1 Introduction
Dye-sensitized solar cells are an attractive alternative to conventional solar cells, since they are cheaper and simpler to produce [1]. The working electrode of these solar cells consists of a nanostructured film of titanium dioxide (TiO2) coated on a conductive glass substrate. A dye is adsorbed on to the surface of this TiO2 film; under illumination, electrons are injected from the excited state of the dye to the conduction band of the TiO2 and transported through an external circuit to the counter-electrode. The circuit is completed within the cell by an electrolyte [1].
The nanostructured films used in these solar cells often contain small holes that allow direct contact between the electrolyte and the conducting layer on the glass [2], and these points of contact act as short-circuits in the cell. The use of a compact, thin layer of TiO2 coated directly on to the glass substrate, applied by spray pyrolysis, has been found to prevent the back transfer of electrons to the electrolyte from the conductive glass substrate [3–5]. The use of a phenol/2-allylphenol copolymer as a blocking layer, applied by electrodeposition, has also been investigated [2]. In this work, the effect on solar cell performance of applying a compact film of TiO2 by a simple dip-coating method has been investigated.
2 Experimental
TiO2 nanoparticles were produced by a sol–gel method. Following the method of Shklover et al. [6], 300 g of dilute (0.1 M) nitric acid solution was placed in a round-bottom flask. Titanium isopropoxide (48 g, Aldrich, 97%) was added drop-wise over a 1-h period under constant stirring. Peptization was then achieved by heating at 80 °C for ~8 h, followed by filtering through a glass frit to remove any remaining agglomerates.
F:SnO2 glass (Hartford Glass Company, sheet resistance 15 Ω per square) was cleaned by an ultrasonic treatment in ethanol and dried at 70 °C. Compact TiO2 blocking layers were applied by dip-coating using the TiO2 sol; samples were produced with 1, 3 and 5 coatings, allowing the films to dry at room temperature for 30 min and at 70 °C for 10 min between each coating. The films were subsequently heat treated at 450 °C for 30 min.
A slurry of a commercially available TiO2 powder (Degussa P25) was made using 4 g TiO2, 8 g distilled water and 250 g poly(ethylene oxide) (Aldrich). A thorough dispersion of the TiO2 was achieved using an ultrasonic horn (Sonics and Materials VCX-750, 750 W, 20 kHz), with treatments for 5 min being applied both before and after adding the PEO to the slurry. Films of this slurry were then coated on the blocking layers by doctor blading. Control samples were also produced with no blocking layer. These films were heat treated at 450 °C for 30 min and stored in a desiccator until used in solar cell construction.
The thickness and roughness of both the sol–gel blocking layer and the P25 nanostructured film were measured by profilometry (Cotec AltiSurf 500). Scanning Electron Microscope (SEM) images were obtained at 25 kV (Hitachi S570).
Prior to dye adsorption, the TiO2 films were heated again at 450 °C for 10 min and then immersed in a ruthenium dye solution (0.3 mM solution of Ru(dcbpy)2(NCS)2, where dcbpy is 4,4′-dicarboxylic acid-2,2′-bipyridine, in 1:1 butanol and acetonitrile) for 24 h. Excess dye solution was removed by rinsing in acetonitrile.
The counter-electrode was produced by coating F:SnO2 glass with a thin layer of a 5 mM solution of H2PtCl6 in isopropanol. This coating was dried at 50 °C for 15 min and heated at 385 °C for 15 min, with a heating rate of 2 °C min–1.
The two electrodes were sealed together with Surlyn polymer film (200 μm thick, DuPont) and the electrolyte (0.5 M LiI (Lancaster), 0.04 M I2 (Lancaster) and 0.05 M 4-tert-butylpyridine (Aldrich) in acetonitrile) was injected through a hole in the counter-electrode, which was then sealed with Surlyn and glass.
The photovoltaic properties of the solar cells were characterized under illumination of a 21-V, 80-W tungsten lamp (Phillips 13160). A source meter (Keithley 2400) was used to measure the current between –0.2 and 0.9 V, under a light intensity of 1 Sun (determined by an externally calibrated photodiode).
3 Results and discussion
The thickness of the nanostructured TiO2 layer (applied on top of the compact layer) was consistently ~10 μm. Electron micrographs of these films are shown in Fig. 1; there was no significant difference in the microstructure of these films for different numbers of blocking layers.
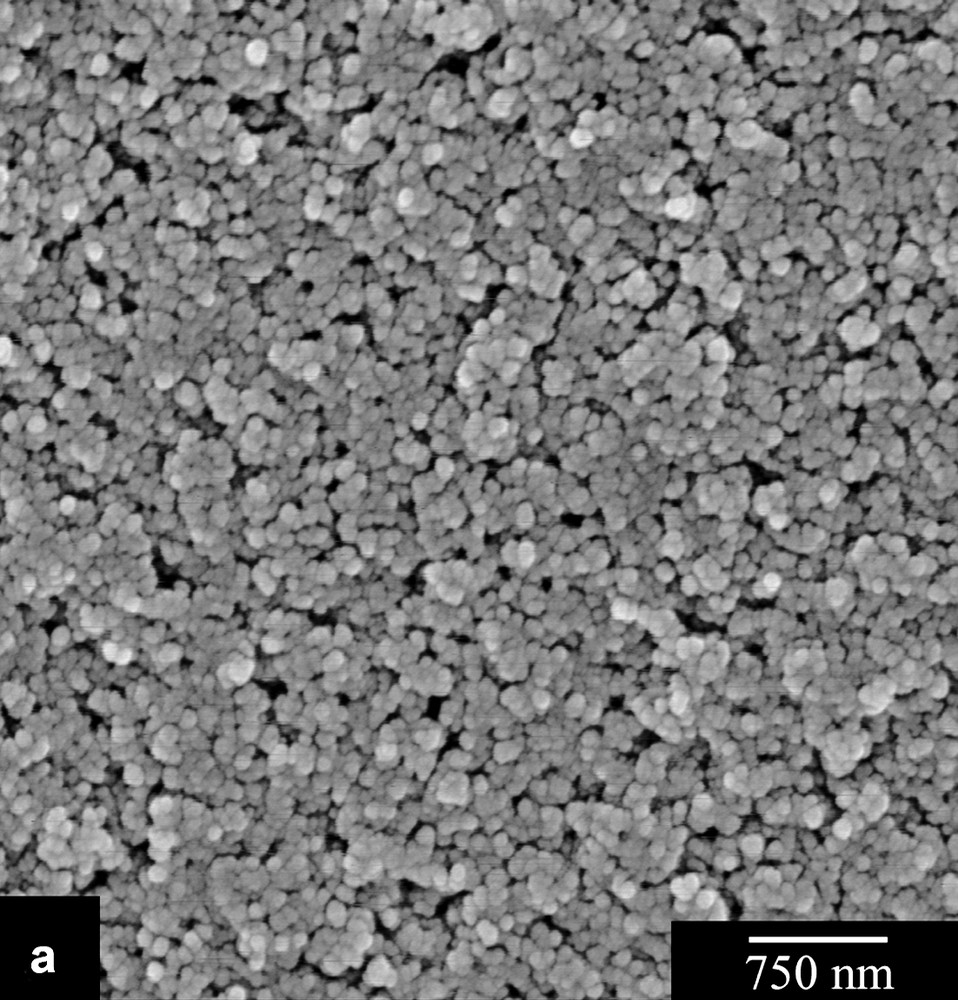
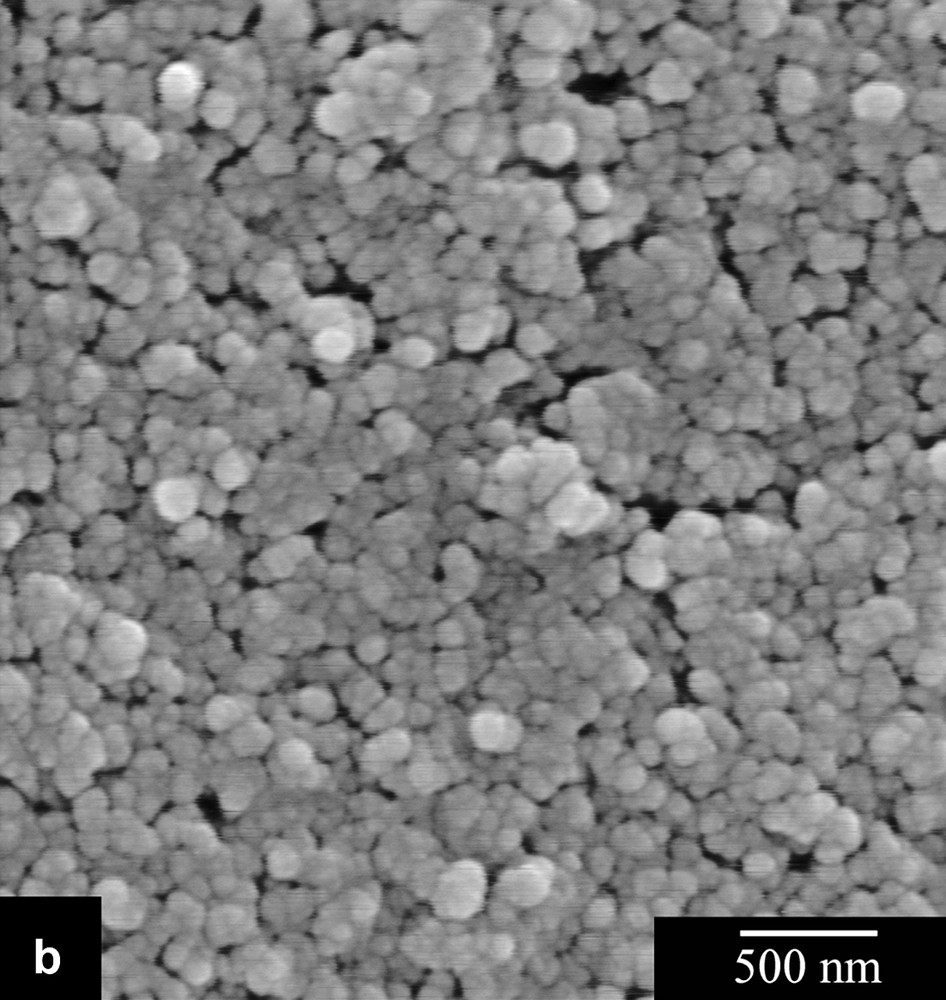
SEM micrographs of nanostructured TiO2 layer for samples with three compact TiO2 blocking layers (a) and five compact TiO2 blocking layers (b).
The photovoltaic properties of the solar cells without a blocking layer and with 1, 3 and 5 TiO2 sol–gel blocking layers are shown in Table 1 and the current–voltage curves for the cells that produced the highest and lowest short-circuit current for each number of blocking layers are shown in Fig. 2. It can be seen that, with increasing the number of coatings of sol–gel TiO2, the short-circuit current and the efficiency of the solar cell increased. This indicates that the back transfer of electrons is suppressed by the blocking layer. There was no significant change in either the open-circuit voltage or the fill factor, which is in agreement with previous work, in which it was found that compact TiO2 blocking layers, applied by spray pyrolysis, prevent the back transfer of electrons to the electrolyte under short-circuit conditions but have little effect under open-circuit conditions [4].
Photovoltaic properties of solar cells with no blocking layer and with one, three and five compact TiO2 sol–gel blocking layers. Uncertainties are given as the 70% confidence interval
Short-circuit current (mA cm−2) | Open-circuit voltage (mV) | Fill factor | Efficiency (%) | |
No blocking layer | 10.7 ± 0.8 | 764 ± 2 | 55 ± 3 | 4.5 ± 0.2 |
One blocking layer | 11.9 ± 1.1 | 755 ± 4 | 54 ± 3 | 4.8 ± 0.2 |
Three blocking layers | 13.1 ± 1.0 | 757 ± 1 | 51 ± 3 | 5.0 ± 0.2 |
Five blocking layers | 13.8 ± 0.9 | 762 ± 6 | 52 ± 3 | 5.49 ± 0.02 |
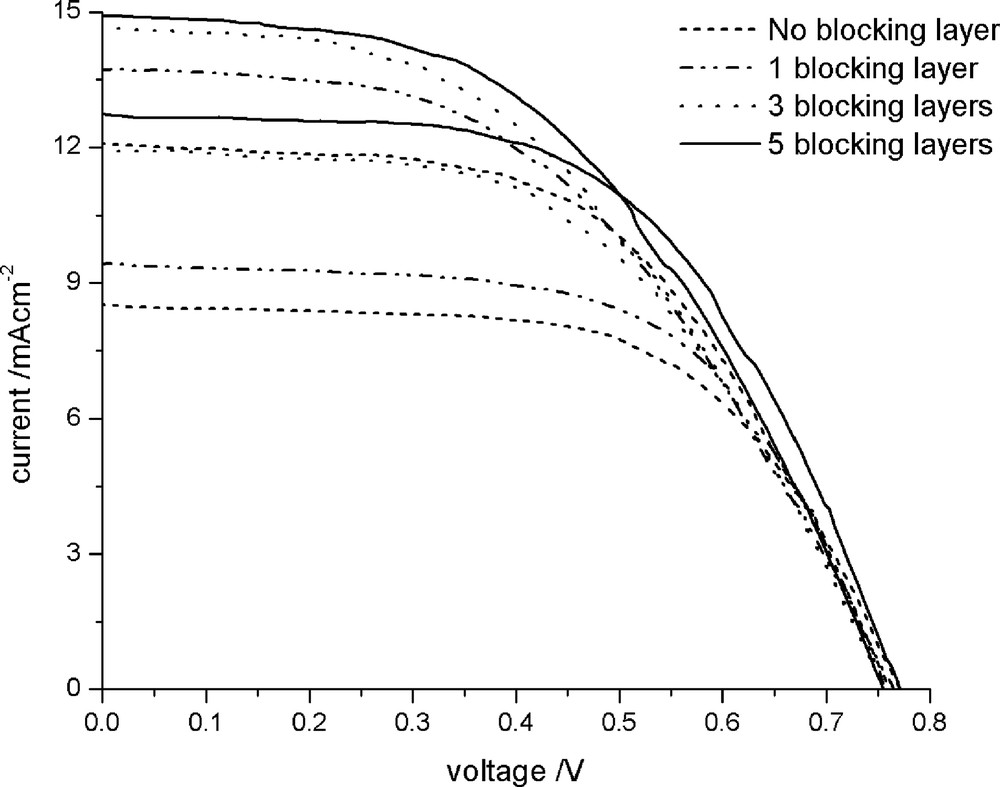
Current–voltage curves for solar cells with no blocking layer and with 1, 3 and 5 TiO2 sol–gel blocking layers.
The thickness and mean-square-roughness of the compact TiO2 layers are shown in Table 2 and electron micrographs of these films are shown in Fig. 3. The thickness and roughness of the films varied between samples and the range in which the values for the majority of samples were found are given in Table 2. As the number of blocking layers that were applied increased, the thickness of this compact TiO2 layer increased. This increase in thickness is the most likely explanation for the improvement in solar cell performance when the number of blocking layers is increased, since a thicker film will more effectively block the back transfer of electrons.
Thickness and root-mean-square roughness of compact TiO2 blocking layers
Thickness (nm) | Roughness (nm) | |
One blocking layer | 30–100 | 25–45 |
Three blocking layers | 200–400 | 10–25 |
Five blocking layers | 250–500 | 10–25 |



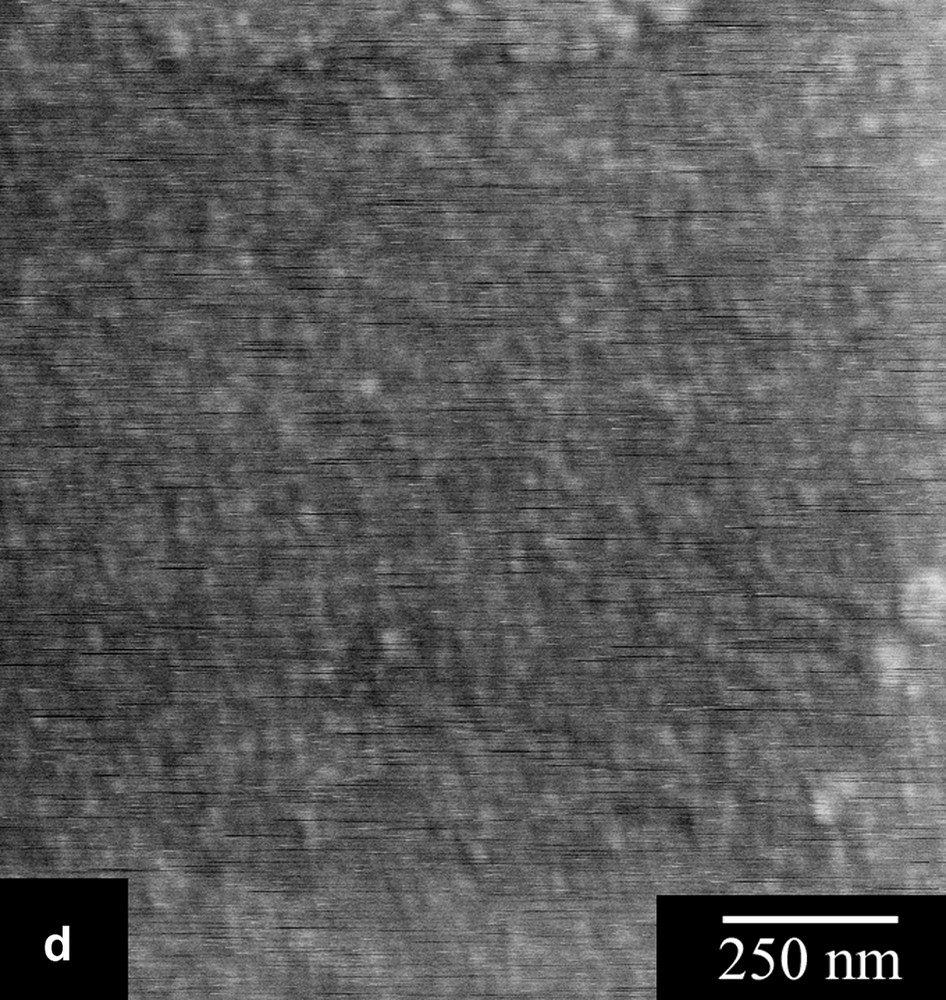
SEM micrographs of compact TiO2 blocking layers for samples with one blocking layer (a), three blocking layers (b) and five blocking layers (c and d).
As the number of blocking layers was increased from 1 to either 3 or 5, the roughness of the film decreased (Table 2). It is likely that the first layer does not completely cover the substrate and still contains some small holes. When further layers are deposited, the film becomes smooth and uniform and the holes are filled, leading to complete coverage of the substrate. This increase in the uniformity and smoothness of the compact TiO2 films probably also contributed to the improvement in solar cell performance when the number of blocking layers increased.
In this work, it has been found that the solar cell performance continued to improve up to the maximum number of blocking layers that were used, suggesting that further work is required to determine if the performance continues to improve as the number of layers is increased and to establish the optimum thickness for the compact TiO2 film.
4 Conclusions
The application of compact TiO2 films to the substrate of the working electrode of dye-sensitized solar cells by dip-coating increased the efficiency of these solar cells. This increase in efficiency was largely due to an increase in the short-circuit current, resulting from the prevention of the back transfer of electrons from the conducting layer on the glass substrate to the electrolyte. As the number of coatings increased, the efficiency of the solar cells also increased, due to the compact TiO2 film providing better coverage of the substrate and due to the thickness of the film increasing, thus providing a greater barrier to the back transfer of electrons.
Further work will include microwave processing of both the TiO2 sol–gel blocking layers and the nanostructured TiO2 films. It is hoped that the use of microwave processing will allow a relatively high efficiency to be achieved with heat treatment at lower temperatures than those used in this work.
Acknowledgements
The authors acknowledge the financial support for this work provided by a Monash University Engineering Research Grant and the Australian Research Council. J.N.H. gratefully acknowledges the assistance provided by Monash University through the Sir James McNeill Foundation Scholarship. The assistance of Dr. Sophie Cerneaux with the French translation is also gratefully acknowledged.