1 Introduction
One of the major technological challenges in this new century is undoubtedly energy storage, hence the fast developing research in that field. For more than three decades, intensive efforts have yielded several generations of highly successful batteries, among which the rechargeable Ni–MH batteries and Li-ion batteries that have conquered the market place. Although widely used, the Li-based systems still suffer from a lack of suitable electrode materials, and will rapidly fall short of satisfying the users’ demands. Aware of such materials demands, chemists have acted at several levels by either designing new materials, or by modifying existing ones, through texture modification and surface treatments. The ‘bake and shake’ synthesis approach together with solution methods were among the most used to achieve such a goal.
Over the years, ball milling processes have been widely applied to so many research fields (magnetism, catalysis, intermetallic alloys) [1–5] that covering its history would take up too much time. For some unknown reason, such a processing/synthesis technique did not capture the field of rechargeable Li-batteries until Disma’s early study [6] on the enhanced Li electroactivity of milled carbons [7,8]. Mechanical milling, which can be viewed as the action of transforming mechanical energy into chemical energy, stands as a simple and environmentally friendly alternative to high temperature synthesis or solution chemistry. It enables the room temperature elaboration of metastable phases (either crystallized or amorphous), which are unreachable via classical routes, and provides a convenient mean to change powders morphology. The nature of the synthesized phases resulting from a ball-milling experiment varies according to both the thermodynamic and kinetic properties of the system and the selected experimental conditions [9].
Usually such experiments are conducted in hermetically-sealed containers hosting grinding balls and precursor powders, and occasionally equipped with gas inlets in order to vary the grinding atmosphere (O2, H2, N2 or vacuum). The grinding is done by placing the containers on various types of grinders, vibratory or planetary, operating either in a shock (SPEX), planetary friction (Fritsch), or combined shock/planetary friction-type modes to obtain powders with highly-controlled physical characteristics. Depending upon the energy of the ball-to-powder interactions, the constraints generated within the solids can relax either by liberating heat, or by promoting the creation of fractures, new surfaces and/or defects [9].
More specifically, at low mechanical energy grinding, the simplest route for constraints relaxation is the heat. Upon increasing the mechanical energy, we favour the appearance of cracks within the particles that, beyond energy threshold, will propagate with the end result being the breaking of particles and the creation of new fresh surfaces. The successive fracture of the particles will lead to a size decrease, which is therefore not unlimited since the increasing particles surface energy can outweigh the mechanical constraint energy, in which case the particles are going to form aggregates [6].
In short, repeated grindings (e.g., welding and fracturing of powders) will enable to create step-by-step new interfaces, and therefore reduce diffusion distances so as to favour the chemical elements interdiffusion at the atomic scale required to produce a new phase. The obtained powders having nanometric-size crystallites are generally very different from those obtained via thermal treatment as far as their structure and texture are concerned. Herein, we will illustrate the wealth/breadth of the mechanosynthesis technique with a few examples selected from the field of Li batteries. More specifically, we will show, through our research effort, how mechanical milling can be used to (1) enhance electrode performances either by adjusting particle texture/morphology, or by modifying particles surfaces through coatings, (2) prepare room temperature highly-crystallized metastable phases, and (3) simulate Li-driven electrochemical reactions. Needless to say that, owing to the present blooming of the ball-milling research activity to confection electrochemically optimized Li-based electrodes, numerous examples from other groups could also have been used as well to convey the same message.
2 Acting on the particle texture/morphology: ball milling of carbons
Carbonaceous materials are key components in today’s Li-ion batteries [10] and super capacitors [11], due to their faradic and capacitive-type behaviours, respectively. Such behaviours strongly depend on the type of carbon used and on its fabrication. Recent trends in supercapacitors involved the development of high-surface-area activated carbon electrodes to optimize the performance in terms of capacitance and overall conductivity, while, for batteries, efforts entailed the fabrication, through pyrolysis of organic substances, of disorganized carbons with large capacities. Within this context, owing to the ability for mechanical milling to both reduce particle size and increase disorder, ball-milling experiments on carbonaceous materials were performed. By adjusting the grinding operating conditions (e.g., nature of the grinders used, type of atmosphere – O2, N2, H2 or vacuum – and ball-to-powder ratio), carbonaceous powders showing varying organization states and having different textural/electrochemical characteristics were obtained. A direct correlation was established between the structural and textural characteristics of ground carbonaceous materials and the electrochemical performances of C/Elec./Li cells or C/Elect./C supercapacitors.
When shock-type grinding was used, we showed that the amount of reacted lithium (x in LixC6) during the first discharge proportionally increased with the specific surface of the ground graphite. Yet, part of Li is trapped during the first charge. This non-recovered amount of Li, corresponding to the irreversible capacity (Capirr) nicely traces the specific surface of the ground carbonaceous materials, namely goes through a maximum (Fig. 1a), and then decreases with increasing milling times. In contrast, the capacity (e.g., length) of the first charge rapidly increases with increasing the milling time, and then progressively levels off [6,12,13]. For long grinding times, carbonaceous materials having the highest reversible capacity (700 mA h g–1) for the lowest irreversible capacity (250 mA h g–1) leading to overall performances, which favourably compare with those of chemically prepared disordered carbons, were obtained. Such results were further improved, namely a lower polarization and an enhanced reversible capacity (720 mA h g–1), when milling experiments were conducted in low-oxygen-pressure conditions (10–6 bar) [14].
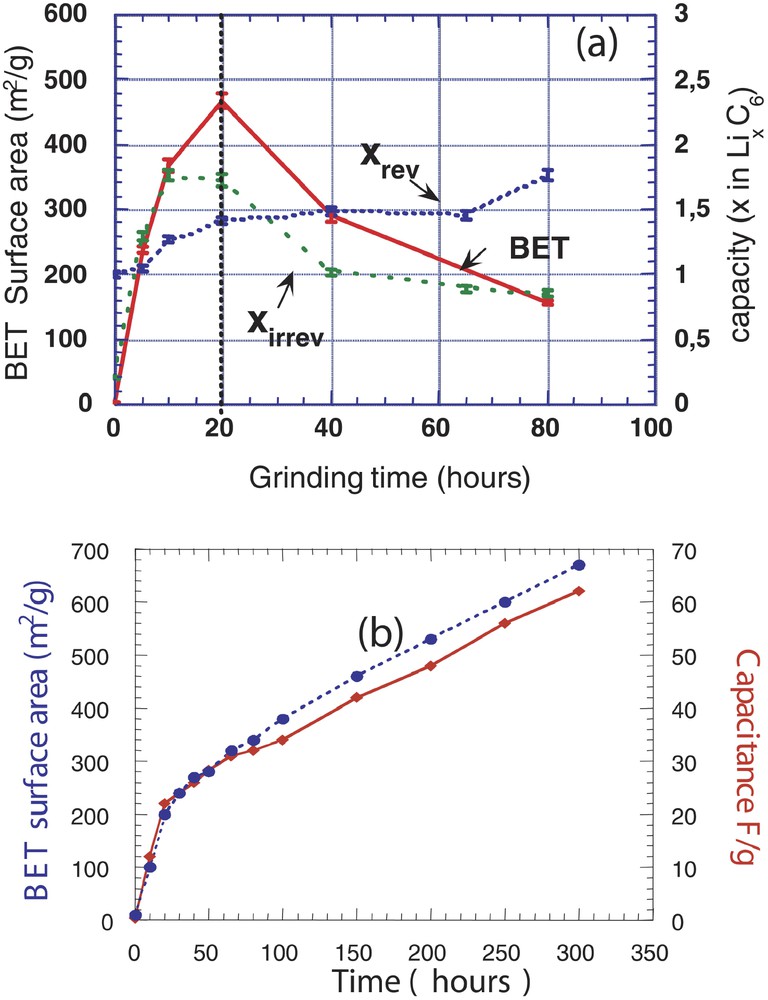
The variation of the BET surface area of carbonaceous materials is plotted (a) as a function of milling time using a shock-type grinder (SPEX). Also shown for the same samples are their reversible and irreversible capacities as deduced from the electrochemical charge/discharge curves of C/Li cells. In (b), the variation of the BET surface area of carbonaceous materials obtained using a shear-type grinder (FRITSH) as a function of milling time is shown together with the capacitance in (F g–1) for the same samples as deduced from C/C symmetric cells.
Interestingly, a totally different behaviour was observed, with namely a continuous increase in the specific surface area with increasing milling time (Fig. 1b), when shear-type instead of shock-type ball milling was performed. Shear-type grinding only resulted in a continuous exfoliation of the sheets that led to large specific areas in opposition to shock grinding, which subsequently led to exfoliation, splitting/breaking, and particle agglomeration. The performances of such high-surface area carbonaceous materials turned out to be detrimental to batteries, for which the irreversible capacity Capirr was found to trace the BET surface area. In contrast, such large BET surface areas were shown to be beneficial to supercapacitor applications, since shear-type milled carbonaceous materials with capacitances ranging from 65 to 100 F g–1 could be elaborated.
Apart from the influence of the ball to powder interaction-type, the addition of a liquid solvent into the milling container was shown as being another crucial parameter to tune the texture/morphology of carbonaceous materials when ball-milled. Janot et al. succeeded by performing shear-type ball milling in the presence of a liquid, such as the dodecane that acts as both a lubricant and a dispersing agent, in preparing graphite powders made of very thin (around 20 nm), well-crystallized and anisometric particles [15]. The latter showed quite a less irreversible capacity during the first discharge than non-milled ones, in spite of a much larger specific surface area (about 100 times greater). Such a finding further highlights the importance of mastering the ball-milling experimental parameters to specifically prepare materials having the suitable texture to also promote electrode materials with high charge–discharge cycling rates, while preserving the material initial capacity and lowering the irreversible one.
Surprisingly, whatever the type of carbon precursors used, similar ball milling-driven textural/physical/electrochemical effects were found, stressing the universal benefits of non-reactive mechanical milling to alter the morphology of carbonaceous materials, and to increase their capacitive or faradic capacity. Finally, aside from carbons, the recent achievement of long-term cyclability for the 3-V redox process in LiMn2O4 electrodes, made from ball-milled powders, is also very illustrative of the spectacular effect that ball milling can have [16]. Within the spinel, upon Li reduction, there is a cubic-to-tetragonal phase transition associated to an 8% volume change, so that upon cycling coarse particles become disconnected, and the capacity progressively fades. In contrast, small particles, as those obtained from ball milling, are able to both expand and accommodate the structural strains due to the lithium insertion more easily than large ones, enabling then a high degree of reversibility for the redox process.
3 Acting on the particle surface: carbons coating
Whatever the battery technologies, a prerequisite for optimum performance is to have electrodes with both good ionic and electronic performances [10]. Electrodes are composites resulting from an intimate mixing of an electrochemically-active material, a binder to ensure particle cohesion, and of carbon additives to increase the composite electronic conduction. The quality of the contact/interface between active material and conductive carbon is crucial for the electrode performances, and is specifically acute for materials having a very low electronic conductivity, such as phosphates [17], from which we solely can tap a few percents of the material’s initial capacity. To remedy this, one must play with the electronic conductance of the composite electrode by (1) acting on the compound formulation through cationic substitution [18], (2) decreasing the dimension of the active material particles, and (3) improving the interfacial connectivity between carbon and active material. Besides the combination of low-temperature synthesis and nanopainting routes [19], mechanical milling, which stands as another viable approach aimed at modifying the electrode/electrolyte interface by altering the particles surface, has been investigated [20].
The influence of ball milling on the amount of inserted Li in a phosphate phase LixFe2(PO4)3 is shown in Fig. 2. The more the material is ball milled with carbon, the more we have access to its theoretical capacity (90% of the theoretical capacity is obtained for the 240-min ball-milled sample). Here again, this ball-milling-induced positive effect was found to be universal, since it was experienced, for all the electroactive phosphates so far investigated, with an optimum grinding time depending on both the phosphate structure and the acido-basic nature of the surface ending groups.
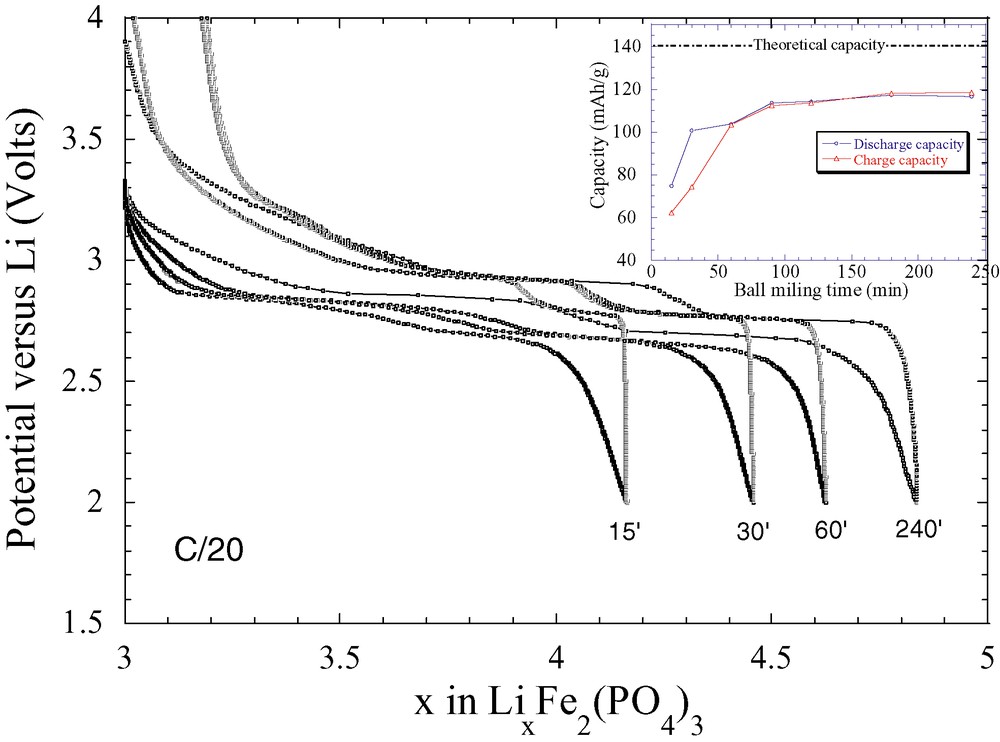
Voltage composition curves for LixFe2(PO4)3/Li cells cycled at C/20 and using a (80:20 weight ratio) phosphate/carbon composite that was milled for various times. The inset shows the variation of the recovered capacity as the function of the milling time with the maximum capacity being reached after a 200-min grinding time using a SPEX-type grinder.
For instance, grinding times as short as 30 min were found to give the best electrochemical capacity for olivine-type structures (LiFePO4, LiMnPO4, etc.) [21]. Such a universal effect is believed to be nested, as deduced by TEM observations, in cumulative effects involving particle size reduction together with the formation of new interfaces. Mechanical grinding results in particle fracturing so that the number of non-fully coordinated atoms at the particle surface increases, thus enabling a better carbon coating (e.g., better carbon–phosphate interface), and therefore an electronic conductivity enhancement. Although it may appear quite simple and magic, caution has to be exercised in blindly applying such a technique to prepare electrochemically-optimised carbon-based composite electrodes. It is essential to know the milling time threshold beyond which the electrochemically active particles agglomerate through surface tension, rather than keep fracturing.
In view of achieving better carbon coatings, Disma’s early findings [6] related to the appearance of a maximum (e.g., beginning of surface agglomeration) in the BET-surface area of shock-ground carbonaceous materials, was further exploited in a similar way, as done earlier in our group by Aymard et al. on metal hydrides [22]. They demonstrated, through the elaboration of highly electroactive carbon/metal hydride composites, that such a particle agglomeration can provide a simple mean (Fig. 3) of coating active particles as long as they are injected into the grinding container prior to the occurrence of carbon agglomeration [23]. A similar approach was applied to the phosphates. By mixing the active material with 300-m2 g–1 pre-ground carbon, we succeeded in obtaining, after only 15 min of ball milling, a carbon/LiFePO4 composite electrode having the same electrochemical performance as the one made in 30 min from an as-received graphite [21].
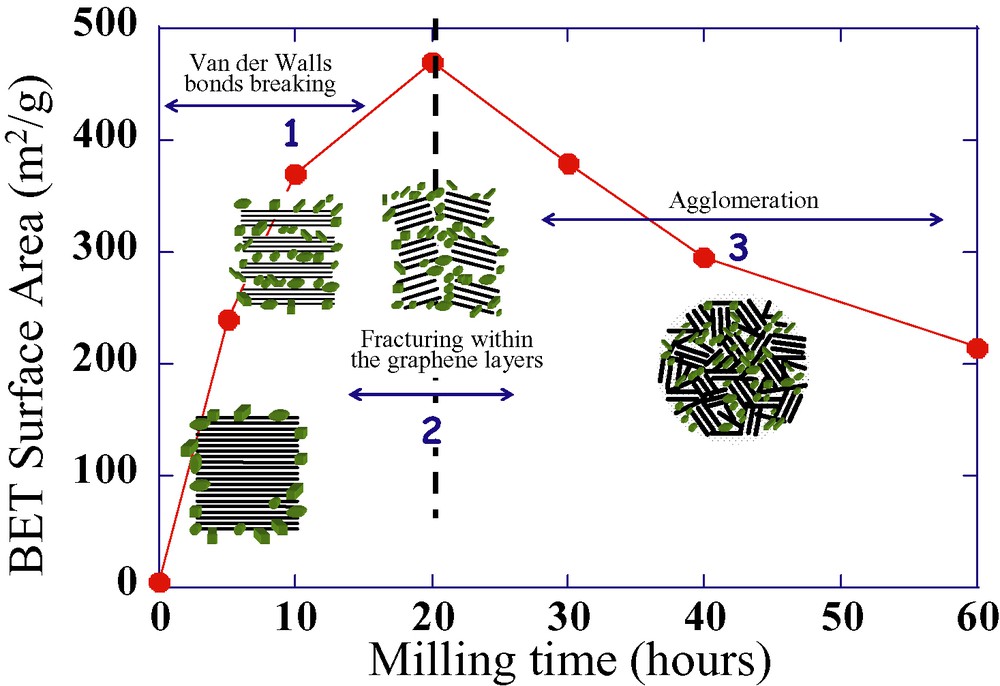
Schematic, as derived from [21], showing how mechanically-induced carbon coating proceeds during a mechanical milling experiment. The process involves three steps. During the first step (denoted 1 on the drawing), the van der Walls interactions between the grapheme layers are weakened, and there is a partial exfoliation of the graphene layers. Upon further grinding (step 2), fracturing does occur within the graphene layers with a beginning of agglomeration, which becomes more efficient as grinding proceeds. Through this process, the treated particles end up to be embedded within the graphene basal units.
In line with such findings, in the future quest for electrode materials, we no longer need materials with good electronic properties. Therefore, numerous disregarded materials must now be revisited. Along that line, we should quote the most recent spectacular results obtained by Amatucci et al. [24] regarding the reactivity of FeF3 towards Li. Such a previously rejected insulating material was shown to reversibly react with 3 Li at 70 °C leading to capacities of 850 mA h g–1, when mechanically milled with 20 wt.% carbon powders.
4 Mechanochemical synthesis of Li insertion compounds
Although mechanosynthesis has been recognized as a technique of choice in the preparation of nanocrystalline powders alloys (CuSn, InSb, SnFe...) [7–9] for rechargeable lithium batteries, it has not been fully exploited to prepare Li-based electrode materials. Due to its high ductility, it is impossible to grind Li without being confronted with sticking problems. Using Li powders and the adjunction of a liquid solvent selected as both a lubricant and dispersing agent, Janot et al. [25,26] recently overcome the Li sticking problems, and succeeded in preparing a super dense and stable lithiated compound having the LiC3 stoichiometry that could so far be only synthesized under both high temperature and isostatic pressure (50 kbar). It turned out therefore to be unfortunate that upon Li oxidation such a phase was found to transform into LiC6, and did not convert back to a LiC3 phase upon the subsequent reduction. Nevertheless, such a work had opened a new path towards the synthesis of metastable Li-based phases, which has been intensively exploited over the last few years, leading to the room-temperature synthesis of new phases such as Li3Sb and LixMPn4, for instance.
The LixMPn4-type phases (M = Ti, V and Pn = As, P, N) were shown to hold great potential with respect to applications in Li-ion cells [27]. Yet, one of the main difficulties resides in the preparation of these compounds that, in spite of drastic synthesis conditions (900 °C in sealed tantalum tubes), produces samples highly contaminated by second phases, primarily Li3P, TiP, and TiP0.63, whose cumulative amounts always exceeded 25%. To circumvent this sample purity issue, our group decided to extend the ball milling approach to the synthesis of single-phased LixTiP4 materials.
Within an argon dry-box, raw powders of Ti, P, and Li elements were mixed in the right stoichiometry to reach the Li9TiP4 reported composition [28]. The optimum milling parameters were determined, and the best result, namely the synthesis of single phase Li9TiP4 with an a-axis of 6.02(2) Å, was reached for a grinding time of 12 h at room temperature. To ensure that our room-temperature ball-milled (BM) sample, displaying broad Bragg peaks (Fig. 4), was not contaminated by impurity phases in their amorphous states, it was annealed at various temperatures. For temperatures as low as 500 °C, we obtained an X-ray powder showing a drastic sharpening of the Bragg peaks corresponding to the Li9TiP4 phase, but always devoid of any impurity phases. The voltage–composition curves for Li/Li9TiP4 cells made from room temperature ball-milled, or 500-°C re-annealed ball-milled sample, as the positive electrode, are shown in Fig. 4a and b, respectively. Both samples can reversibly react with six lithiums (per formula unit) yielding capacities of at least 700 mA h g–1 with therefore a difference in the voltage profile during oxidation, namely a flat vs a sloping voltage, mainly due to the nanosized character of the room-temperature ball-milled produced particles, which generates various interfacial energies, resulting in some potential distribution. While great efforts have still to be made towards optimising such electrode materials, we have shown through this example how ball milling can be useful in enhancing again the interest of materials disregarded on the basis of synthesis complexities.
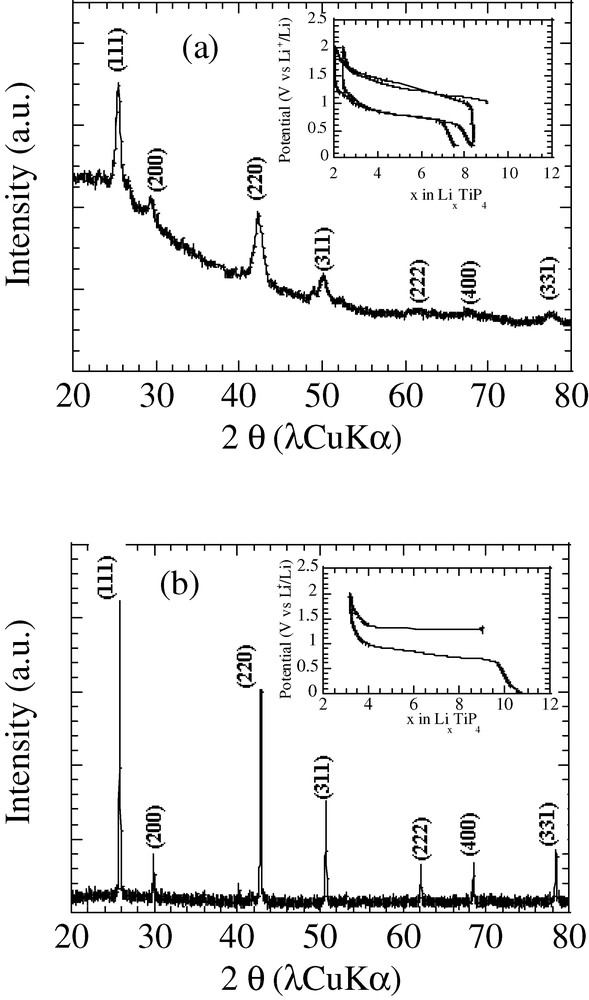
The X-ray powder pattern of the phase obtained after ball milling for 12 h of a mixture of Ti, P, and Li elemental powders having the nominal composition Li9TiP4 is shown in (a). The X-ray powder pattern of the same phase after annealing at 500 °C for 6 h is shown in (b). As insets, the voltage composition curves of Li9TiP4/Li cells cycled at a C/5 rate and using each of these materials as positive electrodes are shown.
5 Simulation of electrochemical discharges: CoSb3; Li4Ti5O12; LixGay
Last, the ball-milling technique was exploited as a way to mimic electrochemical reactions. A twin track approach aimed at either simulating displacement reactions such as MX + 2 Li → M + Li2X, which involves extensive bond breakage, atomic reorganization and formation of new bonds, or Li insertion into host materials while preserving the framework structure, was successfully pursued.
The electrochemical Li reduction of CoSb3, which is known [29] to lead to the formation of a compound made of Li3Sb and metal Co, serves to illustrate the first approach. Indeed, it was demonstrated that ball-milling a mixture of Li and CoSb3 powders for 12 h at ambient temperature and in the presence of dodecane produced a composite (Li3Sb + Co) having an oxidation curve similar to that observed with an electrochemically made (Li3Sb + Co) composite.
Dealing with the second approach, our group recently showed, through grinding studies of Li powders with the well-known Li4Ti5O12 insertion compound, the possibility of also using ball milling as a mild chemical lithiation technique. Effectively, 3h grindings of Li4Ti5O12 in the presence of increasing quantities of Li powder enabled us to prepare a series of ‘Li4+xTi5O12’ compounds, with x values ranging from 0 to 3, and whose electrochemical signature is similar to that of Li4Ti5O12, with a plateau at 1,5 V (Fig. 5).
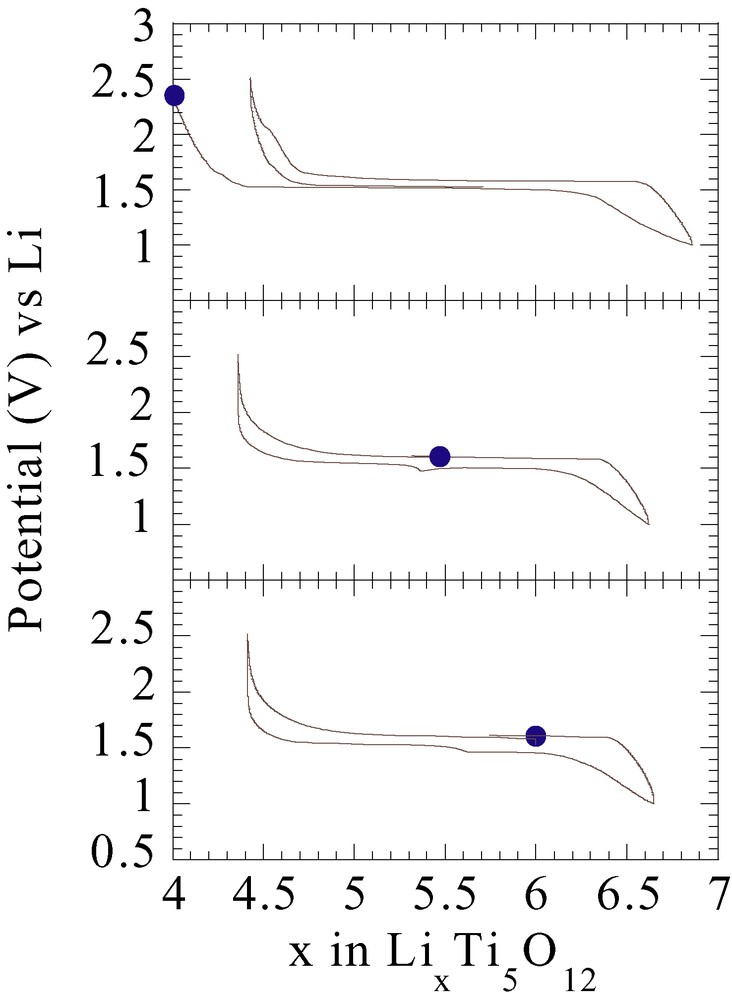
The voltage composition curves are shown for Li4Ti5O12/Li cells using either (a) as-made Li4Ti5O12 or (b) and (c) Li4Ti5O12 electrodes that were previously reduced by ball milling of Li4Ti5O12 with increasing amounts of Li: 2 and 3 per formula unit, respectively. The cells were started on charge and cycled at a C/5 rate. Note that the charge amplitude scales with the amount of the added Li during the milling process, implying the efficiency of the ball-milling reduction process.
Finally, our last example, dealing with the exploration of the Li–Ga room-temperature phase diagram, will illustrate how ball milling can simultaneously be used to mimic electrochemical discharge curves and prepare single-phase materials. The room-temperature electrochemical insertion of Li into Ga can be achieved [30] by discharging a Li/Li-based electrolyte/Ga electrochemical cell down to 0 V vs Li (Fig. 6). The voltage trace that reaches 0 V vs Li+/Li near x = 2 composition (Li2Ga) is not smooth, but presents several staircase steps at x = 0.3 (Li2Ga7) or x = 1 (LiGa) that are indicative of the existence of single-phase materials in agreement with the previously-reported phase diagram [31]. To further explore such single-phase materials from both a structural and electrochemical point of view, we have attempted to prepare them in large quantities by ball milling. Mixtures of Li powders and Ga shots, in nominal compositions to prepare either the Li2Ga7, LiGa or Li2Ga phases, were poured in a hermetically sealed stainless-steel vial that was placed on the SPEX 8000 mixer. From a survey of various grinding times coupled with XRD analyses (Fig. 6), we concluded that only 2 h of ball milling were necessary to produce nicely crystallized single-phase LixGay powders, whose parameters were found to agree with those reported in the JCPDS files. Increasing ball-milling time resulted in a significant Bragg peak broadening, indicative of the beginning of an amorphization process together with an increasing contamination of the samples by iron metal coming from the grinding container. While kept under silence so far, such a type of contamination is an inherent drawback of the ball-milling synthesis process that we must be aware of, and that is not predictable. Indeed, for reasons yet undetermined, the Fe contamination in the LixGay powders was highly increasing upon milling times, reaching values as large as 20% for 10 h of ball milling time, while the presence of Fe could not be detected with other materials prepared under similar conditions.
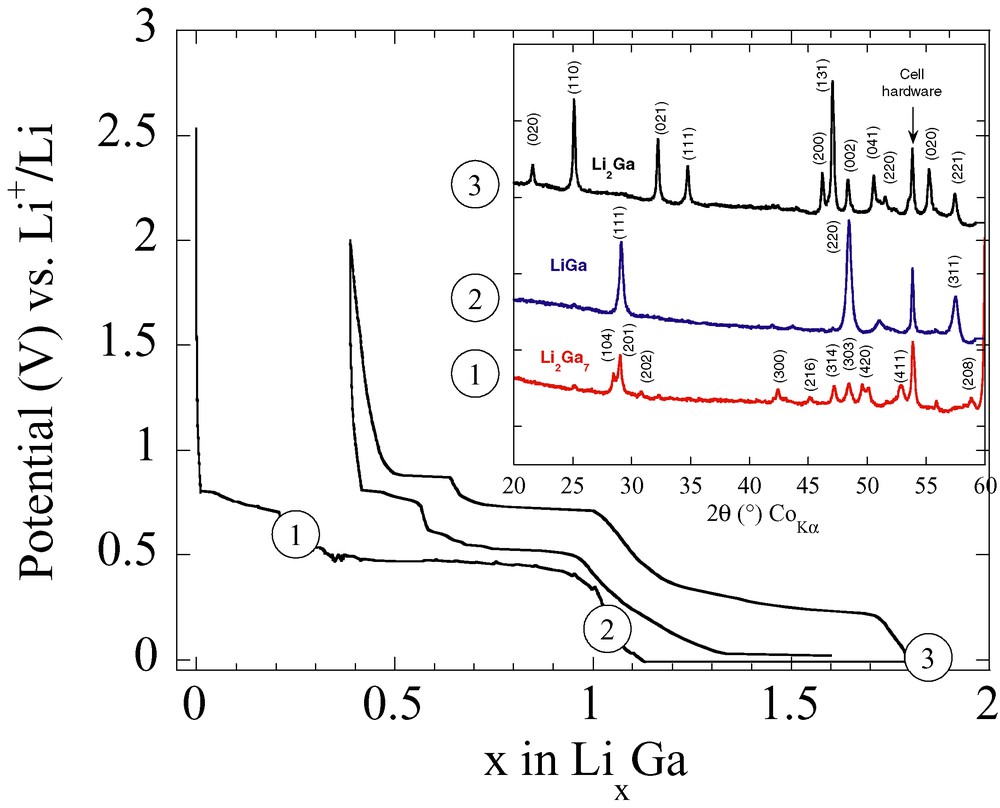
Voltage trace for a Li/Elec./Ga cell discharged at a rate of 1 Li in 100 h. The abrupt voltage drops referred to as 1, 2 and 3 are indicative of the single-phase compositions Li2Ga7, LiGa, and Li2Ga, respectively. The insets show the X-ray diffraction patterns of powder mixtures obtained by room temperature ball milling (see text) of Li and Ga elements having Li/Ga nominal compositions of 2/7, 1 and 0.5. For each studied composition, the materials are single-phased, with sharp Bragg peaks indicative of their high crystalline nature.
6 Discussion/conclusions
Through the above descriptive examples, we hope to have captured the reader’s awareness on the beneficial aspects of mechanochemistry within the field of rechargeable Li-based batteries. More importantly, we should realize that such benefits are not limited to Li-based systems but encompass various battery technologies. To convey this message, let us simply consider the metal-hydride (MH) negative electrode in Ni–MH batteries. For instance, recent attempts to optimize the Mg–Ni–H system are based on some of the same conceptual approaches as those presented for Li-based electrodes.
A striking similarity does exist. We should begin with recalling that, within the Mg–Ni system, the most suitable metastable Mg2Ni electrode composition can only be prepared by mechanical milling [32,33]. Then, to optimize Mg2Ni electrode electroactivity vs H+/H2 while fighting its limited lifetime associated to corrosion reactions in KOH media, numerous coating techniques have been exercised, with the most successful one being the carbon coating of Mg2Ni particles through mechanochemistry [22,34]. Finally, the ball-milling-driven formation of the reduced Mg2NiH4 phase, by grinding Mg2Ni powders under an hydrogen ambient [35], further illustrates the great power of mechanochemistry in mimicking electrochemical reactions. Such a technique is rapidly expanding beyond the elaboration of electrode materials, and is now entering the elaboration of solid electrolyte nanocomposites [36], hoping, on the basis of space charge effect models, ionic conductivities enhancements, as recent results seem to support.
However, although quite exciting, there are practical considerations that should not be overlooked in using mechanochemistry to prepare nanodivided composites having usually large surface areas. Firstly, it is well known that fine powders when prepared as electrodes lead to low packing densities, and therefore to low volumetric energy densities, unless specific measures are taken to improve compaction. Secondly, large surface areas materials are known to favour electrolyte catalytic decomposition if their electroactivity potential range falls outside the thermodynamic stability potential window of the electrolyte used. For instance, ball-milled LiMn2O4 exhibits a nice capacity retention when cycled over the 3-V range vs Li+/Li, and a very poor one when cycled over the 4.1-V range. Luckily, today’s phosphate materials, which are of special interest with respect to applications and display electroactivity vs Li+/Li over the 2.5–4 V potential range, can greatly benefit from mechanical milling.
Overall, it should be realized that the appeal of mechanochemistry to the field of electrode materials lies in its ability to synthesize, under mild conditions, new metastable phases enabling a rapid and easy screening of new electrode materials, since such a technique is not only solvent-free, but also free from the complexities associated to high-temperature processes in sealed environments. Needless to say that such an approach is being implemented worldwide with many different materials.
Acknowledgements
The authors are indebted to M. Figlarz for introducing this approach to the LRCS and all the researchers (F. Chevallier, F. Disma, S. Laruelle, C. Lenain, A. Rougier, and S. Soiron), who have greatly contributed to the establishment of a solid scientific platform from which we can build.