1 Introduction
Many oil/water (o/w) microemulsions employ cosurfactants, electrolytes and other additives in their formulations [1]. Hence, many microemulsion polymerizations have been done with formulations containing alcohols – the most common cosurfactant [2–10]. However, the role of alcohols has not been systematically examined in this kind of polymerization, despite the fact that their presence complicates the basic understanding of the mechanism of microemulsion polymerization because (i) they partition among the different domains of the microemulsion, (ii) they modify the partitioning of the monomer and (iii) they may act as chain transfer agents [11]. In fact, for the modeling of the polymerization of styrene in microemulsions containing sodium dodecylsulfate and an alcohol, Guo et al. introduced several assumptions about the partitioning and added thermodynamic equations to satisfy equilibrium considerations due to the presence of the alcohol [4,5].
Gan et al. investigated the polymerization of styrene in microemulsions stabilized with dodecyltrimethylammonium bromide (DTAB) and several ethoxylated alcohols and reported that the polymerization rates and the polystyrene molar masses were affected by the molar ratio of alcohol to surfactant in the dispersed phase and by the type of alcohol [7]. They concluded that the differences in molar masses may not be due to differences in the chain-transfer constant of the alcohols but to changes in the interfacial fluidity of the particles induced by the alcohols. However, these authors did not compare their results with alcohol-free microemulsion systems. Chern and Liu studied the polymerization of styrene in microemulsions stabilized with SDS and short-chain alcohols [10]. Although no kinetic data were presented, they noticed that the molar masses were larger than those reported in the alcohol-free microemulsion polymerization [12] and that the behavior of the n-butanol system was different from those of the n-pentanol and n-hexanol systems. Recently, we reported the polymerization of vinyl acetate in o/w microemulsions stabilized with Aerosol OT with or without n-butanol as a cosurfactant [13]. Contrary to the results of Gan et al. [7], we found that molar masses decrease with increasing molar alcohol-to-monomer ratio and demonstrated that the alcohol is acting as a chain-transfer agent [13]. Also, recent results still unpublished indicate that the polymerization rate of vinyl acetate decreases as the alcohol-to-AOT ratio increases or as the solubility of the alcohol in water increases for a constant alcohol-to-AOT ratio [14].
In this paper, we examine the polymerization of styrene in o/w microemulsions stabilized with the cationic surfactants DTAB or DTAC and n-butyl, n-hexyl or n-octyl alcohol as cosurfactant initiated with a cationic initiator, V-50, at 60 °C. The kinetics of polymerization, the particle-size evolution and the molar masses are compared with those obtained from the cosurfactant-free microemulsion polymerization of this monomer.
2 Experimental section
Dodecyltrimethylammonium bromide (DTAB) and chloride (DTAC) were 99% pure from Tokyo Kasei. DTAB was further purified by re-crystallization from a 50:50 (v/v) acetone/ethanol mixture. Reagent grade styrene (Scientific Polymer Products) was passed four to five times through a DTR-7 column (SPP) to remove the inhibitor. The alcohols were 99.5% pure from Aldrich. Hydroquinone (99% pure from Aldrich) was used as received. 2,2′-azobis(2-amidinopropane) dihydrochloride (V-50) from Wako Chemicals was re-crystallized from methanol. HPLC grade tetrahydrofurane (Merck) was used as the mobile phase for molar masses determinations. Doubly distilled water was employed.
The one-phase o/w microemulsion region was determined visually by the change from transparent to turbid of aqueous solutions of DTAB or DTAB/cosurfactant (5:1 by weight) that were titrated with styrene (containing inhibitor to avoid polymerization) in a thermostated water bath at 60 °C. To determine more precisely the phase boundaries, samples with compositions slightly below and above the visually determined phase boundaries were made by weight and allowed to reach equilibrium in a water bath at 60 °C. Clear samples that did not exhibit static or streaming birefringence when examined through cross polarizers, were considered as one-phase microemulsions. The phase diagram at high DTAB concentrations was not determined because it is not relevant for the present study.
Reactions were carried out at 60 °C in a 100-ml glass reactor. The reaction vessel was loaded with the microemulsion and heated to 60 °C, sparged with argon, and maintained at this temperature for 30 min, before adding an aqueous solution of initiator to give an overall V-50-to-styrene mass ratio (mV-40/mST) of 0.01. During the reaction, the reacting mixture was continuously stirred and sparged with argon. Samples were withdrawn at different times during the reaction and quenched with an aqueous solution of hydroquinone and cooling in an ice bath. Polystyrene was isolated by filtration after precipitation with excess methanol. Conversion was estimated by gravimetry.
Particle size was measured at 25 °C and an angle of 90° in a Malvern 4700 quasi-elastic light-scattering (QLS) apparatus equipped with an argon laser (λ = 488 nm). Intensity correlation data were analyzed by the method of cumulants to provide the average decay rate, <Γ2> (= q2 D), where q = [(4 π n/λ) sin(θ/2)] is the scattering vector, n the index of refraction and D the diffusion coefficient. The measured diffusion coefficients were represented in terms of apparent diameters (Dz) by means of the Stokes law, assuming that the solvent has the same viscosity as water. Latexes were diluted up to 100 times and filtered through 0.2-μm Millipore filters before QLS measurements to minimize particle–particle interactions and to remove dust particles.
Average molar masses and molar mass distributions were measured with a PerkinElmer LC 30 size-exclusion chromatograph, previously calibrated with narrow molar masses polystyrene standards (Polymer Laboratories), equipped with a LC30 refractive index detector and a Dawn multi-angle light scattering detector from Wyatt Technology. Columns with molar masses range from 105 to 107 g mol–1 were used.
3 Results
Fig. 1 depicts the one-phase o/w microemulsion regions for the alcohol-free system and for the alcohol/DTAB mixtures (1:5 weight ratio). The one-phase region increases slightly with the addition of n-butanol. The microemulsions stabilized with n-hexanol contain more styrene at low surfactant/alcohol overall concentrations than the alcohol-free microemulsion; however, the one-phase region does not extend as far as in the alcohol-free system (Fig. 1). The addition of n-octanol, in turn, allows the maximum solubilization of styrene, but the one-phase region shrinks. Fig. 1 also indicates that at low DTAB concentrations, the n-octanol/DTAB/water system can solubilize more styrene than the other two ones. The dotted lines in Fig. 1 are approximate phase boundaries, since we were not interested in such high surfactant/alcohol concentrations. Also, because these alcohols are partially soluble in water, they allow the solubilization of additional styrene in water. Fig. 2 shows the UV spectra of styrene in water and in water saturated with the alcohols. Clearly, the concentration of styrene in water increases with the presence of the alcohol in the order: n-octanol < n-hexanol < n-butanol.
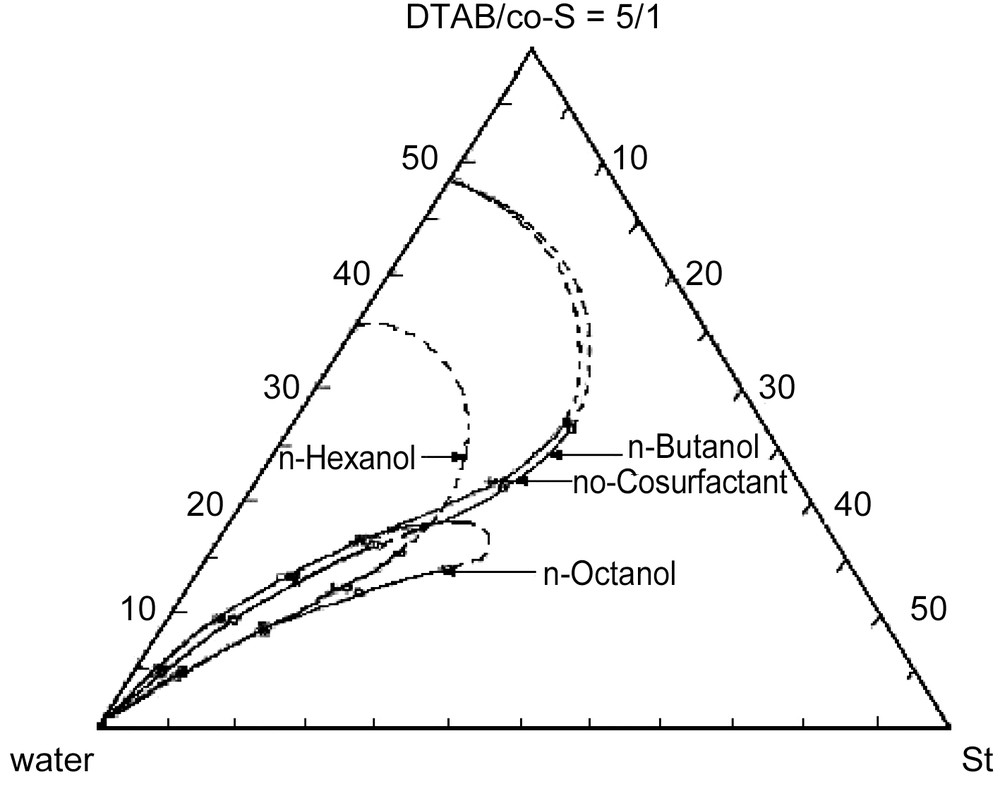
Phase diagram of water, styrene and DTAB/alcohol (5:1 weight ratio) at 60 °C.
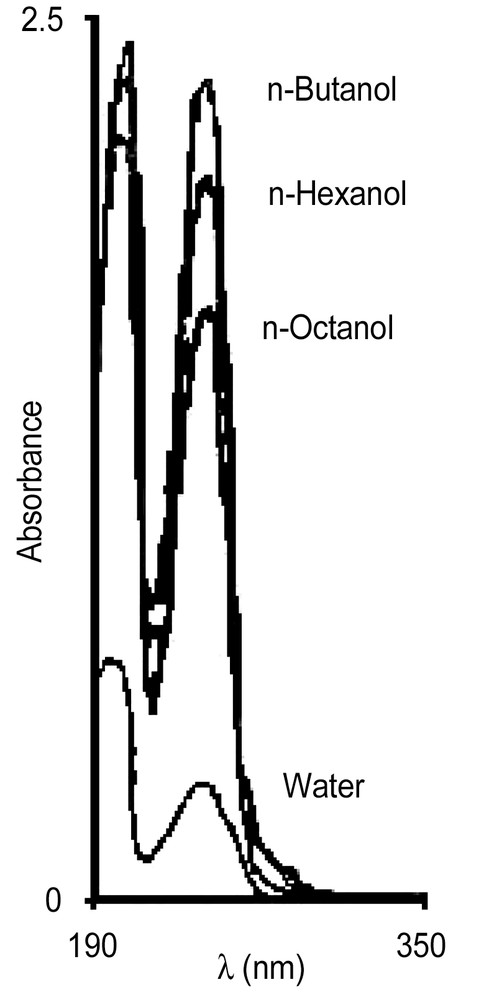
UV spectra of styrene in water and in aqueous solutions of n-butanol, n-hexanol or n-octanol.
Fig. 3 depicts conversion as a function of time for the polymerization of styrene in a microemulsion stabilized with DTAB or with mixtures of DTAB/n-butanol of different weight ratios. Conversions after 90 min diminish with increasing the alcohol content. Clearly, the reaction rate slows down in the presence of n-butanol and conversion decreases with increasing alcohol concentration. The reaction rates, obtained by fitting the conversion-versus-time data to a polynomial and differentiation, exhibit two intervals (Fig. 4 ), which is typical of microemulsion polymerization [15,16]. Notice that the maximum in reaction rate shifts to lower conversion in the systems containing n-butanol (Fig. 4).
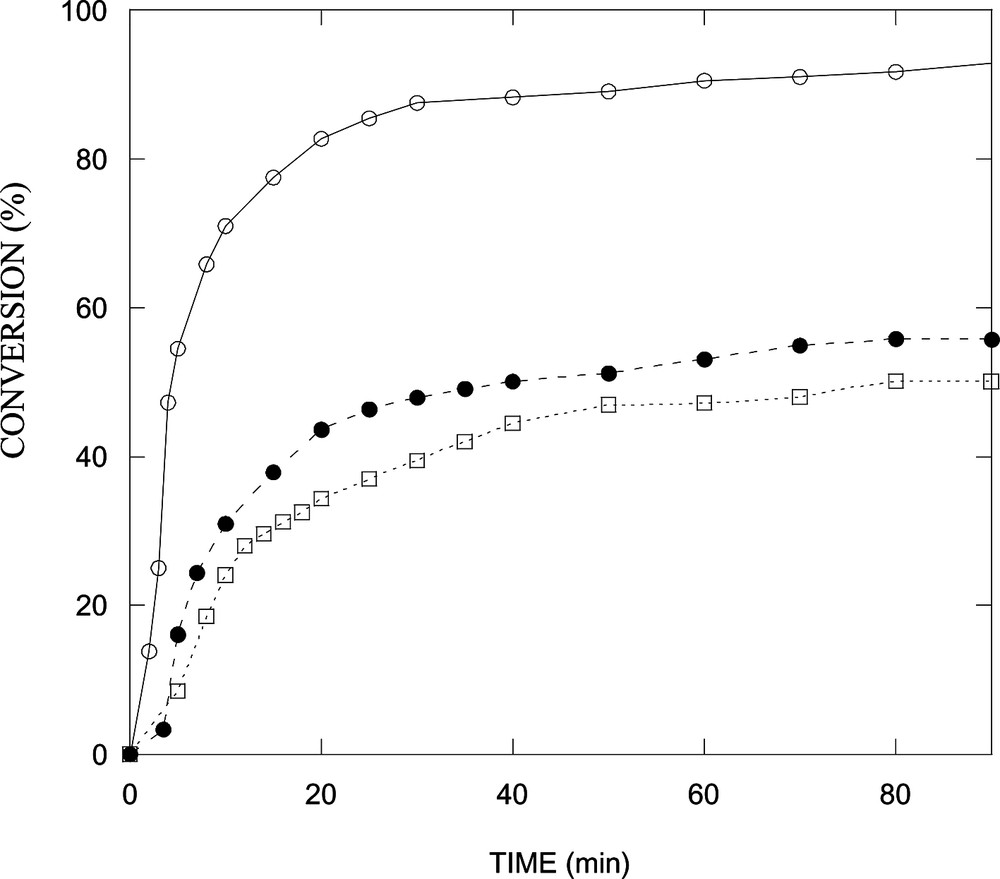
Conversion as a function of time for the polymerization at 60 °C of styrene in microemulsion stabilized with DTAB and n-butanol: (○) 6 wt% ST, 14.1 wt% DTAB and 79.9 wt% H2O; (•) 6 wt% ST, 11.75 wt% DTAB, 2.35 wt% n-butanol and 79.9 wt% H2O; (□) 6 wt% ST, 11.28 wt% DTAB, 2.82 wt% n-butanol and 79.9 wt% H2O.
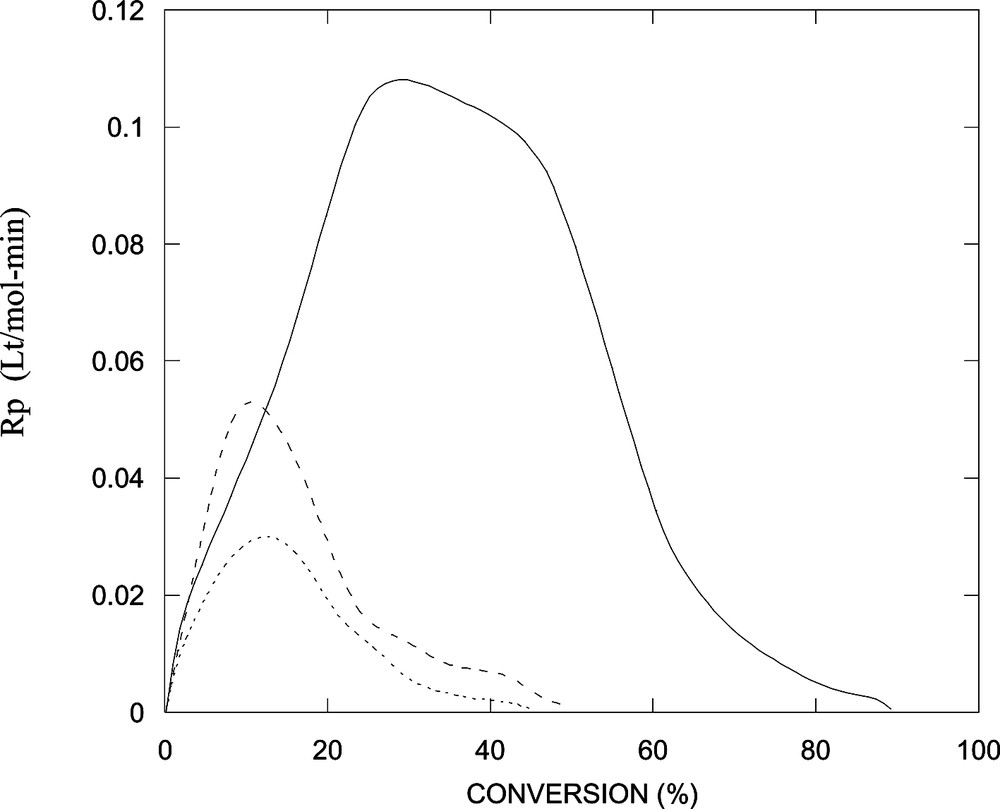
Reaction rate as a function of conversion for data shown in Fig. 3.
Fig. 5 shows conversions versus time for the polymerization at 60 °C of styrene in the alcohol-free microemulsion and in the microemulsions stabilized with alcohol/DTAB weight ratios of 1:5. Again, conversions and reaction rates fall with the addition of the alcohol. The reaction rate decreases with the alcohol in the order n-butanol < n-hexanol < n-octanol (Fig. 6 ). The maximum in the reaction rate also shifts to lower conversions with the addition of the alcohol (Fig. 6).

Conversion as a function of time for the polymerization at 60 °C of styrene in microemulsion stabilized with DTAB/alcohol (5:1 w/w): (•) no cosurfactant; (□) n-octanol; (♦) n-hexanol; (○) n-butanol. Microemulsion recipe: DTAB-cosurfactant/water = 15/85 and 6 wt% styrene.

Reaction rate as a function of conversion for data shown in Fig. 5.
Average molar masses and particle size at the end of the polymerization are reported in Table 1 for the DTAB/n-butanol system as a function of alcohol concentration. Particle size practically does not change during the reaction for these systems (data not shown). The particles at the end of the reaction are slightly larger in the presence of n-butanol compared to those in the alcohol-free system. Also, molar masses are larger for the reactions carried on with n-butanol.
Average molar masses and final particle sizes for the polymerization of styrene in microemulsions stabilized with DTAB/n-butanol
Cn-butanol (wt.%) | Mw × 10–6 (Dalton) | Mn × 10–6 (Dalton) | Dp (nm) |
0.0 | 2.2 | 1.2 | 17 |
2.35 | 3.2 | 1.4 | 20 |
2.82 | 2.9 | 1.8 | 21 |
3.53 | 2.8 | 1.6 | 19 |
Table 2 shows average molar masses and final particle size for the polymerizations in microemulsions containing the various alcohols. Again, final particle size and average molar masses are slightly larger for the reactions carried out in the presence of the alcohols.
Average molar masses and final particle sizes for the polymerization of styrene in microemulsions stabilized with DTAB/alcohol (5:1 by weight)
Cosurfactant | Mw × 10–6 (Dalton) | Mn × 10–6 (Dalton) | Dp (nm) |
None | 2.2 | 1.2 | 17 |
n-Butanol | 3.2 | 1.4 | 20 |
n-Hexanol | 3.1 | 1.4 | 20 |
n-Octanol | 3.5 | 1.4 | 19.0 |
4 Discussion and conclusions
Alcohols are often employed in microemulsions stabilized with ionic surfactants because they screen the electrostatic repulsions of the charged polar heads of the surfactant molecules at the interface, giving as a result larger curvatures and higher oil solubilization [17–19]. In fact, addition of n-butanol or n-hexanol yields larger one-phase microemulsion regions (for overall surfactant concentrations smaller than 20 wt%) compared to that in the alcohol-free system (Fig. 1). However, n-octanol, which is insoluble in water, requires the addition of styrene to induce micelle formation and growth to produce a narrow one-phase microemulsion region (Fig. 1).
The polymerization of styrene in these microemulsions is fast. The initially transparent microemulsions become increasingly bluish as the reaction proceeds, because particle growth and the increasingly larger refractive index difference between the dispersing medium and the reacting particles. However, the addition of an alcohol slows down the reactions (Figs. 3–6) and this effect becomes more severe as the concentration of alcohol is increased (Fig. 4). Several possible explanations are forwarded next.
Alcohols screen the electrostatic interactions among the charged surfactant molecules at the interface, giving as a result droplet growth [17–19]. Because the styrene content is the same in the formulation used here, the alcoholic microemulsions should have bigger droplets but in a smaller number density; as a result, a smaller number of initiated particles for a fixed free-radical flux (since the initiator concentration and the temperature are identical in all the reactions) and slower reactions rates (and possibly larger molar masses, as discussed below) should be expected. Moreover, the addition of the alcohol may decrease the reaction rate because some of the radicals, before entering the particles or the microemulsion droplets, can react in the aqueous phase with alcohol molecules, which act as chain transfer agents, giving as a result more stable radicals that do not continue monomer polymerization. The greater the amount of alcohol, the larger the numbers of radicals that are inhibited, yielding as a result slower reaction rates and lower conversions (Fig. 4). As the length of the alcohol decreases, the reaction rate also decreases, because the alcohol is more water-soluble and the radicals in the aqueous phase have more probability for reaction with alcohol molecules there (Fig. 6). Also, because the same concentration by weight of alcohol-to-DTAB was used, increasing the chain length, the alcohol molar concentration diminishes (0.83, 0.6 and 0.47 for n-butanol, n-hexanol and n-octanol, respectively), which can also explain in part the increase in the reaction rate for the longer alcohols (Fig. 6).
Another factor that contributes to the slowing down of the reactions is the free-radical quenching power of the bromine ion [20]. Addition of alcohol to ionic surfactant solutions decreases the c.m.c. and increases the degree of ionization, α [21–25]. In general, α increases with increasing alcohol concentrations in micellar systems of cationic surfactants [21–25]. Hence, we suggest that the concentration of bromide ions in the continuous phase increases upon addition of alcohols, producing, as a result, a lower efficiency of the positive-charged free radicals of V-50, due to transfer to the bromide ions. The overall result should be slower reaction rates, as shown in Figs. 4 and 6. That the reaction rate is faster with n-octanol and decreases in the order n-hexanol, n-butanol, may be due to the different molar concentrations of alcohol (0.83, 0.6 and 0.47 for n-butanol, n-hexanol and n-octanol, respectively), since the same DTAB/alcohol weight ratios and no molar ratios were used.
To prove conclusively this hypothesis, polymerization reactions were carried out in microemulsions stabilized with DTAC and with DTAC/alcohol (Fig. 7 ). Larger conversions and faster reaction rates are obtained with DTAC and with DTAC/alcohols systems. Notice that the reaction rates are similar, regardless of the absence or presence of the alcohols. The transfer reaction rate constant between bromide ion and the free radicals of V-50 has not been reported. However, for the reaction with SO42–• and the bromide ion, a value of ktr of 3.5 × 109 l mol–1 s–1 has been documented, whereas a value of 2 × 108 l mol–1 s–1 has been reported for the reaction with the chloride ion [20]. Hence, reaction rates should be less affected by an increase in the chloride concentration in the aqueous phase caused by the addition of alcohol compared to reaction in the DTAB/alcohol systems (cf. Figs. 5 and 7).

Conversion as a function of time for the polymerization at 60 °C of styrene in microemulsion stabilized with DTAC/alcohol (5:1 w/w): (•) no cosurfactant; (Δ) n-octanol; (○) n-hexanol; (◊) n-butanol.
The presence of the cosurfactant produced only a small increase in the final particle size (Tables 1 and 2). Likewise, Gan et al. did not observe a particular trend on particle size in the polymerization of styrene in microemulsions stabilized with DTAB and several ethoxylated alcohols [7]. However, higher molar masses, especially weight-average molar masses, were obtained from the polymerization of the alcoholic microemulsions, despite the fact that in mass polymerization – as in some microemulsion polymerizations [13] – alcohols decrease polymer molar masses by a chain-transfer mechanism [26]. Gan et al. attributed this effect to differences in the interfacial fluidity of the microemulsions and not to chain-transfer reactions [7]. Here, however, number-average molar masses are similar for the polymerization with the different alcohols (Table 2). In fact, the chain-transfer constant of alcohol changes very little with increasing the chain length of the alcohol [27]. Moreover, Fig. 8 demonstrates that the termination mechanism is the same for the different alcohols inasmuch as the plots of the logarithm of the number molar mass distribution, P(M), versus the molar mass, M, decay with the same slope, regardless of the type of alcohol [28].
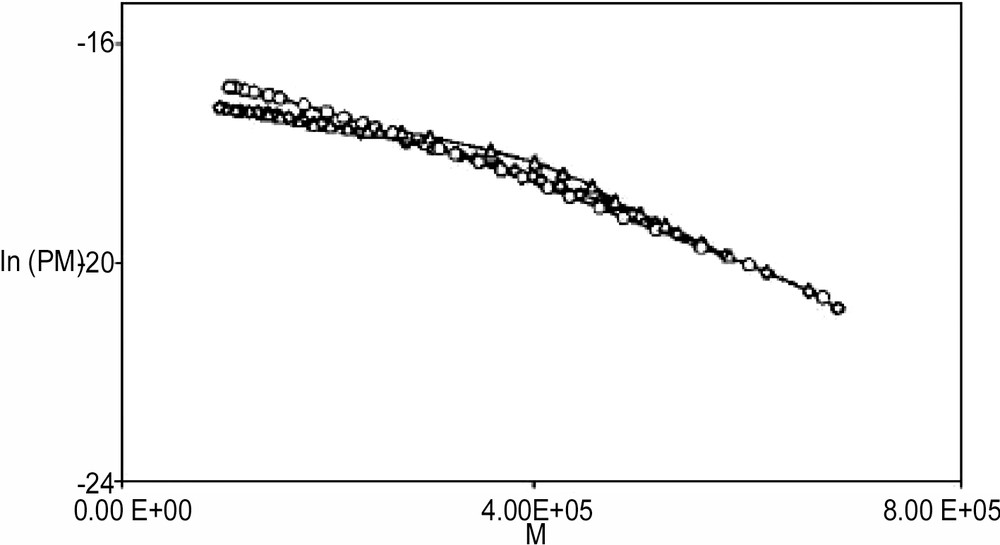
Logarithm of the number molar mass distribution, P(M), versus molar mass, M, at the end of the polymerization of styrene in microemulsions stabilized with DTAB/alcohol (5:1 weight ratio): (♢) n-butanol; (○) n-hexanol; (Δ) n-octanol.
Alcohols are non-solvents for polystyrene and also increase the concentration of styrene in the aqueous phase (Fig. 2). Hence, alcohols should diminish the equilibrium monomer concentration in the particles. As a consequence, the ratio of monomer to polymer should be smaller in the polymerizations carried out with alcohol compared to those in alcohol-free systems, which should increase the possibility of chain transfer reactions to polymer compared to chain transfer to monomer. This explains the larger weight-average molecular weight obtained in the reactions with alcohol (Tables 1 and 2).
In summary, we have reported the polymerization of styrene in o/w microemulsions stabilized with DTAB or DTAC and different alcohols. The addition of the alcohol produces important changes in the kinetics and characteristics of the polystyrene produced.
Acknowledgements
This work was supported by the National Council of Science and Technology of Mexico (CONACyT) through grant # G38725-U.