1 Introduction
The need for sustainable energy sources in the future is of increasing importance due to the rate of use of non-renewable energy sources and increasing population. Thus, research into solar energy devices such as the dye-sensitized solar cell (DSSC) has been increasing [1–13]. One critical component of the DSSC is the semiconducting layer, typically a nanoporous titania layer [1,8,13]. One of the processing steps involved in the production of these working electrodes is the calcination of the thin metal oxide on the conducting oxide substrate.
In this work, a 2.45-GHz microwave reactor [11] was used to provide the heat required for effective calcination of the semiconducting film. As reported earlier, the use of 2.45-GHz microwaves results in cracking of the transparent conducting oxide (TCO) coating on the glass [11,14]. In this work, the use of external SiC susceptors was utilized to overcome the problems that arise due to the TCO film being a microwave absorbing material.
The use of core-shell nanostructures has been shown to alter the performance of the DSSCs, in many cases causing a substantial improvement [10,12,15–24]. In these studies, the working electrodes were processed using conventional heating. This study examines whether increased photovoltaic performances can be obtained by using a core-shell system (ZrO2-coated TiO2) calcined by 2.45-GHz microwaves.
2 Experimental
TiO2 working electrodes were produced from a slurry of 4 ml distilled water, 2 g preformed TiO2 nanopowders (P25, Degussa), 100 μl Triton X-100 (Lancaster) and 25 μl acetylacetone (BDH). The slurry was coated using a doctor blade technique on F:SnO2 glass (TEC8, Hartford Glass Co.). The ZrO2 shells were deposited onto the TiO2 nanostructure via spin-coating a 0.1 M zirconium isopropoxide (Aldrich) solution in isopropanol at 2000 rpm for 10 s. Immediately after spinning, the working electrodes were washed with isopropanol. The ZrO2-coated electrodes were then hydrolyzed at 70 °C in a water-soaked desiccator for 30 min. Some of the uncoated and ZrO2-coated TiO2 working electrodes were then calcined in a 2.45-GHz microwave (MPC, Model 941) using a technique reported earlier [11]. The working electrodes were dyed using a 0.3 mM N3 ([Ru(dcbpy)2(SCN2)] where dcbpy = 4,4´ dicarboxylic acid-2,2´ bipyridine) solution in a 1:1 solution of butanol and acetonitrile for 20 h. From profilometry (Taylor Hobson, Talysurf 10) it was determined that the film thickness was 8 ± 1 μm. In addition, the film thickness was unchanged after calcination and sol–gel modification to form a core-shell nanostructure.
Counter electrodes were produced by coating a thin film of a 5 mM H2PtCl6 solution in isopropanol on F:SnO2 glass. The electrodes were then dried at 50 °C for 15 min and then heated at 2 °C min–1 to 385 °C for 15 min before annealing to room temperature. Counter electrodes were sealed to the working electrodes by heating a Surlyn gasket (200 μm thick, Dupont) and sandwiching the two glass plates together. The electrolyte [0.5 M LiI (Lancaster), 0.04 M I2 (Lancaster) and 0.05 M 4-tert-butylpyridine (Aldrich) in acetonitrile] was administered by a hole in the counter electrode and subsequently heat sealed with a glass slide backed with Surlyn.
DSSCs were tested under illumination of a 21-V 80-W tungsten lamp (Phillips, 13160). A Keithley 2400 source meter recorded the current across a linear voltage sweep from –0.2 to 0.9 V utilizing Labview 6.1 software (National Instruments). Light intensity corresponding to 1 Sun was determined by an externally calibrated photodiode.
3 Results and discussion
Unsintered electrodes were incorporated into DSSCs and were found to be very inefficient (Fig. 1). This is due to poor inter-particle connection between the nanoparticles and thus a lack of efficient pathways for the electrons to migrate to the conductive F:SnO2 substrate. DSSCs were also constructed from ZrO2-coated TiO2 electrodes which were produced by spin-coating of a zirconium isopropoxide solution onto the TiO2 electrode followed by hydrolysis at 70 °C. The additional organic species present in the ZrO2-coated TiO2 working electrodes did not affect the dye attachment with similar currents recorded in the DSSCs (Fig. 1). The addition of the zirconia film mainly influences the Voc (Table 1). This is due to the reduction in the charge recombination from the photoinjected electrons in the titanium dioxide conduction band (TiO2CB) to the oxidized electrolyte species (I3–). This charge recombination reaction results in the I3– being reduced to I– (Eq. (1)) and therefore reducing the cell efficiency (Fig. 2).
(1) |
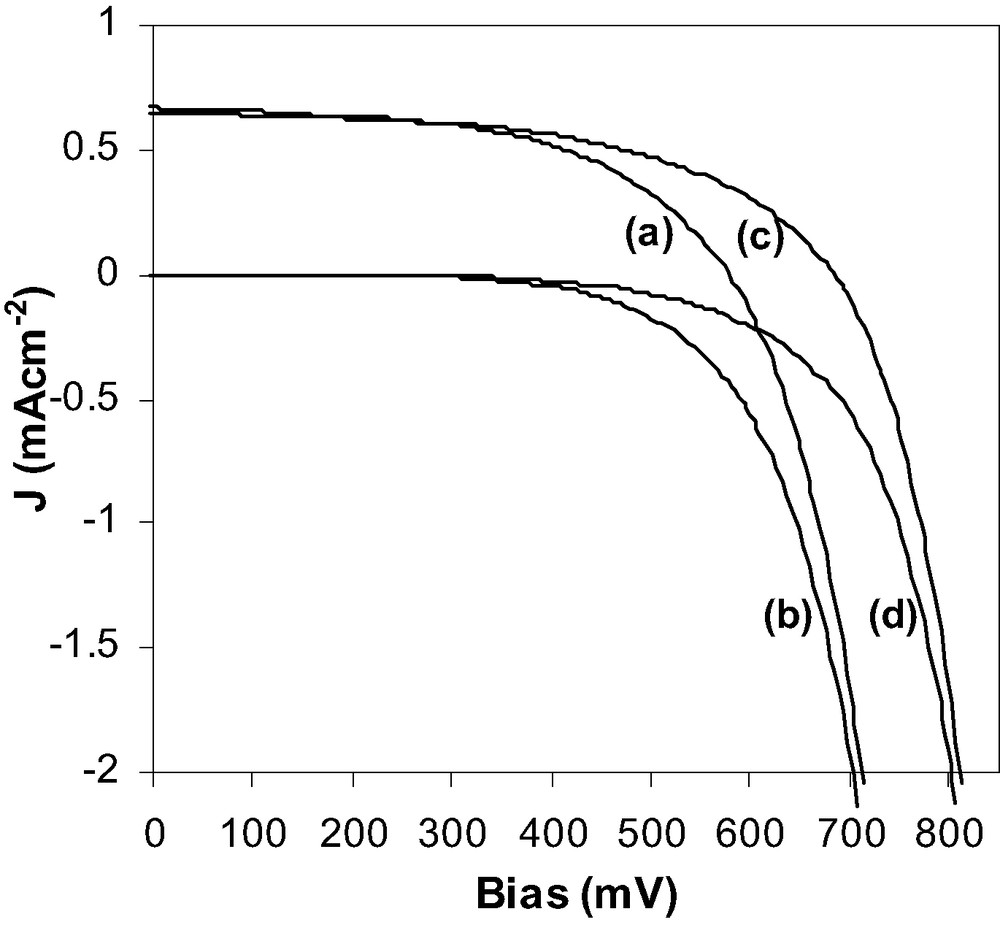
J–V curves for TiO2 under (a) 1 Sun and (b) dark current and for ZrO2-coated TiO2 under (c) 1 Sun and (d) dark current. Both samples were not sintered.
Photovoltaic data of DSSCs constructed from 0.25-cm2 working electrodes determined under 1 Sun illumination where A corresponds to unsintered and B corresponds to microwave sintered working electrodes
Data | Bare TiO2 | ZrO2-coated TiO2 | ||
A | B | A | B | |
Jsc (mA cm−2) | 0.67 | 6.24 | 0.65 | 6.56 |
Voc (mV) | 577 | 692 | 687 | 719 |
FF | 0.54 | 0.56 | 0.53 | 0.65 |
Efficiency (%) | 0.21 | 2.4 | 0.24 | 3.1 |

J–V curves for the DSSCs comprising 2.45-GHz microwave sintered (a) TiO2 and (b) ZrO2-coated TiO2 working electrodes.
This theory is supported by the dark-current data. The dark-current measurements, although not quantitative, give an overall indication of the charge recombination and more specifically the relative recombination rates of the DSSCs. Thus, the introduction of the ZrO2 film (Fig. 1) results in a reduction in that recombination reaction by having a 100-mV positive shift.
The typical heating rate for the working electrodes in the 2.45-GHz microwave was controlled maintaining a forward power of 450–500 W up to 450 °C and then maintaining the temperature by varying the forward power. Incorporation of these electrodes in DSSCs was found to improve the photovoltaic performance from that seen with the unsintered TiO2 (Table 1), up to 2.4% efficiency. This increase is due to increased inter-particle connections forming better pathways for electron migration through the film to the TCO glass support.
As was the case for the unsintered working electrodes, the photovoltaic performance was enhanced by the addition of the ZrO2 shell, consistent with previous work [10,15]. However, in this work the core-shell nanostructure was formed in a one-step process where the precursor solution was coated onto unsintered TiO2 electrodes. The common method by which core-shell nanostructured working electrodes are fabricated is coating sintered working electrodes with the dilute sol–gel precursor solution. This is then calcined to remove residual organics prior to dye adsorption. The one-step process displayed in this work is not optimal; however, it only requires one microwave heat-treatment as opposed to two conventional heat treatments.
From the photovoltaic data (Table 1) it can be seen that the current, voltage and fill factors are all increased with the presence of the ZrO2 shell coating. This can be said to be due to an ‘energy barrier’ at the surface of the semiconducting working electrode to act as an insulator between the photoinjected electrons in the TiO2CB and the oxidized dye molecules and the oxidized electrolyte species (I3–). The dark current measurements (Fig. 3) show that the presence of the ZrO2 shell the cell has a slight positive increase in the voltage. This means that the recombination rate is reduced from the photoinjected electrons in the TiO2CB to either the oxidized dye molecules or the I3–. Thus, the yield is increased with these one-step microwave calcined working electrodes in DSSCs.
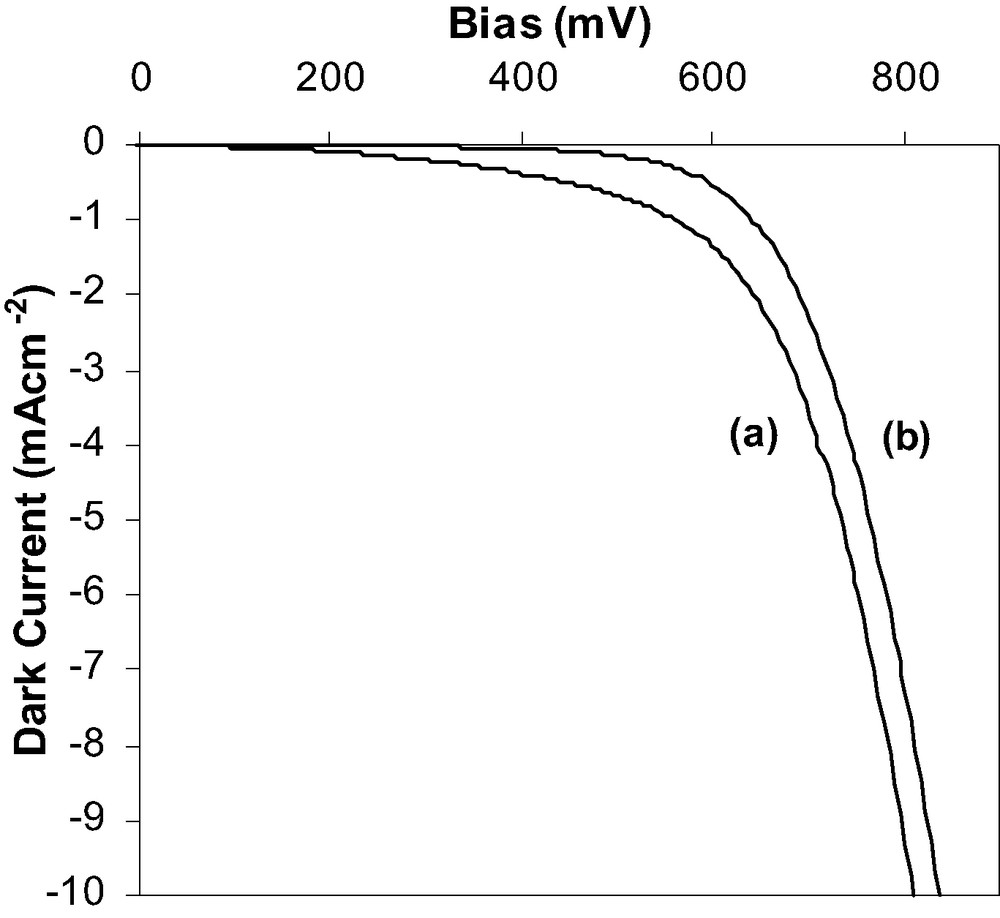
Dark current curves for the DSSCs comprising 2.45 GHz microwave sintered (a) TiO2 and (b) ZrO2-coated TiO2 working electrodes.
4 Conclusions
This work has shown that a thin ZrO2 coating can effectively increase the efficiency of the DSSCs. In addition, it is demonstrated that microwave processing can sinter the TiO2 particles together resulting in a useful nanostructured TiO2 working electrode. Microwave sintering of both bare TiO2 and ZrO2-coated TiO2 working electrodes was found to have a dramatic improvement in the performance of the DSSCs. The microwave-processed TiO2 electrodes were found to be 2.4% efficient, whereas the ZrO2-coated TiO2 electrodes performed greater at 3.1% efficient. This data compares well with that from DSSCs comprising conventionally sintered ZrO2-coated TiO2 electrodes.
Acknowledgements
This work was financially supported by a Monash Engineering Research Grant, the Australian Research Council and a Monash Graduate Scholarship. Special thanks to Dr. Sophie Cerneaux, Monash Solar Cells Group, for the French translation.