1 Introduction
Ground granulated blast furnace slag (GGBS) is a secondary product of cast iron industry. It is produced by rapid cooling of molten slag at the exit of the furnace. Its status of ‘waste’ makes it a more respectful material for the environment than many others in construction. In comparison with classical Portland cement, no energetic expense is necessary and as a consequence no reject of CO2 [1]. GGBS has nearly the same hydraulic ability as Portland cement [2]. Under special conditions, it is able to develop mechanical strength. This binding ability is due to the emergence of a hydration product called C–S–H (calcium silicate hydrate). Blast-furnace slag cement is generally used as a substitution of a part of Portland cement. It was established since many years in civil engineering that using blast furnace slag cement in constructions (sea wall, underground mass of concrete for example) improves consequently the durability (chloride, sulphate, acid attacks...) [3,4]. Nevertheless, a simple addition of water in slag is not enough to induce a hydraulic reaction. Slag must be activated with a basic component that increases the pH to a satisfactory level [5].
The aim of this study is to determine whether blast furnace slag can be used as an entire hydraulic binding agent, with no substitution of other materials (Portland cement or other hydraulic cement). Mechanical performances study allows us to evaluate a couple slag/activator from a macroscopic point of view and NMR, a very powerful technique for the investigation of glassy or ill-crystallised materials, gives information about the microstructure. This double investigation leads to some correspondence between the mechanical strength of a formulation and the nature of its hydration products.
2 Experimental details
2.1 Ground granulated blast furnace slag
GGBS is the rapid cooling floating part of iron mix at the exit of metallurgic furnaces. It can be cooled by water or ambient air. It is a glassy/crystalline composite in which the glassy part can reach 95% of the entire material mass. The slag used in this study is a fine white powder, with a 4500 cm2 g–1 specific area. Its composition is given in Table 1.
Blast furnace slag mass composition (oxide equivalent)
CaO | 41.65% | Na2O | 0.22% |
SiO2 | 34.39% | K2O | 0.30% |
Al2O3 | 12.88% | S2– | 1.04% |
MgO | 7.80% | Other | 1.72% |
2.2 Chemical activation
To understand the activator mechanism in the hydration process of slag, four activators have been studied: Na2CO3, natural gypsum (CaSO42H2O), Ca(OH)2 and Portland cement [6]. These activators were chosen for their slag activation ability and because they do not present large hazards to be handled. The different activators performances are compared to those of Portland cement, which is used in ordinary manufactured slag cement.
2.3 Sample preparation
The entire samples are prepared in the same way, using a water/total binder mass ratio of 0.5. The slag and the activator at the chosen ratio were mixed with water. The samples were then mould in cylindrical test tubes of 40-mm diameter and preserved safe in dark room in a pool of water until the date of the compressive tests. After compression, a central part of the sample was taken and then the hydration process stopped by using acetone/ether mix. The composition of the different samples is shown in Table 2.
Samples composition (C1 < C2 < C3) with a water/binder ratio of 0.5
Formulation | Activator | Concentration |
M1 | Portland cement | C1 |
M2 | C2 | |
M3 | C3 | |
M4 | Na2CO3 | C1 |
M5 | C2 | |
M6 | C3 | |
M7 | Natural gypsum | C1 |
M8 | C2 | |
M9 | C3 | |
M10 | Ca(OH)2 | C1 |
M11 | C2 | |
M12 | C3 |
2.4 Solid state NMR
NMR study is based on quantitative 29Si (spin I = 1/2) high-resolution magic angle spinning experiences [7]. High spinning rate decreases the dipolar interaction and the anisotropic part of the chemical shift, and accumulations (up to 10 000 spectra) are sufficient to obtain a low signal/noise ratio spectrum. Spectra are obtained with a Bruker ASX solid-state NMR spectrometer operating at 11.7-T magnetic field. Spinning rate was about 7 kHz in 7-mm ZrO2 rotors. All experiences use single π/2 pulses, recycling delay of 5.75 s, without 1H decoupling. The relaxation times are respected, and all the spectra are weight-normalised. The 29Si isotropic chemical shifts are referenced relative to tetramethylsilane Si(CH3)4 (TMS) at 0 ppm; Si[(CH3)3]8Si8O20 (Q8M8) is used as a secondary reference.
In order to reduce quadrupolar effects of 27Al nuclei (spin I = 5/2), NMR experiences may be carried out at high magnetic field and high spinning rate. Hence, 27Al NMR was realised in high-field magnets (11.7 T and 19.6 T), with spinning rates up to 30 kHz in 2.5-mm ZrO2 rotors. All experiences employed single π/12 pulses sequences. Chemicals shift are referenced relative to a 1.0 M AlCl3–6 H2O solution.
The assignment of 29Si and 27Al resonance peaks is based on chemical shift range established for minerals and cements [8,9].
2.5 Compressive tests
Compressive tests were made using a hydraulic press with a maximum force of 1500 kN. Each formulation was tested under compression for different hydration times: 7, 14, 28, 90 and 500 days. These times are conventional in French civil engineering [18]. For 90 days of hydration in Portland cement, the hydration ratio is considered to be equal to 95%.
3 Results and discussion
3.1 Hydration products
Basic activator destroys the glassy structure of the slag and releases in the water/slag solution the different elements necessary for the constitution of the hydration products (C–S–H and secondary products of aluminates hydration). Typically, in classical use of GGBS as a substitution of Portland cement, cement alkali plays the role of the slag activator. The hydroxyls ions OH– cut the Al–O and Si–O bonds [5]. Their combination with Ca2+ in solution leads to the formation of calcium silicate hydrate (C–S–H) [(CaO)x(SiO2)y(H2O)z], hydrogarnet (Ca3[Al(OH)6]2), sulphoaluminate hydrate phases like ettringite [(Ca3Al(OH)6.12H2O(SO4)32 H2O)], and Afm phases [(Al2O3–Fe2O3-mono)] [10].
C–S–H can be represented as short chains of silicates with a microstructural order at nanometre scale. The microstructural model of Tobermorite can be used to approach the C–S–H structure. The nature and the structure of C–S–H in Portland cement were discussed by several authors [11,12]. A schematic representation is shown in Fig. 1. Due to their ill-crystallised structure, it is very difficult to study the microstructure by XRD or SEM. Solid-state NMR does not matter with the regularity of the crystalline network. The stoichiometry of such hydrated species is not established. It depends on many parameters and some are not yet identified. Nevertheless, for Ca/Si ratios below 1.0, between 1.0 and 1.5 and upper 1.5, Nonat has identified α, β, and γ types and structures for C–S–H [13]. In other Ca/Si ratios cases, tendencies of long or short chains formation can be evidenced, but no precise chemical formula.
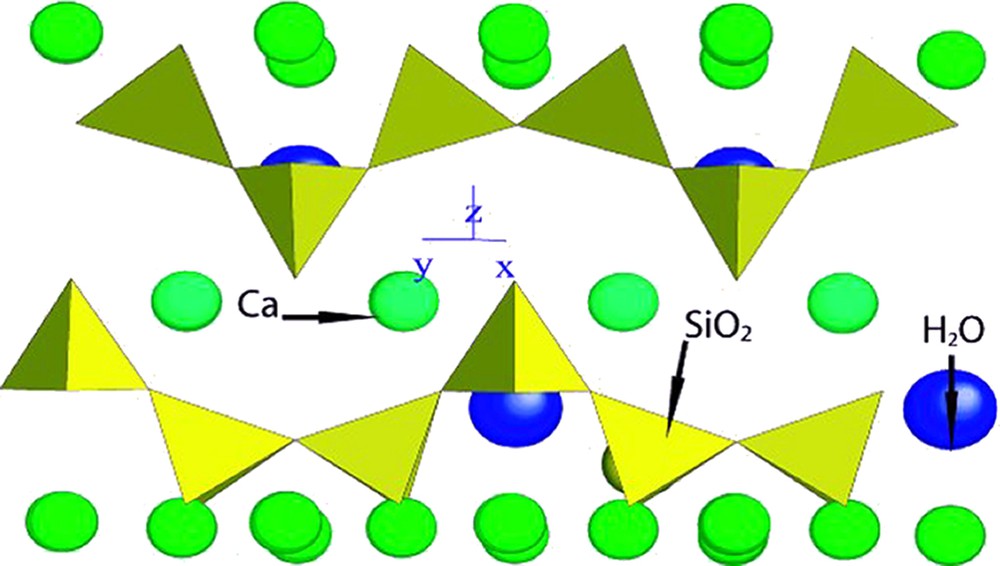
Schematic representation of structural nature of C–S–H.
3.2 Mechanical performances
Experimental curves are shown in Fig. 2. For all the activators, without special curative treatments or special additives, we can observe that the mechanical performances are equal or better than those obtained with a classical Portland cement, except with Ca(OH)2 activation. The reference samples using Portland cement as the activator, after 7 days of hydration, reach 10 MPa, and a maximum of 30 MPa after 90 days for the M3 sample. These results agree with the classical performances of a slag cement grout formulation.

Mechanical compression strength of the different slag/activator compositions from 7 days to 90 days of hydration.
Na2CO3 activation for short hydration times (7 and 14 days) is the most efficient (more than 20-MPa compressive strength at 7 days). At medium and long time of hydration (28 and 90 days), the mechanical performances reach respectively 20-MPa and 24-MPa compressive strength for M4 and M5. Na2CO3 seems to be the more efficient of this study (up to 40 MPa after 90 days of hydration, M5 formulation) but for high activator ratio, some rheological problems can occur, due to a quick rigidification of the grout.
Gypsum activator does not present after 7 days of hydration enough mechanical properties to be measured, whatever the activator concentration is. Nevertheless, this activation presents interesting rheological properties for civil engineering works, considering the great rigidification delay of the grout. After 14 days of hydration, the compressive strength is more than 12 MPa for M7 and 25 MPa for the two others. After 90 days of hydration, M7 reaches 27 MPa, whereas medium and higher concentrations reach 30MPa compressive strength. With gypsum, the mechanical performances are nearly the same, whatever the activator concentration is.
One also obtains very tight results for Ca(OH)2 whatever the concentration is. After 90 days of hydration, the compression strength is only 15 MPa, which is not enough for an industrial use.
In the case of cement, slag or other hydraulic binder, many other parameters like granular stacking, porosity or thermal shrinkage have a great influence on the mechanical performance.
3.3 29Si NMR
The various hydration products of hydrated slag can be observed by the solid-state NMR of several nuclei. The most relevant nuclei are 29Si (spin 1/2), 27Al (spin 5/2), 23Na (spin 3/2), 25Mg (spin –5/2), 1H (spin 1/2 ) and 43Ca (spin –7/2).
First of all, the C–S–H slag study is done by the evaluation of the different electronically environments of the tetrahedron SiO4, elementary unit of the chain structure. Second, the NMR study of 27Al, which can exist in tetrahedral, pentahedral and octahedral coordination, gives information about the hydrated aluminates, the sulphoaluminates products (octahedral coordinence), the possible substitution of aluminium in the SiO4 chain (tetrahedral coordinance) or in the CaO plane (pentahedral and octahedral coordinence).
Fig. 3 shows the different 29Si NMR spectra obtained after 28 days of hydration for the higher activator concentration. For all the activators, spectra can be decomposed into six elementary peaks. According to the chemical shift table of 29Si [9], the attribution of these peaks may be: Q0 (–74ppm), Q1(1Al) (around –75ppm) Q1(–77ppm), Q2B (–82ppm), Q2(1Al) (–80ppm) and Q2 (–84ppm). Qn attributions correspond to the connectivities of SiO4 species, Q2B (where ‘B’ means ‘bridging’) to a middle tetrahedron of the dreierkette C–S–H chain structure. Q0 species corresponds to the anhydrous slag. Nevertheless this first decomposition into Qn unit does not allow us to determine the geometry of the hydrates: the superposition of Q1(1Al) with Q0 peaks and Q2B with Q2(1Al) peaks impedes the calculation of an elementary-chain length. The growth or decrease of the different species when varying the hydration times can be evidenced. The most important decrease of Q0 species occurs for Na2CO3 activation, which corresponds to the high mechanical strength measured. As shown by the 29Si NMR spectra, the different activators have not the same effect on the hydration process. The role of the alkali cation seems to be important in the slag activation/hydration process. A comparison between the different spectra of a same activator family for different activation ratio is represented in Fig. 4. The decreasing kinetics of the Q0 unit increases with the activator ratio.
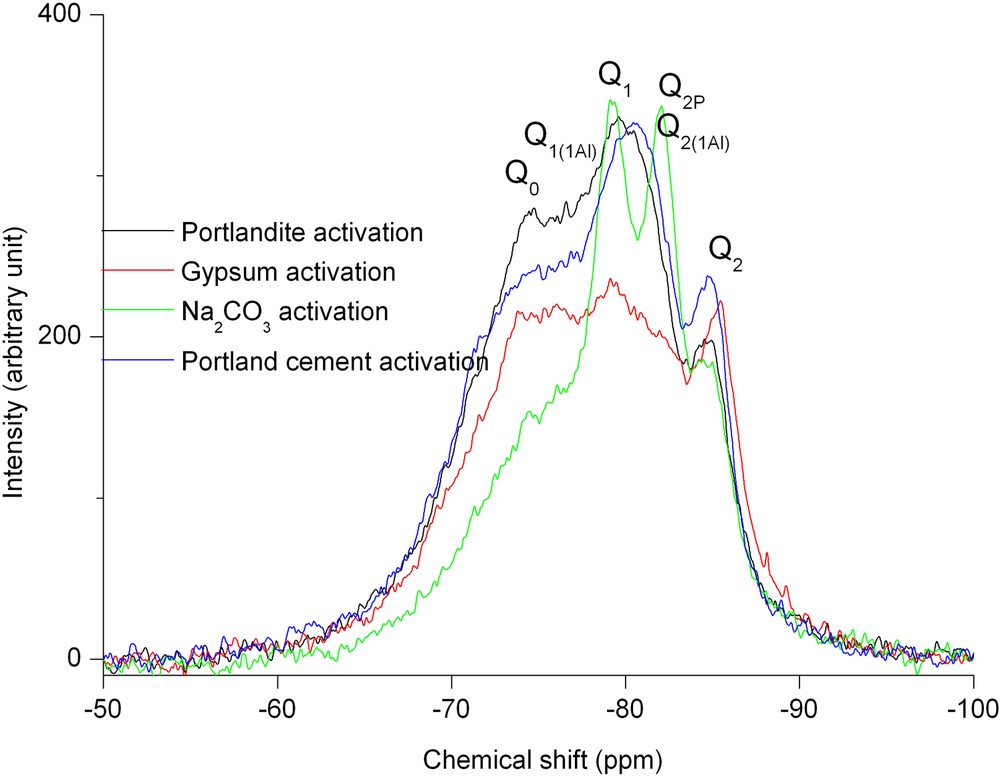
29Si MAS NMR spectra after 28 days hydration of slag/activator compositions. Experiences realised at 11.6 T, 7 kHz spinning rate. Single π/2 pulse sequence. Same activator substitution.
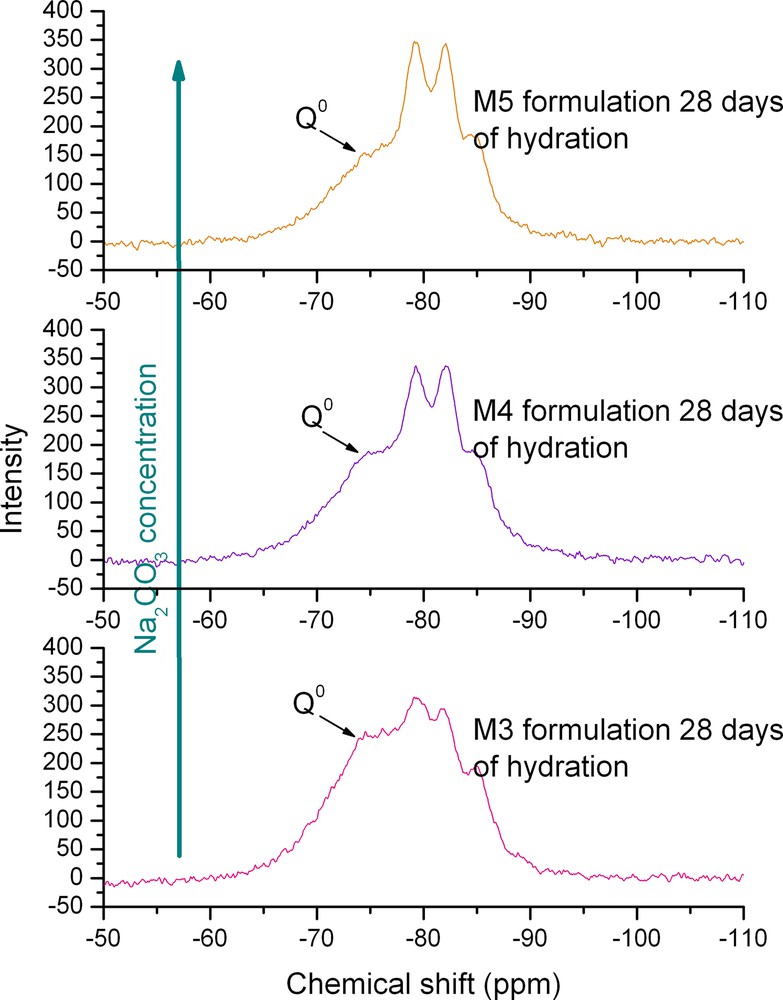
29Si MAS NMR spectra. Na2CO3 activator concentration influence on hydration kinetics. Experiences realised at 11.6 T, 7 kHz spinning rate. Single π/2 pulse sequence. Same hydration time.
3.4 27Al NMR
27Al NMR for classical cement composition is very interesting to evaluate the occurrence of the different hydration products containing aluminium, which can cause serious damages to a construction.
27Al NMR spectra for all the activators are shown in Fig. 5. In octahedral site, 27Al NMR shows three different peaks with Portland and gypsum activation [14]: ettringite (a special form of Aft phases) at 12 ppm (position of the maximum peak resonance intensity), monosulphoaluminate at 9 ppm and a non-assigned peak at 3.5 ppm are formed [17]. With Na2CO3 and Ca(OH)2, Afm phases are present, but ettringite and monosulphoaluminate have disappeared (no SO42– in water/slag solution).

27Al MAS NMR spectra of 28 days hydration slag/activator compositions. Experiences realised at 11.6 T, 30 kHz spinning rate. Single π/12 pulse sequence. Same activator substitution. From top to bottom: M11.500js, M2.500js, M5.500js, M8.500js.
The aluminium inside the anhydrous slag is on a tetrahedral site. By using high-field MAS NMR spectrum (19.6 T), an improvement of the spectrum resolution is obtained (Fig. 6): a great peak appears at 71 ppm, which could be the signal of the silicon substitution by aluminium inside the C–S–H chain. By coupling this result with the substitution hypothesis, it is possible to introduce a hydrated product for hydrated blast furnace slag: C–Al–S–H (alumina-silicate of hydrated calcium). Taking into account this substitution phenomenon in 29Si spectra, we can assign the Q2B peak as a double peak Q2B and Q2(1Al) [15,16].

27Al MAS NMR spectrum on a 19.6 T magnet. 25 kHz spinning rate. Single π/12 pulse sequence. Na2CO3 activator (M5), 365 days of hydration.
4 Conclusion
Four couples of slag/activator with different activator concentration were tested mechanically and their hydration products analysed by 29Si and 27Al NMR. The structures of the different hydration products are quite different from those obtained in the case of pure Portland cement hydration. 27Al solid state NMR has highlighted a strong phenomenon of substitution in the silicate chain so that we could introduce the notion of C–Al–S–H instead of C–S–H. The decreasing kinetics of Q0 units seems to be linked to the mechanical performances of the slag/activator composition. Na2CO3 and gypsum are the most relevant activators from a mechanical point of view, even if higher activator concentration is not really compatible with an industrial use: the quick rigidification time of the grout does not allow us to use such an activation ratio.
Acknowledgements
The authors would like to thank Zehong Gan, from CIMAR, National High Magnetic Field Laboratory, Florida, USA, for the realisation of the high-field 27Al NMR spectra.