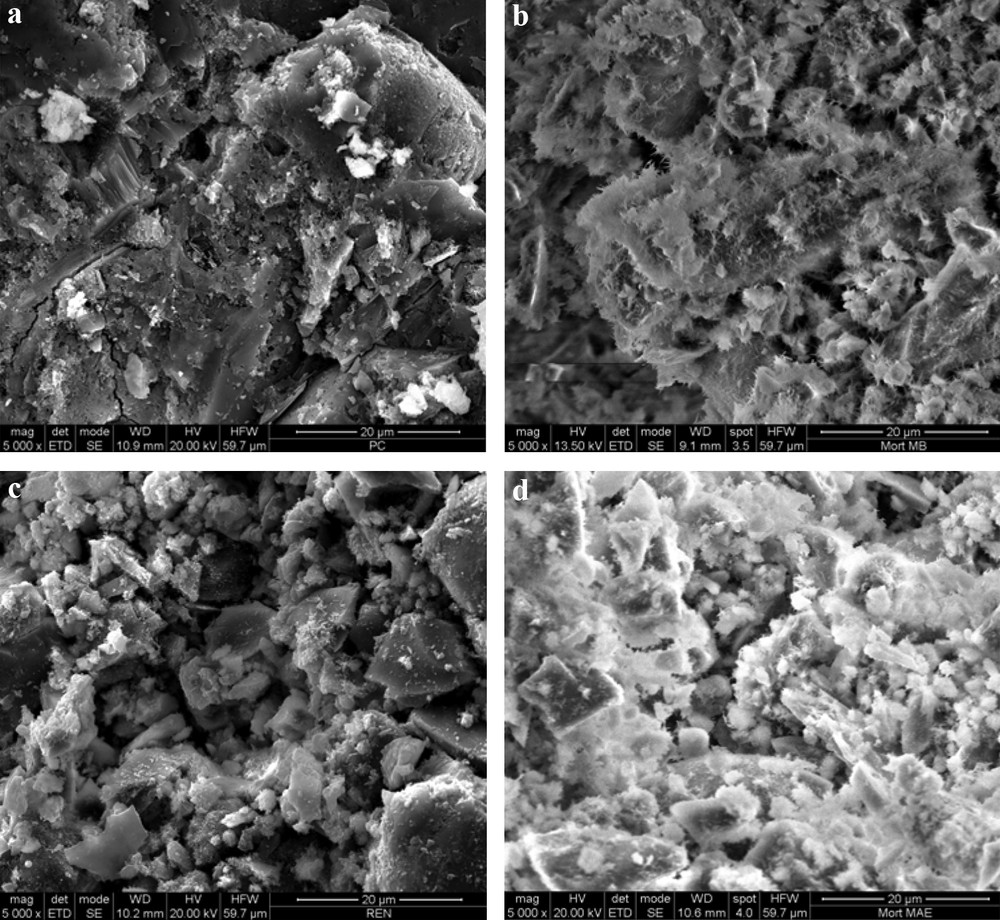
Scanning electron micrographs of lignocellulosic composites (magnification = 5000); a: cement paste; b: composite prepared with raw material; c: composite prepared with enzymatic residues pretreated with aqueous ammonia prior to saccharification (NER); d: composite prepared with enzymatic residues pretreated with acid prior to saccharification (AER).
Preliminary attempts at using a setting accelerator (calcium chloride) in the cementitious matrix have yielded some interesting results. For example, the initial setting time of mortar developed with by-products was reduced to 7 hours (Table 3) and moreover the samples could be demolded after 24 hours [41].
3.4 Impacts on physical and mechanical properties
The apparent bulk densities of the concrete composites and cement pastes are reported in Table 4. The observed decrease in the bulk densities of concrete composites, compared to cement pastes, is mainly due to the low aggregate densities. Furthermore, a microstructural analysis of composite morphology, observed by scanning electron microscopy, revealed that numerous air pores were present when lignocellulosic by-products are mixed with cement paste (Fig. 6). This microstructure may also explain the decrease in bulk densities.
Apparent bulk density of composites (RM: raw material; AER: enzymatic residues pretreated with acid prior to saccharification; NER: enzymatic residues pretreated with ammonia aqueous prior to saccharification).
Samples | Wtt/Dry matter | Bulk density (kg.m−3) |
Cement paste | 0.3 | 1866 ± 13 |
Composite prepared with AER | 0.43 | 1420 ± 16 |
Composite prepared with NER | 0.43 | 1414 ± 8 |
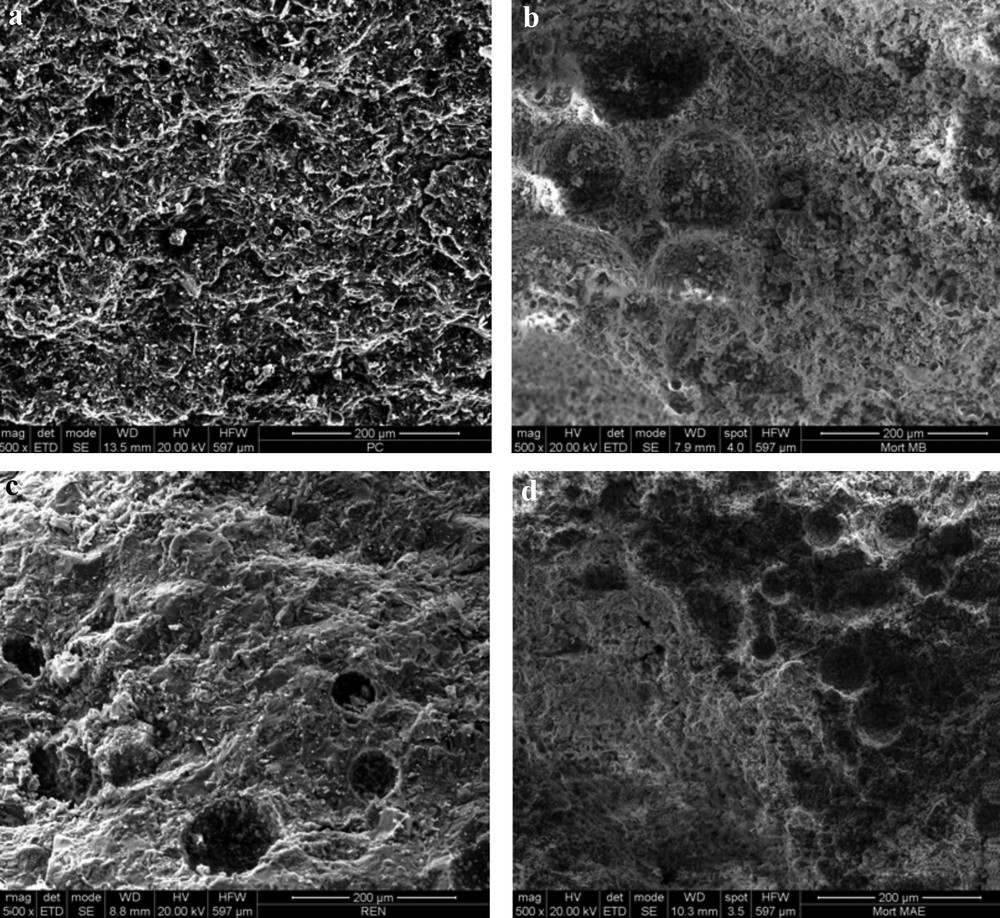
Scanning electron micrographs of lignocellulosic composites (magnification = 500): a: cement paste; b: composite prepared with raw material; c: composite prepared with enzymatic residues pretreated with aqueous ammonia prior to saccharification (NER); d: composite prepared with enzymatic residues pretreated with acid prior to saccharification (AER).
The flexural strength for both composites manufactured with lightweight aggregates did not dramatically change, in comparison with cement paste (Fig. 7a). The compressive strength of composites containing by-products decreased however by 85% in comparison with cement paste and by 62% in comparison with raw material-based composites (Fig. 7b). The lignocellulosic treatment, which includes acid or ammonia treatment followed by saccharification, might have caused the drop in the mechanical strength of by-products [42]. Though several factors might be involved in this loss of mechanical strength, the decrease in composite bulk density would mainly be responsible for such behavior. The artificial air pores observed in the matrix can thus explain the decrease in density reduction. The formation of macropores has consistently been found as a cause of significant strength decreases [43]. An abnormal development of the silicate species (C-S-H) is another potential cause since these species are responsible for ensuring the good mechanical strength of concretes.
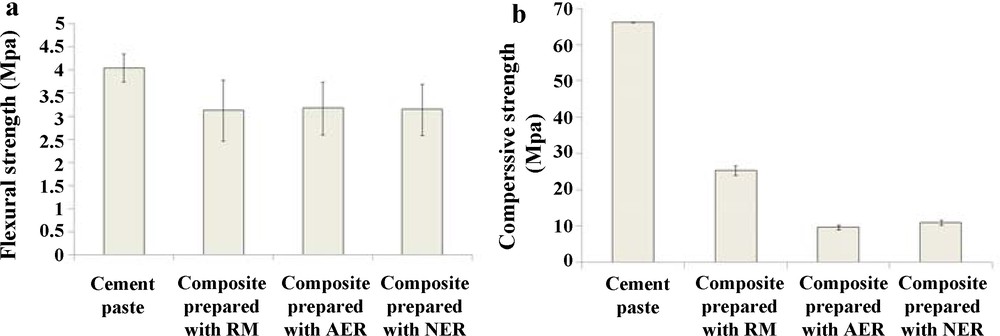
Mechanical properties of the cement pastes and composites; a: flexural strength; b: compressive strength (RM: raw material; AER: enzymatic residues pretreated with acid prior to saccharification; NER: enzymatic residues pretreated with ammonia aqueous prior to saccharification).
Nevertheless, the observed decrease in mechanical strength of composite concretes, i.e. containing 5% miscanthus by-products, would not be due to defective adhesion between matrix and aggregate. No gap zone was observed between cement and lignocellulosic by-products within the composite (Fig. 8). This good adhesion observed between matrix and aggregates resulted from previous aggregate saturation, which served the purpose of avoiding water competition between aggregates and matrix.
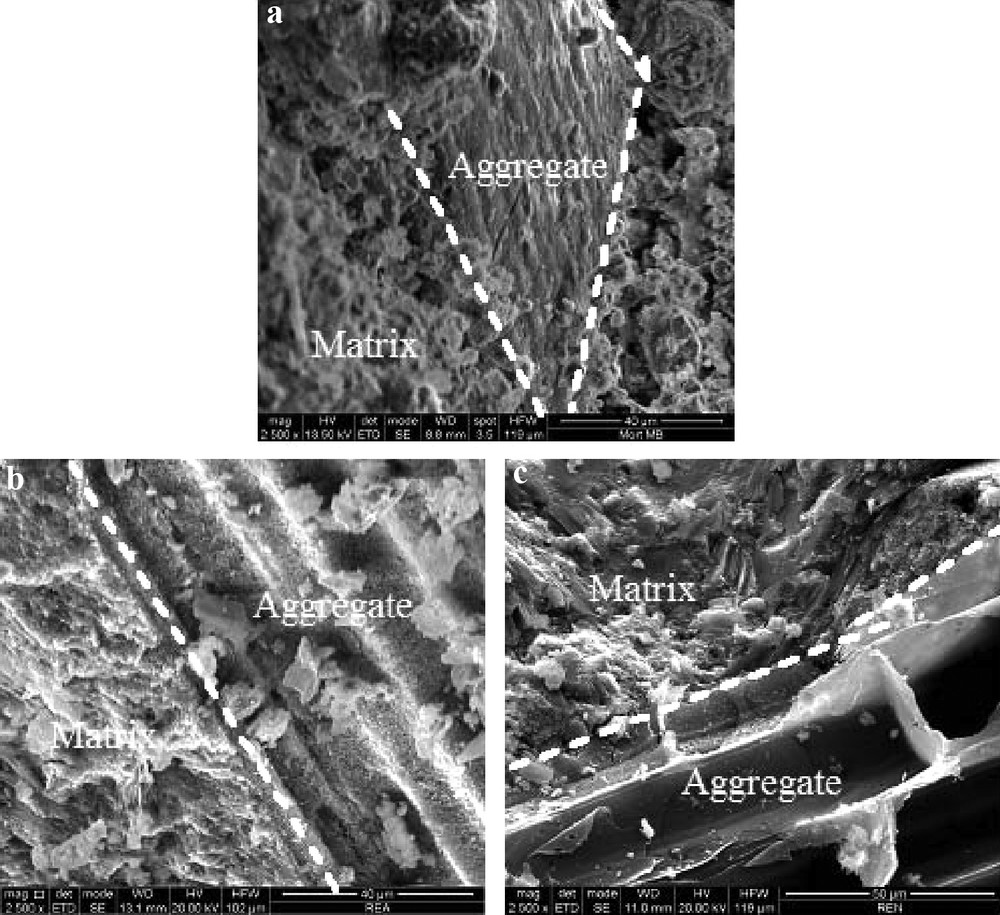
Scanning electron micrographs of adhesion between matrix and aggregate (magnification = 2500); a: composite prepared with raw material; b: composite prepared with enzymatic residues pretreated with aqueous ammonia prior to saccharification (NER); c: composite prepared with enzymatic residues pretreated with acid prior to saccharification (AER).
These mechanical strength values remain comparable however with other lignocellulosic cementitious composites and even better than the strength of reported materials [16].
4 Conclusion
In this study, lightweight building materials have been produced through the introduction of lightweight aggregates: two saccharification by-products have been used herein. Even though the treatments (pretreatments and saccharification) made it possible to decrease the quantity of soluble compounds, results indicate that the use of these by-products delays the setting time and decreases the mechanical properties of composites. Modifications to C-S-H crystal development have also been observed.
The additional time required from the beginning of setting is excessive. Neither pretreatment nor saccharification is a process that enables eliminating the inhibitory compounds of mortar setting. A by-product or matrix treatment would always be necessary like for other lignocelluloses-based cementitious materials. Preliminary attempts at using a setting accelerator (calcium chloride) in the cementitious matrix have yielded interesting results [41].
Disclosure of interest
The authors declare that they have no conflicts of interest concerning this article.
Acknowledgements
The authors wish N. Montrelay for technical assistance, and S. Cadoux and M. Preudhomme (INRA Agro-Impact) for field experiment management and for providing the plant material. The thesis was financially supported by the Region Picardie (MISQUAL project AAP07-52). We are also grateful to Novozymes France for providing cellulase and glucosidase.