1 Introduction
Nanoporous TiO2 thin films for dye-sensitized and ETA solar cells have been under intense study for many years. In addition to the doctor-blade technique [1], the interest to prepare the materials by sol–gel methods [2–4] and chemical vapor deposition [5] has increased remarkably. The use of the sol–gel method applying dip coating, spin-coating or spray pyrolysis techniques to deposit TiO2 films has several advantages, such as low cost, simple apparatus set up and the possibility to control the properties of the film through the solution composition. Polyethylene glycol (PEG) is a well-known additive used in the sol–gel process to increase the porosity of the film [6,7]. Recently porous TiO2 films were prepared by the spray technique and the photovoltaic conversion efficiency of dye sensitized cells was increased up to 5.1% under AM-1.5 conditions [2].
In our earlier studies we found that dense TiO2 anatase films with a refractive index around 2.3 could be prepared by spray pyrolysis and spin-coating techniques using acetylacetone stabilized titanium isopropoxide sol [8,9].
This paper reports on investigations of nanoporous TiO2 films prepared either by spin-coating or spray pyrolysis using PEG in the precursor solution. The effect of the PEG concentration and different annealing routes on film composition, structural properties, morphology, pore and grain sizes is studied.
2 Experimental
TiO2 films were deposited either by spin-coating or spray pyrolysis techniques onto glass and n-type Si (100) substrates. For deposition by spin-coating the solution was prepared with a TTIP/AcAc/EtOH molar ratio of 1:2:42 and the amount of PEG600 in solution was varied in the range 1.5–46 g. Three coating cycles at a rotation speed of 3000 rpm were performed. The films were dried at 100 °C for 35 min. followed by annealing in a temperature region of 300–850 °C for 1 or 2 h.
For spray pyrolysis a precursor solution of TTIP/AcAc/EtOH at molar ratio of 1:2:52 with 46 g of PEG was used and the substrate temperature during the deposition was 350 or 500 °C. The solution was atomized by pneumatic spray nozzle (from Spraying Systems) using compressed air as carrier gas. Pulsed solution feed with an interval of 10 s of spraying and 300 s of pause was used. This procedure was repeated 30–50 times. The final heat treatment was performed in air at 500 °C for 2 h.
The crystal structure of the films was determined by XRD using a Bruker AXS D5005 diffractrometer with monochromatic Cu Kα radiation. The IR spectra of the samples on silicon wafers were recorded on a Perkin Elmer FT-IR GX1 spectrometer. The surface morphology and cross-section studies were performed by scanning electron microscopy (SEM) on a LEO SUPRA 35. The pore and grain sizes were determined by SEM at high magnifications. The thickness of the films was determined from the SEM cross-sectional micrographs.
3 Results
3.1 XRD and IR study
XRD patterns of TiO2 films on glass made by spray pyrolysis at 500 °C are presented in Fig. 1 (as deposited: a, post-annealed at 500 °C: b). The as-deposited films prepared at substrate temperatures below 500 °C are found to be amorphous. As-sprayed films grown at 500 °C (Fig. 1a) show a broad peak belonging to the anatase phase (PDF 21-1272). Post-annealing of the films at 500 °C sharpens the diffraction peaks of the anatase phase (Fig. 1b). Crystallite sizes calculated from the XRD pattern using the Scherrer formula are 5 nm and 9 nm in the as-deposited and the annealed film, respectively.

XRD patterns of sprayed TiO2 films: (a) as-deposited at 500 °C; (b) after film annealing at 500 °C for 2 h in air.
For spin-coated TiO2 films, crystalline anatase is observed only at temperatures above 700 °C (patterns not shown). The IR spectra of TiO2 films deposited either by spin coating or spray pyrolysis are presented in Figs. 2 and 3. The strong absorption bands close to 2875 and 1120 cm−1 in the spin-coated film (Fig. 2, the precursor solutions containing 3 g PEG) dried at 100 °C (Fig. 2a) are assigned to the presence of the PEG (since they are not observed, when PEG is absent). The absorption bands are significantly weakened by annealing at 300 °C indicating the purification from organic residues containing functional groups active in middle infrared spectrum region (Fig. 2b). Further annealing at higher temperatures promotes the formation of Ti–O–Ti anatase bonds, confirmed by the appearance of the peak at around 430 cm−1 [10].

FTIR spectra of TiO2 films prepared by spin-coating technique from the solution containing 3 g PEG and annealed at different temperatures for 1 h.
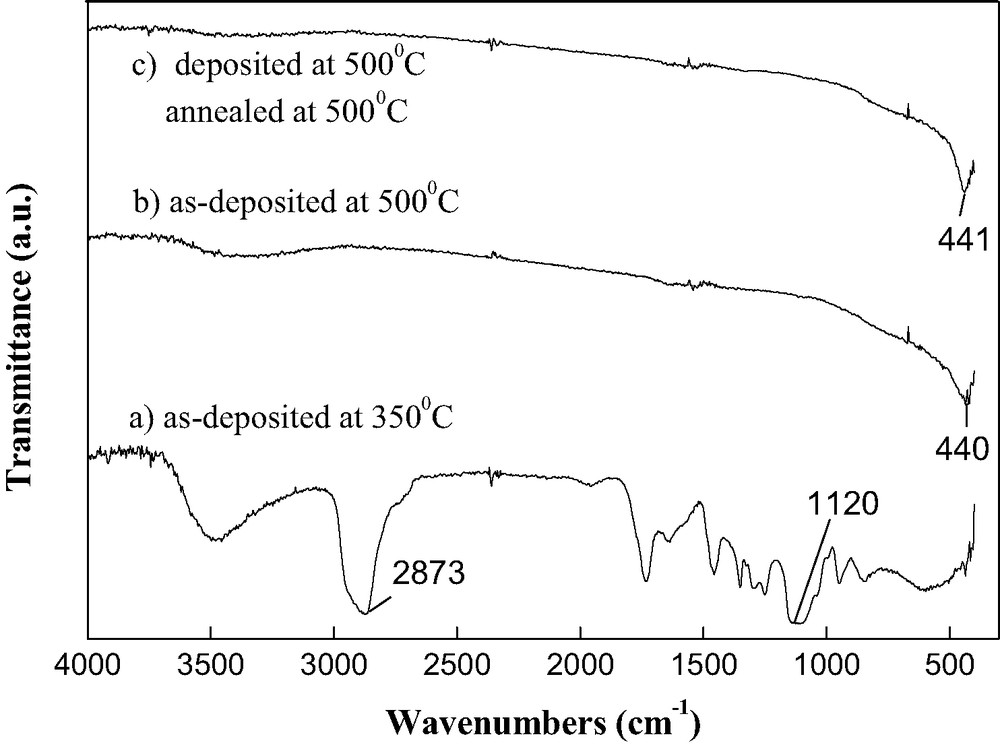
FTIR spectra of TiO2 films prepared by spray pyrolysis technique: (a) as-deposited at T = 350 °C; (b) as-deposited at T = 500 °C, (c) deposited at T = 500 °C and annealed at 500 °C for 2 h in air.
The sprayed films deposited at 350 °C (from precursor solutions containing 46 g PEG) still contain organic compounds (Fig. 3a). This is different from dense, spray-pyrolized TiO2 films that were free of organic residues at growth temperatures as low as 315 °C [9]. Currently spray-pyrolized TiO2 films free from organic compounds can be grown at a substrate temperature of 500 °C. At this temperature the formation of anatase Ti–O–Ti bonds (around 440 cm−1) could be observed. Further annealing at 500 °C for 2 h in air determines the sharpness of this band (Fig. 3c).
3.2 Morphological properties
Fig. 4 shows SEM micrographs of the surface of as-deposited (a) and annealed (b) TiO2 films grown by spray pyrolysis. The SEM investigations show that the as-deposited films contain pores and grains with diameters about 2–7 nm. By annealing at 500 °C the diameters of both increase up to 10–20 nm (Fig. 4b). The SEM micrographs of the cross-section reveal an average pore size of approximately 20 nm in the as-deposited and 40 nm in the annealed film (Fig. 5). The grain size increases from 15 up to 25 nm. The thickness of the film was found to be approximately 2.3 μm after 50 spray pulses.
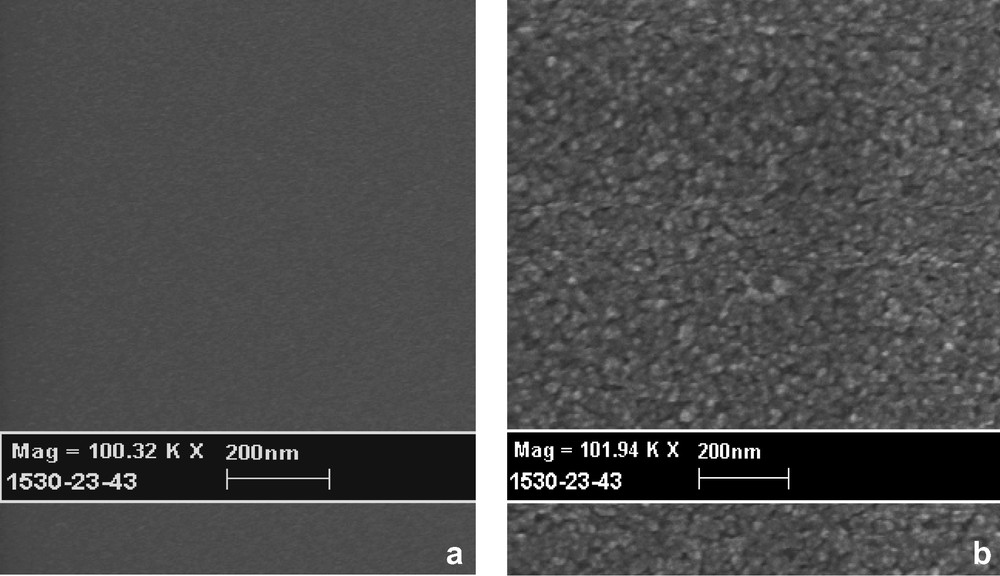
SEM micrographs of sprayed TiO2 films: (a) as-deposited at 500 °C; (b) deposited at 500 °C and annealed at 500 °C for 2 h in air.
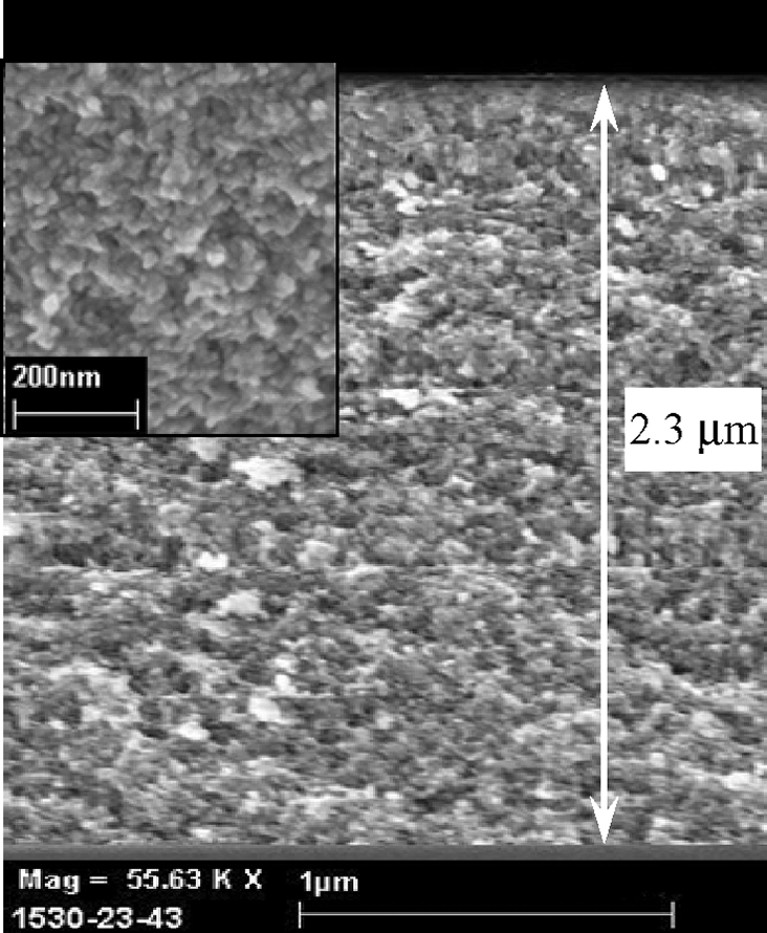
The cross-section of sprayed film shown in Fig. 4b.
Fig. 6 shows SEM micrographs of spin coated TiO2 film surfaces prepared from precursor solutions with different amounts of PEG600 (a–d) (1.5, 4.6, 21 and 46 g, respectively) after annealing at 450 °C. It is observed that the surface morphology is related to the amount of PEG used. The TiO2 films prepared with very small amount of PEG are quite smooth (Fig. 6a). The films contain pores and grains with sizes about 7 and 15 nm, respectively. Higher PEG concentrations in the precursor solution result in increased sizes of pores and grains. Pores of about 10–15 nm and grains of 15–25 nm are obtained for the coatings prepared from the precursor solution containing 4.6 g PEG (Fig. 6b). Pore and grain sizes reach maximum values of 25 and 35 nm, respectively, at 21 g of PEG (Fig. 6c). Further increase of the amount of PEG decreases the sizes of pores and grains (Fig. 6d). A similar effect is observed for spin coated films by other authors as well [11]. According to the SEM cross-sectional micrograph the film thickness is approximately 120 nm.
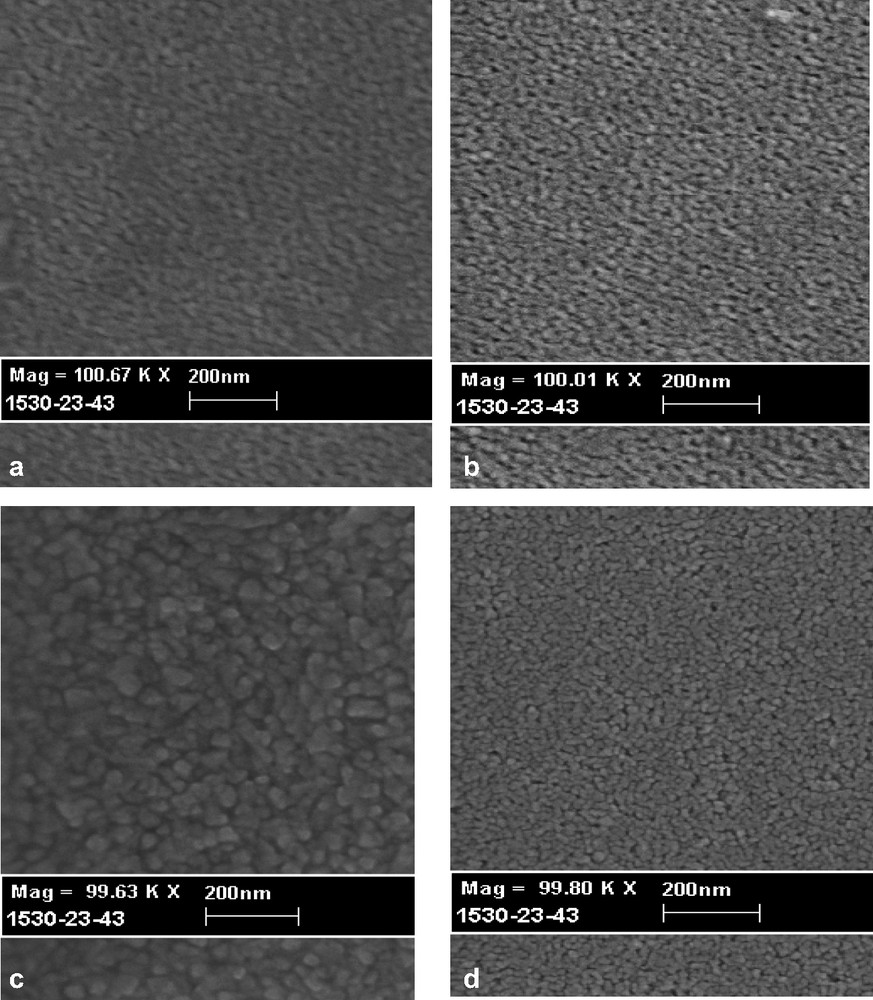
SEM micrographs of spin coated TiO2 films prepared with different amount of PEG600: (a) 1.5 g, (b) 4.6 g, (c) 21 g, (d) 46 g in solution. The films are annealed at 450 °C for 1 h in air.
4 Conclusions
Nanoporous TiO2 films in a thickness range of about 0.1–2.3 μm have been prepared from acetyl acetone stabilized titaniumisopropoxide sols containing PEG as an additive. Spin-coating and spray pyrolysis were compared as film deposition techniques. Crystalline films with anatase structure could be grown by the spray technique at 500 °C. From the XRD peak-width crystallite sizes of 5 and 9 nm were calculated for as-deposited and annealed, respectively. The pore sizes in such films were up to 40 nm after annealing at 500 °C according to SEM.
When depositing the films by spin-coating the formation of Ti–O–Ti anatase bonds in the films is observed after annealing at 450 °C. However, the film becomes crystalline only after annealing at temperatures above 700 °C.
Pore and grain sizes in spin coated film are controlled by the amount of PEG added into the starting sol and can be controlled in the range of 7–25 and 15–35 nm, respectively.
Acknowledgements
This work has been carried out under the financial support from the European Commission RTN-project HRNP-CT-2000-00141 and Estonian Science Foundation grant 5612.