1 Introduction
The United Nations Conference on Environment and Development, held in Rio de Janeiro in 1992, provided the fundamental principles – the Rio Declaration – and the program of action – the Agenda 21 – for achieving sustainable development [1]. Sustainable chemistry is understood as the contribution of chemistry to the implementation of the Rio Declaration and Agenda 21, including its on-going advancements, such as the Johannesburg Declaration of the World Summit of Sustainable Development that was held last year [2].
Principle 1 of the Rio Declaration proclaims: “Human beings are at the centre of concerns for sustainable development. They are entitled to a healthy and productive life in harmony with nature.”
There are currently about 6 billion people on this planet – 1 billion of these in the industrialized countries – and this number will rise to about 9 billion in the year 2050. The population growth will unfold nearly exclusively in the developing countries of today, namely in Africa, Asia, and Latin America, thus causing a change in the ratio of the population in the developing countries to that in the industrial countries from 4:1 today to 7:1 [3] (Fig. 1).
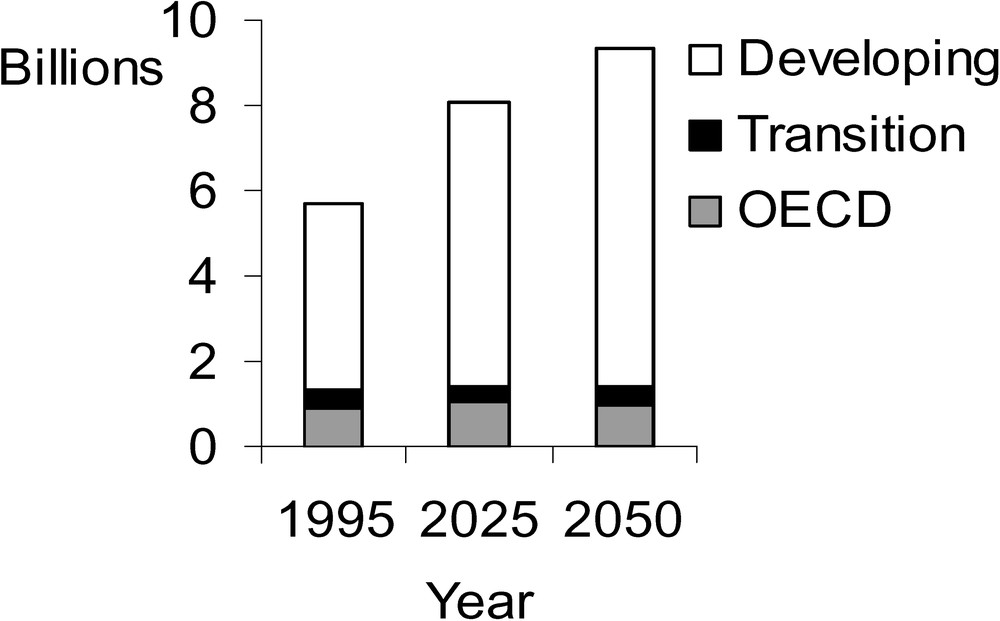
Development of global population 1995–2050 [3].
The standard of living in the developing countries needs to grow and needs to adapt more and more to the one in the industrialized countries, where it should not drop, if Principle 3 of the Rio Declaration is to be met: “The right to development must be fulfilled so as to equitably meet developmental and environmental needs of present and future generations”, and Principle 5: “All states and all people shall cooperate in the essential task of eradicating poverty as an indispensable requirement for sustainable development, in order to decrease the disparities in standards of living and better meet the needs of the majority of the people of the world.”
However, as can be derived from the projections of world energy consumption up to the year 2025, one cannot observe any tendency to decrease disparities; in contrast, disparities are further increasing (Fig. 2). Obviously, there will be an enormous problem [4].
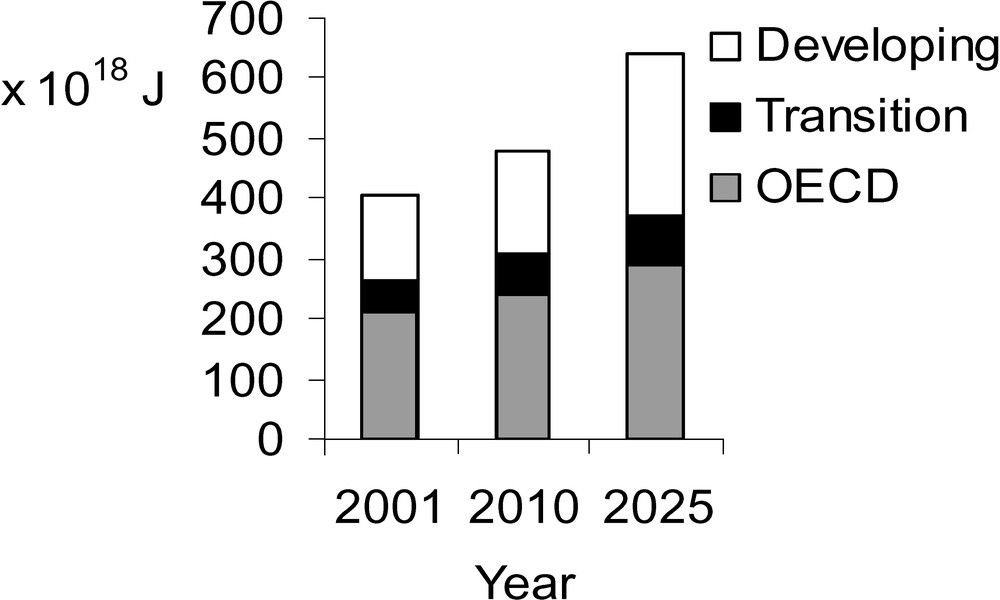
Global Energy Consumption 2001–2025.
Nevertheless, in addition to the demand for food, the demand for other goods will grow substantially. The demand for goods will more than double, and with an increasing adaptation of the standard of living, it will soon grow by a factor of four and more. Resources will have to be used much more efficiently than today, that is, multiple goods will have to be produced with the same or even a lower quantity of resources. Therefore, measures have to be intensified to lower the use of resources per unit of usage significantly. A lowering by a factor of four will not be sufficient, since the existing fossil resources will be increasingly difficult to access [5,6]. Therefore, it has to be assumed that the oil production will already have passed its maximum in this decade, at the latest by 2015–2020, and will then slowly decrease. The global oil reserves were estimated at the end of 2001 to last for 40.3 yr [7].
The increase in the efficiency of resource usage refers to Principle 8 of the Rio Declaration: “To achieve sustainable development and a higher quality of life for all people, States should reduce and eliminate unsustainable patterns of production and consumption and promote appropriate demographic policies”, whereby, as a further essential issue, the protection of the environment addressed in Principle 4 has to be considered: “In order to achieve sustainable development, environmental protection shall constitute an integral part of the development process and cannot be considered in isolation from it.”
The Principles of the Rio conference were specified in Agenda 21, the comprehensive plan of action for the 21st century that was adopted by more than 170 governments in Rio [1]. Agenda 21 “addresses the pressing problems of today and also aims at preparing the world for the challenges of the next century” (Chapter 1.3). The “conservation and management of resources for development” are the main focus of interest. The sciences have to make a considerable contribution if the aim is to be achieved. “There is a need for the sciences constantly to reassess and promote less intensive trends in resource utilization. [...] Thus, the sciences are increasingly being understood as an essential component in the search for feasible pathways towards sustainable development” (Agenda 21, Chapter 35.2) “and chemists must lead in developing the technological dimension of a sustainable civilization” [8].
Strengthening the role of major social groups is outlined, such as the role of business and industry: “The improvement of production systems through technologies and processes that utilize resources more efficiently and at the same time produce less wastes – achieving more with less – is an important pathway towards sustainability for business and industry. Similarly, facilitating and encouraging inventiveness, competitiveness and voluntary initiatives are necessary for stimulating more varied, efficient and effective options.” The ‘World Summit on Sustainable Development’, held in 2002 in Johannesburg, strongly reaffirmed the commitment to the Rio principles, the full implementation of Agenda 21 and the Programme for the further implementation of Agenda 21 [1].
During the last ten years, some essential aspects of the Rio Declaration and Agenda 21 have been tackled. The safety of chemicals, which is addressed in the separate chapter 19 of Agenda 21, has been improved significantly by international agreements [9], to which the worldwide voluntary initiative "Responsible Care" of the chemical industry contributes considerably [10], which is acknowledged in Chapter 30.10 of Agenda 21. In their future programs, the chemical industries of Europe [11], Japan [12], and USA [13,14] have explicitly accepted the contribution of chemistry to a sustainable development. In general, it must be said that the chemical societies, chemical institutions and also chemical companies are attempting to understand the implications of sustainable development for themselves [15].
Chemistry can make important contributions to the conservation of resources by development of:
- • more effective and environmentally more benign chemical processes;
- • chemical products that are based on renewable resources;
- • chemical products that are environmentally more benign, and enhance the efficiency of production processes and products in other areas significantly;
- • products that allow the consumer to use resources more efficiently;
- • a product design that fits into a recycling concept.
This contribution will focus on the first three topics centred on renewable resources.
2 More effective and environmentally benign chemical processes
The energy and environmental profile of the chemical industry in the USA has been investigated and described recently in detail [16,17]. In 1997, the chemical industry used 6.65 EJ (Exa = 1018) of energy, which represents about 7% of all US energy used and 25% of the energy consumed in all manufacturing processes (Fig. 3a). Remarkably, that amounts to about 1.8% of global energy consumption. Energy consumption and carbon dioxide release are closely connected. Approximately 51% of the total was used as feedstock for chemical products, which is the non-energetic consumption, and 49% as process energy for carrying out the processes, that is the energetic consumption. The main energy consumption at 2.640 EJ is invested in the production of the organic base chemicals (Fig. 3b). Similar data are valid for most industrialized countries, whereas there may be some interesting differences in detail.
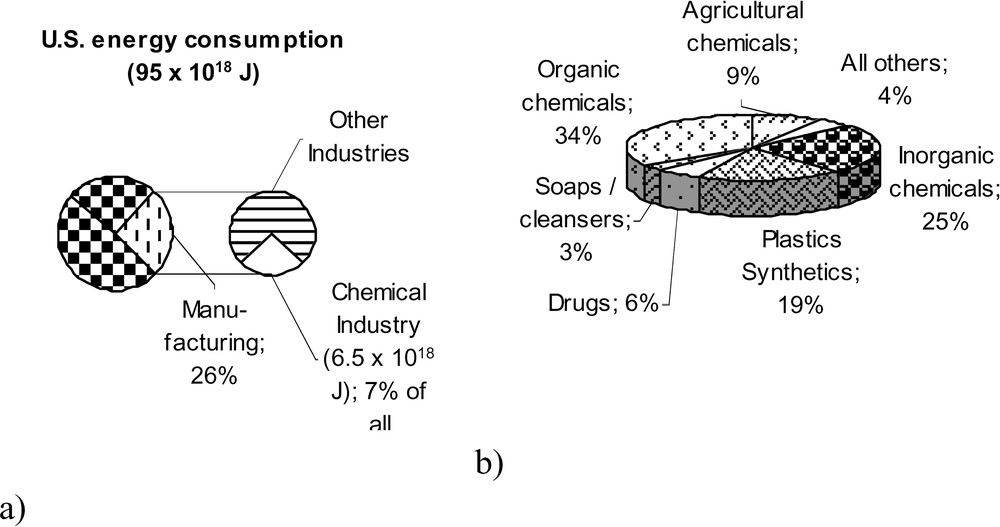
Energy consumption of the US chemical industry (a) as part of the manufacturing and total US energy consumption; (b) distribution of gross energy requirements (GER) by product groups [16,17].
Since base chemicals – namely chemicals that are each produced worldwide in more than a million tons per annum (t/a) – are produced in large quantities, and important product lines are synthesized from them. Their resource-saving and environmentally benign production is hence especially important for sustainable development. An investigation of the most important value-adding chains based on ethylene, propylene, BTX (benzene, toluene, xylene), and butadiene has shown an estimated potential energy saving of approximately 30% of the process energy.
Agenda 21 pointed out – interestingly in chapter 4 Changing consumption patterns: “Reducing the amount of energy and materials used per unit in the production of goods and services can contribute both to the alleviation of environmental stress and to greater economic and industrial productivity and competitiveness.”
Analysis of the production output of the US chemical industry from 1974 - 1997 shows, however, that the energy consumption per unit of emission declined by more than 39% between 1974 to 1988, but that since then it has stagnated, while the total energy consumption from 1974 to 1997 has risen, as a result of the continuous growth of the chemical production, by 80% [16,17]. This leads us to the conclusion that the relatively low-cost, high-return energy investments have already been undertaken. Further gain will require more dramatic changes in process design and in innovative solutions yet to be provided by research and development. If the intention of the US Vision 2020 program can be realized to reduce the energy consumption of the chemical industry related to the end of the 20th century by 30% per product unit by the year 2020, this will be an important contribution to sustainable development [13,14]. However, this will not be sufficient, since the total energy consumption of the chemical industry will remain constant or even increase as a result of the further increase in production.
It is important to consider the gross energy requirements (GER) of important base chemicals [18,19] (Fig. 4). GER indicate the total primary energy consumption of the entire process chain to manufacture a chemical product. The GER include energetic consumption, which in chemical processes is largely the process energy, and non-energetic consumption, namely the direct, material use of fossil energy sources, such as crude oil.
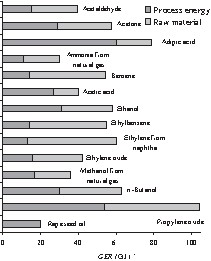
Gross energy requirements (GER) for important base chemicals [18,19].
For example, this is approximately 40 GJ/t for acetaldehyde, 80 GJ/t adipic acid and actually 104 GJ/t for propylene oxide. The GER, in relation to the process energy and the chemical energy accumulated in the product, is a useful measurement for the assessment of bulk products. Rapeseed oil, as an example of a renewable feedstock, is especially remarkable because of the lowest GER of all base chemicals. Here, the differences in the resource consumption are so significant that it can be assumed that products based on vegetable oils could clearly be more environmentally benign than petrochemical products, and its steadily increasing usage should be an important contribution to a sustainable development.
Propylene oxide is the base chemical that has the highest GER and is one of the top 50 chemicals. Approximately 4 million t/a are produced worldwide.
Industrial processes used are:
- • the chlorohydrin process;
- • oxirane processes with isobutane or ethylbenzene [20].
There is no difference in gross energy requirement between the chlorohydrin and the oxirane process [18,19]. Both are indirect processes and the first one in particular is extremely polluting. The oxirane process is a rather more indirect process for the synthesis of tert-butyl alcohol and styrene; economically, it can only be done if these coupled products are sold. At present, this seems to be the case with styrene [21], but this is no longer the case with tert-butyl alcohol, since tert-butyl methyl ether will no longer be used as an additive to gasoline [22]. However, since additional process steps are required, a compulsory formation of coupled products is always less advantageous than a direct process. During the last few years, the epoxidation of propylene with titanium silicalite (TS-1)/hydrogen peroxide (yield > 90%) has been developed [23]. This process requires hydrogen peroxide, which is both a more reactive and a more expensive surrogate for oxygen. Quite recently, it has been shown that carbon dioxide is an excellent solvent for the formation of propylene oxide from hydrogen, oxygen, and propene over a Pd/TS-1 catalyst [24].
A new investment cycle is going on for the existing propylene oxide plants at the beginning of the new millennium. Most of the chlorohydrin plants will be closed down. New plants using the oxirane procedure with styrene as coupled product are being built in the USA as well as in Europe and Asia. A Sumitomo Chemical propylene oxide plant that is set to open in Japan in 2003 is based on the use of cumene in the oxirane process. The dimethylbenzyl alcohol coproduct will be dehydrated and hydrogenated back to cumene [25]. Degussa and Krupp, however, have developed a large-scale catalytic oxidation of propylene with hydrogen peroxide [26], and BASF and Solvay expect to start building a 250 000 metric-ton propylene oxide plant based on hydrogen peroxide [27].
It has finally become very clear that the direct oxidation of propylene or, even better, of propane with oxygen from the air has to be developed for the next investment cycle [2].
Caprolactam (world capacity approximately 4.4 × 106 t/a) and adipic acid (world production approximately 2.3 × 106 t/a in 1995) are other important base chemicals produced by oxidation that have a high demand in resources and whose synthetic process should be improved to be resource-saving and environmentally more benign [2].
Additionally, substitutes for products derived from base chemicals such as propylene oxide, caprolactam, and adipic acid have to be developed.
3 Renewable feedstocks for the chemical industry
Propylene oxide is a reactive base chemical that is transformed to polyetherpolyoles (65–70%) for polyurethanes and to propylene glycol (22%) for polyesters. Obviously, the functionality is used to produce polyurethanes with a diamino compound via isocyanate, and polyesters with a diacid. These functionalities are available from renewable feedstocks [28,29]: carbohydrates [30,31,32], oils and fats [33], proteins and lignins [34]. It should be possible to develop alternatives to products based on propylene oxide based on renewables to make substitution processes feasible. Related considerations can be made for adipic acid, ε-caprolactam and for other oxidized base chemicals. This is an important and great challenge in basic and applied research for chemists and chemical engineers.
The encouragement of environmentally sound renewable natural resources and their sustainable use is an important aim of Agenda 21. The biomass cycle shows the advantages of renewable resources [35] (Fig. 5). Photosynthesis produces biomass, which delivers renewable feedstocks such as vegetable oil, starch and others. These are processed to give the renewable base chemicals such as fatty acids, glycerol, glucose etc. Further processing results in useful products that can be biologically degraded after utilization to give again carbon dioxide and water. This is the ideal type of biomass cycle producing no additional carbon dioxide. Of course, some process energy is necessary. However, the chemical energy accumulated in the product comes completely from the sun.

Biomass cycle.
Most importantly, when renewables are used as base chemicals for organic synthesis, nature’s synthetic input has to be used to obtain in one or only very few chemical reaction steps those complex molecules that petrochemically are only accessible in multi-step reaction sequences. Thus, the production of hydrogen from biomass which is often proposed [36], giving 24 g hydrogen from 180 g biomass and 108 g water, forming 264 g carbon dioxide as coupled product, seems not to be a very sustainable process in comparison to chemical material usage, because only 8.3 weight% of the material, and 13.3 weight% of the biomass input can be used, stoichiometric conversion being assumed (Fig. 6).

Production of hydrogen from biomass.
If hydrogen is to be produced for energy storage purposes, it appears to be more reasonable to prefer other renewable energy sources such as photovoltaic and wind energy, unless synergies of biomass refining are used to produce fuels, chemicals, and power [37]. The power density (~0.6 W m–2) of photosynthesis is much lower than that of photovoltaic and wind energy (~15 W m–2) [38].
At present, the share of renewable raw materials in the feedstock consumption of the chemical industry in the USA and in Germany runs to approximately 5 and 8%, respectively. It is assumed that this percentage will increase notably [39,40,41] (Fig. 7).
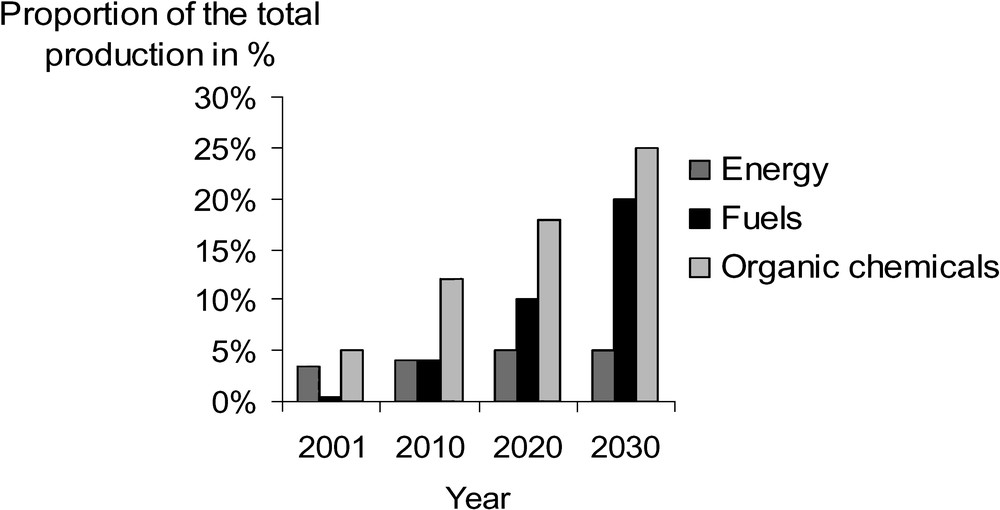
Targets of biobased energy, fuels and organic chemicals in the USA [46].
In the long run, renewables are the only workable solution, and their processing, inter alia, catalytic will make it possible to replace oil and coal as basic feedstocks. It should be pointed out here that the selective catalytic transformation of the complex molecules of biomass is a very great challenge for catalysis. Approximately 51% of the renewable raw materials used at present in Germany are fats and oils. Carbohydrates constitute the second largest portion at 43%, while a further 6% is made up of other renewables such as proteins and lignins [2].
New syntheses with oils and fats as well as carbohydrates [42] as renewable raw materials for the chemical industry were quite recently reviewed [33]. Alkyl polyglucosides are a good example; they are produced as skin-compatible, environmentally benign tensides on a scale of 70 000 t/a [43].
Most products obtained from renewable raw materials are at present not competitive with the products of petrochemistry, a circumstance that will change rapidly when oil resources diminish and the oil price rises. Therefore, it is high time to expand basic research to achieve substitution processes and products, as was pointed out by the German Chemical Society on the occasion of the world summit in Johannesburg [44].
A signal is given by the US Biomass Research and Development Act of 2000. On the basis of the recommendations of the National Research Council of the USA on the estimated development of renewable feedstocks up until 2090 [39,39,40], the ‘Biomass Research and Development Initiative’ (BioInitiative) was created as a multi-agency effort to coordinate and accelerate all federal biobased fuels, power, and products research and development. The agencies that comprise the BioInitiative are conducting, fully funding, or partially funding over 500 active research and development projects in the biofuels, biopower, and bioproducts areas [45].
The ‘Biomass Technical Advisory Committee’ presented the ‘Vision for Bioenergy and Biobased Products in the United States’ [46,47]. In 2030, 25% of the production of organic chemical products is expected to come from renewable feedstocks (Fig. 6)
In Europe, biomass already contributes around 5% of the EU energy supply and 65% of the total primary renewable energy production, predominantly for heat and power applications. In the long term, the contribution of biomass to the European Union energy supply is thought to have the potential to increase to 20%.
The main research and technology development priority in Europe is the development of cost-effective integrated approaches from biomass sustainable procurement to fuel production and use. However, research and technology development for the chemical transformation of biomass to useful biobased products is being totally neglected at present in the European Union as well as in Germany [48]. The question is, what may be the reason for that?
An answer may be found in the CEFIC Report Chemistry – Europe & the Future [11], written with respect to the 6th framework program of the European Union [48]. In this report, a very small section entitled Recycling and Use of Renewable Materials can be found in the chapter Caring for our Planet, containing some lines on renewables. “The use of natural fats and oils, sugars and starch as raw materials in the chemical industry is both a challenge and an opportunity. It is a challenge because of the problem of integrating natural products, which often have very complex compositions, into modern processing and production pathways. These production processes are often limited by ecological and economical considerations and must produce marketable products. It is an opportunity because the use of natural products, which are renewable resources, can be seen as a long-term contribution to sustainable development”.
In other words: the European chemical industry communicated to the European Union that it should not be interested in the use of renewable feedstocks. Obviously, chemical companies are comfortable with petrochemicals and are reluctant to process alternative renewable feedstocks such as plant oils and carbohydrates, which may not be suited for standard petrochemical processing. That is a very general aspect. Chemists learn from the very beginning to think in petrochemical product lines. It is difficult for them to develop alternative thinking in renewable feedstock product lines that have not been available up to now and have to be newly invented [49,50].
The competition of the cultivation of food and of renewable raw materials on the limited available agricultural area [51] could cause problems, because also food demand and consumption will increase dramatically. For that reason, the United Nations program to combat desertification (Agenda 21, Chapter 12, see also United Nations Convention to combat Desertification [52]) is most important. The realization of this program has to be greatly intensified, on the one hand to stop desertification, on the other hand to regenerate agricultural areas by “combating land degradation through, inter alia, intensified soil conservation, afforestation and reforestation activities” (Agenda 21, Chapter 12.4b). The sciences and especially chemistry can make enormous contributions to that program [53], which may contribute to the stabilization of a favourable global climate as well.
4 Sustainable processing of chemical products
The products of the chemical industry display a great chemical diversity. Agenda 21 assumes there are approximately 100 000 chemical substances on the market worldwide. Approximately 1500 compounds make up about 95% of the total world production (Agenda 21, Chapter 19.11). The challenge for chemistry is to realize the manifold and different product characteristics of the mass products of the chemical industry with as few chemical base products as possible, making increasing use of renewable feedstocks.
The vision of a product life cycle management is a scheme of reuse and control of chemical substances in a material cycle concept [54]. An effective and large-scale recycling, which is a goal of Agenda 21 (Chapters 20, 21), ought to be feasible and economic, with only a few base products. The numerous fine and special chemicals have to become more effective, that is, the desired effect needs to be achieved with significantly lower amounts of substance. They need to be mineralised quickly when emitted into the environment. After all, it has to be possible to process chemical industry products in an environmentally benign way. The problem of the emission of volatile organic compounds (VOC) will be discussed exemplarily in more detail.
The products of the chemical industry are mostly processed by the non-chemical industry into products for the end user. Organic solvents are very often used in processing and are emitted as VOCs into the atmosphere [55]. On the one hand this is an immense waste of resources and on the other hand this is a significant cause of the tropospheric ozone formation, which contributes to the summer smog. Total anthropogenic VOC emissions are decreasing slowly [56]. Regulations aimed at reducing tropospheric ozone concentrations have the greatest impact of any of the regulations on solvent usage.
In Germany, these emissions from solvent utilization amounted to 1.160 × 106 t in 1990 (total VOCs: 3.221 × 106 t) and 1 × 106 t in 2000 (total VOCs: 1.6 × 106 t) [57]. The politically determined ozone threshold value of 110 μg m–3 as an environmental quality level in the European Union requires that the emissions of organic compounds into the air have to decrease by 70–80% compared to the reference year (1990). For the Federal Republic of Germany this means: the total emission of VOCs, including that from traffic, has to be reduced to 650 × 103 t by the year 2010. The reductions in emission already achieved by the introduction of compulsory catalytic converters for exhaust gas, as regulated by traffic laws, now suggest that the use of solvents mainly in the processing industry makes up more than half of the total emissions in Germany, which are reducible by technological means [58]. The main emissions are caused in coating, colour printing, and adhesive processing (Fig. 8). The development of chemical products that can be processed without the use and emission of VOCs in areas mentioned is by no means trivial, but is a great challenge to chemistry. More success in this field would mean an important contribution to sustainable development.

Emission of VOCs in Germany by the use of solvents in different industry segments (1988: 1.197 × 106 t/a; 1995: 1.09 × 106 t/a). By the year 2010, VOC emissions have to be reduced to 650 kt/a [56].
The following steps are currently being taken towards the reduction of VOC emissions in the development of new coating systems.
- • use of binders with an essentially higher content of solid matter dissolved in organic solvents (high-solid coatings);
- • use of water-diluted coatings that have a remaining content of organic solvents;
- • use of powder coatings without solvents but frequently with organic cleavage products formed during the curing process;
- • use of radiation-hardening coating systems that to a large extent are free from solvents and even during the hardening do not develop any organic cleavage products.
Binders based on oils and fats seem to be very promising for the development of solvent-free coatings [59]. The benefits of VOC reduction, among other issues, are reflected in the eco-efficiency analysis. For instance, a comparative assessment of four alternative metallic topcoats at Akzo Nobel gave enough information to motivate the marketing and production department to prepare the promising candidate for market introduction [60]. BASF introduced UV-curing water-based coatings that showed high ecoefficiency compared to usual coatings [61].
5 Assessment of the contribution of chemical process and product innovations to a sustainable development
Agenda 21 calls for ‘criteria and methodologies for the assessment of environmental impacts and resource requirements throughout the full life cycle of products and processes’ (Chapter 4.20), and in numerous chapters formulates the aims and measures necessary for chemistry to make an important contribution. These aims and measures have to be considered for an assessment of chemical processes and products with regard to their contribution to a sustainable development. Chemists always have to answer the question: “Which alternative is greener?”
A simple method for a quantitative comparison of the use of resources and environmental impact in syntheses of fine chemicals and pharmaceuticals at the earliest possible stage of process design [62,63], preferably already at the laboratory stage, is essential for the precise development of sustainable processes. Some approaches have been presented during the last few years [64,65,66,67,68,69]. Sheldon’s proposal [70] weights the environmental factor E (mass of waste, that is all compounds used which are not incorporated in the product, per mass unit of product) of a process with substance-specific weighting factors Qoutput. The proposal was developed into an Environmental Assessment Tool for Organic Synthesis (EATOS) [71,72,73]. In this way, an environmental index EIout of the waste is obtained for a process, the value of which reflects the potential environmental impact based on the mass of the product (PEI kg–1). Correspondingly, the mass index S–1 (mass of raw materials used per mass unit of product) is weighted with substance specific weighting factors Qinput to obtain the environmental index EIin, which quantifies the potential environmental impact by the raw materials used (substrates, solvents, catalysts, auxiliary materials for the reaction and work-up procedure). The weighting factor Qinput considers the resources used, as well as the aspects of occupational safety and health, while Qoutput essentially considers the human toxicity and ecotoxicity.
As an example, the environmental factor E and the mass index S–1 were determined both fast and simply to compare two UV curable coatings. The first one is produced on a petrochemical basis using a 1:1-mixture of tripropyleneglycol diacrylate/bisphenol A diglycidether acrylate as a binder. The second one is based on the renewable feedstock linseed oil and used linseed oil epoxide as binder. The reaction scheme is given in (Figs. 9 and 10). Quantitative yields were assumed, and substrate excess, solvents and auxiliary materials were not considered. Fig. 11 shows an important advantage of the renewable coating having a significantly smaller mass index S–1 and environmental factor E, respectively. This result can give first evidence that the coating based on renewable feedstocks may be more sustainable than the petrochemical one. This first evidence was confirmed by a life-cycle assessment (LCA) of the same coatings. In LCA the entire life cycle (product line) of a product (extraction and processing of raw materials, production, distribution and transport, use, consumption and disposal) as well as the potential ecological effects are analysed and the material and energy conversions occurring in the life cycle and the resulting burden on the environment are assessed. The gross energy requirements, the CO2- and NOx-emissions are almost one order of magnitude smaller when linseed oil epoxide was used as a binder [74,75]. This example shows that the software EATOS, with which Fig. 11 was created, is a simple and convenient tool to give a first answer to the question: “So you think your process is green, how do you know?” [76].
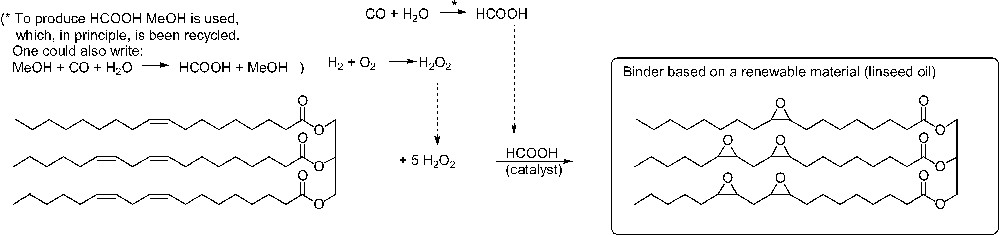
Stoichiometry of the production of a linseed oil-based binder.
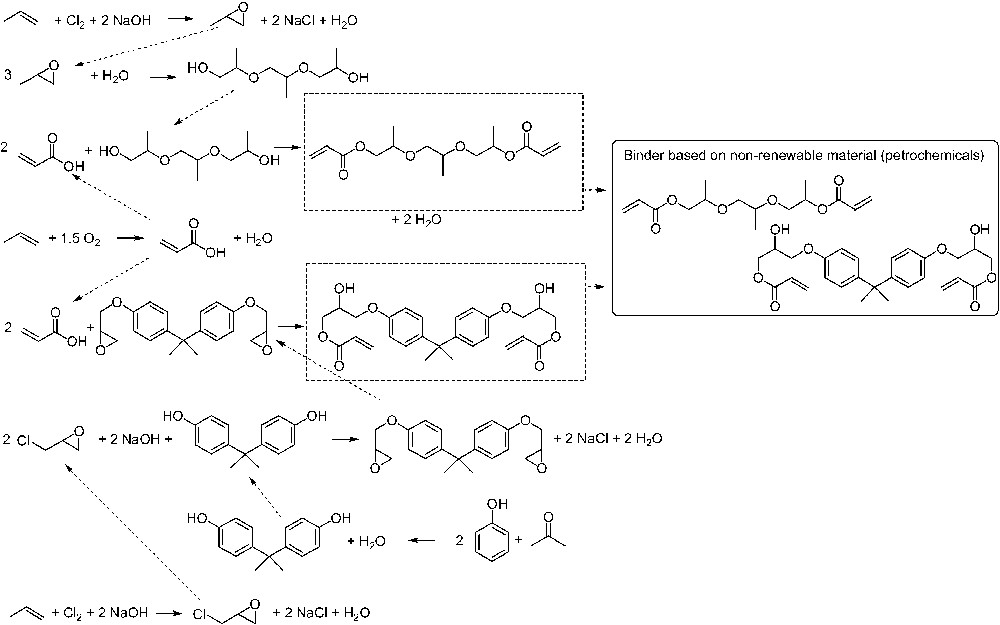
Stoichiometry of the petrochemical route to a binder that consists of a 50:50 mixture of tripropylene glycol diacrylate (TPGDA) and bisphenol A diglycidyl ether acrylate (DGEABA).
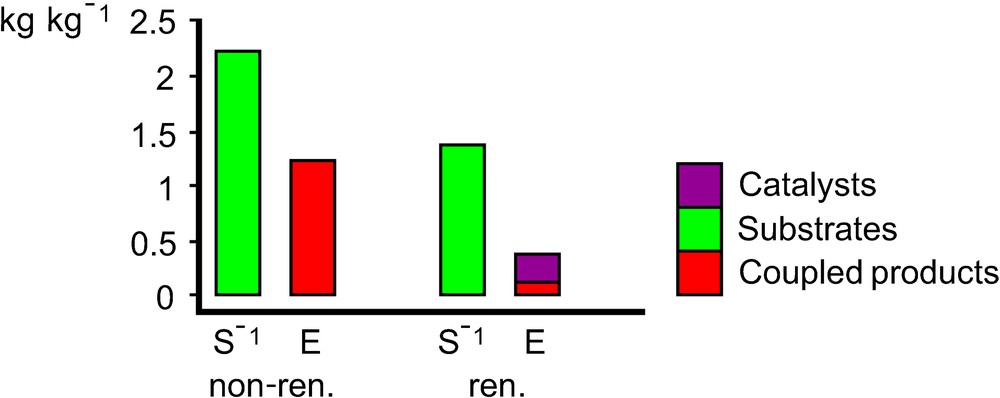
Mass index S–1 and environmental factor E of the binder production shown in Figs. 9 (non-ren.) and 10 (ren.). The software EATOS was used [71,72].
Other examples how quantitative comparisons can be made for the purpose of weak point analysis of resource utilization and raw material costs in synthesis design are given in the literature [77,78].
6 Concluding remarks
The principles laid down in the 1992 Rio Declaration on Environment and Development and in Agenda 21 provide the basis for the development of concepts on the contribution of chemistry to a sustainable development. Our attempt has been to identify the tasks that need to be met by chemistry in fundamental as well as in applied research, and we have given examples of chemical processes and products, particularly for organic chemistry. We have focused on the importance of using renewable raw materials as feedstocks in the chemical industry for a sustainable development. After all, it must be possible to process the products of the chemical industry by applying environmentally friendly procedures, i.e. without VOC emissions.
Inventions of more sustainable chemical processes and products have to be realized in the chemical industry in order to be transformed to innovations for a sustainable development. The time taken to introduce them should be diminished by linking their development with operational innovation management as well as with efficient environmental-political control procedures [2]. Agenda 21, Chapter 30, assigns business and industry an important role in innovations for a sustainable development: “The improvement of production systems through technologies and processes that utilize resources more efficiently and at the same time produce less wastes – achieving more with less – is an important pathway towards sustainability for business and industry. Similarly, facilitating and encouraging inventiveness, competitiveness and voluntary initiatives are necessary for stimulating more varied, efficient and effective options” (Agenda 21, Chapter 30.4).
Vous devez vous connecter pour continuer.
S'authentifier